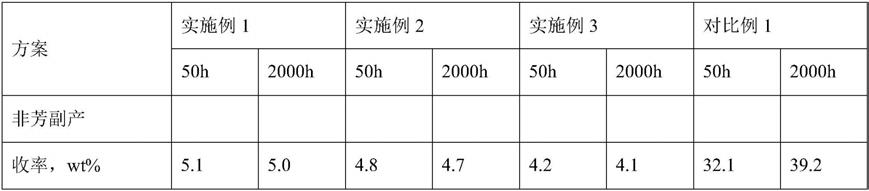
1.本发明涉及石化领域,尤其涉及一种劣质重油加工方法。
背景技术:2.目前,石油资源呈现重质、劣质化趋势,世界范围内重劣质原油产量逐年增加,重劣质原油的加工比例日益增大,迫切需要增大重劣质原油的加工能力,尤其是渣油加工能力。
3.渣油是石化行业炼油厂一次加工装置减压蒸馏所得的残余油,故称减压渣油;有时也将从常压蒸馏塔底所得的重油称为常压渣油。我国所产原油中减压渣油的含量较高,大于500℃减压渣油的产率一般为40%~50%。2019年,全国原油加工量65198.1万吨,减压渣油约为3亿吨。
4.原油资源重质化的趋势,对重质油加工技术的提出了新要求。近年来,国内外炼油技术开发机构在固定床渣油加氢处理、沸腾床加氢裂化、悬浮床加氢裂化技术的工业应用方面做了大量的工作。目前,固定床渣油加氢技术仍是渣油加工主要工业应用技术,但其存在原料适应性差的缺陷;为适应原料劣质化趋势,加工更劣质的重油,沸腾床、悬浮床加氢裂化技术均已得到了工业应用,但此两者存在装置保运成本高、投资大、投资回报周期长的问题。
5.加氢裂化尾油,一般指是炼油厂加氢裂化装置>350℃馏分。bmci低的加氢裂化尾油可用作蒸汽裂解制乙烯原料,bmci高的尾油用作催化裂化进料。对于一些小型炼油厂来说,如果没有乙烯裂解和催化裂化装置,那么结合重芳烃油加以利用,则可以提高加氢裂化尾油的经济性。
6.重芳烃油主要来源于催化重整、乙烯裂解装置。长期以来重芳烃资源没有得到充分利用,除少量用作溶剂和提取c9、c
10
单体芳烃外,其余基本均掺入劣质燃料中烧掉。随着我国环保法规日益完善,掺混、烧掉将受到限制。因此,如何有效利用这些重芳烃资源,将其转化为btx(苯、甲苯、二甲苯),已成为国内外芳烃技术领域的重要课题之一。
7.对劣质重油进行加氢处理过程中,需要用到加氢保护催化剂,以保护下游主催化剂的活性稳定性,有关加氢保护催化剂的专利较多。专利cn102989491b公开了一种重油加氢保护催化剂及其制备和应用方法,氧化物硅铝载体孔容为0.98-1.15ml/g,比表面340-380m2/g。专利cn103285935b公开了的加氢保护催化剂,其载体含有α-氧化铝,载体的孔容为0.5-0.75ml/g,比表面积为2-20m2/g,添加含硅、磷,碱或碱土金属中的一种或几种作为助剂组分。专利cn108421548b采用浸渍法将加氢金属活性组分的水溶性盐和有机络合剂负载到载体上,对半成品催化剂进行浸渍后,进行干燥且不进行焙烧,此加氢保护催化剂脱金属率为96%。专利cn2019109383971中的加氢保护催化剂包括金属活性组分和载体,所述载体主要由富勒烯、萘与氧化铝经混合、挤条成型及干燥、焙烧形成。专利cn1107102c选用田菁粉或炭黑等物质作为扩孔剂,加入量为1.5-5.5wt%。常规物理扩孔剂添加至载体中会导致载体孔分布弥散,大孔部分不能形成连续贯穿的孔道,孔道形状为孔口较小、孔腔较大,
这样的孔道会使催化剂的机械强度降低。
技术实现要素:8.为了解决上述技术问题,本发明提供了一种劣质重油加工方法,通过本发明方法可使劣质重油得到完全利用的同时,所得混合芳烃产品收率高,杂质含量少。
9.本发明的具体技术方案为:一种劣质重油加工方法,包括以下步骤:先将劣质重油和重芳烃油混合,蒸馏分出轻馏分和重馏分;所述轻馏分通过装填有选择性加氢精制催化剂和加氢保护催化剂的选择性加氢精制反应器进行选择性加氢精制生产混合芳烃产品;所述重馏分作为延迟焦化进料。
10.本发明将劣质重油——渣油和加氢裂化尾油与重芳烃油混合,利用重芳烃油中芳烃对渣油和加氢裂化尾油中芳烃的溶解力,经蒸馏,使后两者中的芳烃富集到了轻馏分中,此轻馏分再经本发明的加氢保护催化剂和选择性加氢催化剂的催化作用,生产出产率高、杂质含量少的混合芳烃,作为下游重整装置或制萘装置的进料,可显著提高劣质重油和重芳烃油结合经济性。
11.所述加氢保护催化剂包括金属氧化物活性组分和负载所述金属氧化物活性组分的氧化铝载体;所述金属氧化物为钼和镍的氧化物;加氢保护催化剂的比表面积为50~100m2/g,孔容0.3~0.5ml/g。
12.本发明的加氢保护催化剂具有更好的孔容,具有连续贯穿的孔道,可使催化剂容垢更多的杂质、垢物,可更好地保护下游主催化剂的活性稳定性。
13.作为优选,所述劣质重油包括石油化工行业的常、减压渣油或加氢裂化装置尾油等;所述重芳烃油包括但不限于生产三苯产品过程的重芳烃副产。
14.作为优选,所述劣质重油和重芳烃油的质量比为1∶1~3。
15.作为优选,所述蒸馏为常压蒸馏,切割温度为250℃,即<250℃为轻馏分,>250℃为重馏分。
16.作为优选,所述轻馏分的选择性加氢精制的工艺条件为:体积空速为0.3~1.0h-1
,系统反应压力氢分压为4.0~6.0mpa,反应温度为340~360℃,氢油比为500~1000∶1。
17.作为优选,所述加氢保护催化剂和选择性加氢精制催化剂的装填体积比为1∶2~3;所述选择性加氢精制催化剂为重苯萘选择性加氢精制生产精萘的催化剂。
18.作为优选,所述加氢保护催化剂包括70~95wt%的载体、1~8wt%的金属氧化物活性组分;其中氧化钼占1.0~5.0w%,氧化镍占1.0~5.0w%。
19.作为优选,所述加氢保护催化的制备方法为:(1)将拟薄水铝石与蒽、助挤剂混合均匀,得到混合物;(2)将胶溶酸溶液加入至所述混合物中,经混捏、干燥得到氧化铝载体前体;(3)将硅溶胶与所述氧化铝载体前体混合,经定型、干燥、焙烧得到氧化铝载体;(4)向金属氧化物活性组分的前驱体水溶液中加入非离子表面活性剂以形成混合液,之后将氧化铝载体浸渍于所述混合液中,之后进行干燥、焙烧处理,获得加氢保护催化剂。
20.首先,本发明的加氢保护催化剂采用有机化合物——蒽作为扩孔剂,利用其特性使其在载体焙烧过程中,经历先变成气体再最终燃尽为碳的过程,不同于其它常规物理扩
孔剂如炭黑、纤维素等的造孔过程,蒽在沸点时,先变成气体从载体中缓慢逸出,此时可形成众多的一次孔道;随着温度的升高,最终燃尽变成为碳,又可形成较多的二次孔道。两次成孔的效果,在加入量与常规物理扩孔剂相比没有增多的前提下,使其拥有更好的扩孔效果,可形成连续贯穿的孔道,可以容垢更多的杂质、垢物。如此,一方面避免了常规物理扩孔剂因加入量大,燃尽时形成的颗粒大,而导致载体机械强度下降的问题;另一方面,可更好地保护下游主催化剂的活性稳定性。
21.作为优选,步骤(1)中:所述蒽的加入量为氧化铝载体重量的3.1~5.0%。
22.作为优选,步骤(1)中:所述助挤剂为淀粉、田菁粉、聚乙烯醇、甲基纤维素和聚乙二醇中的一种或几种,以各组分总重量为准,其添加量为2~10wt%。
23.作为优选,步骤(2)中:所述胶溶酸为硝酸、磷酸、柠檬酸、盐酸和乙酸中的一种或多种;所述胶溶酸溶液的温度为40~80℃,加入速度5~10g/min。
24.作为优选,步骤(2)中:所述干燥的温度为100~130℃,干燥时间为5~10h。
25.作为优选,步骤(3)中:所述定型为挤成10-15mm等高径比的圆柱条形;所述干燥的温度为100~140℃;所述焙烧的温度为500~700℃,焙烧时间为5~10h。
26.作为优选,步骤(4)中:所述金属氧化物活性组分的前驱体水溶液中的金属氧化物活性组分的前驱体包括硝酸镍、碱式碳酸镍中的任意一种和钼酸铵和的组合;前驱体水溶液中金属离子的浓度为5~40g/100ml。
27.作为优选,步骤(4)中:所述非离子表面活性剂的加入量为氧化铝载体的2~10wt%。
28.作为优选,步骤(4)中:所述浸渍的时间为5~10h;所述干燥的温度为100~150℃;所述焙烧的温度为400~600℃,焙烧时间为3~10h。
29.与现有技术相比,本发明具有以下技术效果:(1)本发明将劣质重油——渣油和加氢裂化尾油与重芳烃油混合,利用重芳烃油中芳烃对渣油和加氢裂化尾油中芳烃的溶解力,经蒸馏使后两者中的芳烃,富集到了轻馏分中,此轻馏分再经本方法加氢保护催化剂和重苯萘选择性加氢催化剂的催化作用,生产出产率高、杂质含量少的混合芳烃,作为下游重整装置或制萘装置的进料,显著提高了劣质重油和重芳烃油结合经济性。
30.(2)本发明的加氢保护催化剂采用有机化合物——蒽作为扩孔剂,利用其特性使其在载体焙烧过程中,经历先变成气体再最终燃尽为碳的过程,不同于其它常规物理扩孔剂如炭黑、纤维素等的造孔过程,蒽在沸点时,先变成气体从载体中缓慢逸出,此时可形成众多的一次孔道;随着温度的升高,最终燃尽变成为碳,又可形成较多的二次孔道。两次成孔的效果,在加入量与常规物理扩孔剂相比没有增多的前提下,使其拥有更好的扩孔效果,可形成连续贯穿的孔道,可以容垢更多的杂质、垢物。如此,一方面避免了常规物理扩孔剂因加入量大,燃尽时形成的颗粒大,而导致载体机械强度下降的问题;另一方面,可更好地保护下游主催化剂的活性稳定性。
31.(3)本发明为附加值较低的渣油、加氢尾油和重芳烃油提供了一种原料利用率高、产品性质好、综合经济性好的方法和一种加氢保护催化剂,对炼厂减排增效非常有益。
具体实施方式
32.下面结合实施例对本发明作进一步的描述。
33.总实施例一种劣质重油加工方法,包括以下步骤:先将质量比为1∶1~3的劣质重油(包括石油化工行业的常、减压渣油或加氢裂化装置尾油等)和重芳烃油(包括但不限于生产三苯产品过程的重芳烃副产)混合,常压蒸馏分出轻馏分和重馏分。常压蒸馏的切割温度为250℃,即<250℃为轻馏分,>250℃为重馏分。
34.所述轻馏分通过装填有体积比为2~3∶1的选择性加氢精制催化剂(重苯萘选择性加氢精制生产精萘的催化剂,如zl201810201010.x公开的催化剂,命名为1010c)和加氢保护催化剂的选择性加氢精制反应器进行选择性加氢精制生产混合芳烃产品。选择性加氢精制的工艺条件为:体积空速为0.3~1.0h-1
,系统反应压力氢分压为4.0~6.0mpa,反应温度为340~360℃,氢油比为500~1000∶1。
35.所述重馏分作为延迟焦化进料。
36.其中:所述加氢保护催化剂包括1~8wt%的金属氧化物活性组分(氧化钼1.0~5.0w%,氧化镍1.0~5.0w%)和70~95wt%的氧化铝载体;所述金属氧化物为钼和镍的氧化物;加氢保护催化剂的比表面积为50~100m2/g,孔容0.3~0.5ml/g。
37.所述加氢保护催化的制备方法为:(1)将拟薄水铝石与蒽、助挤剂混合均匀,得到混合物。所述蒽的加入量为氧化铝载体重量的3.1~5.0%。所述助挤剂为淀粉、田菁粉、聚乙烯醇、甲基纤维素和聚乙二醇中的一种或几种,以各组分总重量为准,其添加量为2~10wt%。
38.(2)将40~80℃的胶溶酸溶液以加入速度5~10g/min加入至所述混合物中,经混捏、100~130℃干燥5~10,得到氧化铝载体前体。所述胶溶酸为硝酸、磷酸、柠檬酸、盐酸和乙酸中的一种或多种。
39.(3)将硅溶胶与所述氧化铝载体前体混合,挤成10-15mm等高径比的圆柱条形,00~140℃干燥、500~700焙烧5~10h,得到氧化铝载体。
40.(4)向金属氧化物活性组分的前驱体水溶液(包括金属氧化物活性组分的前驱体包括硝酸镍、碱式碳酸镍中的任意一种和钼酸铵和的组合,金属离子的浓度为5~40g/100ml)中加入氧化铝载2~10wt%的非离子表面活性剂以形成混合液,之后将氧化铝载体浸渍于所述混合液中5~10h,之后100~150干燥、400~600℃焙烧处理3~10h,获得加氢保护催化剂。
41.具体实施例加氢保护催化剂c1的制备:取60g拟薄水铝石,加入蒽1.5g、3g田菁粉(助挤剂),混合均匀;于60℃滴加含硝酸(浓度为60%)的水溶液,滴加速度10g/min,混捏,加入量以满足将前述三种物质混合均匀为准,于100℃干燥5h,制得氧化铝载体前体;将硅溶胶与此氧化铝载体前体混合,加入量以满足成型为准,挤成12mm等高径比的圆柱条形,于140℃干燥2h,然后500℃焙烧10h,制成氧化铝载体。再用含有十二脂肪醇聚氧乙烯醚、钼酸铵、碱式碳酸镍的浸渍液(两金属离子浓度均为10g/100ml)等体积浸渍上述载体7.5h,然后于125℃干燥3h,500℃焙烧10h。催化剂最终组成为:氧化钼5.0wt%、氧化镍2.5wt%,余量氧化铝;催化
剂比表面积80m2/g,孔容0.40ml/g。如此制得加氢保护催化剂c1。
42.加氢保护催化剂c2的制备:取72g拟薄水铝石,加入蒽5.0g、8.2g田菁粉(助挤剂),混合均匀;于80℃滴加含柠檬酸(浓度为40%)的水溶液,滴加速度6.5g/min,混捏,加入量以满足将前述三种物质混合均匀为准,于130℃干燥10h,制得氧化铝载体前体;将硅溶胶与此氧化铝载体前体混合,加入量以满足成型为准,挤成12mm等高径比的圆柱条形,于100℃干燥3h,然后700℃焙烧5h,制成氧化铝载体。再用含有十二脂肪醇聚氧乙烯醚、钼酸铵、硝酸镍的浸渍液(两金属离子浓度均为5g/100ml)等体积浸渍上述载体5h,然后于100℃干燥4h,600℃焙烧3h。催化剂最终组成为:氧化钼2.8wt%、氧化镍3.6wt%,余量氧化铝;催化剂比表面积95m2/g,孔容0.32ml/g。如此制得加氢保护催化剂c2。
43.加氢保护催化剂c3的制备:取66g拟薄水铝石,加入蒽3.4g、6g田菁粉(助挤剂),混合均匀;于80℃滴加含乙酸(浓度为50%)的水溶液,滴加速度5.0g/min,混捏,加入量以满足将前述三种物质混合均匀为准,于115℃干燥7.5h,制得氧化铝载体前体;将硅溶胶与此氧化铝载体前体混合,加入量以满足成型为准,挤成12mm等高径比的圆柱条形,于120℃干燥4h,然后600℃焙烧7.5h,制成氧化铝载体。再用含有十二脂肪醇聚氧乙烯醚、钼酸铵、硝酸镍的浸渍液(两金属离子浓度均为8g/100ml)等体积浸渍上述载体10h,然后于150℃干燥2h,400℃焙烧6.5h。催化剂最终组成为:氧化钼1.9wt%、氧化镍4.0wt%,余量氧化铝;催化剂比表面积68m2/g,孔容0.48ml/g。如此制得加氢保护催化剂c3。
44.加氢保护催化剂c4的制备:与加氢保护催化剂c3的区别仅在于将蒽替换为萘。加氢保护催化剂c4的比表面积155m2/g,孔容0.26ml/g。
45.以下实施例中所用重芳烃油采用裂解c
9+
重芳烃原料油,此原料以c9及以上芳烃为主,组成一般为c
8-芳烃、c9芳烃、c
10+
芳烃及萘及衍生物,总芳烃约74.7%,胶质5.1mg/100g,双烯6.1gi2/100g。
46.又及,在如下实施例中,实施例1和实施例2所用的劣质重油为减压渣油,其与重芳烃油混合质量比为1∶1.5;实施例3所用劣质重油为加氢裂化尾油,其与重芳烃油质量比为1∶2。所用减压渣油和加氢裂化尾油性质列于表1。
47.上述劣质重油和重芳烃油混合后,进行常压蒸馏,均以250℃为切割点,得到初馏~250℃的轻馏分和>250℃的重馏分;轻馏分进入选择性加氢精制反应器,自上而下接触所述的加氢保护催化剂和选择性加氢精制催化剂1010c,各实施例工艺条件列于表2;反应经过50h和2000h后,非芳副产和最终所得混合苯类和混合萘类产品性质的结果均列于表3。
48.选择性加氢精制产物经气液分离后,以220℃为蒸馏切割点,得到混合芳烃产品和非芳副产,后者可以和重馏分一起作为延迟焦化装置进料;混合芳烃再蒸馏,分出初馏~200℃的混合苯类和>200℃混合萘类两种产物,分别作为重整装置和精萘装置理想的进料。
49.另需说明的是,如下实施例所采用的各种反应参与物及工艺条件均是较为典型的范例,但经过本案发明人大量试验验证,于上文所列出的其它类型的反应参与物及其它工艺条件也均是适用的,并也均可达成本发明所声称的技术效果。
50.实施例1:采用加氢保护催化剂c1和选择性加氢精制催化剂1010c,装填体积比为1∶2。
51.实施例2:采用加氢保护催化剂c2和选择性加氢精制催化剂1010c,装填体积比为1∶3。
52.实施例3:采用加氢保护催化剂c3和选择性加氢精制催化剂1010c,装填体积比为1∶2。
53.对比例1:采用加氢保护催化剂c4和选择性加氢精制催化剂1010c,装填体积比为1∶2。
54.表1-劣质重油性质原油名称减压渣油加氢裂化尾油密度(20℃),kg
·
m-3
919.2842.0s,μg
·
g-1
12400562n,μg
·
g-1
2200210残碳ccr4.2-金属含量,μg
·
g-1
ꢀꢀ
ni+v53-fe10-bmci-12.7馏程,℃ ibp/10%/30%/50%228/336/407/463249/-/350(13.5%)70%/90%/95%/ebp500(61%)-/-表2-选择性加氢精制反应条件方案实施例1实施例2实施例3对比例1工艺条件
ꢀꢀꢀꢀ
氢分压,mpa5.04.06.06.0反应温度,℃360340350350空速,h-1
0.650.31.01氢油体积比7501000500500表3-非芳副产、混苯和混萘产品性质
本实施例中,非芳副产、混苯、混萘产品的收率均是以混合进料(即按比例混合的劣质重油和重芳烃油混合物)计算得到的。
55.由表3可以看到,采用劣质重油和重芳烃油混合后,蒸馏出轻馏分再经选择性加氢精制反应,所得最终产物混合芳烃收率高达76.0%以上,混苯和混萘产品中三苯含量和萘含量均超过85%,且两产品的硫质量很低,是理想的重整装置和精萘装置进料,可有效降低下游装置的加工成本,显著提升了劣质重油和重芳烃油的经济性,体现了本发明加氢保护催化剂良好的脱除杂质能力和活性稳定性。
56.此外,采用萘为扩孔剂的对比例1,所制得的催化剂保护下游主催化剂的活性差,活性稳定性更差,无法达到本发明同一水平的效果。分析其原因主要在于:1、萘是利用其易升华的特征作扩孔剂,而蒽是利用其沸点挥发的特性,两者造孔机理不同;2、两者分子大小不同,萘明显小于蒽,这对于两者扩孔效果有实质性的影响。
57.本发明中所用原料、设备,若无特别说明,均为本领域的常用原料、设备;本发明中所用方法,若无特别说明,均为本领域的常规方法。
58.以上所述,仅是本发明的较佳实施例,并非对本发明作任何限制,凡是根据本发明技术实质对以上实施例所作的任何简单修改、变更以及等效变换,均仍属于本发明技术方案的保护范围。