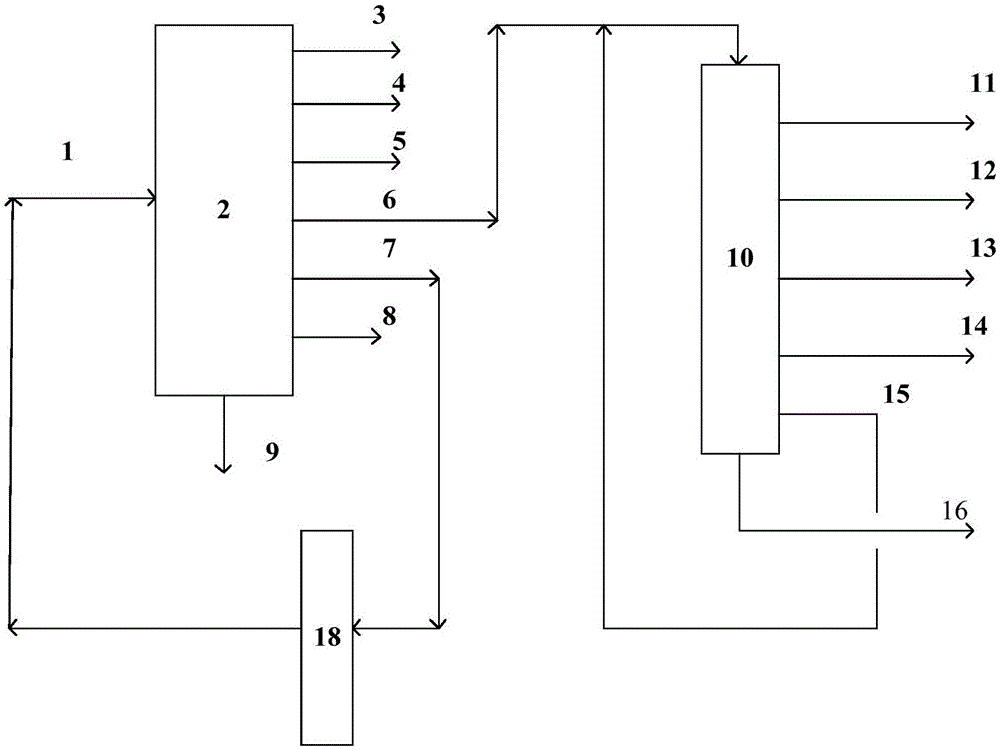
本发明属于化工领域,具体涉及一种采用劣质lco生产高价值化工产品的方法。
背景技术:
:在我国,催化裂化工艺由于操作灵活性好、汽油产率高,一次性投资低而得到广泛的应用。但同时,这也导致我国催化裂化柴油,即lco的产量约占柴油池的三分之一。随着环保立法的日趋严格,劣质lco使炼厂柴油质量升级面临很大困难。如何有效加工lco、消减劣质lco产量、生产高价值产品、提高经济效益成为各炼油技术开发商追求的目标。对上述低价值产品中的lco来说,一般炼厂采用常规加氢精制工艺加工lco,脱除柴油中的硫、氮等杂质、饱和部分芳烃,生产低硫柴油调合出厂。但该工艺过程十六烷值提高幅度有限,且柴油密度也变化不大。对lco的加工利用,国内外各炼油企业纷纷开发相关技术,提高lco加工利用过程的经济性。cn101724454a中公开了一种生产高辛烷值汽油的加氢裂化方法。该方法采用处理柴油馏分或重油馏分的加氢精制催化剂和一种轻油型加氢裂化催化剂,该方法需控制加氢裂化进料的氮含量为30~100μg/g。该方法在一次通过流程下,采用部分循环的操作方式,加氢裂化单程转化率控制为30%~60%,总转化率控制为50%~95%。并且,该方法生产的汽油馏分ron为90.8~93.8。cn103865577a公开了一种催化裂化柴油生产轻质芳烃及清洁燃料油品的方法。该方法包括:(1)催化裂化柴油与氢气混合,与裂化产物混合后同时进行加氢精制反应,以脱除硫氮杂质,并进行烯烃饱和及芳烃加氢饱和;(2)精制后的催化裂化柴油进行切割,其中,>355℃的馏分油与氢气混合后返回进行加氢裂化;(3)对于切割后馏分油进行抽提,得到富含多环芳烃的抽出油和富含烷烃的抽余油;(4)富含烷烃抽余油作为清洁柴油调和组分;(5)富含芳烃抽出油加氢裂化反应生产轻质芳烃及清洁汽油调和组分;(6)抽出油加氢裂化组分经切割分离,>195℃的馏分作为清洁柴油调和组分,<195℃的馏分油得到轻质芳烃产品和清洁汽油调和组分。技术实现要素:本发明的目的是在现有技术的基础上提供一种lco加氢裂化和催化裂化组合的工艺方法,这是一种提高汽油收率和产品质量,延长运转周期的组合工艺方法,该方法可以实现采用劣质lco生产高价值化工产品的效果。本发明的技术思路是:(1)催化裂化反应区分馏部分分离出轻中馏分lco,轻中馏分lco进入加氢裂化反应区,在氢气和加氢精制-加氢裂化催化剂存在下进行加氢脱硫、加氢脱氮、选择性加氢饱和反应、选择性开环及烷基侧链裂化反应等,得到的反应生成油经高压分离器、低压分离器及分馏设施分离后,得到干气、液化气、轻汽油馏分、重汽油馏分、循环油馏分、柴油馏分。其中,部分循环油馏分返回加氢裂化反应区进一步循环转化。(2)催化裂化反应区分馏部分分离得到的重馏分lco与渣油一起进入渣油加氢装置,进行加氢脱金属、加氢脱硫、加氢脱氮等反应,反应产物与加氢渣油再进入催化裂化反应区进一步进行催化裂化反应,在催化裂化催化剂存在下进行裂化反应,经分离后得到干气、液化气、催化裂化汽油、轻中馏分lco、重馏分lco、油浆和焦炭等。具体地,一种采用劣质lco生产高价值化工产品的方法,包括下列步骤:s11:在催化裂化反应区中进行催化裂化反应获得的反应产物进入分馏系统分离后,得到干气、液化气、催化裂化汽油、轻中馏分lco、重馏分lco、油浆和焦炭;s21:将步骤s11中分离得到的轻中馏分lco与氢气混合后,进入装填有加氢精制和加氢裂化催化剂的加氢裂化反应区进行加氢裂化反应,依次经过加氢脱硫、加氢脱氮、芳烃选择性加氢饱和、选择性开环和烷基侧链裂化反应后,反应产物经高压分离器、低压分离器及分馏系统分离后,得到干气、液化气、轻汽油馏分、重汽油馏分、循环油馏分和柴油馏分,用于生产高辛烷值汽油调合组分;s22:将步骤s21中生成的循环油馏分再进入加氢裂化反应区中继续执行步骤s21进行循环转化;s31:将步骤s11中分离得到的重馏分lco与渣油一起进入装填有渣油加氢催化剂的渣油加氢反应区进行渣油加氢反应,经过加氢脱金属、加氢脱硫、加氢脱氮、多环芳烃加氢饱和反应后,将反应产物与加氢渣油返回催化裂化反应区继续执行步骤s11进行循环转化。步骤s11中所述的轻中馏分lco的馏程范围为150℃~340℃,总芳烃含量高于70%,其中双环芳烃含量高于45%,三环芳烃含量小于5%。所述的轻中组分lco来自中间基或环烷基原油,或石蜡基原油与中间基或环烷基原油混合油。步骤s11中所述的重馏分lco的馏程范围为330℃~400℃,总芳烃含量高于70%,其中单环芳烃含量小于5%,两环芳烃含量含量小于12%,且三环及以上芳烃含量高于50%。步骤s21中所述的加氢精制催化剂为rn-411精制催化剂,所述的加氢裂化催化剂为rhc-100裂化催化剂。步骤s21中所述的加氢裂化反应中,其反应条件为:氢分压为2.5mpa~8.0mpa;精制、裂化平均反应温度为300℃~450℃;氢油体积比为400~2500nm3/m3;液时体积空速为0.2h-1~20.0h-1。优选地,步骤s21中所述的加氢裂化反应中,其反应条件为:氢分压为3.5mpa~6.0mpa;精制、裂化平均反应温度为350℃~430℃;氢油体积比为900~1600nm3/m3;液时体积空速为0.5h-1~3.0h-1。步骤s31中所述的渣油加氢反应中,以渣油加氢反应区(18)进料为基准,掺炼的重馏分lco(7)的重量比例≯40%,该反应过程中的操作压力、反应温度、体积空速、氢油比等采用常规渣油加氢处理的反应条件。当该反应区掺炼部分加氢重lco时,渣油加氢操作条件与不掺炼加氢重lco相同,可以不做调整,也可以根据需要适当进行微调。优选地,步骤s31中所述的渣油加氢反应中,以渣油加氢反应区(18)进料为基准,掺炼的重馏分lco(7)的重量比例≤15%。步骤s31中所述的渣油加氢催化剂为rg-30系列、rdm-32、rdm-33c、rms-3、rcs-31催化剂中的任一种或其任意组合,或rht系列催化剂中的hdm、hds、hdccr、hdn中的任一种或其任意组合。在加氢裂化反应区,富含两环芳烃和单环芳烃的轻中馏分lco采用石科院lco加氢裂化生产高辛烷值汽油rlg技术加工,生产高辛烷值汽油调合组分,同时兼顾生产部分低硫柴油调合组分。在该反应区,高芳烃含量的轻中馏分lco与加氢精rn-411催化剂接触、反应,进行加氢脱硫、加氢脱氮、芳烃选择性加氢饱和,有效脱除硫化物和氮化物,并对双环芳烃进行选择性加氢饱和反应,生成四氢萘类单环芳烃。加氢精制产品油进入加氢裂化反应区与rhc-100加氢裂化催化剂接触、反应,完成四氢萘类单环芳烃的选择性开环裂化和烷基侧链裂化反应,生产高辛烷值汽油调合组分,同时兼顾生产部分低硫柴油调合组分。含少部分两环芳烃且富含三环以上芳烃的重馏分lco进入渣油加氢反应区,进行加氢脱硫、加氢脱氮、多环芳烃加氢饱和反应等,反应产物与加氢渣油一起进入催化裂化反应区裂化转化生产干气、液化气、汽油、轻中馏分lco、重馏分lco、hco、油浆、焦炭等。其中,轻中馏分lco返回rlg装置进行裂化转化为高辛烷值汽油调合组分,重馏分lco循环至渣油加氢处理装置继续加氢饱和,然后进入催化裂化单元进一步裂化转化为汽油调合组分。本发明基于现有装置类型特点和原料油性质而专门设计,具有如下优点:(1)采用本发明的方法,可以充分对低价值、劣质的lco进行加工,消减劣质lco高达50%以上;(2)采用本发明的方法,可以生产高价值汽油调合组分等化工产品:加氢裂化反应区可以生产轻汽油ron达87以上,硫含量小于5μg/g,可作为高辛烷值汽油调和组分;重汽油ron达95,硫含量小于3μg/g;同时可兼顾生产硫含量小于10μg/g,十六烷值较原料提高14个单位以上的低硫清洁柴油调和组分;(3)采用本发明的方法,可以延长rlg装置运转周期至少3个月以上,获得较好的经济效益;(4)采用本发明的方法,催化裂化反应区可以提高汽油产率约10%。附图说明图1为本发明提供的一种加工劣质lco生产高价值产品的工艺流程示意图。图中:1渣油加氢反应区反应产物与加氢渣油,2催化裂化反应区,3干气,4液化气,5汽油,6轻中馏分lco,7重馏分lco,8油浆,9焦炭,10加氢裂化反应区,11干气,12液化气,13轻汽油馏分,14重汽油馏分,15循环油馏分,16柴油馏分,18渣油加氢反应区。具体实施方式下面结合附图对本发明所提供的方法进行进一步说明。附图是本发明的工艺流程示意图,图中省略了许多设备,如泵、换热器、压缩机等,但这对本领域普通技术人员是公知的。以下实施例将有助于本领域的技术人员进一步理解本发明,但不以任何形式限制本发明。应当指出的是,对本领域的普通技术人员来说,在不脱离本发明构思的前提下,还可以做出若干调整和改进。这些都属于本发明的保护范围。如图1所示,本发明提供的方法流程详细描述如下:催化裂化反应区2的反应产物之一轻中馏分lco(6)与氢气混合后,进入加氢裂化反应区10,依次与rlg技术专用的加氢精制rn-411催化剂和专用的加氢裂化rhc-100催化剂接触、反应,完成加氢脱硫、加氢脱氮、芳烃加氢饱和、选择性开会及烷基侧链裂化反应等。加氢裂化反应区10的反应产物经高低压分离器及分馏系统分离得到干气11、液化气12、轻汽油馏分13、重汽油馏分14、循环油馏分15和柴油馏分16。其中,循环油馏分15返回加氢裂化反应区10的入口继续进行循环转化。催化裂化反应区2的反应产物之一重馏分lco(7)返回渣油加氢反应区18,完成加氢脱硫、加氢脱氮、加氢脱金属、芳烃加氢饱和等反应,反应产物与加氢渣油混合油经管线一起进入催化裂化反应区2,与催化裂化催化剂接触反应后,裂化生成干气3、液化气4、汽油5、轻中组分lco6,重组分lco7,油浆8和焦炭9等。加氢裂化反应区10采用的专用催化剂为rn-411精制剂和rhc-100裂化剂。该催化剂级配为rlg专利(zl2009810162161.x和zl201240411335.3)专用的催化剂级配方案。渣油加氢反应区18采用的催化剂为渣油加氢催化剂为rg-30系列、rdm-32、rdm-33c、rms-3、rcs-31催化剂中的任一种或其任意组合,或rht系列催化剂中的hdm、hds、hdccr、hdn中的任一种或其任意组合,为石科院自主开发。(zl201310432344.5、zl201310432227.9、zl201310332676.6、zl201310308434.3和zl201310308841.4)。催化裂化反应区2采用的技术为石科院开发的mip技术及配套催化剂。(zl200610113673.3、zl200610169512.6、zl99105903.4和zl99109193.0等)下面实施例将对本发明予以进一步说明,但并不因此而限制本发明。实施例中原料e为轻馏组分lco,原料f为重馏分lco,其物化性能如表1所示。实施例1原料e与氢气和富氢气体混合后进入加氢裂化反应区在rlg条件下进行反应。由表2可见,<65℃轻汽油馏分ron达88,65℃~205℃馏分ron达95.8,mon达83.0,硫含量1.5μg/g;>205℃柴油馏分20℃密度0.892g/cm3,硫含量为3μg/g,十六烷值提高值为16.0。20t/h原料f进入渣油加氢装置经加氢脱硫、加氢脱氮及芳烃加氢饱和后,返回催化裂化单元继续进行裂化反应,可生产约8t/h汽油调合组分。采用该方法,本发明申请人将消减劣质lco约40万吨/年,rlg装置运转周期延长三个月以上。表1原料的物化性能表2反应产物的物化性能产品性质轻汽油重汽油柴油馏分范围,℃<6565~205>205密度(20℃),g/cm30.6350.8250.892硫,μg/g<11.53氮,μg/g<1<1<1ron/mon88/8295.8/83-十六烷值提高值-16.0当前第1页12