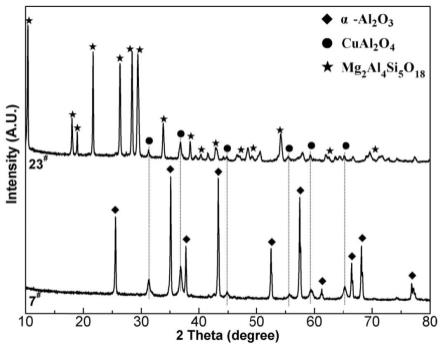
一种陶瓷负载型au基含铜氧化物催化剂及其制备和应用
技术领域
1.本发明属于催化剂技术领域,更具体地,涉及一种陶瓷负载型au基含铜氧化物催化剂及其制备和应用。
背景技术:2.以可再生的生物质能源代替化石能源生产清洁燃料和附加值化学品是节能减排的重要方向。我国是生物质资源大国,由生物质发酵制得的生物乙醇年产量超30亿升且逐年增长,其价格已低于乙烯、汽油等石化产品。发展绿色的乙醇催化转化制备化学品来替代传统高污染的石化工艺路线将助力国家“双碳”战略目标的实现。乙醇气相氧化可以得到乙醛、乙酸和乙酸乙酯等附加值化学品,其中乙醛是关键的中间体,乙酸和乙酸乙酯是其下游产品。目前这些化学品的工业生产主要是采用化石能源为原料的均相催化工艺,均存在不可持续性、腐蚀污染严重、催化剂难以分离回收、设备成本高等缺点,需要发展绿色可持续的生物乙醇气固相催化氧化工艺来实现产业的技术革新。
3.乙醇气相催化脱氢制乙醛可通过无氧脱氢和氧化脱氢两种途径进行。铜催化的乙醇无氧脱氢制乙醛因反应选择性高成为研究的一个热点(green chem.2021,23,7902),但该反应是吸热反应,较高的反应温度(》280℃)会导致铜基催化剂烧结和积碳失活,催化剂面临活性和稳定性不可兼得的挑战。相反的,乙醇氧化脱氢制乙醛是放热反应,可有效避免积碳且在较低的温度(≤250℃)下能获得高催化活性,放出的热量也可以循环利用,但是很难获得高乙醛产率,催化剂活性和选择性的矛盾仍然存在。目前工业上部分采用的泡沫银催化氧化乙醇制乙醛工艺存在反应温度高(》400℃)、乙醛单程产率低(《30%)和催化剂寿命短等缺点,迫切需要发展高效、稳定的乙醇气相氧化脱氢制乙醛催化剂。
4.负载型纳米金催化剂在乙醇气相氧化脱氢反应中表现出较高的催化活性和选择性,特别是liu等报道的au/mgcucr2o4催化剂于250℃能获得高达95%的乙醛产率且连续运行500小时无失活(j.am.chem.soc.2013,135,14032;j.catal.2017,347,45)。纳米金与含铜尖晶石载体之间的au-cu协同催化作用是其高效和高稳定性的关键原因。这种金属与载体之间的au-cu协同催化比常见的aucu合金协同催化乙醇氧化更加高效,已被不同研究者所证实(nano research,2016,9,2681;chemcatchem,2017,9,1363)。为了解决au/mgcucr2o4催化剂含有害金属cr和低温(200℃)活性不高的问题,中国发明专利cn109569647a报道了一种不含cr的含铜复合氧化物(尖晶石型或钙钛矿型)负载金催化剂,于200℃就能获得》90%的乙醛产率且连续反应200小时不失活,显示出良好的应用前景。但是这些负载型au基含铜尖晶石或钙钛矿粉末因具有较低的比表面积(《10m2/g)和较高au负载量(~1wt%),催化剂成型困难。压片或挤条成型易造成催化剂成本高、活性中心利用率低、易破碎粉化等缺点,而硅溶胶或铝溶胶涂覆成型易导致酸性sio2或al2o3催化乙醇脱水副反应。因此需要开发成本低、机械强度高、au-cu协同活性位利用率高、无脱水副反应的成型催化剂,以实现该工艺的工业化应用。
技术实现要素:5.针对现有技术的缺陷,本发明的目的在于提供一种陶瓷负载型au基含铜氧化物催化剂及其制备和应用,以解决现有技术用于乙醇气相氧化的含铜金属氧化物负载au催化剂成型困难、压片或挤条成型易造成催化剂成本高、活性中心利用率低、易破碎粉化等的技术问题。
6.为实现上述目的,本发明提供了一种陶瓷负载型au基含铜氧化物催化剂,包括陶瓷载体,还包括负载在所述陶瓷载体表面的含铜复合氧化物活性组分cum
x
oy和纳米au活性组分,按照质量份计,所述催化剂中各组分的质量份数为:陶瓷载体79.8~96.99份,含铜复合氧化物活性组分cum
xoy 3~20份,纳米au活性组分0.01~0.2份;
7.其中所述陶瓷载体为球形α-al2o3陶瓷、α-al2o3泡沫陶瓷、堇青石蜂窝陶瓷、sic泡沫陶瓷、zro2泡沫陶瓷中的一种;
8.所述m对应的金属元素为mg、al、mn、fe、co、ni、zn、la或ce中的一种或两种;所述x=1~11;所述y根据各金属元素化的合价取值;所述催化剂中金属阳离子cu同时包含+1价和+2价,或者均为+1价。
9.优选地,所述球形α-al2o3陶瓷为具有γ-al2o3相的球形活性氧化铝颗粒烧结得到的陶瓷。
10.按照本发明的另一个方面,提供了一种所述的陶瓷负载型au基含铜氧化物催化剂的制备方法,包括如下步骤:通过溶液浸渍-干燥处理将铜和m金属盐前驱体负载到所述陶瓷载体表面,然后在空气气氛下焙烧得到陶瓷负载型含铜氧化物,再通过尿素均匀沉积-沉淀法负载金,最终得到陶瓷负载型au基含铜氧化物催化剂。
11.优选地,所述的制备方法,包括如下步骤:
12.(1)将陶瓷载体浸入含有铜盐、m金属盐和柠檬酸的混合溶液中,静置0.5~3h后过滤,于80~150℃干燥,重复浸渍-干燥步骤0~2次,得到负载有铜和m金属盐前驱体的载体;
13.(2)将步骤(1)得到的负载有铜和m金属盐前驱体的载体于600~1000℃空气气氛下焙烧5~20h,用酸浸泡除去可溶性氧化物,干燥后得到陶瓷负载型含铜氧化物;
14.(3)将步骤(2)得到的陶瓷负载型含铜氧化物与氯金酸水溶液于90~100℃通过尿素沉积-沉淀负载金,洗涤、干燥后于300~350℃空气气氛中焙烧3~6h,得到陶瓷负载型au基含铜氧化物催化剂。
15.优选地,所述陶瓷载体为球形α-al2o3陶瓷,其通过如下方法获得:将具有γ-al2o3相的球形活性氧化铝颗粒在700~1000℃烧结5~20h后得到。
16.优选地,所述陶瓷载体为堇青石蜂窝陶瓷、α-al2o3泡沫陶瓷、sic泡沫陶瓷或zro2泡沫陶瓷,其使用前均进行预处理以除去表面吸附的杂质,所述预处理包括如下步骤:将各陶瓷用水冲洗后于200~800℃空气气氛中焙烧处理2~5h得到对应的所述陶瓷载体。
17.优选地,步骤(1)所述混合溶液中的铜盐和m金属盐的总浓度为0.5~2mol/l,铜盐和m金属盐的总摩尔数与柠檬酸的摩尔数之比为1:0~0.5,所述陶瓷载体质量与所述混合溶液体积之比为0.2~1.0g/ml。
18.优选地,步骤(3)所述的氯金酸溶液浓度为0.5~5mmol/l,所述陶瓷负载型au基含铜氧化物催化剂中理论au负载量为0.02~0.2wt%。
19.按照本发明的另一个方面,提供了一种所述的陶瓷负载型au基含铜氧化物催化剂
在乙醇气相氧化脱氢反应中的应用。
20.优选地,所述的反应在固定床反应器中连续进行,所述的乙醇气相氧化脱氢反应条件为:乙醇为无水乙醇或50~95%含水生物乙醇,液体进料的空速为0.1~1.0ml/g
cat
/h,氧气与乙醇的摩尔比为1~5:1,气时空速为300~3000ml/g
cat
/h,反应温度为150~250℃。
21.总体而言,通过本发明所构思的以上技术方案与现有技术相比,具有以下有益效果:
22.(1)本发明提供了一种陶瓷负载型au基含铜氧化物催化剂,包括陶瓷载体,还包括负载在所述陶瓷载体表面的含铜复合氧化物活性组分cum
x
oy和纳米au活性组分。采用孔道丰富、机械强度高的成型活性氧化铝或陶瓷,使含铜复合氧化物均匀且稳定地分散在陶瓷载体上,显著地抑制了载体酸性位,这样的结构特点使得较少量的纳米au就可与表面的含铜复合氧化物形成有效的au
0-cu
+
协同催化活性位,最终使得陶瓷负载型au基含铜氧化物催化剂可以作为一种更易工业化应用的、高效高稳定性的乙醇气相氧化脱氢成型催化剂。
23.(2)本发明所述催化剂通过载体焙烧处理、金属铜盐溶液浸渍、焙烧成相、沉积沉淀负载au等步骤制备得到,采用孔道丰富、机械强度高的成型活性氧化铝或陶瓷来浸渍铜和金属盐溶液,通过控制焙烧温度、浸渍溶液组成浓度及浸渍次数来调控含铜复合氧化物负载量和表面cu
+
比例,使含铜复合氧化物均匀且稳定地分散在陶瓷载体上,制备方法简便、可控性强、重现性好,有效地降低了生产成本。
24.(3)本发明通过调控催化剂组成和反应工艺条件可以实现乙醛、乙酸和乙酸乙酯选择性的调控,且催化剂具有优异的稳定性,催化活性和选择性能够至少稳定200h。适合于生物乙醇高值化利用的工业化生产。
25.(4)本发明的陶瓷负载型au基含铜氧化物催化剂au活性组分含量为0.01~0.2wt%,即能够表现出优异的催化活性,相对于现有技术的含铜金属氧化物负载au催化剂的au负载量大有降低,显著降低了催化剂的成本。
附图说明
26.图1是典型催化剂7
#
和23
#
的xrd图。
27.图2是其它典型催化剂和载体的xrd图。
28.图3是典型催化剂和相应负载金前载体的h
2-tpr结果。
29.图4是典型催化剂7
#
和23
#
的tem图。
30.图5是典型催化剂7
#
和23
#
与对比催化剂c
#
和f
#
的xps图。
具体实施方式
31.为了使本发明的目的、技术方案及优点更加清楚明白,以下结合附图及实施例,对本发明进行进一步详细说明。应当理解,此处所描述的具体实施例仅仅用以解释本发明,并不用于限定本发明。
32.本发明提供的一种陶瓷负载型au基含铜氧化物催化剂,包括陶瓷载体,还包括负载在所述陶瓷载体表面的含铜复合氧化物活性组分cum
x
oy和纳米au活性组分,按照质量份计,所述催化剂中各组分的质量份数为:陶瓷载体79.8~96.99份,含铜复合氧化物活性组分cum
xoy 3~20份,纳米au活性组分0.01~0.2份;其中所述陶瓷载体为球形α-al2o3陶瓷、
α-al2o3泡沫陶瓷、堇青石蜂窝陶瓷、sic泡沫陶瓷、zro2泡沫陶瓷中的一种;所述m对应的金属元素为mg、al、mn、fe、co、ni、zn、la或ce中的一种或两种;所述x=1~11;所述y根据各金属元素化合价取值;所述催化剂中金属阳离子cu同时包含+1价和+2价,或者均为+1价。
33.较佳实施例中,所述陶瓷为球形α-al2o3陶瓷、堇青石蜂窝陶瓷、sic泡沫陶瓷或zro2泡沫陶瓷;所述m对应的金属元素为al、mn、fe、co和ce中的一种或两种;较佳的x取值为1~7。更佳实施例中,所述m对应的金属元素为al、fe、ce中的一种或两种;较佳的x取值为1~5。从陶瓷成本考虑,较佳的载体为α-al2o3陶瓷、堇青石蜂窝陶瓷或sic泡沫陶瓷。zro2泡沫陶瓷成本较其它载体高,但实验表明其与sic泡沫陶瓷均表现出了较为突出的乙酸选择性。
34.本发明所述的陶瓷负载型au基含铜氧化物催化剂可以包含不会对其催化性能产生实质影响的其它成分,例如由于使用商业载体、可溶性金属盐等而引入的少量杂质。
35.一些实施例中,所述球形α-al2o3陶瓷的前体为具有γ-al2o3物相的商用活性氧化铝球形颗粒。所述球形α-al2o3陶瓷为通过具有γ-al2o3相的球形活性氧化铝颗粒烧结得到的陶瓷,烧结使得活性氧化铝颗粒转化为惰性的球形α-al2o3陶瓷来抑制催化剂应用时表现出酸催化的乙醇脱水副反应。较佳实施例中,所述球形γ-al2o3活性颗粒的直径为3~8mm,比表面积为150~350m2/g,平均孔径5~20nm,孔容0.3~0.7ml/g。
36.经实验证实,本发明还可以采用α-al2o3泡沫陶瓷、堇青石蜂窝陶瓷、sic泡沫陶瓷或zro2泡沫陶瓷作为陶瓷载体,陶瓷载体可以为各种形状,比如长方体、正方体、不规则块体、柱体或球体等,任意一个方向上的尺寸不小于10mm,孔隙率70~90%,比表面积1~10m2/g。优选采用成分相对惰性的载体种类。
37.本发明较佳实施例中,陶瓷载体包括α-al2o3泡沫陶瓷、堇青石蜂窝陶瓷、sic泡沫陶瓷或zro2泡沫陶瓷,在使用前均进行水洗并焙烧预处理,以去除表面吸附的杂质。
38.本发明还提供了所述的陶瓷负载型au基含铜氧化物催化剂的制备方法,包括如下步骤:通过溶液浸渍-干燥处理将铜和m金属盐前驱体负载到所述陶瓷载体表面,然后在空气气氛下焙烧得到陶瓷负载型含铜氧化物,再通过尿素均匀沉积-沉淀法负载金,最终得到陶瓷负载型au基含铜氧化物催化剂。该方法通过控制焙烧温度、浸渍液组成浓度及浸渍-干燥次数,可以提高含铜氧化物的负载量和表面cu
+
/cu
2+
的比例,从而形成更多的au
0-cu
+
协同催化活性位来更有效地促进乙醇气相氧化脱氢反应。
39.一些实施例中,该制备方法具体包括如下步骤:
40.(1)将所述陶瓷载体浸入含有铜盐、m金属盐和柠檬酸的混合溶液中,静置0.5~3h后过滤,于80~150℃干燥,重复浸渍-干燥步骤0~2次,得到负载有铜和m金属盐前驱体的载体;
41.(2)将步骤(1)得到的负载有铜和m金属盐前驱体的载体于600~1000℃空气气氛下焙烧5~20h,用稀酸浸泡除去可溶性氧化物,干燥后得到陶瓷负载型含铜氧化物;
42.(3)将步骤(2)得到的陶瓷负载型含铜氧化物与氯金酸水溶液于90~100℃通过尿素沉积-沉淀负载金,洗涤、干燥后于300~350℃空气气氛中焙烧3~6h,最终得到陶瓷负载型au基含铜氧化物催化剂。
43.上述制备方法中,所述的铜和m金属前驱体可以是硝酸盐、乙酸盐、乙酰丙酮盐等可溶性盐。所述铜和m金属前驱体混合溶液中前驱体的浓度和比例可根据所需催化剂中含
铜氧化物组成和负载量进行确定。
44.一些实施例中,步骤(1)所述混合溶液的铜盐和m金属盐的总浓度为0.5~2mol/l,铜盐和m金属盐的总摩尔数与柠檬酸的摩尔数之比为1:0~0.5,所述陶瓷载体质量与混合溶液体积之比为0.2~1.0g/ml。步骤(2)所述稀酸可以为稀硝酸,稀盐酸等,其浓度为1~5mol/l。步骤(3)所述的氯金酸溶液浓度为0.5~5mmol/l,所述陶瓷负载型au基含铜氧化物催化剂中理论au负载量为0.02~0.2wt%。
45.一些实施例中,步骤(3)具体为:将步骤(2)得到的陶瓷负载型含铜氧化物与氯金酸水溶液和尿素水溶液混合,于90~100℃反应4~6小时,用去离子水充分淋洗固体表面后,于300~350℃空气气氛中焙烧3~6h,最终得到陶瓷负载型au基含铜氧化物催化剂。
46.一些实施例中,所述陶瓷为球形α-al2o3陶瓷时,其通过如下方法获得:将具有γ-al2o3相的球形活性氧化铝颗粒在700~1000℃内烧结5~20h后得到。所述陶瓷为堇青石蜂窝陶瓷、α-al2o3泡沫陶瓷、sic泡沫陶瓷、zro2泡沫陶瓷时,其使用前进行预处理以去除表面吸附杂质,所述预处理包括如下步骤:将陶瓷用水冲洗后在200~800℃空气气氛中焙烧处理3~5h得到所述陶瓷载体。
47.本发明所述的陶瓷负载型au基含铜氧化物催化剂可用于乙醇气相氧化脱氢反应。一些实施例中,所述的反应在固定床反应器中连续进行,所述的乙醇气相氧化脱氢反应条件为:乙醇为无水乙醇或50~95%含水生物乙醇,液体进料的空速为0.1~1.0ml/g
cat
/h,氧气与乙醇的摩尔比为1~5:1,气时空速为300~3000ml/g
cat
/h,反应温度为150~250℃。调整乙醇含水量、进料空速、气时空速、反应温度可以实现乙醇转化率和乙醛、乙酸、乙酸乙酯选择性的调控,催化活性和选择性能够至少稳定200h。
48.如无特别说明,本技术的实施例中的原料均通过商业途径购买。其中乙醇是95%的含水生物乙醇;活性γ-al2o3小球的直径为3~5mm,比表面积230m2/g,平均孔径10nm,孔容0.5ml/g;堇青石蜂窝陶瓷为镁铝硅复合氧化物,块体尺寸100mm
×
100mm
×
40mm,比表面积2.7m2/g,孔密度25孔/cm2。α-al2o3泡沫陶瓷、sic泡沫陶瓷和zro2泡沫陶瓷的圆柱状块体尺寸均为18mm
×
22mm,孔隙率70~90%,比表面积1~10m2/g。
49.实施例1
50.以球形活性氧化铝为载体制备催化剂:
51.以表1中的序号1为例,将活性氧化铝小球于700℃焙烧5h;将摩尔比为3:1:8:4的硝酸镁/硝酸铜/硝酸铝/柠檬酸在去离子水中溶解配成总浓度为1.5mol/l的混合溶液60ml,将50g焙烧后的氧化铝加入混合盐溶液于室温浸渍1h,抽滤后将小球颗粒置于120℃干燥3h,然后置于马弗炉900℃焙烧5h,冷却后将小球置于5mol/l稀硝酸中浸泡2h,抽滤洗至滤液为中性后于120℃干燥3h;将冷至室温的小球颗粒加入浓度为1.2mmol/l的haucl4溶液,使理论au负载量为0.05wt%,再加入浓度为1mol/l的尿素水溶液使尿素与au摩尔比为100,升温至90℃保持5h,冷却后过滤并用去离子水淋洗5~10次,将小球颗粒置于350℃马弗炉焙烧5h,即得到所述成型催化剂1
#
,其化学表达式记为au/mg3cual8o
16
/al2o
3-700-1-900-0.05,其中“700”表示活性氧化铝的焙烧温度为700℃,“1”表示浸渍次数为1,“900”表示浸渍后的焙烧温度为900℃,“0.05”表示金活性组分的理论负载量。
52.按照以上步骤,调整焙烧温度、浸渍液组成浓度、浸渍次数、氯金酸用量等参数,得到序号2~17一系列催化剂,记为催化剂2
#
~17
#
,如表1所示,其化学表达式au/cum
x
oy/
al2o
3-t
1-x-t
2-y,其中t1和t2分别表示载体焙烧温度和浸渍后焙烧温度,x表示浸渍次数,y表示理论au负载量
×
100。其中,浸渍次数为“2”表示第一次浸渍和干燥步骤完成之后,再重复一次前面的浸渍和干燥步骤,以提高金属氧化物负载量,以此类推。
53.以堇青石蜂窝陶瓷及三种泡沫陶瓷为载体制备催化剂:
54.以表1中的序号18为例,将堇青石蜂窝陶瓷(简称为cor)水洗后于800℃焙烧5h后切割成20mm
×
20mm
×
40mm小块体;将摩尔比为1:2:1的硝酸铜/硝酸铝/柠檬酸在去离子水中溶解配成总浓度为1.5mol/l的混合溶液100ml,将切割后的四小块cor载体浸入混合溶液于室温浸渍1h,吹出孔中残留的液体后置于120℃干燥1h,再进行一次浸渍-干燥后置于马弗炉900℃焙烧5h,冷却后将块体置于5mol/l稀硝酸中浸泡1h,水洗后于120℃干燥2h;将冷至室温的块体浸入浓度为0.5mmol/l的haucl4溶液,使理论au负载量为0.05wt%,再加入浓度为1mol/l的尿素水溶液使尿素与au摩尔比为100,升温至90℃保持5h,水洗后将块体置于350℃马弗炉焙烧5h,即得到所述成型催化剂18
#
,其化学表达式记为au/cual2o4/cor-800-2-900-0.05。
55.按照以上步骤,调整焙烧温度、浸渍液组成浓度、浸渍次数、氯金酸用量等参数,得到序号19~27系列催化剂,记为催化剂19
#
~27
#
,如表1所示,其化学表达式au/cum
x
oy/cor-t
1-x-t
2-y,其中t1和t2分别表示载体焙烧温度和浸渍后焙烧温度,x表示浸渍次数,y表示理论au负载量
×
100。
56.将α-al2o3泡沫陶瓷(简称为α-al2o3)、sic泡沫陶瓷(简称为sic)和zro2泡沫陶瓷(简称为zro2)水洗后于200℃焙烧5h,其它制备条件与催化剂23
#
相同,得到催化剂28
#
~30
#
,如表所示,其化学表达式分别为au/cual2o4/α-al2o
3-200-3-700-0.05,au/cual2o4/sic-200-3-700-0.05,au/cual2o4/zro
2-200-3-700-0.05。
57.催化剂表征:
58.对编号为7
#
、11
#
、12
#
、13
#
、20
#
、23
#
、25
#
、26
#
八个催化剂及对应的al2o
3-900和cor-500载体进行了xrd表征,其中7
#
和23
#
两个催化剂的xrd结果如图1所示,其它样品的xrd结果如图2所示。
59.需要说明的是,编号为7
#
、9
#
、10
#
和20
#
四个催化剂,在溶液浸渍步骤中没有加入除铜盐以外的其它金属盐,但是从7
#
催化剂的xrd结果可以看出,有较大量的cual2o4尖晶石物相存在,其衍射峰比11
#
~13
#
催化剂(在溶液浸渍步骤中分别加入了除铜盐以外的al、mn、fe金属盐)出现的cum2o4(m=al,mn,fe)尖晶石衍射峰更强,这表明活性氧化铝载体负载铜盐后在高温焙烧过程中表面氧化铝会与氧化铜物种发生反应形成cual2o4尖晶石,同时氧化铝载体进一步地向惰性的陶瓷α-al2o3相转变。为了区别,将7
#
、9
#
和10
#
三个催化剂的化学表达式记为au/cual2o4@al2o
3-t
1-x-t
2-y。相反的,从20
#
催化剂(载体为堇青石蜂窝陶瓷)的xrd结果可以看出,没有cual2o4尖晶石物相生成,只有少量cuo物相存在,这表明堇青石蜂窝陶瓷载体中所含的铝氧化物非常稳定,不能与氧化铜物种发生反应形成cual2o4尖晶石。从23
#
和25
#
催化剂的xrd可以看出,分别存在明显的cual2o4和cumn2o4尖晶石结构,而26
#
催化剂同时存在cufe2o4和fe2o3相。
60.对编号为7
#
、11
#
、12
#
、13
#
、16
#
、23
#
、25
#
、26
#
、27
#
九个催化剂在负载au前后分别进行了h
2-tpr表征,如图3所示(虚线为负载au前,实线为负载au后),结果显示负载au后cum
x
oy物种的还原峰均向低温方向移动,表明纳米au颗粒高度分散在催化剂表面并与cum
x
oy物种发
生强相互作用,纳米au的氢溢流效应导致cum
x
oy物种更加容易被还原。相对球形氧化铝陶瓷负载催化剂而言,堇青石蜂窝陶瓷载体上cum
x
oy物种的还原峰在负载纳米au后向低温移动更加显著。
61.对编号为7
#
和23
#
催化剂进行了tem表征,如图4所示,结果表明cual2o4尖晶石呈现为结构不规则的纳米块体,均匀分布在陶瓷载体表面上,纳米au平均直径~5nm,高度分散在cual2o4颗粒和载体表面。相对而言,由于堇青石蜂窝陶瓷的比表面积较小,堇青石蜂窝陶瓷载体上纳米au颗粒和cual2o4尖晶石颗粒更加密集、相互作用更强,这与上述的h
2-tpr表征结果相一致。
62.对编号为7
#
和23
#
催化剂还进行了xps表征,如图5所示,两个催化剂表面均存在较多的cu
+
物种,cu
+
/cu摩尔比~21%。这可能是由于浸渍到载体表面的柠檬酸在焙烧过程中会部分碳化并具有一定的还原性,将cum
x
oy表面的铜物种部分还原至cu
+
物种,从而增加了催化剂表面cu
+
含量,有利于提高au
0-cu
+
协同催化活性。
63.另外,cum
x
oy物种和纳米au的实际负载量列于表2。结果表明,以球形氧化铝为载体负载含铜氧化物时,浸渍一次效果较好,增加浸渍次数cum
x
oy复合氧化物的负载量增加不明显,而au的实际负载量反而下降(1
#
vs.2
#
、7
#
vs.10
#
);但是以堇青石蜂窝陶瓷为载体负载含铜氧化物时,增加浸渍次数cum
x
oy复合氧化物的负载量明显增加,浸渍三次负载量趋于稳定。
64.表1
65.[0066][0067]
实施例2
[0068]
催化剂用于乙醇气相氧化脱氢反应:
[0069]
实施例1制备的序号1~30的催化剂1
#
~催化剂30
#
,用于乙醇气相氧化脱氢反应,在反应温度175~225℃,气时空速300~1000h-1
,乙醇进料流速1.2~1.5ml/h,o2/乙醇摩尔比~2,将乙醇和空气通入载有10~20g所述催化剂的固定床反应器,发生氧化脱氢反应,生成乙醛(ac)为主产物,乙酸(aa)和乙酸乙酯(et)为联产物,乙醚和co2为副产物。
[0070]
每个温度下反应稳定后,乙醇转化率和产物选择性均利用气相色谱在线分析。反应结果如表2所示,通过调控催化剂的组成、催化剂的制备条件及反应条件(包括反应温度、进料流速和气时空速)可以调控催化剂的活性和选择性。
[0071]
对于球形α-al2o3陶瓷负载的催化剂1
#
~17
#
来说,在较低的乙醇进样流速和较高
的气时空速条件下,于低温(≤200℃)可以获得较高的乙醛选择性(83~97%);在较高的乙醇进样流速和较低的气时空速条件下,有利于提高乙酸乙酯的选择性(12~20%);在225℃时co2选择性低于5%的情况下乙酸选择性可达40%。催化剂7
#
于200℃能获得90%的乙醇转化率和97%的乙醛、乙酸、乙酸乙酯综合选择性,co2选择性只有3%。
[0072]
对于堇青石蜂窝陶瓷负载的催化剂18
#
~27
#
来说,在较低的乙醇进样流速和较高的气时空速条件下,于低温(≤175℃)可以获得很高的乙醛选择性(91~98%);在较高的乙醇进样流速和较低的气时空速条件下,有利于提高较低温度(≤200℃)下的乙酸选择性(14~58%)。催化剂23
#
于200℃能获得93%的乙醇转化率和95%的乙醛、乙酸、乙酸乙酯综合选择性,co2选择性只有2%;催化剂27
#
于200℃能获得96%的乙醇转化率和93%的乙醛、乙酸、乙酸乙酯综合选择性,co2选择性只有5%。
[0073]
对于三种泡沫陶瓷负载的催化剂28
#
~30
#
来说,乙酸的选择性明显提高,特别是以sic和zro2泡沫陶瓷为载体时,催化剂于200℃能获得88~92%的乙醇转化率和80~86%的乙酸选择性,co2选择性均只有3%。
[0074]
需要说明的是,乙醛(ac)、乙酸乙酯(et)和乙酸(aa)的沸点分别是~21℃、77℃和118℃,差异比较显著有利于产物分离,在工业生产中可以根据需要来选择乙醛联产乙酸乙酯或者乙醛联产乙酸的催化剂。
[0075]
表2
[0076][0077][0078]
对比例1
[0079]
对比催化剂的制备:
[0080]
针对上述实施例1中的催化剂7
#
,采用其未负载au的载体cual2o4@al2o
3-900-1-900为对比催化剂a
#
,采用900℃焙烧后的al2o
3-900载体直接负载0.05wt%的au作为对比催化剂b
#
(化学表达式为au/al2o
3-900-0.05),采用浸渍液不加柠檬酸而其它条件相同的制备条件制得了对比催化剂c
#
(化学表达式为au/cual2o4@al2o
3-900-1-900-0.05-ii)。
[0081]
针对上述实施例1中的催化剂23
#
,采用其未负载au的载体cual2o4/cor-500-3-700为对比催化剂d
#
,采用500℃焙烧后的cor-500载体直接负载0.05wt%的au作为对比催化剂e
#
(化学表达式为au/cor-500-0.05),采用浸渍液不加柠檬酸而其它条件相同的制备条件制得了对比催化剂f
#
(化学表达式为au/cual2o4/cor-500-3-700-0.05-ii)。
[0082]
对比催化剂用于乙醇气相氧化脱氢反应:
[0083]
采用以上对比催化剂a
#
~f
#
进行乙醇气相氧化脱氢反应,反应条件与实施例2相同,结果如表3所示。
[0084]
表3
[0085][0086]
表3的数据显示,不含au的陶瓷负载含铜氧化物的催化活性很低,而不含cum
x
oy的陶瓷负载纳米au的催化活性也较低,这表明纳米au和含铜氧化物必须同时存在才能获得较高的催化活性,充分证明了au-cu协同催化对乙醇气相氧化脱氢反应的重要性。对比实施例2的催化剂7
#
与表3中的催化剂c
#
,以及催化剂23
#
与催化剂f
#
的催化活性结果,可以看出制备催化剂时浸渍液中添加柠檬酸有助于提高催化活性,这可以从xps结果得到解释,如图5所示,不添加柠檬酸的催化剂c
#
和f
#
表面cu
+
物种明显少于相应的催化剂7
#
和23
#
,充分证明了浸渍液中添加柠檬酸可以增加负载的cum
x
oy复合氧化物中cu
+
缺陷位,从而增加au
0-cu
+
协同催化活性位并增强au-cu协同催化作用。
[0087]
实施例3
[0088]
以市售95%的生物乙醇为原料配制含水质量百分比为15%、25%和50%的生物乙醇水溶液,采用7
#
催化剂au/cual2o4@al2o
3-900-ca-900-0.05进行乙醇气相氧化脱氢反应,反应条件与实施例2相同,结果如表4所示。
[0089]
表4
[0090][0091]
表4的数据显示,随着乙醇中含水量升高,乙酸选择性明显提高。另外,催化剂7
#
在含水25wt%的生物乙醇连续进样反应200h后,反应温度为175℃时乙醇转化率保持为79%,反应温度为200℃时乙醇转化率保持为97%,选择性基本不变;催化剂23
#
在含水15wt%的生物乙醇连续进样反应200h后,反应温度为175℃时乙醇转化率保持为73%,乙醛选择性保持为95%,反应温度为200℃时乙醇转化率保持为98%,乙醛选择性为50%,乙酸选择性为40%,co2选择性为3%。这些结果充分证明了本发明的陶瓷负载型au基含铜氧化物催化剂具有良好的催化稳定性。
[0092]
专利cn109569647a公开的一种乙醇气相氧化制乙醛的催化剂,将非铬的可变价金属b引入含铜氧化物载体,调变载体的氧化还原特性,形成au-cu-b三个活性中心之间的协同作用,促进分子氧和乙醇在低温下的活化,抑制乙醛的深度氧化。该专利文献为本技术发明人前期的工作成果,该催化剂在气相氧化制乙醛应用上表现出了很高的选择性和乙醇转化率,然而由于该催化剂为纳米粉体材料,在工业化应用时成型困难,容易导致催化剂成本较高、活性位利用率低、易破碎粉化等缺点。为了解决前述工作存在的这一技术问题,本技术发明人试图制备一种块体催化剂,最初尝试采用硅溶胶或铝溶胶涂覆方法,直接将前述粉体催化剂负载于载体表面,然而实验发现,硅溶胶或铝溶胶涂覆直接成型制备的催化剂易导致酸性sio2或al2o3催化乙醇脱水副反应,催化选择性和效率较低。进而提出采用浸渍法,将载体浸渍在含有铜盐和m金属盐前驱体溶液中,然后干燥-焙烧-尿素沉淀负载金,这一制备方法并非直接将上述专利中的纳米粉体催化剂负载在载体上,而是重新制备具有完全不同的结构和组成的au基含铜金属氧化物成型催化剂。因此,本发明提出的一种用于乙醇气相氧化的陶瓷负载型au基含铜氧化物催化剂,并非是简单地将前面的纳米粉体催化剂负载于陶瓷载体表面,而是在催化剂的组成(包括含铜金属氧化物中的元素的种类以及配比)、结构上已经与前述文献中粉体催化剂存在根本的不同。前述专利文献中粉体催化剂为采用低温燃烧法制备得到,而本发明采用浸渍-焙烧法制备得到,不同的制备方法得到的金属氧化物结构完全不同。前述文献中通过低温燃烧法制备得到的粉体催化剂均为尖晶石或钙钛矿结构,而本发明通过浸渍-焙烧制备得到的陶瓷负载型含铜金属氧化物只有采用球形α-氧化铝陶瓷作为载体,且金属前驱体溶液中不含有铝离子时,浸渍-焙烧能够原位形成cual2o4尖晶石,其他载体或其他前驱体溶液浸渍-焙烧得到的金属氧化物多为普通的金属混合氧化物,并不具有唯一的尖晶石结构。不同的催化剂组成和结构使得其用于乙醇氧化的催化效果不能预期。第三,与前述文献仅能够高选择性制备乙醛不同,本发明提出的陶瓷负载型au基含铜氧化物催化剂在用于乙醇气相氧化时能够同时制备三种产物,乙醛、乙酸乙酯和乙酸的沸点分别是~21℃、77℃和118℃,差异比较显著有利于产物分离,在工业生产中可以根据需要来选择乙醛联产乙酸乙酯或者乙醛联产乙酸。第四,本发明通过实验发
现,不同的载体、不同的金属氧化物组成其催化选择性和催化活性各不相同,且差异较大。工业生产中可根据生产需要,选择相应的载体种类获得需求产品。比如采用球形α-氧化铝陶瓷作为载体时,负载cual2o4(6
#
,7
#
,11
#
)、cumn2o4(12
#
)、cufe2o4(13
#
)、cuco2o4(14
#
)、cuce2o5(17
#
)复合氧化物的催化剂比负载前述文献中具有较高活性的mg3cual8o
16
(1
#
~3
#
)和mg3cufe8o
16
(4
#
)复合氧化物的催化剂催化活性更高;采用堇青石蜂窝陶瓷作为载体时,负载cual2o4(23
#
,24
#
)和cuce2o5(27
#
)复合氧化物的催化剂比负载其它复合氧化物的催化剂的催化效果更好;再比如,采用sic泡沫陶瓷和zro2泡沫陶瓷负载cual2o4复合氧化物的催化剂(29
#
,30
#
)比其它催化剂具有较高的乙酸选择性。第五,实验中还发现,球形活性氧化铝前体中二氧化硅的含量不宜太高,否则制备得到的球形α-al2o3陶瓷负载催化剂其催化性能不佳,有较多的乙醇脱水副产物。一般而言,本发明球形α-al2o3陶瓷载体中二氧化硅的含量应低于1%。
[0093]
本领域的技术人员容易理解,以上所述仅为本发明的较佳实施例而已,并不用以限制本发明,凡在本发明的精神和原则之内所作的任何修改、等同替换和改进等,均应包含在本发明的保护范围之内。