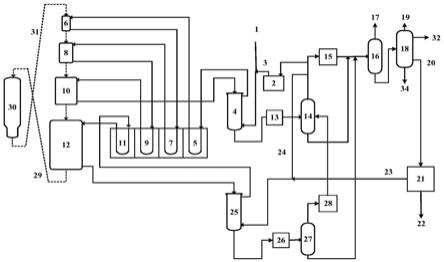
1.本发明为一种石脑油催化重整方法,具体地说,是一种有两个反应区的石 脑油催化重整方法。
背景技术:2.催化重整工艺是一种重要的生产芳烃或高辛烷值汽油组分以及氢气的炼 油工艺。催化重整过程中发生的反应包括烷基环己烷脱氢、烷基环戊烷脱氢异 构化、链烷烃脱氢环化、链烷烃氢解和加氢裂解、链烷烃异构化、烷基苯脱烷 基以及催化剂上的生焦反应。为了尽可能多地得到芳烃和高辛烷值汽油组分, 除了使易反应的环烷烃转化成芳烃外,还要使难反应的链烷烃尽可能地转化为 芳烃,同时减少裂化,降低催化剂积炭。对于催化重整工艺,同时提高芳烃产 率和c
5+
收率,降低反应压力是有效的工艺措施,而提高反应温度、降低空速 虽然能提高芳烃产率,却增加了烷烃裂解反应,降低了c
5+
收率。
3.与半再生重整工艺相比,连续重整工艺具有更高的反应苛刻度,反应压力 和氢/油比较低,从而具有更高的芳烃产率。20世纪70年代初开发的第一代连 续重整工艺的平均反应压力是0.98mpa,80年代末开发的第二代连续重整工艺 的平均反应压力降低到0.45mpa。此后连续重整工艺的平均反应压力保持 0.45mpa,未继续降低。
4.继续大幅度降低反应压力,在工程中是不现实的,需要进一步降低各加热 炉、反应器、换热器以及管线的压降;另外需要提高氢气循环量,以抑制催化 剂积炭速率的增加,否则需要增大催化剂的再生处理能力。
5.cn101921616b公开了一种多产芳烃的半再生重整系统及其方法,精制石 脑油经加热后进入第1反应器,而后再经加热进入第2反应器,从第2反应器 排出的反应产物经冷凝后进入高压分离器进行气液分离,再进入稳定塔,在塔 顶采出干气、液化气和少量水,塔底得到的重整生成油(馏程为35~196℃)去 芳烃抽提系统,抽余油脱水后再经加热进入第3反应器,而后经加热进入第4 反应器,第4反应器产物再进入高压分离器,与第1反应器和第2反应器产物 共用一个高压分离器。该组合工艺利用芳烃抽提技术将重整前两个反应器的产 物进行分离,将难反应的链烷烃分离出来,再用第3反应器和第4反应器去转 化,有利于提高芳烃产率,但两个反应区需在相同压力下进行反应。
6.cn104711016a公开了一种连续催化重整方法,将石脑油送往第一催化重 整单元,将至少一部分链烷烃和/或环烷烃转化成芳族化合物和氢气;从第一催 化重整单元取出第一流出物,并送往芳烃分离单元,分离出芳族馏分和含有未 转化的环烷烃和/或链烷烃的萃余液;将萃余液送往第二催化重整单元转化成芳 族化合物和氢气。第一和第二催化重整单元的反应压力相同,为0.3mpa~1mpa, 平均反应器入口温度为420~600℃。该组合工艺利用芳烃抽提技术将产物进行 分离,将第一催化重整单元难反应的链烷烃和/或环烷烃分离出来,送到第二催 化重整单元反应,有利于提高芳烃产率和降低催化剂积炭速率。
7.cn103374395b公开了一种以石脑油为原料生产芳烃和乙烯的方法,将石 脑油在压力0.15~3.0mpa、温度300~540℃,体积空速2.1~50h-1
的临氢条件下 与重整催化剂接
触进行浅度催化重整反应,使石脑油中的环烷烃转化率大于85 质量%,链烷烃转化为芳烃和c
4-烃的转化率小于30质量%。将催化重整得到 的重整生成油送入芳烃分离装置分离芳烃与链烷烃,得到富含芳烃的馏分和富 含链烷烃的馏分。将富含链烷烃的馏分送入蒸汽裂解装置进行裂解反应生成乙 烯。
8.us5683573公开了一种有两个反应分区的连续重整工艺,第一个分区使用 连续重整双功能催化剂,第二个分区使用非酸性分子筛催化剂,如含铂非酸性 l分子筛催化剂,油气顺序通过两个反应区。该工艺可提高反应苛刻度,增加 处理量及芳烃产率,能够用于现有连续催化重整装置的升级改造。由于含铂非 酸性l分子筛催化剂对原料组成及其杂质含量要求极高,大大高于连续重整催 化剂对此的要求,因此将两者简单组合在一起,将难以实现工业化。
技术实现要素:9.本发明的目的是提供一种石脑油催化重整方法,该法将连续重整装置分成 两个独立的反应区,控制不同的反应条件,以石脑油为原料可以生产更多的芳 烃。
10.本发明提供的石脑油催化重整方法,包括将连续重整装置的反应器分成第 一反应区和第二反应区,将石脑油送入第一反应区,在0.3~0.8mpa、460~520℃、 进料液时体积空速2~6h-1
的条件下与重整催化剂接触反应,得到的第一反应产 物进入第一气液分离系统进行气液分离;将石脑油重整产物中的c7~c8非芳烃 组分送入第二反应区,在0.14~0.28mpa、480~530℃、进料液时体积空速 0.5~1.8h-1
的条件下与重整催化剂接触反应,得到的第二反应产物进入第二气液 分离系统进行气液分离。
11.本发明方法在连续重整方法的基础上,将其反应器分成两个不同压力的反 应区,使石脑油在较高压力的第一反应区进行重整反应,石脑油重整产物中的 c7~c8非芳烃组分再在较低压力的第二反应区进行反应生成芳烃。所述方法可 提高石脑油重整反应的芳烃产率、液体收率及氢气产率。
附图说明
12.图1为现有连续重整方法流程示意图,使用重叠式反应器,反应器间催化 剂流动方向与反应物流动方向相同。
13.图2为本发明连续重整方法流程示意图,使用重叠式反应器,反应器间催 化剂流动方向与反应物流动方向相同。
具体实施方式
14.本发明方法将连续重整装置的反应器分成两个独立的反应区,两个反应区 的原料不同,反应产物互不相通,各自进入所属反应区的气液分离系统。石脑 油进入第一反应区进行重整反应,石脑油重整产物中的c7~c8非芳烃组分进入 第二反应区进行反应,在催化剂作用和较低压力下使所述c7~c8非芳烃组分更 多地转化为芳烃。所述方法可有效提高石脑油连续重整产物中的液体收率、芳 烃产率,并增加氢气产率。
15.本发明方法所述的重整催化剂包括氧化铝载体和以载体为基准计算的含 量为0.1~3质量%的铂、0.1~3质量%的锡和0.5~3质量%的氯。所述的氧化铝 优选γ-氧化
铝。所述的铂含量优选0.1~1质量%、锡含量优选0.1~1质量%,氯 含量优选0.5~2质量%。氧化铝形状优选为球形。
16.本发明所述的连续重整装置优选移动床连续重整装置,含有反应系统和催 化剂再生系统,反应系统包括依次串连的反应器,重整催化剂在移动床连续重 整装置第一反应区的反应器和第二反应区的反应器中连续移动。再生系统包括 催化剂再生器。反应时,反应原料进入反应器,反应器中催化剂在反应器中连 续缓慢移动,直至从流向最后一个反应器流出,流出的待再生催化剂进入催化 剂再生器进行再生,再生催化剂重新返回反应器。催化剂再生按常规移动床催 化重整的催化剂再生方法进行。
17.连续重整催化剂可以不同方式进入反应器,反应器间催化剂的流动方向与 反应物流的流动方向相同的为顺流,相反的为逆流,错流指催化剂首先进入第 一个反应器,再依次进入最末一个反应器、倒数第二个反应器、倒数第三个反 应器,或按其它与顺流或逆流不同的顺序进入反应器。
18.本发明中,第二反应区中的催化剂与连续重整装置中催化剂总量的体积比 优选为30~60%、更优选40~55%。
19.本发明所述的第一反应区和第二反应区的反应相互独立,第二反应区原料 不是第一反应区的产物,而是石脑油重整产物中的c7~c8非芳烃组分,且两个 反应区产物的气液分离也彼此独立设置。
20.本发明所述的第一反应区基本保持常规的连续重整条件,但催化剂装量相 对减少,主要进行环烷烃脱氢、环烷烃脱氢异构生成芳烃,以及部分烷烃的芳 构化反应。第一反应区优选包含2~4个串连的反应器,优选地,每个反应器前 设加热炉。
21.第二反应区的反应原料为石脑油重整产物中的c7~c8非芳烃组分,一般为 芳烃抽余油。所述的c7~c8非芳烃组分可为所述的连续重整装置的反应产物经 气液分离所得液相中的c7~c8烃组分经芳烃抽提得到的抽余油,也可为所述的 连续重整装置的反应产物经气液分离所得液相中的c7~c8烃组分经芳烃抽提得 到的抽余油掺入外加的c7~c8非芳烃组分。所述c7~c8非芳烃组分中可含有少 量c9非芳烃和芳烃,优选地,所述c7~c8非芳烃组分中含85.5~100质量%的 c7~c8非芳烃、0~12.5质量%的c9非芳烃,0~2质量%的芳烃。所述的非芳烃 为烷烃和环烷烃,其中烷烃含量为85~95质量%,环烷烃含量为5~15质量%。
22.第二反应区主要进行烷烃的脱氢环化反应,其它反应包括烷烃的加氢裂化 和异构化反应。所述外加的c7~c8非芳烃组分可来自其它工艺产生的芳烃抽提 所得的c7~c8非芳烃组分,如芳烃联合装置产生的c7~c8芳烃抽余油。
23.第二反应区优选包含1个或2~4个并联的反应器,优选地,每个反应器前 设加热炉。第二反应区的压力较第一反应区低,优选为0.16~0.25mpa。
24.所述第一反应区的温度为平均床层温度,其值优选480~510℃,反应压力 优选0.4~0.7mpa,氢/烃摩尔比优选1~6、更优选1.5~4。进料液时体积空速优 选3~5h-1
。
25.所述第二反应区的温度亦为平均床层温度,其值可略高于第一反应区的温 度,优选为482~520℃,反应压力优选0.16~0.25mpa,氢/烃摩尔比优选2~10、 更优选3~8,进料液时体积空速优选0.8~1.5h-1
。
26.本发明所述方法中的压力均为绝对压力。
27.本发明方法中,所述第二反应产物进入第二气液分离系统进行气液分离, 将所得
气相经过增压后送入第一气液分离系统,将所得液相与第一气液分离系 统分离所得的液相合并。
28.优选地,第一气液分离系统气液分离得到的气相的一部分分成两路分别返 回第一反应区和第二反应区,另一部分经增压后与气液分离得到的液相合并进 入再接触系统,所述的液相也可包括第二反应产物经气液分离所得的液相。在 再接触系统中,气液分离所得的气相经增压后与液相接触,在增压条件下,气 液分离所得的气相中的c3~c4烃组分(液化气)进入液相,分出的富氢气体(氢 气含量至少为90体积%,其余为c1~c2烃)排出,液相进入分馏系统,经过分 馏得到液化气、c5~c6烃组分、c7~c8烃组分和c
9+
烃组分,将c7~c8烃组分进 行芳烃抽提得到抽余油。
29.所述的分馏系统优选包括依次串连的脱丁烷塔、脱己烷塔和重整生成油分 馏塔。
30.优选地,所述再接触系统分出的液相先进入分馏系统中的脱丁烷塔,塔顶 得到液化气,塔底得到的c
5+
烃组分再进入脱己烷塔,塔顶得到c5~c6烃组分, 塔底得到的c
7+
烃组分,将c
7+
烃组分进入重整生成油分馏塔,塔顶得到c7~c8烃组分,塔底得到c
9+
烃组分。上述c
9+
馏分可送入芳烃联合装置分离出芳烃, 也可作为汽油烃组分。所述脱己烷塔塔顶得到的c5~c6组分可以用脱戊烷塔进 一步分离c5和c6烃组分,脱戊烷塔塔顶得到c5烃组分,塔底得到c6烃组分。
31.所述的重整生成油分馏塔塔顶得到c7~c8烃组分送入芳烃抽提装置,优选 经液液萃取得到混合芳烃和c7~c8非芳烃组分。所述芳烃抽提装置进行液液萃 取分离芳烃的操作温度优选100~150℃,压力0.6~1.0mpa,溶剂与原料质量比 为3.0~8.0,回流比优选0.5~1.0,所用溶剂优选为环丁砜、n-甲酰基吗啉和四 甘醇中的一种或几种。
32.本发明所述第一气液分离系统和第二气液分离系统均包括气液分离罐,气 液分离罐前设置冷却器,气液分离罐顶部管线与增压器连接。
33.所述的再接触系统包括冷却器和再接触罐。再接触系统的操作压力优选 1.0~3.0mpa,温度优选0~4℃。
34.所述第一气液分离系统的气液分离罐压力优选0.3~0.5mpa、温度优选 15~45℃;第二气液分离系统气液分离罐的压力优选0.12~0.20mpa、温度优选 15~45℃,其顶部排出的气相需增压后送至第一气液分离系统的气液分离罐。
35.本发明进入第二反应区的c7~c8非芳烃组分为进入第一反应区的石脑油的 10~60质量%、优选15~38质量%。
36.本发明方法所述的石脑油选自直馏石脑油、加氢裂化石脑油、焦化石脑油、 催化裂化石脑油或油田凝析油。
37.以下结合附图进一步说明本发明。
38.图1为现有常规移动床连续重整方法流程示意图,由管线1进入的精制石 脑油与来自循环压缩机2的循环管线3的氢气混合进入换热器4,与从反应器 12排出的反应产物换热,然后依次进入加热炉5、反应器6、加热炉7、反应器 8、加热炉9、反应器10、加热炉11、反应器12。在进入反应器前经加热炉加 热到所需温度,反应器12底部排出的反应产物经过换热器4与反应原料换热后 进入冷却器13冷却,再进入第一气液分离罐14。第一气液分离罐14顶部排出 的气相分两路,一路给反应器提供循环氢气,另一路经增压机15增压后,与来 自第一气液分离罐14罐底的液相混合通入再接触系统16,富氢气体由管线17 排出,再接触
系统排出的液相进入分馏系统18。分馏系统18为脱丁烷塔(图 中未画出),进入分馏系统的物料进入脱丁烷塔,塔顶得到液化气,由管线19 排出,塔底得到的c
5+
烃组分经管线33排出,可进入芳烃联合装置分离出芳烃, 也可作为汽油组分。所述四个反应器—反应器6、反应器8、反应器10和反应 器12依次串连,反应时,催化剂由上至下依次通过反应器6、反应器8、反应 器10和反应器12,从反应器12排出的待再生催化剂由管线29进入催化剂再 生器30进行再生,再生方法按常规移动床催化重整的催化剂再生方法进行,再 生后催化剂由管线31进入反应器6。
39.图2为本发明连续重整方法的流程示意图,与图1流程所示方法不同的是, 将四个反应器分为两个独立的反应区,第一反应区包括反应器6、反应器8和 反应器10,第二反应区只有一个反应器12。由管线1进入的精制石脑油与来自 循环压缩机2的循环管线3的氢气混合进入换热器4,与从反应器10排出的第 一反应产物换热后,依次进入加热炉5、反应器6、加热炉7、反应器8、加热 炉9、反应器10,在进入反应器前经加热炉加热到所需温度,从反应器10底部 排出的第一反应产物经过换热器4与精制石脑油换热后进入冷却器13冷却,再 进入第一气液分离罐14。第一气液分离罐14的顶部排出的气相分成三路,其 中一路给第一反应区提供循环氢气,另一路经管线24给第二反应区提供循环氢 气,第三路经增压机15增压后,与来自第一气液分离罐14罐底排出的液相混 合进入再接触系统16,再接触系统16包括冷却器和再接触罐(图中未画出), 富氢气体由管线17排出,再接触系统排出的液相进入分馏系统18。分馏系统 18包括脱丁烷塔、脱己烷塔和重整生成油分馏塔(图中未画出),进入分馏系 统的物料先进入脱丁烷塔,塔顶得到液化气,由管线19排出,塔底得到的c
5+
烃组分进入脱己烷塔;脱己烷塔塔顶得到的c5~c6烃组分由管线32排出,脱己 烷塔塔底得到的c
7+
烃组分进入重整生成油分馏塔;重整生成油分馏塔塔顶得 到c7~c8烃组分,塔底得到c
9+
烃组分。上述c
9+
烃组分经管线34排出。上述 c7~c8烃组分经管线20进入芳烃抽提装置21,经萃取分离,如液液萃取分离, 混合芳烃由管线22排出,抽余油即c7~c8非芳烃组分由管线23排出,与从第 一气液分离罐14上部由管线24排出的循环氢气(主要含氢气)混合,进入换 热器25,与从反应器12排出的第二反应产物换热后,依次进入加热炉11、反 应器12。从反应器12排出的第二反应产物经过换热器25换热后进入冷却器26 冷却,然后进入第二气液分离罐27,其顶部排出的气相经增压机28增压后, 进入第一气液分离罐14,底部排出的液相与第一气液分离罐14排出的液相合 并后进入再接触罐16。
40.下面通过实例进一步详细说明本发明,但本发明并不限于此。
41.实例1
42.按本发明方法进行石脑油催化重整生产芳烃。
43.使用中国石化催化剂公司生产的小球形铂锡催化剂,牌号为rc011,pt含 量为0.28质量%,锡含量为0.30质量%,氯含量为1.1质量%,余量为γ-氧化 铝载体。
44.重整精制石脑油各碳数烃族组成见表1,其馏程为81~158℃、密度0.738 g/cm3,硫质量分数《0.5μg/g,氮质量分数《0.5μg/g,砷硫质量分数《3.0ng/g, 铅质量分数《2.0ng/g,平均分子量106。
45.按图2的流程进行石脑油催化重整反应,不同的是反应器6、反应器8、 反应器10和反应器12是依次串连的固定床反应器,反应器6、反应器8、反应 器10和反应器12的催化剂装填量分别为30ml、45ml、75ml和120ml,四 个反应器催化剂的装填体积比为1:1.5:2.5:4。
反应器6、反应器8和反应器 10为第一反应区,反应器12为第二反应区,第二反应区的催化剂装填量占催 化剂总装量的44体积%。
46.将上述重整精制石脑油由管线1通入第一反应区,进料量为442.8g/h,来 自氢气循环压缩机2的循环管线3的循环气在标准状况下流量为240m3/h,循 环气中氢气含量为88体积%,氢/烃摩尔比为2.3。第一反应区三个反应器的平 均反应压力0.50mpa、平均温度为482℃,进料液时体积空速4.0h-1
。
47.从反应器10排出的第一反应产物经换热和冷却后进入第一气液分离罐14, 第一气液分离罐14操作温度为20℃、压力为0.38mpa。
48.将第一气液分离罐14顶部排出的气相的一部分增压后和底部排出液相混 合送入再接触系统16,接触系统16的再接触罐压力为2.5mpa,温度为4℃, 顶部管线17排出富氢气体,纯度为91体积%,再接触罐排出的液相物料进入 分馏系统18,分馏系统包括脱己烷塔、脱丁烷塔和重整生成油分馏塔,进入分 馏系统的物料先进入脱丁烷塔,塔顶得到液化气,塔底得到c
5+
烃组分进入脱 己烷塔;脱己烷塔塔底得到的c
7+
烃组分进入重整生成油分馏塔;塔顶得到 c7~c8烃组分,塔底得到c
9+
烃组分。脱丁烷塔的塔底温度为215℃、塔顶温度 为65℃、塔顶压力为1.0mpa;脱己烷塔的塔底温度为150℃、塔顶温度为88℃、 塔顶压力为0.18mpa;重整生成油分馏塔的塔底温度为194℃、塔顶温度为143℃、 塔顶压力为0.15mpa。
49.重整生成油分馏塔塔顶得到的c7~c8烃组分送入芳烃抽提装置21,采用液 液萃取分离芳烃和非芳烃,所用萃取溶剂为环丁砜,液液萃取所用的抽提塔塔 底温度为100℃、塔底压力0.6mpa,萃取溶剂与原料的质量比为4.0,回流比 为0.6,液液萃取得到的芳烃由管线22排出,抽余油为c7~c8非芳烃组分,进 入管线23。所述抽余油中c7~c8烷烃含量为82.4质量%、c7~c8环烷烃含量为 5.7质量%、c9烷烃含量为7.7质量%、c9环烷烃含量为3.1质量%、芳烃含量 为1.1质量%,平均分子量107,密度0.698g/cm3。具体地,所述抽余油中含 c7烷烃52.1质量%、c8烷烃30.3质量%、c9烷烃7.7质量%,c7环烷烃2.9质 量%,c8环烷烃2.8质量%,c9环烷烃3.1质量%。
50.上述抽余油由管线23经换热和加热后进入第二反应区的反应器12,进料 量为83.4g/h,该进料量是反应器6的进料量的18.8质量%,液时体积空速为 1.0h-1
,来自第一气液分离罐14的由管线24排出的循环气在标准状况下流量为 109l/h,氢/烃摩尔比为5.5,反应器12的压力为0.23mpa、温度为488℃。
51.由反应器12排出的反应产物经换热和冷却后进入第二气液分离罐27,第 二气液分离罐27操作温度为20℃、压力为0.14mpa。从第二气液分离罐27排 出的气相经增压机28增压后,进入第一气液分离气液分离罐14,底部排出的 液相物料与第一气液分离罐14排出的液相合并后进入再接触系统16。
52.装置石脑油进料量为442.8g/h,经过两个反应区的反应,所得纯h2产率为 4.0质量%、c
5+
收率为88.2质量%、芳烃产率为73.4质量%。
53.实例2
54.按实例1的方法对精制石脑油进行重整,不同的是反应器12的催化剂装 填量为150ml,四个反应器催化剂的装填体积比为1:1.5:2.5:5,第二反应 区的催化剂装填量占催化剂总装量的50体积%;进入反应器12的物料总进料 是104.9g/h,来自芳烃抽提装置管线23的抽余油的进料量为84.6g/h,再补加 来自芳烃联合装置的外加c7~c8芳烃抽余油(c7~
c8非芳烃组分),其进料量 为20.3g/h。
55.补加的c7~c8芳烃抽余油中,c7~c8烷烃含量为81.8质量%、c7~c8环烷烃 含量为5.7质量%,c9烷烃含量为8.0质量%、c9环烷烃含量为3.3质量%、芳 烃含量为1.2质量%,平均分子量107,密度0.698g/cm3。具体地,所述抽余油 中含c7烷烃50.2质量%、c8烷烃31.6质量%、c9烷烃8.0质量%,c7环烷烃 2.8质量%,c8环烷烃2.9质量%,c9环烷烃3.3质量%。
56.装置第一反应区石脑油进料量为442.8g/h,反应器12的总进料量是反应器 6进料量的23.7质量%,反应器12的进料液时体积空速为1.0h-1
,来自第一气 液分离罐14的由管线24排出的循环气在标准状况下的流量为137l/h,氢/烃摩 尔比为5.5,反应器12的压力为0.23mpa、温度488℃。
57.装置总进料量为463.1g/h,经过两个反应区的反应,所得纯h2产率为4.1 质量%、c
5+
收率为88.0质量%、芳烃产率为73.2质量%。
58.实例3
59.按实例2的方法对精制石脑油进行重整,不同的是补加的c7~c8芳烃抽余 油的进料量为60.7g/h。装置第一反应区石脑油进料量为442.8g/h,来自芳烃抽 提装置管线23的c7~c8芳烃抽余油的进料量为97.2g/h,反应器12的总进料量 为157.9g/h,该进料量是反应器6进料量的35.7质量%,反应器12的进料液时 体积空速为1.5h-1
,来自气液分离罐14的由管线24排出的循环气在标准状况 下的流量为124l/h,氢/烃摩尔比为3.3,反应器12的压力为0.23mpa、温度 488℃。
60.装置总进料量为503.5g/h,经过两个反应区的反应,所得纯h2产率为4.1 质量%、c
5+
收率为87.7质量%、芳烃产率为71.5质量%。
61.实例4
62.按实例1的方法对精制石脑油进行催化重整,不同的是反应器12的装填 75ml的催化剂,四个反应器催化剂的装填体积比为1:1.5:2.5:2.5,第二反 应区的催化剂装填量占催化剂总装量的33体积%,装置第一反应区石脑油进料 量为442.8g/h,进入反应器12的物料来自芳烃抽提装置由管线23排出的c7~c8芳烃抽余油,所述抽余油进料量为92.6g/h,该进料量是反应器6的进料量的 20.9质量%,反应器12的进料液时体积空速为1.8h-1
,来自气液分离罐14的由 管线24排出的循环气在标准状况下的流量为98l/h,氢/烃摩尔比为4.5,反应 器12的压力为0.23mpa、温度492℃。
63.装置石脑油进料量为442.8g/h,经过两个反应区的反应,所得纯h2产率为 4.0质量%、c
5+
收率为88.6质量%、芳烃产率为72.3质量%。
64.对比例1
65.按图1的流程,以实例1所述的精制石脑油为重整原料,并将实例1所述 的催化剂装入反应器6、反应器8、反应器10和反应器12四个反应器,催化剂 装填量依次分别为30ml、45ml、75ml、120ml。四个反应器催化剂的装填体 积比为1:1.5:2.5:4。
66.四个反应器为同一个反应区,精制石脑油进料量为442.8g/h,进料液时体 积空速为2.2h-1
,来自氢气循环压缩机2的循环管线3的循环气在标准状况下 流量为240l/h,氢/烃摩尔比为2.3。前三个反应器的平均反应压力0.50mpa, 平均温度为482℃。
67.从反应器10得到的产物直接进入反应器12。反应器12的平均反应压力 0.43mpa,温度为493℃。
68.从反应器12排出的反应产物经换热和冷却后进入第一气液分离罐14,第 一气液分离罐14操作温度为20℃、压力为0.34mpa。
69.将第一气液分离罐14顶部排出气相的一部分增压后和底部排出液相混合 后送入再接触系统16,再接触系统16的接触罐压力为2.5mpa,温度为4℃, 顶部管线17排出富氢气体,纯度为91体积%,再接触罐排出的液相物料进入 分馏系统18的脱丁烷塔,塔顶得到液化气,由管线19排出,塔底得到的c
5+
烃组分经管线33排出。脱丁烷塔的塔底温度为217℃、塔顶温度为65℃、塔顶 压力为1.0mpa。
70.装置石脑油进料量为442.8g/h,经过一个反应区的反应,所得纯h2产率为 3.7质量%、c
5+
收率为88.9质量%、芳烃产率为69.5质量%。
71.对比例2
72.按实例1的方法对精制石脑油进行催化重整,不同的是反应器12的反应 压力0.50mpa,进入反应器12的c
7+
抽余油的进料量为83.2g/h,该进料量是反 应器6进料量的18.8质量%,反应器12的进料液时空速1.0h-1
,来自氢气循环 压缩机2的管线3的循环气在标准状况下流量为108l/h,氢/烃摩尔比比为5.5, 反应器12的温度491℃。
73.装置石脑油进料量为442.8g/h,经过两个反应区的反应,所得纯h2产率为 3.8质量%、c
5+
收率为86.9质量%、芳烃产率为71.4质量%。
74.表1
75.烃碳数烷烃,质量%环烷烃,质量%芳烃,质量%c50.420.270c67.944.800.67c712.4412.032.60c815.9014.505.36c910.707.631.32c
10
2.930.470.02总计,质量%50.3339.709.97