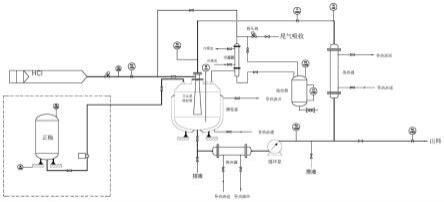
1.本技术涉及化工领域,更具体来说涉及一种适用于以连续方式进行酸解反应的循环反应器以及使用该反应器制备乙烯利的方法。
背景技术:2.如何以高效的连续工艺在结构简单的反应器系统中进行平稳的气-液相反应一直是化工领域的技术人员所面对的一个难题。例如乙烯利的酸解合成工艺就是这样一个典型的例子。
3.已知乙烯利具有植物生长调节效果,通常可以以水溶液的形式用于提供促进作物的种子萌发、开花结果、果实成熟等功能。另外,人们也普遍在对橡胶树进行割胶的时候采用乙烯利刺激橡胶树的割口,增加天然乳胶的流量。乙烯利在上述领域中具有广阔的应用前景和日益增长的需求。
4.目前乙烯利的化学合成包括使得2-氯乙基磷酸二(2-氯乙基)酯(下文中称作“正酯”)与氯化氢气体发生气-液相/酸解反应,以生成乙烯利的反应,图1显示了该反应的机理。
5.最初上述气-液相反应是在常规的釜式反应器中进行的,但是这不可避免地导致反应釜内气-液传质不良、反应不均匀、反应效率差、传热控制不良等缺陷,另外在较差的传热和传质条件下,局部的高温也很容易导致反应器内的泵和压缩机等部件受到氯化氢的快速腐蚀,上述问题都给乙烯利的工业化大规模生产带来了显著的不利影响。
6.在现有技术中为了克服上述问题,人们已经进行了大量的研究,尝试对反应器的结构设计以及工艺步骤进行改进。例如人们报道的改进方式包括使得气体物料从反应器底部进料,尝试通过气体鼓泡来改善反应器内的传热和传质;还有一种报道的改进思路是将多个釜式反应器串联起来,使得反应物料依次通过这多个反应釜以期望借此提高反应效率。但是遗憾的是,现有技术的这些努力仅能以有限的程度提高传质和传热,上述技术缺陷仍然不同程度地存在。因此现有技术中,上述所有的技术难题都仍然存在。
7.因此,本领域中仍然急需开发一种改进的独特的技术方案,以简单而低成本的设计显著改善反应器中的混合均匀性以及传热和传质,以显著改善反应效率,并且还希望该工艺中各部件内都分别采用尽可能低的温度,以减轻高温条件下氯化氢对反应器部件的酸腐蚀。
技术实现要素:8.针对上述问题,本技术的发明人进行了深入的研究,成功地开发出一种连续酸解循环反应器和使用该反应器进行连续反应以制备乙烯利的方法,从而有效地解决了现有技术中长久以来急需解决的难题,本发明的反应器和方法也可以用来进行其他具有类似需求的气-液相反应。
9.本技术的第一个方面提供了一种连续酸解循环反应器,该反应器包括反应釜、文
丘里部件、液体循环系统和气体分离-循环系统,所述反应釜包括位于其底部的液体出口,位于其顶部的气体入口、液体入口和气体出口;所述文丘里部件是一个管状部件,从上至下包括文丘里喷嘴、混合段和扩散段,所述文丘里部件的下部插入所述反应釜内,上部从从反应釜的顶部突出;所述液体循环系统包括至少一个换热器以及至少一个循环泵,所述液体循环系统与反应釜的液体出口以及文丘里喷嘴流体连通;所述气体分离-循环系统包括冷凝器和接收器,所述气体分离-循环系统与反应釜的气体出口以及气体入口流体连通。
10.本技术的第一个方面提供了一种连续进行气-液两相反应,更具体来说是以连续方式酸解合成乙烯利的方法,该方法在本技术的反应器中进行,该方法包括:通过气体入口将至少一种气相反应物加入反应釜,通过液体入口将至少一种液体反应物加入反应釜,所述至少一种气相反应物和至少一种液相反应物在反应釜内发生反应生成液相产物;将反应釜内的液相物料的至少一部分引入液体循环系统,收获至少一部分液相产物,并将剩余的液相物料至少部分地经过文丘里部件循环回到反应釜中;将反应釜内的气相物料的至少一部分引入气体分离-循环系统,分离至少一部分气相副产物并将其收集到接收器中,并将剩余的气相物料至少部分地经过文丘里部件循环回到反应釜中。
附图说明
11.在接下来的段落中结合附图对本技术的各种实施方式进行论述。但是此处需要指出的是,附图中所示和以下具体描述的实施方式仅仅是本技术的一些优选实施方式,本技术的保护范围由权利要求书来限定,而非仅限于这些优选的实施方式。另外,为了清楚显示的目的,说明书附图中显示的反应器和各个部件并非按照真实比例绘制。
12.图1显示了2-氯乙基磷酸二(2-氯乙基)酯与氯化氢气体反应以生成乙烯利的机理;
13.图2显示了根据本技术一个实施方式,本技术反应器中反应釜的示例性结构;
14.图3显示了根据本技术一个示例性实施方式,本技术反应器的示意图。
具体实施方式
15.本文所公开的“范围”以下限和上限的形式。可以分别为一个或多个下限,和一个或多个上限。给定范围是通过选定一个下限和一个上限进行限定的。选定的下限和上限限定了特别范围的边界。所有可以这种方式进行限定的范围是包含和可组合的,即任何下限可以与任何上限组合形成一个范围。例如,针对特定参数列出了60-120和80-110的范围,理解为60-110和80-120的范围也是预料到的。此外,如果列出的最小范围值1和2,和如果列出了最大范围值3,4和5,则下面的范围可全部预料到:1-3、1-4、1-5、2-3、2-4和2-5。
16.在本技术中,除非有其他说明,数值范围“a-b”表示a到b之间的任意实数组合的缩略表示,其中a和b都是实数。例如数值范围“0-5”表示本文中已经全部列出了“0-5”之间的全部实数,“0-5”只是这些数值组合的缩略表示。
17.在本技术中,如果没有特别的说明,本文所提到的所有实施方式以及优选实施方式可以相互组合形成新的技术方案。
18.在本技术中,如果没有特别的说明,本文所提到的所有技术特征以及优选特征可以相互组合形成新的技术方案。
19.在本技术中,如果没有特别的说明,本文所提到的“包括”表示开放式,也可以是封闭式。例如,所述“包括”可以表示还可以包含没有列出的其他组分,也可以仅包括列出的组分。
20.在本技术中,当描述一个装置或部件与另一个装置或部件“流体连通”,则表示二者之间通过一种或多种措施或器件直接或间接地连通,使得流体(例如气体、液体、或其混合物等)有能力在二者之间流动,但是“流体连通”并不一定表示流体在任何时间都可以在二者之间流动,二者之间还可以设置有诸如开关、阀门、导流装置等,以按需要暂时隔断二者之间的流动。
21.本技术的反应器可以用于进行各种气相反应物和液相反应物之间发生的气-液相反应,在本技术的说明书中主要以2-氯乙基磷酸二(2-氯乙基)酯(下文中称作“正酯”)与氯化氢气体发生气-液相/酸解反应、以生成乙烯利的反应为例来介绍本技术的反应器结构和工艺条件设计,但是本技术的反应器和方法也可以用于其他的各种气相反应物和液相反应物之间的反应,特别是适用于会产生大量放热以及反应原料、产物和/或副产物具有较大酸性、碱性或腐蚀性的反应,并同样基于本技术的反应器和方法而获得类似的技术效果。所述其他的气-液相反应的非限制性例子可以包括各种酯类的酸解,各种有机化合物的卤化反应等。
22.本技术的反应器是能够以连续方式进行反应的反应器,其包括反应釜、文丘里部件、液体循环系统和气体分离-循环系统,所述反应釜包括位于其底部的液体出口,位于其顶部的气体入口、液体入口和气体出口。
23.图2显示了根据本技术一个实施方式的反应器中所包括的反应釜和文丘里部件的示意图。反应釜具有密封的釜体,在反应釜的底部设置有一个液体出口,在反应釜的顶部设置有气体入口、液体入口、气体出口,文丘里部件从反应釜的顶部插入反应釜内,所述气体入口用于将气相反应物引入反应釜内,所述液体入口用于将液相反应物引入反应釜内,所述气体出口用于在连续反应过程中将至少一部分气相物料从反应釜引出并经由气体分离-循环系统进行气相物料的分离和循环操作,所述液体循环系统则用于在连续反应过程中将至少一部分液相物料从反应釜引出并经由液体循环系统进行液态产物的采出(收获)以及未反应液相原料的循环操作。根据本技术的一个独立的实施方式,所述液体入口和气体入口均可以设置在反应釜的顶部,分别用来将液相反应物和气相反应物引入反应釜中。根据本技术的另一个独立的实施方式,所述液体入口和气体入口中的至少一个可以设置在文丘里部件的喷嘴处,例如设置成位于文丘里喷嘴的顶部或者位于文丘里部件喷嘴部分外侧吸气室侧壁上的物料进口。根据本技术的一个实施方式,可以将所述液体入口设置在文丘里部件的喷嘴处,例如设置成位于文丘里部件喷嘴顶部或喷嘴外侧吸气室侧壁上的物料进口。根据本技术的另一个实施方式,可以将所述气体入口设置在文丘里部件的喷嘴处,例如设置成位于文丘里部件喷嘴部分外侧吸气室侧壁上的物料进口。根据本技术的另一个实施方式,可以将所述所述液体入口和气体入口均设置在文丘里部件的喷嘴处,例如设置成位于文丘里部件喷嘴顶部或者喷嘴外侧吸气室侧壁上的物料进口。
24.根据本技术的一个实施方式,如图2所示,所述文丘里部件按照从上到下的顺序包括喷嘴(文丘里喷嘴)、混合段和扩散段。喷嘴可以具有上窄下宽的截顶圆锥形形状,在喷嘴外侧设置有吸气室,喷嘴外壁上设置有小孔或者狭缝,与吸气室流体连通。当从喷嘴上方流
入的物料(例如循环的液体物料)在流经该喷嘴的时候随着喷嘴形状的变化,通过文丘里效应对吸气室内的物料(例如上文所述从吸气室侧壁上的进口流入的液体或气体物料)产生负压吸力,将吸气室内的物料吸入喷嘴中,从而使得来自吸气室侧壁进口的物料与来自文丘里喷嘴顶部的物料一起进入喷嘴中,并向下流动进入喷嘴下方的混合段中。
25.所述文丘里部件的混合段可以具有圆筒形的形状,也可以具有截顶圆锥形形状,从文丘里喷嘴顶部和吸气室侧壁的进口进入的物料在该混合段,在该混合段内充分混合,然后向下流动进入扩散段。扩散段具有截顶圆锥形形状,其上部与混合段的底部相连,下部则插入反应釜内的液面之下,使得来自喷嘴的物料(循环液相物料、循环气相物料、液相反应原料和气相反应原料中的至少一种)在混合段中混合之后经由该扩散段进入反应釜内的反应物料之内。根据本技术的另一个实施方式,所述液相反应原料可以从文丘里部件顶部喷嘴加入。
26.在图2所示的实施方式中,所述文丘里部件的顶部(喷嘴部分)从反应釜的顶部突出出来,中部(大致在混合段的高度)固定在反应釜的顶部,文丘里部件与反应釜结合处用密封圈密封(此处可设置有可拆卸的固定盖板,以便于文丘里部件的安装、替换以及日常维护和检修),下部(扩散段)则位于反应釜的内部,并且扩散段的底部开口在反应过程中始终插入反应釜内的液面之下。
27.根据本技术的一个实施方式,在反应过程中控制进料量和出料量达到平衡,维持反应釜内液面高度不变,从文丘里部件扩散段高速喷射的液体物流或气液混合物流可以对反应釜内的物料提供搅拌效果。
28.根据本技术的一个实施方式,所述反应釜上还可以根据需要设置其他各种部件,例如搅拌装置(磁力搅拌装置、机械搅拌器、鼓泡式搅拌器等)、温度传感器、压力传感器、取样口等。反应釜的外侧还可以设置有加热套,例如电热丝加热套或导热油加热套,用于在反应过程中将反应釜内的温度控制在所需水平。
29.根据本技术的一个实施方式,反应釜、文丘里部件、液体循环系统和气体分离-循环系统各自独立地由选自以下的材料制成:耐腐蚀金属、塑料材料、陶瓷材料、碳化硅材料、钢衬碳化硅、钢衬塑料、钢衬搪玻璃和钢衬搪瓷,所述塑料和钢衬塑料中的塑料可以是例如聚乙烯、聚四氟乙烯等。例如反应釜可以使用钢衬搪瓷材料制成,液体循环系统中的管道和循环泵涡扇叶可以用钢衬塑料(例如钢衬四氟乙烯)材料制成。
30.根据本技术的一个实施方式,所述液体循环系统包括至少一个换热器以及至少一个循环泵,所述液体循环系统与反应釜底部的液体出口以及文丘里装置的喷嘴顶部入口流体连通。根据本技术一个进一步的实施方式,所述液体循环装置可以包括两个或更多个换热器以及一个、两个或更多个循环泵,所述循环泵位于至少一个换热器(前换热器)的下游和至少一个另外的换热器(后换热器)的上游。所述换热器可以是本领域已知的任意合适的换热器,例如可以是使用冷却水或导热油的换热器,优选是使用导热油的换热器。根据本技术的一个优选的实施方式,所述液体循环系统包括两个换热器(一个前换热器和一个后换热器)和一个循环泵。通过将循环泵设置在至少一个前换热器的下游,使得循环泵经历的工作温度低于反应釜内的反应温度。根据本技术的一个实施方式,在反应过程中,反应釜内的反应温度保持在120-160℃,例如125-155℃,或者130-150℃,或者135-145℃,或者140-142℃,或者可以在上述任意两个端值相互组合得到的数值范围之内;而所述液体循环系统在
工作过程中,其中的循环泵的工作温度的温度为等于或低于120℃,例如80-120℃,或者90-120℃,或者100-120℃,或者100-115℃,或者110-115℃,或者可以在上述任意两个端值相互组合得到的数值范围之内。不希望局限于任意理论,由于循环泵在上文所述较低的工作温度下运行,能够有效地防止循环泵中使用的塑料衬层(例如ptfe衬层)的老化及其与下方钢材基底的分离,从而有效地延长循环泵的使用寿命,减少反应设备的停机维护和检修,降低工艺的复杂程度和减少运行及维护的成本。根据本技术的一个实施方式,通过使用前换热器使得流经循环泵的液流具有上文所述≤120℃的温度,然后当液流通过循环泵并流经后换热器的时候,再将液流的温度升高至接近反应釜内的温度,例如反应釜内的温度
±
5℃,例如125-165℃,或者130-150℃,或者135-140℃,或者可以在上述任意两个端值相互组合得到的数值范围之内。根据本技术的另一个实施方式,本发明使用的换热器可以是管壳式换热器,例如管程内衬碳化硅的管壳式换热器,壳程的换热流体可以包括冷却水、水蒸气、导热油等,换热流体可以根据所需的目标温度改变。
31.根据本技术的一个实施方式,在所述液体循环系统中设置有液体产物出口(也称为“出料口”),例如该液体产物出口可以设置在循环泵的下游、后换热器的上游,用于将流经该液体循环系统的液流中的一部分液体产物(例如乙烯利)以连续的方式出料。
32.根据本技术的另一个实施方式,在所述液体循环系统中各部件(每个换热器以及循环泵)的上游和下游处可以根据需要设置一个或多个装置,例如开关、阀门、流量传感器、压力传感器、温度传感器、排液阀门、连接管道、旁路管道等。例如,可以根据需要在前换热器的上游处以及循环泵的下游(但是位于后换热器的上游)处设置排液阀门,在进行连续反应的过程中,可以根据需要开启该排液阀门,排掉一部分液相物流,作为取样分析、产物收集或废料处理等用途。
33.根据本技术的一个实施方式,本技术的连续反应器还包括气体分离-循环系统,所述气体分离-循环系统包括冷凝器和接收器,所述气体分离-循环系统与反应釜的气体出口以及气体入口流体连通。根据本技术的一个实施方式,所述冷凝器包括顶部出口和底部出口,底部出口连接至接收器,用于接收来自冷凝器底部的副产物(例如二氯乙烷),顶部出口则主要将未反应的气相反应原料分离出来,并将该未反应的气相原料至少部分地循环回到反应釜中,例如循环回到文丘里部件的喷嘴处,更具体来说是循环回到文丘里部件喷嘴部分外侧吸气室侧壁上的物料进口。
34.根据本技术的一个实施方式,冷凝器顶部出口还与尾气吸收装置经由阀门或开关流体连通,所述尾气吸收装置主要用来根据需要收集所述所述气体分离-循环系统中的气态副产物以及/或者其他气态物料,或者用于根据需要排出一部分气态物料以维持气体分离-循环系统中所需的压力和/或组成。
35.根据本技术的另一个实施方式,在所述冷凝器的下游设置有背压阀,例如所述背压阀可以设置在所述冷凝器顶部出口的下游,更具体来说设置在所述冷凝器顶部出口与尾气吸收装置之间。
36.本技术使用的背压阀具有膜片和内置弹簧,通过内置弹簧的弹力来实现动作,背压阀的启动压力是可以设定的,当气体分离-循环系统内的气体压力比设定压力小的时候,背压阀内的膜片在弹簧弹力的作用下堵塞管路;当气体分离-循环系统内的气体压力比背压阀的设定压力大时,膜片压缩弹簧,管路接通,使得气体分离-循环系统内的气体通过背
压阀。
37.根据本技术的一个实施方式,通过使用背压阀,在有效地进行尾气排放的同时,能够对气体分离-循环系统内的气体压力进行有效的控制,由此在进行气相循环的过程中不会对反应釜内的压力(气相压力)造成任何负面影响。根据本技术的一个实施方式,所述反应釜内的压力(气相压力)可以保持在0.30-0.80mpa,例如0.40-0.70mpa,或者0.50-0.60mpa,或者可以保持在上述任何两个端值相互组合得到的数值范围之内;根据本技术的另一个实施方式,通过使用背压阀,使得所述气体分离-循环系统内的气体压力保持在与反应釜内的气体压力基本相同的水平,例如使得所述气体分离-循环系统内的气体压力保持在0.40-0.70mpa,或者0.50-0.60mpa,或者可以保持在上述任何两个端值相互组合得到的数值范围之内。
38.根据本技术的另一个实施方式,在所述气体分离-循环系统中各部件(冷凝器、背压阀、接收器)的上游和下游处可以根据需要设置一个或多个装置,例如开关、阀门、流量传感器、压力传感器、温度传感器、排液阀门、连接管道、旁路管道等。例如,可以根据需要在接收器的顶部、底部或侧部设置采出开关和管道,用来将接收器中接受的副产物采出;还可以在接收器的顶部安装气体输送管道,用来将流入接收器的一些气相物料(例如未反应的气相原料)引出,送去尾气吸收装置或者与冷凝器顶部出口的气相流出物合并之后循环回到反应釜。
39.图3显示了根据本技术一个实施方式的连续酸解循环反应器,在图3所示的反应器中分别包括气相原料罐(例如氯化氢原料罐)和液相原料罐(例如正酯原料罐),反应釜,文丘里部件、液体循环系统和气体分离-循环系统。在所述各部分之间通过管道连接,并且管道中根据需要可以设置有一种或多种功能的器件,例如开关、阀门、流量计、温度计、压力计、端口、压力调节装置、温度调节装置等。
40.所述文丘里部件的结构如上所述,包括喷嘴、混合段和扩散段,围绕喷嘴设置有吸气室,所述文丘里部件的顶部(喷嘴部分)从反应釜的顶部突出出来,中部(大致在混合段的高度)固定在反应釜的顶部,文丘里部件与反应釜结合处用密封圈密封(此处可设置有可拆卸的固定盖板,以便于文丘里部件的安装、替换以及日常维护和检修),下部(扩散段)则位于反应釜的内部,并且扩散段的底部开口在反应过程中始终插入反应釜内的液面之下。在图3所示的反应釜中,液相原料入口设置在反应釜的顶部,而非设置在文丘里部件的喷嘴处,气相原料的入口设置在文丘里部件的喷嘴处(具体来说,设置在围绕文丘里喷嘴的吸气室侧壁处)。另外在图3所示的实施方式中,与气体分离-循环系统相连的气体出口设置在反应釜的顶部,而在气体分离-循环系统中循环之后的气相循环物料入口设置在文丘里部件的喷嘴处(具体来说,设置在围绕文丘里喷嘴的吸气室侧壁处);与液体循环系统相连的液体出口设置在反应釜的底部,而在液体循环系统中循环之后的液相循环物料的入口设置在文丘里部件的喷嘴顶部,也即经由文丘里部件的喷嘴的顶部将循环后的液相物料喷入反应釜中。
41.根据本技术的一个实施方式,通过以下方式进行液体原料(例如正酯)和气体原料(hcl)的反应。首先将液体原料经由液体进口(该液体进口位于反应釜的顶部,或者位于文丘里装置的喷嘴顶部)输入反应釜中,达到特定的液面高度,使得文丘里喷嘴的底部在整个反应过程中始终没在液面下方。液体原料加入至指定液面高度之后,封闭反应釜,根据需要
在反应釜内填充所需的气氛,例如充氮气,随后打开尾气吸收装置处的阀门,使用真空泵将反应釜中的氮气全部抽出,再关闭所有阀门以将反应釜密封。通过气体原料入口向反应釜内充入气体原料,使得反应釜内达到预定压力,例如0.30-0.80mpa。通过设定背压阀使得反应釜和气体分离-循环系统中具有基本相同的压力,例如二者中的压力可以均为大约0.30-0.80mpa,或者0.40-0.70mpa,或者0.50-0.60mpa,或者可以保持在上述任何两个端值相互组合得到的数值范围之内。
42.此时暂时停止气体原料的进料,开始对反应釜进行加热,例如将反应釜内的温度加热至120-160℃,例如125-155℃,或者130-150℃,或者135-145℃,或者140-142℃,或者可以在上述任意两个端值相互组合得到的数值范围之内。启动液体循环系统以及气体分离-循环系统,启动液体循环系统中的前换热器和后换热器以及循环泵,例如将前换热器的温度设置在等于或低于120℃,例如80-120℃,或者90-120℃,或者100-120℃,或者100-115℃,或者110-115℃,或者可以在上述任意两个端值相互组合得到的数值范围之内;使得循环泵的工作温度的温度为等于或低于120℃,例如80-120℃,或者90-120℃,或者100-120℃,或者100-115℃,或者110-115℃,或者可以在上述任意两个端值相互组合得到的数值范围之内;将后换热器的温度设置在与反应釜内的温度基本相当,例如反应釜的温度
±
5℃,例如125-165℃,或者130-150℃,或者135-140℃,或者可以在上述任意两个端值相互组合得到的数值范围之内。通过上述设置,使得反应釜内的液体物料连续地从反应釜底部引出,经过前换热器降至较低的温度,流经循环泵之后再重新升温至与反应釜内的温度基本相当,然后再从文丘里喷嘴顶部进入文丘里装置,通过文丘里装置喷射入反应釜内的液面之下。在上述循环的过程中,从液体循环系统中的一个或多个排液口对液体物流取样并检测其组成,当确认液体物流中目标产物的浓度达到预期水平之时,以连续的方式从出料口出料获得目标产物,同时开始以连续的方式成比例地向反应釜内补充气体原料和液体原料,使得反应釜内的液面高度保持不变。根据本技术的一个实施方式,此处连续采出的液体物料中目标液体产物(例如乙烯利)的浓度≥95%,例如95-99.5%,或者95-99%,或者95-98%,或者95-97%,或者95-96%,以上所述的浓度为质量浓度。
43.另外,在进行连续反应的过程中,从反应釜顶部将反应釜内液面上方的气相引入,流经气体分离-循环系统。具体来说,这部分循环气相首先经过冷凝器,所述冷凝器使用的冷媒温度可以为-16℃至30℃,使用的冷媒可以是烃类制冷剂、氨水、冷凝水或导热油,可以根据所需的目标温度来选择合适的冷媒。在所述冷凝器内对流经该冷凝器的气相物料进行冷凝,以从中分离至少一部分的副产物。对于正酯和hcl的反应,气相物料中包含的副产物可以包括二氯乙烷以及少量的其他卤代烃类等,这部分副产物冷凝之后从冷凝器底部流出,收集在接收器中。经过上述冷凝之后,气相物料从冷凝器顶部流出,该顶部流出物主要包含未反应的气相原料(例如氯化氢气体),该部分气体物料被循环至文丘里部件,例如输送至文丘里部件的喷嘴顶部,或者输送至文丘里部件的喷嘴外周设置的吸气室侧壁的循环气体进口处。根据本技术的一个实施方式,还设置有与冷凝器顶部出口相连的尾气吸收装置,在所述冷凝器顶部出口和尾气吸收装置之间设置有背压阀,所述背压阀的结构以及设置压力如上文所述。当背压阀所经受的气体压力大于设定值的时候,则打开背压阀进行尾气排放,使得气体分离-循环系统内的压力降至预定压力之下的时候,背压阀自动关闭,由此将气体分离-循环系统内的压力以及反应釜内的压力都保持在预期的水平,这有利于反
应器内反应的顺利而高效的进行,能够显著改进反应物转化率和产物选择性。
44.根据本技术的另一个实施方式,在接收器的顶部设置气体输送管道,用来将流入接收器的一些气相物料(例如未反应的气相原料)引出,送去尾气吸收装置或者与冷凝器顶部出口的气相流出物合并之后循环回到反应釜。
45.根据本技术的一个实施方式,在液体循环系统循环过的液体循环物料回到文丘里部件的喷嘴顶部,经由喷嘴向下流入反应釜内的液面之下。该液体循环物料流经喷嘴的时候产生负压,由此对从吸气室侧壁入口流入的物料产生吸力,所述负压可以是-0.05mpa至-0.1mpa。
46.根据本技术的另一个实施方式,在连续反应过程中,以连续的方式向反应釜内输入液体原料和气体原料,使得反应釜内的液面高度保持不变,并且液体原料输入反应釜时的压力可以保持在0.10-0.80mpa,例如0.20-0.70mpa,或者0.10-0.30mpa,或者0.40-0.60mpa,或者可以在上述任意两个端值相互组合得到的数值范围之内。
47.根据本技术的一个实施方式,所述液相反应物(例如正酯)和气相反应物(例如氯化氢气体)以连续的方式输入所述反应釜中,并且液相反应物和气相反应物输入的摩尔比为1:1.0至1:3.0,例如1:2.0至1:3.0,或者1:2.5至1:3.0,或者可以在上述任意两个端值相互组合得到的数值范围之内。
48.根据本技术的一个实施方式,在液体循环系统中以连续的方式收获液相反应产物,在收获液相反应产物的同时,以对应的补充量向反应釜中补充气相反应原料和液相反应原料,使得新补充的原料与通过文丘里装置循环回到反应釜的循环气相和液相物料混合之后,将反应釜内的液面高度保持不变。产物采出量与新鲜原料补充量能够确保采出产物中目标产物(例如乙烯利)的浓度(纯度)保持在恒定的水平,在该前提下尽可能增大产物的采出量,以实现乙烯利生产能力最大化。
49.根据本技术的一个实施方式,通过上文所述以连续的方式进行液相产物(例如乙烯利)、气相副产物(例如二氯乙烷)的采出,气相循环物料根据需要的尾气排放(利用背压阀设定的压力进行控制),气相和液相循环物料的循环,以及新鲜气体原料和新鲜气体原料的补充,反应釜内保持基本恒定的液面高度和气体压力,实现气-液相反应的连续进行。原料的转化率(以正酯的转化率计)可以为95-99%,例如95-98%,或者95-97%,或者95-96%,或者可以在上述任意任意两个端值相互组合得到的数值范围之内。产物(正酯)的纯度(也即采出的液相物料中目标产物的重量含量)可以为≥95%,例如95-99.5%,或者95-99%,或者95-98%,或者95-97%,或者95-96%。
50.本发明的反应器和方法可以实现以下的一个或多个优点:
51.1.本技术通过将反应釜与液体循环系统和气体分离-循环系统组合使用,能够以高效的方式实现产物采出、气-液相物料循环和新鲜原料补充的连续进行,实现了优异的反应反应性能、反应工艺复杂程度降低、工艺单位时间产量的提高,工艺简单、装置紧凑且占地面积小、投资少、能耗低、原料利用率高、反应速率快、产品质量;
52.2.利用背压阀改善了整个反应体系内压力的稳定化控制,消除了反应体系内压力浮动对反应的不利影响,提高了反应速率;
53.3.实现了副产物高效分离以及气相循环物料的有效输送,促进了反应平衡的正向移动,提高了原料的转化率、利用率和反应转化性能;
54.4.通过采用文丘里装置改善了反应器内物料混合和反应的效率,进一步改善了反应性能和反应速率;
55.5.通过在液体循环系统中采用特别的双换热器设计,能够使得高温反应与低温循环泵工作在温度上隔离开来,能够有效地改善循环泵中金属衬四氟乙烯部件的使用寿命,经过循环泵之后的液体流在后换热器中再重新升温至适合于在反应釜中进行反应的温度,不会对循环液体物料在反应釜内的反应造成负面影响,同时前后两个换热器之间可以进行换热,实现对废热的有效循环利用。
56.下文以具体实施例的方式描述本技术,其目的在于更好地理解本技术的内容。应理解,这些实施例仅仅是阐述性的,而非限制性的。实施例中所使用的试剂,除非另有说明,否则都是从市场上常规购得。实施例中所使用的方法和条件,如无特殊说明,均为常规方法和条件。
57.实施例
58.在以下的实施例中,在本技术的反应器中考察了正酯与氯化氢反应生成乙烯利的工艺过程。以下的实施例仅为本技术列举的具体实例,但本技术的技术特征并不局限于此。任何以本技术为基础,为解决基本相同的技术问题,基本相同的技术效果,而所作出简单的变化、等同替换或其他修饰等,皆涵盖在本技术的保护范围内。
59.实施例1
60.在该实施例1中依照图3所示构建了本技术的连续酸解循环反应器,反应釜为钢衬搪瓷材料制成,反应系统内的各个管道为钢衬聚四氟乙烯材料,液体循环系统包括一个前换热器和一个后换热器,二者均为管程内衬碳化硅的管壳式换热器,循环泵是钢衬聚四氟乙烯材料,气体分离-循环系统的冷凝器为管程内衬碳化硅的管壳式冷凝器,接收器是钢衬搪瓷材料制成。
61.该实施例1中使用的正酯由发明人在实验室中按照已知的合成工艺合成得到。
62.将正酯一次性投入反应釜中至预定液面高度,将反应釜密封,充氮气至0.2mpa,检测反应釜的密封性,确认密封性合格之后,连通尾气吸收装置处的直通阀,用连接于此处的真空泵抽出反应釜内的全部氮气,然后关闭此处的直通阀。从氯化氢原料罐向反应釜内充入氯化氢气体,直至背压阀处测得的压力为0.4mpa,此时暂时关闭氯化氢阀门。启动液体循环系统中的循环泵,开启反应釜外部加热套的加热,反应釜温度设为130℃;开启循环泵前换热器,温度设为120℃,开启循环泵后换热器,温度设为135℃;启动气体分离-循环系统,开启冷凝换热器,15℃的冷凝水在该冷凝换热器中流动。待温度全部到达设定温度后再次开启氯化氢阀门,将氯化氢连续导入至反应釜,使得反应釜内和气体分离-循环系统内的压力保持在0.4mpa,开始进行酸解反应,通过液体循环系统出料口采出物料取样进行中控分析,当采出的液体物料中乙烯利纯度达到96重量%时,开始以1.02kg/h的流量从液体循环系统的出料口连续采出纯度为96重量%的乙烯利产物。同时以大约2.0kg/h连续地向反应釜内补充正酯原料(正酯原料入口位于反应釜顶部)和氯化氢原料(氯化氢原料入口位于文丘里装置喷嘴外吸气室侧壁处),使得反应釜内的液面高度保持不变。反应釜内和气体分离-循环系统内的压力保持在0.4mpa,补充新鲜氯化氢原料的通量为0.76kg/h。在该连续反应的过程中,接收器持续地接收从冷凝器底部流出的二氯乙烷副产物。在实施例1的工艺条件下,通过以上述流量进行液体产物的引出以及气液相原料的加入,同时保持二氯乙烷的
收集,确保反应器内液面高度保持不变。在该连续循环过程中对液相物料取样分析,通过气相色谱测得正酯原料的转化率为95%。
63.实施例2:
64.在该实施例2中使用与实施例1相同的反应器和按照现有工艺合成的正酯原料。
65.将正酯一次性投入反应釜中至预定液面高度,将反应釜密封,充氮气至0.2mpa,检测反应釜的密封性,确认密封性合格之后,连通尾气吸收装置处的直通阀,用连接于此处的真空泵抽出反应釜内的全部氮气,然后关闭此处的直通阀。从氯化氢原料罐向反应釜内充入氯化氢气体,直至背压阀处测得的压力为0.5mpa,此时暂时关闭氯化氢阀门。启动液体循环系统中的循环泵,开启反应釜外部加热套的加热,反应釜温度设为150℃;开启循环泵前换热器,温度设为120℃,开启循环泵后换热器,温度设为155℃;启动气体分离-循环系统,开启冷凝换热器,15℃的冷凝水在该冷凝换热器中流动。待温度全部到达设定温度后再次开启氯化氢阀门,将氯化氢连续导入至反应釜,使得反应釜内和气体分离-循环系统内的压力保持在0.5mpa,开始进行酸解反应,通过液体循环系统出料口采出物料取样进行中控分析,当采出的液体物料中乙烯利纯度达到96重量%时,开始以1.30kg/h的流量从液体循环系统的出料口连续采出纯度为96重量%的乙烯利产物。同时以大约2.5kg/h连续地向反应釜内补充正酯原料(正酯原料入口位于反应釜顶部)和氯化氢原料(氯化氢原料入口位于文丘里装置喷嘴外吸气室侧壁处),使得反应釜内的液面高度保持不变。反应釜内和气体分离-循环系统内的压力保持在0.5mpa,补充新鲜氯化氢原料的通量为0.85kg/h。在该连续反应的过程中,接收器持续地接收从冷凝器底部流出的二氯乙烷副产物。在实施例2的工艺条件下,通过以上述流量进行液体产物的引出以及气液相原料的加入,同时保持二氯乙烷的收集,确保反应器内液面高度保持不变。在该连续循环过程中对液相物料取样分析,通过气相色谱测得正酯原料的转化率为97%。
66.实施例3:
67.在该实施例3中使用与实施例1相同的反应器和按照现有工艺合成的正酯原料。
68.将正酯一次性投入反应釜中至预定液面高度,将反应釜密封,充氮气至0.2mpa,检测反应釜的密封性,确认密封性合格之后,连通尾气吸收装置处的直通阀,用连接于此处的真空泵抽出反应釜内的全部氮气,然后关闭此处的直通阀。从氯化氢原料罐向反应釜内充入氯化氢气体,直至背压阀处测得的压力为0.3mpa,此时暂时关闭氯化氢阀门。启动液体循环系统中的循环泵,开启反应釜外部加热套的加热,反应釜温度设为140℃;开启循环泵前换热器,温度设为120℃,开启循环泵后换热器,温度设为145℃;启动气体分离-循环系统,开启冷凝换热器,15℃的冷凝水在该冷凝换热器中流动。待温度全部到达设定温度后再次开启氯化氢阀门,将氯化氢连续导入至反应釜,使得反应釜内和气体分离-循环系统内的压力保持在0.5mpa,开始进行酸解反应,通过液体循环系统出料口采出物料取样进行中控分析,当采出的液体物料中乙烯利纯度达到96重量%时,开始以1.54kg/h的流量从液体循环系统的出料口连续采出纯度为96重量%的乙烯利产物。同时以大约3.0kg/h连续地向反应釜内补充正酯原料(正酯原料入口位于反应釜顶部)和氯化氢原料(氯化氢原料入口位于文丘里装置喷嘴外吸气室侧壁处),使得反应釜内的液面高度保持不变。反应釜内和气体分离-循环系统内的压力保持在0.5mpa,补充新鲜氯化氢原料的通量为1.06kg/h。在该连续反应的过程中,接收器持续地接收从冷凝器底部流出的二氯乙烷副产物。在实施例3的工艺条
件下,通过以上述流量进行液体产物的引出以及气液相原料的加入,同时保持二氯乙烷的收集,确保反应器内液面高度保持不变。在该连续循环过程中对液相物料取样分析,通过气相色谱测得正酯原料的转化率为96%。
69.实施例4:
70.在该实施例4中使用与实施例1相同的反应器和按照现有工艺合成的正酯原料。
71.将正酯一次性投入反应釜中至预定液面高度,将反应釜密封,充氮气至0.2mpa,检测反应釜的密封性,确认密封性合格之后,连通尾气吸收装置处的直通阀,用连接于此处的真空泵抽出反应釜内的全部氮气,然后关闭此处的直通阀。从氯化氢原料罐向反应釜内充入氯化氢气体,直至背压阀处测得的压力为0.7mpa,此时暂时关闭氯化氢阀门。启动液体循环系统中的循环泵,开启反应釜外部加热套的加热,反应釜温度设为150℃;开启循环泵前换热器,温度设为120℃,开启循环泵后换热器,温度设为155℃;启动气体分离-循环系统,开启冷凝换热器,10℃的冷凝水在该冷凝换热器中流动。待温度全部到达设定温度后再次开启氯化氢阀门,将氯化氢连续导入至反应釜,使得反应釜内和气体分离-循环系统内的压力保持在0.7mpa,开始进行酸解反应,通过液体循环系统出料口采出物料取样进行中控分析,当采出的液体物料中乙烯利纯度达到96重量%时,开始以1.84kg/h的流量从液体循环系统的出料口连续采出纯度为96重量%的乙烯利产物。同时以大约3.5kg/h连续地向反应釜内补充正酯原料(正酯原料入口位于反应釜顶部)和氯化氢原料(氯化氢原料入口位于文丘里装置喷嘴外吸气室侧壁处),使得反应釜内的液面高度保持不变。反应釜内和气体分离-循环系统内的压力保持在0.7mpa,补充新鲜氯化氢原料的通量为1.04kg/h。在该连续反应的过程中,接收器持续地接收从冷凝器底部流出的二氯乙烷副产物。在实施例4的工艺条件下,通过以上述流量进行液体产物的引出以及气液相原料的加入,同时保持二氯乙烷的收集,确保反应器内液面高度保持不变。在该连续循环过程中对液相物料取样分析,通过气相色谱测得正酯原料的转化率为98%。
72.实施例5
73.在该实施例5中使用与实施例1相同的反应器和按照现有工艺合成的正酯原料。
74.将正酯一次性投入反应釜中至预定液面高度,将反应釜密封,充氮气至0.2mpa,检测反应釜的密封性,确认密封性合格之后,连通尾气吸收装置处的直通阀,用连接于此处的真空泵抽出反应釜内的全部氮气,然后关闭此处的直通阀。从氯化氢原料罐向反应釜内充入氯化氢气体,直至背压阀处测得的压力为0.6mpa,此时暂时关闭氯化氢阀门。启动液体循环系统中的循环泵,开启反应釜外部加热套的加热,反应釜温度设为160℃;开启循环泵前换热器,温度设为120℃,开启循环泵后换热器,温度设为165℃;启动气体分离-循环系统,开启冷凝换热器,5℃的冷凝水在该冷凝换热器中流动。待温度全部到达设定温度后再次开启氯化氢阀门,将氯化氢连续导入至反应釜,使得反应釜内和气体分离-循环系统内的压力保持在0.6mpa,开始进行酸解反应,通过液体循环系统出料口采出物料取样进行中控分析,当采出的液体物料中乙烯利纯度达到96重量%时,开始以2.12kg/h的流量从液体循环系统的出料口连续采出纯度为96重量%的乙烯利产物。同时以大约4.0kg/h连续地向反应釜内补充正酯原料(正酯原料入口位于反应釜顶部)和氯化氢原料(氯化氢原料入口位于文丘里装置喷嘴外吸气室侧壁处),使得反应釜内的液面高度保持不变。反应釜内和气体分离-循环系统内的压力保持在0.6mpa,补充新鲜氯化氢原料的通量为1.14kg/h。在该连续反应的
过程中,接收器持续地接收从冷凝器底部流出的二氯乙烷副产物。在实施例5的工艺条件下,通过以上述流量进行液体产物的引出以及气液相原料的加入,同时保持二氯乙烷的收集,确保反应器内液面高度保持不变。在该连续循环过程中对液相物料取样分析,通过气相色谱测得正酯原料的转化率为99%。
75.通过以上发明实施例可以看到,本发明实施例均实现了极佳的原料转化率和产物纯度。另外,通过采用本技术的连续生产工艺,所实现的日均产量达到了现有技术记载中从未企及的高度。
76.比较例1
77.在该比较例1中使用与实施例1相同的反应器和按照现有工艺合成的正酯原料,但是未采用循环泵前换热器,导致反应釜内的温度以及循环管路的温度都会被限制在120℃以下。
78.将正酯一次性投入反应釜中至预定的液面高度,将反应釜密封,充氮气至0.2mpa,检测反应釜的密封性,确认密封性合格之后,连通尾气吸收装置处的直通阀,用连接于此处的真空泵抽出反应釜内的全部氮气,然后关闭此处的直通阀。从氯化氢原料罐向反应釜内充入氯化氢气体,直至背压阀处测得的压力为0.4mpa,此时暂时关闭氯化氢阀门。启动液体循环系统中的循环泵,开启反应釜外部加热套的加热,反应釜温度设为115℃;开启循环泵后换热器,温度设为120℃;启动气体分离-循环系统,开启冷凝换热器,15℃的冷凝水在该冷凝换热器中流动。待温度全部到达设定温度后再次开启氯化氢阀门,按给定的流量将氯化氢连续导入至反应釜,使得反应釜内和气体分离-循环系统内的压力保持在0.4mpa,开始进行酸解反应,通过液体循环系统出料口采出物料取样进行中控分析,采出的液体物料中乙烯利纯度达到65%时,开始以1.02kg/h的流量从液体循环系统的出料口连续采出纯度为65%的乙烯利产物。同时以大约2.0kg/h连续地向反应釜内补充正酯原料(正酯原料入口位于反应釜顶部)和氯化氢原料(氯化氢原料入口位于文丘里装置喷嘴外吸气室侧壁处),使得反应釜内的液面高度保持不变。反应釜内和气体分离-循环系统内的压力保持在0.4mpa,补充新鲜氯化氢原料的通量为0.76kg/h。在该连续循环过程中,接收器持续地接收从冷凝器底部流出的二氯乙烷副产物。在比较例1的工艺条件下,通过以上述流量进行液体产物的引出以及气液相原料的加入,同时保持二氯乙烷的收集,确保反应器内液面高度保持不变。对液相物料取样分析,通过气相色谱测得正酯原料的转化率为70%。