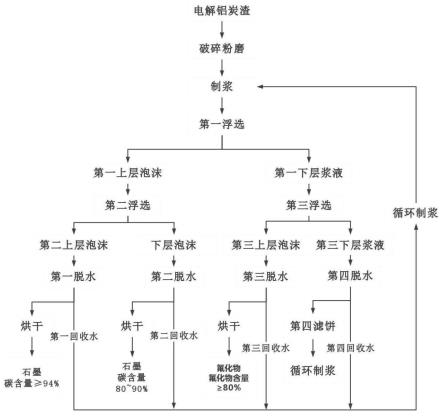
1.本发明涉及固体废弃物回收处理领域,尤其涉及一种从电解铝渣中浮选回收石墨的方法。
背景技术:2.铝是地球上广泛使用的第三大金属,所具有的优良特性使其广泛应用于诸多领域,在金属加工业中,铝是仅次于铁的最常用金属。目前,我国电解铝行业每生产一吨铝,炭渣的产生量大约是15~30kg,据统计2020年我国电解铝累计产量3708.0万吨,由此折合电解铝渣的产生量大约50~100万吨。按照《国家危险废物名录》(2021年版)的规定,电解铝生产过程产生的炭渣属于危险废物,废物代码是321-025-48,危险特性为t,且所述炭渣的主要化学成分为c、na3alf6、alf3、caf2、mgf2、lif、kf、al2o3等,碳含量约为20~40%,其石墨化程度较高,是一种高石墨化的炭。
3.鉴于电解铝渣存在相对比较分散,资源化利用的程度整体不高,现有技术大多采用露天堆放和填埋的方法处理,对环境的影响相当大。部分电解铝厂也零星采用浮选、酸碱浸取、高温煅烧等方法,进行电解铝渣的资源化利用。其中,现有技术中的浮选法处理过程的工艺复杂,且浮选效率偏低,浮选获得石墨产品含碳量低。因此,亟需一种工艺简单、浮选效率高的从电解铝渣中回收得到含碳量高的石墨的方法。
技术实现要素:4.本发明的目的在于提供一种从电解铝渣中浮选回收石墨的方法,本发明提供的从电解铝渣中浮选回收石墨的方法,工艺简单、浮选效率高,能够分别获得碳含量≥94%的石墨、碳含量为80~90%的石墨和氟化物。
5.为了实现上述发明目的,本发明提供以下技术方案:
6.本发明提供了一种从电解铝渣中浮选回收石墨的方法,包括以下步骤:
7.(1)将电解铝渣进行破碎粉磨,得到预处理的电解铝渣;
8.(2)将所述步骤(1)得到的预处理的电解铝渣和水混合后调浆,得到电解铝渣浆液;
9.(3)将所述步骤(2)得到的电解铝渣浆液与捕收剂、表面活性剂、分散剂和起泡剂混合后,进行第一浮选,得到第一上层泡沫和第一下层浆液;
10.(4)将所述步骤(3)得到的第一上层泡沫和水混合后,进行第二浮选,得到第二上层泡沫和下层泡沫;
11.(5)将所述步骤(3)得到的第一下层浆液与捕收剂和起泡剂混合后,进行第三浮选,得到第三上层泡沫和第二下层浆液;
12.(6)分别将所述步骤(4)得到的第二上层泡沫和下层泡沫以及所述步骤(5)得到的第二下层浆液依次进行脱水和烘干,得到碳含量≥94%的石墨、碳含量为80~90%的石墨和氟化物;
13.所述步骤(4)和步骤(5)没有先后顺序之分。
14.优选地,所述步骤(1)中预处理的电解铝渣的粒径≤60目。
15.优选地,所述步骤(2)中的调浆在搅拌的条件下进行,所述搅拌的时间为1~12分钟,所述搅拌的速率为10~1200r/min。
16.优选地,所述步骤(2)中电解铝渣浆液中的电解铝渣的质量分数为8~30%。
17.优选地,所述步骤(3)中电解铝渣浆液中的电解铝渣与捕收剂、表面活性剂、分散剂和起泡剂的质量比为1000:(3~65):(0.1~0.55):(0.3~1.25):(2~6)。
18.优选地,所述步骤(3)中第一浮选的方式为刮泡浮选,所述第一浮选的时间根据捕收剂、表面活性剂、分散剂和起泡剂的总质量进行调整。
19.优选地,所述步骤(4)中第二浮选的方式为刮泡浮选,所述第二浮选的时间根据所述步骤(3)中捕收剂、表面活性剂、分散剂和起泡剂的总质量进行调整。
20.优选地,所述步骤(3)中电解铝渣浆液中的电解铝渣与所述步骤(5)中捕收剂和起泡剂的质量比为1000:(3~8):(0.5~1.5)。
21.优选地,将所述步骤(5)中得到第三上层泡沫进行第四脱水,得到第四回收水和第四滤饼;所述第四回收水直接用于所述步骤(2)中调浆,制备电解铝渣浆液;所述第一滤饼直接作为所述步骤(2)中的预处理的电解铝渣。
22.优选地,将所述步骤(6)中脱水得到的所有回收水直接用于所述步骤(2)中调浆,制备电解铝渣浆液。
23.本发明提供了一种从电解铝渣中浮选回收石墨的方法,首先将电解铝渣进行破碎粉磨,以打破所述电解铝渣中的石墨和氟化物之间的紧密嵌布状态,促使石墨和氟化物之间的充分解离,得到预处理的电解铝渣;将所述预处理的电解铝渣和水混合后调浆,得到电解铝渣浆液;再将所述电解铝渣浆液与捕收剂、表面活性剂、分散剂和起泡剂混合后,进行第一浮选,由于电解铝渣中石墨表面相对地表现为疏水,电解铝渣中氟化物表面相对地表现为亲水,所述捕收剂可以使电解铝渣粘附在捕收剂表面,相应地增加电解铝渣中石墨表面的疏水性,表面活性剂使捕收剂在电解铝渣浆液中更均匀地分散,使得石墨颗粒与捕收剂更紧密的粘附,分散剂与表面活性剂共同作用是使电解铝渣浆液中的固体颗粒的分散效果更好,起泡剂可以增加电解铝渣浆液中气泡的数量和泡沫强度,所述石墨颗粒会在捕收剂的作用下黏附在气泡上,随气泡上浮到液面上,通过包括捕收剂、表面活性剂、分散剂和起泡剂在内的浮选药剂的协同作用,有利于后续的第一浮选将石墨和氟化物分离并分开,提高浮选效率,得到含石墨的第一上层泡沫和含氟化物的第一下层浆液;将所述第一上层泡沫和水混合后进行第二浮选,第一上层泡沫中纯度较高的石墨与纯度较低的石墨在水中分层,利用第二浮选进一步提高回收石墨产品的纯度,回收石墨的同时可以使石墨产品的品级有一定的区分,得到第二上层泡沫和下层泡沫;并且将第一下层浆液与捕收剂和起泡剂混合后进行第三浮选,所述捕收剂可以使第一下层浆液中固体颗粒粘附在捕收剂表面,相应地增加第一下层浆液中的石墨表面的疏水性,起泡剂可以增加第一下层浆液中的气泡的数量和泡沫强度,所述固体颗粒会在捕收剂的作用下黏附在气泡上,随气泡上浮到液面上,通过包括捕收剂和起泡剂在内的浮选药剂协同作用,有利于后续第三浮选将石墨和氟化物进一步分离,以提高浮选效率,得到第三上层泡沫和含氟化物的第二下层浆液;分别将所述第二上层泡沫、下层泡沫与含氟化物的第二下层浆液依次进行脱水和烘干,除去水分,
可以得到碳含量≥94%的石墨、碳含量为80~90%的石墨和氟化物。本发明提供的浮选回收石墨的方法,工艺简单,不用酸碱溶液,从而可以避免部分二次污染,清洁环保、操作条件温和、生产成本较低,能够实现精细浮选,得到三种产品,在高效回收石墨的同时保证石墨产品的质量稳定,并同时高效回收氟化物,满足不同的产品用途和市场需求,基本上做到电解铝渣的全组分利用。其中,所述的氟化物可以循环进入电解铝生产环节作为电解质,实现电解铝行业氟化物的循环利用。实施例的结果显示,利用本发明提供的从电解铝渣中浮选回收石墨的方法,可以得到碳含量为94.06~95.48%的石墨,以及碳含量为86.99~88.64%的石墨,质量分数83.65~87.54%的氟化物,总碳回收率可达79.38%,氟化物回收率可达73.12%。
附图说明
24.图1为本发明提供的从电解铝渣中浮选回收石墨的方法的工艺流程图。
具体实施方式
25.本发明提供了一种从电解铝渣中浮选回收石墨的方法,包括以下步骤:
26.(1)将电解铝渣进行破碎粉磨,得到预处理的电解铝渣;
27.(2)将所述步骤(1)得到的预处理的电解铝渣和水混合后调浆,得到电解铝渣浆液;
28.(3)将所述步骤(2)得到的电解铝渣浆液与捕收剂、表面活性剂、分散剂和起泡剂混合后,进行第一浮选,得到第一上层泡沫和第一下层浆液;
29.(4)将所述步骤(3)得到的第一上层泡沫和水混合后,进行第二浮选,得到第二上层泡沫和下层泡沫;
30.(5)将所述步骤(3)得到的第一下层浆液与捕收剂和起泡剂混合后,进行第三浮选,得到第三上层泡沫和第二下层浆液;
31.(6)分别将所述步骤(4)得到的第二上层泡沫和下层泡沫以及所述步骤(5)得到的第二下层浆液依次进行脱水和烘干,可以得到碳含量≥94%的石墨、碳含量为80~90%的石墨和氟化物;
32.所述步骤(4)和步骤(5)没有先后顺序之分。
33.在本发明中,若无特殊说明,所采用的原料均为本领域常规市售的产品。
34.本发明将电解铝渣依次进行破碎粉磨,得到预处理的电解铝渣。
35.本发明对所述破碎粉磨的方式没有特殊的限制,采用本领域常规的技术方案能够使预处理的电解铝渣的粒径达到要求即可。
36.在本发明中,所述预处理的电解铝渣的粒径优选为≤35目,更优选为≤60目。本发明将预处理的电解铝渣的粒径控制在上述范围内,有利于充分打破所述电解铝渣中的石墨和氟化物之间的嵌布结合状态,促使石墨和氟化物的充分解离,从而有利于后续进行第一浮选,提高浮选效率。
37.得到预处理的电解铝渣后,本发明优选将所述预处理的电解铝渣和水混合后进行调浆,得到电解铝渣浆液。
38.本发明对所述混合的方式没有特殊的限制,实现各组分混合均匀即可。
39.在本发明中,所述调浆优选在搅拌的条件下进行;所述搅拌的时间优选为1~12分钟,更优选为2~10分钟,所述搅拌的速率优选为10~1200r/min,更优选为20~100r/min。本发明将搅拌的时间和速率控制在上述范围内,能够防止搅拌时间过短和速率过低,导致电解铝渣浆液中固体颗粒在水中难以充分分散,能够防止搅拌时间过长导致的由于颗粒效应导致部分微细颗粒二次团聚,影响破碎粉磨解离的效果。
40.在本发明中,所述电解铝渣浆液中的电解铝渣的质量分数优选为5~35%,更优选为8~30%。在本发明中,所述电解铝渣浆液中的电解铝渣的质量分数根据电解铝渣浆液中的固体颗粒的粒度大小进行调整,固体颗粒的粒度较细时,所述电解铝渣浆液中的电解铝渣的质量分数即矿浆浓度不宜过高,否则将不利于固体颗粒在水中完全分散并与后续加入的浮选药剂作用。本发明将电解铝渣浆液中的电解铝渣的质量分数控制在上述范围内,有利于电解铝渣浆液中的固体颗粒分散均匀,并与后续加入的浮选药剂充分作用,提高浮选效率。
41.得到电解铝渣浆液后,本发明将所述电解铝渣浆液与捕收剂、表面活性剂、分散剂和起泡剂混合后,进行第一浮选,得到第一上层泡沫和第一下层浆液。
42.在本发明中,所述捕收剂优选为煤油和柴油中的一种或两种混合使用。在本发明中,当所述捕收剂由煤油和柴油混合使用时,所述煤油与柴油的质量比优选为(1~5):1。在本发明中,由于电解铝渣中石墨表面相对地表现为疏水,电解铝渣中氟化物表面相对地表现为亲水,捕收剂可以使电解铝渣粘附在捕收剂表面,相应地增加电解铝渣中的石墨表面的疏水性,进而通过后续第一浮选中的气泡的作用将石墨和氟化物分离并分开,从而提高浮选效率。
43.在本发明中,所述表面活性剂优选为十二烷基磺酸钠和十二烷基苯磺酸钠中的一种或两种混合。在本发明中,表面活性剂有利于使捕收剂在电解铝渣浆液中更均匀地分散,使得石墨颗粒与捕收剂更紧密的粘附,从而提高石墨的疏水性,进而利用后续第一浮选将石墨和氟化物分离并分开,从而提高浮选效率。
44.在本发明中,所述分散剂优选为六偏磷酸钠和碳酸钠中的一种或两种混合。在本发明中,分散剂与表面活性剂协同作用,使电解铝渣浆液中的固体颗粒的分散效果更好,从而有利于后续第一浮选的进行,提高浮选效率。
45.在本发明中,所述起泡剂优选为仲辛醇和杂醇油中的一种或两种混合。在本发明中,起泡剂可以增加电解铝渣浆液中的气泡的数量和强度,石墨颗粒会在捕收剂的作用下黏附在气泡上,随气泡上浮到液面上,有利于石墨和氟化物的分离,提高浮选效率。
46.在本发明中,所述电解铝渣浆液中的电解铝渣与捕收剂、表面活性剂、分散剂和起泡剂的质量比优选为1000:(3~65):(0.1~0.55):(0.3~1.25):(2~6),更优选为1000:(3~60):(0.15~0.50):(0.3~1.20):(2.5~5.5)。本发明将电解铝渣浆液中的电解铝渣和捕收剂的质量比控制在上述范围内,避免捕收剂用量过低,则无法将炭渣中全部石墨颗粒表面润湿,导致浮选不彻底以及浮选的石墨产品的产率降低,起不到较好的润湿分离效果,同时避免捕收剂用量过高时,会因为捕收剂过量而不加选择的黏附其它组分,导致氟化物也可能被黏附在捕收剂上随气泡进入浮选产品中,影响石墨产品质量。本发明将电解铝渣浆液中的电解铝渣和表面活性剂的质量比控制在上述范围内,避免表面活性剂添加过多会导致捕收剂选择性下降,影响浮选选择性和石墨精矿产品的品质,同时避免表面活性剂的
添加量过少则因为分散不完全,影响捕收剂对目标物的润湿捕获作用,进而降低浮选效果和效率。本发明将电解铝渣浆液中的电解铝渣和分散剂的质量比控制在上述范围内,避免分散剂用量过少时,则会导致电解铝渣浆液中的固体颗粒分散不够充分,致使石墨精矿中夹带一些氟化物,影响浮选选择性和石墨精矿产品的品质,同时避免分散剂用量过多时,会导致电解铝渣浆液的粘度增加,影响浮选作用以及提高生产成本。本发明将电解铝渣浆液中的电解铝渣和起泡剂的质量比控制在上述范围内,避免起泡剂添加量过高时,会因为泡沫过多、气泡尺寸过大而影响浮选过程的选择性,导致氟化物混入捕收剂吸附的石墨颗粒中,影响石墨精矿产品质量,而且会形成大量的气泡造成产品脱水困难,同时避免起泡剂添加量过少,则会造成因为难以产生足够的气泡,而导致浮选的石墨产品的产率下降。
47.在本发明中,所述电解铝渣浆液与捕收剂、表面活性剂、分散剂和起泡剂的混合方式优选为向电解铝渣浆液中加入捕收剂后,进行第一搅拌0.5~3分钟,再同时加入表面活性剂和分散剂,进行第二搅拌2~12分钟,然后加入起泡剂,进行第三搅拌1~10分钟,得到混合物料。
48.本发明对所述第一搅拌、第二搅拌和第三搅拌的速率没有特殊的限制,采用本领域常规速率即可。
49.得到混合物料后,本发明将所述混合物料进行第一浮选,得到第一上层泡沫和第一下层浆液。
50.在本发明中,所述第一浮选的方式优选为刮泡浮选。在本发明中,所述第一浮选的时间优选根据捕收剂、表面活性剂、分散剂和起泡剂的总质量进行调整;所述第一浮选的时间优选随总质量的增大而延长。在本发明中,所述第一浮选的时间优选为2~14分钟,更优选为3~12分钟。在本发明中,第一浮属于粗选,较完全地将电解铝渣浆液中石墨和氟化物分离开,得到含石墨的第一上层泡沫和含氟化物的第一下层浆液。
51.得到第一上层泡沫后,本发明将所述第一上层泡沫和水混合后,进行第二浮选,得到第二上层泡沫和下层泡沫。
52.在本发明中,所述水的用量优选根据第一上层泡沫的石墨含量调整,避免水的用量过少,不利于后续第二浮选进行。
53.在本发明中,所述第一上层泡沫和水的混合方式优选为向第一上层泡沫中加入水,搅拌1~10分钟。
54.在本发明中,所述第二浮选的方式优选为刮泡浮选。在本发明中,所述第二浮选的时间优选根据上述捕收剂、表面活性剂、分散剂和起泡剂的总质量进行调整;所述第二浮选的时间优选随总质量的增大而延长。在本发明中,第二浮选的时间优选为1~10分钟,更优选为2~8分钟。在本发明中,第二浮选可进一步提高石墨产品纯度,回收石墨的同时可以使石墨产品的品级有一定的区分,第二浮选得到的第二上层泡沫经后处理得到含碳量94%以上的石墨,碳回收率可达50%以上,第二浮选得到的下层泡沫经后处理得到含碳量80~90%的石墨,石墨的总回收率60%以上,获得纯度均较高的两种不同的石墨。
55.得到第二上层泡沫后,本发明优选将所述第二上层泡沫进行第一脱水,得到第一滤饼和第一回收水。
56.本发明对所述脱水的方式没有特殊的限制,采用本领域常规技术方案即可。在本发明中,所述脱水的设备优选为板框压滤机和离心脱水机。
57.得到第一滤饼后,本发明将所述第一滤饼进行第一烘干,得到碳含量≥90%的石墨。
58.本发明对所述第一烘干的方式没有特殊的限制,采用本领域常规技术方案即可。在本发明中,所述第一回收水后优选直接用于调浆,制备电解铝渣浆液。在本发明中,当将第一回收水直接用于调浆,制备电解铝渣浆液时,优选根据第一回收水中浮选药剂(即捕收剂、表面活性剂、分散剂和起泡剂)的含量,调节后续浮选过程中的浮选药剂的用量。
59.得到下层泡沫后,本发明优选将所述下层泡沫进行第二脱水,得到第二滤饼和第二回收水。
60.本发明对所述第二脱水的方式没有特殊的限制,采用本领域常规技术方案即可。在本发明中,所述第二脱水的设备优选为板框压滤机和离心脱水机。
61.得到第二滤饼后,本发明将所述第二滤饼进行第二烘干,得到碳含量为80~90%的石墨。
62.本发明对所述第二烘干的方式没有特殊的限制,采用本领域常规技术方案即可。在本发明中,所述第二回收水后优选直接用于调浆,制备电解铝渣浆液。在本发明中,当将第二回收水直接用于调浆,制备电解铝渣浆液时,优选根据第二回收水中浮选药剂(即捕收剂、表面活性剂、分散剂和起泡剂)的含量,调节后续浮选过程中的浮选药剂的用量。
63.得到第一下层浆液后,本发明将所述第一下层浆液与捕收剂和起泡剂混合后,进行第三浮选,得到第三上层泡沫和第二下层浆液。
64.在本发明中,所述捕收剂优选为煤油和柴油中的一种或两种混合。在本发明中,当所述捕收剂由煤油和柴油混合使用时,所述煤油与柴油的质量比优选为(1~5):1。在本发明中,捕收剂可以使第一下层浆液中固体颗粒粘附在捕收剂表面,相应地增加第一下层浆液中的石墨表面的疏水性,进而通过后续第三浮选中的气泡的作用将石墨和氟化物分离并分开,从而提高浮选效率。
65.在本发明中,所述起泡剂优选为仲辛醇和杂醇油中的一种或两种混合。在本发明中,起泡剂增加浆液中的气泡数量和泡沫强度,所述固体颗粒会在捕收剂的作用下黏附在气泡上,随气泡上浮到液面上,有利于石墨和氟化物的分离,提高浮选效率。
66.在本发明中,所述电解铝渣浆液中的电解铝渣、捕收剂和起泡剂的质量比优选为1000:(3~45):(2~6),更优选为1000:(3~40):(2.5~5.5),进一步优选为1000:(3~38):(2.5~5.0)。本发明将电解铝渣浆液中的电解铝渣和捕收剂的质量比控制在上述范围内,避免捕收剂用量过低,则无法将第一下层浆液中全部石墨颗粒表面润湿,导致浮选不彻底,起不到较好的润湿分离效果,降低氟化物产品的质量,同时避免捕收剂用量过高时,会因为捕收剂过量而不加选择的黏附其它组分,导致氟化物也可能被黏附在捕收剂上随气泡进入浮选产品中,降低氟化物产品产率。本发明将电解铝渣浆液中的电解铝渣和起泡剂的质量比控制在上述范围内,避免起泡剂添加量过高时,会因为泡沫过多、气泡尺寸过大而影响浮选过程的选择性,导致氟化物混入捕收剂吸附的石墨颗粒中,降低氟化物产品产率,而且会形成大量的气泡造成产品脱水困难,同时避免起泡剂添加量过少,则会造成因为难以产生足够的气泡,而导致浮选不彻底,降低氟化物产品的质量。
67.在本发明中,所述电解铝渣浆液与捕收剂和起泡剂的混合方式优选为向第一下层浆液中加入捕收剂后,进行第四搅拌0.5~6分钟,然后加入起泡剂,进行第五搅拌0.5~7分
钟。
68.本发明对所述第四搅拌和的第五搅拌速率没有特殊的限制,采用本领域常规速率即可。
69.在本发明中,所述第三浮选的方式优选为刮泡浮选。在本发明中,所述第三浮选的时间优选根据捕收剂和起泡剂的总质量进行调整;所述第三浮选的时间优选随总质量的增大而延长。在本发明中,第三浮选的时间优选为0.5~10分钟,更优选为1~8分钟。在本发明中,第三浮选可进一步分离第一下层浆液中的石墨和氟化物,提高氟化物产品纯度,回收氟化物的同时可以使氟化物产品的品级有一定的区分。
70.在本发明中,上述第二浮选和第三浮选没有先后顺序之分。
71.得到第二下层浆液后,本发明优选将所述第二下层浆液进行第三脱水,得到第三滤饼和第三回收水。
72.本发明对所述第三脱水的方式没有特殊的限制,采用本领域常规技术方案即可。在本发明中,所述第三脱水的设备优选为板框压滤机和离心脱水机。
73.得到第三滤饼后,本发明将所述第三滤饼进行第三烘干,得到氟化物。
74.本发明对所述第三烘干的方式没有特殊的限制,采用本领域常规技术方案即可。在本发明中,所述第三回收水优选直接用于调浆,制备电解铝渣浆液。在本发明中,当将第三回收水直接用于调浆,制备电解铝渣浆液时,优选根据第三回收水中浮选药剂(即捕收剂、表面活性剂、分散剂和起泡剂)的含量,调节后续浮选过程中的浮选药剂的用量。
75.得到第三上层泡沫后,本发明优选将第三上层泡沫进行第四脱水,得到第四滤饼和第四回收水。
76.在本发明中,所述第四滤饼优选直接作为所述预处理的电解铝渣。在本发明中,所述第四回收水优选直接用于调浆,制备电解铝渣浆液。在本发明中,当将第四回收水直接用于调浆,制备电解铝渣浆液时,优选根据第四回收水中浮选药剂(即捕收剂、表面活性剂、分散剂和起泡剂)的含量,调节后续浮选过程中的浮选药剂的用量。
77.下面将结合本发明中的实施例,对本发明中的技术方案进行清楚、完整地描述。显然,所描述的实施例仅仅是本发明一部分实施例,而不是全部的实施例。基于本发明中的实施例,本领域普通技术人员在没有做出创造性劳动前提下所获得的所有其他实施例,都属于本发明保护的范围。
78.本发明提供的从电解铝渣中浮选回收石墨的方法的工艺流程图如图1所示,其中,首先将电解铝渣进行破碎粉磨,得到预处理的电解铝渣,然后将所述预处理的电解铝渣和水混合后,进行调浆,得到电解铝渣浆液,加入捕收剂、表面活性剂、分散剂和起泡剂后,进行第一浮选,得到第一上层泡沫和第一下层浆液,将所述第一上层泡沫和水混合后,进行第二浮选,得到第二上层泡沫和下层泡沫;将所述第二上层泡沫进行第一脱水,得到第一滤饼和第一回收水,将所述第一滤饼进行第一烘干,得到碳含量≥94%的石墨,将第一回收水循环使用,直接用于调浆,制备电解铝渣浆液;将所述下层泡沫进行第二脱水,得到第二滤饼和第二回收水,将所述第二滤饼进行第二烘干,得到碳含量为80~90%的石墨,将第二回收水循环使用,直接用于调浆,制备电解铝渣浆液;将所述第一下层浆液与捕收剂和起泡剂混合后,进行第三浮选,得到第三上层泡沫和第二下层浆液;将第三上层泡沫进行第四脱水,得到第四滤饼和第四回收水,将所述第四滤饼优选循环使用,直接作为所述预处理的电解
铝渣,将所述第四回收水循环使用,直接用于调浆,制备电解铝渣浆液;将所述第二下层浆液进行第三脱水,得到第三滤饼和第三回收水,将所述第三滤饼进行第三烘干,得到氟化物,所述第三回收水循环使用直接用于调浆,制备电解铝渣浆液;将第一回收水、第二回收水、第三回收水和第四回收水循环使用,直接用于调浆,制备电解铝渣浆液。
79.实施例1
80.一种从电解铝渣中浮选回收石墨的方法
81.(1)将100g电解铝渣进行破碎粉磨,得到粒径≤60目的预处理的电解铝渣;
82.(2)将所述步骤(1)得到的预处理的电解铝渣和水混合后,在1000r/min下搅拌5分钟进行调浆,得到电解铝渣浆液;
83.所述电解铝渣浆液中的电解铝渣的质量分数为10%;
84.(3)向所述步骤(2)得到的电解铝渣浆液中加入2.4g捕收剂后,进行第一搅拌1分钟,再加入0.048g十二烷基磺酸钠表面活性剂和0.1g六偏磷酸钠分散剂,进行第二搅拌5分钟,然后加入0.48g仲辛醇起泡剂,进行第三搅拌3分钟,得到混合物料,进行刮泡浮选即第一浮选5分钟,得到第一上层泡沫和第一下层浆液;
85.所述步骤(3)中电解铝渣浆液中的电解铝渣与捕收剂、表面活性剂、分散剂和起泡剂的质量比为1000:24:0.48:1:4.8;
86.所述捕收剂由质量比2:1的煤油与柴油混合组成;
87.(4)向所述步骤(3)得到的第一上层泡沫加入900g水,搅拌4分钟后,进行刮泡浮选即第二浮选3分钟,得到第二上层泡沫和下层泡沫;
88.(5)向所述步骤(3)得到的第一下层浆液加入0.6g煤油捕收剂,进行第四搅拌2分钟,然后加入0.12g仲辛醇起泡剂,进行第五搅拌2分钟,进行刮泡浮选即第三浮选2分钟,得到第三上层泡沫和第二下层浆液;
89.所述步骤(3)中电解铝渣浆液中的电解铝渣与所述步骤(5)中捕收剂和起泡剂的质量比为1000:6:1.2;
90.将第三上层泡沫进行第四脱水,得到第四滤饼和第四回收水,将所述第四滤饼优选循环使用,直接作为所述预处理的电解铝渣,将所述第四回收水循环使用,直接用于所述步骤(2)中调浆,制备电解铝渣浆液;
91.(6)将所述步骤(4)得到的第二上层泡沫进行第一脱水,得到第一滤饼和第一回收水,将所述第一滤饼进行第一烘干,得到22.80g的碳含量质量分数为94.06%的石墨,将第一回收水循环使用,直接用于所述步骤(2)中调浆,制备电解铝渣浆液;
92.将所述步骤(4)得到的下层泡沫进行第二脱水,得到第二滤饼和第二回收水,将所述第二滤饼进行第二烘干,得到7.92g的碳含量质量分数为88.64%的石墨,将第二回收水循环使用,直接用于所述步骤(2)中调浆,制备电解铝渣浆液;
93.将所述步骤(5)得到的第二下层浆液进行第三脱水,得到第三滤饼和第三回收水,将所述第三滤饼进行第三烘干,得到50.34g的质量分数为83.87%的氟化物,所述第三回收水循环使用直接用于所述步骤(2)中调浆,制备电解铝渣浆液。
94.将第一回收水、第二回收水、第三回收水和第四回收水循环使用,直接用于所述步骤(2)中调浆,制备电解铝渣浆液时,根据第一回收水、第二回收水、第三回收水和第四回收水中浮选药剂(即捕收剂、表面活性剂、分散剂和起泡剂)的含量,调节适当减少后续浮选过
程中的浮选药剂的用量;
95.所述步骤(4)和步骤(5)没有先后顺序之分。
96.实施例2
97.按照实施例1的方法从电解铝渣中浮选回收石墨,具体结果见表1;
98.与实施例1不同的是,所述步骤(3)中加入6g煤油捕收剂后,进行第一搅拌1分钟,再加入0.048g十二烷基磺酸钠表面活性剂和0.1g碳酸钠分散剂,进行第二搅拌9分钟,然后加入0.48g杂醇油起泡剂,进行第三搅拌3分钟,得到混合物料;所述步骤(3)中电解铝渣浆液中的电解铝渣与捕收剂、表面活性剂、分散剂和起泡剂的质量比为1000:60:0.48:1:4.8。
99.实施例3
100.按照实施例1的方法从电解铝渣中浮选回收石墨,具体结果见表1;与实施例1不同的是,所述步骤(3)中加入2.4g柴油捕收剂后,进行第一搅拌1分钟,再加入0.048g十二烷基磺酸钠表面活性剂和0.1g碳酸钠分散剂,进行第二搅拌9分钟,然后加入0.48g杂醇油起泡剂,进行第三搅拌3分钟,得到混合物料;所述步骤(3)中电解铝渣浆液中的电解铝渣与捕收剂、表面活性剂、分散剂和起泡剂的质量比为1000:24:0.48:1:4.8。
101.实施例4
102.按照实施例1的方法从电解铝渣中浮选回收石墨,具体结果见表1;与实施例1不同的是,电解铝渣用量为150g,电解铝渣浆液中的电解铝渣的质量分数为15%,所述步骤(3)中加入3.6g捕收剂后,进行第一搅拌1分钟,再加入0.072g十二烷基磺酸钠表面活性剂和0.15g六偏磷酸钠分散剂,进行第二搅拌5分钟,然后加入0.72g仲辛醇起泡剂,进行第三搅拌3分钟,得到混合物料,进行第一刮泡浮选5分钟,得到第一上层泡沫和第一下层浆液;所述捕收剂由质量比2:1的煤油与柴油混合组成;所述步骤(3)中电解铝渣浆液中的电解铝渣与捕收剂、表面活性剂、分散剂和起泡剂的质量比为1000:24:0.48:1:4.8;
103.所述步骤(5)中加入0.9g煤油捕收剂,进行第四搅拌2分钟,然后加入0.18g仲辛醇起泡剂;所述步骤(3)中电解铝渣浆液中的电解铝渣与所述步骤(5)中捕收剂和起泡剂的质量比为1000:6:1.2。
104.表1为实施例1~4获得的石墨的碳含量和回收率,以及氟化物的质量分数和回收率,其中,利用灰分测试检测碳含量;碳回收率的计算过程为石墨产品石墨含量与原样中石墨含量之比;总碳回收率的计算过程为各部分石墨产品碳回收率之和;利用氟离子交换法检测氟化物质量分数;氟化物回收率的计算过程为氟化物产品中氟化物含量与原样中氟化物含量之比。
105.表1实施例1~4获得的石墨的碳含量和回收率,以及氟化物的质量分数和回收率
[0106][0107]
由实施例和表1可知,利用本发明提供的从电解铝渣中浮选回收石墨的方法,可以得到碳含量为94.06~95.48%的石墨,以及碳含量为86.99~88.64%的石墨,质量分数83.65~87.54%的氟化物,总碳回收率可达79.38%,氟化物回收率可达73.12%。本发明首先将电解铝渣进行破碎粉磨,以打破所述电解铝渣中的石墨和氟化物之间的嵌布结合状态,促使石墨和氟化物的充分解离,从而有利于后续进行第一浮选,提高浮选效率,得到预处理的电解铝渣,经调浆,得到电解铝渣浆液,加入捕收剂、表面活性剂、分散剂和起泡剂,进行第一浮选,通过包括捕收剂、表面活性剂、分散剂和起泡剂在内的浮选药剂协同作用,有利于后续第一浮选将石墨和氟化物分离并分开,以提高浮选效率,得到第一上层泡沫和第一下层浆液;将所述第一上层泡沫进行第二浮选,提高后续得到石墨产品的纯度,得到第二上层泡沫和下层泡沫;并且将第一下层浆液与捕收剂和起泡剂混合后进行第三浮选,通过包括捕收剂和起泡剂在内的浮选药剂协同作用,有利于后续第三浮选将石墨和氟化物进一步分离,以提高浮选效率,得到第三上层泡沫和第二下层浆液;分别将所述第二上层泡沫、下层泡沫与含氟化物的第二下层浆液依次进行脱水和烘干,除去水分,得到相应的碳含量≥94%的石墨、碳含量为80~90%的石墨和氟化物。
[0108]
以上所述仅是本发明的优选实施方式,应当指出,对于本技术领域的普通技术人员来说,在不脱离本发明原理的前提下,还可以做出若干改进和润饰,这些改进和润饰也应视为本发明的保护范围。