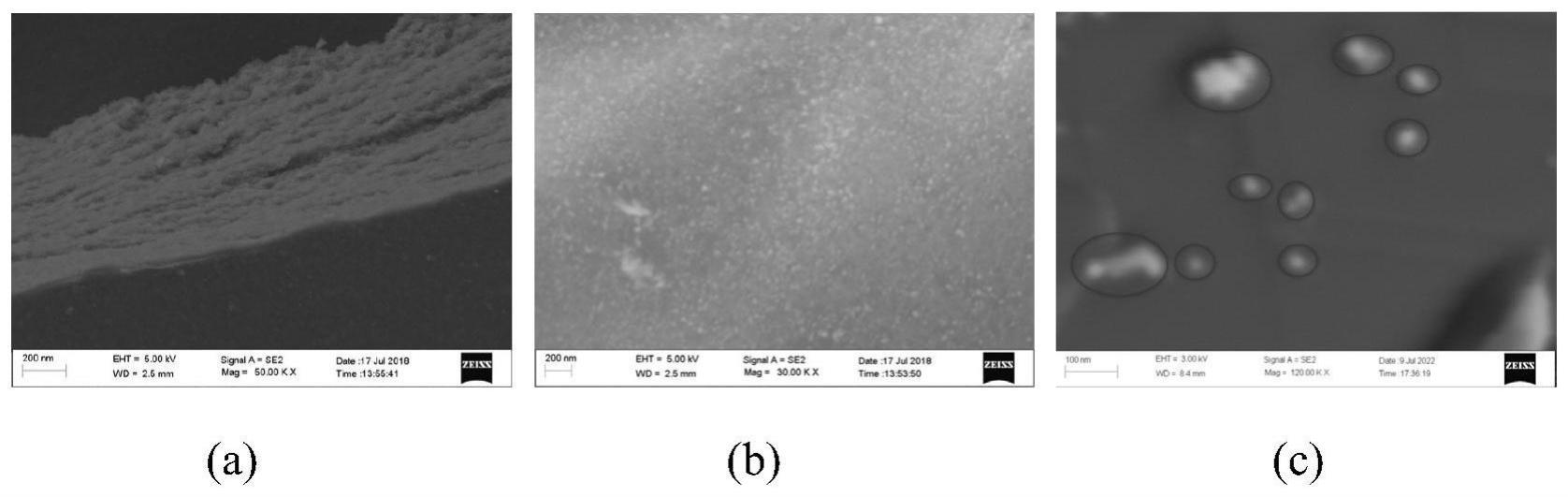
1.本发明涉及工业催化技术领域,特别是涉及一种氧化物膜限域低碳烷烃干重整用的镍基催化剂及其制备方法和用途。
背景技术:2.国内外围绕二氧化碳-低碳烷烃重整制备合成气技术已经开展了30多年的研究,主要是研发高活性、高稳定性贵金属催化剂和ni基催化剂。但贵金属催化剂价格昂贵,工艺成本太高,基本上不具有经济效益。因此,近年来对非贵金属催化剂(主要是以ni为主活性金属的催化剂体系)的研究成为主流,研究重点主要集中在高温、常压条件下镍基催化剂抗积碳和抗烧结性能的研究。其中,甲烷-水蒸气重整催化剂的研究最多,二氧化碳-低碳烷烃重整相关技术研究较少。
3.中国石油大学(北京)报道了其将焦炉煤气中ch4与co2进行重整反应的技术,其研发的镍基催化剂中活性组分实现原子尺度分散,添加的助剂具有强化co2吸附、活化和转化功能,确保了镍基催化剂在高温条件下高活性运行,但该技术并没有获得相关专利授权。日本千代田化工建设株式会社披露了其co2重整技术,相关专利主要有cn201780002255等,公开了氧化钙层包裹的氧化镁球载体的制备及以钌或/和铑为活性组分的催化剂制备方法,该技术采用钌或/和铑为活性组分,成本高昂。专利cn99107321.5公开了一种将超细氧化锆粉体浸渍一定浓度的硝酸镍溶液,经蒸发、干燥和焙烧制备的用于二氧化碳-甲烷重整制合成气的镍基催化剂,其特征是所用超细氧化锆粉体以氧氯化锆为前躯体,以稀释后的氨水为沉淀剂,得到水凝胶混再用无水乙醇置换成醇凝胶,再在高压釜内通氮气处理得到。专利cn200910154283.4公开了以nd为助剂、ni为活性组分、有序介孔二氧化硅(sba-15)为载体,采用β-环糊精改性的浸渍法先后将稀土金属nd及活性金属组分ni负载于载体上,制备了稀土金属nd改性的ni/nd/sba-15催化剂,采用催化剂仅能在常压下运行,过高的温度和体系压力会导致分子筛载体的坍塌。专利cn200810117478.7披露了以γ-al2o3或nial2o4为载体,以ni为活性组分,少量pt为助剂的催化剂应用于甲烷二氧化碳重整反应,pt为贵金属,资源有限且价格昂贵,限制了其在工业上的广泛应用前景。专利cn201310581082.9公开了以孔道内表面经过醇羟基的修饰的具有高温稳定性的介孔氧化物作为载体,在搅拌条件下将镍的前驱体盐输运到其介孔孔道内得到镍分散度好的干重整催化剂;其特征是以醇为运输载体,将镍前驱体输运到载体的介孔孔道内,醇羟基对载体孔道内壁的修饰作用可以使镍物种的尺寸控制在一个更小的范围内,从而制得均匀分散的小尺寸的氧化镍纳米颗粒固定在介孔孔道内,醇在煅烧过程中形成的碳模板还可以阻止镍物种从孔道内部迁移到外表面,进一步抑制了氧化镍的高温团聚;以上述方法制备的催化剂在过高的温度和体系压力下会导致具有介孔结构的载体坍塌。专利cn201710480165.7披露了以三甲基铝和水为反应源,基板采用k9玻璃和jgsl石英玻璃,通过原子沉积沉淀法,在浸渍法制备的ni/γ-al2o3负载型催化剂表面沉积1-100层惰性γ-al2o3薄膜,制备γ-al2o3/ni/γ-al2o3三明治夹层结
构催化剂;以上述方法制备γ-al2o3/ni/γ-al2o3三明治夹层结构催化剂只能处理粉末样品,原子沉积沉淀法对加工设备要求极高,工艺成本高昂,且在工业上800-1100℃高温、高气速的苛刻工况下γ-al2o3/ni/γ-al2o3三明治夹层结构中的γ-al2o3会迅速相转变成α-al2o3,进而导致三明治夹层结构坍塌破坏。专利cn201710480366.7披露了一种以有机硅、有机镍、有机钴及有机活性剂为原料制备的nico/sio2核壳催化剂,该方案利用多孔氧化硅包裹nico合金纳米粒子抑制nico合金纳米粒子的团聚和烧结行为,但同样无法满足工业上800-1200℃高温、高气速的苛刻工况下进行要求,同时含氧化硅组分的粉体催化剂无法满足工业对重整催化剂机械强度的要求。
4.基于以上分析可见,目前国内外对低碳烷烃干重整制合成气技术的研究报道基本集中在实验室和小规模的中试相关工作上,而工业上为了满足需求通常通过提高镍负载量来实现催化剂的较高活性和长程稳定性,这就牺牲了催化剂的抗积碳性能同时催化剂的使用温度尤其是干重整催化剂难以降至600℃以下,较高的反应温度极易导致催化剂结构不稳定,活性位烧结团聚和组分流失,这就不仅要求制备的催化剂原粉具有良好的催化性能还要保证其载体结构稳定、成型工艺以及机械强度均需要满足工业需求,因此研制具备空间限域微结构的高活性、高热稳定的镍基催化剂尤为关键。
技术实现要素:5.为解决低碳烷烃干重整催化剂在高温(600℃~1200℃)、高空速工况下催化剂结构不稳定、表面活性位极易烧结团聚和组分流失导致催化剂表面镍颗粒长大而出现活性迅速降低与积碳问题,本发明提供一种氧化物膜限域低碳烷烃干重整用的镍基催化剂及其制备方法和用途。
6.为实现上述目的及其他相关目的,本发明第一方面提供一种氧化物膜限域低碳烷烃干重整用的镍基催化剂,包括以下质量百分比的各组分:
7.氧化镍5~30%,如5~5.61%、5.61~12.85%、12.85~28.97%或28.97~30%;
8.载体金属氧化物68~94.99%,如68~69.24%、69.24~86.02%、86.02~93.82%或93.82~94.99%;
9.具有氧化物膜结构的m元素氧化物0.01~2%,如0.01~0.57%、0.57~1.13%、1.13~1.79%或1.79~2%;
10.m元素选自铈、锆和铝中的至少一种。
11.优选地,所述载体金属氧化物选自氧化镁、氧化锆和氧化铝中的至少一种。
12.本发明第二方面提供上述镍基催化剂的制备方法,包括如下步骤:
13.1)将镍负载载体金属氧化物粉料与m元素的氟化物粉料混合并模压成型,得到成型前驱体;
14.模压成型获得满足工业需求的成型前驱体,比如拉西环、多孔异型等;
15.2)在干燥空气气氛下,将所述成型前驱体进行老化、干燥和造孔,得到造孔物料;
16.3)将所述造孔物料在惰性气氛下进行m元素的氟化物升华-沉积,得到沉积物料;
17.4)将所述沉积物料在惰性气氛下进行第一降温,然后切换为包含水蒸气的空气气氛下进行第二降温,得到所述镍基催化剂。
18.沉积在孔道内壁的m元素的氟化物与空气气氛中水蒸气反应形成对应的氧化物
膜。
19.优选地,还包括如下技术特征中的至少一项:
20.11)步骤1)中,所述镍负载载体金属氧化物粉料的粒度范围为1~200微米;
21.12)步骤1)中,所述镍负载载体金属氧化物粉料中镍与载体金属氧化物的质量比为0.05~0.5:1,如0.05~0.11:1、0.11~0.32:1或0.32~0.5:1;
22.13)步骤1)中,所述镍负载载体金属氧化物粉料通过包括如下步骤的制备方法获得:将包含镍源的水溶液浸渍于载体金属氧化物上,然后进行干燥、焙烧、研磨和筛分;
23.14)步骤1)中,m元素的氟化物粉料的粒度范围为1~50微米;
24.15)步骤1)中,镍负载载体金属氧化物粉料与m元素的氟化物粉料的质量比为100:0.01~100:2,如100:0.01~100:0.44、100:0.44~100:1.1、100:1.1~100:1.73或100:1.73~100:2;
25.21)步骤2)中,所述干燥空气气氛中水蒸气含量按干气体计不超过20g/m3;所述干燥空气气氛可以通过干燥剂如氯化钙进行脱水处理后获得;
26.22)步骤2)中,所述干燥空气气氛为流动的空气气氛;
27.23)步骤2)中,老化温度为室温,室温是指环境温度,如20~35℃;
28.24)步骤2)中,老化时间为24~72小时,如24~50小时或50~72小时;
29.25)步骤2)中,老化至成型前驱体侧压强度在150n以上;
30.26)步骤2)中,干燥温度为100~150℃,如100~120℃或120~150℃;
31.27)步骤2)中,干燥时间为12~48小时;
32.28)步骤2)中,以2~20℃/min升温速率升温至造孔温度;
33.29)步骤2)中,造孔温度为400~800℃;
34.210)步骤2)中,造孔时间为2~5h;
35.31)步骤3)中,将干燥空气气氛切换为惰性气氛,如高纯氮气、高纯氩气等,高纯是指体积浓度大于99.9999%;
36.32)步骤3)中,所述惰性气氛为静态的惰性气氛,减少和避免升华的组分流失;
37.33)步骤3)中,升温至1400~1800℃进行升华-沉积;
38.34)步骤3)中,升华-沉积的时间为2~5h;
39.35)步骤3)中,沉积部位为造孔孔道的内壁;
40.36)步骤3)中,沉积物为m元素氧化物膜的沉积前驱物;
41.41)步骤3)中,所述惰性气氛为静态的惰性气氛;
42.42)步骤4)中,第一降温至300~800℃,如300~400℃或400~800℃;
43.43)步骤4)中,第一降温的降温速率为10~20℃/min,如10~15℃/min或15~20℃/min;
44.44)步骤4)中,第二降温至室温~600℃;
45.45)步骤4)中,第二降温的降温速率为10~20℃/min,如10~15℃/min或15~20℃/min;
46.46)步骤4)中,所述空气气氛为流动的空气气氛;
47.47)步骤4)中,m元素氧化物膜的沉积前驱物与空气气氛中水蒸气反应生成m元素的氧化物膜;
48.48)步骤4)中,所述空气气氛中水蒸气含量为80~200g/m3,如80~130g/m3或130~200g/m3。
49.更优选地,还包括如下技术特征中的至少一项:
50.111)特征11)中,所述镍负载载体金属氧化物粉料的粒度范围为5~100微米;
51.131)特征13)中,包含镍源的水溶液中镍的浓度为0.2~4mol/l;
52.132)特征13)中,载体金属氧化物的粒度范围为1~200微米;
53.133)特征13)中,干燥温度为100~150℃,如100~120℃或120~150℃;
54.134)特征13)中,焙烧温度为500~1400℃,如500~600℃或600~1400℃;
55.135)特征13)中,焙烧时间为1~6h;
56.141)特征14)中,m元素的氟化物粉料的粒度范围为1~10微米。
57.进一步更优选地,还包括如下技术特征中的至少一项:
58.1111)特征111)中,所述镍负载载体金属氧化物粉料的粒度范围为10~40微米;
59.1341)特征134)中,焙烧温度为800~1300℃。
60.更优选地,还包括如下技术特征中的至少一项:
61.291)特征29)中,造孔温度为500~700℃;
62.2101)特征210)中,造孔时间为3~5h。
63.更优选地,还包括如下技术特征中的至少一项:
64.331)特征33)中,升温速率为2~20℃/min;
65.332)特征33)中,升温至1400~1600℃进行升华-沉积;
66.341)特征34)中,升华-沉积的时间为3~5h。
67.本发明第三方面提供上述镍基催化剂在低碳烷烃干重整中的用途,如低碳烷烃烷-二氧化碳重整制合成气、低碳烷烃烷-水蒸气重整制氢、低碳烷烃烷-二氧化碳-水蒸气混合重整。
68.优选地,所述镍基催化剂进行还原活化后再进行低碳烷烃干重整;
69.和/或,所述低碳烷烃干重整为低碳烷烃烷-二氧化碳重整、低碳烷烃烷-水蒸气重整或低碳烷烃烷-二氧化碳-水蒸气混合重整;
70.和/或,反应压力为0.1~4mpa,如0.1~0.5mpa、0.5~1.5mpa、1.5~3mpa或3~4mpa;
71.和/或,反应温度为600~1200℃,如600~850℃、850~950℃、950~1150℃或1150~1200℃;
72.和/或,反应空速为1000~150000ml
·gcat-1
·
h-1
,如1000~7443ml
·gcat-1
·
h-1
、7443~8747ml
·gcat-1
·
h-1
或8747~150000ml
·gcat-1
·
h-1
。
73.如上所述,发明具有以下有益效果中的至少一项:
74.1)上述镍基催化剂适用以非常规天然气或焦炉气、驰放气、烟道气等富含低碳烷烃的尾气、废气为原料的低碳烷烃烷-二氧化碳重整制合成气工艺、低碳烷烃烷-水蒸气重整制氢工艺、低碳烷烃烷-二氧化碳-水蒸气混合重整工艺,工艺操作灵活、合成气h2/co比可调。
75.2)上述制备方法通过造孔获得催化剂丰富的孔结构,利用m元素的氟化物粉料升华-沉积处理获得m元素氧化物膜的沉积前驱物,再经m元素氧化物膜的沉积前驱物与空气
气氛中的水蒸气反应得到具有氧化物膜限域结构的镍基催化剂,氧化物膜限域结构确保工业条件下还原活化后催化剂表面镍活性位点的物理隔离,进而实现镍活性位点在600~1200℃反应工况下的高分散与高热稳定性,有效抑制镍颗粒迁移团聚现象,确保催化剂具有高活性、高抗积碳性能。
76.3)上述镍基催化剂适用反应压力0.1~4mpa、温度600~1200℃、空速1000~150000ml g
cat-1
h-1
的反应条件。
附图说明
77.图1为还原活化前后氧化物膜限域镍基催化剂孔道内壁氧化物膜断面。
78.(a)还原活化前氧化物膜限域镍基催化剂孔道内壁氧化物膜断面。
79.(b)850℃氢气/氮气混合气还原活化后微观形貌一。
80.(c)850℃氢气/氮气混合气还原活化后微观形貌二(圈出位置为镍颗粒)。
81.图2为炉温850℃、空速7443ml
·gcat-1
·
h-1
、反应压力0.5mpa、原料气ch4/co2摩尔比1/1的条件下甲烷-二氧化干重整反应评价结果。
82.图3为炉温1150℃、空速8747ml
·gcat-1
·
h-1
、反应压力0.5mpa、原料气ch4/co2/h2o摩尔比1/1/0.2的条件下甲烷-二氧化碳-水蒸气混合重整反应评价结果。
83.图4为炉温950℃、空速3929ml
·gcat-1
·
h-1
、反应压力1.5~3.0mpa、原料气ch4/co2摩尔比1/1.7的条件下甲烷-二氧化碳干重整反应评价结果。
具体实施方式
84.下面结合实施例进一步阐述本发明。应理解,这些实施例仅用于说明本发明,而非限制本发明的范围。下列实施例中未注明具体条件的实验方法及未说明配方的试剂均为按照常规条件或者制造商建议的条件进行或配置。
85.实施例1
86.镍负载载体金属氧化物粉料:称取粒度范围10~40微米的氧化镁粉体100g,喷淋加入20ml摩尔浓度为4mol/l的硝酸镍水溶液,用高速混合机充分捏合,经120℃干燥2h、500℃焙烧3h,充分研磨、筛分,取粒度范围10~40微米的粉料备用。
87.m元素的氟化物粉料:三氟化铝粉体0.5g,取粒度范围1~5微米。
88.1)用高速混合机将粒度范围10~40微米的镍负载氧化镁原粉、粒度范围1~5微米的铝的氟化物粉体等充分混合后用机械成型机模压成型(拉西环状),得到成型前驱体,其中,mgo:ni(no3)2:alf3=100:14.62:0.5(质量比)。
89.2)在干燥的流动空气气氛下室温老化50h,成型前驱体侧压强度在150n以上,然后于120℃干燥12h,随后将成型前驱体转移至高温炉,同样在干燥的流动空气气氛下20℃/min升温至400℃恒温5h,进行充分的造孔,得到造孔物料,其中,干燥的流动空气气氛是指水蒸气含量按干气体计不超过20g/m3。
90.3)400℃恒温造孔过程完成后开始通入高纯氮气置换炉腔内的空气气氛,同时5℃/min缓慢升温至1400℃后密封炉腔,保持静态高纯氮气气氛并恒温3h,进行氟化物升华/汽化-沉积,得到沉积物料。
91.4)将沉积物料以10℃/min降温速率降温至400℃后停止高纯氮气并切换为流动空
气(水蒸气含量为80g/m3),继续以15℃/min降温速率降温至室温,得到镍基催化剂:氧化镍5.61%,载体氧化镁93.82%,具有氧化物膜结构的氧化铝0.57%。
92.还原活化前氧化物膜限域镍基催化剂孔道内壁氧化物膜断面,见图1(a),在还原活化前催化剂内表面由一层厚度约200nm的氧化铝膜均匀覆盖(即具有氧化物膜结构的氧化铝)。850℃下用50%氢气/氮气混合气还原活化后微观形貌,见图1(b),经还原活化后,大量粒径小于5nm的镍颗粒均匀镶嵌在氧化物膜表面,见图1(c),获得的催化剂在还原活化前后具有特殊的形貌,有效抑制镍颗粒迁移团聚,具有高活性和高热稳定性。
93.将经步骤1)至步骤4)制备获得的拉西环状催化剂颗粒在100g装填量的单管装置进行单颗催化剂评价,炉温850℃下用50%h2/n2原位还原3小时即可用于甲烷-二氧化碳干重整反应,在炉温850℃、空速7443cm3/(gh)即ml
·gcat-1
·
h-1
、反应压力0.5mpa、原料气ch4/co2摩尔比1/1的条件下测试了催化剂的性能,其结果如图2所示。
94.实施例2
95.镍负载载体金属氧化物粉料:称取粒度范围5~100微米的氧化铈粉体100g,喷淋加入140ml摩尔浓度为4mol/l的硝酸镍水溶液,用高速混合机充分捏合,经120℃干燥2h、600℃焙烧3h,充分研磨、筛分,取粒度范围5~100微米的粉料备用。
96.m元素的氟化物粉料:四氟化锆粉体3.5g,取粒度范围1~10微米。
97.1)用高速混合机将粒度范围5~100微米的镍负载氧化铈原粉、粒度范围1~10微米的铈的氟化物粉体等充分混合后用机械成型机模压成型(拉西环状),得到成型前驱体,其中,ceo:ni(no3)2:zrf4=100:102.31:3.5(质量比)。
98.2)在干燥的流动空气气氛下室温老化50h,成型前驱体侧压强度在150n以上,然后于120℃干燥12h,随后将成型前驱体转移至高温炉,同样在干燥的流动空气气氛下20℃/min升温至800℃恒温5h,进行充分的造孔,得到造孔物料,其中,干燥的流动空气气氛是指水蒸气含量按干气体计不超过20g/m3。
99.3)800℃恒温造孔过程完成后开始通入高纯氮气置换炉腔内的空气气氛,同时5℃/min缓慢升温至1800℃后密封炉腔,保持静态高纯氮气气氛并恒温3h,进行氟化物升华/汽化-沉积,得到沉积物料。
100.4)将沉积物料以20℃/min降温速率降温至800℃后停止高纯氮气并切换为流动空气(水蒸气含量为130g/m3),继续以10℃/min降温速率降温至室温,得到镍基催化剂:氧化镍28.97%,载体氧化铈69.24%,具有氧化物膜结构的氧化铈1.79%。
101.还原活化前催化剂内表面由氧化锆膜均匀覆盖(即具有氧化物膜结构的氧化锆)。850℃下用50%h2/n2混合气还原活化后大量镍颗粒均匀镶嵌在氧化物膜表面,获得的催化剂在还原活化前后具有特殊的形貌,有效抑制镍颗粒迁移团聚,具有高活性和高热稳定性。
102.将经步骤1)至步骤4)制备获得的拉西环状催化剂颗粒在100g装填量的单管装置进行单颗催化剂评价,炉温850℃下用50%h2/n2原位还原3小时即可用于甲烷-二氧化碳-水蒸气混合重整反应,在炉温1150℃、空速8747cm3/(gh)即ml
·gcat-1
·
h-1
、反应压力0.5mpa、原料气ch4/co2/h2o摩尔比1/1/0.2的条件下测试了催化剂的性能,其结果如图3所示。
103.实施例3
104.镍负载载体金属氧化物粉料:称取粒度范围5~100微米的氧化铝粉体100g,喷淋加入100ml摩尔浓度为2mol/l的硝酸镍水溶液,用高速混合机充分捏合,经120℃干燥2h、
600℃焙烧3h,充分研磨、筛分,取粒度范围5~100微米的粉料备用。
105.m元素的氟化物粉料:三氟化铈粉体1.5g,取粒度范围1~10微米。
106.1)用高速混合机将粒度范围5~100微米的镍负载氧化铝原粉、粒度范围1~10微米的铝的氟化物粉体等充分混合后用机械成型机模压成型(拉西环状),得到成型前驱体,其中,al2o3:ni(no3)2:cef3=100:36.54:1.5(质量比)。
107.2)在干燥的流动空气气氛下室温老化50h,成型前驱体侧压强度在150n以上,然后于120℃流动干燥空气气氛下干燥12h,随后将成型前驱体转移至高温炉,同样在干燥的流动空气气氛下20℃/min升温至800℃恒温5h,进行充分的造孔,得到造孔物料,其中,干燥的流动空气气氛是指水蒸气含量按干气体计不超过20g/m3。
108.3)800℃恒温造孔过程完成后开始通入高纯氩气置换炉腔内的空气气氛,同时5℃/min缓慢升温至1800℃后密封炉腔,保持静态高纯氩气气氛并恒温3h,进行氟化物升华/汽化-沉积,得到沉积物料。
109.4)将沉积物料以15℃/min降温速率降温至800℃后停止高纯氩气并切换为流动空气(水蒸气含量为200g/m3),继续以20℃/min降温速率降温至室温,得到镍基催化剂:氧化镍12.85%,载体氧化铝86.02%,具有氧化物膜结构的氧化铈1.13%。
110.还原活化前催化剂内表面由氧化铈膜均匀覆盖(即具有氧化物膜结构的氧化铈)。850℃下用50%h2/n2混合气还原活化后大量镍颗粒均匀镶嵌在氧化物膜表面,获得的催化剂在还原活化前后具有特殊的形貌,有效抑制镍颗粒迁移团聚,具有高活性和高热稳定性。
111.将经步骤1)至步骤4)制备获得的拉西环状催化剂颗粒在100g装填量的单管装置进行单颗催化剂评价,炉温850℃下用50%h2/n2原位还原3小时即可用于甲烷-二氧化碳干重整反应,在炉温950℃、空速3929cm3/(gh)即ml
·gcat-1
·
h-1
、反应压力1.5~3.0mpa(反应时间≤24h,反应压力为1.5mpa;反应时间>24h,反应压力为3mpa)、原料气ch4/co2摩尔比1/1.7的条件下测试了催化剂的性能,其结果如图4所示。
112.以上的实施例是为了说明本发明公开的实施方案,并不能理解为对本发明的限制。此外,本文所列出的各种修改以及发明中方法、组合物的变化,在不脱离本发明的范围和精神的前提下对本领域内的技术人员来说是显而易见的。虽然已结合本发明的多种具体优选实施例对本发明进行了具体的描述,但应当理解,本发明不应仅限于这些具体实施例。事实上,各种如上所述的对本领域内的技术人员来说显而易见的修改来获取发明都应包括在本发明的范围内。