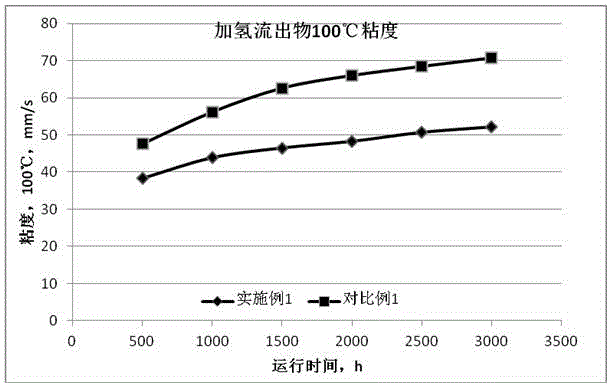
本发明涉及一种烃类加氢处理技术,具体地说是一种渣油加氢脱金属处理方法。
背景技术:
:渣油加氢技术是在高温、高压和催化剂存在的条件下,使渣油和氢气进行催化反应,脱除渣油分子中硫、氮和金属等有害杂质,同时,渣油中部分较大的分子裂解并加氢,变成分子较小的理想组分。相比于其它渣油加工技术,固定床加氢处理技术的投资和操作费用低,运行安全简单,是迄今为止工业应用最多和技术最成熟的渣油加工技术。固定床渣油加氢装置可为催化裂化装置提供合格进料,同时生成部分汽、柴油等轻质产品。由于渣油原料密度大、粘度大,不利于渣油原料在渣油加氢处理催化剂孔道中扩散,特别是原料中的胶质、沥青质等大分子物质无法进入催化剂微孔也就无法反应转化为小分子物质,这样不但影响了渣油加氢反应中的杂质脱除率及脱残炭率,还影响催化剂使用寿命、操作稳定性。原料粘度越大,系统压降及物流波动就越大,操作稳定性就越差。再者,由于渣油中金属含量高、残炭值高,在转化率较低时就会出现沥青质聚沉现象,导致催化剂积炭而快速失活,缩短装置操作周期。目前,渣油加氢装置原料为了控制适当原料粘度等指标,通过掺炼低密度、低粘度、低残炭的轻质油品(例如焦化蜡油、催化裂化柴油和循环油、瓦斯油等)来调整原料粘度、残炭等加工指标,达到装置加工要求。cn106367113a公开了一种渣油加氢处理方法。该方法使用渣油固定床加氢装置,渣油原料掺入劣质轻质油品,依次通过加氢保护剂、加氢脱金属催化剂、加氢脱硫催化剂、加氢脱氮催化剂和加氢脱残炭催化剂,产物经分馏得到汽油、煤油、柴油馏分以及加氢尾油。所述劣质轻质油品可以为催化裂化柴油及一中油、裂解柴油或碳十重芳烃。该方法可以降低渣油固定床加氢装置进料体系粘度的同时改善体系反应性能和产品品质。cn1488719a公开了一种重烃加氢处理方法,渣油原料依次通过保护剂床层、加氢脱金属催化剂床层、加氢脱硫催化剂床层、加氢脱氮催化剂床层,并且在保护剂床层后及加氢脱硫催化剂床层之前引入脱沥青油和/或焦化蜡油,其引入位置在部分加氢脱金属催化剂床层之后。该方法用于渣油和脱沥青油、焦化蜡油共同加氢处理,为下游催化裂化或加氢裂化等轻质化装置提供优质进料。乙烯焦油是乙烯生产中的副产品,占乙烯产量的15%左右,其由各种烷烃、c8~c15的芳烃、芳烯烃及含n、s、o等元素的杂环化合物等组成,主要是双环以上稠环芳烃的混合物,芳烃含量达90%以上,密度(20℃)1.0g/cm3以上,硫和氮等杂质含量低,基本不含金属杂质(含有微量的铁等金属杂质主要是设备腐蚀原因带入),粘度(100℃)达到200mm/s以上,远远高于常规的渣油加氢处理原料,不适宜用于渣油加氢的降低粘度组份,同时由于基本不含金属杂质,一般也不需要进行加氢脱金属反应。乙烯焦油中350℃以前的馏分约占30%~40%,为轻质油;350℃以后的馏分是重质油,常温下是黑色固体,约占60%~70%。近几年,随着乙烯工业的迅猛发展,乙烯焦油产量也飞速增加,因此,合理利用乙烯焦油使其产生较高的经济效益,对乙烯装置整体效益及乙烯副产资源深加工都有着重大影响,这也是当前乙烯后加工行业亟待解决的重要课题之一。关于乙烯焦油综合利用的研究主要包括以下几个方面:(1)从乙烯焦油中提取萘、甲基萘及其系列物;(2)利用乙烯焦油制备碳石油树脂、纤维沥青、碳纤维等;(3)将乙烯焦油的轻馏分掺炼到其他装置中进一步加工;(4)将乙烯焦油制备为芳烃溶剂油、针状焦、炭黑。由于乙烯焦油成分的复杂性,上述研究未得到工业上大规模应用,目前,乙烯焦油主要用作锅炉或窑炉的燃料油使用,只有很少部分乙烯焦油加工生产炭黑,整体利用率不高,经济价值低,且由于乙烯焦油中含有重烯基芳烃等,燃烧时易产生黑烟及结焦,造成环境污染,导致上述对乙烯焦油的处理工艺存在着工艺条件苛刻、成本高,乙烯焦油转化率低、产品收率低、综合利用率不高、产品附加值低等缺点。cn1970688a公开了一种乙烯焦油综合加工工艺。该工艺先将乙烯焦油切出沸点小于260~280℃的轻馏分,再用加氢精制的方法除去轻馏分中的不饱和烃类,然后再从中提取萘及甲基萘产品,同时副产少量溶剂油产品。该方法只利用了乙烯焦油中所占比例很少的轻馏分,尚有约80%以上的乙烯焦油馏分没有得到有效处理;同时其所提供的加氢精制条件无法处理沸点高于280℃的乙烯焦油馏分。cn102234538a公开了一种乙烯焦油的加氢处理方法。该方法将乙烯焦油分馏成轻馏分和重馏分,切割点为400~450℃,轻馏分依次经过加氢保护催化剂、加氢精制催化剂、加氢脱残炭催化剂和加氢裂化催化剂,所得产物分离得到汽油和柴油馏分;重馏分依次经加氢保护催化剂、加氢脱残炭催化剂和加氢转化催化剂,所得的加氢转化生成油循环去重馏分加氢反应区,剩余部分经分离得到汽油和柴油馏分。该方法单独加工乙烯焦油,由于重馏分的密度大、粘度高,对加氢装置以及配套设备的要求增高,还需另设分馏塔用于切割乙烯焦油,而且重馏分的加工需要大量的加氢转化生成油循环,工艺过程复杂,较难实现工业化。技术实现要素:针对现有技术的不足,本发明提供了一种渣油加氢脱金属处理方法。本发明发明人意外发现,采用乙烯焦油作为物料粘度调节助剂加到渣油原料中,能够在加氢脱金属反应条件下,通过各组分的协同作用,有效降低了反应条件下的体系粘度,促进了渣油加氢脱金属的进行,并也有利于后续脱硫、脱残炭等反应性能的提升。对于渣油加氢来说,原料的性质和催化剂失活状况是影响渣油加氢的两个重要因素。渣油加氢是扩散控制的反应,而原料油的粘度和反应物分子的大小都对扩散有很大的影响,因此,在本领域中通常是降低原料油的粘度,减小反应物分子的尺寸,进而改善原料油的扩散性能,促进渣油加氢反应的进行。特别是在渣油加氢脱金属反应区,由于比后续加氢脱硫及加氢转化反应区的反应温度相对低、渣油转化率相对低(生成低分子量低粘度的组分少),该阶段物料的粘度较高,粘度对该阶段反应的影响更为突出。催化剂会由于金属沉积或积炭等原因,影响催化剂的孔道结构和表面性能,进而影响催化剂的扩散及反应性能。而乙烯焦油中稠环芳烃含量高,粘度高,若将乙烯焦油作为渣油加氢处理原料,从原料性质和对催化剂失活影响来看,对渣油加氢均不利。发明人意外发现,虽然对于本领域技术人员来说,从乙烯焦油的组成和性质上均不符合常规改善渣油加氢性能的要求,特别是对渣油加氢脱金属反应区的不利影响将会更为突出,但发明人出乎意料地,将乙烯焦油作为物料粘度调节助剂加到渣油原料中,在加氢脱金属反应条件下,反应体系脱金属性能不但没有降低,反而有促进作用,该阶段反应流出物的粘度、金属脱除率等指标有明显的提升,可以判断该反应体系在加氢脱金属反应条件下扩散性能更有利于脱金属反应,各组分的协同作用有效降低了反应条件下的体系粘度,促进了渣油加氢脱金属的进行,并也有利于后续脱硫、脱残炭等反应性能的提升。本发明提供的渣油加氢脱金属处理方法,进料包括渣油原料、氢气和物料粘度调节助剂,其中,物料粘度调节助剂包括乙烯焦油,进料经过加氢脱金属反应区进行加氢处理反应,得到加氢流出物。所述乙烯焦油的用量占渣油原料质量的0.1%~30%,优选为5%~20%,进一步优选为8%~20%。所述乙烯焦油的性质如下:密度(20℃)为1.000g/cm3以上,一般为1.000~1.200g/cm3,残炭含量为10wt%~30wt%,凝点为30~40℃,100℃粘度为200~500mm/s。所述乙烯焦油中,硫和氮的含量较低,基本不含金属杂质,其中,硫含量为0.05wt%以下,一般为0.03wt%~0.05wt%,氮含量为80μg/g以下,一般为10~80μg/g,ni和v的含量在5μg/g以下,进一步为3μg/g以下。所述的渣油原料为渣油加氢处理装置常用的原料,渣油原料可以包括常压渣油和/或减压渣油。任选地,所述的渣油原料还可以包括用于改善渣油性质、便于加工等方面的常规辅助原料,比如为了控制适当原料粘度等指标而加入低密度、低粘度的轻质油品,所述的轻质油品可以为来自直馏、减压或二次加工而得的轻质油品,可以为蜡油、柴油、瓦斯油等中的至少一种,其中二次加工可以为焦化、催化裂化、减粘等中的至少一种。比如蜡油可以为直馏蜡油、减压蜡油、焦化蜡油中的一种或几种,由催化裂化而得的轻质油品可以为催化裂化柴油、催化裂化回炼油、催化裂化循环油等中的至少一种。所述常规辅助原料的加入量,本领域技术人员可以根据原料性质等来调整。所述渣油原料的性质如下:密度(20℃)为0.955~0.996g/cm3,残炭含量为9wt%~14wt%,金属杂质含量以ni和v计为10~110μg/g,凝点为27~38℃,100℃粘度为60~120mm/s。所述渣油原料中硫、氮含量较高,硫含量一般为0.8wt%~3.5wt%,氮含量一般为1500~5000μg/g。本发明渣油加氢脱金属处理方法中,加氢脱金属反应区的操作条件如下:反应温度为300~410℃,氢分压为10~20mpa,液时体积空速为0.1~2.0h-1,氢油体积比为500~2000,优选的操作条件如下:反应温度为350~395℃,氢分压为13~18mpa,液时体积空速为0.1~1.5h-1,氢油体积比为500~2000。本发明渣油加氢脱金属处理方法中,加氢脱金属反应区为常规渣油加氢工艺中设置的加氢脱金属反应区至少装填一个加氢脱金属催化剂床层,优选为2~5个加氢脱金属催化剂床层。一般来说,加氢脱金属反应区主要是进行加氢脱金属反应,同时也进行加氢脱硫、加氢脱残炭等反应。本发明渣油加氢脱金属处理方法中,优选采用固定床加氢工艺,其中含加氢脱金属反应区的反应器可以采用上流式进料方式,也可以采用下流式进料方式。本发明渣油加氢脱金属处理方法中,还可以设置有加氢保护反应区,这是本领域技术人员根据原料的性质能够确定的。在加氢脱金属反应区之前设置加氢保护反应区。加氢保护反应区至少装填一个加氢保护剂床层,优选为2~4个加氢保护剂床层。本发明渣油加氢脱金属处理方法中,所述的加氢保护剂、加氢脱金属催化剂可以选自本领域常规的商业催化剂或采用现有技术的常规方法制备。上述催化剂包括载体和活性金属组分,其中载体可以为氧化铝基载体,可以加入硼、硅、锆、磷、氟、钛等中的至少一种,活性金属组分一般选自第vib族和∕或第viii族金属中的一种或多种,第viii族金属优选为ni和∕或co,第vib族金属优选为mo和∕或w。本发明催化剂可以采用挤出成型物或球形。例如可以采用中国石化抚顺石油化工研究院开发的fzc系列商业催化剂,比如加氢保护剂fzc-100b、fzc-12b、fzc-103d、fzc-13b等,加氢脱金属催化剂fzc-28a、fzc-204a等。本发明渣油加氢脱金属处理方法中,催化剂级配装填采用常规的原则进行,比如催化剂按物流方向,孔径逐渐变小、活性金属组分含量逐渐增大,粒径逐渐减小。本发明渣油加氢脱金属处理方法中,加氢保护剂中加氢活性金属以氧化物计的质量含量为3%~12%,其中第vib族金属以氧化物计的质量含量为2.0%~11.5%,第viii族金属以氧化物计的质量含量为0.2%~5.0%。本发明渣油加氢脱金属处理方法中,加氢脱金属催化剂中加氢活性金属以氧化物计的质量含量为4%~22%,其中第vib族金属以氧化物计的质量含量为3%~21%,第viii族金属以氧化物计的质量含量为0.5%~6.0%。本发明渣油加氢脱金属处理方法所得的加氢流出物的粘度小于独立以渣油原料为液相进料时所得加氢流出物的粘度。其中粘度是指100℃粘度,单位mm/s。本发明渣油加氢脱金属处理方法所得的加氢流出物中金属ni和v的脱除率高于独立以渣油原料为液相进料时所得加氢流出物中金属ni和v的脱除率。本发明渣油加氢脱金属处理方法所得的加氢流出物中硫的脱除率高于独立以渣油原料为液相进料时所得加氢流出物中硫的脱除率。其中,本发明渣油加氢脱金属处理方法所得的加氢流出物与独立以渣油原料为液相进料时所得加氢流出物,两者仅在进料不同的情况下,分别得到加氢流出物,其中独立以渣油原料为液相进料,是指与本发明渣油加氢脱金属处理方法相比,仅用等质量的相同渣油原料替换乙烯焦油,其他均与本发明的渣油加氢脱金属处理方法相同。本发明还提供了一种渣油加氢处理方法,其中,所述的加氢流出物经加氢脱硫反应区和加氢脱氮和/或加氢转化反应区进行加氢反应,得到加氢产物。所述的加氢产物进入分离系统,分离出汽油、柴油和加氢重油,加氢重油优选作为催化裂化装置的进料。所述的加氢脱硫反应区主要进行加氢脱硫反应,一般至少设置一个加氢脱硫催化剂床层,所述的加氢脱氮和/或加氢转化反应区主要进行加氢脱氮和加氢转化反应,一般至少设置一个加氢脱氮和/或加氢转化催化剂床层。本发明渣油加氢处理方法中,所述的加氢脱硫催化剂、加氢脱氮和/或转化催化剂可以选自本领域常规的商业催化剂或采用现有技术的常规方法制备。上述催化剂包括载体和活性金属组分,其中载体可以为氧化铝基载体,可以加入硼、硅、锆、磷、氟、钛等中的至少一种,活性金属组分一般选自第vib族和∕或第viii族金属中的一种或多种,第viii族金属优选为ni和∕或co,第vib族金属优选为mo和∕或w。本发明催化剂可以采用挤出成型物或球形。例如可以采用中国石化抚顺石油化工研究院开发的fzc系列商业催化剂,比如加氢脱硫催化剂fzc-33b,加氢脱氮催化剂fzc-41c等。本发明渣油加氢处理方法中,各催化剂的装填种类和用量,本领域技术人员可以根据实际需要进行调整。与现有技术相比,本发明的有益技术效果如下:(1)本发明方法是发明人意外发现的,采用乙烯焦油作为物料粘度调节助剂加到渣油原料中,能够在加氢脱金属反应条件下,反应体系脱金属性能不但没有降低,反而有促进作用,该阶段反应流出物的粘度、金属脱除率等指标有明显的提升,可以判断该反应体系在加氢脱金属反应条件下扩散性能更有利于脱金属反应,各组分的协同作用有效降低了反应条件下的体系粘度,促进了渣油加氢脱金属的进行,并也有利于后续脱硫、脱残炭等反应性能的提升。(2)本发明方法可以在常规渣油加氢处理装置上进行,易于工业化。附图说明图1为实施例1和对比例1在不同运转时间下所得加氢流出物的粘度对比图;图2为实施例1和对比例1在不同运转时间下所得加氢流出物的金属ni和v的脱除率的对比图;图3为实施例1和对比例1在不同运转时间下所得加氢流出物的硫的脱除率的对比图。具体实施方式下面结合实施例对本发明作进一步的详细说明,但本发明的保护范围不受实施例的限制。本发明中,wt%为质量分数。实施例1本实施例采用一个固定床反应器r1,其中设置有加氢保护反应区和加氢脱金属反应区,各反应区装填的催化剂见表2。将渣油原料a与乙烯焦油a预热混合,然后与氢气一起,采用上进料方式进入反应器,在加氢脱金属条件下依次与表2级配的催化剂接触并进行加氢反应,得到加氢流出物,其性质见表3。在不同运转时间下,加氢流出物的粘度、金属ni和v的脱除率以及硫的脱除率分别见图1-3。其中,渣油原料a和乙烯焦油a的性质见表1,催化剂种类和级配见表2,其中加氢保护剂为fzc-1系列,加氢脱金属催化剂为fzc-2系列。工艺条件见表3,固定床加氢结果见表4。实施例2本实施例与实施例1基本相同,不同点在于:本实施例采用渣油原料b、乙烯焦油b和重循环油,工艺条件见表3,固定床加氢结果见表4。实施例3本实施例与实施例1基本相同,不同点在于,本实施例采用渣油原料a和乙烯焦油b,工艺条件见表3,固定床加氢结果见表4。实施例4本实施例与实施例1基本相同,不同点在于:调节乙烯焦油a的用量和工艺条件,工艺条件见表3,固定床加氢结果见表4。实施例5在实施例1一个反应器r1的基础上,增加一个反应器r2,反应器r2设置加氢脱硫反应区和加氢脱氮反应区,各反应区装填的催化剂见表5。将渣油原料a与乙烯焦油a预热混合,然后与氢气一起,采用上进料方式依次进入串联设置的反应器r1和r2,在加氢处理条件下依次与表5级配的催化剂接触并进行加氢反应,得到加氢产物,所得产物由反应器r2底部排出进入分离系统,分离出少量汽油和柴油馏分,其它馏分(350℃以上馏分)即加氢重油进入催化裂化装置。其中,渣油原料a和乙烯焦油a的性质见表1,催化剂种类和级配见表5,其中加氢保护剂为fzc-1系列,加氢脱金属催化剂为fzc-2系列,加氢脱硫催化剂为fzc-3系列,加氢脱氮催化剂为fzc-4系列。两个固定床反应器的工艺条件见表6,固定床加氢结果见表7。对比例1本对比例的方法与实施例1基本相同,不同点在于:采用渣油原料a代替含乙烯焦油a的渣油原料a。其中,工艺条件见表3,固定床加氢结果见表4。在不同运转时间下,加氢流出物的粘度、金属ni和v的脱除率以及硫的脱除率分别见图1-3。对比例2本对比例的方法与实施例1基本相同,不同点在于:采用含多芳烃油(催化裂化回炼油,性质见表1)的渣油原料a代替含乙烯焦油a的渣油原料a。其中,工艺条件见表3,固定床加氢结果见表4。对比例3本对比例的方法与实施例1基本相同,不同点在于:采用含催化裂化重循环油(性质见表1)的渣油原料a代替含乙烯焦油a的渣油原料a。其中,工艺条件见表3,固定床加氢结果见表4。对比例4本对比例的方法与实施例1基本相同,不同点在于:采用将乙烯焦油a作为原料代替含乙烯焦油a的渣油原料a。其中,工艺条件见表3,固定床加氢结果见表4。对比例5本对比例的方法与实施例5基本相同,不同点在于:采用渣油原料a代替含乙烯焦油a的渣油原料a。其中,工艺条件见表6,加氢结果见表7。对比例6本对比例的方法与实施例5基本相同,不同点在于:采用含多芳烃油(催化裂化回炼油,性质见表1)的渣油原料a代替含乙烯焦油a的渣油原料a。其中,工艺条件见表6,加氢结果见表7。表1渣油原料、乙烯焦油和轻质油品的性质分析项目渣油原料a渣油原料b乙烯焦油a乙烯焦油b多芳烃油重循环油分析方法硫含量,μg/g3060028400494351190015600sh/t0689-2000氮含量,μg/g30024831271714002100sh/t0704-2001残炭,wt%13.6511.2120.1612.410.230.65gb/t17144-1997重金属含量ni,μg/g22.3219.360.160.261-3.45astmd5708-2005v,μg/g68.4565.422.800.008-5.26astmd5708-2005凝点,℃32253432--gb/t510-1983粘度,100℃,mm/s93.6692.17317.8285.0-8.90gb/t11137密度(20℃),g/cm30.98750.98281.11971.0430.9571.056gb/t13377-1992模拟蒸馏,%astmd7169-2005ibp/10,℃228/455243/472165/238156/224186/228222/36330/50,℃545/586547/605358.6/478.4343/462256/293387/40270/90,℃621/679643/695558.2/676541/658318/359419/44595.3,℃694714750730375470表2催化剂级配方案(以体积分计)r1-加氢保护反应区r1-加氢脱金属反应区实施例1fzc-100b:fzc-12b:fzc-103d:fzc-13b=7:8:8:23fzc-28a:fzc-204a=45:86实施例2fzc-100b:fzc-12b:fzc-103d:fzc-13b=7:8:8:23fzc-28a:fzc-204a=45:86实施例3fzc-100b:fzc-12b:fzc-103d:fzc-13b=7:8:8:23fzc-28a:fzc-204a=45:86实施例4fzc-100b:fzc-12b:fzc-103d:fzc-13b=7:8:8:23fzc-28a:fzc-204a=45:86表3各例工艺条件实施例1实施例2实施例3实施例4原料渣油原料a+乙烯焦油a渣油原料b+乙烯焦油b+重循环油渣油原料a+乙烯焦油b渣油原料a+乙烯焦油a乙烯焦油与渣油原料的重量比1:101:101.5:1.00.6:10重循环油与渣油原料的重量比-0.5:10--反应器(r1)氢分压,mpa15.216.817.116.7反应温度,℃385379382388液时体积空速,h-10.420.400.430.46氢油体积比650650750800续表3对比例1对比例2对比例3对比例4原料渣油原料a渣油原料a+多芳烃油渣油原料a+重循环油乙烯焦油a轻质油品与渣油原料的重量比-1:10(多芳烃油)1:10(重循环油)-反应器(r1)氢分压,mpa15.215.215.215.2反应温度,℃385386386387液时体积空速,h-10.420.420.420.42氢油体积比650650650650表4各例反应结果分析项目实施例1实施例2实施例3实施例4运转时间,h1500150015001500加氢流出物性质硫含量,μg/g11132107861120811850氮含量,μg/g2160306220952294残炭,%8.216.828.088.31重金属含量ni,μg/g5.324.835.096.15v,μg/g15.5114.7814.6516.28凝点,℃16161716粘度,100℃,mm/s46.4850.2153.8255.86密度(20℃),g/cm30.9660.9630.9690.962续表4分析项目对比例1对比例2对比例3对比例4运转时间,h150015001500500加氢流出物性质硫含量,μg/g128251198611413296氮含量,μg/g21402049209714残炭,%8.127.587.8616.14重金属含量ni,μg/g6.575.836.03--v,μg/g19.0417.317.69--凝点,℃18181828粘度,100℃,mm/s62.5858.2460.61220.86密度(20℃),g/cm30.9580.9550.9611.052由表4中实施例1和对比例1的结果对比可知,本发明方法加入的乙烯焦油虽然其残炭含量高于渣油原料,但由加氢流出物的残炭含量推得,本发明方法的脱残炭率要略高于对比例1。表5催化剂级配方案(以体积分计)r1-加氢保护反应区r1-加氢脱金属反应区r2实施例5fzc-100b:fzc-12b:fzc-103d:fzc-13b=7:8:8:23fzc-28a:fzc-204a=45:86fzc-33b:fzc-41a=45:145表6各例工艺条件实施例5对比例5对比例6原料渣油原料a+乙烯焦油a渣油原料a渣油原料a+多芳烃油乙烯焦油与渣油原料的重量比1:10--多芳烃油与渣油原料的重量比--1:10反应器(r1)氢分压,mpa15.215.215.2反应温度,℃385385385液时体积空速,h-10.420.420.42氢油体积比650650650反应器(r2)氢分压,mpa14.914.914.9反应温度,℃391391391液时体积空速,h-10.390.390.39氢油体积比600600600表7各例加氢结果分析项目实施例5对比例5对比例6运转时间,h150015001500加氢重油性质硫含量,μg/g415050294723氮含量,μg/g166015851512残炭,wt%5.725.465.32重金属含量ni,μg/g3.274.093.78v,μg/g9.3812.2511.64凝点,℃111312粘度,100℃,mm/s27.3233.4329.24密度(20℃),g/cm30.9430.9350.930为了进一步考察本发明方法对活性、稳定性的影响,对实施例5和对比例5进行催化剂稳定性试验,一反氢分压为15.2mpa,二反氢分压为14.9mpa,一反液时体积空速0.42h-1,二反液时体积空速0.39h-1,一反平均反应温度385℃,二反平均反应温度391℃,一反氢油比体积(v/v)650,二反氢油比体积(v/v)600的工艺条件下,进行加氢反应,反应结果见表8。表8渣油加氢稳定性试验结果固定床反应器1500h2000h2500h3000h加氢重油s,wt%实施例54150420343594572加氢重油s,wt%对比例55029512153895502加氢重油ccr,wt%实施例55.726.036.326.68加氢重油ccr,wt%对比例55.465.816.176.52加氢重油ni+v,µg/g实施例512.6513.7514.9616.22加氢重油ni+v,µg/g对比例516.3417.5318.0919.97由表8中实施例5和对比例5的结果对比可知,本发明方法加入的乙烯焦油虽然其残炭含量高于渣油原料,但由加氢重油的残炭含量推得,在不同运转时间下,本发明方法的脱残炭率与对比例5相当,甚至略高于对比例5。由表8长时间运转周期的考察可见,采用实施例5的渣油加氢处理方法得到了预料不到的反应效果,经过3000小时稳定运行,加氢重油中硫含量为4572µg/g,残炭小于6.7%,金属小于17µg/g,比采用对比例5现有方法进行反应得到的生成油性质有了明显改善,有利于延长装置的运转周期。当前第1页12