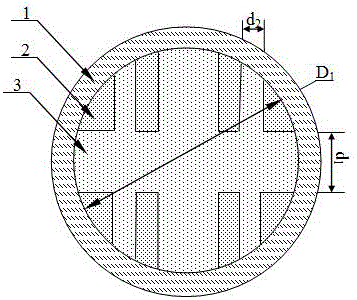
本发明涉及一种含酸原油的加氢处理方法,尤其是采用上流式加氢工艺技术处理含酸原油的方法。
背景技术:
:石油中通常含有酸类化合物,主要是以环烷酸的形式存在。石油中酸的浓度或含量使用总酸值来表示。总酸值(tan)是指中和1克原油或石油馏分所有酸性组分所需要的氢氧化钾(koh)的毫克数,单位是mgkoh/g。在石油炼制过程中,石油中的环烷酸可以直接与铁发生反应,造成加热炉管等炼油设备腐蚀;也可以与炼油设备上的保护膜fes发生反应,使金属设备露出新的表面,受到新的腐蚀。目前,普通的炼油设备仅能加工总酸值小于0.3mgkoh/g的含酸烃油,而当含酸烃油中的总酸值超过1mgkoh/g时,设备腐蚀会非常严重;总酸值达到0.5mgkoh/g时就会对炼油设备造成显著腐蚀。由于含酸原油的腐蚀性,炼厂通常不愿意加工酸值大于1mgkoh/g的原油。高酸原油是典型的劣质廉价原油,在全球新发现和新开发的油田中,重质和劣质的高酸原油占较大比例。2012年,全球高酸原油产量超过4亿吨,占原油总产量的10%。同样在国际原油市场上造成高酸原油供过于求的现象,高酸原油价格也普遍较低,尽管加工高酸原油可能会引起诸多问题,但是可以看出采用高效经济的技术手段对其进行预处理,高酸原油加工将具有好的经济效益。近年来,随着原油资源日趋重质化、高酸值化以及化学或微生物采油技术的广泛应用,使得原油中金属离子的种类和含量不断上升,其中以钙离子含量日趋增多。例如,中国辽河稠油的总酸值为2.10mgkoh/g,钙含量高达284μg/g,苏丹混合原油酸值13.82mgkoh/g,钙含量最高可达1600μg/g。绝大多数原油中钙含量与酸值存在着一定的对应关系,酸值增加,钙含量也增加。高酸原油中的钙大部分以环烷酸钙形式存在,环烷酸钙易溶于油而难溶于水,在脱盐过程中不能被脱除。目前世界原油市场上含酸原油的产量每年约占全球原油总产量的5%左右,并且每年还以0.3%的速度增长。因此,如何有效地对高金属含酸原油进行处理,是目前面临的重大课题。随着含酸原油开采量的增加,由含酸烃油引起的设备腐蚀问题也越来越受到人们的关注。含酸烃油脱酸的方法一般有物理吸附、溶剂抽提、化学转化,最常用的还是化学转化方法,如热解、加氢脱酸等。加氢脱酸是含酸烃油中的石油酸和氢气反应脱去羧基生成烃和水的方法。us5897769首先提出使用工业化生产的小孔加氢精制催化剂,在反应温度200〜370°c、液时空速0.1〜10h-1、氢分压345〜3450kpa和氢油比10〜100的条件下,能够选择性脱除原油中相对分子质量小于450的环烷酸,脱酸率最高可达到91.6%。us5910242介绍,若将上述加氢精制催化剂先进行预硫化或者在氢气中加入摩尔分数为4%的h2s,还可以提高原油中的环烷酸的脱酸率。上流式反应器工艺特征是油气混合物进料从反应器底部向上通过上流式催化剂床层,并且在反应器内是液相连续,气相呈鼓泡形式通过,使整个催化剂床层轻微膨胀,金属和焦炭等沉积物可以均匀地沉积在整个催化剂床层,避免集中在某一局部,较好地发挥了所有催化剂的性能,减缓催化剂床层压降的快速增长。该技术可用于原油的脱酸,但是采用常规的上流式催化剂加工劣质含酸原油,由于铁钙含量以及固体颗粒含量高容易堵塞前部催化剂床层,造成运行周期短、催化剂失活快等难题。cn104560134a提出一种含酸烃油加工方法,含酸烃油经过加热或者换热至160〜220℃后分为两路,其中,第一路含酸烃油与氢气混合后进入沸腾床反应器,第二路含酸烃油与沸腾床反应器在线置换的循环物料混合后通过反应器分布器上部的入口进入沸腾床反应器,第一路含酸烃油和第二路含酸烃油与催化剂接触进行反应,反应生成物经冷却分离后得到气体和液体产物。cn101240189a公开了一种含酸原油的固定床加氢处理方法。该方法是在加氢反应器中装填的加氢催化剂至少包括两个或两个以上催化剂床层,上部催化剂床层装填大孔径加氢保护催化剂,下部催化剂床层装填双峰孔加氢催化剂。双峰孔加氢催化剂中,孔直径主要集中在5~10nm和10~20nm。上述催化加氢脱酸的方法,存在原料适应性差,在加工劣质高酸、高钙劣质含酸原油时,在反应器顶部容易引起结焦、板结问题,导致催化剂失活快,装置运行周期大幅缩短。技术实现要素:为了克服现有技术中的不足之处,本发明提供了一种含酸原油的加氢处理方法,该方法采用特定的催化剂以及上流式加氢工艺技术处理含酸原油,具有良好的加氢脱酸性能和脱容金属能力,同时具有一定的脱硫和残炭及沥青质转化能力,加氢活性高,装置运转周期长。而且,本发明可以将该单一品种催化剂应用于上流式反应器中,克服了目前上流式反应器中催化剂种类多,装卸繁琐及不同种类催化剂返混等问题。本发明提供了一种含酸原油的加氢处理方法,包括至少一个上流式加氢反应器,其中,含酸原油和氢气进入所述上流式加氢反应器进行加氢反应,得到加氢脱酸后的产物;所述上流式加氢反应器内至少装填如下一种加氢处理催化剂;所述的加氢处理催化剂,包括载体和活性组分,其中所述载体具有三维贯通孔道的球形,该载体具有七个通孔,其中通过球心的x轴、y轴和z轴方向各设置有一个通孔即中间通孔三个,且在x轴、y轴和z轴中的两个方向上还设有与相同方向上中间通孔平行且分布于中间通孔两侧的侧通孔四个,侧通孔之间以及侧通孔与第三个方向上的中间通孔相互贯通,其中球形外直径为6.0~10.0mm,中间通孔的孔直径为球形外直径的25%~40%,侧通孔的孔直径为球形外直径的10%~20%。本发明所述加氢处理催化剂中,所述通孔可以为任何形状,优选为圆柱形通孔。本发明所述加氢处理催化剂中,所述活性金属组分包括第二金属组分即第ⅵb族金属元素和第三金属组分即第ⅷ族金属元素。本发明所述加氢处理催化剂载体,以al2o3-sio2为载体,其中sio2重量含量为20%~50%,优选为30%~40%。本发明所述加氢处理催化剂中,所述活性金属组分第ⅵb族金属元素优选为mo,第ⅷ族金属元素优选为ni和/或co。其中,以催化剂的重量为基准计,第二金属组分以氧化物计的含量为1.0%~10.0%,优选为1.5%~6.5%,第一金属组分和第三金属组分的总含量以氧化物计为3.0%~10.0%,优选为4.0%~8.0%,氧化硅的含量为25.0%~35.0%,氧化铝的含量为55.0%~65.0%,第三金属组分与第二金属组分的以原子计摩尔比为1.5:1~4.5:1。本发明所述加氢处理催化剂中,载体优选还含有第一金属组分氧化物,所述第一金属组分氧化物为nio。所述第一金属组分氧化物nio与al2o3的摩尔比为0.03:1~0.13:1,优选为0.05:1~0.11:1。本发明所述加氢处理催化剂载体,其性质如下:比表面积为100~200m2/g,孔容为0.70ml/g以上,优选0.75~1.15ml/g,孔直径20~100nm所占的孔容为总孔容的35%~60%,平均孔直径为18nm以上,优选为20~30nm。本发明所述加氢处理催化剂的制备方法,包括:(1)向硅源中加入酸性胶溶剂,进行酸化处理;(2)向步骤(1)中加入拟薄水铝石、固化剂,配制成膏状物料;(3)将步骤(2)所得膏状物料加入模具中,再将盛有膏状物料模具加热一定时间,使膏状物料固化成型;(4)将步骤(3)物料脱出模具,经洗涤、干燥、焙烧,得到催化剂载体;(5)将步骤(4)所得载体浸渍负载催化剂活性金属组分,再经干燥、焙烧,得到加氢处理催化剂。本发明所述加氢处理催化剂的制备方法中,载体中优选引入第一金属氧化物,可以在步骤(1)和/或步骤(2)中引入第一金属源(镍源),优选引入方法具体如下:向步骤(1)所得的物料中加入镍源,并使之溶解于物料中。镍源可以采用可溶性镍盐,其中可溶性镍盐可以为硝酸镍、硫酸镍、氯化镍中的一种或几种,优选硝酸镍。本发明所述加氢处理催化剂的制备方法中,步骤(1)中所述硅源为水玻璃、硅溶胶中的一种或几种,其中硅以氧化硅计的质量含量为20%~40%,优选25%~35%;所述酸性胶溶剂为硝酸、甲酸、醋酸、柠檬酸中的一种或几种,优选为硝酸,所述酸性胶溶剂的质量浓度为55%~75%,优选60%~65%;酸性胶溶剂加入量以氢离子与二氧化硅的摩尔比为1:1.0~1:1.5;所述硅源进行酸化处理后的ph值为1.0~4.0,优选1.5~2.5。本发明所述加氢处理催化剂的制备方法中,步骤(2)所述拟薄水铝石的干基重量为70%以上,经高温焙烧转化为γ-al2o3后的性质如下:孔容为0.95ml/g以上,优选孔容为0.95~1.2ml/g,比表面积为270m2/g以上,优选比表面积为270~330m2/g。所述固化剂为尿素、有机铵盐中的一种或多种。所述有机铵盐为六次甲基四铵。所述固化剂的加入量以氮原子与二氧化硅的摩尔比为1:1.5~1:2.0;所述配制成膏状物料中固含量以二氧化硅、氧化铝重量计为25%~45%,优选28%~40%,其膏状物料应具有一定流动性的可塑体。本发明所述加氢处理催化剂的制备方法中,步骤(3)所述模具包含带有球形空腔的壳体和能形成贯通通道的导模,壳体选用刚性材质,外部形状可以为任意形状,优选为球形等对称几何形状。本发明以外部形状是球形为例进行说明,球形壳体可由两个完全相同的半球体组成,也可以由四个四分之一球体组成。球形空腔的直径可以根据催化剂颗粒的大小来调节,可以为6.0~20.0mm。所述导模选用加热或燃烧可除掉的物质,比如石墨、木材、纸、石蜡或石油树脂等。所述导模的结构与载体中的三维贯通的孔道相配,即除去导模后所产生的孔道即为通孔。本发明所述加氢处理催化剂的制备方法中,步骤(3)首先将各部分球形壳体相互固定,使之成为两个完整的半球体空腔,将能三维贯通的孔道的导模放入一个半球体空腔内,这时将膏状物料注入或压入两个半球体空腔,充满整个空腔后将两个半球体合在一起形成一个完整的球体并固定。本发明所述加氢处理催化剂的制备方法中,步骤(3)将盛有膏状物料模具加热温度为70~200℃,优选100~150℃,恒温时间为30~240分钟,优选50~120分钟,使物料固化。本发明所述加氢处理催化剂的制备方法中,步骤(4)中脱出模具,即取下壳体由于模具中膏状物料受热后释放碱性气体,使膏状物料固化并收缩后自动脱模。步骤(4)中,所述洗涤是用去离子水将脱模后的球状物料洗涤至中性。所述干燥温度为100~150℃,干燥时间为4~10小时。所述焙烧温度为500~900℃,优选为550~800℃,焙烧时间为2~8小时。其中,在焙烧过程中将导模除去,留下三维贯通的孔道,而导模焙烧过程中释放的气体也能达到催化剂载体扩孔的目的。本发明所述加氢处理催化剂的制备方法中,所述步骤(5)中载体浸渍催化剂活性金属组分后的干燥和焙烧条件如下:在100~150℃干燥4~10小时,再在400~600℃焙烧2~6小时。本发明含酸原油的加工处理方法中,采用至少一个上流式加氢反应器,一般采用一个或两个上流式加氢反应器。所述一个上流式加氢反应器内至少装填本发明的一种加氢处理催化剂,优选至少有两个催化剂床层,且各催化剂床层装填同一种本发明加氢处理催化剂。本发明的含酸原油的加氢处理方法中,所述一个上流式反应器优选设置2~5个催化剂床层,各催化剂床层优选采用本发明同一种加氢处理催化剂。反应器内各个床层高度可适当调整。所述一个上流式反应器设置两个催化剂床层时,下部为第一床层,上部为第二床层,其中第一床层占该上流式反应器内催化剂总装填体积的35%~50%,第二床层占该上流式反应器内催化剂总装填体积的50%~65%。所述一个上流式反应器设置三催化剂床层时,下部为第一床层,中部为第二床层,上部为第三床层,第一床层占该上流式反应器内催化剂总装填体积的20%~30%,第二床层占该上流式反应器内催化剂总装填体积的25%~35%,第三床层占该上流式反应器内催化剂总装填体积的30%~45%。根据加工原料的不同,床层高度可以设置相同,也可以不同。本发明提供的含酸原油的加工处理方法,其中,上流式加氢反应器采用的操作条件如下:反应温度为200~400℃,优选为240~350℃;氢分压为3~20mpa,优选为5~15mpa;液时体积空速为0.1~10h-1,优选为1~5h-1;氢油体积比100~400,优选为150~350。所述的含酸原油可以为高酸值原油、拔头高酸原油或高酸值原料油与重油和∕或渣油的混合物,也可以为高酸值原油与低酸值原油的混合物,含酸原油的总酸值大于0.5mgkoh/g,进一步可大于1.0mgkoh/g。本发明尤其适合处理劣质高酸、高铁、高钙等高金属含量的劣质含酸原油。本发明含酸原油的加工处理方法中,原料油进入上流式反应器前,需经过预处理,所述的预处理过程为常规的原油脱盐、脱水等过程,除去原油中大部分盐类物质、水等。本发明方法中,经加氢脱酸后的产物的加工方案可根据原油性质、市场对产品的需求、经济效益以及环保要求等因素来确定。本发明推荐采用如下方法之一处理,其中所述轻质馏分通常是指汽油、柴油馏分:(1)加氢脱酸后的产物经气液分离后,所得的液相产物送到常压分馏装置,得到轻质馏分和常压渣油。常压渣油可作为渣油加氢处理原料在更高的温度和压力下进行深度加氢精制,分离所得的加氢常渣可作为下游催化裂化进料;(2)加氢脱酸后的产物经气液分离后,所得的液相产物送到减压分馏装置进行分馏,得到轻质馏分、减压瓦斯油和减压渣油。减压渣油可作为焦化的进料,由于经过加氢脱酸除去了部分硫等杂质,因而可得到高价值的低硫石油焦。与现有技术相比,本发明的优点在于:1、本发明的上流式加氢处理反应器内至少使用一种本发明具备独特的外形和孔结构的加氢处理催化剂,不但具有较高的机械强度和耐磨性能,而且还具有如下特点:(1)具有良好的扩散通道和反应通道,能够消除扩散对反应的影响,并使反应更加高效,催化剂利用效果更好;(2)具有良好的抗结焦和床层热稳定性;(3)具备良好加氢脱酸能力;(4)具有良好的脱金属杂质能力,同时还具有一定的脱硫氮和残炭杂质的能力。2、本发明方法在上流式加氢反应器中装填具备独特的外形和孔结构的加氢处理催化剂,既能够脱除高酸原油中存在大量的铁、钙等金属悬浮物及积炭类杂质等,也能防止高酸原油中镍和钒等重金属杂质堵孔,延长催化剂的使用寿命及装置的运转周期。另外,催化剂具备一定的加氢能力,在加氢处理环境下取得良好的脱酸效果。3、采用本发明方法,优选在上流式加氢反应器内,装填相同的本发明加氢处理催化剂,由于沿着反应物流的方向,物料性质逐步改善,加氢反应是放热反应,反应温度会逐步提高,而且后部催化剂床层在整个反应过程中处于氢气量较少的环境下,采用大孔径低耗氢的上流式催化剂有利于催化剂床层的稳定和催化剂性能的发挥。另外,沿着反应物流方向反应温度逐步提高,如果在温度较高的反应区,采用较高活性的催化剂,更容易引起床层局部的缺氢反应,容易导致床层热点的产生和床层的波动。因此,对于上流式反应器可通过催化剂活性的控制,使其能够实现活性和稳定性的平衡。4、在上流式加氢反应器中,尽管不如沸腾床反应器内物料处于强烈返混状态。但由于其物流流向特点和催化剂床层的微膨胀状态,如果采用固定床加氢技术中在同一催化剂床层采用不同催化剂级配技术,易引起床层返混和床层反应的波动,对装置的稳定运行产生不利影响。5、本发明的上流式加氢处理催化剂具有良好的容铁钙能力和脱容金属的能力,得益于催化剂的优化的孔道设计和载体结构的优化,该催化剂除了具备较高的性能的脱酸能力同时,具有一定的脱金属、脱硫和残炭及沥青质转化能力,因此该催化剂具有长周期稳定运行的特点。特别是高酸原油中存在大量的铁、钙等金属悬浮物,还有积炭类杂质,效果更为显著。附图说明图1为本发明渣油加氢处理催化剂载体制备过程的示意剖面图;图2为形成模具壳体的半球形空腔模具示意图;图3为形成贯通通道的导模模具示意图;图4制备的催化剂载体剖面示意图;附图标记说明如下:1.模具壳体;2.膏状物料;3.能形成贯通通道的导模;4.空腔;5.横穿“十字”的圆柱体;6.中间大的“十字”体;7.两侧小的“十字”体;8.贯通通道。具体实施方式下面结合实施例对本发明的技术方案作进一步详细的说明,但实施例并不限制本发明的保护范围。本发明中,wt%为质量分数。本发明中,所述的比表面积、孔容、孔径和孔分布是采用低温液氮吸附法测得的。如图1-4所示,本发明制备渣油加氢处理催化剂载体时,所述模具包含带有球形空腔的壳体1(见图1)和能形成贯通通道的导模3(见图1)。本发明以外部形状是球形为例进行说明,球形壳体可由两个完全相同的半球体组成。球形空腔的直径为d1(见图1)。所述导模选用加热或燃烧可除掉的物质,比如石墨、木材、纸、石蜡或石油树脂等。所述导模的结构与载体中的三维贯通的孔道相配,导模包括横穿“十字”的圆柱体5、中间大的“十字”体6和两侧小的“十字”体7(见图3),其中,横穿“十字”的圆柱体5和中间大的“十字”体6的直径为d1,两侧小的“十字”体7的直径为d2,具体见图1。除去导模后所产生的孔道为贯通通道8。本发明方法中,首先将各部分球形壳体相互固定,使之成为两个完整的半球体空腔4(见图2),将能三维贯通的孔道的导模放入一个半球体空腔4内,这时将膏状物料2压入两个半球体空腔4,充满整个空腔后将两个半球体合在一起形成一个完整的球体并固定。导膜形成的相互垂直的载体贯通通道8,如图4所示。实施例和比较例所用的含酸原油原料的性质见表3,所用加氢处理催化剂的性质见表1和表2。实施例1称取氧化硅含量为30wt%的水玻璃400g加入烧杯中,启动搅拌装置,向烧杯中缓慢加入质量浓度为62%的硝酸溶液150g,再加入42.9g硝酸镍,搅拌溶解后烧杯中水玻璃溶液的ph值为2.0,再向上述溶液中加入385.3g拟薄水铝石(性质如下:孔容1.05ml/g,比表面积为306m2/g,干基为70wt%),搅拌均匀后再加入固化剂尿素35g,待尿素全部溶解后加入去离子水,使烧杯中物料呈具有一定流动性的膏状,且以二氧化硅和氧化铝计的固含量为33%。将上述膏状物料压入具有球形空腔的两个完全相同的半球体中。其中,一个半球休中放入导模,导模由木材制备。导模的结构为通过球心的x轴、y轴和z轴方向各有一个圆柱体,圆柱体长度为球形空腔的直径,并在x轴和y轴两个方向上各设有两个圆柱体,两个圆柱体分别在球形空腔半径的二分之一处,圆柱体长度为球形空腔半径二分之一处球冠直径。膏状物料压入两个半球体空腔,充满整个空腔后将两个半球体合在一起形成一个完整的球体并固定。将盛有膏状物料模具加热至为120℃,恒温60分钟,由于模具中膏状物料受热后释放氨气使膏状物料固化并收缩后自动脱模成为球状凝胶,再用去离子水洗涤球状凝胶至中性,在120℃下干燥5小时,经750℃焙烧3小时得到本发明球状催化剂载体a。其中,所得催化剂载体a的外直径约为7.0mm,中间通孔直径约为1.9mm,侧通孔直径约为1.3mm。将载体a浸渍mo-ni-p溶液,在120℃下干燥6小时,经500℃焙烧3小时得到本发明催化剂ac,催化剂性质见表1。实施例2制备过程如实施例1,只是二氧化硅和氧化铝计的固含量为35%,且更换模具,增大空腔和圆柱体直径,制备的催化剂载体b及催化剂bc,其性质见表1。其中,所得催化剂载体b的外直径约为9.5mm,中间通孔直径约为3.0mm,侧通孔直径约为1.6mm。实施例3制备过程如实施例1,只是不加入硝酸镍,制备的催化剂载体c及催化剂cc,其性质见表1。其中,所得催化剂载体c的外直径约为7.0mm,中间通孔直径约为1.9mm,侧通孔直径约为1.3mm。比较例1称取氧化硅含量为30wt%的水玻璃400g加入烧杯中,启动搅拌装置,向烧杯中缓慢加入质量浓度为62%的硝酸溶液150g,再加入42.9g硝酸镍,搅拌溶解后烧杯中水玻璃溶液的ph值为2.0,再向上述溶液中加入385.3g拟薄水铝石(性质如下:孔容1.05ml/g,比表面积为306m2/g,干基为70wt%),搅拌均匀后再加入固化剂尿素35g,待尿素全部溶解后加入去离子水,使烧杯中物料呈具有一定流动性的膏状,且以二氧化硅和氧化铝计的固含量为33%。将上述膏状物料压入两个相同直径的半球状中空结构的刚性体模具中,球形空腔直径同实施例1所用模具的球形空腔直径,充满整个空腔后将两个半球体合在一起形成一个完整的球体并固定。将盛有膏状物料模具加热至为120℃,恒温60分钟,由于模具中膏状物料受热后释放氨气使膏状物料固化并收缩后自动脱模成为球状凝胶,再用去离子水洗涤球状凝胶至中性,在120℃下干燥5小时,经750℃焙烧3小时得到本比较例球状催化剂载体d,所得催化剂载体d的外直径约为7.0mm。将载体d浸渍mo-ni-p溶液,在120℃下干燥6小时,经500℃焙烧3小时得到本比较例催化剂dc,催化剂性质见表1。实施例4高酸原料(性质见表3)和氢气进入上流式加氢反应器,与加氢催化剂接触进行加氢反应。其中分别采用加氢催化剂ac、bc、cc、dc,操作条件如下:反应温度300℃,反应压力10.0mpa,氢油体积比300,液时体积(lhsv)为1.2h-1,反应所得产物的性质见表4。实施例5高酸原料(性质见表3)和氢气进入上流式加氢反应器,与加氢催化剂接触进行加氢反应,其中采用加氢催化剂ac,并采用两个催化剂床层,其体积比为1:1,反应温度分别为260℃、280℃、300℃、350℃,反应压力10.0mpa,氢油体积比300,液时体积(lhsv)为1.2h-1,反应所得产物的性质见表5。比较例2与实施例5相比,将加氢催化剂ac替换为加氢催化剂dc,得到加氢生成油。生成油性质详见表6。比较例3与实施例5不同的是上流式加氢反应器采用的双层床催化剂,其中下部装填fzc10uh,上部装填fzc11uh。其中,fzc10uh属于常规的上流式脱金属催化剂,fzc11uh属于上流式脱硫催化剂,反应温度分别为260℃、280℃、300℃、350℃,反应压力10.0mpa,氢油体积比300,液时体积(lhsv)为1.2h-1催化剂性质见表2,反应所得产物的性质见表7。表1实施例和比较例所制备催化剂的性质催化剂载体编号载体a载体b载体c载体d孔容,ml/g0.7820.7810.7810.771比表面积,m2/g140141143146平均孔直径,nm22.322.221.921.1孔分布,%<8.0nm0.60.60.51.08-20nm62.562.262.763.5>20.0nm36.937.236.835.5催化剂编号催化剂ac催化剂bc催化剂cc催化剂dc金属含量,%moo38.68.58.68.6nio4.44.42.44.4侧压强度,n/粒41463488表2比较例所用加氢催化剂的性质催化剂牌号fzc-10ufzc-11u功能脱金属催化剂脱硫催化剂颗粒形状球形球形颗粒外径,mm2.92.9强度,n.mm-13230比表面积,m2/g110148磨损率,wt%0.30.4金属含量,wt%moo35.210.8nio1.22.4表3高酸原油的性质分析项目数据密度(20℃),g/cm30.9362总酸值,mgkoh/g3.45硫,wt%0.80氮,μg/g3720铁,μg/g27.2钙,μg/g45.6镍+钒,μg/g28.8产物收率<350℃收率,wt%25.07350~500℃收率,wt%35.45>500℃收率,wt%39.48表4加氢反应所得产物的性质催化剂编号催化剂ac催化剂bc催化剂cc催化剂dc总酸值,mgkoh/g0.060.050.050.11硫,wt%0.250.260.220.42氮,μg/g3130314231453256铁,μg/g3.562.243.337.32钙,μg/g5.604.605.057.75镍+钒,μg/g12.5011.7912.1316.50表5采用实施例1制备的催化剂ac在不同操作条件下所得产物的性质反应温度,℃260280300350总酸值,mgkoh/g0.180.120.060.04硫,wt%0.620.460.250.12氮,μg/g3359324831302774铁,μg/g13.308.63.562.25钙,μg/g15.6812.25.61.22镍+钒,μg/g22.617.112.55.8表6采用比较例1制备的催化剂dc在不同操作条件下所得产物的性质反应温度,℃260280300350总酸值,mgkoh/g0.280.230.110.07硫,m%0.650.520.420.26氮,μg/g3410336332563061铁,μg/g17.3012.557.323.40钙,μg/g16.3012.557.753.11镍+钒,μg/g23.219.116.58.8由表5和表6结果表明,在260~350℃、10.0mpa的条件下,采用本发明加氢处理催化剂ac,脱除环烷酸的效果明显好于采用比较例催化剂dc。由于原料油中的钙含量高达45.6μg/g,铁含量也达到27.2μg/g,而采用本发明催化剂ac脱除钙、铁等金属杂质的效果也要好于采用比较例催化剂dc,有效地避免了在反应器顶部结焦、板结问题,延长了装置的运转周期。而且从试验结果来看,本发明催化剂脱除硫、氮杂质的性能也较高,降低了原料油后续加工的难度。表7采用比较例3催化剂的加氢反应所得产物的性质反应温度,℃260280300350总酸值,mgkoh/g0.330.270.150.08硫,m%0.720.550.500.31氮,μg/g3467341233233155铁,μg/g18.8015.39.624.40钙,μg/g19.6114.257.985.32镍+钒,μg/g25.3521.5418.7812.72实施例6与实施例5相比,选定反应温度为300℃,其它条件不变的情况下,分别采用实施例1催化剂ac和比较例1催化剂dc,以相同的原料油进行催化剂稳定性进行考察,结果见下表8。表8催化剂稳定性试验结果催化剂ac催化剂dc运行时间(天)总酸值(mgkoh/g)总酸值(mgkoh/g)100.060.11500.060.12800.070.151000.070.181200.070.201500.080.21由表8长时间运转周期的考察,可见采用本发明催化剂系统具有稳定的脱酸活性,原料油经过加氢处理,使产物的酸值大幅降低小于0.10mgkoh/g,达到了本发明的目的。而且从卸出的催化剂来看也没有明显的结焦现象。而采用比较例催化剂时其脱酸稳定性较差,到了150天,加氢产品酸值增长到0.21mgkoh/g。当前第1页12