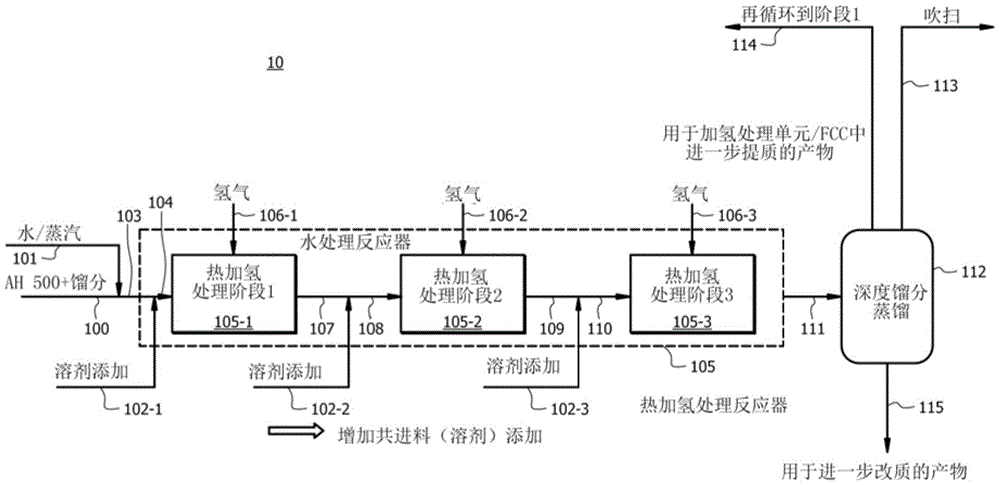
本申请要求2019年1月29日提交的第62/798,409号美国临时申请的优先权和权益,其全部内容通过引用并入本文。
技术领域:
本发明总体上涉及原油和/或重油和/或渣油的精炼。更具体地,本发明涉及原油和/或重油和/或渣油的热加氢处理以生产中间产物,然后可以将其用于制造有价值的化学品,例如烯烃和芳族化合物。
背景技术:
将全石油原油转化为本领域实践的化学品包括使用一系列加氢裂化器、流化催化裂化器(FCC)和蒸汽裂化器以仅生产高价值化学品或生产高价值化学品和燃料的组合。然而,加氢裂化、流化催化裂化和蒸汽裂化工艺涉及在实际将烃进料到最终转化单元例如蒸汽裂化器或FCC以生产烯烃和/或芳族化合物之前使用多步工艺(例如渣油加氢裂化、焦化、中间馏出物加氢裂化、石脑油系列加氢裂化等)对原油重质馏分进行改质时出现问题。此外,所采用的加氢处理条件涉及至多200barg的高压,这需要高昂的设备投资成本。因为改质涉及在每个阶段使用多个进料制备单元,例如加氢裂化器、焦化器和加氢处理器,不仅有分子的强制裂化和添加H2以满足由于在每个阶段裂化而引入的氢不足,还有通过这些进料制备单元中的每一个的进料预热炉将进料预热到操作温度。这也导致在公用事业方面消耗大量燃料。因此,需要利用使用最少数量的处理单元并采用以最佳方式将原油转化为下游转化单元的进料的工艺的更强化的工艺来将进料改质和转化为化学品。下游转化单元将进料转化为高价值化学品;并且希望在生产丙烯和苯的同时优先使乙烯最大化。技术实现要素:已发现为与加工原油和/或重油和/或渣油相关的至少一些问题提供解决方案。该解决方案的前提是使用氢气和水和/或蒸汽来有效改质原油和/或重油和/或渣油的复杂工艺。然后将改质产物送入转化单元,其将这些改质产物转化为烯烃和芳族化合物,如乙烯、丙烯、丁烯和苯。本发明的实施方案包括一种处理烃的方法。该方法包括使一种混合物在处理单元中经受足以将原料的至少一些烃分子转化为碳原子数少于所述至少一些烃分子的分子的条件,其中所述混合物包括(1)原油和/或重油和/或渣油的原料,(2)水和/或蒸汽,(3)氢气,(4)选择性溶解沥青质的溶剂。该方法还包括从处理单元回收中间产物料流,其包括:(1)主要包含C1至C4烃的气体料流,(2)主要包含饱和物的液体料流。此外,该方法包括裂化液体料流以生产乙烯、丙烯、丁烯和苯中的一种或多种。本发明的实施方案包括一种处理烃的方法。该方法包括将(1)原油和/或重油和/或渣油的原料,(2)水和/或蒸汽,(3)氢气,(4)选择性用于溶解沥青质的溶剂流入处理单元,所述处理单元包括(a)包含多个反应器的反应器单元和(b)包含蒸馏塔的分离单元。该方法还包括使一种混合物在所述多个反应器的第一个反应器中经受足以将原料的至少一些烃分子转化为碳原子数少于所述原料的至少一些烃分子的分子的条件,其中所述混合物包括原油和/或重油和/或渣油的原料、水和/或蒸汽、氢气的第一部分和溶剂的第一部分。在该方法的实施方案中,没有为转化所述至少一些烃分子提供催化剂,并且在混合物中提供溶剂,其量足以使来自原料的至少90wt%的沥青质保持在溶液中,从而沥青质不会在转化过程中析出(crashout)。该方法还包括使第一反应器流出物从第一反应器流入多个反应器中的第二反应器,并使第一反应器流出物、氢气的第二部分和溶剂的第二部分在多个反应器的第二反应器中经受足以将第一反应器流出物的至少一些烃分子转化为碳原子数少于第一反应器流出物的至少一些烃分子的分子的反应条件。多个反应器的构造实际上可以是单个大反应器(例如管式反应器、泡罩塔反应器、喷射环流反应器或其他类型),沿其长度分阶段注入溶剂和氢气。该方法还包括使反应器单元流出物从反应器单元流入分离单元,并在蒸馏塔中蒸馏反应器单元流出物,以产生蒸汽,其包括:(1)主要包含C1至C4饱和物的气体料流,(2)主要包含饱和物的液体产物料流。该方法还可包括从反应器单元去除焦炭。该方法还包括在蒸汽裂化器中裂化液体产物料流以生产乙烯、丙烯、丁烯和苯中的一种或多种。以下包括在整个说明书中使用的各种术语和短语的定义。在说明书和/或权利要求书中使用的术语“原油”是指来自地下的未加工制造产品如汽油、石脑油、煤油、瓦斯油和渣油的油。原油的比重可为4至80°API,更通常为15至45°API。说明书和/或权利要求书中使用的术语“重油”是指沸点高于350℃的原油部分,其可以产生作为原油常压塔底物或原油的在原油减压塔中产生的沸点为350℃至550℃的减压瓦斯油部分或作为原油减压塔底物产生的沸点高于550℃的减压渣油部分。说明书和/或权利要求书中使用的术语“渣油(residual)”(或“渣油(resid)”)是指石油化合物的混合物,包括芳族化合物、链烷烃、硫、氮金属,是通过去除沸点低于某个沸点的物质从全原油中产生的。例如,当蒸馏全原油以去除沸点低于120℃的烃时,会产生120+℃的渣油作为底物。术语“饱和物”是指单独或任意组合的链烷烃、异链烷烃和环烷烃类型的烃。术语“树脂”是指具有多于3至4个芳香环的烃,带有或不带有侧链以及带有或不带有环烷类物质。术语“沥青质”是指具有岛和群岛结构的分子以及具有带和不带杂原子的多环的分子。术语“约”或“近似”被定义为接近于,如本领域普通技术人员所理解的。在一个非限制性实施方案中,这些术语被定义为在10%以内,优选在5%以内,更优选在1%以内,最优选在0.5%以内。术语“重量%”、“体积%”或“摩尔%”分别是指基于包括组分的材料的总重量、总体积或总摩尔数计的组分的重量、体积或摩尔百分比。在非限制性实施例中,在100mol材料中的10mol组分为10mol%的组分。术语“基本上”及其变体被定义为包括10%以内,5%以内,1%以内或0.5%以内的范围。术语“抑制”或“减少”或“防止”或“避免”,或这些术语的任何变体,当用在权利要求和/或说明书中时,包括任何可测量的下降或完全抑制以实现所需的结果。如在说明书和/或权利要求书中使用的术语“有效”是指足以实现期望的、预期的或打算的结果。当在权利要求书或说明书中与术语“包含”、“包括”、“含有”或“具有”一起使用时,词语“一(a)”或“一(an)”的使用可表示“一个(one)”,但其也具有“一个或多个”、“至少一个”和“一个或多于一个”的含义。词语“包含(comprising)”(以及包含的任何形式,例如“包含(comprise)”和“包含(comprises)”)、“具有(having)”(以及具有的任何形式,例如“具有(have)”和“具有(has)”)、“包括(including)”(以及包括的任何形式,例如“包括(include)”和“包括(includes)”)或“含有(containing)”(以及含有的任何形式,例如“含有(contain)”和“含有(contains)”)是包含的或开放的且不排除额外的、未列举的元素或方法步骤。本发明的工艺可以“包含”在整个说明书中公开的特定成分、组分、组合物等,“基本上由其组成”或“由其组成”。术语“主要”,如在说明书和/或权利要求中使用的该术语,表示大于50重量%、50摩尔%和50体积%中的任一个。例如,“主要”可以包括50.1重量%至100重量%和其间的所有值和范围、50.1摩尔%至100摩尔%和其间的所有值和范围或50.1体积%至100体积%和其间的所有值和范围。本发明的其它目的、特征和优点将从以下附图、详细描述和实施例中变得显而易见。然而,应当理解,在指出本发明的具体实施方案的同时,附图、详细描述和实施例仅以说明的方式给出,而不意味着限制。另外,预期从本详细描述中,在本发明的精神和范围内的改变和修改对于本领域技术人员将变得显而易见。在其他实施方案中,来自具体实施方案的特征可以与来自其他实施方案的特征组合。例如,来自一个实施方案的特征可以与来自任何其他实施方案的特征组合。在进一步实施方案中,可以向本文所述的具体实施方案添加附加特征。附图说明为了更全面的理解,现结合附图参考以下描述,其中:-图1是根据本发明的实施方案的一种用于对原油和/或重油进行热加氢处理的系统;-图2是根据本发明的实施方案的一种用于对原油和/或重油和/或渣油进行热加氢处理的方法;-图3是根据本发明的实施方案的一种与蒸汽裂化器单元组合的用于对原油和/或重油和/或渣油进行热加氢处理的系统;和-图4是根据本发明的实施方案的一种用于对原油和/或重油和/或渣油进行热加氢处理的方法。具体实施方式已发现一种用于对全原油和/或重油和/或渣油进行改质的方法,其涉及在热加氢处理单元中使用氢气和水和/或蒸汽。改质后的产物随后被转化为烯烃(如乙烯、丙烯和丁烯)和芳族化合物(如苯)。图1显示了根据本发明的实施方案的用于对原油和/或重油和/或渣油进行热加氢处理的系统10。图2显示了根据本发明的实施方案的用于对原油和/或重油和/或渣油进行热加氢处理的方法20。使用系统10可以实施方法20。表A显示了图1所示的AH500+馏分和AL500+馏分的特性。应当注意,本发明的实施方案可以包括在表A中所示值的10%范围内的特性值。表A性质AL505+℃馏分AH505+℃馏分API比重9.55.5密度(g/cc)1.00241.0223K因子11.6411.56总硫量,重量%4.095.32总氮量,ppm22092861康拉逊碳残留物,重量%17.221.91沥青质,重量%6.3914.69根据本发明的实施方案,方法20包括,在方框200处,将进料100(原油和/或重油和/或渣油)流入热加氢处理反应器105。在本发明的实施方案中,进料100包含AH500+℃。根据本发明的实施方案,AH500+℃馏分具有以下特性:5.0至6.0API比重,0.92007至1.12453密度(g/cc),10.404至12.716K因子,4.788至5.852重量%总硫量,2574.9至3147.1ppm总氮量,19.72至24.10重量%康拉逊碳残留物,13.22至16.16重量%沥青质。本发明的实施方案中的方框200包括将进料100与H2O料流101(水和/或蒸汽)组合以形成组合进料103。根据本发明的实施方案,以相对于进料100供应至少大于0.2重量%的氢气所需的流速提供H2O。在本发明的实施方案中,H2O料流101处于25至300℃的温度。根据本发明的实施方案,组合进料103可以在25至500℃的范围内的温度下进入热加氢处理反应器105。作为在热加氢处理反应器105外混合进料100和H2O料流101以形成组合进料103的替代或补充,在本发明的实施方案中,进料100可以在热加氢处理反应器105(可以是一个反应器或可以包括多个子反应器)内与H2O料流101组合。根据本发明的实施方案,热加氢处理反应器105包括在热加氢处理反应器105中实施多个阶段的多个子反应器。如图1所示,热加氢处理反应器105可包括子反应器105-1、子反应器105-2和子反应器105-3,其中每个子反应器实施在热加氢处理反应器105中的热加氢处理阶段。根据本发明的实施方案,在方框201处,将溶剂102-1加入到组合进料103中以形成混合物104,其被进料到热加氢处理反应器105(特别是子反应器105-1)。替代地或另外地,在本发明的实施方案中,组合进料103或其组分可在热加氢处理反应器105(特别是子反应器105-1)内与溶剂102-1组合。根据本发明的实施方案,将溶剂102-1用于溶解沥青质并将其保持在溶液中。在本发明的实施方案中,溶剂102-1主要包括芳族化合物和/或树脂。在本发明的实施方案中,溶剂102-1包括原油、阿拉伯轻质油、阿拉伯重质油或其组合。用于本发明实施方案的其他溶剂可以是溶胀溶剂,例如丙酮、乙腈、甲醇、乙酸乙酯,烃溶剂例如己烷、庚烷、异辛烷,电子供体溶剂(有机碱)例如吡啶、四氢呋喃、胺,及其组合。应当注意,将溶剂102-1添加到组合进料103和/或子反应器105-1中的混合物中防止沥青质在操作期间从溶液中析出(沉淀)。在方框202处,在本发明的实施方案中,将氢气料流106-1加入到子反应器105-1中。在本发明的实施方案中,氢气料流106-1包括来自蒸汽甲烷重整器的纯氢气或氢气网或富氢料流例如燃料气。燃料气可包含H2、C1、C2和在某种程度上的C3。在本发明的实施方案中,优选使氢气料流106-1包含大于50重量%的H2。根据本发明的实施方案,氢气料流106-1可以在25至500℃的范围内的温度下进入热加氢处理反应器105。根据本发明的实施方案,在方框203处,混合物104和氢气料流106-1的混合物在子反应器105-1中经受足以改质进料100的反应条件。以此方式,进料100的烃分子被转化为更小的分子。根据本发明的实施方案,改质工艺可以在子反应器105-1中在400-550℃范围内,优选在450-470℃范围内的温度;至多200barg,优选100barg或更低的压力下进行。在这里,该工艺包括用水和/或蒸汽、在氢气压力下的共同进料(溶剂)处理全原油或重油,这将全原油或重油转化为较轻的化合物,例如馏出物。如本文所公开的,在热加氢处理反应器105(特别是子反应器105-2)中包括氢气也具有减少焦炭形成的作用并导致更高的碳效率。根据本发明的实施方案,在反应器中引入水/蒸汽可具有减少焦炭形成的益处。在方框204处,根据本发明的实施方案,流出物107从子反应器105-1流出。根据本发明的实施方案,存在于子反应器105-1、子反应器105-2、子反应器105-3中的每一个的进料(混合物)中的350+℃的材料转化为350-℃的材料达到100%,或者90%、80%、70%和不少于60%的程度。这种转化可以通过子反应器105-1、子反应器105-2、子反应器105-3来实现。在本发明的实施方案中,方法20包括在方框205处将溶剂102-2添加到流出物107以形成混合物108,在方框206处将其进料至子反应器105-2。根据本发明的实施方案,方法20在方框207处包括将氢气料流106-2添加到子反应器105-2。在本发明的实施方案中,氢气料流106-2具有与氢气料流106-1相似或相同的组成。根据本发明的实施方案,氢气料流106-2可以在25至500℃的范围内的温度下进入子反应器105-2。根据本发明的实施方案,在方框208处,混合物108和氢气料流106-2的混合物在子反应器105-2中经受足以将混合物108的烃分子转化为更小的分子的反应条件(进料100的进一步改质)。根据本发明的实施方案,所述进一步改质可以在子反应器105-2中在400-550℃范围内,优选在450-470℃范围内的温度;至多200barg,优选100barg或更低的压力下进行。在方框209处,根据本发明的实施方案,流出物109从子反应器105-2流出。根据本发明的实施方案,存在于子反应器105-1、子反应器105-2、子反应器105-3中的每一个的进料(混合物)中的350+℃的材料转化为350-℃的材料达到100%,或者90%、80%、70%和不少于60%的程度。这种转化可以通过子反应器105-1、子反应器105-2、子反应器105-3来实现。在本发明的实施方案中,方法20包括在方框210处将溶剂102-3添加到流出物109以形成混合物110,在方框211处将其进料至子反应器105-3。根据本发明的实施方案,方法20在方框212处包括将氢气料流106-3添加到子反应器105-3。在本发明的实施方案中,氢气料流106-3具有与氢气料流106-1相似或相同的组成。根据本发明的实施方案,氢气料流106-3可以在25至500℃的范围内的温度下进入热子反应器105-3。根据本发明的实施方案,在方框213处,混合物110和氢气料流106-3的混合物在子反应器105-3中经受足以将混合物110的烃分子转化为更小的分子的反应条件(进料100的进一步改质)。根据本发明的实施方案,所述进一步改质可以在子反应器105-3中在400-550℃范围内,优选在450-470℃范围内的温度;至多200barg,优选100barg或更低的压力下进行。根据本发明的实施方案,添加溶剂以将沥青质保持在溶液中并且使得转化率随着阶段的增加而增加(例如,从子反应器105-1,到子反应器105-2,到子反应器105-3)。温度可以从子反应器105-1,到子反应器105-2,再到子反应器105-3而升高。根据本发明的实施方案,可连续增加反应器进料的加工苛刻度以获得较高的转化率。在方框214处,根据本发明的实施方案,流出物111从子反应器105-3流入蒸馏塔112。随着转化在子反应器105-1、然后是子反应器105-2、然后是子反应器105-3中进行,溶液中的沥青质趋向于聚集和沉淀出来。根据本发明的实施方案,通过形成共进料/溶剂混合物(即,添加溶剂102-1、溶剂102-2和溶剂102-3)以将沥青质保持在溶液中来克服该趋势。如果不添加使沥青质保持在溶液中的溶剂,进料的高转化率会导致严重的焦化和严重的操作问题(例如堵塞)。另一个目的是使用溶剂来放松/扩大沥青质层之间的距离以防止聚集,并且还可以用作氢供体,并且在使用极性溶剂(例如吡啶、THF)时还可以用作电子供体。应当注意,在本发明的实施方案中,在每个阶段,即在子反应器105-1、子反应器105-2和子反应器105-3处添加的溶剂(共进料)的量增加。换言之,在实施方案中,添加到子反应器105-2的溶剂102-2的量大于添加到反应器105-1的溶剂102-1的量。并且在实施方案中,添加到子反应器105-3的溶剂102-3的量大于添加到子反应器105-2的溶剂102-2的量。总之,根据本发明的实施方案,分阶段加入富含芳族化合物和树脂的溶剂以将这些沥青质保持在溶解形式,从而导致它们更高的转化率。根据本发明的实施方案,在系统10中进行方法20,使得工艺液体处于沥青质稳定条件下,其中P值大于1且更接近于1.2。P值定义为P=1+Xmin(壳牌标准SMS1600-01),其中临界十六烷稀释度(Xmin)是十六烷的毫升数,1g样品可以用它稀释,直到它不会将沥青质絮凝。根据本发明的实施方案,在方框215处,蒸馏塔112蒸馏流出物111以产生用于进一步改质的产物料流115、用于再循环到任何先前子反应器的再循环料流114和用于防止不需要的固体/焦炭在一段时间内积累的重质吹扫料流113。在高苛刻条件(包括400至550,优选450℃至470℃范围内的温度和至多200barg(通常为100barg或更低)的压力)下操作热加氢处理反应器105(统称为子反应器105-1、子反应器105-2和子反应器105-3),导致产物料流115,即来自该工艺的液体产物,具有超过97重量%的沸点低于350℃的烃。由于方法20是一种热加氢处理过程,因此预期产物将比其他过程具有更多的烯烃。实际上,对沸点低于240℃的液体产物的分析表明,在详细烃分析仪(DHA)中使用ASTMD6730进行分析时,具有8重量%的烯烃含量。此外,在本发明的实施方案中,作为热加氢处理的结果,预期在气相中存在一些烯烃并且发现该气体具有0.65mol%的烯烃。在本发明的实施方案中,蒸汽裂化器进料应优选包含小于1wt%的烯烃以使得焦化最小化。因此,可以将来自热加氢处理的产物(例如流出物111)进料到下游深度加氢单元以饱和烯烃以及打开环化合物,从而可以将其进料到蒸汽裂化器。现在,该料流将富含饱和烃,并且可以送入蒸汽裂化器以生产高价值化学品,如乙烯、丙烯、丁烯和苯。根据本发明的实施方案,加氢处理反应器105产生焦炭料流116。在加氢处理反应器105是固定床反应器的本发明实施方案中,焦炭在再生过程中燃烧。在加氢处理反应器105是沸腾床的本发明的实施方案中,可以存在焦炭燃烧步骤。在加氢处理反应器105是淤浆反应器或泡罩塔反应器的本发明的实施方案中,可以通过从下游蒸馏单元吹扫少量底部料流来去除焦炭。图3是根据本发明的实施方案,与进行深度氢化的加氢处理器和蒸汽裂化器单元组合的用于对原油和/或重油和/或渣油进行热加氢处理的系统30。图4显示了根据本发明的实施方案的用于对原油和/或重油和/或渣油进行热加氢处理的方法40。可以使用系统30实施方法40。在本发明的实施方案中,全原油300在方法40的方框400中在闪蒸塔301中闪蒸以分离出原油300中固有存在的轻质气体。应当注意,在本发明的实施方案中,闪蒸塔301的进料可以是重油。在本发明的实施方案中,轻质气体302可以被进料到专用气体裂化器或混合进料裂化蒸汽裂化器。如图3和图4所示,在本发明的实施方案中,在方框401处,将轻质气体302从闪蒸塔301进料到蒸汽裂化器307。根据本发明的实施方案,轻质气体302包含0至5重量%的C2、30至40重量%的C3、10至20重量%的iC4和45至55重量%的nC4。根据本发明的实施方案,来自闪蒸塔301底部的稳定化的原油303被进料到高苛刻度热加氢处理单元304(例如上述系统10)以在方框402处如上面方法20中所述的生产气体、液体和焦炭产物。在本发明的实施方案中,来自热加氢处理单元304的气体产物被进料到气体裂化器或混合进料裂化炉,液体被进料到深度加氢单元,然后被进料到液体蒸汽裂化器或混合进料炉并且在下游锅炉/气化器/任何其他应用场合中使用吹扫,其从吹扫或使用吹扫回收能量值,用于下游应用,如电极、鼓风炉等。在本发明的实施方案中,吹扫用于产生氢气和/或合成气,作为燃料,和/或在道路建设应用和/或防水中用作焦油组分。在本发明的实施方案中,方法40包括,在方框403处,产物料流305(例如,产物料流115)与轻质气体302一起流入蒸汽裂化器307。另外地或替代地,在本发明的实施方案中,使产物料流316(例如产物料流111或其一部分)流入加氢处理器315,其对产物料流316进行加氢处理以形成主要包含饱和烃的饱和产物料流317。然后使饱和产物料流317流入蒸汽裂化器307进行处理。根据本发明的实施方案,产物料流316包含25至35wt%链烷烃、25至35wt%异链烷烃、6至10wt%烯烃、12至15wt%环烷烃和12至15wt%芳族化合物。根据本发明的实施方案,饱和产物料流317包含30至50重量%链烷烃、25至35重量%异链烷烃、0至10重量%环烷烃和0至5重量%芳族化合物。在方框404处,蒸汽裂化器307将轻质气体302、产物料流305和/或饱和产物料流317裂化以产生蒸汽裂化器流出物料流308。根据本发明的实施方案,操作蒸汽裂化器307以提供以下工艺反应条件:800至860℃范围内的温度、2至3barg范围内的压力和0.1至0.5秒的接触时间。根据本发明的实施方案,蒸汽裂化器流出物料流308包含0.5至1.5重量%氢气、15至20重量%甲烷、35至45重量%乙烯、15至20重量%丙烯、10至15重量%C4化合物、0.5重量%裂解汽油、0至0.5重量%燃料油、5至10重量%苯和2.5至7.5重量%焦炭。在方框405处,蒸汽裂化器流出物被送至蒸汽裂化器炉下游段309,在那里蒸汽裂化器流出物308经受本领域已知的标准分离技术并在工业上实践以生产轻质气体烯烃310,链烷烃气体料流(未在图3中示出,但再循环至蒸汽裂化器炉307),用作工厂燃料或用于生产氢气的甲烷和氢气料流(图3中也未显示)和在方框406处的蒸汽裂化器下游流出物311,以进料到芳族化合物提取段312以通过已知的商业方法分离苯。根据本发明的实施方案,在以下条件下操作蒸汽裂化器307:800至860℃范围内的温度、2至3barg范围内的压力和0.1至0.5秒的接触时间。根据本发明的实施方案,轻质气体烯烃310包含50至65重量%的乙烯、25至30重量%的丙烯和15至20重量%的丁烯。在本发明的实施方案中,在方框407处,使蒸汽裂化器下游流出物311流入芳族化合物萃取单元312,其萃取苯313以离开再循环料流314。根据本发明的实施方案,再循环料流314包含45至55重量%的汽油和45至55重量%的燃料油。为了避免产物中的燃料油或热解汽油从蒸汽裂化器307出来,通过在提取较高价值的苯之后将再循环料流314送回热加氢处理单元304而将再循环料流314循环耗尽。在将苯提取到热加氢处理单元304之后再循环料流314的再循环是有利的,因为该料流富含芳族化合物并且将有助于在热加氢处理单元304中的转化期间保持沥青质处于可溶状态并减少该单元中的结垢/使焦炭最小化。方法40可导致乙烯收率超过30重量%,而来自原油的高价值化学品(即乙烯、苯、丙烯和丁烯/丁二烯)的收率可能超过70重量%。此外,在本发明的实施方案中,乙烯/丙烯的质量收率比高于1.2,优选高于1.5,更优选高于2。该工艺中产生的甲烷可用于产生氢气。此外,该工艺中产生的甲烷和氢气可用作蒸汽裂化炉/热加氢处理预热炉的燃料,或用于石油化工综合设施中的公用事业部分的能源价值。此外,可以通过将分离的甲烷和氢气混合物进料通过PSA/膜单元或任何此类氢气回收单元来从来自蒸汽裂化器的裂化气产物中回收氢气。回收的氢气可在热加氢处理单元304内部使用,而分离的甲烷气体可用于其在熔炉中的能量含量,利用氢气发生单元(蒸汽甲烷重整器)生产额外的氢气,或用于转化单元,如甲烷氧化偶合(OCM)单元以生产附加的高价值乙烯。尽管已经参考图2和图4的方框描述了本发明的实施方案,但是应理解,本发明的操作不限于图2和图4中所示的特定方框和/或方框的特定顺序。因此,本发明的实施方案可以使用与图2和图4的不同顺序的各种方框来提供如本文所述的功能。实施例实施例1(原油热加氢处理效果的证明)作为本发明的公开内容的一部分,下面包括具体的实施例。所述实施例仅用于说明的目的,并不旨在限制本发明。本领域的技术人员将容易认识到可改变或改进以产生实质上相同结果的参数。本研究中使用了沸点分布范围为120℃至705℃的WestTexas混合原油残渣。沸点范围为120℃至240℃的进料组合物包含25.047重量%链烷烃、22.343重量%异链烷烃、0.287重量%烯烃、11.727重量%环烷烃、16.938重量%芳族化合物、0.385重量%重质烃和23.275重量%其他未知的烃类型。进料在30℃下的密度为0.85g/cc。该料流的沸点分布如下表1所示。表1进料料流的沸点分布本研究中使用的反应器是位于3区分裂管炉内的固定床反应器。反应器内径为13mm,具有同心设置的3.17mm外径的热电偶套管。反应器长度为91.3cm。反应器填充有中性氧化铝,用于将热量传递给用作进料的来自WestTexas混合原油的120+℃沸点馏分残渣。将反应器保持在重时空速(WHSV)为1hr-1(油流速为20.4g/hr,即0.4ml/min)、H2/HC比为400NL/L的液体进料(流速为9.4NL/h的H2气)、压力为40.8barg(600psig)和反应器惰性床温度为450℃的操作条件下。将反应器流出气体(例如烃产物)冷却以在压力下冷凝液体(即液体产物形式的处理过的烃料流)同时允许未冷凝的气体(例如甲烷、乙烷或其组合)分离为气体产物并流入湿气表。使用炼油厂气体分析仪气相色谱(来自M/sACAnalyticalControlsBV的定制气体分析仪)分析流出气体流。从填充床反应器获得的液体产物通过模拟蒸馏(SIMDIS)气相色谱仪分析沸点分布,如表2所示。SIMDIS结果表明,从终沸点高于700℃的进料开始,整个产品的沸点低于350℃。该液体通过详细烃分析仪(ASTMD6730)进一步分析,并具有沸点低于240℃的产物的PIONA组成,如表3所示,其中液体产物中的烯烃浓度约为7.8重量%。这表明产物中的烯烃在进料到进行深度加氢反应的加氢处理器中的蒸汽裂化器之前需要饱和化。然而,也可以通过更高的反应器压力或采用较高的H2/烃比来增加氢气分压而改变反应器的苛刻度以及液体产物中的烯烃浓度。利用这些工艺流程,液体产物中的烯烃可能会低于1重量%,这将使下游加氢处理器成为任选。表2进料和液体产物的沸点分布表3Bp低于240℃的液体产物和进料的详细烃分析样品号样品pIONA重质物未知物1进料25.04722.3430.28711.72716.9380.38523.2752液体产物26.5524.5157.79313.9213.1140.02614.082例如,从含有22.9g沸点低于240℃的PIONA化合物的100g进料开始,生成的液体产物具有58.5g沸点低于240℃的PIONA化合物,其可以如下表4所示量化。表4粗反应器流出气体含有氢气,并且对该气体的分析表明气体产物中0.65mol%的烯烃,如表5所示。表5气体分析气体组分mol%C1,mol%9.1C2-C4饱和物,mol%4.26C2-C4烯烃,mol%0.65在无氢基础上,气体组分的mol%表示甲烷浓度为65.2重量%,C2-C4烯烃浓度为4.6重量%,如表6所示。表6气体分析气体组分mol%C1,mol%65.2C2-C4饱和物,mol%30.2C2-C4烯烃,mol%4.6这可以在蒸汽裂化器分离系统中分离以得到C2-C4烯烃产物、用作燃料/甲烷氧化偶联/任何其他目的的进料的甲烷以及用作蒸汽裂化器进料的C2-C4饱和物产物。实施例2(使用具有更高热导率的惰性碳化硅之类的效果)与实施例1中描述的方法类似地进行实验,不同之处在于惰性氧化铝被碳化硅替代,碳化硅与氧化铝相比具有更高的热导率。从反应获得的液体产物通过模拟蒸馏(SIMDIS)气相色谱仪分析沸点分布,如表7所示。超过96.5%的材料沸点在350℃以下,而来自实施例1中获得的产物的全部100%材料沸点在350℃以下。这可能再次归因于氧化铝与碳化硅相比具有更高的保温能力。残留酸度数据(如果在中性氧化铝中使用)将共享以证明残留酸度的贡献。在现实中观察到的影响将是残留酸度、热导率和工艺条件的综合影响。表7实施例4获得的液体产物的沸点分布表8Bp低于240℃的进料和液体产物的详细烃分析实施例3(与蒸汽裂化器相关的热加氢处理构思的影响)本实施例旨在说明与蒸汽裂化器相关的热加氢处理构思的有益效果,以生产高收率的高价值化学品,即乙烯、丙烯、苯和丁烯。图3是闪蒸塔与热加氢处理单元、使液体烯烃饱和的下游加氢处理单元和蒸汽裂化器单元组合的图示。进料原油在原油闪蒸塔中闪蒸,其中目的是仅从液体进料中去除H2、H2S和C1-C4烃,在碱洗/任何其他方法以去除H2S后,将其送入气体裂化器或混合进料炉以最大限度地转化为乙烯。来自闪蒸塔底部的稳定化的原油被送入热加氢处理单元,以生产其中超过97重量%的沸点低于350℃的液体产物。来自该单元的气体产物如上述供入气体裂化器,液体产物在加氢处理器中使进料中的烯烃饱和后供入液体蒸汽裂化器或混合进料炉。蒸汽裂化过程中产生的燃料油和裂解汽油进行苯抽提,余料循环回热加氢单元耗尽。这种再循环不仅有助于最大限度地获得所需的产物,而且有助于增加热加氢处理单元中的芳族化合物含量,这将有助于将沥青质保持在溶液中。表9中指示的质量平衡表明可以实现约38重量%乙烯、18重量%丙烯、12重量%丁烯和7.5重量%苯的典型收率。这使这些高价值化学品的收率达到整个原油的大约77重量%。该工艺的好处是乙烯与丙烯的比率约为2.1,这对于生产化学品相对于原油而言非常高。该工艺中焦炭的损失约为5-6重量%,这是炼油厂中典型的燃料和损失数字。可以从产物气体中分离出1重量%的H2收率以部分满足热加氢处理单元中的氢气需求,而平衡要求可以通过氢气发生单元来满足。工艺中产生的甲烷可用于满足工艺中的炉加热要求,或任何可用的剩余甲烷可用于制氢单元或可用作下游甲烷氧化偶联(OCM)或其他气体转化单元的进料,以生产用于乙烯生产或制备合成气的附加化学品。焦炭可用作产生蒸汽、热量的燃料,或可用于生产合成气,用于其他应用。表9蒸汽裂化器与热加氢单元组合的流程图的典型质量平衡在本发明的上下文中,至少描述了下面20个实施方案。实施方案1是一种处理烃的方法。该方法包括使一种混合物在处理单元中经受足以将原料的至少一些烃分子转化为碳原子数少于所述至少一些烃分子的分子的条件,其中所述混合物包括(1)原油和/或重油和/或渣油的原料,(2)水和/或蒸汽,(3)氢气,(4)选择性溶解沥青质的溶剂。该方法还包括从处理单元回收中间产物料流,其包括:(1)主要包含C1至C4烃的气体料流,(2)主要包含饱和物的液体料流,并裂化该液体料流以生产乙烯、丙烯、丁烯和苯中的一种或多种。实施方案2是实施方案1所述的方法,其中所述处理单元包括反应器单元和分离单元,并且所述方法进一步包括,在经受步骤之前,使(1)原油和/或重油和/或渣油的原料、(2)水和/或蒸汽、(3)氢气和(4)选择性溶解沥青质的溶剂流入反应器单元,其中该经受步骤在反应器单元中进行。所述方法还包括使流出物从反应器单元流入分离单元,其中分离单元包含蒸馏塔。所述方法进一步包括在蒸馏塔中蒸馏来自反应器单元的流出物以产生:(1)气体料流和(2)液体料流。实施方案3是实施方案2所述的方法,其中所述反应器单元包含多个反应器且所述经受步骤包括使一种混合物在所述多个反应器的第一反应器中经受足以将原料的至少一些烃分子转化为碳原子数少于所述原料的至少一些烃分子的分子的条件,其中所述混合物包括原油和/或重油的原料、水和/或蒸汽、氢气的第一部分和溶剂的第一部分。所述方法还包括使第一反应器流出物从第一反应器流入多个反应器中的第二反应器。所述方法还包括使第一反应器流出物、氢气的第二部分和溶剂的第二部分在多个反应器的第二反应器中经受足以将第一反应器流出物的至少一些烃分子转化为碳原子数少于第一反应器流出物的至少一些烃分子的分子的反应条件。实施方案4是实施方案3所述的方法,其中反应器单元包含两个反应器并且第二反应器流出物是来自反应器单元的流出物。实施方案5是实施方案3所述的方法,其还包括使第二反应器流出物从第二反应器流入多个反应器中的第三反应器,并使第二反应器流出物、氢气的第三部分和溶剂的第三部分在多个反应器的第三反应器中经受足以将第二反应器流出物的至少一些烃分子转化为碳原子数少于第二反应器流出物的至少一些烃分子的分子的反应条件。实施方案6是实施方案5所述的方法,其中反应器单元包含三个反应器并且第三反应器流出物是来自反应器单元的流出物。实施方案7为实施方案1至6任一项所述的方法,其中氢气由含有燃料气的富氢料流、裂化气和来自蒸汽甲烷重整的H2提供。实施方案8为实施方案2至7任一项所述的方法,其中氢气在反应器单元中维持在至多100barg、更优选至多70barg的压力下。实施方案9是实施方案1至8任一项所述的方法,其中所述溶剂主要包含芳族化合物、树脂和少于0.1重量%的苯。实施方案10是实施方案1至9任一项所述的方法,其中沥青质是稳定的,具有大于1的P值。实施方案11是实施方案1至10任一项所述的方法,其中所述方法不包括催化剂的使用。实施方案12为实施方案2至11任一项所述的方法,其中水和/或蒸汽以氢供应为原料的至少0.2重量%所需的流速供应至处理单元。实施方案13为实施方案1至12任一项所述的方法,其中乙烯/丙烯的质量收率比高于1.2,优选高于1.5且更优选高于2,并且乙烯收率高于35重量%。实施方案14为实施方案1至13任一项所述的方法,其中所述裂化进一步产生甲烷。实施方案15为实施方案14所述的方法,其中甲烷用于产生氢气。实施方案16为实施方案14所述的方法,其中所产生的甲烷被偶联以产生乙烯。实施方案17为实施方案1至15任一项所述的方法,进一步包括在裂化步骤之前对液体料流进行加氢处理。实施方案18是实施方案1至16任一项所述的方法,其中在经受步骤之前,原油和/或重油和/或渣油的原料被闪蒸以除去沸点低于35℃的材料。实施方案19为实施方案2至16任一项所述的方法,其中从裂化步骤中使用的蒸汽裂化器回收氢气并且将回收的氢气用于反应器单元。实施方案20为实施方案1至19任一项所述的方法,其中所述溶剂以足以使来自原料的至少90重量%的沥青质保持在溶液中的量提供在混合物中。尽管已经详细描述了本申请的实施方案及其优点,但是应当理解,在不脱离由所附权利要求限定的实施方式的精神和范围的情况下,可以在其中进行各种改变、替换和更改。此外,本申请的范围不旨在限于说明书中描述的工艺、机器、制造、物质组成、手段、方法和步骤的特定实施方案。如本领域普通技术人员将从以上公开内容容易地理解的,可以利用目前存在的或以后将开发的起到与本文所描述的相应实施方案基本相同的功能或实现与本文描述的相应实施方案基本相同的结果的工艺、机器、制造、物质组成、装置、方法或步骤。因此,所附权利要求旨在在其范围内包括这样的工艺、机器、制造、物质组成、手段、方法或步骤。当前第1页12