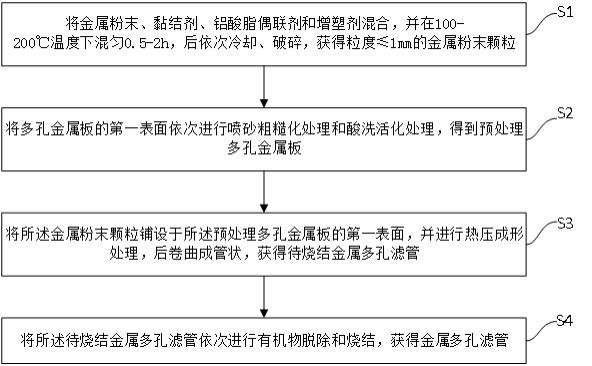
1.本发明属于过滤材料技术领域,特别涉及一种无支撑型金属多孔滤管及其制备方法。
背景技术:2.多孔金属材料可作为过滤材料,常应用在能源、化工、医药、环保等方面,在实际使用时,其材料种类可分为粉末冶金多孔材料、复合丝网材料、粉网复合材料、金属纤维材料等。
3.目前,粉末冶金多孔过滤管可以是由金属粉末经等静压压制成型后烧结而成,其管壁较厚(3-5mm),作为过滤元件强度高,但过滤通量小。复合丝网滤管是由多层丝网复合轧制而成,再经高温烧结而成,具有较高的过滤通量,但强度差,容易变形,常会在管内添加孔管支撑或骨架作为支撑,且过滤精度低。金属粉末或金属纤维与丝网复合制得的复合过滤材料,具有高通量和高精度的优异性能,类似的专利如cn 106964261 a“柔性金属过滤薄膜及其制造方法”、cn 108079666 a“一种低阻降过滤材料及其制备方法”等,可将高过滤精度与高通量性能结合,性能优异,主要应用在高温低压除尘领域,使用效果受到了良好的评价。但这种复合过滤材料滤芯受限于设备和技术,往往只能做成1m-1.5m一个单元,然后通过焊接或螺纹连接,制成长度6-8m的滤芯,由于这种材质较软,往往内部也需要添加通孔管或骨架作为支撑,造成工艺复杂,且套入通孔管或骨架时容易发生剐蹭,破坏滤材表面质量。因此,本领域亟需研发一种在高通量和高精度的前提下,实现无支撑的过滤材料。
技术实现要素:4.本技术的目的在于提供一种无支撑型金属多孔滤管及其制备方法,解决现有的过滤材料无法实现在高通量和高精度的前提下,满足无支撑的技术问题。
5.第一方面,本发明实施例提供一种无支撑型金属多孔滤管,一种无支撑型金属多孔滤管,其特征在于,包括多孔金属板和粉末烧结层,所述粉末烧结层贴设于所述多孔金属板的第一表面,并部分填充于所述多孔金属板的多个孔隙。
6.可选的,所述粉末烧结层的原料组分包括金属粉末,所述金属粉末包括不锈钢粉末、镍合金粉末和钛合金粉末的任意一种。
7.可选的,所述粉末烧结层的原料组分包括黏结剂,所述黏结剂为pvb、pmma和peg的混合物。
8.可选的,所述粉末烧结层的原料组分包括增塑剂,所述增塑剂为dop或dbp。
9.可选的,所述多孔金属板的材质为不锈钢、镍、镍合金、钛和钛合金中的一种。
10.可选的,所述多孔金属板在纵向边界处设有3-5mm的致密处,以供氩弧焊或电阻焊焊接。
11.可选的,所述多孔金属板的尺寸包括长度≤2m,宽度≤1m,厚度为0.6-1.2m。
12.可选的,所述多孔金属板的多个所述孔隙的形状为圆孔和/或方孔,直径为0.3-0.5mm。
13.第二方面,本发明实施例提供一种第一方面所述的无支撑型金属多孔滤管的制备方法,所述方法包括:将金属粉末、黏结剂、铝酸脂偶联剂和增塑剂混合,并在100-200℃温度下混匀0.5-2h,后依次冷却、破碎,获得粒度≤1mm的金属粉末颗粒;将多孔金属板的第一表面依次进行喷砂粗糙化处理和酸洗活化处理,得到预处理多孔金属板;将所述金属粉末颗粒铺设于所述预处理多孔金属板的第一表面,并进行热压成形处理,后卷曲成管状,获得待烧结金属多孔滤管;将所述待烧结金属多孔滤管依次进行有机物脱除和烧结,获得金属多孔滤管。
14.可选的,所述热压成形处理的工艺条件包括:成形温度:140-300℃,成型压力:15-20吨,给料速度:0.1-0.5m/min。
15.可选的,所述烧结包括从始至终的第一阶段烧结、第二阶段烧结、第三阶段烧结和第四阶段烧结,其中,所述第一阶段烧结的工艺条件包括:以2-4℃/min的升温速度从室温升到100-120℃保温30min;所述第二阶段烧结的工艺条件包括:以1℃/min的升温速度从所述第一阶段烧结的终点温度升到250-350℃保温1-2h;所述第三阶段烧结的工艺条件包括:以2-4℃/min的升温速度从所述第二阶段烧结的终点温度升到500-550℃保温1h,所述第四阶段烧结的工艺条件包括:以5-10℃/min的升温速度从所述第三阶段烧结的终点温度升至 900-1200℃保温2-4h。
16.本发明实施例中的一个或多个技术方案,至少具有如下技术效果或优点:本发明实施例提供的无支撑型金属多孔滤管,通过多孔金属板和粉末烧结层的联合使用,采用多孔金属板作为基体,具有良好的抗变形能力,不需要另添加打孔管作为支撑体,在多孔金属板表面设置了粉末烧结层,大幅提高了过滤精度,同时还具有良好的过滤通量,以此达到了金属多孔滤管在高通量和高精度的前提下,满足无支撑。
17.上述说明仅是本发明技术方案的概述,为了能够更清楚了解本发明的技术手段,而可依照说明书的内容予以实施,并且为了让本发明的上述和其它目的、特征和优点能够更明显易懂,以下特举本发明的具体实施方式。
附图说明
18.为了更清楚地说明本发明实施例中的技术方案,下面将对实施例描述中所需要使用的附图作一简单地介绍,显而易见地,下面描述中的附图是本发明的一些实施例,对于本领域普通技术人员来讲,在不付出创造性劳动的前提下,还可以根据这些附图获得其它的附图。
19.图1是本发明实施例提供的方法的流程图。
具体实施方式
20.下文将结合具体实施方式和实施例,具体阐述本发明,本发明的优点和各种效果将由此更加清楚地呈现。本领域技术人员应理解,这些具体实施方式和实施例是用于说明本发明,而非限制本发明。
21.在整个说明书中,除非另有特别说明,本文使用的术语应理解为如本领域中通常所使用的含义。因此,除非另有定义,本文使用的所有技术和科学术语具有与本发明所属领域技术人员的一般理解相同的含义。若存在矛盾,本说明书优先。本文中所使用的专业术语只是为了描述具体实施例的目的,并不是旨在限制本发明的保护范围。例如,室温可以是指10~35℃区间内的温度。特别地,本文使用的“第一”、“第二”等词语,不表示顺序关系,用作区分可以理解为名词。
22.除非另有特别说明,本发明中用到的各种原材料、试剂、仪器和设备等,均可通过市场购买得到或者可通过现有方法制备得到。
23.本文中缩略语的中文定义如下:pvb:聚乙烯醇缩丁醛酯,pmma:聚甲基丙烯酸甲酯,peg:聚乙二醇,dop:邻苯二甲酸二辛酯,dbp:邻苯二甲酸二丁酯。
24.本技术实施例的技术方案为解决上述技术问题,总体思路如下:第一方面,本发明实施例提供一种无支撑型金属多孔滤管,包括多孔金属板和粉末烧结层,所述粉末烧结层贴设于所述多孔金属板的第一表面,并部分填充于所述多孔金属板的多个孔隙。
25.一般情况下,粉末烧结层距第一表面的厚度为60-100μm,原因是粉末烧结层过厚会影响透气性,过薄则肯能会有粉末缺失、烧结强度不足的缺陷。
26.在一些实施方式中,所述粉末烧结层的原料组分包括金属粉末、黏结剂、铝酸脂偶联剂和增塑剂。
27.本技术中,粉末烧结层的原料可以为金属粉末、黏结剂、铝酸脂偶联剂和增塑剂的混合物,以质量份数计,四者的用量可以是金属粉末7-8份、黏结剂1-2.5份、铝酸脂偶联剂0.05-0.2份和增塑剂0.1-1份,具体应用时,配比可以如下:1、金属粉末8份、黏结剂1份、铝酸脂偶联剂0.1份和增塑剂0.9份;2、金属粉末7份、黏结剂2份、铝酸脂偶联剂0.2份和增塑剂0.8份;3、金属粉末7.5份、黏结剂1.5份、铝酸脂偶联剂0.2份和增塑剂0.8份;金属粉末的作用可以是:组成粉末烧结层,通过粉末堆积烧结控制过滤精度。
28.黏结剂的作用可以是:使粉末与多孔金属板在成形时黏结。
29.铝酸脂偶联剂的作用可以是:对金属粉末进行改性,使表面亲有机,提高粉末的分散性。
30.增塑剂的作用可以是:降低黏结剂的玻璃化转变温度,使黏结剂在热压成型后,还具有良好的塑形和韧性,在卷管时不会裂开。
31.在一些实施方式中,所述金属粉末包括不锈钢粉末、镍合金粉末和钛合金粉末的任意一种,所述黏结剂为pvb、pmma和peg的混合物,所述增塑剂为dop或dbp。
32.金属粉末选用不锈钢粉末、镍合金粉末和钛合金粉末的进一步积极作用:不同的工况会选择不同的材质,不锈钢粉末烧结后可在400-800℃的工况下使用,镍合金粉末可以在600-1000℃下使用,而钛合金粉末烧结相比不锈钢粉末可以在较低温度下的一些腐蚀工况下使用,如含氯离子腐蚀工况。黏结剂选用pvb、pmma和peg的混合物的进一步积极作用:这种混合黏结剂具有熔体塑性好,易脱脂的优点。
33.增塑剂选用dop或dbp的进一步积极作用:能够有效降低pvb和pmma的玻璃化转变温度。
34.在一些实施方式中,所述金属粉末的平均粒度范围为5-30μm。
35.金属粉末的平均粒度范围为5-30μm的进一步积极作用:这个范围内的粉末成本适宜,流动性好,过滤精度可满足大部分工况需求,取值过小的不利影响是成本高,易团聚且过小烧结后孔径小会极大的降低透气性,取值过大的不利影响是不能满足过滤精度要求。
36.在一些实施方式中,所述多孔金属板的材质为不锈钢、镍、镍合金、钛和钛合金中的一种。
37.多孔金属板的材质选用不锈钢、镍、镍合金、钛或钛合金的进一步积极作用:与粉末材质对应,有利于烧结结合。
38.在一些实施方式中,所述多孔金属板的尺寸包括长度≤2m,宽度≤1m,厚度为0.6-1.2mm。
39.多孔金属板的尺寸设计为长度≤2m,宽度≤1m,厚度为0.6-1.2mm的进一步积极作用:市场上常用滤筒单元尺寸为60-160mm,因此宽度≤1m已可以满足市场需求,滤筒长度太长一方面会增加运输成本,一方面也会增加焊接难度。
40.在一些实施方式中,所述多孔金属板的多个所述孔隙的形状为圆孔和/或方孔,直径为0.3-0.5mm。
41.孔隙的形状为圆孔和/或方孔的进一步积极作用:这种形状的孔容易填充,成本低。
42.直径为0.3-0.5mm的进一步积极作用:取值过小的不利影响是多孔金属板的孔隙率会变低,影响透气性,取值过大的不利影响是网孔过大,降低刚性。
43.第二方面,如图1所示,本发明实施例提供一种第一方面所述的无支撑型金属多孔滤管的制备方法,所述方法包括:s1、将金属粉末、黏结剂、铝酸脂偶联剂和增塑剂混合,并在100-200℃温度下混匀0.5-2h,后依次冷却、破碎,获得粒度≤1mm的金属粉末颗粒;s2、将多孔金属板的第一表面依次进行喷砂粗糙化处理和酸洗活化处理,得到预处理多孔金属板;s3、将所述金属粉末颗粒铺设于所述预处理多孔金属板的第一表面,并进行热压成形处理,后卷曲成管状,获得待烧结金属多孔滤管;s4、将所述待烧结金属多孔滤管依次进行有机物脱除和烧结,获得金属多孔滤管。
44.本技术中,金属粉末颗粒控制为粒度≤1mm的原因:能够有良好的颗粒流动性,可以均匀的填充在多孔金属板上。
45.冷却的工艺条件可以是:风冷或室外冷却至室温即可;喷砂粗糙化处理的目的是增加粗糙度,使金属粉末颗粒软化后能更好的与多孔金
属板结合不至于折叠后开裂、脱落,喷砂粗糙化至第一表面的粗糙度达到ry60-100μm;酸洗活化处理的目的是去除表面氧化层,使表面粗糙化,使粉末颗粒更容易与多孔金属板形成良好的冶金结合;卷曲成管状过程中,一般可采用氩弧焊对纵缝处进行焊接固定;有机物脱除的工艺可以为:先使用50-70℃的蒸馏水将待烧结金属多孔滤管浸泡0.5-1h,以将大部分peg脱出。再通过后续烧结前三段工艺进一步的脱去有机物。
46.在一些实施方式中,所述热压成形处理的工艺条件包括:成形温度:140-300℃,给料速度:0.1-0.5m/min。
47.该热压成形处理的工艺条件的积极作用是使粉末颗粒中的有机物融化,在压力作用下能与多孔金属板形成良好的粘结,同时热压处理也可以使粉末颗粒充分的填充到多孔金属板的空隙中;其中,成形温度取值过小的不利影响是不能使黏结剂软化,黏结剂塑形流动性较差,取值过大的不利影响是有机物会挥发脱出,形成气孔;给料速度取值过小的不利影响是影响生产效率,取值过大的不利影响是轧制时间过短,轧制不上。
48.在一些实施方式中,所述烧结包括从始至终的第一阶段烧结、第二阶段烧结、第三阶段烧结和第四阶段烧结,其中,所述第一阶段烧结的工艺条件包括:以2-4℃/min的升温速度从室温升到100-120℃保温30min;所述第二阶段烧结的工艺条件包括:以1℃/min的升温速度从所述第一阶段烧结的终点温度升到250-350℃保温1-2h;所述第三阶段烧结的工艺条件包括:以2-4℃/min的升温速度从所述第二阶段烧结的终点温度升到500-550℃保温1h,所述第四阶段烧结的工艺条件包括:以5-10℃/min的升温速度从所述第三阶段烧结的终点温度升至 900-1200℃保温2-4h。
49.本技术中,将烧结设置为上述从始至终的第一阶段烧结、第二阶段烧结、第三阶段烧结和第四阶段烧结的目的为第一段烧结温度为了充分去除料中的水汽,保温是为了防止水汽过快逸出形成气孔;第二烧结温度是缓慢脱除料中的pvb、pmma和增塑剂;第三烧结温度是进一步脱出料中残余的有机物;第四阶段烧结温度是使粉末颗粒之间及粉末颗粒与金属板之间形成良好的烧结结合。烧结处理可以在保护气氛中进行,保护气氛可以为氢气、氮气和分解氨气体中的任意一种。
50.下面将结合实施例、对照例及实验数据对本技术的方案进行详细说明。
51.实施例1本实施例提供一种无支撑型金属多孔滤管的制备方法,所述方法包括:s101、将金属粉末、黏结剂、铝酸脂偶联剂和增塑剂按8:1:0.1:0.9比例混合,并在200℃温度下混匀2h,后依次冷却、破碎,获得粒度为1mm的金属粉末颗粒;金属粉末为纯钛粉末,黏结剂为pvb、pmma和peg的混合物,比例为4:1:5,增塑剂为dop;金属粉末的平均粒度范围为30μm;
s201、将多孔金属板的第一表面依次进行喷砂粗糙化处理和酸洗活化处理,得到预处理多孔金属板;多孔金属板的材质为钛合金;多孔金属板在纵向边界处设有3mm的致密处,以供氩弧焊或电阻焊焊接;多孔金属板的尺寸包括长度2m,宽度1m,厚度为1.2mm;多孔金属板的多个所述孔隙的形状为圆孔,直径为0.5mm;s3011、将长、宽尺寸相同的不锈钢致密薄板与多孔金属板的第二表面对齐并固定封住,后将所述金属粉末颗粒铺设于所述预处理多孔金属板的第一表面,该面朝上,送进加热型辊压机以0.5m/min的给进速度并在300℃、20吨成型压力下成形;s3012、拆除不锈钢致密薄板,剪裁后卷曲成管状,并采用氩弧焊对纵缝处进行焊接固定,获得待烧结金属多孔滤管;s401、将所述待烧结金属多孔滤管依次进行有机物脱除和烧结,获得金属多孔滤管;有机物脱除的工艺可以为:先使用70℃的蒸馏水将待烧结金属多孔滤管浸泡1h,以将大部分peg脱出。
52.烧结包括从始至终的第一阶段烧结、第二阶段烧结、第三阶段烧结和第四阶段烧结,气氛选用氮气保护,其中,所述第一阶段烧结的工艺条件包括:以4℃/min的升温速度从室温升到120℃保温30min;所述第二阶段烧结的工艺条件包括:以1℃/min的升温速度从所述第一阶段烧结的终点温度升到350℃保温2h;所述第三阶段烧结的工艺条件包括:以4℃/min的升温速度从所述第二阶段烧结的终点温度升到550℃保温1h,所述第四阶段烧结的工艺条件包括:以10℃/min的升温速度从所述第三阶段烧结的终点温度升至 1100℃保温4h。
53.实施例2本实施例提供一种无支撑型金属多孔滤管的制备方法,所述方法包括:s102、将金属粉末、黏结剂、铝酸脂偶联剂和增塑剂按7:2:0.2:0.8混合,并在100-200℃温度下混匀0.5-2h,后依次冷却、破碎,获得粒度为1mm的金属粉末颗粒;金属粉末为310s不锈钢粉末,黏结剂为pvb、pmma和peg的混合物,增塑剂为dop;金属粉末的平均粒度范围为20μm;s202、将多孔金属板的第一表面依次进行喷砂粗糙化处理和酸洗活化处理,得到预处理多孔金属板;多孔金属板的材质为310s不锈钢;多孔金属板在纵向边界处设有5mm的致密处,以供氩弧焊或电阻焊焊接;多孔金属板的尺寸为长度2m,宽度1m,厚度为0.9mm;多孔金属板的多个所述孔隙的形状为圆孔,直径为0.4mm;s3021、将长、宽尺寸相同的不锈钢致密薄板与多孔金属板的第二表面对齐并固定封住,后将所述金属粉末颗粒铺设于所述预处理多孔金属板的第一表面,该面朝上,送进加
热型辊压机以0.3m/min的给进速度并在220℃、18吨成型压力下成形;s3022、拆除不锈钢致密薄板,剪裁后卷曲成管状,并采用氩弧焊对纵缝处进行焊接固定,获得待烧结金属多孔滤管;s402、将所述待烧结金属多孔滤管依次进行有机物脱除和烧结,获得金属多孔滤管;有机物脱除的工艺可以为:先使用60℃的蒸馏水将待烧结金属多孔滤管浸泡0.8h,以将大部分peg脱出。
54.烧结包括从始至终的第一阶段烧结、第二阶段烧结、第三阶段烧结和第四阶段烧结,气氛选用氢气保护,其中,所述第一阶段烧结的工艺条件包括:以3℃/min的升温速度从室温升到110℃保温30min;所述第二阶段烧结的工艺条件包括:以1℃/min的升温速度从所述第一阶段烧结的终点温度升到300℃保温1.5h;所述第三阶段烧结的工艺条件包括:以3℃/min的升温速度从所述第二阶段烧结的终点温度升到520℃保温1h,所述第四阶段烧结的工艺条件包括:以8℃/min的升温速度从所述第三阶段烧结的终点温度升至 1150℃保温3h。
55.实施例3本实施例提供一种无支撑型金属多孔滤管的制备方法,所述方法包括:s103、将金属粉末、黏结剂、铝酸脂偶联剂和增塑剂按7.5:1.5:0.2:0.8混合,并在100-200℃温度下混匀0.5-2h,后依次冷却、破碎,获得粒度0.5mm的金属粉末颗粒;金属粉末为inconel625镍合金粉末,黏结剂为pvb、pmma和peg的混合物,增塑剂为dbp;金属粉末的平均粒度范围为5μm;s203、将多孔金属板的第一表面依次进行喷砂粗糙化处理和酸洗活化处理,得到预处理多孔金属板;多孔金属板的材质为inconel600合金;多孔金属板在纵向边界处设有4mm的致密处,以供氩弧焊或电阻焊焊接;多孔金属板的尺寸包括长度为1m,宽度为0.5m,厚度为0.6mm;多孔金属板的多个所述孔隙的形状为方孔,直径为0.3mm;s3031、将长、宽尺寸相同的不锈钢致密薄板与多孔金属板的第二表面对齐并固定封住,后将所述金属粉末颗粒铺设于所述预处理多孔金属板的第一表面,该面朝上,送进加热型辊压机以0.1m/min的给进速度并在140℃、15吨成型压力下成形;s3032、拆除不锈钢致密薄板,剪裁后卷曲成管状,并采用氩弧焊对纵缝处进行焊接固定,获得待烧结金属多孔滤管;s403、将所述待烧结金属多孔滤管依次进行有机物脱除和烧结,获得金属多孔滤管;有机物脱除的工艺可以为:先使用50℃的蒸馏水将待烧结金属多孔滤管浸泡0.5-1h,以将大部分peg脱出。
56.烧结包括从始至终的第一阶段烧结、第二阶段烧结、第三阶段烧结和第四阶段烧结,气氛选用分解氨气体保护,其中,所述第一阶段烧结的工艺条件包括:以2℃/min的升温速度从室温升到100℃保温30min;所述第二阶段烧结的工艺条件包括:以1℃/min的升温速度从所述第一阶段烧结的终点温度升到250℃保温1h;所述第三阶段烧结的工艺条件包括:以2℃/min的升温速度从所述第二阶段烧结的终点温度升到500℃保温1h,所述第四阶段烧结的工艺条件包括:以5℃/min的升温速度从所述第三阶段烧结的终点温度升至 900℃保温2h。
57.为证明发明的优越性,特以对比例1-2进行对照对比例1 使用平均粒径为30μm的纯钛粉通过冷等静压压制成3mm厚的多孔过滤管,直径与实施例1相同,并以5℃/min升至1100℃下烧结4h,随炉冷却出炉,取样进行对比测试。对比例2 使用平均粒度为20μm的310s粉末与黏结剂、铝酸脂偶联剂和增塑剂按实施例2中的工艺进行混料和制粒,并使用实例2中相同成型工艺,但将支撑体310s多孔板换成80目310s丝网,脱脂和烧结工艺也与之相同,制出样品后进行对比测试。
58.抗变形能力采用万能试验机将宽度为50mm的滤管放在压缩强度测试模具上进行压缩试验,将压头位移量2mm所对应的最大力为样品的抗变形力。孔径测试与通量按照国标gb/t32361-2015进行测试,孔隙率测试按gb/t5164-1985进行。
59.对实施例1-3和对比例1-2的无支撑型金属多孔滤管进行性能检测,检测结果如下表所示:本发明实施例中的一个或多个技术方案,至少具有如下技术效果或优点:(1)本发明实施例提供的无支撑型金属多孔滤管采用多孔金属板作为基体,本身就具有良好的抗变形能力,不需要添加打孔管作为支撑体,生产成本低;(2)在多孔金属板表面制备了一层粉末烧结层,大幅提高了过滤精度,同时还具有良好的过滤通量;(3)本发明实施例提供的无支撑型金属多孔滤管的膜表面光滑平直,无缺陷,孔隙分布均匀。
60.最后,还需要说明的是,术语“包括”、“包含”或者其任何其他变体意在涵盖非排他性的包含,从而使得包括一系列要素的过程、方法、物品或者设备不仅包括那些要素,而且还包括没有明确列出的其他要素,或者是还包括为这种过程、方法、物品或者设备所固有的要素。
61.尽管已描述了本发明的优选实施例,但本领域内的技术人员一旦得知了基本创造性概念,则可对这些实施例作出另外的变更和修改。所以,所附权利要求意欲解释为包括优选实施例以及落入本发明范围的所有变更和修改。
62.显然,本领域的技术人员可以对本发明进行各种改动和变型而不脱离本发明的精神和范围。这样,倘若本发明的这些修改和变型属于本发明权利要求及其等同技术的范围之内,则本发明也意图包含这些改动和变型在内。