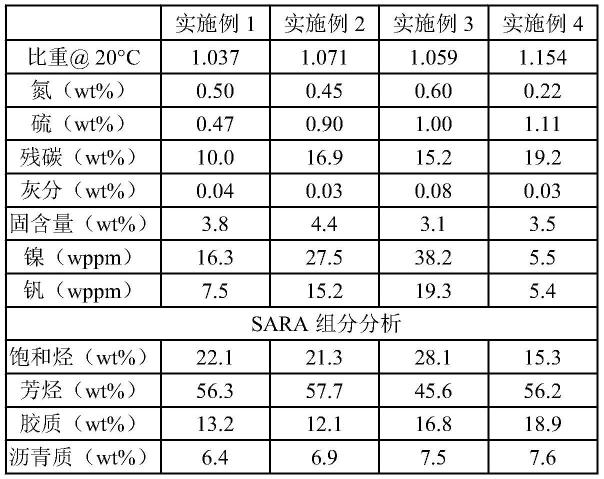
1.本技术涉及石油化工领域,特别涉及到一种针状焦生产工艺。
背景技术:2.油系针状焦原料,一般来自炼厂的催化裂化装置的催化油浆。催化油浆如果作为燃料油出售,经济效益很差。如果利用催化油浆生产针状焦,可显著提高产品的附加值。催化油浆生产针状焦的需求很大,一是基础原料较容易获得,二是国内针状焦市场缺口较大,目前还需要大量进口。针状焦不仅可用于制备超高功率石墨电极,也可用于制备热结构石墨、特种炭素制品及二次电池电极等。我国针状焦已实现工业化生产,但部分生产超高功率石墨电极用针状焦还依赖进口。针状焦品质的优劣主要与原料的筛选、处理和焦化工艺有关。在原料条件基本相同的前提下,焦化工艺操作条件不同,制备的针状焦质量差异明显。因此,如何有效处理油浆,以及优化焦化的工艺参数,是生产高质量针状焦需要解决的主要问题之一。
技术实现要素:3.本技术的目的是提供一种针状焦生产工艺,解决现有技术中针状焦生产质量差效率低的问题。
4.为实现上述目的,本技术实施例采用以下技术方案:一种针状焦生产工艺,包括以下步骤:萃取:通过萃取单元对催化油浆进行溶剂萃取,获得富芳烃油;脱硫:若富芳烃油中的硫含量高于0.5wt%,则通过脱硫单元将其中的硫含量降至0.5wt%以下;焦化:若富芳烃油中的硫含量低于0.5wt%,则通过焦化单元对富芳烃油进行焦化处理;
5.其中,萃取单元包括进料管线、沥青分离塔、多级分离装置以及汽提回收装置,多级分离装置包括至少一个分离塔,通过设置多级分离装置的数量控制富芳烃油的芳烃富集程度。对于不同品质的油浆,即使劣质油浆,也可以实现针状焦生产。
6.在上述技术方案中,本技术实施例通过采用脱硫单元对硫含量高于0.5wt%的富芳烃油进行脱硫处理,避免影响焦化步骤中针状焦的产生。同时,萃取单元采用超临界萃取及梯级分离方式,根据进料不同,选用不同的溶剂组合,可灵活生产芳烃富集程度不同的产品。
7.进一步地,根据本技术实施例,其中,进料管线与沥青分离塔的中部连接,将催化油浆输送至沥青分离塔内分离沥青,进料的催化油浆与萃取溶剂在进料管线内混合。
8.进一步地,根据本技术实施例,其中,沥青分离塔处于亚临界状态下进行满液操作,进料在沥青分离塔中被分离成第一物料和第二物料,第一物料包括溶剂和脱沥青油,第二物料包括沥青和夹带的少量溶剂。
9.进一步地,根据本技术实施例,其中,汽提回收装置包括汽提塔一,汽提塔一的中部与沥青分离塔的底部通过管道五连接,将聚集在沥青分离塔底部的第二物料输送至汽提塔一内;汽提塔一内分离出的溶剂从汽提塔一的顶部排出,剩余产品为沥青,从汽提塔一的
底部排出。
10.进一步地,根据本技术实施例,其中,多级分离装置包括第一分离塔,第一分离塔与沥青分离塔的顶部连通,将第一物料输入第一分离塔进行分离;第一分离塔为满液操作,且操作温度低于溶剂临界温度,操作压力高于溶剂临界压力,即为亚临界操作状态;升温后的第一物料进入第一分离塔后持续分离,分离出第三物料和第四物料,其中,第三物料为第一物料中的较轻组分,具体包括溶剂和富烷烃油,第四物料为第一物料中的较重组分,包括富芳烃油和夹带的少量溶剂。
11.进一步地,根据本技术实施例,其中,汽提回收装置包括汽提塔二,汽提塔二的中部与第一分离塔的底部连接,将聚集在第一分离塔底部的第四物料输送至汽提塔二内;汽提塔二内分离出的溶剂从汽提塔二的顶部排出,剩余产品为富芳烃油,从汽提塔二的底部排出。
12.进一步地,根据本技术实施例,其中,多级分离装置至少包括一第二分离塔,第二分离塔与第一分离塔的顶部连接,将物料三输送至第二分离塔内进行进一步的分离,第二分离塔内的操作状态为超临界操作状态,此时溶剂处于气液不分的状态,不必通过相变气化溶剂来分离溶剂和油,可通过超临界状态下溶剂与油的密度差将溶剂分离出来,第二分离塔中的产物为第五物料和第六物料,第五物料具体为溶剂,第六物料包括富集直链烷烃和夹带的少量溶剂。
13.进一步地,根据本技术实施例,其中,第二分离塔顶部设置有溶剂循环管一,用于将聚集在第二分离塔顶部的第五物料输送出来;溶剂循环管的末端与进料管线连通,将溶剂与进料混合并循环利用。
14.进一步地,根据本技术实施例,其中,汽提回收装置包括汽提塔三,汽提塔三的中部与第二分离塔的底部连接,将聚集在第二分离塔底部的第六物料输送至汽提塔三内;汽提塔三内分离出的溶剂从汽提塔三的顶部排出,剩余产品为富烷烃油,从汽提塔三的底部排出。
15.为了实现上述目的,本技术实施例还公开一种针状焦生产工艺,包括以下步骤:萃取:通过萃取单元对催化油浆进行溶剂萃取,获得富芳烃油;脱硫:若富芳烃油中的硫含量高于 0.5wt%,则通过脱硫单元将其中的硫含量降至0.5wt%以下;焦化:若富芳烃油中的硫含量低于0.5wt%,则通过焦化单元对富芳烃油进行焦化处理;
16.其中,萃取单元排出的富芳烃油通过管道六输送至脱硫单元或焦化单元,管道六末端设置有两路管线:
17.若管道六内的富烷烃油的硫含量高于0.5wt%,则被输送至脱硫单元进行脱硫处理,经过脱硫的富芳烃油通过管道八输送至焦化单元中的分馏塔内;
18.若管道六内的富烷烃油的硫含量低于0.5wt%,则通过另一路管道七输送至焦化单元。
19.在上述技术方案中,本技术实施例通过采用脱硫单元对硫含量高于0.5wt%的富芳烃油进行脱硫处理,避免影响焦化步骤中针状焦的产生。同时,通过管道八与焦化单元中的分馏塔连通,将富烷烃油输送至分馏塔内。据此,本技术高度整合和简化了脱硫单元和焦化单元,节省了传统加氢脱硫装置的汽提塔和分馏塔。
20.进一步地,根据本技术实施例,其中,所脱硫单元包括依次串联的加热炉一、脱硫
反应器和热分离罐;
21.富烷烃油和氢气在加热炉一的入口处混合形成第七物料;加热炉一将第七物料加热至反应进料温度,输送至脱硫反应器的顶部;第七物料经过脱硫反应器精制后,从脱硫反应器的底部排出,输送至热分离罐;在热分离罐内,第七物料中的富烷烃油和氢气分离,富烷烃油从热分离罐的底部排出,氢气从热分离罐的顶部排出;热分离罐的顶部与冷分离罐连接,进一步分离氢气中夹带的富烷烃油;管道八设置在冷分离罐的底部,管道八与热分离罐的底部连通,用于收集和输送分离出来的富烷烃油。
22.进一步地,根据本技术实施例,其中,冷分离罐内分离出的氢气从冷分离罐的上方排出,夹杂反应生成的少量低碳烷烃,以及h2s、nh3等杂质;冷分离罐与氨吸收塔连接,用于去除氢气中的h2s和nh3等杂质。
23.进一步地,根据本技术实施例,其中,焦化单元还包括焦化塔,焦化塔的顶部与分馏塔的中部连通,分离塔的底部与焦化塔的底部连通,物料在分馏塔和焦化塔之间循环。
24.进一步地,根据本技术实施例,其中,在分馏塔内,从焦化塔顶来的热油气进入分馏塔换热段,与来自脱硫单元或萃取单元的低硫富芳烃油直接换热后,冷凝出重馏分油落入塔底,由塔底泵送至加热炉二和焦化塔。
25.进一步地,根据本技术实施例,其中,在分馏塔内,从下往上依次分馏出蜡油、柴油、石脑油和富气(c
1-c4)。
26.进一步地,根据本技术实施例,其中,分馏塔塔底焦化油经塔底泵送至加热炉二,焦化油在炉管内快速升温到500-520℃左右,然后经四通阀进入焦化塔底部。
27.进一步地,根据本技术实施例,其中,焦化单元还包括管道十和加热炉三,管道十连接分馏塔的中部和焦化塔的底部,用于在焦化塔生焦阶段间歇注入轻油,进行拉焦处理。
28.与现有技术相比,本技术具有以下有益效果:
29.首先,本技术采用脱硫单元对硫含量高于0.5wt%的富芳烃油进行脱硫处理,避免影响焦化步骤中针状焦的产生。若富芳烃油中的硫含量低于0.5wt%,则无需进行脱硫处理,可以直接送入焦化单元进行焦化处理;
30.其次,本技术通过萃取单元,根据相似相溶的萃取原理,可进行多级分离,从而更精准的优化分离生产适合针状焦的原料油。对于不同品质的油浆,即使劣质油浆,也可以实现针状焦生产;
31.最后,本技术通过向焦化塔内间隙注入轻油,可以提高针状焦的质量。具体地,在焦化塔生焦阶段,塔内进行缩合反应生成焦炭。但传统的焦化装置,即使经过原料预处理,也会有部分焦炭不达标,生成普通的海绵焦。如果在反应后期,480-500℃温度下,注入一股轻油,进行拉焦处理。拉焦可促进针状焦的单向孔径排列,可确保焦炭全部生成针状焦。
附图说明
32.下面结合附图和实施例对本技术进一步说明。
33.图1是本技术中一种针状焦生产工艺的流程图。
34.图2是本技术中萃取单元的结构示意图。
35.图3是本技术中脱硫单元和焦化单元的结构示意图。
36.附图中
37.101、进料管线
ꢀꢀꢀꢀꢀꢀꢀꢀꢀꢀꢀꢀ
102、沥青分离塔
ꢀꢀꢀꢀꢀꢀꢀꢀꢀꢀꢀꢀꢀꢀꢀ
103、第一分离塔
38.104、第二分离塔
ꢀꢀꢀꢀꢀꢀꢀꢀꢀꢀ
105、管道一
ꢀꢀꢀꢀꢀꢀꢀꢀꢀꢀꢀꢀꢀꢀꢀꢀꢀꢀꢀ
106、管道二
39.107、管道三
ꢀꢀꢀꢀꢀꢀꢀꢀꢀꢀꢀꢀꢀꢀ
108、管道四
ꢀꢀꢀꢀꢀꢀꢀꢀꢀꢀꢀꢀꢀꢀꢀꢀꢀꢀꢀ
109、溶剂循环管一
40.110、换热器一
ꢀꢀꢀꢀꢀꢀꢀꢀꢀꢀꢀꢀ
111、换热器二
ꢀꢀꢀꢀꢀꢀꢀꢀꢀꢀꢀꢀꢀꢀꢀꢀꢀ
112、管道五
41.113、汽提塔一
ꢀꢀꢀꢀꢀꢀꢀꢀꢀꢀꢀ
114、汽提塔二
ꢀꢀꢀꢀꢀꢀꢀꢀꢀꢀꢀꢀꢀꢀꢀꢀꢀ
115、汽提塔三
42.116、溶剂回收管
ꢀꢀꢀꢀꢀꢀꢀꢀꢀ
117、溶剂回收罐
ꢀꢀꢀꢀꢀꢀꢀꢀꢀꢀꢀꢀꢀꢀꢀ
118、溶剂循环管二
43.201、管道六
ꢀꢀꢀꢀꢀꢀꢀꢀꢀꢀꢀꢀꢀꢀ
202、新氢机
ꢀꢀꢀꢀꢀꢀꢀꢀꢀꢀꢀꢀꢀꢀꢀꢀꢀꢀꢀ
203、循氢机
44.204、加热炉一
ꢀꢀꢀꢀꢀꢀꢀꢀꢀꢀꢀ
205、脱硫反应器
ꢀꢀꢀꢀꢀꢀꢀꢀꢀꢀꢀꢀꢀꢀꢀ
206、热分离罐
45.207、冷分离罐
ꢀꢀꢀꢀꢀꢀꢀꢀꢀꢀꢀ
208、胺吸收塔
ꢀꢀꢀꢀꢀꢀꢀꢀꢀꢀꢀꢀꢀꢀꢀꢀꢀ
209、管道七
46.210、管道八
47.301、分馏塔
ꢀꢀꢀꢀꢀꢀꢀꢀꢀꢀꢀꢀꢀ
302、加热炉二
ꢀꢀꢀꢀꢀꢀꢀꢀꢀꢀꢀꢀꢀꢀꢀꢀꢀ
303、第一焦化塔
48.304、第二焦化塔
ꢀꢀꢀꢀꢀꢀꢀꢀꢀꢀ
305、管道九
ꢀꢀꢀꢀꢀꢀꢀꢀꢀꢀꢀꢀꢀꢀꢀꢀꢀꢀꢀ
306、管道十
49.307、加热炉三
ꢀꢀꢀꢀꢀꢀꢀꢀꢀꢀꢀꢀ
308、回流罐
具体实施方式
50.为了使本发明的目的、技术方案进行清楚、完整地描述,及优点更加清楚明白,以下结合附图对本发明实施例进行进一步详细说明。应当理解,此处所描述的具体实施例是本发明一部分实施例,而不是全部的实施例,仅仅用以解释本发明实施例,并不用于限定本发明实施例,本领域普通技术人员在没有做出创造性劳动前提下所获得的所有其他实施例,都属于本发明保护的范围。
51.在本发明的描述中,需要说明的是,术语“中心”、“中”、“上”、“下”、“左”、“右”、“内”、“外”、“顶”、“底”、“侧”、“竖直”、“水平”等指示的方位或位置关系为基于附图所示的方位或位置关系,仅是为了便于描述本发明和简化描述,而不是指示或暗示所指的装置或元件必须具有特定的方位、以特定的方位构造和操作,因此不能理解为对本发明的限制。此外,术语“一”、“第一”、“第二”、“第三”、“第四”、“第五”、“第六”仅用于描述目的,而不能理解为指示或暗示相对重要性。
52.在本发明的描述中,需要说明的是,除非另有明确的规定和限定,术语“安装”、“相连”、“连接”应做广义理解,例如,可以是固定连接,也可以是可拆卸连接,或一体地连接;可以是机械连接,也可以是电连接;可以是直接相连,也可以通过中间媒介间接相连,可以是两个元件内部的连通。对于本领域的普通技术人员而言,可以具体情况理解上述术语在本发明中的具体含义。
53.出于简明和说明的目的,实施例的原理主要通过参考例子来描述。在以下描述中,很多具体细节被提出用以提供对实施例的彻底理解。然而明显的是,对于本领域普通技术人员,这些实施例在实践中可以不限于这些具体细节。在一些实例中,没有详细地描述公知方法和结构,以避免无必要地使这些实施例变得难以理解。另外,所有实施例可以互相结合使用。
54.图1显示了本技术中一种针状焦生产工艺的具体流程,主要包括以下步骤:
55.萃取:通过萃取单元对催化油浆进行溶剂萃取,获得富芳烃油;
56.脱硫:若上述获得的富芳烃油中的硫含量高于0.5wt%,则通过脱硫单元将其中的
硫含量降至0.5wt%以下;
57.焦化:通过焦化单元对含硫量低于0.5wt%的富芳烃油进行焦化处理。
58.对此,由于原料催化油浆的来源不同,而在萃取步骤中对硫的脱除不强烈,由此获得的富芳烃油的硫含量不稳定。由于富芳烃油中硫的存在会抑制针状焦的产生,所以在进行焦化处理时要保证富芳烃油的硫含量低于0.5wt%,优选为0.1-0.3wt%。所以,本技术采用脱硫单元对硫含量高于0.5wt%的富芳烃油进行脱硫处理,避免影响焦化步骤中针状焦的产生。若富芳烃油中的硫含量低于0.5wt%,则无需进行脱硫处理,可以直接送入焦化单元进行焦化处理。
59.其中,本技术中选用的催化油浆应具有以下几个特点:
60.1)芳烃质量分数较高(大于40wt%),尤其2-5环芳烃比例高的催化油浆;
61.2)催化剂颗粒(固含量)低,尽量低至0.5wt%以下,可通过沉降、过滤、离心分离或静电分离等方法预处理达到;
62.3)硫含量低,如果萃取后的富芳烃油硫高于0.5wt%,则需要脱硫单元处理降低硫含量至0.5wt%以下再进入焦化单元,所以为了简化步骤,尽可能选择硫含量低的催化油浆;
63.4)比重大于1.0,越重的催化油浆,生焦率越高。
64.进一步地,图2显示了上述萃取单元的具体结构。如图2所示,所述的萃取单元包括进料管线101、沥青分离塔102、多级分离装置以及汽提回收装置。萃取单元采用超临界萃取及梯级分离方式,根据进料不同,选用不同的溶剂组合,可灵活生产芳烃富集程度不同的产品。溶剂一般采用异丁烷、正丁烷、异戊烷或者相邻二者组合。
65.其中,进料管线101与沥青分离塔102的中部连接,将催化油浆输送至沥青分离塔101 内分离沥青。进料的催化油浆与萃取溶剂在进料管线101内混合,混合比例为1:4-6。在本技术中,沥青分离塔102处于亚临界状态下进行满液操作,即沥青分离塔102的操作压力高于溶剂临界压力,操作温度低于溶剂临界温度。沥青分离塔102中设有进料分布器,以及传统萃取/聚结型内件,促进萃取分离效果。进料在沥青分离塔102中被分离成第一物料和第二物料,第一物料包括溶剂和脱沥青油,第二物料包括沥青和夹带的少量溶剂。
66.在沥青分离塔102中,可以通过变温来调节萃取效果,操作温度高,分离效果好,沥青收率高,脱沥青油收率低并且夹带的沥青和重金属等杂质含量低。反之,操作温度低,沥青收率低,脱沥青油收率高并且夹带的沥青和重金属等杂质含量高。对于固定的溶剂,温度的调节范围一般为
±
0-20℃。
67.在沥青分离塔102的顶部设置有管道一105,管道一105将聚集在沥青分离塔102顶部的第一物料输出。管道一105与管道二106连通,管道一105和管道二106之间设置有换热器一110,管道一105和管道二106分别连接换热器一110的壳程两端。管道二106与多级分离装置连通,用于输送第一物料。多级分离装置包括第一分离塔103,以及至少一个第二分离塔104,可以根据不同的芳烃富集程度不同的产品需求,设置不同数量的第二分离塔104,本技术中以一个第二分离塔104为例,当并不限制本技术。
68.具体地,管道二106的末端与第一分离塔103的中部连接,将第一物料输入该第一分离塔103进行分离。第一物料在换热器一110内进行升温处理,并进一步地在管道二106上设置加热器一对其进行加热,但还是要保持其温度低于溶剂的临界温度。第一分离塔103为
满液操作,且操作温度低于溶剂临界温度,操作压力高于溶剂临界压力,即为亚临界操作状态。升温后的第一物料进入第一分离塔103后持续分离,分离出第三物料和第四物料,其中,第三物料为第一物料中的较轻组分,具体包括溶剂和富烷烃油,第四物料为第一物料中的较重组分,包括富芳烃油和夹带的少量溶剂。
69.在第一分离塔103中,可以通过调节操作温度来控制底部富芳烃油收率。温度高,塔底产品收率高,塔顶产品收率低但杂质少;温度低,塔底产品收率低。塔顶产品收率高但杂质多。操作温度通过进塔前的换热器控制。对于固定的溶剂,本塔调节范围较大,
±
0-30℃。
70.第一分离塔103的顶部设置有管道三107,管道三107用于将聚集在第一分离塔103塔顶的第三物料输出。管道三107与管道四108连通,在管道三107和管道四108之间设置有换热器二111,管道三107与管道四108分别连接换热器111的管程两端。管道四108与第二分离塔104的中部连接,将物料三输送至第二分离塔104内进行进一步的分离。第三物料在换热器二111内进行升温处理,并进一步地在管道四108上设置加热器二对其进行加热,使其进入第二分离塔104后的温度高于溶剂的临界温度,即第二分离塔104内的操作状态为超临界操作状态,此时溶剂处于气液不分的状态,不必通过相变气化溶剂来分离溶剂和油,可通过超临界状态下溶剂与油的密度差将溶剂分离出来,从而节省大量能源。因此,第二分离塔104中的产物为第五物料和第六物料,第五物料具体为溶剂,第六物料包括富集直链烷烃和夹带的少量溶剂。
71.第二分离塔104顶部设置有溶剂循环管一109,用于将聚集在第二分离塔104顶部的第五物料(溶剂)输送出来。溶剂循环管109的末端与进料管线101连通,将溶剂与进料混合并循环利用。溶剂循环管一109依次穿过换热器二111和换热器一110,分别与第三物料和第一物料进行换热,回收循环溶剂中的热能。
72.此外,汽提回收装置包括多个汽提塔,多个汽提塔与沥青分离塔102、第一分离塔103 和第二分离塔104一一对应。在本技术中,汽提塔的具体数量为三个,分为汽提塔一113、汽提塔二114和汽提塔三115。
73.其中,汽提塔一113的中部与沥青分离塔102的底部通过管道五112连接,将聚集在沥青分离塔102底部的第二物料输送至汽提塔一113内。管道五112上设置有加热器三,对第二物料进行加热。第二物料在汽提塔一113内进行过热蒸汽汽提,从而回收溶剂,减少溶剂损失。汽提塔一113采用传统的板式塔,内有塔板。汽提塔一113内分离出的溶剂从汽提塔一113的顶部排出,剩余产品为沥青,从汽提塔一113的底部排出。
74.汽提塔二114的中部与第一分离塔103的底部连接,将聚集在第一分离塔103底部的第四物料输送至汽提塔二114内。在汽提塔二114的输入口处设置有加热器四,对第四物料进行加热。第四物料在汽提塔二114内进行过热蒸汽汽提,从而回收溶剂,减少溶剂的损失。汽提塔二114采用传统的板式塔,内有塔板。汽提塔二114内分离出的溶剂从汽提塔二114 的顶部排出,剩余产品为富芳烃油,从汽提塔二114的底部排出。
75.汽提塔三115的中部与第二分离塔104的底部连接,将聚集在第二分离塔104底部的第六物料输送至汽提塔三115内。在汽提塔三115的输入口处设置有加热器五,对第六物料进行加热。第六物料在汽提塔三115内进行过热蒸汽汽提,从而回收溶剂,减少溶剂的损失。汽提塔三115采用传统的板式塔,内有塔板。汽提塔三115内分离出的溶剂从汽提塔三
115 的顶部排出,剩余产品为富烷烃油,从汽提塔三115的底部排出。
76.来自汽提塔一113、汽提塔二114和汽提塔三115塔顶的溶剂通过溶剂回收管116汇集至溶剂回收罐117。溶剂回收管116上设置有冷却器。溶剂进入溶剂回收罐117后,分离水相和溶剂。在溶剂回收罐117的下方出口设置有溶剂循环管二118,溶剂循环管二118与溶剂循环管一109连通,将回收的溶剂送至前端与进料混合循环利用。
77.在上述技术方案,所述的萃取单元根据相似相溶的萃取原理,可进行多级分离,从而更精准的优化分离生产适合针状焦的原料油。对于不同品质的油浆,即使劣质油浆,也可以实现针状焦生产。
78.图3显示了脱硫单元和焦化单元的具体结构。如图3所示,从汽提塔2底部排出的富烷烃油通过管道六201输送至脱硫单元或焦化单元,即管道六201末端设置有两路管线,若管道六201内的富烷烃油的硫含量高于0.5wt%,则被输送至脱硫单元进行脱硫处理,若管道六 201内的富烷烃油的硫含量低于0.5wt%,则通过管道七209输送至焦化单元。
79.其中,脱硫单元包括依次串联的加热炉一204、脱硫反应器205和热分离罐206。富烷烃油和氢气在加热炉一204的入口处混合形成第七物料,所述第七物料的氢油比为300-800标立氢气/吨油。氢气可以来自新氢机202,也可以来自循氢机203,来自循氢机203的氢气为脱硫单元内回收的氢气,新氢机主要用来补偿反应消耗的氢气,保证反应器操作压力稳定。加热炉一204将上述第七物料加热至反应进料温度,输送至脱硫反应器205的顶部。脱硫反应器为氢精制反应器,是传统的固定床反应器,内置传统的蜡油加氢精制催化剂,通过冷氢控制反应温度。第七物料经过脱硫反应器205精制后,从脱硫反应器205的底部排出,输送至热分离罐206。在热分离罐206内,第七物料中的富烷烃油和氢气分离,富烷烃油从热分离罐206的底部排出,氢气从热分离罐206的顶部排出。热分离罐206的顶部与冷分离罐207 连接,进一步分离氢气中夹带的富烷烃油。冷分离罐207的底部设置有管道八210,管道八 210与热分离罐206的底部连通,用于收集和输送分离出来的富烷烃油。
80.此外,冷分离罐207内分离出的氢气从冷分离罐207的上方排出,夹杂反应生成的少量低碳烷烃,以及h2s、nh3等杂质。冷分离罐207与氨吸收塔208连接,用于去除氢气中的 h2s和nh3等杂质,以及排放一定比例的弛放气,保证氢气纯度80-90mol%。
81.本技术通过设置脱硫单元来控制富烷烃油中的硫含量。若富烷烃油中的硫含量高,不利于针状焦的生成,会促进海绵焦的生成,所以针状焦进料需要将硫含量降至0.5wt%以下,越低越好。但过于低,一是成本太高,二是加氢脱硫会破坏并饱和富芳烃油中的芳烃,所以降至0.3-0.5wt%即可。
82.其次,管道八210与焦化单元中的分馏塔301连通,将富烷烃油输送至分馏塔301内。据此,本技术高度整合和简化了脱硫单元和焦化单元,节省了传统加氢脱硫装置的汽提塔和分馏塔。
83.进一步地,焦化单元还包括焦化塔,焦化塔的顶部与分馏塔201的中部连通,分离塔201 的底部与焦化塔的底部连通,物料在分馏塔201和焦化塔之间循环。
84.具体地,在分馏塔201内,从焦化塔顶来的热油气进入分馏塔201换热段,与来自脱硫单元或萃取单元的低硫富芳烃油直接换热后,冷凝出重馏分油(焦化油)落入塔底,由塔底泵送至加热炉二302和焦化塔。其余大量油气进入塔上部分馏段蒸馏分离。在分馏塔中,从下往上依次分馏出蜡油、柴油、石脑油和富气(c
1-c4)。分馏塔顶的油气经分馏塔顶空冷器
或水冷器冷却到40℃后,流入分馏塔顶回流罐308,罐内分离出的石脑油由泵送至下游吸收稳定工段;分离出的气相送至下游富气压缩机脱硫工段;分离出的水相(酸性水)经泵送出装置去酸性水汽提处理。
85.具体地,分馏塔201塔底焦化油经塔底泵送至加热炉二302。焦化油在炉管内快速升温到500-520℃左右,然后经四通阀进入焦化塔底部。加热炉二302设2-4个注蒸汽点,以加速炉管内流速,减缓炉管内结焦。焦化塔交替操作,可设计为2-4个塔,在本技术中设置为2 个,分别为第一焦化塔303和第二焦化塔304,一个塔生焦,另一个塔清焦,然后切换。焦化油在焦化塔内由于高温并且长时间停留,产生裂解、缩合等一系列反应,最终生成富气、石脑油、柴油、蜡油等产品和针状焦炭。针状焦炭积聚在塔内,高温油气经急冷油急冷后,从焦炭塔顶流入分馏塔底部进行油气分离。与普通石油焦的延迟焦化不同,针状焦的焦化操作压力为0.4-0.5mpag,比石油焦的延迟焦化高0.3-0.4mpa。
86.此外,本技术中的焦化单元还包括管道十306和加热炉三307,管道十306连接分馏塔 301的中部和焦化塔的底部,用于在焦化塔生焦阶段间歇注入轻油,进行拉焦处理。拉焦可促进针状焦的单向孔径排列,可确保焦炭全部生成针状焦。加热炉三304设置在管道十306 上,将轻油加热至480-510℃。轻油可以是分馏塔307内自产的柴油,也可以是其他装置产的柴油。
87.在上述技术方案中,本技术通过向焦化塔内间隙注入轻油,可以提高针状焦的质量。具体地,在焦化塔生焦阶段,塔内进行缩合反应生成焦炭。但传统的焦化装置,即使经过原料预处理,也会有部分焦炭不达标,生成普通的海绵焦。如果在反应后期,480-500℃温度下,注入一股轻油,进行拉焦处理。拉焦可促进针状焦的单向孔径排列,可确保焦炭全部生成针状焦。
88.下面通过列举实施例及对比例对本技术的技术方案进行进一步的说明,但本技术并不限于这些实施例。
89.首先,本技术实施例中催化油浆选用一下四种,其物性参数如表1所示。
90.表1
[0091][0092]
对上述原料进行萃取处理,萃取的操作工艺如表2所示。
[0093]
表2
[0094][0095]
实施例5-8获得的产物主要为沥青及脱沥青油,具体物性如表3-8所示。
[0096]
表3
[0097][0098]
实施例9-10的产物主要为沥青、重脱沥青油和轻脱沥青油,具体物性如表4所示。
[0099]
表4
[0100][0101]
上述产物中脱沥青油的组分如表5所示。
[0102]
表5
[0103][0104][0105]
由上表可知,实施例5-8经过萃取处理后,除硫含量外,其余指标基本上都可以满足针状焦进料要求。通过实施例9-10可看出,脱沥青油,可进一步分离为轻脱沥青油和重脱沥青油,两种油的比重,硫、芳烃、胶质等含量不同,可根据下游需要实现灵活混兑。而针状焦的进料,残碳不能过高,一般控制在3.0wt%左右,低于3.5wt%,所以残碳作为分离指标来控制脱沥青油的收率。
[0106]
下面通过对表5中的含硫量高于0.5wt%的脱沥青油进行加氢脱硫处理,脱硫前后对比如表6所示。
[0107]
表6
[0108][0109]
表6中的进料氢油比为500nm3(氢)/ton(油),氢纯:》90%,氢耗0.05-0.15wt%,催化剂选用石科院加氢脱硫催化剂。由表6可以看出,经过加氢脱硫,硫含量都降低到0.5wt%以下,但芳香分含量基本上损失1-2wt%,芳香分高,有利于生成针状焦,但损失1-2wt%影响不大。
[0110]
下面进行焦化处理。焦化处理的进料及操作参数如表7所示。
[0111]
表7
[0112][0113]
由此获得的产物如表8所示。
[0114]
表8
[0115][0116][0117]
其中,针状焦的物性如表9所示。
[0118]
表9
[0119][0120]
由上表可以看出,没有拉焦处理的针状焦产品,真密度都低于1.35g/cm3,属于不合格产品,而对于硫含量告于0.5wt%的进料,真密度普遍低于1.30g/cm3,质量更差。
[0121]
尽管上面对本技术说明性的具体实施方式进行了描述,以便于本技术领域的技术人员能够理解本技术,但是本技术不仅限于具体实施方式的范围,对本技术领域的普通技术人员而言,只要各种变化只要在所附的权利要求限定和确定的本技术精神和范围内,一切利用本技术构思的申请创造均在保护之列。