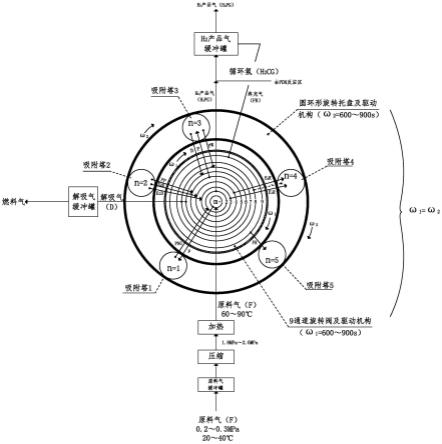
pdh原有工艺的改变,并且新工艺流程长、动态设备投资大、占地面积大,以及psa装置中程序控制阀及调节阀组数目巨大导致的装置稳定性差等诸多问题依然无法解决,尤其是石化厂中空间有限,psa工艺装置占地面积较大而受到很大的应用限制。因此,若在深冷工序后面增加一套或二套多塔轴向流固定床psa装置来实现循环氢气中满足烯烃总量小于0.05%前提下同时得到高纯度h2产品气,投资、占地面积与稳定性就会大大限制其应用。此外,由于pdh混合气中的烯烃组分属于极性较强的吸附质组分,在吸附过程中容易发生深度吸附导致解吸困难,使得在吸附与解吸循环操作中因吸附剂解吸再生不完全导致少量的烯烃组分穿透而流入到非吸附相气体中,进而使得循环氢气中的烯烃含量超标。即使采用全温程变压吸附(ftrpsa)工艺,但因烯烃分子中存在着双键,尤其是丁二烯等不对称的双键,会在较高的温度下仍然会发生深度吸附的问题。这是由于传统的轴向流固定床层吸附塔具有一定的高径比,使得传质路径足够的长而使得吸附质组分被吸附,而对于烯烃组分而言,过长的传质路径也容易导致深度吸附。同时,减少吸附时间或循环操作时间,可以避免深度吸附,但又会造成烯烃过早地穿透,导致循环氢气中的烯烃含量不达标。针对烯烃组分吸附容易再生困难的突出问题,工业上采取了几种处理方法,第一,采用固定床ftrpsa工艺,通过事先找到一个合适的操作温度范围进行吸附与解吸的循环操作,使得烯烃吸附质组分在吸附与解吸过程中达到一种动态的平衡,即,吸附容易解吸也容易。现有公开的“一种丙烷脱氢制丙烯循环氢的ftrpsa提氢方法”等专利为代表,但由于固定床操作自身由于较大的死空间率,即使避免了深度吸附,但“产品收率与纯度之间的反比关系”的矛盾却无法避免;第二,对于含烯烃组分的pdh混合气中脱除c
2+
提纯h2而言,c
2+
(尤其是烯烃)的psa操作压力低有利于避免深度吸附导致的解吸困难问题,这与psa提取h2工段需要较高的操作压力有利于h2的收率提升形成明显的矛盾,吸附相组分的浓缩与非吸附相组分的提纯过程之间存在较大差异,因此,常规的psa工艺是分拆成两段,低压吸附脱除c
2+
,高压吸附提纯h2,导致流程过长、设备与控制阀门大幅度增加、装置稳定性更差、占地面积更大。第三,pdh混合气中吸附质组分非常复杂,表现在其吸附机理通常为平衡吸附与动力学吸附乃至化学吸附混合型,如ch4与乙烷(c2h6)通常在活性炭及分子筛上以动力学扩散速度为主导的吸附,乙烯、丙烯、丁二烯等烯烃类c
2+
组分多为平衡吸附或双键型的化学吸附主导,而丁烷等高沸点烷烃组分常常在不同的吸附剂上的吸附机理完全不同,而且容易发生深度吸附导致解吸困难,co2的吸附机理在通常的平衡型吸附剂上的吸附机理为平衡吸附,而在碳分子筛上却表现出较强的动力学吸附机理特征,同时,co2与ch4、co2与c2h6、ch4与c2h6等组分在吸附剂上会发生共吸附现象等,使得吸附过程变得复杂。这种原料工况的复杂性,目前只有传统的轴向流固定复合吸附剂床层的多段psa工艺才能较好的应对;第四,美国uop公司曾采用吸附剂循环的循环移动床(cmb)变温吸附(tsa)工艺净化脱除与回收c
2+
,同时增设一套轴向流固定床psa提取h2装置与之配套而实现了乙烯混合气中获得h2纯度为99.99%、收率为86%的脱除c
2+
与提纯h2过程,但由于吸附剂循环过程中的磨损非常大导致吸附剂使用寿命缩短,并且吸附剂再生是在200℃以上的较高温度下进行的,吸附时是在较低温度下进行的,因而吸附剂循环过程中还因自身存在的温度应力差异导致吸附剂的磨损更加大,消耗更加多,进而,uop已放弃该工艺。
技术实现要素:4.针对前述现有pdh混合气脱c
2+
提纯h2的各种固定床(fb)或移动床(mb)吸附工艺的一些问题,本发明提出了一种全温程模拟旋转移动变压吸附(full temperature range simulated rotated moving psa——ftrsrmpsa)新工艺用于pdh混合气psa脱除c
2+
提纯h2,该工艺是一种以变压吸附(psa)为基础,充分利用pdh混合气中h2与主要吸附质c
2+
杂质组分,尤其是烯烃在60~120℃温度范围,以及0.2~4.0mpa压力范围内的吸附分离系数及物理化学性质的差异性,将置于一多通道旋转阀中央且在其周围安置于一圆环形旋转托盘上多个轴向流固定床吸附塔并通过管道连接以及调控旋转阀旋转方向与旋转速度(ω1)、圆环形旋转托盘旋转方向与旋转速度(ω2),使得流经旋转阀通道及通道进出口端与圆环形旋转托盘上的吸附塔进出口端连接的管道及吸附塔中旋转移动的吸附床层的气体,在不断地通过进出每个吸附塔进出口的位置及每个吸附床层在旋转同时完成各自的吸附与解吸步骤的传质,进而形成了“模拟旋转移动床”的变压吸附过程,实现了轴向流固定床变压吸附基础上的模拟旋转移动床变压吸附过程,使得吸附与解吸多步骤的循环操作,在实现收率与纯度“双高”及避免深度吸附的同时,适用于pdh混合气相应的流量、组分浓度、压力或温度的波动工况,充分利用了轴向流固定床变压吸附及现有技术包括循环床、流化床、旋转轮吸附及模拟移动床的各种优势,克服了这些现有技术工艺的缺陷,具体方案如下:一种pdh混合气脱c
2+
提h2的全温程模拟旋转移动床变压吸附工艺,所述的全温程模拟旋转移动床变压吸附(ftrsrmpsa)系统是由n(4≤n≤20的自然整数)个装载有一种或多种吸附剂的轴向流固定床层吸附塔并安置在一个以旋转速度(ω2,秒(s)为单位)的圆环形旋转托盘上的吸附塔、有m(6≤m≤36的自然整数)个通道并安置在圆环形旋转托盘中央的以旋转速度(ω1,秒(s)为单位)旋转的旋转阀、旋转阀与系统外物料气体进出的物料管道以及连接于经圆环形托盘内置管道至吸附塔上下与旋转阀之间的工艺管道,以及相应的驱动圆环形旋转托盘及旋转阀旋转方向及其调控其旋转速度(ω1与ω2)的驱动机构、缓冲罐、真空泵/或增压机所构成而形成一个ftrsrmpsa系统,其特征在于,吸附塔进出口与旋转阀进出口连接的管道是通过预设在圆环形旋转托盘的内置管道相连形成工艺管道且与旋转阀通道数m相同,进出ftrsrmpsa系统物料气体的位置是由多通道旋转阀旋转的通道加以分配来固定,其物料气体包括pdh混合气为原料气(f)、包括循环氢(h2cg)在内的h2产品气(h2pg)、系统外的冲洗气(p)、系统外的终充气(fr)以及逆放(d)气或/与抽真空气(v)或/与冲洗废气(pw)组成的解吸气(d),并相应的连接包括缓冲罐(器)、增压/抽真空泵、循环泵在内的设备,由旋转阀进出口与吸附塔进出口之间通过圆环形旋转托盘中内置管道连接的工艺管道中工艺气体流动的位置是移动变化的,工艺气体是在ftrsrmpsa系统内流动,包括原料气(f)、顺放气(pp)、系统内外的冲洗气(p)、均压降气(ed)、逆放气(d)气或/与抽真空气(v)或/与冲洗废气(pw)组成的解吸气(d)、均压升气(er)、终充气(fr)及产品氢气(h2pg),具体吸附与解吸的循环过程为,来自ftrsrmpsa系统外的原料pdh混合气(f)进入多通道旋转阀原料气(f)通道进口,并经旋转阀原料气(f)通道及出口、圆环形旋转托盘内置管道及圆环形旋转托盘上对应的处于吸附状态的一个或多个轴向流固定床吸附塔进口连接的工艺管道,从吸附塔底部进入进行吸附(a),经过旋转阀旋转方向及旋转速度(ω1)与圆环形旋转托盘旋转方向及旋转速度(ω2)之间的调控匹配连续地步进,从处于吸附状态的吸附塔顶部流出的非吸附相气体正好经工艺管道进入多通道旋转阀h2产品气(h2pg)通道,并从
旋转阀h2产品气(h2pg)通道流出形成h2产品气(h2pg),h2纯度大于等于99.95%,其中的烯烃总含量小于等于0.05%,一部分作为循环氢(h2cg)返回至pdh反应区循环使用,一部分作为产品气进入h2产品气缓冲罐后输出,另一部分直接用于pdh产品分馏区中的炔烃丙二烯选择性加氢(shp),处于吸附状态的吸附塔完成吸附(a)步骤后,随着多通道旋转阀与圆环形旋转托盘继续旋转步进,或/与吸附(a)结束的吸附塔对另一个或几个处于冲洗(p)或均压升(er)状态的吸附塔通过系统内的工艺管道进行顺放(pp)或均压降(ed),结束顺放(pp)或均压降(ed)步骤的吸附塔,随着多通道旋转阀与圆环形旋转托盘持续地旋转步进而进入逆放(d)或/与抽真空(v)或/与冲洗(p)步骤,从吸附塔流出的逆放气(d)或/与抽真空气(v)或/与冲洗废气(pw)所形成的解吸气(d),或流经圆环形旋转托盘内置管道或外置管道以及旋转阀逆放气(d)/抽真空气(v)/冲洗废气(pw)通道及其出口端流出并流经解吸气(d)缓冲罐,或作为燃料气使用,或进行碳氢比调节后作为原料气进入到天然气/轻烃类水蒸气重整反应制备氢气(smb)装置循环使用,结束逆放(d)或/与抽真空(v)或/与冲洗(p)步骤的吸附塔,随着多通道旋转阀与圆环形旋转托盘连续不断地旋转步进而进入均压升(er)或/与等待区(-)步骤,从处于均压降(ed)步骤的吸附塔流出并经圆环形旋转托盘内置管道及旋转阀均压降气(ed)通道而进入处于均压升(er)步骤的吸附塔进行均压,使得处于均压升(er)步骤的吸附塔内的压力与处于均压降(ed)步骤的吸附塔内的压力相等为止,结束均压升(er)或/与等待区(-)步骤的吸附塔,随着多通道旋转阀与圆环形旋转托盘进一步连续旋转而进入终充(fr)步骤,来自h2产品气(h2pg)或原料气(f)作为终充气(fr)流经多通道旋转阀终充气(fr)通道与圆环形旋转托盘内置管道进入吸附塔进行充压直至吸附塔内的压力达到吸附(a)步骤所需的吸附压力为止,并准备下一轮吸附与解吸的循环操作,其中,每一个吸附塔或进行一个步骤或多个步骤且进行每一步骤,均通过多通道旋转阀旋转方向及旋转速度(ω1)与圆环形旋转托盘旋转方向及旋转速度(ω2)之间的调控匹配,使得旋转中的多通道旋转阀中m个通道与圆环形旋转托盘旋转中的n个吸附塔吸附与解吸的循环操作中的时序表首尾连接成圆,并完整地形成变压吸附(psa)吸附与解吸过程的操作循环性,所有的物料气体及工艺气体被均匀交替地分布在系统中的旋转阀中m个圆通道与圆环形旋转托盘中内置管道及各个吸附塔内,并将一个循环周期的变压吸附(psa)通过旋转的多通道旋转阀与接通的相应旋转的圆环形旋转托盘上吸附塔分别同时进行吸附与解吸过程中的各个步骤,进出吸附塔的工艺气体位置是通过旋转阀旋转方向及旋转速度(ω1)与圆环形旋转托盘旋转方向及旋转速度(ω2)匹配而不断地变化,使得每个吸附塔重复进行吸附与解吸步骤,相当于每个固定床吸附塔在多通道旋转阀与圆环形旋转托盘旋转的同时完成各自的吸附与解吸步骤,进而形成了“模拟旋转移动床”的变压吸附过程,由此,从含h2/c
2+
的pdh混合气中脱除c
2+
并获得的包括循环氢(h2cg)在内的产品h2(h2pg),其纯度大于等于99.95%,其中,烯烃总量小于等于0.05%,h2产品气(h2pg)收率大于等于92%。
5.更进一步的,所述的一种pdh混合气脱c
2+
提h2的全温程模拟旋转移动床变压吸附工艺,其特征在于,所述的多通道旋转阀及圆环形旋转托盘旋转方向及其调控其旋转速度(ω1与ω2)之间的调控匹配,包括,1)同向同步,顺时针或逆时针方向的同向旋转,且,ω1=ω2且ω1≠0/ω2≠0,2)同向异步,顺时针或逆时针方向的同向旋转,且,ω1>ω2或ω1<ω2或ω1≠0/ω2=0或ω1=0/ω2≠0,3)异向同步,顺时针/逆时针或逆时针/顺时针的异向旋转,且,ω1=ω2且ω1≠0/ω2≠0,4)异向异步,顺时针/逆时针或逆时针/顺时针的异向旋
转,且,ω1>ω2或ω1<ω2或ω1≠0/ω2=0或ω1=0/ω2≠0,优选的,同向同步,且,ω1=ω2且ω1≠0/ω2≠0,或,同向异步,顺时针或逆时针方向的同向旋转,且ω1>ω2或ω1≠0/ω2=0或ω1=0/ω2≠0。
6.更进一步的,所述的一种pdh混合气脱c
2+
提h2的全温程模拟旋转移动床变压吸附工艺,其特征在于,所述的全温程模拟旋转移动床变压吸附(ftrsrmpsa)的吸附与解吸的闭合循环操作步骤的组合还包括,1次分浓度吸附、1~2次均压、1~2批次冲洗、1次抽真空、1~2次的加热与冷却换热的变温变压吸附、1次顺放步骤与均压降步骤顺序相互错位、1~2个等待区、1次置换解吸步骤,且,吸附塔数(n)与相应的多通道旋转阀通道数(m)增加、吸附塔高(半)径比(h/r)减少,以及多通道旋转阀或圆环形旋转托盘旋转速度足够快或旋转周期足够短,pdh混合气h2与c
2+
的分离与净化的效果无限接近移动床“稳态”传质分离与净化效果,最终获得h2产品气(h2pg)的纯度大于等于99.99%,且,其中的烯烃总含量小于等于0.01%,产品气收率大于等于95%。
7.更进一步的,所述的一种pdh混合气脱c
2+
提h2的全温程模拟旋转移动床变压吸附工艺,其特征在于,所述的作为原料的pdh混合气(f)来自,或uop-pdh的oleflex工艺的冷箱不凝气体,或abb lummus-pdh的无循环氢catofin工艺的冷箱不凝气体,或“丙烷脱氢制丙烯反应混合气冷油吸收与psa耦合的分离方法”工艺的中冷油吸收工艺的吸收塔不凝气体,主要组分为,浓度为80~98%的氢气(h2)、1~10%的甲烷、1~5%烷烃与烯烃及微量的co2与co,温度为10~160℃,压力为常压至4.0mpa,且,经过加热或冷却或直接至60~120℃,与,增压或直接至0.2~4.0mpa,作为原料气进入ftrsrmpsa系统。
8.更进一步的,所述的一种pdh混合气脱c
2+
提h2的全温程模拟旋转移动床变压吸附工艺,其特征在于,所述的均压降(ed)与均压升(er),最多次数为2,最少次数为1,且吸附操作压力范围为大于等于0.6mpa与小于等于4.0mpa。
9.更进一步的,所述的一种pdh混合气脱c
2+
提h2的全温程模拟旋转移动床变压吸附工艺,其特征在于,所述的冲洗气(p),或来自系统内的顺放气(pp),或来自系统外的h2产品气(h2pg),通过多通道旋转阀通道(槽道)中一个或多个的开孔实现分批次进行冲洗,开孔数至多为4个,优选的来自系统内的顺放气(pp)作为冲洗气(p),h2产品气(h2pg)的收率达到93%以上。
10.更进一步的,所述的一种pdh混合气脱c
2+
提h2的全温程模拟旋转移动床变压吸附工艺,其特征在于,所述的逆放解吸步骤采用抽真空方式进行解吸,增设的真空泵,或与解吸气流出多通道旋转阀的物流管道相连,或与圆环形旋转托盘上的吸附塔出口端连接的外置管道直接相连且在外置管道上设有控制阀门,优选的与圆环形旋转托盘上的吸附塔出口端连接的外置管道直接相连且在外置管道上设有控制阀门。
11.更进一步的,所述的一种pdh混合气脱c
2+
提h2的全温程模拟旋转移动床变压吸附工艺,其特征在于,所述的终充气(fr),或来自系统外的转化气原料(f)或h2产品气(h2pg),在h2产品气(h2pg)纯度大于等于99.99%且烯烃总量小于等于0.01%的工况下,优选的采用h2产品气(h2pg)作为终充气(fr)。
12.更进一步的,所述的一种pdh混合气脱c
2+
提h2的全温程模拟旋转移动床变压吸附工艺,其特征在于,所述的ftrsrmpsa系统所产生的h2产品气(h2pg),用作循环氢气使用与用作产品氢气输出的氢气之间的比例,或,用作循环氢气(h2cg)使用的氢气与用于pdh产品分
馏区的氢气之间的比例,根据循环氢气(h2cg)循环量、系统中多通道旋转阀与圆环形旋转托盘的旋转速度(ω1与ω2)、n个吸附塔的吸附剂装填量与吸附塔高径比以及循环氢气(h2cg)中烯烃总量的要求进行调节,以保证满足pdh反应区内循环氢气(h2cg)量的严格要求。
13.本发明的有益效果是:(1)通过本发明,可以将传统的全温程固定复合床层psa的吸附与解吸循环操作模式模拟变成全温程旋转轮移动床psa工艺,获得比固定床层或典型的扇形吸附室旋转轮psa效率更高的产品h2的纯度与收率,突破了常规与全温程固定吸附床层所具有的“纯度与收率呈反比关系”的技术限制,又大幅度降低了旋转轮psa工艺与装备制造复杂性及成本,使得h2产品气的纯度大于等于99.95%,收率大于等于92~95%,并且作为pdh制丙烯工艺中循环氢气(h2cg)中的烯烃总含量小于等于0.01~0.05%,满足pdh循环氢气的严格要求。
14.(2)本发明通过对多通道旋转阀与圆环形旋转托盘的旋转方向与旋转速度(ω1与ω2)之间的调控匹配,能够在传统的固定床psa工艺上实现多组合多步骤的吸附与解吸的psa循环操作,并能灵活地根据产品h2的技术指标要求进行调节且含盖了包括多通道旋转阀与传统的固定床psa组合工艺以及典型的扇形吸附室旋转轮psa或快轮psa的移动床工艺等现有的移动床psa工艺。
15.(3)本发明大幅度降低了传统的固定床psa或全温程变压吸附(ftrpsa)的pdh混合气脱c
2+
提h2装置的程序控制阀门及调节阀门的数量,同时也将现有全温程变压吸附(ftrpsa)工艺的二段psa(浓缩与提氢)合并成一个ftrsrmpsa系统,进一步降低了设备投资、占地面积与生产成本。
16.(4)本发明通过多通道旋转阀与圆环形旋转托盘的旋转方向与旋转速度(ω1与ω2)之间的调控匹配来适应于不同pdh工艺所产生的混合气及其出现较大的波动工况,包括组分、浓度、压力、流量等的波动,操作弹性较大,并无需旋转轮或快轮psa工艺所需的昂贵的规整式吸附剂,可采用常规的颗粒吸附剂并组成复合吸附剂床层。
17.(5)本发明依据pdh工艺中循环氢循环量及其烯烃总含量的限制指标,可以通过多通道旋转阀转速ω1与圆环形旋转托盘转速ω2的调配、吸附塔的高径比与吸附剂装填量等措施,来调节pdh工艺中循环氢(h2cg)与外输产品氢气(h2pg)的比例,并通过多通道旋转阀通(槽)道中开设通孔及工艺气体共用通道等措施,打破了现有的多通道旋转阀制造过程中通道数受到限制的缺陷,使得本发明的吸附与解吸循环操作的步骤增加,进一步提升了传质效率,获得高纯度与高收率的“双高”h2产品。
18.(6)本发明根据pdh混合原料气及其波动工况和循环氢气(h2cg)与产品h2技术指标的要求,通过调节多通道旋转阀及圆环形旋转托盘的旋转方向及旋转速度ω1与ω2的匹配以及吸附压力与温度,对吸附塔的高径比进行调整与设计,使得轴向流固定床中的径向扩散忽略不计而满足轴向流固定床成熟的传质模型,而轴向流扩散随着ω1或ω2的加快以及高径比的减少,其影响越来越小,进而使得吸附塔内的传质过程更加趋近循环床为代表的移动床所具有的“稳态”效应,h2产品的纯度与收率更趋向于“双高”。
附图说明
19.图1为本发明实施例1流程示意图。
20.图2为本发明实施例3流程示意图。
具体实施方式
21.为了使本领域的技术人员更好地理解本发明,下面将结合本发明实施例中的附图对本发明实施例中的技术方案进行清楚、完整的描述。
22.实施例1如图1所示,一种pdh混合气脱c
2+
提h2的全温程模拟旋转移动床变压吸附工艺,其中,全温程模拟旋转移动床变压吸附(ftrsrmpsa)系统是由5(n=5)个高径比为2.5~3.0且装载有三氧化二铝、硅胶、活性炭与分子筛多种吸附剂组成的轴向流固定复合床层吸附塔并安置在一个以旋转速度(ω2=600~900s)的圆环形旋转托盘上的吸附塔、有9(m=9)个通道并安置在圆环形旋转托盘中央的以旋转速度(ω1=600~900s)旋转的9通道旋转阀、9通道旋转阀与系统外物料气体进出的物料管道以及连接于经圆环形旋转托盘内置管道至吸附塔上下与9通道旋转阀之间的工艺管道,以及相应的驱动圆环形旋转托盘及9通道旋转阀旋转方向及其调控其旋转速度(ω1与ω2)的驱动机构、缓冲罐与压缩机所构成而形成一个ftrsrmpsa系统,吸附塔进出口与旋转阀进出口连接的管道是通过预设在圆环形旋转托盘的内置管道相连形成工艺管道且与9通道旋转阀通道数相同,进出ftrsrmpsa系统物料气体的位置是由9通道旋转阀旋转的通道加以分配来固定,其物料气体包括pdh混合气的原料气(f)、包括循环氢气(h2cg)在内的h2产品气(h2pg)、以h2产品气(h2pg)为终充气(fr)以及逆放气(d)和冲洗废气(pw)组成的解吸气(d),并相应的连接包括缓冲罐(器)、压缩机在内的设备,由9通道旋转阀进出口与5个吸附塔进出口之间通过圆环形旋转托盘中内置管道连接的工艺管道中工艺气体流动的位置是移动变化的,工艺气体是在ftrsrmpsa系统内流动,包括原料气(f)、系统内的冲洗气(p)、一均压降气(e1d)、二均压降气(e2d)、顺放气(pp)、逆放气(d)与冲洗废气(pw)组成的解吸气(d)、一均压升气(e1r)、二均压升气(e2r)、等待区(-)、以h2产品气(h2pg)为终充气(fr),以及包括循环氢气(h2cg)在内的产品氢气(h2pg),具体吸附与解吸的循环过程为,来自ftrsrmpsa系统外的原料气(f),是以uop-pdh的oleflex工艺中冷箱(深冷)产生的不凝气体为原料气,其组成主要包括浓度为92~98%的氢气(h2)、1~2%的甲烷、乙烷等烷烃、0.1~0.5%的烯烃,以及微量的co、co2及水杂质组分,温度为20~40℃,压力为0.2~0.3mpa,经压缩机增压至1.8~2.0mpa且加热至60~90℃后进入9通道旋转阀原料气(f)进口,并经旋转阀原料气(f)通道(如m=1)及出口、圆环形旋转托盘内置管道及圆环形旋转托盘上对应的处于吸附状态的1个轴向流固定床吸附塔(如图1所示的吸附塔1,n=1)进口连接的工艺管道,从吸附塔底部进入进行吸附(a),经过9通道旋转阀旋转方向及旋转速度(ω1)与圆环形旋转托盘旋转方向及旋转速度(ω2)之间的调控匹配为,顺时针同向且ω1=ω2=600~900s的同向同步,并连续地步进,从处于吸附(a)步骤的吸附塔(n=1)顶部流出的非吸附相气体正好经工艺管道进入9通道旋转阀h2产品气(h2pg)通道(如m=2),并从9通道旋转阀h2产品气(h2pg)通道流出形成h2产品气(h2pg),h2的纯度大于等于99.99%,其中的烯烃总含量小于等于0.01%,70%作为循环氢气(h2cg)返回至pdh反应区循环使用,20%作为产品气进入h2产品气(h2pg)缓冲罐后输出,10%直接用于pdh产品分馏区中的炔烃丙二烯选择性加氢(shp)使用,随着9通道旋转阀与圆环形旋转托盘继续地同向同步的旋转步进,全部完成吸附(a)步骤后的吸附塔1同时也旋转至如图1所示的吸附塔2(n=2)的原先位置,依次进入第一次均压降(e1d)、第二次均压降(e2r)与顺放(pp)步骤,吸附塔2也由如图1所示的初
始位置旋转步进至图1所示的吸附塔3的初始位置上,而吸附塔3同时从其初始位置旋转步进至吸附塔4的初始位置上,吸附塔4步进移动至吸附塔5的初始位置,而吸附塔5步进移动至吸附塔1的初始位置,5个吸附塔在连续地旋转步进中进行各自相应的吸附与解吸的步骤,与此同时,从吸附塔1塔底流出的一次均压降气(e1d)流经圆环形旋转托盘内置管道及9通道旋转阀旋转中对应的一次均压降气(e1d)与一次均压升气(e1r)共用通道(如m=3)及对应的圆环形旋转托盘内置管道与正处于一次均压升(e1r)步骤的吸附塔4(n=4)进口而进入吸附塔4进行一次均压升(e1r)步骤,使得吸附塔1与吸附塔4内的压力相等于0.8~0.9mpa为止,结束一次均压降(e1d)步骤的吸附塔1随着9通道旋转阀与圆环形旋转托盘继续同向同步地旋转步进进入第二次均压降(e2d)步骤,产生的二次均压降气(e2d)流经圆环形旋转托盘内置管道与9通道旋转阀中二次均压降气(e2d)与二次均压升气(e2r)共用通道(如m=4)及对应的圆环形旋转托盘内置管道进入处于第二次均压升(e2r)步骤的吸附塔4进行二次均压升(e2r)步骤,使得吸附塔1与吸附塔4内的压力相等于0.2~0.3mpa为止,结束二次均压降(e2d)步骤的吸附塔1随着9通道旋转阀与圆环形旋转托盘继续同向同步地旋转步进进入顺放(pp)步骤,由此产生的顺放气(pp)作为系统内的冲洗气(p)流经圆环形旋转托盘内置管道与9通道旋转阀中顺放气(pp)与冲洗气(p)共用通道(如m=5)及对应的圆环形旋转托盘内置管道进入处于冲洗(p)步骤的吸附塔3进行冲洗(p),吸附塔3产生的冲洗废气(pw)作为解吸气(d)流经圆环形旋转托盘内置管道与9通道旋转阀冲洗废气(pw)通道(如m=7)及通道出口端与解吸气(d)缓冲罐连接的物料管道进入解吸气(d)缓冲罐,随着9通道旋转阀与圆环形旋转托盘继续同向同步地旋转步进,结束顺放(pp)步骤的吸附塔1旋转步进至如图1所示的吸附塔3的初始位置,依次进行逆放(d)与冲洗(p)步骤,吸附塔2、3、4与5也依次旋转步进移动至相应的新位置进行各自的吸附与解吸步骤,吸附塔1进行逆放(d)步骤产生的逆放气(d)作为解吸气(d)流经圆环形旋转托盘内置管道及9通道旋转阀逆放气(d)通道(如m=6)及通道出口端与解吸气(d)缓冲罐连接的物料管道进入解吸气(d)缓冲罐并输出作为燃料气使用,结束逆放(d)步骤的吸附塔1随后进行冲洗(p)步骤,来自处于顺放(pp)步骤的吸附塔5(n=5)的顺放气(pp)作为冲洗气(p)对吸附塔1进行冲洗(p),从中产生的冲洗废气(pw)作为解吸气(d)流经圆环形旋转托盘内置管道与9通道旋转阀冲洗废气(pw)通道(如m=7)及通道出口端与解吸气(d)缓冲罐连接的物料管道进入解吸气(d)缓冲罐,随着9通道旋转阀与圆环形旋转托盘继续同向同步地旋转步进,结束冲洗(p)步骤的吸附塔1旋转步进至如图1所示的吸附塔4的初始位置,依次进行二次均压升(e2r)、一次均压升(e1r)与等待(-)步骤,吸附塔2、3、4与5也依次旋转步进移动至相应的新位置进行各自的吸附与解吸步骤,来自此时处于二次均压降(e2d)步骤的吸附塔4产生的二次均压降气(e2d)流经圆环形旋转托盘内置管道与9通道旋转阀中二次均压降气(e2d)与二次均压升气(e2r)共用通道(如m=4)及对应的圆环形旋转托盘内置管道进入处于第二次均压升(e2r)步骤的吸附塔1进行二次均压升(e2r)步骤,使得吸附塔1与吸附塔4内的压力相等于0.2~0.3mpa为止,结束二次均压升(e2r)步骤的吸附塔1随着9通道旋转阀与圆环形旋转托盘继续同向同步地旋转步进而进入等待区(-)步骤,此时,对应的9通道旋转阀等待区(-)通道为空道(如m=8),结束等待(-)步骤的吸附塔1随后进入一次均压升(e1r)步骤,来自此时处于一次均压降(e1d)步骤的吸附塔4塔底流出的一次均压降气(e1d)流经圆环形旋转托盘内置管道及9通道旋转阀旋转中对应的一次均压降气(e1d)与一次均压升气(e1r)共用通道(如m=3)及对应的圆环形旋转托
盘内置管道与正处于一次均压升(e1r)步骤的吸附塔1进口而进入吸附塔1进行一次均压升(e1r)步骤,使得吸附塔1与吸附塔4内的压力相等于0.8~0.9mpa为止,结束一次均压升(e1r)步骤的吸附塔1,随着9通道旋转阀与圆环形旋转托盘继续同向同步地旋转步进至如图1所示的吸附塔5的初始位置而进入终充(fr)步骤,吸附塔2、3、4与5也依次旋转步进移动至相应的新位置进行各自的吸附与解吸步骤,来自h2产品气(h2pg)作为终充气(fr)流经9通道旋转阀终充气(fr)通道(如m=9)与圆环形旋转托盘内置管道进入吸附塔1进行充压直至吸附塔内的压力达到吸附(a)步骤所需的吸附压力1.8~2.0mpa为止,并准备下一轮吸附与解吸的循环操作,其中,每一个吸附塔进行每一步骤或多个步骤,均通过9通道旋转阀旋转方向(顺时针)及旋转速度(ω1=600~900s)与圆环形旋转托盘旋转方向(顺时针)及旋转速度(ω2=600~900s)之间的同向同步的调控匹配,使得旋转中的9通道旋转阀中9个通道与圆环形旋转托盘旋转中的5个吸附塔吸附与解吸的循环操作中的时序表首尾连接成圆,并完整地形成变压吸附(psa)吸附与解吸过程的操作循环性,即,吸附(a)-一次均压降(e1d)/二次均压降(e2d)/顺放(pp)-逆放(d)/冲洗(p)-二次均压升(e2r)/等待(-)/一次均压升(e1r)-终充(fr),所有的物料气体及工艺气体被均匀交替地分布在系统中的9通道旋转阀中9个圆通道与相应的圆环形旋转托盘中内置管道及5个吸附塔内,并将一个循环周期的变压吸附(psa)通过旋转的9通道旋转阀(ω1)与接通的相应旋转的圆环形旋转托盘(ω2)上吸附塔分别同时进行吸附与解吸过程中的各个步骤,进出各个吸附塔的工艺气体位置是通过9通道旋转阀旋转方向及旋转速度(ω1)与圆环形旋转托盘旋转方向及旋转速度(ω2)同向同步的匹配而不断地变化,使得每个吸附塔均可重复吸附与解吸步骤,相当于每个固定床吸附塔在9通道旋转阀与圆环形旋转托盘同向同步旋转步进的同时完成各自的吸附与解吸步骤,进而形成了“模拟旋转移动床”的变压吸附(psa5-1-2p,即,5塔-1塔吸附-2次均压-逆放与冲洗解吸)过程,由此,从含h2/c
2+
的pdh混合气中获得的满足于pdh工艺循环氢气(h2cg)要求的产品h2,其纯度大于等于99.99%,其中烯烃总含量小于等于0.01%,其收率为92~93%。
23.实施例2如图1所示,在实施例1基础上,原料气进入ftrsrmpsa系统,其中,将系统中的圆环形旋转托盘的旋转速度ω2调整为0,即不转动,而9通道旋转阀旋转方向仍然维持在顺时针方向,其旋转速度ω1调整为ω1=300~400s水平,5个吸附塔的位置固定,而通过9通道旋转阀定期顺时针旋转步进使得每个吸附塔均经历吸附(a)-一次均压降(e1d)/二次均压降(e2d)/顺放(pp)-逆放(d)/冲洗(p)-二次均压升(e2r)/等待区(-)/一次均压升(e1r)-终充(fr)的吸附与解吸的循环操作步骤,其中,冲洗气(p)来自系统内的顺放气(pp),冲洗废气(pw)与逆放气(d)作为解吸气(d),一次均压降(e1d)/一次均压升(e1r)步骤结束的吸附塔内的压力均为0.8~0.9mpa,二次均压降(e2d)/二次均压升(e2r)步骤结束的吸附塔内的压力均为0.2~0.3mpa,9通道旋转阀中的9个通道作用分别为,1个通道(如m=1)供原料气(f)、1个通道(如m=2)供h2产品气(h2pg)、1个共用通道(如m=3)供一次均压降(e1d)与对应的一次均压升(e1r)、1个共用通道(如m=4)供二次均压降(e2d)与对应的二次均压升(e2r)、1个共用通道(如m=5)供顺放气(pp)与对应的作为冲洗气(p)、1个通道(如m=6)供作为解吸气(d)的逆放气(d)、1个通道(如m=7)供作为解吸气(d)冲洗废气(pw)、1个通道(如m=8)供等待区(空道)、1个通道(如m=9)供h2产品气(h2pg)为终充气(fr)使用,所有的物料气体及工艺气体被均匀交替地分布在系统中的9通道旋转阀中9个圆通道与圆环形旋转托盘中内置管道
及各个吸附塔内,并将一个循环周期的变压吸附(psa)通过旋转的9通道旋转阀(ω1)与接通的相应静止的圆环形旋转托盘(ω2=0)上吸附塔分别同时进行吸附与解吸过程中的各个步骤,进出吸附塔的工艺气体位置是通过9通道旋转阀旋转方向及旋转速度(ω1)而不断地变化,使得每个吸附塔重复吸附与解吸步骤,相当于每个固定床吸附塔在不旋转下随着9通道旋转阀旋转过程中完成各自的吸附与解吸步骤,进而形成了“模拟旋转移动床”的变压吸附(psa5-1-2p,即,5塔-1塔吸附-2次均压-冲洗解吸)过程,由此,从含h2/c
2+
的转化气中获得的产品h2,其纯度大于等于99.95%,其中的烯烃总含量小于0.05%,其收率为92%,相较于实施例1,由于圆环形旋转托盘静止不移动,而9通道旋转阀旋转速度加快,以此来弥补圆环形旋转托盘不转动,但得到的h2产品的纯度与收率略低于实施例1。
24.实施例3如图2所示,在实施例2基础上,采用抽真空(v)解吸步骤替代逆放(d)步骤,抽真空(v)形成的解吸气(d)从吸附塔出口端流出并流经与圆环形旋转托盘上的吸附塔出口端连接的外置管道且在外置管道上设有真空泵及控制阀门控制流量后进入解吸气(d)缓冲罐,最大真空度为-0.08mpa,相应的9通道旋转阀中原来的逆放气(d)通道(如m=6)变为空道,而随后的以顺放气(pp)为冲洗气(p)除了冲洗(p)还填充了吸附塔的真空状态,使得吸附塔回到常压或微正压状态,并且冲洗废气(pw)返回至原料气(f)缓冲罐中,进一步回收冲洗废气(pw)中的有效组分h2,与此同时,9通道旋转阀的旋转速度ω1调整为400~600s,圆环形旋转托盘依旧静止不移动(ω2=0),psa吸附与解吸的循环操作周期略为延长,由此,本实施例中,每个吸附塔经历了吸附(a)-一次均压降(e1d)/二次均压降(e2d)/顺放(pp)-抽真空(v)/冲洗(p)-二次均压升(e2r)/等待区(-)/一次均压升(e1r)-终充(fr)的吸附与解吸的循环操作步骤,但相较于实施例2,h2产品气(h2pg)的纯度大于等于99.95%,收率大于等于93%,其解吸比较彻底,吸附剂使用寿命比较长。
25.显而易见的,上面所述的实施例仅仅是本发明实施例中的一部分,而不是全部。基于本发明记载的实施例,本领域技术人员在不付出创造性劳动的情况下得到的其它所有实施例,或在本发明的启示下做出的结构变化,凡是与本发明具有相同或相近的技术方案,均落入本发明的保护范围之内。