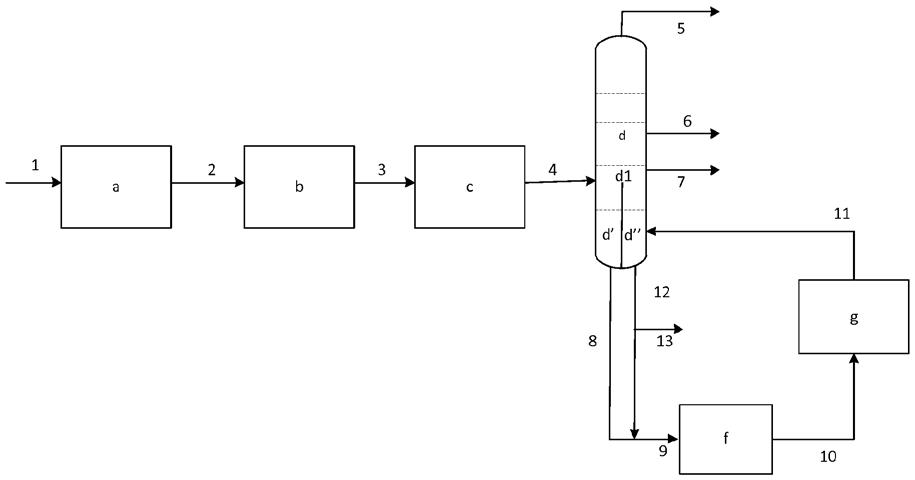
使用分区蒸馏塔的两步加氢裂化方法
1.发明领域本发明涉及两步加氢裂化方法,其可以消除重质多环芳族化合物(hpna)而不降低可改质产物的收率。
2.加氢裂化方法通常用于将烃混合物转化为可易于改质的产物的精炼厂中。这些方法可用于将轻质馏分(例如石油)转化为更轻质的馏分(lpg)。然而,它们通常更多地用于将较重质的原料(例如重质合成馏分或石油馏分,例如由减压蒸馏产生的瓦斯油或来自费
‑
托单元的流出物)转化为石油或石脑油、煤油、瓦斯油。
3.某些加氢裂化方法还可以获得高度纯化的渣油,所述渣油可构成油的优良基础油。加氢裂化方法特别针对的一种流出物是中间馏出物(包含瓦斯油馏分和煤油馏分的馏分),即具有至少150℃的初沸点和上限恰好低于渣油的初沸点的终沸点(例如低于340℃、或低于370℃)的馏分。
4.加氢裂化是从以下三个主要要素中总结出其灵活性的方法:所用的操作条件、所用的催化剂类型以及可以一步法或两步法实施烃原料的加氢裂化的事实。
5.特别地,减压馏出物或vd的加氢裂化可以产生比vd本身更易于改质的轻质馏分(瓦斯油、煤油、石脑油等)。该催化方法无法将vd完全转换为轻质馏分。因此,在分馏之后存在或多或少显著比例的未转化的vd馏分,称为uco或未转化的油。为了提高转化率,可以将该未转化的馏分在一步加氢裂化方法的情况下再循环至加氢处理反应器的入口或者加氢裂化反应器的入口,或者在两步加氢裂化方法的情况下再循环至在分馏步骤结束时处理未转化的馏分的第二加氢裂化反应器的入口。
6.已知的是,将来自分离步骤的所述未转化的馏分再循环至两步法的第二加氢裂化步骤导致在裂化反应期间形成称为hpna的重质(多环)芳族化合物,并因此导致所述化合物在再循环环路中的不希望的积聚,进而导致第二加氢裂化步骤的催化剂性能下降和/或导致其结垢。通常在所述未转化的馏分的再循环中设置排出物(purge),其通常设置在分馏塔底管线中,从而降低再循环环路中的hpna化合物的浓度,调节排出物流量以平衡其形成流量。具体而言,hpna越重质,它们被保留在该环路中、积聚以及变得更重质的趋势就越大。
7.然而,两步加氢裂化方法中的转化率与和hpna同时排出的重质产物的量是直接相关的。
8.根据所述方法的操作条件,相对于引入的vd母料,所述排出物可为重质馏分的0
‑
5重量%,优选0.5
‑
3重量%。可改质产物的收率因此而降低,这对精炼厂造成不小的经济损失。
9.贯穿本文的其余部分中,hpna化合物被定义为多环或多核芳族化合物,其因此包含若干个稠合的苯核或苯环。它们通常被称为hpa(即重质多核芳族化合物)、pna或hpna。这些在不希望的副反应期间形成的化合物是稳定的且几乎不可能被加氢裂化。通常,“重质
”ꢀ
hpna是包含若干个稠合苯环的多环芳烃化合物,例如,晕苯(含24个碳的化合物)、二苯并(e,ghi)苝(含26个碳的化合物)、萘并[8,2,1
‑
abc]晕苯(含30个碳的化合物)和卵苯(含32个碳的化合物),它们是最容易例如通过色谱法鉴定和量化的化合物。
现有技术
[0010]
专利申请wo 2016/102302描述了将未转化的馏分或渣油中的hpna浓缩的方法,以消除hpna并减少排出的渣油的量,从而提高转化率,同时通过在分馏塔的进料点下方取出侧流来改善可改质产物的收率,被取出的物流具有低浓度的hpna和高比例的未在上游加氢裂化段中转化的烃。还可以在进料板下方和渣油排放点上方将汽提气体注入分馏塔的最低区段,从而汽提蒸馏渣油,从而在完全排出所述渣油之前将所述渣油中的最重质的化合物浓缩。这可以限制与排出物中的hpna稀释相关的收率的损失。
[0011]
具有低浓度hpna和高比例的未转化的烃的侧流的第二次取出可以有利地在进料板和用于取出最重质馏出物馏分的塔板之间进行。可以在外部汽提塔中汽提第二次取出的物流,然后将分离出的气态流出物的全部或一部分再循环到该塔中,并且将液体流出物的全部或一部分再循环到加氢裂化步骤中。在该方法中,不进行将未转化的渣油再循环至分馏塔的步骤。未转化的渣油也不再循环至加氢裂化步骤。将其完全排出。
[0012]
专利us 8 852 404描述了烃原料的加氢裂化方法,其中分馏塔在其下部包括垂直隔离壁,从而形成两个隔室,允许在所述塔的一个隔室中浓缩hpna,然后使用所述隔室作为汽提器将其消除或排出。该实施方案的目的是将由所述隔室中的hpna汽提段产生的蒸气用作用于分馏塔的另一个隔室的汽提区的汽提蒸气,而不是在所述塔中使用两种不同的汽提蒸气物流的两个入口。这可以限制与排出物中的hpna稀释相关的收率的损失。
[0013]
专利us 9 580 663描述了其中将在未转化的馏分(uco)中的hpna浓缩、从而将它们除去的加氢裂化方法,这导致转化并改善了收率。具体而言,所述专利us 9 580 663描述了一种加氢裂化方法,其中将来自分馏塔底部的未转化的馏分(uco)的一部分在所述分馏塔外部的汽提塔中以逆流方式汽提,从而在汽提塔的顶部产生蒸气馏分以及具有高浓度hpna的经汽提的液体馏分,然后将该蒸气馏分再循环至分馏塔的底部。排出具有高浓度hpna的重质液体馏分的至少一部分,可以将该馏分的另一部分再循环至汽提塔。该方法可以在排出hpna之前对其进行浓缩。重质液体馏分中的高浓度hpna可以以较低的排出物流量来除去hpna,这导致较高的总方法转化率,并改善了可改质产物的收率。
[0014]
这些方法在减少hpna方面带来了改进,但经常损害所需可改质产物的收率和成本。
[0015]
通过本申请人进行的研究发现,在两步加氢裂化方法中,实施其中使用隔离壁蒸馏塔的蒸馏步骤,可以在由所述塔内的隔离壁界定的特定隔室中浓缩hpna并排出它们,从而使其纯度是不使用所述隔离壁的方法中的纯度的两倍,所述隔离壁仅将所述塔的下部分隔成两个隔室,并且所述隔离壁位于所述塔采用来自第一加氢裂化步骤的液体烃流出物进料的进料点下方的塔的区段中。
[0016]
实际上,所述蒸馏塔在垂直隔离壁的任一侧上一方面进料有来自第一加氢裂化步骤的液体烃流出物,另一方面进料有来自第二加氢裂化步骤的液体烃流出物,从而在由所述隔离壁界定的所述塔的特定隔室中实现来自第二加氢裂化步骤的流出物中所含的hpna的浓缩,并因此避免了所述hpna被来自第一加氢裂化步骤的液体烃流出物稀释。
[0017]
因此,可以以更纯的方式排出hpna。在相同的hpna分流量下,排出物物流流量较小。然而,两步加氢裂化方法中的转化率与和hpna同时排出的重质产物的量是直接相关的。增加排出物中的hpna的浓度会减少从所述方法中提取的未转化产物的量,从而使总方法转
化率最大化。
[0018]
本发明的另一个优点是提供在相同的总方法转化率下,可以增加第二加氢裂化步骤的循环时间的方法。
[0019]
发明主题具体而言,本发明涉及烃原料的两步加氢裂化方法,所述烃原料包含至少20体积%、优选至少80体积%的沸点高于340℃的化合物,所述方法包括至少以下步骤:a)在氢气和至少一种加氢处理催化剂的存在下、在200℃
‑
400℃的温度下、在2
‑
16mpa的压力下、在0.2
‑
5h
‑1的空速下、并且采用使得氢气的升数/烃的升数的体积之比为100
‑
2000l/l的引入的氢气量来将所述原料加氢处理的步骤,b)将来自步骤a)的流出物的至少一部分加氢裂化的步骤,在氢气和至少一种加氢裂化催化剂的存在下、在250℃
‑
480℃的温度下、在2
‑
25mpa的压力下、在0.1
‑
6h
‑1的空速下、并且采用使得氢气的升数/烃的升数的体积之比为80
‑
5000l/l的引入的氢气量来进行加氢裂化步骤b),c)在高压下分离来自加氢裂化步骤b)的流出物以产生至少气态流出物和液体烃流出物的步骤,d)将来自步骤c)的液体烃流出物的至少一部分蒸馏的步骤,所述步骤d)在至少一个蒸馏塔中进行,所述蒸馏塔在其底部包括垂直隔离壁,所述垂直隔离壁将所述塔的底部分隔成两个独立的隔室,即第一隔室和第二隔室,通过在低于或等于所述隔离壁上端的高度处将所述流出物引入所述第一隔室,从所述步骤d)中取出如下物质:
‑
任选的气态馏分,
‑
任选的沸点低于150℃的汽油馏分,
‑
沸点为150℃
‑
370℃、优选150℃
‑
350℃、优选150℃
‑
340℃的中间馏出物馏分,
‑
在所述第一隔室的下端处取出的沸点大于340℃、优选大于350℃、优选大于370℃的未转化的液体馏分,和
‑
在由所述隔离壁界定的所述第二隔室的下端处取出的沸点大于340℃、优选大于350℃、优选大于370℃的含hpna的未转化的重质液体馏分,e)将在步骤d)的蒸馏塔的所述第二隔室的下端处取出的所述沸点大于340℃、优选大于350℃、优选大于370℃的含hpna的未转化的重质液体馏分的至少一部分排出,f)对从蒸馏塔的所述第一隔室的下端处取出的来自步骤d)的沸点大于340℃、优选大于350℃、优选大于370℃的未转化的液体馏分的至少一部分和在所述第二隔室的下端处取出的来自步骤d)的沸点大于340℃、优选大于350℃、优选大于370℃的含hpna的未转化的重质液体馏分的未被排出的那部分的混合物进行的第二加氢裂化步骤,在氢气和至少第二加氢裂化催化剂的存在下、在250℃
‑
480℃的温度下、在2
‑
25mpa的压力下、在0.1
‑
6h
‑1的空速下、并且采用使得氢气的升数/烃的升数的体积之比为100
‑
2000l/l的引入的氢气量来进行所述步骤f),g)在高压下分离来自第二加氢裂化步骤f)的流出物以产生至少气态流出物和液体烃流出物的步骤,h)在低于所述隔离壁上端的高度处将来自步骤g)的所述液体烃流出物的至少一部分再循环到所述蒸馏步骤d)的由隔离壁界定的第二隔室中。
[0020]
发明详述原料本发明涉及被称为母料的烃原料的加氢裂化方法,所述烃原料包含至少20体积%、优选至少80体积%的沸点高于340℃、优选高于350℃、优选为340℃
‑
580℃的化合物(即对应于包含至少15
‑
20个碳原子的化合物)。
[0021]
所述烃原料可有利地选自vgo(减压瓦斯油)或减压馏出物(vd),例如由原油的直接蒸馏产生或由转化单元诸如fcc单元(例如lco或轻质循环油)、焦化器或减粘裂化单元产生的瓦斯油,还选自由从润滑油基础油中提取芳族化合物的单元产生或由润滑油基础油的溶剂脱蜡产生的原料,或选自由atr(常压渣油)和/或vr(减压渣油)的脱硫或加氢转化产生的馏出物,或所述原料可有利地为脱沥青油、或由生物质产生的原料或上述原料的任意混合物,优选为vgo。
[0022]
由费
‑
托方法产生的链烷烃不包括在内。
[0023]
通常,所述原料具有高于340℃、甚至更优选高于370℃的沸点t5,也就是说,所述原料中存在的95%的化合物具有高于340℃、甚至更优选高于370℃的沸点。
[0024]
在根据本发明的方法中处理的母料的氮含量通常大于500重量ppm,优选为500
‑
10000重量ppm,更优选为700
‑
4000重量ppm,并且还更优选为1000
‑
4000重量ppm。在根据本发明的方法中处理的母料的硫含量通常为0.01重量%
‑
5重量%,优选为0.2重量%
‑
4重量%,并且更优选为0.5重量%
‑
3重量%。
[0025]
所述原料可任选地包含金属。在根据本发明的方法中处理的原料的镍和钒的累积含量优选小于1重量ppm。
[0026]
沥青质含量通常小于3000重量ppm,优选小于1000重量ppm,甚至更优选小于200重量ppm。
[0027]
所述原料可任选地包含沥青质。沥青质含量通常小于3000重量ppm,优选小于1000重量ppm,甚至更优选小于200重量ppm。
[0028]
在所述原料包含树脂和/或沥青质类型的化合物的情况下,有利的是使原料预先通过不同于加氢裂化催化剂或加氢处理催化剂的催化剂床或吸附剂床。
[0029]
步骤a)根据本发明,所述方法包括在氢气和至少一种加氢处理催化剂的存在下、在200℃
‑
450℃的温度下、在2
‑
18mpa的压力下、在0.1
‑
6h
‑1的空速下、并且采用使得氢气的升数/烃的升数的体积之比为100
‑
2000l/l的引入的氢气量来将所述原料加氢处理的步骤a)。
[0030]
根据所述原料的性质、所需的产物品质以及精炼厂可支配的设备,操作条件诸如温度、压力、氢气的再循环程度或时空速可以广泛地变化。
[0031]
优选地,根据本发明的加氢处理步骤a)在250℃
‑
450℃、非常优选在300℃
‑
430℃的温度下、在5
‑
16mpa的压力下、在0.2
‑
5h
‑1的空速下、并且采用使得氢气的升数/烃的升数的体积之比为300
‑
1500l/l的引入的氢气量来进行。
[0032]
可以有利地使用常规的加氢处理催化剂,其优选包含至少一种无定形载体和至少一种选自至少一种来自第vib族和第viii族的非贵金属元素、并且通常选自至少一种来自第vib族的元素和至少一种来自第viii族的非贵金属元素的加氢
‑
脱氢元素。
[0033]
优选地,所述无定形载体是氧化铝或二氧化硅/氧化铝。
[0034]
优选的催化剂选自:负载于氧化铝上的nimo、niw或como催化剂以及负载于二氧化硅
‑
氧化铝上的nimo或niw催化剂。
[0035]
来自加氢处理步骤并进入加氢裂化步骤b)的流出物通常具有优选小于300重量ppm、优选小于50重量ppm的氮含量。
[0036]
步骤b)根据本发明,所述方法包括将来自步骤a)的流出物的至少一部分、优选其全部加氢裂化的步骤b),所述步骤b)在氢气和至少一种加氢裂化催化剂的存在下、在250℃
‑
480℃的温度下、在2
‑
25mpa的压力下、在0.1
‑
6h
‑1的空速下、并且采用使得氢气的升数/烃的升数的体积之比为100
‑
2000l/l的引入的氢气量来进行。
[0037]
优选地,根据本发明的加氢裂化步骤b)在320℃
‑
450℃,非常优选330℃
‑
435℃的温度下、在3
‑
20mpa的压力下、在0.2
‑
4h
‑1的空速下、并且采用使得氢气的升数/烃的升数的体积之比为200
‑
2000l/l的引入的氢气量来进行。
[0038]
在一个可以使中间馏出物的产量最大化的实施方案中,根据本发明的方法中使用的操作条件通常可以获得大于15重量%、更优选为20重量%
‑
95重量%的转化为沸点低于340℃、优选低于370℃的产物的单程转化率。
[0039]
在一个可以使石脑油的产量最大化的实施方案中,根据本发明的方法中使用的操作条件通常可以获得大于15重量%、更优选为20重量%
‑
95重量%的转化为沸点低于190℃、优选低于175℃的产物的单程转化率。
[0040]
根据本发明的加氢裂化方法涵盖从温和的加氢裂化延伸到高压加氢裂化的压力和转化率范围。术语“温和的加氢裂化”是指产生适中的转化率(通常小于40%)、并且在低压、优选2mpa
‑
6mpa下进行的加氢裂化。高压加氢裂化通常在5mpa
‑
20mpa的更大的压力下进行,从而获得大于50%的转化率。
[0041]
无论所述方法在哪一种压力下实施,根据本发明的加氢裂化方法都在两个步骤中进行。其在一种或多种加氢裂化催化剂的存在下、在一个或多个配备有一个或多个固定床或沸腾床反应器的反应单元中进行,所述反应器可能用一个或多个高压分离段和/或低压分离段隔开。
[0042]
加氢处理步骤a)和加氢裂化步骤b)可以有利地在相同反应器中或在不同反应器中进行。当它们在相同反应器中进行时,所述反应器包括若干个催化床,即包含一种或多种加氢处理催化剂的第一催化床和随后的包含一种或多种加氢裂化催化剂的催化床。
[0043]
加氢裂化步骤b)的催化剂加氢裂化步骤b)中使用的加氢裂化催化剂是常规的双功能类型的加氢裂化催化剂,其将酸功能物质(function)与氢化功能物质以及任选的至少一种粘合剂基质组合在一起。
[0044]
优选地,所述一种或多种加氢裂化催化剂包含至少一种来自第viii族的金属,其选自铁、钴、镍、钌、铑、钯和铂,并且优选选自钴和镍,和/或至少一种来自第vib族的金属,其选自铬、钼和钨,单独地或作为混合物使用,并且优选选自钼和钨。
[0045]
优选nimo、nimow、niw型的氢化功能物质。
[0046]
优选地,所述一种或多种加氢裂化催化剂中的来自第viii族的金属含量有利地为0.5重量%
‑
15重量%,优选2重量%
‑
10重量%,该百分数以氧化物的重量百分数表示。
[0047]
优选地,所述一种或多种加氢裂化催化剂中的来自第vib族的金属含量有利地为5重量%
‑
25重量%,优选15重量%
‑
22重量%,该百分数以氧化物的重量百分数表示。
[0048]
所述一种或多种催化剂还可以任选地包含至少一种沉积在催化剂上并且选自磷、硼和硅的助催化剂元素、任选地至少一种来自第viia族的元素(优选氯、氟)和任选地至少一种来自第viib族的元素(优选锰)、任选地至少一种来自第vb族的元素(优选铌)。
[0049]
优选地,所述一种或多种加氢裂化催化剂包含选自usy沸石的沸石,所述沸石单独地或与选自β沸石、zsm
‑
12沸石、izm
‑
2沸石、zsm
‑
22沸石、zsm
‑
23沸石、sapo
‑
11沸石、zsm
‑ꢀ
48沸石和zbm
‑
30沸石(单独地或作为混合物)的其他沸石组合使用。优选地,所述沸石是单独的usy沸石。
[0050]
所述一种或多种加氢裂化催化剂可任选包含至少一种氧化物类型的多孔或不良结晶的矿物基质,其选自氧化铝、二氧化硅、二氧化硅
‑
氧化铝、铝酸盐、氧化铝
‑
氧化硼、氧化镁、二氧化硅
‑
氧化镁、氧化锆、氧化钛、粘土,单独地或作为混合物使用,优选为氧化铝。
[0051]
优选的催化剂包含至少一种来自第vi族的金属和/或至少一种来自第viii族的非贵金属、沸石y和氧化铝粘合剂、并优选由其组成。
[0052]
甚至更优选的催化剂包含镍、钼、磷、y沸石和氧化铝,并优选由其组成。
[0053]
另一种优选的催化剂包含镍、钨、y沸石和氧化铝或二氧化硅
‑
氧化铝,并优选由其组成。
[0054]
通常,加氢裂化步骤b)中使用的一种或多种催化剂有利地包含:
‑ꢀ
0.1
‑
60重量%的沸石,
‑ꢀ
0.1
‑
40重量%的至少一种第vib族和第viii族的元素(以氧化物%表示)
‑ꢀ
0.1
‑
99.8重量%的基质(以氧化物%表示)
‑ꢀ0‑
20重量%、优选0.1
‑
20重量%的至少一种选自p、b、si的元素(以氧化物%表示),
‑ꢀ0‑
20重量%、优选0.1
‑
20重量%的至少一种第viia族的元素,
‑ꢀ0‑
20重量%、优选0.1
‑
20重量%的至少一种第viib族的元素,
‑ꢀ0‑
60重量%、优选0.1
‑
60重量%的至少一种第vb族的元素;百分数表示为相对于催化剂总重量的重量百分数,所述催化剂的构成元素的百分数之和等于100%。
[0055]
步骤c)根据本发明,所述方法包括高压分离步骤c),步骤c)包括分离装置,例如在2
‑
25mpa的高压下运行的一系列分离器(disengager),步骤c)的目的是产生借助压缩机被再循环至步骤a)、步骤b)和/或步骤e)中的至少一个的氢气物流以及在加氢裂化步骤b)中产生的烃流出物,该烃流出物被优选送至优选在0.5
‑
2mpa的压力下运行的蒸汽汽提步骤,蒸汽汽提步骤的目的是从至少在步骤b)中产生的所述烃流出物中分离出溶解的硫化氢(h2s)。
[0056]
步骤c)可以产生液体烃流出物,然后将所述液体烃流出物送至蒸馏步骤d)。
[0057]
步骤d)根据本发明,所述方法包括将来自步骤c)的液体烃流出物蒸馏的步骤d)。
[0058]
根据本发明,所述蒸馏步骤d)在至少一个蒸馏塔中进行,所述蒸馏塔在其底部包
括垂直隔离壁,所述垂直隔离壁将所述塔的底部分隔成两个独立的隔室,即第一隔室和第二隔室,并优选在至少所述塔的下部三分之二处、优选在至少所述塔的三分之一处。
[0059]
所述蒸馏塔在0.1
‑
0.4mpa的绝对压力下运行。
[0060]
因此,界定出两个独立的隔室的所述隔离壁位于所述塔的下端。
[0061]
不含隔离壁的塔的上部称为顶部隔室。
[0062]
根据本发明,将在步骤c)中分离且由第一加氢裂化步骤b)产生的液体烃流出物在低于或等于所述隔离壁的上端的高度处引入第一隔室中。
[0063]
所述第一隔室可有利地包括8
‑
25个、有利地为12
‑
20个理论塔板。所述第二隔室可有利地包括8
‑
25个、有利地为12
‑
20个理论塔板。
[0064]
将在步骤c)中分离且由第一加氢裂化步骤b)产生的液体烃流出物进料到位于所述第一隔室的上半部的塔板处。因此,例如,如果第一隔室包括14个理论塔板,则将所述流出物进料到第1块塔板和第7块塔板之间,沿液体的流动方向对塔板进行编号。
[0065]
根据本发明,所述蒸馏塔在垂直隔离壁的任一侧上一方面进料有来自第一加氢裂化步骤b)、经由分离步骤c)产生的液体烃流出物,另一方面进料有来自第二加氢裂化步骤f) 、经由分离步骤g)产生的液体烃流出物,从而在由所述隔离壁界定的所述塔的特定隔室(第二隔室)中实现来自第二加氢裂化步骤f)的流出物中所含的hpna的浓缩,并因此避免了所述hpna被来自第一加氢裂化步骤b)并在步骤c)中分离的液体烃流出物稀释。
[0066]
所述蒸馏步骤d)可以取出:
‑
任选的气态馏分,和任选的至少一种沸点低于150℃的汽油馏分,
‑
沸点为150℃
‑
370℃、优选150℃
‑
350℃、优选150℃
‑
340℃的中间馏出物馏分,优选单一的中间馏出物馏分,
‑
在所述第一隔室的下端处取出的沸点大于340℃、优选大于350℃、优选大于370℃的在步骤a)和步骤b)中未转化的液体馏分,和
‑
含hpna并且沸点大于340℃、优选大于350℃、优选大于370℃的在第二加氢裂化步骤e)中未转化的重质液体馏分,所述馏分在所述第二隔室的下端处取出。
[0067]
被集成在单个常压蒸馏塔中并位于所述塔的下端的两个独立的隔室一方面可以分离来自步骤a)和步骤b)的未转化的液体馏分,另一方面,可以分离来自步骤f)的未转化的液体馏分。所述壁的存在可以避免这两种未转化的馏分的混合,因此可以避免在第二加氢裂化步骤f)中未转化的所述重质液体馏分中所含的hpna被来自步骤c)的液体烃流出物(对应于来自第一加氢裂化步骤b)的液体烃流出物)稀释。
[0068]
步骤e)根据本发明,所述方法包括排出在步骤d)的蒸馏塔的所述第二隔室下端的高度处取出的含hpna的在第二加氢裂化步骤f)中未转化的所述重质液体馏分的至少一部分的步骤e)。
[0069]
排出物物流主要由来自第二加氢裂化步骤f)、经由分离步骤g)产生的产物组成,并且不被来自第一加氢裂化步骤b)的分子稀释。排出的目的是提取与在方法中(尤其是在步骤f中)形成的hpna一样多的hpna。本发明可以不稀释hpna,并因此在相同的排出的hpna分流量(和因此相同的形成的hpna分流量)下,从所述方法中排出较少量的目标产物。
[0070]
所述方法的实施还可以在相同的总方法转化率下增加第二加氢裂化步骤的循环
时间。
[0071]
步骤f)根据本发明,所述方法包括对在步骤d)的蒸馏塔的所述第一隔室的下端处取出的沸点大于340℃、优选大于350℃、优选大于370℃的在步骤a)和步骤b)中未转化的液体馏分的至少一部分、优选全部和在步骤d)的蒸馏塔的所述第二隔室的下端处取出的沸点大于340℃、优选大于350℃、优选大于370℃的含hpna的在步骤e)中未转化的重质液体馏分的未被排出的那部分的混合物进行的第二加氢裂化步骤f)。
[0072]
优选地,步骤f)的原料仅由沸点大于340℃的在步骤a)和步骤b)中未转化的液体馏分的一部分、优选全部和沸点大于340℃的含hpna的在步骤e)中未转化的重质液体馏分的未被排出的那部分组成。
[0073]
优选地,不将蒸馏步骤d)中取出的中间馏出物馏分再循环到加氢裂化步骤f)中。
[0074]
根据本发明,所述步骤f)在氢气和至少第二加氢裂化催化剂的存在下、在250
‑
480℃的温度下、在2
‑
25mpa的压力下、在0.1
‑
6h
‑1的空速下、并且采用使得氢气的升数/烃的升数的体积之比为100
‑
2000l/l的引入的氢气量来进行。
[0075]
再循环比定义为进入步骤f)的原料物流与进入所述方法(步骤a)中)的烃原料的重量比,其为0.2
‑
4,优选0.5
‑
2。
[0076]
优选地,根据本发明的加氢裂化步骤f)在320℃
‑
450℃、非常优选330℃
‑
435℃的温度下、在3
‑
20mpa、非常优选在9
‑
20mpa的压力下、在0.2
‑
3h
‑1的空速下、并且采用使得氢气的升数/烃的升数的体积之比为100
‑
2000l/l的引入的氢气量来进行。
[0077]
在可以使中间馏出物的产量最大化的实施方案中,在根据本发明的方法的步骤f)中使用的这些操作条件通常可以获得大于15重量%、更优选为20重量%
‑
80重量%的转化为沸点低于380℃、优选低于370℃、优选低于340℃的产物的单程转化率。然而,步骤f)中的单程转化率通常为10
‑
80重量%,优选为20
‑
70重量%,优选为30
‑
60重量%,从而使得所述方法对沸点为150
‑
370℃的产物(中间馏出物)的选择性最大化。单程转化率受到在第二加氢裂化步骤f)的环路上使用高再循环比限制。该再循环比定义为步骤f)的进料流量与步骤a)的原料流量之比;优选地,该再循环比为0.2
‑
4,优选0.5
‑
2。
[0078]
在可以使石脑油的产量最大化的实施方案中,在根据本发明的方法的步骤f)中使用的这些操作条件通常可以获得大于15重量%、更优选为20重量%
‑
80重量%的转化为沸点低于190℃、优选低于175℃、优选低于150℃的产物的单程转化率。然而,步骤f)中的单程转化率保持较低,从而使所述方法对于沸点为80℃
‑
190℃的产物(石脑油)的选择性最大化。单程转化率受到在第二加氢裂化步骤f)的环路上使用高再循环比限制。该再循环比定义为步骤f)的进料流量与步骤a)的原料流量之比;优选地,该再循环比为0.2
‑
4,优选0.5
‑
2。
[0079]
根据本发明,加氢裂化步骤f)在至少一种加氢裂化催化剂的存在下进行。优选地,第二步骤加氢裂化催化剂选自本领域技术人员已知的常规加氢裂化催化剂。在所述步骤f)中使用的加氢裂化催化剂可以与在步骤b)中使用的加氢裂化催化剂相同或不同,并且优选不同。
[0080]
加氢裂化过程中使用的加氢裂化催化剂都是双功能类型的,其将酸功能物质与氢化功能物质组合在一起。酸功能物质由具有大表面积(通常为150
‑
800m2·
g
‑1)的具有表面
酸性的载体提供,例如卤化(尤其是氯化或氟化)氧化铝、氧化硼和氧化铝的组合、无定形二氧化硅/氧化铝和沸石。氢化功能物质由一种或多种来自元素周期表第viii族的金属或至少一种来自元素周期表第vib族的金属和至少一种来自第viii族的金属的组合提供。
[0081]
优选地,步骤f)中使用的一种或多种加氢裂化催化剂包括氢化功能物质,所述氢化功能物质包含至少一种来自第viii族的金属,其选自铁、钴、镍、钌、铑、钯和铂,优选选自钴和镍,和/或至少一种来自第vib族的金属,其选自铬、钼和钨,单独地或作为混合物使用,优选选自钼和钨。
[0082]
优选地,一种或多种加氢裂化催化剂中的来自viii族的金属含量有利地为0.5重量%
‑
15重量%,优选2重量%
‑
10重量%,该百分数以氧化物的重量百分数表示。
[0083]
优选地,一种或多种加氢裂化催化剂中的来自第vib族的金属含量有利地为5重量%
‑
25重量%,优选15重量%
‑
22重量%,该百分数以氧化物的重量百分数表示。
[0084]
步骤e)中使用的一种或多种催化剂还可以任选地包含至少一种沉积在催化剂上并且选自磷、硼和硅的助催化剂元素、任选地至少一种来自第viia族的元素(优选氯、氟)和任选地至少一种来自第viib族的元素(优选锰)、任选地至少一种来自第vb族的元素(优选铌)。
[0085]
优选地,步骤e)中使用的一种或多种加氢裂化催化剂包含选自氧化铝、二氧化硅/氧化铝和沸石(优选选自沸石y),并且优选选自二氧化硅/氧化铝和沸石的酸功能物质。
[0086]
步骤e)中使用的优选的催化剂包含至少一种来自第vi族的金属和/或至少一种来自第viii族的非贵金属、沸石y和氧化铝,并优选由其组成。
[0087]
甚至更优选的催化剂包含镍、钼、y沸石和氧化铝,并优选由其组成。
[0088]
另一种优选的催化剂包含镍、钨和氧化铝或二氧化硅
‑
氧化铝,并优选由其组成。
[0089]
步骤g)根据本发明,所述方法包括来自第二加氢裂化步骤f)的流出物的高压分离步骤g),所述步骤包括分离装置,例如在2
‑
25mpa的高压下运行的一系列分离器,步骤g)的目的是产生借助压缩机被再循环至步骤a)、步骤b)和/或步骤f)中的至少一个的氢气物流以及在加氢裂化步骤f)中产生的烃流出物,该烃流出物可被任选送至优选在0.5
‑
2mpa的压力下运行的蒸汽汽提步骤,蒸汽汽提步骤的目的是从至少在步骤f)中产生的所述烃流出物中分离出溶解的硫化氢(h2s)。
[0090]
步骤g)还可以产生液体烃流出物,然后将所述液体烃流出物的全部或一部分送至步骤d)的蒸馏塔,特别是送至步骤d)的第二隔室。
[0091]
步骤h)根据本发明,所述方法包括在低于所述隔离壁的上端的高度处将来自步骤g)的所述液体烃流出物的至少一部分、优选全部再循环到所述蒸馏步骤d)的由隔离壁界定的第二隔室。
附图说明
[0092]
将vd原料经由管线1引入加氢处理步骤a)。将来自步骤a)的流出物经由管线2送至第一加氢裂化步骤b)。将来自步骤b)的流出物经由管线3送至对来自加氢裂化步骤b)的流出物进行高压分离的步骤c),从而产生至少一种气态流出物(图中未示出)和液体烃流出物
4,将液体烃流出物4送至在至少一个蒸馏塔中进行的蒸馏步骤d),所述蒸馏塔在其底部包括垂直隔离壁(d1),所述隔离壁将所述塔的下部分隔成两个独立的隔室(d')和(d''),在等于所述隔离壁上端的高度处将所述流出物引入第一隔室(d')。
[0093]
所述蒸馏步骤可以取出:
‑
气态馏分5,
‑
在设置排放过程以使石脑油的产量最大化的情况下,经由管线6取出沸点低于150℃、优选低于175℃的汽油馏分,
‑
经由管线7取出沸点为150℃
‑
370℃、优选150℃
‑
350℃、优选150℃
‑
340℃的中间馏出物馏分,
‑
在第一隔室(d')下端的高度处经由管线8取出沸点大于340℃的未转化的液体馏分,和
‑
在由所述间隔壁界定的第二隔室(d'')下端的高度处经由管线12取出沸点大于340℃的含hpna的未转化的重质液体馏分。
[0094]
在步骤d)的蒸馏塔的所述第二隔室(d'')的下端处经由管线13取出沸点大于340℃的含hpna的所述未转化的重质液体馏分的一部分来将其排出。
[0095]
将在蒸馏塔的所述第一隔室(d')下端的高度处取出的来自步骤d)的沸点大于340℃的未转化的液体馏分的全部与在所述第二隔室(d'')下端的高度处取出的来自步骤d)的沸点大于340℃的含hpna的未转化的重质液体馏分的未被排出的那部分的混合物经由管线9送至第二加氢裂化步骤f)。
[0096]
将来自第二加氢裂化步骤f)的流出物经由管线10送至高压分离步骤g),从而产生至少一种气态流出物(未在图1中示出)和经由管线11的液体烃流出物。
[0097]
然后将所述液体烃流出物经由管线11在低于所述隔离壁的上端的高度处再循环到所述蒸馏步骤d)的由隔离壁界定的第二隔室(d”)。
[0098]
实施例
‑
瓦斯油最大化模式实施例1:不根据本发明加氢裂化单元处理表1中所述的减压瓦斯油(vgo)原料:
[0099]
将vgo原料注入预热步骤中,然后注入在表2中列出的下列条件下的加氢处理反应
器中:
[0100]
所使用的催化剂是负载于氧化铝上的como催化剂。
[0101]
随后将来自该反应器的流出物与氢气物流混合以进行冷却,然后注入在表3的条件下运行的第二“加氢裂化”反应器r2中:
[0102]
所使用的催化剂是负载于沸石上的金属催化剂。
[0103]
r1和r2构成了第一加氢裂化步骤,来自r2的流出物随后被送至由回收热量、然后进行高压分离的队列(包括再循环压缩机)组成的分离步骤,其一方面可以分离出氢气、硫化氢和氨,另一方面分离出液体烃流出物,将所述液体烃流出物进料至汽提器、然后进料至常压蒸馏塔,从而分离出其中相对于h2s,石脑油、煤油、瓦斯油被浓缩至所需规格的物流;和未转化的重质液体流出物。常压蒸馏塔的下部未设置垂直隔离壁。将所述未转化的重质液体流出物注入构成第二加氢裂化步骤的加氢裂化反应器r3中。该反应器r3在表4中列出的下列条件下使用:
[0104]
所使用的催化剂是负载于无定形二氧化硅/氧化铝上的金属催化剂。
[0105]
随后将来自r3的流出物注入第一加氢裂化步骤下游的高压分离步骤中。反应器r3的入口处的重量流量等于vgo原料的重量流量;在蒸馏塔底部对未转化的油物流进行相当于vgo原料流量的2重量%的排出。
[0106]
加氢裂化器中产生并从蒸馏塔中回收的馏出物馏分符合欧v规范;特别地,其具有小于10重量ppm的硫。
[0107]
再循环环路中的hpna浓度为1000重量ppm。
[0108]
对于沸点大于380℃的烃的98重量%的总转化率,该方法的中间馏出物的收率为85重量%。
[0109]
实施例2:根据本发明实施例2涉及在与实施例1相同的条件和相同的原料下进行的两步加氢裂化方法,不同之处在于,实施例2的蒸馏塔在其底部包括垂直隔离壁和在所述塔的进料注入处的上方和向下直至塔的底部的两个实际的塔板,所述隔离壁将所述塔分隔成两个独立的隔室。在实施例2中,常压蒸馏塔的底部被分隔成两个隔室,其一方面处理来自r2的液体烃流出物,另一方面处理来自r3的液体烃流出物。
[0110]
在实施例2中,将经汽提的液体烃流出物进料至所述常压蒸馏塔的第一隔室。所述隔室实现了在r1和r2中进行的加氢处理步骤和加氢裂化步骤中未转化的沸点为340℃的液体馏分的分离。
[0111]
将该馏分在所述第一隔室下端的高度处取出,并与在r3中未转化且沸点为340℃的液体馏分的未被排出的那部分混合送入构成第二加氢裂化步骤的加氢裂化反应器r3中。
[0112]
将来自r3并经高压分离之后的液体烃流出物再循环到常压蒸馏塔的第二隔室中。
[0113]
所述第二隔室实现了在r3中进行的加氢裂化步骤中未转化的沸点为340℃的液体馏分的分离。
[0114]
所述未转化的液体馏分包含hpna。
[0115]
在实施例2中,排出物相当于vgo原料流量的1重量%。由于排出物流量降低了一半,因此再循环环路中的hpna浓度保持与实施例1中相同。因此,再循环环路中的hpna浓度为1000重量ppm。
[0116]
因此,在两个实施例中,催化循环时间相同。对于沸点大于380℃的烃的99重量%的总转化率,该方法的中间馏出物的收率为86重量%。