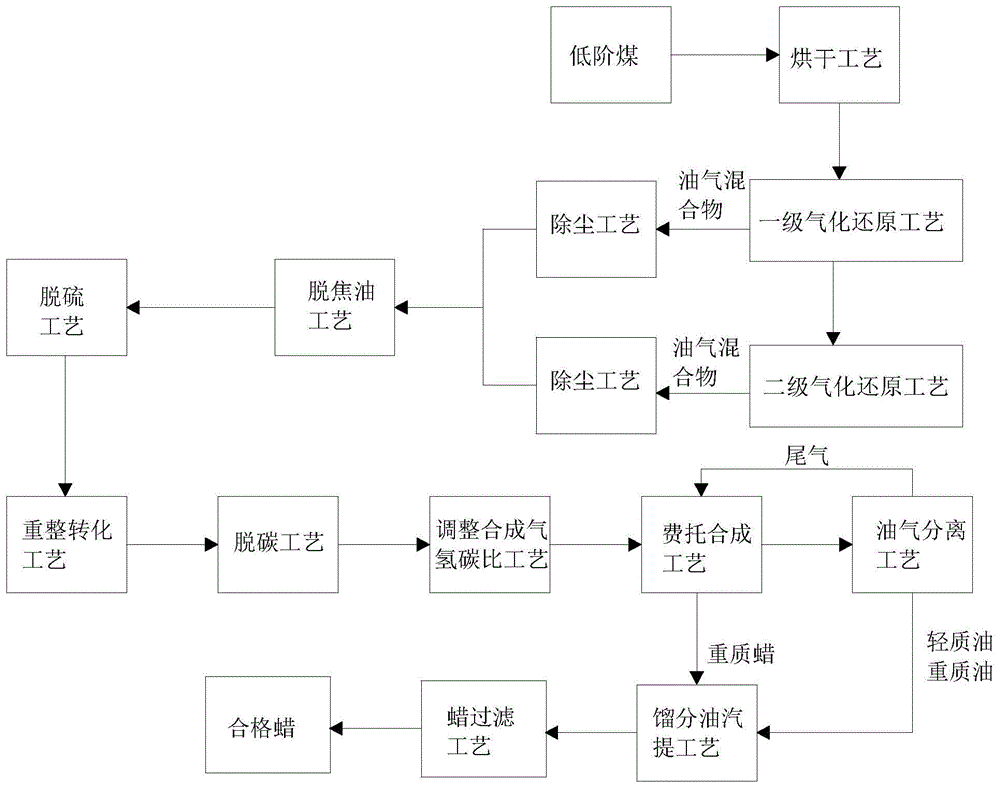
本发明涉及煤物质清洁利用
技术领域:
,尤其涉及一种利用低阶煤中挥发分费托合成蜡的方法。
背景技术:
:我国是一个富煤、贫油、少气的国家,煤炭消费量占一次能源消费量的60%以上,这决定了在相当长的一段时间内,以煤为主的能源结构难以改变。从已探明的煤矿品质看,我国的中低阶煤所占比重非常大,因而合理而高效的利用中低阶煤生产高品质化工产品显得尤为重要。我国目前对煤炭资源利用的方式手段比较单一,只是简单的燃烧获得其中的燃烧化学能,这种简单的利用方式不仅仅是对能源资源的巨大的浪费,而且燃烧产生的各种产物还会严重地污染环境。按照我国现阶段的国情和能源结构情况,把我国富含的煤和天然气资源就地转化为更方便运输和更加环保的液体燃料,不仅可以解决资源浪费的问题,同时也可以对我国的环境改善做出贡献。煤经费托合成制取燃料油和化学品是洁净煤
技术领域:
的重要内容之一。费托合成是将煤制气转化成为高级烃的化学过程,是非石油含碳资源(煤炭、天然气、渣油以及生物质等)高效转化利用最重要的途径。煤制气在催化剂的作用下生成一系列不同碳数的高级烃,同时得到一些低碳烯烃和醇类等。初产品经进一步处理得到汽油、柴油等油品以及乙烯、丙烯、润滑油和石蜡等化学品。费托铁基浆态床出来的产品以汽油、柴油为主。就汽油来说,我国的汽油替代办法已经很多(如乙醇汽油、甲醇汽油、mtg巯基乙酸单乙醇胺、天然气、lpg液化石油气)。特别是近期国家正在制定相关标准,大力推广替代汽油的应用。因此,采用费托合成生产汽油不是最佳途径。随着汽车工业的快速发展和环境保护意识的增强,高档润滑油在市场份额中所占的比例越来越大,而优质基础油原料处于长期结构性短缺状态。费托合成粗产品中软蜡的饱和度高,几乎不含硫、氮、芳烃,是制备高档润滑油基础油不可多得的优质原料,具有可观的商业利益。技术实现要素:有鉴于此,本发明的目的是针对现有技术的不足,提供了一种利用低阶煤中挥发分费托合成蜡的方法,通过将低阶煤中的挥发分气化还原获得油气混合物,将油气混合物净化处理除掉杂质得到包含h2、co和烃类的混合气体,利用催化重整将混合气体中的烃类重整转化来增大混合气体中h2和co的体积百分总比,应用费托合成技术将合成气用于生产轻质油、重质油和蜡等,产品附加值高,利于运输,从而提高了资源的利用率;而且本发明原料来源广泛,工艺能耗低,有利于节省生产成本。为解决上述技术问题,本发明提供了如下技术方案:一种利用低阶煤中挥发分费托合成蜡的方法,低阶煤依次通过烘干工艺和气化还原工艺处理得到油气混合物,所述气化还原工艺是在无氧或微氧条件下对烘干后的低阶煤进行加热的化学反应工艺;所述油气混合物经净化工艺得到包含co、h2和烃类的混合气体;所述混合气体经部分烃类重整转化工艺处理得到包含co和h2的重整转化气,所述重整转化气通过脱碳工艺处理得到合成气,通过补充co或h2将所述合成气的氢碳比调整为1.5-2.2;所述合成气在费托合成催化剂作用下进行费托合成反应并经油气分离工艺得到粗重质油、粗轻质油、重质蜡和尾气,所述粗重质油、粗轻质油和重质蜡经馏分油汽提工艺得到重质油、石脑油和轻质蜡,所述轻质蜡经蜡过滤工艺处理得到产品合格蜡,所述尾气作为所述费托合成反应的循环气。烘干工艺将低阶煤中大部分的水分去除,得到烘干后的低阶煤和废气,烘干后的低阶煤进入气化还原工艺发生反应得到高温的油气混合物和带有一定温度的提质煤;气化还原工艺采用的无氧或微氧环境中氧气的来源主要分以下几种情况:(1)、原料低阶煤内部的空隙,物料与物料之间的空隙夹带的空气;(2)从气化还原工艺的进料口、出料口等泄露混入的少量空气;(3)、在爆炸极限值以下,气化还原工艺内可以稍微通入占煤炭质量百分比5%的o2或者(空气),进一步优选通入占煤炭质量百分比3%的o2或者(空气),有利于提高气化还原反应的温度、防止结焦等,而且同时保证了整个气化还原工艺反应的安全稳定性;优选烘干后的低阶煤在无氧环境进行气化还原反应,避免了烘干后的低阶煤在进入气化还原工艺反应过程中烘干后的低阶煤与氧气发生燃烧反应,生成大量不能燃烧的co2,从而保证得到的高温的油气混合物中co2的体积百分较小,有利于后续制备高能量密度的合成气,工艺步骤少,简单易操作,以使得反应能够安全进行;高温的油气混合物中含有co、h2、co2、烃类、灰尘、煤焦油和含硫化合物等,通过净化工艺除去灰尘、煤焦油和含硫化合物等杂质气体,从而得到净化后的混合气体;混合气体主要包含co、h2和烃类,众所周知,co和h2可直接作为化工合成的一级原料,烃类则需要重整转化才能生成co和h2,因此利用重整转化工艺将混合气体中部分烃类重整转化得到包含co和h2的重整转化气,重整转化气中co和h2一部分来源于混合气体原有的co和h2,另一部分来源于部分烃类重整转化得到包含co和h2,大大提高了重整转化气中co和h2总的体积百分比。重整转化气中的co2对于费托合成蜡属于无效气体,因此采用脱碳工艺尽可能降低重整转化气中的co2的体积百分比,以便获得体积百分比更大的co和h2,从而得到主要包含co和h2的合成气。因为费托反应合成蜡要求合成的原料气中的氢碳比在1.5-2.2之间,因此需要调整重整转化气的氢碳比以便得到符合费托合成原料气条件的合成气,本发明中采用补充co或h2的办法使得的重整转化气的氢碳比界于1.5-2.2之间,即为所得气体为氢碳比为1.5-2.2的合成气。合成气在费托合成催化剂作用下进行费托合成反应,反应后的气体通过油气分离得到粗重质油、粗轻质油、重质蜡和尾气,尾气作为循环气进入费托合成,粗重质油、粗轻质油和重质蜡经馏分油汽提工艺得到产品合格蜡,同时还能得到高附加值的重质油和石脑油。优选的,所述净化工艺包括除尘工艺、脱焦油工艺和脱硫工艺。高温的油气混合物中含有灰尘、煤焦油、水蒸气、co2、h2s和cos等;先利用除尘工艺除尘,防止在除尘过程中由于油气混合物的温度降低,导致煤焦油和水蒸气等冷凝成液态并粘附大量灰尘造成后续工艺管道堵塞,造成除尘效果下降。再利用脱焦油工艺除掉大量的焦油和水蒸气,防止有水冷却附着在工艺管道中堵塞管道,积碳等问题。进一步优选的,冷却后的油水混合物再通过油水分离即可得到副产品煤焦油。最后再将脱焦油工艺处理后的剩余的气体进入脱硫工艺脱除h2s和cos等,避免后续工艺中的催化剂中毒。优选的,所述费托合成反应是在1.0-4.5mpa的压力、180-250℃的温度和催化剂存在的条件下进行的。目前费托合成工艺主要包括高温费托合成和低温费托合成。高温费托合成工艺一般采用流化床反应器,多采用fe基催化剂,温度在300-350℃之间,压力约为2.5mpa,主要得到c1-c15的化合物,生产汽油和直链低分子量烯烃,其不饱和烃的选择性高达67%。低温费托合成工艺一般采用固定床或浆态床反应器,使用fe基或co基催化剂,温度在180-250℃之间,压力为1.0-4.5mpa,反应能耗低,主要生产高分子量直链石蜡烃,因此本发明中优选低温费托合成目标产品蜡。优选的,所述气化还原工艺的反应温度为350-800℃。在此温度下,烘干后的低阶煤中的挥发分从低阶煤中逸出,从而得到高温的油气混合物,气化还原反应后剩余的固体残渣即为带温的提质煤,提质煤中的挥发分含量为8-15wt%。其中,气化还原工艺可以为一级,也可以为多级。当采用一级气化还原工艺时,主要是为了得到大部分高温的油气混合物,温度的高低直接影响后续产气量、提质煤的产量和一级提质煤的温度;当采用多级气化还原工艺时,多级气化还原工艺主要作用是把上一级气化还原工艺内的无法气化的固体物质(包括气化后的粉煤,固体杂质等),一定量的、无法在一定停留时间内气化的、类似沥青等高沸点油状物继续气化和停留时间短、来不及析出或者温度达不到酚类化合物、芳香烃化合物等的缩聚反应条件,继续反应气化,有利于提高气体产量和提质煤的品质。优选的,所述气化还原工艺包括一级气化还原工艺和二级气化还原工艺,将所述烘干后的低阶煤依次通过一级气化还原工艺和二级气化还原工艺处理得到油气混合物和提质煤。优选的,所述混合气体经部分烃类重整转化工艺为将混合气体中的各组分气体不经分离直接通过部分烃类重整转化为co和h2的烃类重整转化工艺。因为重整转化的目的只是为了将烃类转化生成co和h2,得到重整转化气,而混合气体中自身已含有一部分co和h2,因此无需将烃类从混合气体中分离出来再进行烃类的重整转化,采用这样的操作节省了工艺步骤,经济效益高。重整转化工艺包括部分催化氧化、蒸汽催化重整转化和非催化重整转化。部分催化氧化、蒸汽催化重整转化均需要催化剂,重整转化工艺的催化剂多为负载型催化剂,活性组分主要是ni、co、fe、cu等非金属和rh、ru、pt等贵金属。重整转化一般需要供热,可以采用直接供热或者间接供热的方式。重整转化气中co和h2的来源为两个部分,一部分为混合气体中部分烃类通过催化转化得到的co和h2,另一部分为混合气体中的原有h2和co。部分催化氧化是采用氧气与一部分烃类燃烧直接供热,在催化剂的作用下的,混合气体中的部分烃类与水蒸气反应生成co和h2;蒸汽催化重整转化时采用外界供热,在催化剂的作用下使得混合气中的部分烃类与水蒸气反应生成co和h2;两种方法的主要反应机理为:(1)cmhn+mh2o=mco+1/2(n+2m)h2主反应,吸热反应(2)co+h2o=co2+h2副反应,吸热反应非催化重整转化重整不需要催化剂,主要反应机理为:ch4+1/2o2→co+2h2,除甲烷外其他烃类与甲烷与o2的反应机理类似。因此优选的,所述重整转化工艺为部分催化氧化,所述部分催化氧化为将纯氧和水蒸气通入混合气体中,在850-1300℃的温度和催化剂存在的条件下,混合气体中的部分烃类与水蒸气反应,得到co和h2。优选的,所述重整转化工艺为蒸汽催化重整转化,所述蒸汽催化重整转化为将水蒸气通入混合气体中,在间接供热使温度达到850-1200℃和催化剂存在的条件下,混合气体中部分烃类与水蒸气反应得到co和h2。优选的,所述重整转化工艺为非催化重整转化,所述非催化重整转化为将纯氧通入混合气体中,混合气体中的部分烃类与纯氧反应得到co和h2。优选的,所述馏分油汽提工艺的介质为过热蒸汽,所述过热蒸汽的压力为2.0-2.5mpa,所述过热蒸汽的温度为350℃-380℃。基于以上技术方案,本发明相对于现有技术具有以下有益效果:1、本发明在无氧或微氧条件下将烘干后的低阶煤气化还原制备成混合气体,减少了混合气体中n2和co2等无效气体的量,提高了混合气体的co、ch4和h2能量密度,混合气体主要来自低阶煤中的挥发分,将低阶煤中的挥发分用于生产轻质油、重质油和蜡等液体产品,产品附加值高,利于运输,从而提高了资源的利用率。2、低温费托合成工艺能耗低,设备要求低,有利于节省生产成本。3、本发明中费托合成蜡的饱和度高,几乎不含硫、氮、芳烃,是制备高档润滑油基础油不可多得的优质原料,具有可观的商业利益。附图说明为了更清楚地说明本发明中实施例或现有技术中的技术方案,下面将对实施例中所需要使用的附图作简单地介绍,显而易见地,下面描述中的附图仅是本发明中记载的一些实施例,对于本领域普通技术人员来讲,还可以根据这些附图获得其他的附图。图1为一种利用低阶煤中挥发分费托合成蜡的方法的流程示意图。具体实施方式下面结合具体实施例来对本发明进行进一步说明,但并不将本发明局限于这些具体实施方式。本领域技术人员应该认识到,本发明涵盖了权利要求书范围内所可能包括的所有备选方案、改进方案和等效方案。本发明中,若非特指,所采用的原料和设备等均可从市场购得或是本领域常用的。下述实施例中的方法,如无特别说明,均为本领域的常规方法。如图1所示,本发明公开了一种利用低阶煤中挥发分费托合成蜡的方法,低阶煤依次通过烘干工艺和气化还原工艺处理得到油气混合物,所述气化还原工艺是在无氧或微氧条件下对烘干后的低阶煤进行加热的化学反应工艺;所述油气混合物经净化工艺得到包含co、h2和烃类的混合气体;所述混合气体经部分烃类重整转化工艺处理得到包含co和h2的重整转化气,所述重整转化气通过脱碳工艺处理得到合成气,通过补充co或h2将所述合成气的氢碳比调整为1.5-2.2;所述合成气在费托合成催化剂作用下进行费托合成反应并经油气分离工艺得到粗重质油、粗轻质油、重质蜡和尾气,所述粗重质油、粗轻质油和重质蜡经馏分油汽提工艺得到重质油、石脑油和轻质蜡,所述轻质蜡经蜡过滤工艺处理得到产品合格蜡,所述尾气作为所述费托合成反应的循环气。本发明的原料低阶煤可以是粉煤也可以是块煤,当低阶煤采用块煤时,对过大块煤可以通过破碎、筛分处理以获得粒度较小的粉煤。优选采用粉煤作为原料,一方面是因为粉煤无需再经破碎、筛分处理,节省工艺步骤,烘干时受热面积大,烘干效率高,另一方面是粉煤相对块煤价格低廉。优选采用粒度小于20mm的粉煤,再进一步优选采用粒度小于6mm的粉煤。低阶煤主要包括褐煤和烟煤,低阶煤中挥发分含量一般为20%-55%,焦油的含量为3%-15%左右,固定碳的含量为30%-60%、水的含量为10%-40%,剩余为灰尘等其他杂质。低阶煤的煤化程度低,但蕴藏丰富的油气资源,低阶煤中富含的挥发分对提取合成气非常有利,因此优选挥发分在30%-55%之间的低阶煤。烘干一般只能除去低阶煤中大部分的自由水,而不能除掉低阶煤中的结合水,因此,低阶煤通过烘干工艺处理后得到烘干后的低阶煤和废气,所得烘干后的低阶煤依然含有一定量的水分,这部分剩余的水分可在后续的气化还原工艺中气化变成水蒸气。若低阶煤中含有大量的水分,会导致气化还原反应过程中耗热量大,因此,本发明的技术方案首选对低阶煤通过烘干工艺进行处理先除掉低阶煤中的一部分水分。烘干工艺的烘干介质可为烟气或者水蒸气,烘干可分为直接烘干和间接烘干。当利用烟气作为烘干介质时,虽然烟气与低阶煤直接接触的烘干的效率是最高的,但是采用烟气进行烘干时要严格控制烘干工艺环境中氧气的体积百分比在爆炸极限以下,以防止爆燃,烟气间接烘干的效率也并不理想,因此为了生产安全和烘干效率,优选水蒸气烘干。水蒸气直接烘干容易有可能导致水蒸气混入与低阶煤中,不仅造成了反应煤资源的消耗资,有降低了烘干效率,因此采用水蒸气间接烘干低阶煤的烘干方式,以防止水蒸气中的水分进入低阶煤中。另外,烘干过程中如果水蒸气压力过大,水蒸气带来的温度过高容易导致在烘干过程中,低阶煤中部分挥发分会逃逸出来,一方面挥发分的逸出会带来安全隐患,另一方面会影响后续气化还原工艺的产气量,因此烘干过程中烘干蒸汽压力不易过大,以保证既能保证烘干效果,又可以保证低阶煤中的挥发分不被气化。因此,优选的,烘干工艺采用水蒸汽间接烘干,水蒸汽的压力为0.3-1.5mpa,水蒸汽的温度为105-250℃,在此工艺条件下可以最大化的降低低阶煤中的含水率,甚至可以使得从烘干工艺的出料口排出的低阶煤中的含水量降低至7wt%以下,此时大部分的水分伴随着煤粉等扬尘从低阶煤中逸出,并且以水蒸气的形式进入烘干后产生的废气中,烘干工艺的出口物料温度为50-150℃;再进一步优选,当水蒸气的压力为0.6-1.2mpa,水蒸气的温度为120-200℃时,烘干后低阶煤的含水率将降低至6wt%以下,烘干工艺的出口物料温度为80℃-130℃。本发明的烘干工艺可以为一级,也可以为多级,因为如果一级烘干工艺后低阶煤的含水率仍然达不到工艺的要求,可以采用二级烘干、三级烘干工艺等多级烘干继续进一步干燥,直到烘干后低阶煤的含水率符合工艺条件为止。另外,多级烘干工艺可以串联设置也可以并联设置,采用多级烘干工艺串联时可以加强干燥效果,并联时可以增大烘干工艺的处理量,因此根据实际生产工艺的需求,对多级烘干工艺是串联还是并联或者串联并联同时的设计,可以根据实际情况进行调整,只要能达到相同的技术效果即可,具体的,比如,当烘干工艺的进料量以20-30t/h的低阶煤计,可采用一级蒸汽烘干工艺;当烘干工艺的进料量以50-70t/h的低阶计,可采用二级蒸汽烘干工艺,这样更经济合理些。优选的,通过烘干工艺烘干后的低阶煤进入至气化还原工艺进行反应,在烘干后的低阶煤进入气化还原工艺前还可以增设气化进料工艺,以便将烘干后的低阶煤快速进入气化还原工艺,增大物料的表面积,有利于加快气化还原反应。其中,气化还原工艺是在无氧或微氧条件下对烘干后的低阶煤进行加热的化学反应工艺。烘干后的低阶煤进入气化还原工艺,在烟气等加热介质的加热下,反应过程中无需加入添加剂等其他物质,温度一般为350℃-800℃,压力≤30kpa下发生复杂化学反应的过程,得到固态的碳和高温的油气混合物,其中,固态的碳即为提质煤,提质煤中的挥发分8-15wt%。高温的油气混合物为包含co、h2、co2、烃类、煤焦油、灰尘和有机硫等多种杂质气体。其中,气化还原工艺采用的无氧或微氧环境氧的来源主要分以下几种情况:(1)、原料低阶煤内部的空隙,物料与物料之间的空隙夹带的空气,这部分的空气中的o2在气化还原工艺中高温的环境下立即与煤反应生成co2或co;(2)从气化还原工艺的进料口、出料口等泄露混入的少量空气,这部分空气的氧气,这部分微量的o2在气化还原工艺中高温的环境下立即与煤反应生成co2或co;(3)、在爆炸极限值以下,气化还原工艺内可以稍微通入占煤炭质量百分比5%的o2或者(空气),这种操作具有以下优点:①可提高气化还原工艺内的温度和能量利用率;②提高了炭的转化率;③防止煤结焦;④少量o2与低阶煤不完全燃烧产生了更多的co,为后续带来了更多的合成气。由于气化还原工艺内部温度较高,通入的少量o2瞬间会发生氧化反应(包括燃烧反应),很多可燃物的燃点都在气化还原反应的反应温度以下。因co与空气混合爆炸限12%-74.2%;h2爆炸值为4%-75%。o2占空气比例为21%。折算后纯氧的爆炸极限上值为6%左右。通过理论测算,100kg的煤会产生约80nm3的co和h2。所以,通入占煤炭质量百分比5%的o2是安全的;再进一步优选,通入占煤炭质量百分比3%的o2,以确保整个气化还原工艺反应的安全稳定性。但是,当气化还原反应的温度满足工艺要求时,也可以不通入氧气,优选烘干后的低阶煤在无氧环境进行气化还原反应,以使得反应能够安全进行。其中,气化还原工艺可以为一级,也可以为多级。当采用一级气化还原工艺时,主要是为了得到大部分高温的油气混合物,温度的高低直接影响后续产气量、提质煤的产量和一级提质煤的温度,气化还原工艺的反应温度为350℃-800℃,提质煤中的挥发分含量为8-15wt%,进一步优选,气化还原工艺的反应温度为400-750℃;再进一步优选450-700℃。当采用多级气化还原工艺时,多级气化还原工艺主要作用是把上一级气化还原工艺内的无法气化的固体物质(包括气化后的粉煤,固体杂质等),一定量的、无法在一定停留时间内气化的、类似沥青等高沸点油状物继续气化和停留时间短、来不及析出或者温度达不到酚类化合物、芳香烃化合物等的缩聚反应条件,继续反应气化,有利于提高气体产量和提质煤的品质。除了保证气化还原工艺的温度合理之外,同时也得保证气化还原工艺内一定的停留时间,停留时间太短,挥发分还未完全逸出气化,影响气体产量的同时,更多的影响提质煤的质量;停留时间太长,虽然产品得到了保证,但产量跟不上,所以保持一个合理的气化还原反应停留时间对产品产量和质量的至关重要。由于原料低阶煤的品种不同,一般气化还原工艺内物料的停留时间为30min-4h。本发明中优选采用两级气化还原工艺,烘干工艺烘干后的物料先进入一级气化还原工艺再进入二级气化还原工艺,烘干后的低阶煤先进入一级气化还原工艺得到一级气体和一级固体,一级固体再进入二级气化还原工艺继续气化得到二级气体和二级固体,二级固体即为提质煤;一级气化还原工艺的进料温度为80℃-120℃,出气温度为180℃-550℃,反应温度为450℃-650℃,出料温度为350℃-600℃;所述二级气化还原工艺的进料温度为350℃-600℃,出料温度为450℃-750℃,反应温度为550℃-800℃,出气温度为450℃-700℃。当采用两级气化还原工艺时,主要是为了使大部分挥发分完全气化掉,既能得到大量的气体又能得到挥发分更低的提质煤,其中提质煤中的挥发分含量为3-8wt%。提质煤的单位价格一般为500-600元/t,气化还原后的提质煤可用于售卖等。二级气化后的提质煤挥发分更低,基本燃烧无烟,亦称为无烟煤,可做钢厂烧结煤,无烟煤的市售价格约800-1400元/吨。从气化还原工艺得到的高温的油气混合物进入净化工艺以除掉固体灰尘、焦油和含硫化合物等以即可得到混合气体。净化工艺包括除尘工艺、脱焦油工艺和脱硫工艺,油气混合物依次经除尘工艺、脱焦油工艺和脱硫工艺处理得到包含co、h2和烃类的混合气体。高温的油气混合物中含有灰尘、煤焦油、水蒸气、co2、h2s和cos等;先利用除尘工艺除尘,例如采用旋风除尘器,防止在除尘过程中由于油气混合物的温度降低,导致煤焦油和水蒸气等冷凝成液态并粘附大量灰尘造成后续工艺管道堵塞,造成除尘效果下降。再利用脱焦油工艺除掉大量的焦油和水蒸气,防止有谁冷却附着在工艺管道中堵塞管道,积碳等问题。例如,脱焦油工艺采用喷淋塔,冷却油气。进一步优选的,冷却后的油水混合物再通过油水分离即可得到副产品煤焦油,煤焦油的单位价格为2000-2500元/t,富产的煤焦油的价值较高。最后再将脱焦油工艺处理后的剩余的气体进入脱硫工艺。最后再将油气冷却工艺处理后的剩余的气体通过脱硫工艺使得硫化物的含量降低到10ppm以下,防止含硫化合物造成后续重整转化工艺中的催化剂中毒,例如干法脱硫等,只要能达到脱硫的效果即可。采用以上工艺可除掉杂质气体和固体,以便得到净化后的混合气体,混合气体杂质少,便于后续工艺处理,保证了后续设备的稳定性。为了进一步优化工艺,如果油气混合物中含不饱和烃的体积分数过高,还可以增设加氢工艺将其转化为饱和烃,防止不饱和烃脱碳而引起积碳等问题;进一步地,还可以增设脱硝工艺或脱氯工艺以实现进一步净化油气混合物。本发明中优选采用两级气化还原工艺,每级气化还原工艺分别依次与各自的除尘工艺、脱焦油工艺和脱硫工艺等连接;每级气化还原后产生的高温油气中的灰尘量较大,因此,为了进一步优化工艺,每级气化还原工艺先与各自的除尘工艺连接,每级的除尘工艺再与同一套脱焦油工艺和脱硫洗工艺依次连接,以节省工艺环节。从净化工艺得到混合气体进入重整转化工艺进行处理即得到包含co和h2的重整转化气。其中,混合气体中包括co、h2、co2和包含ch4的烃类等。为了进一步优化工艺,混合气体再进入重整转化工艺处理前可先进行压缩处理提高混合气体的压力,便于重整转化反应的发生。混合气体经部分烃类重整转化工艺为将混合气体中的各组分气体不经分离直接通过部分烃类重整转化为co和h2的烃类重整转化工艺。因为重整转化的目的只是为了将烃类转化生成co和h2,而混合气体中自身已含有一部分co和h2,因此无需将烃类从混合气体中分离出来再进行烃类的重整转化,采用这样的操作节省了工艺步骤,经济效益高。重整转化主要包括部分催化氧化、蒸汽催化重整转化和非催化重整转化。部分催化氧化、蒸汽催化重整转化均需要催化剂,重整转化工艺的催化剂多为负载型催化剂,活性组分主要是ni、co、fe、cu等非金属和rh、ru、pt等贵金属。重整转化一般需要供热,可以采用直接供热或者间接供热的方式。重整转化气中co和h2的来源为两个部分,一部分为混合气体中部分烃类通过催化转化得到的co和h2,另一部分为混合气体中的原有h2和co。部分催化氧化是采用氧气(纯氧)与一部分烃类燃烧直接供热,使反应温度达到850-1300℃,在催化剂的作用下的,混合气中的部分烃类与水蒸气反应生成co和h2;蒸汽催化重整转化时采用外界供热,使温度达到850-1200℃,在催化剂的作用下使得混合气体中的部分烃类与水蒸气反应生成co和h2;两种方法的主要反应机理为:(1)cmhn+mh2o=mco+1/2(n+2m)h2主反应,吸热反应(2)co+h2o=co2+h2副反应,吸热反应以ch4为例,主要反应方程式为ch4+h2o→co+3h2,生成的h2和co的摩尔比为3:1,比例较大,对制备合成气非常有利。非催化重整转化重整不需要催化剂,主要反应机理为:ch4+1/2o2→co+2h2,生成的h2和co的摩尔比为2:1,有利于制备重整转化气。除甲烷外其他烃类与甲烷与o2的反应机理类似。表1:重整转化前混合气体中各个组分体积百分比的范围值:组分h2包含ch4的烃类coco2其他含量15-45%10-52%5-25%5-25%0.1-10%其他组分为n2、水蒸气等,重整转化前混合气体中各组分的体积百分比的总和为100%。表2:重整转化后混合气体中各个组分体积百分比的范围值:组分h2包含ch4的烃类coco2其他含量30-70%1-5%10-30%3-35%0.1-10%其他组分为n2和水蒸气等,重整转化后混合气体中各组分的体积百分比的总和为100%。由表1和表2可知,混合气体经重整转化工艺处理后,混合气体中的烃类的体积比百分比由原来的10-52%降低为1-5%,重整转化后的混合气体中即为重整转化气,重整转化气中的h2和co的体积比百分比大幅提高。重整转化气进入脱碳工艺脱除co2,重整转化气中的co2对于费托合成蜡属于无效气体,因此采用脱碳工艺尽可能降低重整转化气中的co2的体积百分比,以便获得体积百分比更大的co和h2,从而得到主要包含co和h2的合成气。工业上脱除co2的方法很多,总的来说可以分为两大类:一类是溶剂吸收法,另一类是变压吸附法(psa)。溶剂吸收法包括物理吸收法、化学吸收法以及物理-化学吸收法,物理吸收法,如低温甲醇洗法,聚乙二醇二甲醚法,碳酸丙烯酯法;化学吸收法,一般像naoh,koh,ba(oh)2等碱性较强的碱液能够很有效地吸收co2气体,其原理是因为co2气体溶于水生成碳酸,碳酸小部分电离生成的氢离子与碱液中的氢氧根离子反应生成水,因此可脱除co2。psa法是利用吸附剂对吸附质在不同分压下具有不同的吸附容量、吸附速度和吸附力,并且在一定压力下对被分离的气体混合物的各组分有选择吸附的特性,加压吸附除去原料气中杂质组分,减压脱除这些杂质而使吸附剂获得再生、该法具有工艺简单、操作稳定、能耗低、无“三废”排放问题等优点,是一种节能脱co2的新技术,前景广阔。另外本工艺工的脱除的co2也可以进行回收再利用。进一步优选的,在对合成气进行精脱硫处理使得合成气的硫化物的含量降低到5ppm以下,精脱硫例如采用脱硫吸附剂等。再进一步优选的,增设脱水工艺,一遍进一步脱除合成气中的水蒸气。费托合成蜡所需的原料气中的有效组分为h2和co,对合成气中氢碳比的要求有以下表达式:r=(h2-co2)/(co+co2),其中,原料气的氢碳比r=(h2-co2)/(co+co2)理论值为2.0,最佳值为1.5-2.2。当r值大于2.2时,代表氢多碳少,此时费托合成反应后的尾气气量大,循环气压缩机功耗大,许多原料气体经过多重工序制备的有用的h2、co等随着尾气送入燃料系统烧掉,造成严重资源浪费,原料消耗量增加。当原料气的r值小于1.5时,不能满足费托合成蜡的要求。而脱碳工艺处理后的气体的r值一般不能刚好满足氢碳比界于1.5-2.2之间,因此需要对其r值进行调整。脱碳后的气体一般通过补充高纯度的co或者h2的办法来使得合成气的氢碳比界于1.5-2.2之间。费托合成的主要反应为:生成烯烃:nco+2nh2=cnh2n+nh2o2nco+nh2=cnh2n+nco2生成烷烃:nco+(2n+1)h2=cnh2n+2+nh2o2nco+(n+1)h2=cnh2n+2+nco2副反应的反应如下:生成醇类:nco+2nh2=cnh2n+1oh+(n-1)h2o生成甲烷:co+3h2=ch4+h2o生成醛类:(n+1)co+(2n+1)h2=ch2n+1+nh2o水煤气反应:co+h2o=h2+co2结炭反应:2co=c+co2目前费托合成工艺分两类:高温费托合成和低温费托合成。高温费托合成工艺一般采用流化床反应器,多采用fe基催化剂,温度在300-350℃之间,压力约为2.5mpa,主要得到c1-c15的化合物,生产汽油和直链低分子量烯烃,其不饱和烃的选择性高达67%。低温费托合成工艺一般采用固定床或浆态床反应器,使用fe基或co基催化剂,温度在180-250℃之间,压力为1.0-4.5mpa,反应能耗低,主要生产高分子量直链石蜡烃,因此本发明中优选低温费托合成目标产品蜡。与fe基催化剂相比,co基催化剂具有较高的活性和链增长能力、较低的水汽变换反应,产物中含氧化合物少、二氧化碳低、反应过程中不易积碳、稳定性高、失活速率低等优点,因此,co基催化剂被认为是低温费托合成反应的最佳选择。油气分离:低温费托在生成反应后的气体主要为烃类物质,固态或者液态渣状物质主要为重质蜡,烃类物质进入油气分离工艺处理后分别得到粗重质油、粗轻质油和尾气,尾气可作为循环气进入费托合成工艺,以便节省气体原料,提高合成气的利用率。馏分油汽提:馏分油汽提主要包括汽提塔和释放气压缩机。来自油气分离工艺的粗轻质油经过加热后送至汽提塔中上部。来自费托反应器的重质蜡自汽提塔底部进入汽提塔。油气分离工艺分离出的粗重质油经加热后进入汽提塔中下部。汽提介质采用压力为2.3-2.5mpa、温度为350℃-380℃的过热蒸汽,由汽提塔底部进入。各段中间油品自上向下与汽提塔底部的油气逆向接触汽提。各组份在汽提塔内经充分传质、传热后,汽提塔顶部分离出的气相物流经过冷却降温至50℃以下,进入汽提塔顶分液罐进行油、水、气三相分离,分离出的释放气至释放气压缩机,分离出的轻质石脑油一部分作为回流液返回至汽提塔顶部塔盘,另一部分送低温油洗单元;分离出汽提凝液送入水处理厂。汽提塔中部抽出的稳定重质油。汽提塔底部分离出的高温稳定蜡进入后续的蜡过滤工艺。释放气经过释放气压缩机分液罐分液后进入释放气压缩机,释放气经压缩后与来自费托反应后的部分尾气合并进行脱除co2处理。蜡过滤:由于从馏分油汽提得到的轻质蜡中含有少量的含油催化剂粉末或颗粒的重质烃,为避免这些杂质影响蜡的产品质量,在160-180℃的温度和0.4-0.8mpa压力的操作环境下,将来自馏分油汽提的稳定蜡和合成费托合成过程中排出的渣蜡通过过滤器过滤得到合格蜡。综上所述,本发明相对于现有技术具有以下有益效果:1、本发明在无氧或微氧条件下将烘干后的低阶煤气化还原制备成混合气体,减少了混合气体中n2和co2等无效气体的量,提高了混合气体的co、ch4和h2能量密度,混合气体主要来自低阶煤中的挥发分,将低阶煤中的挥发分用于生产轻质油、重质油和蜡等液体产品,产品附加值高,利于运输,从而提高了资源的利用率。2、低温费托合成工艺能耗低,设备要求低,有利于节省生产成本。3、本发明中费托合成蜡的饱和度高,几乎不含硫、氮、芳烃,是制备高档润滑油基础油不可多得的优质原料,具有可观的商业利益。以上所述,以上实施例仅用以说明本发明的技术方案,而非对其限制;尽管参照前述实施例对本发明进行了详细的说明,本领域的普通技术人员应当理解:其依然可以对前述各实施例所记载的技术方案进行修改,或者对其中部分技术特征进行等同替换;而这些修改或者替换,并不使相应技术方案的本质脱离本发明各实施例技术方案的精神和范围。当前第1页12