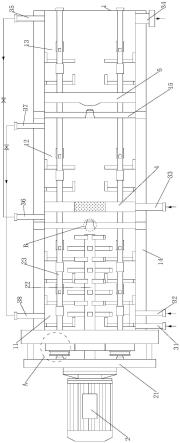
1.本实用新型涉及碳酸钙加工设备领域,特别是碳酸钙全自动连续湿法表面处理活化设备。
背景技术:2.纳米碳酸钙是80年代发展起来的一种新型超细固体材料,其粒径在1~100nm之间。日本在纳米碳酸钙生产技术、新产品开发、应用方面处于国际领先地位,现已有纺锤形、立方形、针状、链状等纳米级超细碳酸钙产品及改性产品50余种。我国对纳米碳酸钙的研制开发始于80年代初,到目前为止,已经有多个厂家、多种晶形的产品问世。
3.纳米碳酸钙是碳酸钙中的精品,也是一种最廉价的纳米材料,它所具有的特殊的量子隧道效应、小尺寸效应、表面效应、体积效应等,使其与常规粉体材料相比在补强型、透明性、分散性、触变性和流平性等方面都显示出明显的优势。现在,纳米碳酸钙正朝着专用化、精细化和功能化方向发展。
4.碳酸钙属于无机粉体材料,碳酸钙表面具有许多羟基,容易吸收水分,未经表面处理的碳酸钙粉未颗粒表面亲水疏油,因而不能与硅烷类橡胶、塑料等高分子有机物发生化学交联,在有机介质中难于均匀分散,界面难于形成良好的黏结;而且,碳酸钙粒径小,具有极大的比表面积和较高的比表面能,在制备和后处理过程中极易发生粒子团聚,形成二次粒子,使粒子粒径变大,在最终应用过程中失去超细微粒所具备的功能,从而影响实际应用效果,即不能起到功能填料的作用,相反因界面缺陷在某种程度上会降低制品的某些物理性能。
5.为了解决以上两个问题,需要对碳酸钙进行表面处理,使其表面转变为亲油疏水性,并减少团聚,使其在聚合物中的分散性和相溶性得到改善。碳酸钙的表面改性方法主要是化学包覆,辅之以机械化学;使用的表面改性剂包括硬脂酸(盐),钛酸酯偶联剂,铝酸酯偶联剂、锆铝酸盐偶联剂以及无规聚丙烯,聚乙烯蜡等。
6.目前,工厂内所使用的碳酸钙表面活性处理方法为传统方法,其采用间歇式一步活化法,通过通入低压蒸汽加热碳酸钙浆液然后将碳酸钙与表面处理剂相结合对碳酸钙进行改性处理;
7.现有专利cn201821210608.7,公开了一种轻质碳酸钙粉体的解聚、改性系统,其包括反应罐、与反应罐连通的中转罐、输送组件、集料仓、打散装置和改性剂喷淋组件,利用循环实现多次打散从而减少多余打散设备的安装,提高打散效率也减少设备安装维护成本。
8.但是该专利与工厂目前使用的传统方法一样,其均采用单一搅拌设备对碳酸钙进行表面处理,大量碳酸钙在反应罐中无法完全且充分的与表面处理剂相接触反应,从而导致其活化程度受打散装置的限制,活化率受限,较低;
9.而且,各种反应罐、中转罐、输送组件等涉及到大量罐体设备,为了满足投产产量的要求,反应罐和中转罐的体积均较大,从而导致整套表面处理设备(系统)其占地面积很大,且安装不便,设备成本很高。
10.所以,工厂内目前所用传统的碳酸钙表面处理活化系统存在活化率受打散装置限制造成最终活化率较低、整套设备占地面积大成本较高的问题。
技术实现要素:11.本实用新型的目的在于,提供碳酸钙全自动连续湿法表面处理活化设备。本实用新型采用多级分布连续活化处理,具有限制相对较少,最终活化率高,整套设备占地面积小成本相对较低的优点。
12.本实用新型的技术方案:碳酸钙全自动连续湿法表面处理活化设备,包括主体、设于主体内的搅拌单元和两块设于主体内将主体分隔成三部分的分隔板;所述分隔板中部开设有喷射口,喷射口呈漏斗状,其末端设有上设可开闭阀门的喷射管;所述搅拌单元包括搅拌电机、设于主体中部的主搅拌杆和四根均匀分布于主搅拌杆四周的次搅拌杆;所述主体的前端设有一号进料口和二号进料口,后端设有出料口;所述主体内从左往右分隔成一级搅拌区、二级搅拌区和三级搅拌区,主体上端设有对应设置的两根回流管路。
13.前述的碳酸钙全自动连续湿法表面处理活化设备中,所述主体外侧设有调温夹层,调温夹层的右侧下端设有进液口,其左侧上端设有出液口,进液口与出液口分别与调温设备相连;所述调温夹层内流通有调温流体,调温流体采用市面上常见的材料即可,如热蒸汽、导热油等等,其作用是对主体进行加热,确保碳酸钙处于稳定的活化温度范围内。
14.前述的碳酸钙全自动连续湿法表面处理活化设备中,所述三级搅拌区的末端上方设有一号回料口,二级搅拌区的前端上方设有四号进料口,一号回料口与四号进料口之间通过输料管相连;所述二级搅拌区的末端上方设有二号回料口,一级搅拌区的前端上方设有五号进料口,二号回料口与五号进料口之间通过输料管相连;所述输料管上设有单向阀。
15.前述的碳酸钙全自动连续湿法表面处理活化设备中,所述主搅拌杆上设有多个均匀分布的主搅拌叶,相邻主搅拌叶之间设有45
°
夹角;所述次搅拌杆上设有多个均匀分布的次搅拌叶,相邻次搅拌叶之间设有45
°
夹角;所述次搅拌叶与主搅拌叶相互对应设置。
16.前述的碳酸钙全自动连续湿法表面处理活化设备中,所述主体左侧端部设有用于安装搅拌电机的电机架,搅拌电机的输出轴通过联轴器与主搅拌杆相连;所述主搅拌杆和设于主搅拌杆上下两端的次搅拌杆上设有相互齿合的转动齿轮;位于主搅拌杆上下两端的次搅拌杆上设有位于转动齿轮外的皮带轮,位于主搅拌杆左右两端的次搅拌杆上设有对应的皮带轮;上端的皮带轮与左端的皮带轮通过皮带相连,对应的,下端的皮带轮与右端的皮带轮通过皮带相连。
17.前述的碳酸钙全自动连续湿法表面处理活化设备中,所述次搅拌杆贯穿分隔板设于主体内,所述主搅拌杆设于一级搅拌区内;所述主搅拌叶为十字形搅拌叶,次搅拌叶为一字型搅拌叶;所述主搅拌叶和次搅拌叶均由对应数量的搅拌直叶构成;所述次搅拌叶的一端设有与主体内壁对应抵接的刮料板。
18.前述的碳酸钙全自动连续湿法表面处理活化设备中,所述二级搅拌区前端和三级搅拌区前端分别设有主混料板和次混料板;所述二级搅拌区下端设有与主混料板连通的三号进料口。
19.前述的碳酸钙全自动连续湿法表面处理活化设备中,所述主混料板包括前后两端对应设置的盖板和设于盖板之间喷淋环;两块所述盖板的中部设有一根絮状混料管,盖板
的四周分布有与次搅拌杆对应的通槽,盖板上均匀设有料孔;所述喷淋环与三号进料口可拆卸连通。
20.前述的碳酸钙全自动连续湿法表面处理活化设备中,所述喷淋环包括外环和内环,内环与外环之间设有四根沿圆周均匀分布的连接管;所述外环的内侧壁和内环的外侧壁上均开设有喷淋孔。
21.前述的碳酸钙全自动连续湿法表面处理活化设备中,所述次混料板包括一块栅格板和设于栅格板中部的导料凸块;所述导料凸块前端呈球形,其与喷射管相对应。
22.与现有技术相比,本实用新型通过主体内分隔成多级搅拌区,结合搅拌单元进行搅拌,从而将碳酸钙浆料进入一级、二级和三级搅拌,实现分级多次搅拌,确保其搅拌更充分;
23.通过设置两根回流管路,使得反应过程中部分物料回流到前一搅拌区内,搅拌更充分彻底;最终制备出的活化碳酸钙浆料的活化率高;
24.本技术只需设置一个主体,无需配置多个罐体,相比来说占地面积更小,成本也相对较低。
25.因此,本实用新型采用多级分布连续活化处理,具有限制相对较少,最终活化率高,整套设备占地面积小成本相对较低的优点。
附图说明
26.图1是本实用新型的结构示意图;
27.图2是图1中a处放大图;
28.图3是图1中b处放大图;
29.图4是本实用新型搅拌单元的投影截面图;
30.图5是本实用新型搅拌单元联动机构的投影截面图;
31.图6是本实用新型搅拌单元中主搅拌杆的投影结构图;
32.图7是本实用新型搅拌单元中次搅拌杆的投影结构图;
33.图8是本实用新型次搅拌杆上次搅拌叶片的结构示意图;
34.图9是本实用新型主混料板的结构示意图;
35.图10是本实用新型主混料板的侧面结构示意图;
36.图11是本实用新型主混料板中喷淋环的结构示意图;
37.图12是本实用新型次混料板的结构示意图。
38.附图中的标记为:1-主体,11-一级搅拌区,12-二级搅拌区,13-三级搅拌区,14-调温夹层,15-分隔板,16-喷射口,161-喷射管,162-阀门,2-搅拌电机,21-电机架,22-主搅拌杆,221-主搅拌叶,23-次搅拌杆,231-次搅拌叶,232-搅拌直叶,233-刮料板,26-转动齿轮,27-皮带轮,31-一号进料口,32-二号进料口,33-三号进料口,34-出料口,35-一号回料口,36-四号进料口,37-二号回料口,38-五号进料口,4-主混料板,41-盖板,42-絮状混料管,43-通槽,44-料孔,45-外环,46-内环,47-连接管,5-次混料板,51-栅格板,52-导料凸块。
具体实施方式
39.下面结合附图和实施例对本实用新型作进一步的说明,但并不作为对本实用新型
限制的依据。
40.实施例。碳酸钙全自动连续湿法表面处理活化设备,构成如图1所示,包括呈圆筒状的主体1、设于主体1内的搅拌单元和两块设于主体1内从而将主体1分隔成一级搅拌区11、二级搅拌区12和三级搅拌区13的分隔板15;
41.如图3,每块分隔板15中部都开有喷射口16,其呈做大右小的漏斗状,末端出口处设有带可开闭阀门162的喷射管161,阀门162为电控阀门;通过在喷射口16设置带阀门162的喷射管161,即可起到物料流通通断的作用,又可通过调整阀门162开闭程度来调节物料喷出的速度;
42.搅拌单元包括搅拌电机2、设于主体1内部中心处的主搅拌杆22和四根均匀分布于主搅拌杆22四周的次搅拌杆23,次搅拌杆23相互之间呈90
°
夹角;主体1一级搅拌区11前端的下方设有一号进料口31和二号进料口32,三级搅拌区13后端下方设有出料口34,一号进料口31和二号进料口32分别用于通入碳酸钙原料和表面处理剂;主体1上端设有对应设置的两根回流管路。
43.主体1外侧设有中空的调温夹层14,调温夹层14的右侧下端设有进液口,其左侧上端设有出液口,进液口与出液口分别与调温设备相连通,调温夹层14内部流通有导热油等调温流体。
44.如图,1,三级搅拌区13的末端上方设有一号回料口35,二级搅拌区12的前端上方设有四号进料口36,一号回料口35与四号进料口36之间通过输料管相连;二级搅拌区12的末端上方设有二号回料口37,一级搅拌区11的前端上方设有五号进料口38,二号回料口37与五号进料口38之间通过输料管相连;输料管上设有单向阀,输料管上同样安装有流量计,其数据发送到中控系统进行统计,通过dcs指令配合阀门162、单向阀进行自动控制和调节回流比。
45.如图1和4,主搅拌杆22上设有多个均匀分布的主搅拌叶221,相邻主搅拌叶221之间设有45
°
夹角;次搅拌杆23上设有多个均匀分布的次搅拌叶231,相邻次搅拌叶231之间设有45
°
夹角;次搅拌叶231与主搅拌叶221相互对应设置,确保转动过程中不会出现干涉。
46.如图1、2和5,主体1的左侧端部设有用于安装搅拌电机2的电机架21,搅拌电机2的输出轴通过联轴器与主搅拌杆22相连;主搅拌杆22和设于主搅拌杆22上下两端的次搅拌杆23上设有相互齿合的转动齿轮26;位于主搅拌杆22上下两端的次搅拌杆23上设有位于转动齿轮26外的皮带轮27,位于主搅拌杆22左右两端的次搅拌杆23上设有对应的皮带轮27;上端的皮带轮27与左端的皮带轮27通过皮带相连,对应的,下端的皮带轮27与右端的皮带轮27通过皮带相连;从而实现通过一个搅拌电机2提供动力带动主搅拌杆22和次搅拌杆23联动转动。
47.如图1,次搅拌杆23贯穿分隔板15设于主体1内,所述主搅拌杆22设于一级搅拌区11内;如图7和8,主搅拌叶221为十字形搅拌叶,次搅拌叶231为一字型搅拌叶;主搅拌叶221和次搅拌叶231均由对应数量的搅拌直叶232构成;次搅拌叶231的一端设有与主体1内壁对应抵接的刮料板233,利用刮料板233对主体1内壁进行刮料作业,防止主体1内出现内壁结垢的现象。
48.如图1,二级搅拌区12前端和三级搅拌区13前端分别设有主混料板4和次混料板5;二级搅拌区12下端设有与主混料板4连通的三号进料口33,三号进料口33用于通入表面处
理剂;一级搅拌区11和二级搅拌区12通入的表面处理剂可以是一种或者多种,其根据实际生产需要选择即可;通过两级通入表面处理剂可确保碳酸钙浆料活化更充分,保证其合格率。
49.如图9,所主混料板4包括两块对应设置的盖板41和设于盖板41之间的喷淋环;两块盖板41的中部设有一根絮状混料管42,絮状混料管42内部设有不规则行程的絮状体,从而使得其内部具有不规则的流通通道,使得碳酸钙能与表面处理剂进行混合反应,盖板41的四周分布有与次搅拌杆23对应的通槽43,盖板41上均匀设有料孔44;喷淋环与三号进料口33可拆卸连通。
50.如图10和11,喷淋环包括外环45和内环46,内环46与外环45之间设有四根沿圆周均匀分布的连接管47;外环45的内侧壁和内环46的外侧壁上均开设有喷淋孔,利用喷淋环将表面处理剂喷淋到流经的碳酸钙上,使得碳酸钙与表面处理剂能充分混合。
51.如图12,次混料板5包括一块栅格板51和设于栅格板51中部的导料凸块52;导料凸块52前端呈球形,其与喷射管161相对应。
52.通过主混料板4和次混料板5的设置,在搅拌的基础上对流通的流道进行改进,使得碳酸钙浆料在流动过程中就可与表面处理剂进行混合,进一步提高混合程度,提高活化率。
53.工作原理:
54.碳酸钙料浆(含固量一定)从一号进料口31连续流进一级搅拌区11内,配制好的表面处理剂从二号进料口32按设定的比例流量流进一级搅拌区11内,搅拌电机2驱动主搅拌杆22和次搅拌杆23以一定转速进行搅拌从而对一级搅拌区11内的物料进行一级表面处理;经过搅拌后的物料经喷射口16喷入下一区域,即二级搅拌区12;
55.物料在进入二级搅拌区12时会通过主混料板4,物料无论是经过絮状混料管42还是经过通槽43都会与三号进料口33通入并由喷淋环喷出的表面处理剂相接触并混合,从而进一步提高了物料的活化率;二级搅拌区12同样会对物料进行搅拌,待搅拌后在经喷射口16喷入三级搅拌区13内;
56.在搅拌过程中,部分物料经一号回料口35和二号回料口37分别汇流到二级搅拌区12和一级搅拌区11内,从而使得其能进行再次搅拌混合;直至最终表面处理合格后的活性碳酸钙浆料从出料口34流出进入下一工序。
57.采用本技术,其实现了实现连续化、数据化、自动化生产的物料料浆表面处理生产,且只需一个动力设备(搅拌电机)其动力消耗低,进行多级且回流搅拌处理,表面处理剂利用率高,能实现多组组合生产,其活化率高且产量也高;
58.通过安装流量计等计量设备或者检测设备,相关数据能实时发送到中控系统,然后通过dcs指令,实现自动控制和调节回流比;能控制一级搅拌区11内的活化率达到60—80%,二级搅拌区12内的活化率达到90—95%,三级搅拌区13内的活化率达到100%。