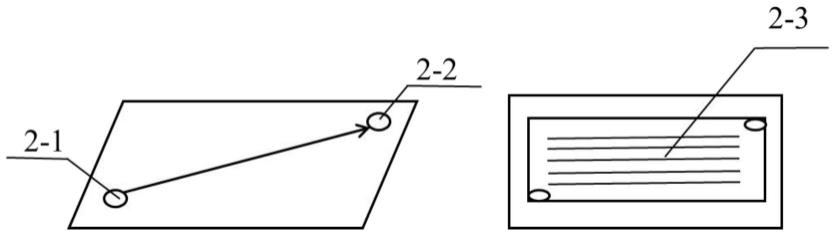
1.本发明属化工分离技术领域,具体涉及一种油水两相的微通道分离方法和微通道分离装置。
背景技术:2.水体污染中,油类(油脂类、石油类、亲油性有机溶剂等)已成为重要污染物之一,含油废水对生态环境和人类健康造成了巨大威胁。含油废水广泛存在,涉及于生活餐饮、农业生产、交通运输、化学化工、制造工业、石油工业等诸多领域。随着城市化和工业化进程的不断加快,水体中的油类污染物问题日益突出,受到愈多的重视和关注。传统的油水分离方法如重力分离法、离心分离法、超声波分离法、吸附分离法和膜分离法等都存在效率低或对环境造成二次污染的弊端,对含油废水的处理往往需要较高的成本和能源消耗,这也造成了巨大的经济负担和资源浪费。因此,对于高效低成本的油水分离技术研究具有重要意义。
技术实现要素:3.针对以上不足,本发明的目的是提供一种油水两相的微通道分离方法和微通道分离装置。为实现上述目的,本发明采用的技术方案为:一种用于强化油水分离的微通道分离装置,该微分离装置包括上盖板、下盖板以及依次密封安装在上盖板、下盖饭之间的微分离器-1、微分离器-2。所述上盖板上设置有油水原料混合液的入口孔和油水两相分离后的水相(油相)出口孔,所述下盖板上设置油水两相分离后的油相(水相)出口孔,均为通孔;所述微分离器-1、微分离器-2依次密封安装在上盖板、下盖饭之间,微分离器-1的两端分别与上盖板设置的油水原料混合液入口孔和油水两相分离后的水相(油相)出口孔相连通;微分离器-2的两端分别与分离器-1上对应的油水原料混合液的入口孔、与下盖板上对应的油水两相分离后的油相(水相)出口孔相连通。
4.本发明提供的强化油水两相分离的高效微通道分离装置中,所述微分离器-1由一片微分离板构成或两片以上的微分离板叠加组成,微分离板上设置有与上盖板上对应的油水原料混合液的入口孔、与上盖板上对应的油水两相分离后的水相(油相)的出口孔,入口孔和出口孔均为通孔;微分离板上设有微分离通道,微分离通道的两端分别与油水原料混合液入口孔和油水两相分离后的水相(油相)出口孔相连通。
5.本发明提供的强化油水两相分离的高效微通道分离装置中,所述微分离器-2由一片微分离板构成或两片以上的微分离板叠加组成,微分离板上设置有与分离器-1上对应的油水原料混合液的入口孔、与下盖板上对应的油水两相分离后的油相(水相)出口孔,入口孔为非通孔,出口孔为通孔;微分离板上设有微分离通道,微分离通道端与油水两相分离后的油相(水相)出口孔相连通。
6.本发明提供的强化油水两相分离的高效微通道分离装置中,所述微分离器-1的微分离板上设置有由微通道组成的油水原料混合液分离腔,微通道的表面具有亲水(疏水)性,分离腔起始端分别连接有微分离器-1的油水原料混合液入口孔和油水两相分离后的水
相(油相)出口孔。
7.本发明提供的强化油水两相分离的高效微通道分离装置中,所述微分离器-2的微分离板上设置有由微通道组成的油水原料混合液分离腔,微通道的表面具有疏水(亲水)性,分离腔始端连接有微分离器-2的油水原料混合液入口孔,分离腔终端连接有微分离器-2的油水两相分离后的油相(水相)出口孔。
8.本发明提供的强化油水两相分离的高效微通道分离装置中,所述上盖板、下盖板以及依次密封安装在上盖板、下盖饭之间的微分离器-1和微分离器-2的材质相同,为不锈钢、铜、钛中的任意一种,相邻两个模块间的密封连接均采用真空扩散焊接方式;相邻两个模块间的密封连接具体指模块上除微通道、通孔所占面积之外的其余部分均进行焊接密封。
9.本发明提供的强化油水两相分离的高效微通道分离装置中,所述微通道为蛇形通道或螺旋形通道,当量直径为50~3000 μm、截面形状为圆形或长方形或正方形,入口通孔及出口通孔的当量直径为2~6 mm。
10.本发明提供油水两相的微通道分离方法,所述分离方法使用上述的微通道分离装置,将油水的原料混合液依次经上盖板、微分离器-1和微分离器-2上的通孔,进入微分离器-1和微分离器-2,在微分离器-1和微分离器-2内进行油水两相的分离,分离产物中油相(水相)经微分离器-1和上盖板上的通孔流出微分离装置,水相(油相)经微分离器-2和下盖板上的通孔流出微分离装置。
11.本发明提供的油水两相的微通道分离方法中,所述油水混合液为乳液或油水分层状态,含有油相和水相,所述油相为煤油、柴油、汽油、十二烷、十四烷、十六烷、十八烷等长链烷烃,苯、甲苯、二甲苯、混苯、四氯化碳、二氯甲烷、三氯甲烷等中的至少一种;水相为水或聚乙烯醇、明胶、聚乙二醇、盐酸、硝酸、氢氧化钠水等的水溶液中的至少一种。所述油水混合液进料量为0~200 ml/min,分离选择性为100%。本发明所涉及的油水两相,在所公知的各类油水体系中的油水组成均可应用于本发明。
12.本发明采用一种微通道分离装置,在持续分离过程中,油水两相可在微通道内快速、高效分离,并且在高进料量下可实现100%分离选择性。该微分离装置利用微通道的表面性质和尺寸限域作用,使分离过程更易控,有效提升油水体系的分离效率,降低能耗。最终实现化工分离技术领域的油水两相分离过程强化和设备微型化,极大程度上提高系统的分离效率。
附图说明
13.图1为用于强化油水两相分离的高效微通道分离装置的上盖板结构示意图;图中,1-1为原料混合液的入口通孔;1-2为经微分离器-1分离后的水相(或油相)出口通孔。
14.图2为用于强化油水两相分离的高效微通道分离装置的微分离器-1结构示意图;图中,2-1为原料混合液的入口通孔;2-2为微分离器-1分离后的水相(或油相)出口通孔;2-3为微分离器-1的微分离板。
15.图3为用于强化油水两相分离的高效微通道分离装置的微分离器-2结构示意图;图中,3-1为原料混合液入口孔;3-2为微分离器-2分离后的油相(或水相)出口通孔;3-3为微分离器-2的微分离板。
16.图4为用于强化油水两相分离的高效微通道分离装置的下盖板结构示意图;图中,4-1为经微分离器-2分离后的油相(或水相)出口通孔。
17.图5为用于强化油水分离的微分离装置结构示意图。
具体实施方式
18.以下将参照附图,对本发明的优选实施例进行详细的描述。应当理解,优选实施例仅为了说明本发明,而不是为了限制本发明的保护范围。本发明涉及的是强化油水分离的微通道分离装置的发明设计,实质上是利用微通道的表面性质和尺寸限域作用实现化工分离技术领域的油水两相分离过程强化和设备微型化,提高系统的分离效率。
19.1.图5所示为用于强化油水分离的微分离装置结构示意图的一个示例,该微分离装置由上盖板(图1)、下盖板(图4)以及依次密封安装在上盖板与下盖板之间的微分离器-1(图2)、微分离器-2(图3)组成。
20.2.本发明提供的用于强化油水分离的微分离装置中,所述上盖板上设置有原料混合液的入口通孔(图1,1-1)、经微分离器-1分离后的水相(或油相)出口通孔(图1,1-2)。
21.3.本发明提供的用于强化油水分离的微分离装置中,所述微分离器-1由一片或两片以上的微分离板叠加组成,微分离器-1板上设置有与上盖板上对应的原料混合液的入口通孔(图2,2-1);与上盖板上对应的经微分离器-1分离后水相(或油相)出口通孔(图2,2-2)。
22.4.本发明提供的用于强化油水分离的微分离装置中,所述微反应器-2由一片或两片以上的微分离板叠加组成,微分离器-2板上设置有与微分离器-1板上对应的原料混合液的入口孔(图3,3-1),微分离器-2板上设置有经微分离器-2分离后油相(或水相)出口通孔(图3,3-2)。
23.5.本发明提供的用于强化油水分离的微分离装置中,所述下盖板上设置有与微分离器-2对应的经微分离器-1、微分离器-2分离后的油相(或水相)出口通孔(图4,4-1)。
24.6.本发明提供的用于强化油水分离的微分离装置中,所述微分离器-1(图2)的微分离板上设置有由并行微通道组成的分离腔(图2,2-3),分离腔内设置有微分离器-1的原料混合液入口孔(图2,2-1)和微分离器-1的分离产物出口孔(图2,2-2)。
25.7.本发明提供的用于强化油水分离的微分离装置中,所述微分离器-2(图3)的微分离板上设置有由并行微通道组成的分离腔(图3,3-3),分离腔内设置有微分离器-2的原料混合液入口孔(图3,3-1)和微分离器-2的分离产物出口孔(图3,3-2)。
26.8.本发明提供的用于强化油水分离的微分离装置中,所述上盖板(图1)、微分离器-1(图2)、微分离器-2(图3)及下盖板(图4)的材质相同,可为不锈钢、铜、钛等金属材质中的任意一种,优选为不锈钢材质,所述相邻两个模块间的密封连接均采用真空扩散焊接方式;所述相邻两个模块间的密封连接具体指模块上除微通道、通孔所占面积之外的其余部分均进行焊接密封。
27.9.本发明提供的用于强化油水分离的微分离装置中,所述微通道为蛇形通道或螺旋形通道,优选蛇形通道;当量直径为50~3000 μm,优选为500~1000 μm;截面形状为圆形或长方形或正方形,优选为长方形;入口分布腔和出口集流腔的形状为三角形;入口通孔及出口通孔的当量直径为2~6mm,优选为3~5 mm。
28.10. 图5为本发明中用于微分离装置密封及承载原料混合液进出的整体结构及内部结构常见模式,在具体实施过程中并不限于这种模式,可在以图5为基本结构的基础上进行其它优化改进。
29.11. 图2为本发明中用于分离油水两相的微分离器-1的整体结构及内部结构常见模式,两者在具体实施过程中并不限于这种模式,可在以图2为基本结构的基础上进其它优化改进。
30.12. 图3为本发明中用于分离油水两相的微分离器-2的整体结构及内部结构常见模式,两者在具体实施过程中并不限于这种模式,可在以图3为基本结构的基础上进其它优化改进。
31.实施例1:微分离器-1的微通道具有疏水表面,微通道为蛇形通道,当量直径为500 μm、截面形状为正方形;微分离器-2的微通道具有亲水表面,微通道为蛇形通道,当量直径为500 μm、截面形状为正方形;微分离器-1和微分离器-2的均为不锈钢材质,入口通孔及出口通孔的当量直径为4 mm,分离体系为处于油水分层状态的正己烷/水混合液。
32.将正己烷/水混合溶液经上盖板上的通孔(图1,1-1)、微分离器-1上的通孔(图2,2-1),进料量为100 ml/min,进入微分离器-1和微分离器-2,在微分离器-1和微分离器-2内进行油水两相的分离,分离后的正己烷依次经微分离器-1上的通孔(图2,2-2)、上盖板上的通孔(图1,1-2)流出,分离后的水依次经微分离器-2上的通孔(图3,3-1)、下盖板上的通孔(图4,4-1)流出。
33.经微分离器分离后,分离选择性为100%。
34.实施例2:微分离器-1的微通道具有亲水表面,微通道为螺旋形通道,当量直径为500 μm、截面形状为正方形;微分离器-2的微通道具有疏水表面,微通道为螺旋形通道,当量直径为500 μm、截面形状为正方形;微分离器-1和微分离器-2的均为不锈钢材质,入口通孔及出口通孔的当量直径为4 mm,分离体系为处于乳液状态的甲苯/聚乙烯醇混合液。
35.将甲苯/1wt%聚乙烯醇水溶液混合溶液经上盖板上的通孔(图1,1-1)、微分离器-1上的通孔(图2,2-1),进料量为100 ml/min,进入微分离器-1和微分离器-2,在微分离器-1和微分离器-2内进行油水两相的分离,分离后的聚乙烯醇依次经微分离器-1上的通孔(图2,2-2)、上盖板上的通孔(图1,1-2)流出,分离后的甲苯依次经微分离器-2上的通孔(图3,3-1)、下盖板上的通孔(图4,4-1)流出。
36.经微分离器分离后,分离选择性为100%。
37.实施例3:微分离器-1的微通道具有亲水表面,微通道为蛇形通道,当量直径为1000 μm、截面形状为圆形;微分离器-2的微通道具有疏水表面,微通道为蛇形通道,当量直径为1000 μm、截面形状为圆形;微分离器-1和微分离器-2的均为金属钛,入口通孔及出口通孔的当量直径为3 mm,分离体系为处于油水分层状态的三氯甲烷/硝酸水溶液混合液。
38.将三氯甲烷/10 wt%硝酸水溶液混合溶液经上盖板上的通孔(图1,1-1)、微分离器-1上的通孔(图2,2-1),进料量为150 ml/min,进入微分离器-1和微分离器-2,在微分离器-1和微分离器-2内进行油水两相的分离,分离后的硝酸水溶液依次经微分离器-1上的通
孔(图2,2-2)、上盖板上的通孔(图1,1-2)流出,分离后的三氯甲烷依次经微分离器-2上的通孔(图3,3-1)、下盖板上的通孔(图4,4-1)流出。
39.经微分离器分离后,分离选择性为100%。
40.本发明未述及之处适用于现有技术。