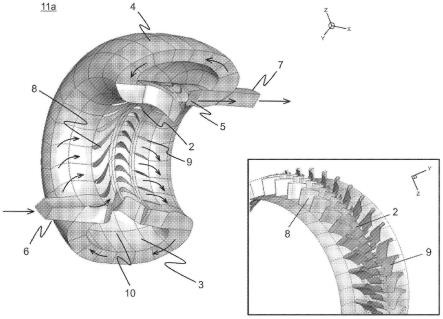
冲击波反应器及其用途、反应器组件、装置和方法
1.本技术是申请日为2014年7月3日,申请号为201480081693x,发明名称为“方法及旋转机型反应器”的中国发明专利申请的分案申请。
技术领域
2.本发明涉及石油和石化精炼领域,特别是涉及用于含烃化合物的热裂解(cracking)的反应器。
背景技术:3.裂解方法在历史上已经用于炼油厂和石油化工厂,以将重烃流转化为更轻的烃馏分。虽然石油和石化精炼领域被称为是成熟且根深蒂固的技术领域之一,但石油和石化工业出现的趋势之一要求任何开发技术都将满足两个主要的要求。这些要求可简要地被表述为节能和减少从不可再生的原材料来源提取的原料的消耗。这些也是用于开发主要石化方法之一(大规模生产低级(低分子量)烯烃)要考虑的问题。
4.低分子量烯烃(诸如乙烯、丙烯和丁烯)是石油化学工业的基本产物,并且用作塑料、橡胶、聚合物、弹性体和其他合成材料以及纤维和涂料的商业生产中的原料。用于低级烯烃的现有生产技术包括将中等重量烃(诸如石脑油或气油)和轻质烃(如戊烷、丁烷、丙烷和乙烷)热解为管式炉中的轻量基本上不饱和的可聚合组分,该技术产生于半个多世纪以前并且几乎不能满足成本有效的原料利用的现代需求。管式炉对热解方法具有限制:反应温度因为管材料的耐久性而不能增加,以及从管壁到处理气体的热传递具有物理限制。这导致原料滞留时间,其对于该方法不是最佳的。管式裂解炉中不足的原料加热速率导致热解方法的增加的持续时间。该事实导致这样的情况,即,当在初始阶段形成时,烯烃在反应炉中停留足够长的时间以开始进入二次反应,其自然后果是目标产物的损失。次级产物还包括焦炭,其引起管中的热传递问题和位于下游的设备中的结垢。传统技术不能提供用于消除上述问题的合理解决方案,这是因为常规热解炉的辐射段中的热传递速率已经达到了技术限制。在常规管式反应器中,热量因此通过反应器壁被输送至反应区。
5.除了管式炉之外,用于热解设备的解决方案是已知的。这些包括具有复杂的转子叶片布置的旋转反应器。用于建造和维护这样的设备的成本高于可通过其获得的利润。
6.因此,用于通过热降解生产低分子量烃的传统方法遇到了以下问题:1.管式炉反应器的性能系数差;2.有价值的原料材料的损失;3.反应时间长;4.高的二次反应速率;4.高能耗;5.非最佳的(小于可能的)产物产率和选择性。
技术实现要素:7.本发明的目的是通过实施原料的热处理、热化学处理或催化热化学处理的新方法(诸如含烃化合物的热裂解)来至少缓解上述问题。
8.该目的通过提供适合于含烃原料的热解的旋转机型反应器来实现。
9.在一种实施方式中,螺旋通道反应器(helical-path reactor)包括具有轴和设置
有形成轴流转子叶栅的叶片的盘的转子、可选地设置有邻接轴流转子叶栅的至少两个固定叶栅(静叶珊,静止叶珊,stationary vane cascade)的固定引导环形缘、和壳体。布置在壳体内的引导缘(directing rim)的外表面与壳体的内表面一起基本上限定管道(duct)以保持在其间。可替代地,固定叶栅中的至少一些可以例如形成在壳体的限定管道壁的内表面上。管道在子午面中的横截面形成环形轮廓。
10.管道可以包括以形成若干个操作室这样的方式设置的若干个分隔壁(dividing partition)。操作室优选地具有相等的尺寸;然而,在适当的情况下,其他技术实施方式是可能的。
11.反应器包括至少一个用于原料流的入口端口(入口)和至少一个用于产物流的出口端口(出口)。入口端口优选地沿转子的旋转方向布置在每个分隔壁之后,并且出口端口优选地布置在分隔壁之前。入口端口和出口端口可以被集成在管道内。
12.反应器可以进一步配置有布置在轴流转子叶栅上游的第一固定叶栅;以及布置在轴流转子叶栅下游的第二固定叶栅。因此,固定叶栅可以设置有引导缘。前述固定叶栅以使得在第一叶栅出口点和第二叶栅入口点之间产生无叶空间这样的方式布置。
13.在一种实施方式中,反应器被配置为具有所有上述叶栅(即固定叶栅和转子叶栅),其在管道内基本上是邻近的。
14.在一些实施方式中,反应器内的所有叶栅的三维排列适于引导含有处理流(工艺流)的原料在入口端口和出口端口之间的管道内传播时按照螺旋轨迹重复地经过所述叶栅和无叶空间,并适于顺序地生成固定冲击波(激波)以加热反应器内的原料。轴流转子叶栅因此被配置为向含有处理流的原料提供动能,从而增加其速度,并且位于其下游的固定叶栅被配置为降低处理流的速度并将动能转换成热。
15.提供所有叶栅及其叶使得允许处理流的流速度能够在所有叶栅处达到超过声速(即超音速)的速度,同时在管道内的无叶空间中的流速保持亚音速(次音速,subsonic)。
16.在一种实施方式中,轴流转子叶栅设置有工作叶片(blade),该叶片具有主动超音速冲击涡轮叶片的轮廓(分布,profile),这些叶片以使其凹侧指向转子旋转的方向这样的方式被安装转子。
17.在一些实施方式中,第一固定叶栅设置有多个叶(vane),这些叶具有弯曲的轮廓并且通过其凸侧沿转子旋转的方向设置;并且第二固定叶栅设置有多个叶,这些叶具有弯曲的超音速压缩机(超音速压气机,supersonic compressor)轮廓,并且还通过其凸侧沿转子旋转的方向设置。
18.根据一些其他实施方式,反应器被配置为轴流压气机型机器(轴向压缩机式机械,轴流式压缩机,axial compressor type machine)。该实施方式的轴反应器(轴向反应器,axial reactor)包括细长的转子,沿该细长的转子将多个转子叶片布置成许多顺序行以形成一个或多个轴流转子叶栅。转子封装在壳体内,壳体的内表面设置有定子叶栅,所述定子叶栅被布置成使得转子叶栅和定子叶栅的叶片/叶沿着所述转子的长度交替。
19.在各种实施方式中,反应器适于处理流体原料,优选气态原料物质。
20.在一些实施方式中,反应器适于处理含氧原料物质,诸如基于碳水化合物的原料物质和基于甘油酯(诸如例如甘油三酯)的原料物质。
21.在又一实施方式中,反应器适于处理以气态形式提供到反应器中的基于生物质的
原料物质、优选纤维素衍生的原料物质或者特别是木质纤维素衍生的原料物质。
22.在本发明的另一方面,提供了一种反应器组件,其包括连接至驱动发动机、热回收单元和淬火单元的本发明的反应器。
23.在本发明的又一方面,提供了热解设备形式的装置(arrangement),所述装置包括至少两个串联或并联连接的本发明的反应器。
24.在本发明的再一方面,提供了一种利用本文公开的反应器的实施方式来热裂解含烃原料的的方法。
25.在本发明的又一方面,提供了一种通过冲击波对快速吸热化学反应输入能量的方法,该冲击波由本文公开的反应器的旋转叶栅的机械能产生。
26.取决于本发明的每种具体实施方式,本发明的实用性由各种原因产生。首先,根据一些实施方式所实施的旋转机型反应器使得能够在接近完美流位移反应器的操作模式的条件下进行新的裂解工艺(方法)。旋转机型反应器因此提供了用于含烃化合物的热解的新方法,特别适合于获得低分子量的含烃化合物。反应器设计基于将机械能转换为反应器内的高热能的高速转子,并且本文提供的热解方法与通过向反应混合物供热的方法的常规热裂解技术不同。然而在常规管式热解炉中,用于热解的热量通过管状盘管壁传递,本文公开的反应器被配置为使得能够直接在反应混合物内生成热量。
27.反应器中的分解反应由于当含有处理流的原料穿过一系列高强度的稳定冲击波时在该原料中直接生成的热量而发生。这种供热方法使得能够显著降低限定反应区的壁的温度,因此提供了克服在供热速度上的限制的机会,供热速度上的限制另外对于管式炉是典型的。原料气体在由固定叶栅和转子叶栅所限制的空间以及无叶空间组成的反应区中度过的时间非常短(大约0.01秒或更短),这比常规热解炉短了约10倍。因此,该方法比常规热裂解更可控,但化学反应保持基本上相同。因为可以降低压力和减少原料气体在反应区中的停留时间,以及由于在处理流的横截面中更均匀的温度分布,因此所期望的热解产物的产率增加。由于上述方法的特征在于例如主要产物(诸如烯烃)的产率极高,因此所提供的技术首先代表了开发裂解方法的下一步骤,以由较少量的原料(诸如油和气体)产生额外的价值。在工业中利用所述反应器使得能够更加成本有效地处理原材料,因此积极地影响油精炼设备的效率和收益率。
28.其次,提供旋转机型反应器使得可以解决焦炭形成问题。与常规技术相比降低焦炭形成速率的原因是气态原料在反应区中较低的停留时间结合反应器静态部件(壁)的较低的温度。此外,较低的停留时间有利于对所需产物的反应选择性。
29.本发明的反应器还使得能够处理衍生自例如基于生物的原料的含氧原料材料。所述反应器的其他可能的应用领域因此包括在诸如将植物油(例如松油)或动物脂肪直接催化氢化成例如相应烷烃的方法中精炼生物质或生物质衍生的物质以产生可再生的燃料。另外,可以通过本发明的反应器实施基于生物的热解气体或合成气体的增值(提升,valorization),其中术语“增值”在本文中提及来指示气态物质的增强或精制。
30.可替代地或另外,本发明的反应器可以设置有一个或多个催化表面以使得能够进行催化反应。
31.特别关注本发明的轴流压气机型或涡轮机型反应器的各种实施方式,可以获得所谓的塞流模型(plug flow model)。同时,由于产物和原料混合而在转子室中发生和导致焦
化的不期望的副反应可以通过所提出的装置避免。与其中两个不同的定子叶栅的叶片具有不同的结构和位置角度的早前提出的其他旋转反应器解决方案相比,本文使用的固定叶栅可以具有相同或至少类似的类型。
32.术语“热解”和“裂解”在本公开中主要作为关于较重的含烃化合物热降解为较轻的含烃化合物的方法的同义词使用。
33.表述“许多(至少一个,若干,一些,a number of)”在本文中是指从一(1)开始例如到一、二、三等的任何正整数。
34.表述“多个(a plurality of)”在本文中是指从二(2)开始例如到二、三、四等的任何正整数。
35.除非另有明确说明,否则术语“第一”和“第二”在本文中不表示任何特定的优先级或顺序。相反,它们用于将一个实体(诸如物理元件)与其他实体区分开。
36.术语“流体”在本文中主要是指气态物质,诸如例如在蒸汽稀释剂存在或不存在的情况下的处理流气相。
37.术语“弦(chord)”在本文中表示连接弧(在此为弯曲的叶片/叶)的终点的直线。
38.术语“气化的”在本文中用于表示通过任何可能的方式转化成气态形式的物质。
39.术语“流体动力学的”在本文中用于表示流体的动力学,在本公开中,流体主要由气体表示。因此,所述术语在本公开中用作术语“空气动力学的”的同义词。
40.通过考虑详细的描述和附图,本发明的不同实施方式将变得显然。
附图说明
41.图1例示了根据本发明的用于热解含烃原料的反应器的一种实施方式。
42.图2a例示了图1的反应器的内部布置。
43.图2b更详细地例示了图2a的反应器中的叶布置和流动流(stream flow)。
44.图2c例示了图1和图2a、图2b的反应器的几何参数和操作条件。
45.图3a是图1和图2a至图2c的反应器内的气流的温度历史图。
46.图3b例示了图1和图2a至图2c的反应器内的叶分布。
47.图4a例示了在本文中被配置为轴向涡轮机的反应器的另一实施方式。
48.图4b例示了两个图4a的轴反应器的顺序连接。
49.图5是基于本发明的反应器的反应器组件和相关裂解方法的高级框图。
具体实施方式
50.在此参考附图公开了本发明的详细实施方式。在整个附图中使用相同的附图标记来指代相同的构件。以下编目(引用,citation)用于构件:
51.1-转子轴;
52.1a-转子盘;
53.2-具有转子叶片的轴流叶栅(cascade);
54.3-引导缘;
55.4-壳体;
56.5-分隔壁;
57.6-进料入口端口;
58.6a-第二进料入口端口或蒸汽注入端口;
59.7-产物出口端口;
60.8-具有喷嘴叶(nozzle vane)的第一固定叶栅;
61.9-具有扩散叶的第二固定叶栅;
62.10-具有无叶空间的管道;
63.11a-根据第一实施方式的旋转机型反应器;
64.11b-根据第二实施方式的旋转机型反应器;
65.11c-根据一种可行实施方式的包括至少两个互连的反应器的操作模块;
66.12-催化元件;
67.13-冷却介质注入端口;
68.14-冷却或加热端口;
69.101-驱动发动机;
70.102-旋转机型反应器;
71.103-热回收单元;
72.104-淬火(quenching)单元;
73.105-空气过滤器。
74.在图1中示出了根据本发明的一种实施方式的用于热解含烃原料的螺旋通道反应器11a的截面图(参见如在反应器顶视图的嵌入式微型图(虚线框)中所指示的截面a-a')。反应器包括设置有转子轴1的转子,将转子盘1a固定至该转子轴1。转子盘1a又设置有形成轴流转子叶栅2的多个转子叶片。轴流转子叶栅的转子叶片优选地具有主动超音速冲击式涡轮叶片的轮廓;通过它们的凹侧朝转子旋转的方向将它们径向地定向并安装。转子叶片的周向速度适于为至少250m/s。反应器11a还包括邻接轴流转子叶片的顶端的内部固定环形缘3和壳体4的内表面。外部壳体4包围缘3和转子1的外周,以限定环形管道10保持在缘3的外表面和壳体4的内表面之间。因此,管道10的子午截面(meridian cross-section)形成环形轮廓。反应器11a还包括至少至少一个用于原料流的入口端口6和至少一个用于产物流的出口端口7。在适当的情况下,反应器11a可以被配置为具有两个入口端口和两个出口端口。
75.设置有该实施方式的反应器11a基本上以环的环面(ring torus)的形状实施。因此,图2a提供了环面形反应器的极向横截面,以便示出关于基本上环形的结构的入口端口和出口端口的空间位置。
76.管道10的内部可以被实施成未分割的。在可替代的实施方式中,管道10可以包括布置在其中的若干个分隔壁5,以变形成至少两个操作室(图2a)。所述室的尺寸优选是相同的;然而在适当的情况下不排除其他技术实施方式。入口端口6优选地沿转子旋转方向布置在每个分隔壁5之后,并且出口端口7优选地布置在每个分隔壁5之前。入口端口和出口端口可以被集成在管道内。
77.接下来将参考图2a-图2c,其基于反应器11a的cfd(计算流体动力学)模拟模型创建。本文中图2b表现的图对应于用于cfd计算的单个计算域。
78.环的环面形反应器11a还设置有至少两个固定(定子)叶栅8、9。因此,第一固定叶
栅8布置在轴流转子叶栅2的上游,并且包括多个叶,该叶优选地具有弯曲的轮廓并且通过它们的凸侧沿转子旋转的方向设置。第一固定叶栅8的叶优选地被配置为喷嘴叶,因此为了清楚起见,第一叶栅还将被称为“喷嘴叶栅”。
79.第二固定叶栅9布置在轴流转子叶栅2的下游,并且包括多个叶,该叶优选地具有弯曲的超音速压气机轮廓并且也通过它们的凸侧沿转子旋转的方向设置。第二固定叶栅9的叶优选地被配置为扩射叶,因此为了清楚起见,第二叶栅还将被称为“扩散叶栅”。
80.设置有两种固定叶栅(8、9)的叶可以被实施为两种叶栅同样具有弯曲的轮廓。
81.固定叶栅8、9可以设置有引导缘3(图1、图2a)或者设置在壳体4的内表面的限定管道的壁上,如基于图(参见图2a上的框)是明显的。以使得在扩散叶栅9的出口和进入喷嘴叶栅8的入口之间形成无叶空间的方式优选地布置固定叶栅8和9。
82.根据一些实施方式,反应器11a被配置成使叶栅2、8和9在管道10内基本相邻。
83.图2c例示了反应器11a的几何参数和一组操作条件。
84.反应器操作原理是基于将处理流的动能转化为热。反应器11a的设置使得用于处理原料分子的热不通过反应器的壁传递,而是进入反应器的已蒸发的原料和蒸汽的混合物由于设置有叶栅的叶的气动阻力而被反应混合物内直接产生的热加热。
85.反应器11a基本上如下操作。转子1的旋转迫使每个操作室中的气体从入口端口6转移到出口端口7。将含有处理流的原料(包括例如可调节比例的烃基原料和蒸汽稀释剂(在压力下由外源提供,未示出))供应到反应器入口端口6中。原料-稀释剂比例很大程度上取决于反应器管道内形成的压力;压力的降低因此导致供应到具有处理流的反应器中的蒸汽稀释剂的量减少。含有处理流的原料进一步被引导在入口端口和出口端口之间的管道10内循环时根据螺旋轨迹重复地经过喷嘴叶栅8、轴流叶栅2、扩散叶栅9和无叶空间。叶栅2、8和9以及位于它们上的叶的设置使得允许处理流的流速在所有叶栅处是超音速的,而管道10内的无叶空间中的流速仍然是亚音速的。因为含有处理流的原料被连续地迫使按照螺旋轨迹经过定子-转子-定子叶栅,所以反应器在本公开内有时被称为螺旋通道反应器(helical-path reactor)。
86.轴流转子叶栅2另外被配置为向含有处理流的原料提供动能,从而向其添加流速,而扩散叶栅9被配置为降低穿过其中的处理流的流速。在停留在反应区内的时间期间,含有处理流的原料分别穿过叶栅8、2和9若干次,并且每次当穿过轴流转子叶栅2时将处理流加速,因此接收动能在扩散叶栅9中流速减小时进一步转化为热。所建立的运动由此产生了在反应器内加热气态原料的稳定冲击波。事实上,在处理流受到高强度的稳定冲击波影响的时间期间,所述流在连续脉冲(冲击,impulse)中被加热。图3a例示了在示例性模型反应器11a内的停留时间期间由处理流生成的时间依赖性温度曲线。虚线表示处理流经过定子-转子-定子叶栅8、2、9的时刻并且虚线圆圈限定了处理阶段(i-v)。图3a的温度曲线因此具有整体温度从约500℃增加到几乎1000℃的锯齿状结构。将原料在大约600℃下引入反应器中,并进一步加热,随后穿过叶栅和无叶空间。这种布置导致所有处理流颗粒具有基本相同的温度历史的事实。后一事实使得螺旋通道反应器在其技术特性方面接近于完美的柱塞流型反应器。图3a所示的示例性温度历史图是通过环的环面形反应器的模拟建模获得的,假设在气态原料流动穿过叶栅(稳态流动模拟)时有序运动(颗粒的流动)和单独分子的混乱运动的动能的总和是恒定的。
87.对于示例性的模型反应器11a(图3a),需要五个阶段(i-v)来获得高达至900℃的温度,在该温度下吸热反应消耗了大部分热输入,因为后来的能量输入将完全用于裂解而不是进一步升温。因此,可以在此实施方式的反应器中在原料处理流以超音速通过高强度的稳定冲击波的多个转变期间进行热裂解的过程。当在扩散叶栅9的叶间管道的入口处出现稳定的冲击波时,发生显著的温度跳跃。
88.图3b例示了示例性反应器11a内的叶片/叶分布。由于再生压缩/能量添加过程期间的温度升高,处理气体的密度沿着反应器11a从入口端口6到出口端口7变化。因此定子叶和其间的节距(间距/螺距,pitch)的分布是不均匀的。图3b因此例示了如上所述的示例性五阶段布置。对于转子,节距/弦比(节/弦比,pitch/chord ratio)不能改变,并且其以值0.75总共固定80个叶片(参见图2c),假设每个叶片具有16mm(0.016m)的轴向弦参数和0.151m的平均半径。在表1中提供了固定叶栅的节距/弦参数。
89.表1.用于定子叶栅的几何参数。
[0090][0091]
尽管在本反应器中在500-1000℃下进行常规热解反应,但所需的最小“开始”温度可以向下调节至200℃。对于一些生物技术应用,最小温度可以调节到极低值,诸如例如室温。这样的生物技术应用包括处理碳水化合物,诸如例如糖。
[0092]
操作期间反应器管道10中的压力可以通过调节入口和出口压力来调节。对于用作气态原料的重烃,管道10中的压力可以为约2巴绝对压力(0.2mpa);其他的较低的压力设置可能是可取的。
[0093]
可以这样调节反应器参数,使得气态原料在反应区中度过的时间(停留时间)从几秒钟向下变化到几毫秒,优选地向下到大约10毫秒。绝对停留时间可以取决于许多处理阶段和如上所指示的无叶空间的体积(图3a)。
[0094]
参照图4a,例示了用于另一旋转反应器的可替代的实施方式。根据该实施方式,反应器11b被配置为轴流压气机型反应器或涡轮机。该实施方式的反应器11b包括延伸的(细长的)转子1,多个转子叶片沿着该转子布置成许多顺序行以形成一个或多个轴流转子叶栅2。
[0095]
转子1被封装在壳体4内,该壳体的内表面分别设置有固定(定子)第一叶栅8和第二叶栅9,其被布置成使得转子叶栅和定子叶栅2、8和9的叶片/叶沿着转子1在纵向方向上(沿着转子长度)交替。定子叶栅(8、9)叶优选地布置在壳体4的管道壁限定的内表面的相对侧上。因此,沿着转子1在纵向方向上的某个位置的转子叶栅2的叶片可以被考虑形成具有相邻的定子叶对(叶栅8和9)的所谓的叶栅单元(级联单元)或“阶段”,其在图4a中通过虚线圆而被突出。后续阶段在它们之间具有无叶片/叶空间。该空间可以含有如下文所考虑的其
他元件。在合适的情况下,其他阶段配置自然是可能的。
[0096]
在转子1和壳体4的内表面之间提供的容积(空间)被定义为管道10,其因此包围转子叶栅2和定子叶栅8、9。反应器11b还包括至少一个用于原料流的入口端口6和至少一个用于产物流的出口端口7。反应器11b可以包括例如用于注入冷却介质的至少一个附加端口13。另外,反应器11b可以包括催化元件或催化空隙(催化孔洞,catalytic void)12(中间催化空间),如进一步更详细公开的。然而,所选择的叶片和/或叶可以设置有催化材料,例如以催化涂层的形式。
[0097]
对于前述实施方式公开的定子叶非均匀分布也可适用于轴反应器11b。
[0098]
上述配置使得能够进行高度定制的化学方法,其中反应区中的反应时间、温度和/或气态原料停留时间可以被定制以实现最佳选择性/转化率。为了控制温度和/或稀释速率,该实施方式的反应器可以包括用于反应性组分和/或给料稀释剂的附加蒸汽注入端口。根据该实施方式的反应器的设置使得当原料气流进入反应室时,其受到由固定叶栅8、9和转子叶栅2的协同机械功造成的冲击波产生的热的影响。设置在转子-定子叶栅内的叶片/叶配置可以与前述实施方式相同;然而,轴涡轮机型实施方式通过改变甚至在行内的转子叶栅和定子叶栅叶片/叶的结构参数(即该设计可在特定叶栅的顺序行内交替)而允许在调整反应参数方面有额外的灵活性。
[0099]
在图4b中示出了操作模块11c的实施方式,其包括至少两个依次或串联连接的上述实施方式的轴涡轮机型反应器11b。图4b的配置示出了两个互连的反应器单元11b,驱动发动机元件101位于所述反应器单元之间。“串联”配置可以设置有额外的入口端口6a,其可例如用于额外的给料注入或用于蒸汽注入。用于引入冷却或加热介质的附加端口14可以布置在设置在两个反应器单元11b之间的连接管处。然而,应当理解,操作模块11c的最终布置在很大程度上取决于生产线的尺寸和目的以及其中单独的反应器单元的数量。
[0100]
如以上所间接提及的,根据本发明的不同实施方式的反应器11a、11b通常可以设置有用于实现催化反应的一个或多个催化表面或一个或多个其他催化元件。催化表面优选地通过在反应区内的至少一个叶栅(blade cascade)/叶栅(vane cascade)的单个叶片或叶中的至少一些的催化涂覆(catalytic coating)而形成。设置有叶栅并位于反应区内的叶可以在适当时被催化涂覆。可替代地或另外地,催化涂层可以施加到例如反应区内的壳体的管道壁限定的内表面上。可替代地或另外地,一个或多个催化元件或一个或多个催化空隙可以布置在反应区内,由具有活性涂层的陶瓷的或金属的一个或多个基底或一个或多个支撑载体形成或设有具有活性涂层的陶瓷的或金属的一个或多个基底或一个或多个支撑载体。可替代地,可以利用整体蜂窝催化剂(单片蜂窝催化剂,monolithic honeycomb catalysts)。催化元件在图4a和图4b中用数字12指示。
[0101]
根据各种可行实施方式的反应器(如上所述的反应器)通常适于处理气态原料材料,并且实际上,旋转反应器可以被配置为例如处理含氧原料物质。因此,原料材料的选择可以自然地延伸超出由烃基原料所限定的限制。在一种实施方式中,反应器可适于生物质精炼以在诸如植物油直接催化氢化成相应烷烃或作为费-托法的阶段之一的气态烃的催化脱氢的方法中产生可再生燃料。适于生物精炼的反应器可以适于利用基于气态生物质的预处理原料。在反应器被调整用于气化生物质处理的情况下,特别是与本文其他部分所公开的催化涂覆表面相结合,可以开发用于生产可再生燃料的新的成本有效的方法。生物精炼
相关应用的另一实例是甲烷的催化高温(约900℃)二聚,其作为用于天然气液化的有前途的方法被广泛研究。
[0102]
可以提供反应器组件,其包括连接到驱动发动机、热回收单元和淬火单元的本发明的反应器或操作模块的实施方式。在图5中示出了一种仅示例性的设备,其描绘了基于根据本发明的任何实施方式的一个或多个反应器的反应器组件的高级框图,且包括发动机101、至少一个旋转机型反应器102、热回收单元103(诸如蒸汽锅炉)、淬火设备104和空气过滤器-消音器105。虽然上述设备可以与一个旋转反应器102一起运行,但图5例示了两个示例性布置,其中可以将三个反应器102并联(虚线框)或“串联”(实线框)连接。反应器102之间的功能连接由卷曲线指示。反应器102的数量及其在图5上的布置仅是示例性的,并且在实践中将在很大程度上取决于设备尺寸/容量和生产量。本文提供的反应器优选地是裂解单元;然而不排除其在裂解应用之外的利用。
[0103]
该组件可以利用多种驱动发动机,诸如电动机、气体活塞发动机、燃气涡轮机和蒸汽涡轮机。然而,燃气涡轮机或气体活塞发动机被证明是当前用于旋转反应器的最可行的驱动发动机之一。旋转反应器组件可能需要与常规热解炉设备基本上相同的加热和/或冷却单元。因此,旋转反应器可以被配置为在常规裂解中方便地替换辐射段盘管(radiant section coil),不另外影响整个单元的操作模式。此外,与常规工厂相比,由于副产物的较低产率,可以减小工艺下游设备的尺寸。
[0104]
还提供了用于螺旋通道反应器组件的操作模型的测试驱动的实例。
[0105]
实施例1.与不同制造商的常规管式热解炉相比,用于示例性螺旋通道反应器组件的测试驱动。
[0106]
开发并制造了螺旋通道反应器的小容量模型以评估在试验驱动条件下新的热解方法的技术可行性。为了进行实验,构建了试验台。试验系列的主要目的是获得关于热解产物产率和组成的数据。模型反应器因此配备有具有增速传动装置(step up gearing)的90kw电动机以驱动转子。模型反应器的技术特征如下:反应区的体积:2
×
10-3
m3;转子转速:18,000-20,000rpm。
[0107]
模型反应器的试验驱动过程中的处理条件设置类似于通常用于商业规模的反应器中的条件设置:热解反应的温度为约900℃;原料在反应区中的停留时间为0.025-0.030秒;以及出口压力为约1.2巴绝对压力。使用具有170℃的终沸点的石脑油作为原料。含有处理流的原料的流速为约40kg/h,并用包括50%的蒸汽稀释石脑油。本领域的专家检查了取样程序、原料和热解反应产物的分析以及产物产率的计算。裂解气体的分析由两个独立的专家组在不同的设备(varian cp-3800和lhm-8md)上进行。
[0108]
在上述驱动试验期间,在螺旋通道反应器中首次进行含烃材料的热裂解(热解)程序。试验结果证实,与在大多数先进的常规管式裂解炉中获得的主要产物产率相比,在螺旋通道反应器中获得了显著更高的主要产物产率。在石脑油的热解过程中每次运行的主要产物产率的数据总结在表2中。因此,表2提供了由模型螺旋通道反应器的试验驱动和由通过领先公司(诸如abb lummus、technip以及kellogg、brown和root(kbr))开发的常规管式裂解炉中进行的平行反应获得的比较数据。结果表明,在螺旋通道反应器中进行的热解导致总产率提高超过20%。
[0109]
表2.在模型螺旋通道反应器中和在常规管式裂解炉中进行热解反应期间每次运
行的主要产物的产率。
[0110][0111][0112]
数据证实,在装备有螺旋通道反应器的设备中,相同原料的热解导致最终乙烯产率的1.5倍增加,而与装备有通过常规技术操作的管式炉的设备相比,乙烯和丙烯的最终产率的总和可以增加1.25-1.3倍。
[0113]
虽然乙烯和丙烯是如上所述的石脑油裂解方法的主要产物,但是可以由其获得其他有价值的和有用的副产物。例如,在常规技术炉中用作燃料气体的甲烷(和未分离的氢气)可以用于驱动螺旋通道反应器的发动机。在热裂解方法中还产生了更重的有价值的副产物,如汽油和c4的混合物。在常规技术中,这些产物相对于离开热解单元的裂解气体的比率为大约20%至30%。在螺旋通道反应器的情况下,该比率为《20%。在实践中,这意味着虽然该方法的材料余量将显著降低,但是因为副产物的较低产率,可以降低下游设备的尺寸并且分离单元的操作成本可能更低。
[0114]
在本发明的各个方面和实施方式中,在通过增加或降低转子的旋转速度来调节反应器的内部压力的期间,例如,可以控制反应本身和相关参数。此外,可以通过例如压气机来提高入口流的压力。
[0115]
在此提供的反应器被配置为用于进行高温工艺的装置。本文进行的大多数反应是吸热的,因为原料在反应室中度过的停留时间短。然而,不排除进行伴随热释放(即放热)的反应。
[0116]
在本发明的各个方面和实施方式中提供的反应器被配置为主要旨在进行裂解方法的装置。然而,反应器可以被调节用于多种原料(包括基于碳水化合物的和/或基于甘油酯的预处理原料物质)的蒸汽裂解和催化裂解。因此,含有脂肪酸的原料物质可以由松油代表。
[0117]
因此,反应器可以适于新的应用,诸如裂解通过例如分解植物油和/或动物脂肪中所含有的甘油三酯而获得的游离脂肪酸。上述含有甘油三酯的产物的直接和/或逐步分解可以通过任何合适的方法进行。
[0118]
此外,由此公开的反应器可以适于例如减排或另外适于任何毒性/有毒气态物质的中和。在这种情况下,反应温度接近用于热解反应的温度。
[0119]
对于本领域技术人员清楚的是,所公开的反应器的常见技术参数(诸如转子速度、反应室的温度、停留时间历史等)被配置为在由原料性质、反应内部参数和/或由装置的技术实现(电机、环直径、环面距离等)所建立的特定限制内是可调节的。
[0120]
在本发明的另一方面,提供了热解设备形式的装置,其中所述装置包括至少两个串联或并联连接的旋转反应器。因此,提供旋转反应器单元支持模块化布置。示例性设备1000kt/乙烯设备单元可装备有40个螺旋通道反应器,其中32个反应器正在操作且8个反应器是备用的。所述反应器可以并联构建。工业规模的螺旋通道反应器可以优选地设置有具有约10mw轴的变速驱动发动机,用于向一个反应器输送动力。操作速度可以是例如约3600rpm。用于驱动发动机的能量可优选地由在裂解过程期间所产生的燃料气体提供。燃料气体又由甲烷和氢气分离单元获得。在由利用螺旋通道反应器提供的技术中,燃料气体可能用于驱动反应器发动机,而在常规技术中,已燃烧的燃料气体的热量用于加热原料/稀释蒸汽、锅炉给水和用于使对流段中的高压蒸汽过热。
[0121]
在本发明的另一方面,提供了一种用于热裂解含烃原料的方法,其包括以下项目中的至少一些:
[0122]
a.获得如本文所述的旋转机型冲击波反应器11a(螺旋通道)、11b(轴向的)的实施方式,其具有壳体4、转子1(其外周含有轴流叶栅2)以及特别是图1和图2a、图2b的实施方式中的引导缘3,其设置有邻接轴流转子叶栅的至少两个固定叶栅8、9,其中壳体4基本上包围转子1和引导缘3的外周;其中壳体4设置有入口端口6和出口端口7;其中具有基本上环形子午截面轮廓的管道10形成在具有入口端口和出口端口的壳体的内表面与转子引导缘之间;
[0123]
b.增加所述转子的旋转速度以达到预定的处理速度或速度范围;
[0124]
c.将含有处理流的原料给料到入口端口6中,于是两个固定叶栅8、9和转子叶栅2开始引导含有处理流的原料在入口端口和出口端口之间的管道内传播时按照螺旋轨迹重复地经过所述叶栅,并且顺序地生成固定的冲击波以加热反应中的原料流,从而引起其热降解或热解,以及
[0125]
d.将热解产物流通过出口端口引导到预定单元,诸如淬火设备。
[0126]
在本发明的又一方面,提供了一种输入用于快速吸热反应或快速放热反应的能量的方法,快速放热反应是例如通过由旋转叶栅的机械能产生的冲击波的催化氢化反应,所述方法包括:
[0127]
a.获得如本文所述的冲击波反应器11a、11b的实施方式,以及
[0128]
b.将含有烃原料或基于生物质的原料物质的预热气相传送到设置有生成机械能以建立冲击波的旋转叶片的反应器11a、11b中,所述冲击波为气相的吸热反应提供热量。
[0129]
然而,应当理解的是,上述数字以及公开的技术方案是示例性的,并且不旨在限制本发明,而是教导本领域技术人员在独立权利要求中所公开的本发明的保护范围的限制内实施本发明。