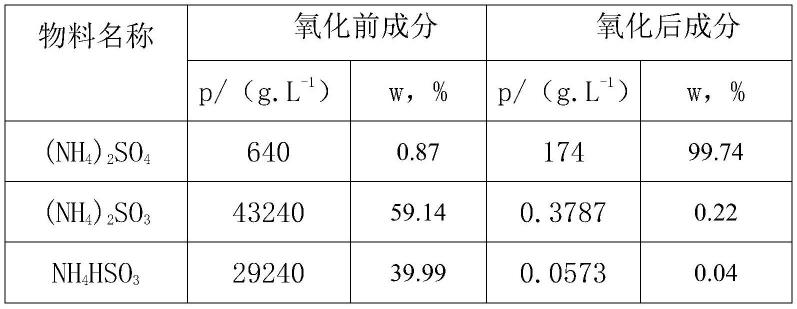
12.nh4hso3+nh3→
(nh4)2so313.(nh4)2so3+so2+h2o
→
2nh4hso314.so3+h2o
→
h2so415.除雾净化段设置有除氨、除水雾及除气溶胶装置,被脱除so2后含有微量氨和水雾的尾气在净化段自下而上流动,通过尾气与除雾装置的撞击及液滴自身重力的作用,被捕集脱除尾气得到净化,经过净化后的尾气引入烟囱排放。
16.控制工艺指标ph值在5.0-6.0操作液气比0.5-0.8l/m3循环液密度1080-1160kg/m3在相应的范围内脱硫效率可达94%以上,对脱硫效率影响最大的是氨水雾化效果和ph值,设计时采用螺旋式喷嘴增大氨水与烟气的接触面积,生产时通过调节ph值在工艺指标范围内来控制出塔气体中so2的含量使排出烟囱气体中ρ(so2)《100mg/m3酸雾(p)小于30mg/m3。
17.吸收液补充水采用脱盐水以防止吸收液在45℃以上结垢形成钙盐堵塞塔内的喷嘴。
18.氧化处理:吸收二氧化硫及硫酸雾后达到一定浓度的吸收液通过玻璃钢管道送到氧化塔,同时向氧化塔内加入氨水调节溶液的ph值在4.5-5.5使其中的亚硫酸氢铵被中和成亚硫酸铵,从塔底通入100m3/h、100kpa的压缩空气和165℃、0.55mpa、34kg/h的低压饱和蒸汽压缩空气经塔底微孔曝气装置与加热后的吸收液充分接触使亚硫酸氢铵和亚硫酸铵氧化成硫酸氢铵和硫酸铵,氧化塔采用穿孔曝气氧化技术。
19.氧化系统的主要反应有:
20.nh4hso3+nh3→
(nh4)2so321.2nh4hso3+o2→
2nh4hso422.2(nh4)2so3+o2→
2(nh4)2so423.氧化后合格的硫酸铵溶液从氧化塔,上部溢流至硫铵液槽,氧化塔内过量的压缩空气通过气液平衡管送至吸收塔最终随净化尾气一起排放。
24.硫酸比重控制:磺化后,连续稀释,用七个反应釜操作在第一釜加22%母液,并对温度进行控制,第二稀释釜中补充母液,酸的比重控制在
±
1.70。
25.作为本发明的进一步方案:所述吸收处理中,尾气中的微量氨及大粒径水雾,其质量浓度≤75mg/m3。
26.作为本发明的进一步方案:所述硫酸比重控制中,将温度控制在70℃内。
27.进一步的,该处理工艺主要有以下工艺特点:
28.1)、吸收液补充水采用脱盐水避免产生钙盐堵塞喷嘴。
29.2)、吸收效率高so2吸收率达94%以上,硫酸雾吸收率达71%以上,脱硫前p(so2)为720mg/m3硫酸雾(p)为23mg/m3,脱硫后p(so2)为38.5mg/m3硫酸雾(p)为6.6mg/m3。
30.3)、氧化系统氧化效果好,最终的成品硫酸铵溶液质量分数在99%以上,氧化前后物料组成见下表。
[0031][0032]
本发明的有益效果在于:
[0033]
本发明通过采用七个反应釜对尾气进行处理,同时由于该处理工艺将氨基磺酸磺化物连续稀释,彻底解决了现有技术中劳动强度转移物料,原间断稀释劳动强度大,费用高,转移困难,工艺难控制,操作不方便,因此本工艺提供的连续稀释工艺操作方便,工人劳动强度低,产品收率高,质量好,同时可以最大限度的回收60%浓度的硫酸,作为副产品回收使用,大部分稀硫酸可以使用,减少了废硫酸的排放量。
具体实施方式
[0034]
下面将对本发明实施例中的技术方案进行清楚、完整地描述,显然,所描述的实施例仅仅是本发明一部分实施例,而不是全部的实施例。基于本发明中的实施例,本领域普通技术人员在没有做出创造性劳动前提下所获得的所有其他实施例,都属于本发明保护的范围。
[0035]
实施例1:
[0036]
一种氨基磺酸生产用硫酸排放处理工艺,包括以下处理工艺:
[0037]
吸收处理:尾气吸收塔采用塔槽一体结构硫酸尾气通过烟气管道引入吸收塔中下部吸收段,尾气在吸收塔内由下而上流动与自上而下喷淋的吸收液逆向接触尾气中的so2与吸收液中的吸收剂氨水反应生成亚硫酸氢铵及亚硫酸铵,同时,亚硫酸氢铵和氨继续反应生成亚硫酸铵,当吸收液达到一定浓度后送入氧化塔中氧化脱除so2后的硫酸尾气进入吸收塔上部除雾净化段。
[0038]
吸收系统的主要反应:
[0039]
nh3+h2o+so2→
nh4hso3[0040]
2nh3+h2o+so2→
(nh4)2so3[0041]
nh4hso3+nh3→
(nh4)2so3[0042]
(nh4)2so3+so2+h2o
→
2nh4hso3[0043]
so3+h2o
→
h2so4[0044]
除雾净化段设置有除氨、除水雾及除气溶胶装置,被脱除so2后含有微量氨和水雾的尾气在净化段自下而上流动,通过尾气与除雾装置的撞击及液滴自身重力的作用,被捕集脱除尾气得到净化,经过净化后的尾气引入烟囱排放。
[0045]
控制工艺指标ph值在5.0-6.0操作液气比0.5-0.8l/m3循环液密度1080-1160kg/m3在相应的范围内脱硫效率可达94%以上,对脱硫效率影响最大的是氨水雾化效果和ph值,
设计时采用螺旋式喷嘴增大氨水与烟气的接触面积,生产时通过调节ph值在工艺指标范围内来控制出塔气体中so2的含量使排出烟囱气体中ρ(so2)《100mg/m3酸雾(p)小于30mg/m3。
[0046]
吸收液补充水采用脱盐水以防止吸收液在45℃以上结垢形成钙盐堵塞塔内的喷嘴。
[0047]
氧化处理:吸收二氧化硫及硫酸雾后达到一定浓度的吸收液通过玻璃钢管道送到氧化塔,同时向氧化塔内加入氨水调节溶液的ph值在4.5-5.5使其中的亚硫酸氢铵被中和成亚硫酸铵,从塔底通入100m3/h、100kpa的压缩空气和165℃、0.55mpa、34kg/h的低压饱和蒸汽压缩空气经塔底微孔曝气装置与加热后的吸收液充分接触使亚硫酸氢铵和亚硫酸铵氧化成硫酸氢铵和硫酸铵,氧化塔采用穿孔曝气氧化技术。
[0048]
氧化系统的主要反应有:
[0049]
nh4hso3+nh3→
(nh4)2so3[0050]
2nh4hso3+o2→
2nh4hso4[0051]
2(nh4)2so3+o2→
2(nh4)2so4[0052]
氧化后合格的硫酸铵溶液从氧化塔,上部溢流至硫铵液槽,氧化塔内过量的压缩空气通过气液平衡管送至吸收塔最终随净化尾气一起排放。
[0053]
实施例2:
[0054]
一种氨基磺酸生产用硫酸排放处理工艺,包括以下处理工艺:
[0055]
吸收处理:尾气吸收塔采用塔槽一体结构硫酸尾气通过烟气管道引入吸收塔中下部吸收段,尾气在吸收塔内由下而上流动与自上而下喷淋的吸收液逆向接触尾气中的so2与吸收液中的吸收剂氨水反应生成亚硫酸氢铵及亚硫酸铵,同时,亚硫酸氢铵和氨继续反应生成亚硫酸铵,当吸收液达到一定浓度后送入氧化塔中氧化脱除so2后的硫酸尾气进入吸收塔上部除雾净化段。
[0056]
吸收系统的主要反应:
[0057]
nh3+h2o+so2→
nh4hso3[0058]
2nh3+h2o+so2→
(nh4)2so3[0059]
nh4hso3+nh3→
(nh4)2so3[0060]
(nh4)2so3+so2+h2o
→
2nh4hso3[0061]
so3+h2o
→
h2so4[0062]
除雾净化段设置有除氨、除水雾及除气溶胶装置,被脱除so2后含有微量氨和水雾的尾气在净化段自下而上流动,通过尾气与除雾装置的撞击及液滴自身重力的作用,被捕集脱除尾气得到净化,经过净化后的尾气引入烟囱排放。
[0063]
控制工艺指标ph值在5.0-6.0操作液气比0.5-0.8l/m3循环液密度1080-1160kg/m3在相应的范围内脱硫效率可达94%以上,对脱硫效率影响最大的是氨水雾化效果和ph值,设计时采用螺旋式喷嘴增大氨水与烟气的接触面积,生产时通过调节ph值在工艺指标范围内来控制出塔气体中so2的含量使排出烟囱气体中ρ(so2)《100mg/m3酸雾(p)小于30mg/m3。
[0064]
吸收液补充水采用脱盐水以防止吸收液在45℃以上结垢形成钙盐堵塞塔内的喷嘴。
[0065]
氧化处理:吸收二氧化硫及硫酸雾后达到一定浓度的吸收液通过玻璃钢管道送到氧化塔,同时向氧化塔内加入氨水调节溶液的ph值在4.5-5.5使其中的亚硫酸氢铵被中和
成亚硫酸铵,从塔底通入100m3/h、100kpa的压缩空气和165℃、0.55mpa、34kg/h的低压饱和蒸汽压缩空气经塔底微孔曝气装置与加热后的吸收液充分接触使亚硫酸氢铵和亚硫酸铵氧化成硫酸氢铵和硫酸铵,氧化塔采用穿孔曝气氧化技术。
[0066]
氧化系统的主要反应有:
[0067]
nh4hso3+nh3→
(nh4)2so3[0068]
2nh4hso3+o2→
2nh4hso4[0069]
2(nh4)2so3+o2→
2(nh4)2so4[0070]
氧化后合格的硫酸铵溶液从氧化塔,上部溢流至硫铵液槽,氧化塔内过量的压缩空气通过气液平衡管送至吸收塔最终随净化尾气一起排放。
[0071]
硫酸比重控制:磺化后,连续稀释,用七个反应釜操作在第一釜加22%母液,并对温度进行控制,第二稀释釜中补充母液,酸的比重控制在
±
1.70。
[0072]
吸收处理中,尾气中的微量氨及大粒径水雾,其质量浓度≤75mg/m3。
[0073]
硫酸比重控制中,将温度控制在70℃内。
[0074]
通过采用七个反应釜对尾气进行处理,同时由于该处理工艺将氨基磺酸磺化物连续稀释,彻底解决了现有技术中劳动强度转移物料,原间断稀释劳动强度大,费用高,转移困难,工艺难控制,操作不方便,因此本工艺提供的连续稀释工艺操作方便,工人劳动强度低,产品收率高,质量好,同时可以最大限度的回收60%浓度的硫酸,作为副产品回收使用,大部分稀硫酸可以使用,减少了废硫酸的排放量。
[0075]
实施例3:
[0076]
一种氨基磺酸生产用硫酸排放处理工艺,包括以下处理工艺:
[0077]
(1)化灰槽采用泵送浆液至稀酸收集池,稀酸收集池排酸期间保持碱性,循环无水中和。
[0078]
(2)板框反吹回流液和戈尔膜排渣液经架设管线回收进稀酸收集池。
[0079]
(3)树脂预处理,经2bv质量分数10%氯化钠溶液浸泡18-20h,用清水漂洗净,使排出的水不显黄色,再用质量分数2%-4%氢氧化钠或质量分数5%盐酸溶液(其量与上同)浸泡2-4h(或小流量清洗),放尽碱或酸液后冲洗树脂至水接近中性待用。
[0080]
(4)大孔径树脂使用大于或等于3周期以后,如吸附效果不佳可采用甲醇进行洗脱。
[0081]
采用以上优化工艺处理硫酸厂污水,具有以下优势:
[0082]
1)稀酸中和化灰过程不添加一次水,氢氧化钙处理可使污水中部分阳离子得到沉淀。
[0083]
2)板框及戈尔膜的二级过滤保证了污水ph值及悬浮物符合环保要求。
[0084]
3)通过比较选用大孔径树脂降低污水cod,其效果好,无二次污染,且利用硫酸厂自产稀硫酸对树脂进行洗脱,降低了系统运行成本,可使得污水中部分有机物富集,具备回收条件。
[0085]
4)处理后污水达到甚至优于环保标准,可二次回收利用,节约一次水量约66000-95000m3/a。
[0086]
对比例1:
[0087]
药剂法处理cod为目前常规处理方案,具有操作方便、见效快等特点,在生产过程
中cod降解药剂的反应速度非常快,可在2-3min内完成反应,可直接对污水进行处理,结合现场环境决定在二级沉淀池富集污水中内使用,原污水cod为714.1mg/m3,对该污水加人不同量的cod降解药剂,处理后污水cod值见下表。
[0088]
处理项目数值原污水cod/(mg.m-3
)714.1加入药剂1g/l后污水cod/(mg.m-3
)601.8加入药剂2g/l后污水cod/(mg.m-3
)492.3加入药剂3g/l后污水cod/(mg.m-3
)396.7加入药剂4g/l后污水cod/(mg.m-3
)309.5加入药剂5g/l后污水cod/(mg.m-3
)197.6加入药剂7g/l后污水cod/(mg.m-3
)110.6加入药剂9g/l后污水cod/(mg.m-3
)42.6
[0089]
经测试,污水cod高时药剂法平均投入1g/l,cod可降低约100mg/m3,随着污水中cod的下降,降解效果逐步衰弱。
[0090]
结合目前硫酸厂污水实际情况,理论计算1m3污水中需添加9kgcod降解剂方能达到污水排放要求,每天处理污水120m3需添加药剂980kg,其方法药剂消耗量大、成本高,且添加药剂后处理污水不利用回用,所以药剂法不适合低浓度污水cod处理。
[0091]
最后应说明的几点是:虽然,上文中已经用一般性说明及具体实施例对本发明作了详尽的描述,但在本发明的基础上,以上各实施例仅用以说明本发明的技术方案,而非对其限制;尽管参照前述各实施例对本发明进行了详细的说明,本领域的普通技术人员应当理解:其依然可以对前述各实施例所记载的技术方案进行修改,或者对其中部分或者全部技术特征进行的同替换;而这些修改或者替换,并不使相应技术方案的本质脱离本发明各实施例技术方案的范围。