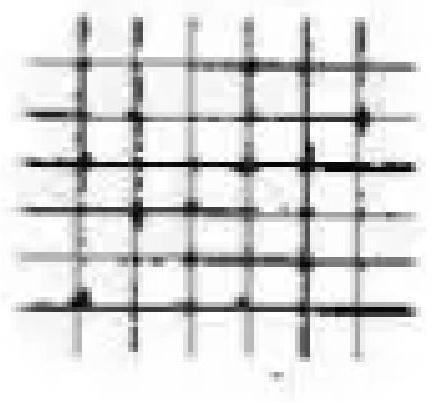
1.本公开涉及汽车喷漆技术领域,具体地,涉及一种修补汽车车漆的方法。
背景技术:2.汽车是人们日常生活中的一种交通工具,随着人们生活水平的不断提高,私家车的拥有量也是逐年激增,城市大街小巷上的车辆越来越多,随之而来的行车安全问题也越来越多,小碰小擦更是数不胜数,小碰擦会造成车辆漆面的损伤,影响美观。
3.无论是主机厂还是4s店,汽车油漆修补一直存在色差问题,尤其是金属漆,在同一个环境、不同工艺手法下喷涂的效果不一样;同样工艺手法、不同环境作业下喷涂后的效果也会不一样,且金属漆修补易出现附着力不合格现象,这会导致返修不良,需要二次返修,严重影响车辆的使用。
技术实现要素:4.本公开的目的是提供一种修补汽车车漆的方法,该方法环保经济、操作步骤简单,能够增加漆面的机械强度和附着力,解决金属漆修补色差较大和附着力较差的问题。
5.本公开提供一种修补汽车车漆的方法,所述方法包括以下步骤:
6.(1)在车漆损伤部位喷涂第一面漆,形成第一面漆层;在所述第一面漆层上喷涂第二面漆,形成第二面漆层;在所述第二面漆层上喷涂第三面漆,形成第三面漆层;
7.(2)在原车漆与所述第三面漆层交界处喷洒驳口稀料,待所述驳口稀料表干后进行烘烤和抛光;
8.其中,所述第一面漆和第三面漆各自包含清漆和清漆固化剂,所述驳口稀料包含丙烯酸聚氨酯;
9.所述第一面漆中清漆与清漆固化剂的质量比为(8~14):1。
10.可选地,所述清漆为丙烯酸酯清漆,优选为羟基丙烯酸树脂清漆,所述清漆固化剂包含异氰酸酯、二甲苯、乙酸正丁酯和乙酸-1-甲氧基-2-丙基酯;
11.以所述清漆固化剂的总重量为基准,所述异氰酸酯的含量为80~85重量%,所述二甲苯的含量为1~2重量%,所述乙酸正丁酯的含量为5~10重量%,所述乙酸-1-甲氧基-2-丙基酯的含量为2~3重量%。
12.可选地,所述清漆固化剂中异氰酸酯与所述乙酸正丁酯的质量比为(8~16):1,所述异氰酸酯与所述乙酸-1-甲氧基-2-丙基酯的质量比为(33~50):1。
13.可选地,所述第一面漆中清漆与清漆固化剂的质量比为(9~11):1;所述第三面漆中清漆与清漆固化剂的质量比为(1~3):1。
14.可选地,所述第二面漆选自溶剂型底色漆,所述溶剂型底色漆包括金属底色漆或珍珠底色漆,所述金属底色漆包括羟基丙烯酸树脂、颜料、银浆粉和有机稀释剂。
15.可选地,该方法还包括:在步骤(1)之前,对车漆损伤部位进行打磨处理;可选地,所述打磨处理包括:使用800~1000目的砂纸在车漆损伤部位进行第一打磨,使用1500~
2000目的砂纸在车漆损伤部位进行第二打磨;其中所述第二打磨的面积范围超出所述第一打磨的面积范围。
16.可选地,所述第一面漆在25℃的施工粘度为14~16s,所述第一面漆层的膜厚为3~5μm;所述第二面漆在25℃的施工粘度为14~17s,所述第二面漆层的膜厚为15~25μm;所述第三面漆在25℃的施工粘度为16~18s,所述第三面漆层的膜厚为30~45μm。
17.可选地,步骤(1)中所述第一面漆的喷涂方法包括:在温度为20~25℃、湿度为50~65%条件下喷涂2~3层第一面漆,每层喷涂完静置闪干5~10min再喷涂下一层;
18.所述第二面漆的喷涂方法包括:待所述第一面漆层表干后,在温度为20~25℃、湿度为50~65%条件下喷涂2~3层第二面漆,每层喷涂完静置闪干10~15min再喷涂下一层;
19.所述第三面漆的喷涂方法为:待所述第二面漆层表干后,在温度为20~25℃、湿度为50~65%条件下喷涂2~3层第三面漆,每层喷涂完静置闪干5~10min再喷涂下一层。
20.可选地,步骤(2)中所述驳口稀料的喷洒条件包括:在所述第三面漆喷完3~5分钟后进行喷洒;
21.所述烘烤的条件包括:使用红外烤灯在距离修补漆面的60~90cm处进行烘烤,烘烤的温度为80~100℃,烘烤时间为15~25min。
22.可选地,所述第一面漆、第二面漆和第三面漆均采用喷枪进行喷涂,所述喷枪为下压式喷枪,所述喷枪喷口的直径为1.3~1.4mm,所述喷枪的空气压力为0.18~0.3mpa。
23.通过上述技术方案,本公开提供一种修补汽车车漆的方法,该方法在喷涂第二面漆前先喷涂特定组成的第一面漆,随后喷涂第二面漆和第三面漆,其中第一面漆中清漆过量于清漆固化剂,使得第一面漆中部分清漆先固化,剩余的未固化的清漆会与第三面漆中的清漆固化剂作用而交联,增加分子间氢键,从而增加第二面漆的附着力,增加漆面的机械强度;采用驳口稀料进行打磨,减少补漆的色差;该方法环保经济、操作步骤简单,具有较强的适用性和推广性。
24.本公开的其他特征和优点将在随后的具体实施方式部分予以详细说明。
附图说明
25.附图是用来提供对本公开的进一步理解,并且构成说明书的一部分,与下面的具体实施方式一起用于解释本公开,但并不构成对本公开的限制。在附图中:
26.图1是实施例2的漆膜划格试验的效果图片;
27.图2是实施例3的漆膜划格试验的效果图片;
28.图3是对比例1的漆膜划格试验的效果图片;
29.图4是对比例2的漆膜划格试验的效果图片;
30.图5是对比例3的漆膜划格试验的效果图片。
具体实施方式
31.以下结合附图对本公开的具体实施方式进行详细说明。应当理解的是,此处所描述的具体实施方式仅用于说明和解释本公开,并不用于限制本公开。
32.本公开提供一种修补汽车车漆的方法,所述方法包括以下步骤:
33.(1)在车漆损伤部位喷涂第一面漆,形成第一面漆层;在所述第一面漆层上喷涂第
二面漆,形成第二面漆层;在所述第二面漆层上喷涂第三面漆,形成第三面漆层;
34.(2)在原车漆与所述第三面漆层交界处喷洒驳口稀料,待所述驳口稀料表干后进行烘烤和抛光;
35.其中,所述第一面漆和第三面漆各自包含清漆和清漆固化剂,所述驳口稀料包含丙烯酸聚氨酯;
36.所述第一面漆中清漆与清漆固化剂的质量比为(8~14):1。
37.在上述技术方案中,本公开提供一种修补汽车车漆的方法,该方法在喷涂第二面漆前先喷涂特定组成的第一面漆,随后喷涂第二面漆和第三面漆,其中第一面漆中清漆过量于清漆固化剂,使得第一面漆中部分清漆先固化,剩余的未固化清漆会与第三面漆中的清漆固化剂作用而交联,增加分子间氢键,从而增加第二面漆的附着力;采用驳口稀料喷涂补漆边缘部分,可以减少补漆的色差;该制备方法环保经济,操作步骤简单,具有较强的适用性和推广性。
38.在本公开的一种实施方式中,所述清漆为丙烯酸酯清漆,优选为羟基丙烯酸树脂清漆,所述清漆固化剂包含异氰酸酯、二甲苯、乙酸正丁酯和乙酸-1-甲氧基-2-丙基酯;以所述清漆固化剂的总重量为基准,所述异氰酸酯的含量为80~85重量%,所述二甲苯的含量为1~2重量%,所述乙酸正丁酯的含量为5~10重量%,所述乙酸-1-甲氧基-2-丙基酯的含量为2~3重量%。在上述实施方式中,通过选用优选组分的清漆和清漆固化剂,使得第一面漆分散性良好,有利于大面积施工时漆膜融合,使接驳口平整。
39.在本公开的一种实施方式中,所述清漆固化剂中异氰酸酯与所述乙酸正丁酯的质量比为(8~16):1,所述异氰酸酯与所述乙酸-1-甲氧基-2-丙基酯的质量比为(33~50):1。在上述实施方式中,通过选用优选配比的清洗固化剂,可以加快清漆固化,有利于进行下一步反应。
40.在本公开的一种实施方式中,所述第一面漆中清漆与清漆固化剂的质量比为(9~11):1;所述第三面漆中清漆与清漆固化剂的质量比为(1~3):1。在上述实施方式中,通过选用优选比例的第一面漆和第三面漆,有利于第一面漆中过量的未固化的清漆与第三面漆中的清漆固化剂作用而交联,进而增加第二面漆的附着力。
41.在本公开的一种实施方式中,所述第二面漆选自溶剂型底色漆,所述溶剂型底色漆包括金属底色漆或珍珠底色漆,所述金属底色漆包括羟基丙烯酸树脂、颜料、银浆粉和有机稀释剂。
42.在本公开的一种实施方式中,该方法还包括:在步骤(1)之前,对车漆损伤部位进行打磨处理;可选地,所述打磨处理包括:使用800~1000目的砂纸在车漆损伤部位进行第一打磨,使用1500~2000目的砂纸在车漆损伤部位进行第二打磨;其中所述第二打磨的面积范围超出所述第一打磨的面积范围,也即第二打磨包括对车漆损伤部位的边缘进行打磨。在上述实施方式中,通过对车漆损伤位置和损伤边缘进行打磨处理,可以使得接驳口过渡平顺,便于后续抛光处理,有利于新旧油漆颜色保持一致,减少补漆色差。
43.在本公开的一种实施方式中,所述第一面漆在25℃的施工粘度为14~16s,所述第一面漆层的膜厚为3~5μm;所述第二面漆在25℃的施工粘度为14~17s,所述第二面漆层的膜厚为15~25μm;所述第三面漆在25℃的施工粘度为16~18s,所述第三面漆层的膜厚为30~45μm。在上述实施方式中,通过选用优选粘度的第一面漆、第二面漆和第三面漆,有利于
第一面漆、第二面漆和第三面漆喷涂后扩散,使得固化后的面漆层膜厚较薄,便于控制补漆与原漆的色差;选用优选膜厚的第一面漆层、第二面漆层和第三面漆层,有利于面漆分子间进行交联,使得漆面快速干燥,增加漆面的机械强度、附着力和光泽饱满度。
44.在本公开的一种实施方式中,步骤(1)中所述第一面漆的喷涂方法包括:在温度为20~25℃、湿度为50~65%条件下喷涂2~3层第一面漆,每层喷涂完静置闪干5~10min再喷涂下一层;所述第二面漆的喷涂方法包括:待所述第一面漆层表干后,在温度为20~25℃、湿度为50~65%条件下喷涂2~3层第二面漆,每层喷涂完静置闪干10~15min再喷涂下一层;所述第三面漆的喷涂方法为:待所述第二面漆层表干后,在温度为20~25℃、湿度为50~65%条件下喷涂2~3层第三面漆,每层喷涂完静置闪干5~10min再喷涂下一层。在上述实施方式中,通过采用优选地喷涂方法,有利于喷涂完的面漆快速闪干,增加漆面附着力。
45.在本公开的一种实施方式中,步骤(2)中所述驳口稀料的喷洒条件包括:在所述第三面漆喷完3~5分钟后进行喷洒;所述烘烤的条件包括:使用红外烤灯在距离修补漆面的60~90cm处进行烘烤,烘烤的温度为80~100℃,烘烤时间为15~25min。在上述实施方式中,通过选用优选地烘烤条件,有利于驳口稀料的内部分子扩散运动,使得局部分子不易变形,提高面漆的硬度和韧性。
46.在本公开的一种实施方式中,所述第一面漆、第二面漆和第三面漆均采用喷枪进行喷涂,所述喷枪为下压式喷枪,所述喷枪喷口的直径为1.3~1.4mm,所述喷枪的空气压力为0.18~0.3mpa。在上述实施方式中,通过选用优选地喷枪进行喷涂,有利于喷涂均匀、平整、无颗粒感,漆色光泽好。
47.本公开提供的修补汽车车漆的方法在喷涂第二面漆前先喷涂特定组成的第一面漆,随后喷涂第二面漆和第三面漆,其中第一面漆中清漆过量于清漆固化剂,使得第一面漆中部分清漆先固化,剩余的未固化清漆会与第三面漆中的清漆固化剂作用而交联,增加分子间氢键,从而增加第二面漆的附着力,增加漆面的机械强度;采用驳口稀料进行打磨,减少补漆的色差;该方法环保经济、操作步骤简单,具有较强的适用性和推广性。
48.下面通过实施例和对比例来进一步说明本公开,但是本公开并不因此而受到任何限制。
49.以下实施例和对比例中,如无特殊说明,所使用的原料均为商购产品。
50.清漆为河北科丰水性漆有限公司公司生产的cx926丙烯酸聚氨酯清漆;
51.清漆固化剂为河北科丰水性漆有限公司公司生产的cx825h丙烯酸聚氨酯面漆固化剂;
52.溶剂型金属底色漆为河北科丰水性漆有限公司公司生产的cx825t丙烯酸聚氨酯面漆稀释剂;
53.驳口稀料为河北科丰水性漆有限公司公司生产的cx825t丙烯酸聚氨酯面漆稀释剂。
54.硬度测试标准:《gb6739—86涂膜硬度铅笔测定法》;
55.附着力测试标准:gb/t 9286-1998《色漆和清漆漆膜的划格试验》;
56.面漆施工粘度测试标准:gb/t 1723-93;
57.漆膜厚度测试标准:gb/t 1764-79。
58.实施例1
59.本实施例采用商用客车进行修补车漆,具体步骤如下:
60.1、对于不需要喷涂的部位用保护膜、遮蔽纸或胶带进行遮蔽;
61.2、使用砂纸型号800目的砂纸打磨商用客车受损部位的旧漆(这里指旧漆轻度划伤,或产生色差,如有凹坑等严重损伤,需要进行原子灰修补和喷涂处理),使用1500目的砂纸打磨受损部位的旧漆和旧漆边缘,其中800目砂纸的打磨面积范围超出金属底色漆喷涂范围,但不能超过1500目砂纸的打磨范围;
62.3、在温度为25℃、湿度为65%的条件下喷涂2~3层第一面漆,第一面漆中清漆与清漆固化剂的质量比为10:1,每层喷涂完静置闪干5~10min再喷涂下一层,其中,第一面漆的施工粘度为16s,形成的第一面漆层的膜厚为5μm;
63.4、待第一面漆层表干后,在温度为25℃、湿度为65%的条件下,喷涂2~3层溶剂型金属底色漆,每层喷涂完静置闪干10~15min后再喷涂下一层;其中,第二面漆的施工粘度为14s,形成的第二面漆层的膜厚为20μm,溶剂型金属底色漆由羟基丙烯酸树脂、进口颜料、进口银粉浆和有机稀释剂等材料配制而成。
64.5、待第二面漆层表干后,在温度为25℃、湿度为65%的条件下喷涂2~3层第三面漆,第三面漆中清漆与清漆固化剂的质量比为2:1,每层喷涂完静置闪干15min后再喷涂下一层,其中,第三面漆的施工粘度为16s,形成的第三面漆层的膜厚为30μm;
65.6、第三面漆喷完5分钟后喷洒丙烯酸聚氨酯驳口稀料,待表干5分钟,使用红外烤灯在修补漆面的80cm处进行烘烤,烘烤的温度为80℃,烘烤时间为25min,烘烤后进行抛光24h;
66.其中,清漆包含羟基丙烯酸树脂清漆,清漆固化剂包含异氰酸酯、二甲苯、乙酸正丁酯和乙酸-1-甲氧基-2-丙基酯;以清漆固化剂的总质量为基准,异氰酸酯的含量为80~85重量%,二甲苯的含量为1~2重量%,乙酸正丁酯的含量为5~10重量%,乙酸-1-甲氧基-2-丙基酯的含量为2~3重量%;清漆固化剂中异氰酸酯与乙酸正丁酯的质量比为(8~16):1,异氰酸酯与乙酸-1-甲氧基-2-丙基酯的质量比为(33~50):1;第一面漆、第二面漆和第三面漆均采用喷枪进行喷涂,喷枪为下压式喷枪,喷枪喷口的直径为1.3~1.4mm,喷枪的空气压力为0.2mpa;
67.漆膜性能测试:硬度≥h,附着力0级,切割边缘完全光滑,无任何方格分层。
68.实施例2
69.与实施例1的方法相同,区别仅在于:第一面漆中,清漆与清漆固化剂的质量比为8:1;漆膜性能测试:硬度≥h,附着力1级,切口交叉处有少许涂层脱落,但交叉切割面积受影响不超过5%,效果如图1所示。
70.实施例3
71.与实施例1的方法相同,区别仅在于:第三面漆中清漆与清漆固化剂的质量比为3:1;漆膜性能测试:硬度≥h,附着力1级,切口交叉处有少许涂层脱落,但交叉切割面积受影响不超过5%,效果如图2所示。
72.对比例1
73.与实施例1的方法相同,区别仅在于:第一面漆中,清漆与清漆固化剂的质量比为7:1;漆膜性能测试:硬度≥hb,附着力2级,涂层受影响的交叉切割面积为5~15%,效果如
图3所示。
74.对比例2
75.与实施例1的方法相同,区别仅在于:第一面漆中清漆与清漆固化剂的质量比为15:1;漆膜性能测试:硬度≥h,附着力2级,涂层受影响的交叉切割面积为5~15%,效果如图4所示。
76.对比例3
77.与实施例1的方法相同,区别仅在于:打磨后不喷涂第一面漆,直接喷涂金属底色漆;漆膜性能测试:硬度≥h,附着力2级,涂层受影响的交叉切割面积为5~15%,效果如图5所示。
78.测试例:
79.采用实施例和对比例制得的修补漆进行漆膜划格试验,测试标准为gb/t 9286-1998《色漆和清漆漆膜的划格试验》,结果分析:实施例1的切割边缘完全光滑,无任何方格分层,实施例2~3的切口交叉处有少许涂层脱落,但交叉切割面积受影响不超过5%,而对比例1~3的涂层受影响的交叉切割面积为5~15%。
80.通过以上可知,实施例1~3采用本公开的方法,修补后的车漆表面光滑,可有效的减少车身修补的色差,可以提高修补效率,修补后的金属漆整体看起来颗粒更具有立体感、金属感、闪烁度,具有较强的适用性和推广性。
81.以上结合附图详细描述了本公开的优选实施方式,但是,本公开并不限于上述实施方式中的具体细节,在本公开的技术构思范围内,可以对本公开的技术方案进行多种简单变型,这些简单变型均属于本公开的保护范围。另外需要说明的是,在上述具体实施方式中所描述的各个具体技术特征,在不矛盾的情况下,可以通过任何合适的方式进行组合,为了避免不必要的重复,本公开对各种可能的组合方式不再另行说明。
82.此外,本公开的各种不同的实施方式之间也可以进行任意组合,只要其不违背本公开的思想,其同样应当视为本公开所公开的内容。