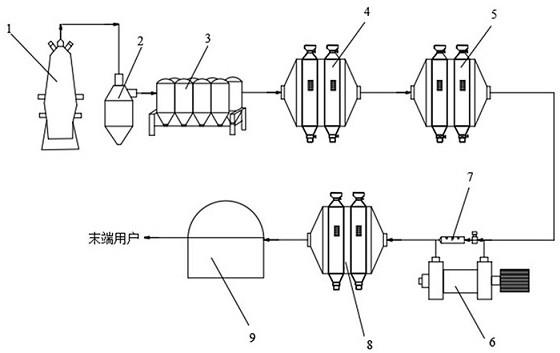
1.本发明涉及资源综合利用技术领域,特别涉及一种基于超细化钢渣的高炉煤气脱酸剂及其制备方法和脱酸系统。
背景技术:2.高炉煤气作为生铁冶炼过程中副产的可燃性气体,具备可观的压力、温度和热值,是一种重要的二次能源。为了响应国家推进节能减排、发展循环经济的号召,钢铁企业正在大力发展高炉煤气的干法除尘工艺以及余压余热发电技术。但是,干法除尘后的高炉煤气中仍存在大量的h2s、hcl等酸性气体。在煤气输送与使用过程中,这些酸性气体会与冷凝的水蒸气形成酸液,会严重腐蚀设备管道、导致trt叶片积盐结垢、热风炉格子砖蓄热效率降低等问题,严重影响了余压余热回收装置的正常运转。另一方面,这些酸性气体(尤其是hcl)会富集并占据后端水解催化剂表面的碱性位点,降低催化剂对高炉煤气中有机硫的水解活性,从而导致后端高炉煤气用气点的烟气中so2无法达到国家要求的超低排放指标,额外增加后续脱硫成本。因此,对高炉煤气中进行脱酸处理已经势在必行。
3.目前,国内外针对高炉煤气中酸性气体的脱除工艺主要分为湿法和干法。湿法工艺是采用碱液喷淋的形式脱除煤气中的酸性气体,虽可以有效降低煤气中的酸性组分,但碱液也会造成管道和设备的腐蚀、结垢堵塞,同时带来脱酸废液处理问题,并在很大程度上抵消了干法除尘的节水、利用煤气显热等优势。干法工艺则是利用固体脱酸剂与煤气中的酸性气体进行化学反应,将其固定在脱酸剂上,从而达到酸性气体脱除的目的。采用干法的方式,不喷水,不降温,无废液处置问题,最大限度保留干法除尘带来的节能环保效益,还能解决包括trt在内的所有设备及管网的腐蚀或积盐结垢问题,具有较大应用潜力。但是由于高炉煤气存在煤气量大,煤气温度较低,co2、水蒸气和粉尘含量都比较高的特点,现有的常规脱酸剂不能同时满足脱酸效果和经济性两方面的指标。针对高炉煤气脱酸,目前尚缺少成本低廉,性能优良的脱酸剂。因此,研发一种低成本且高效脱除高炉煤气中酸性组分的脱酸剂具有很大的工业应用价值。
4.钢渣是钢铁冶炼过程中产生的固体废弃物。随着钢铁行业的蓬勃发展,钢铁产能逐渐提高,相应的排放的钢渣也逐渐增多,据报道我国每年产生大约2亿吨的钢渣,但是其综合利用率不到30%,这就造成了大量钢渣堆存地表,不但占用耕地,而且污染环境。因此寻找一种合理、有效地将工业固废进行再利用的途径已经迫在眉睫。钢渣主要由氧化钙40%~60%,二氧化硅13%-20%,氧化镁3%~10%,金属铁2%~8%,氧化铝2%~8%,氧化锰1%~5%等组成,利用钢渣富含碱性氧化物的特点,可用于烟气中so2的脱除。中国专利cn 108295806 b公开了一种利用工业固废制备脱硫吸附剂的方法,所制备的脱硫吸附剂使用简单,而且可重复利用;由于制备原料中加入了工业废钢渣和废玻璃,增强了脱硫吸附剂的强度,提高耐磨性,并显著降低脱硫吸附剂的生产成本。目前,利用钢渣脱除烟气中so2的报道较多,却鲜有关于利用钢渣进行煤气脱酸剂的报道。
5.钢渣中具有较高含量的f-cao和f-mgo,这两者在遇水后一方面会生成具有呈强碱
性的ca(oh)2和mg(oh)2,可以与酸性气体如hcl、h2s发生酸碱中和反应,另一方面,f-cao和f-mgo遇水后体积会增大1-3倍,形成疏松结构,加速非均相反应的发生。受此启发,利用钢渣作为原材料制备高炉煤气脱酸剂,可以实现高炉煤气中酸性气体脱除,可有效避免酸性物质对后续设备管道的腐蚀及催化剂的影响。因此,本发明提供的一种基于超细化钢渣制备高炉煤气脱酸剂的方法,不仅有效的利用了工业固废钢渣,解决了固废污染问题以及缓解了大气污染问题,而且给钢铁企业带来了巨大的经济效益,符合国家“资源-产品-废弃物-再生资源”的发展模式。
技术实现要素:6.本发明提供一种基于超细化钢渣的高炉煤气脱酸剂及其制备方法和脱酸系统,解决目前高炉煤气脱酸剂存在的制备工艺复杂、成本高昂、不适合应用于高炉煤气脱酸领域的问题。
7.为解决上述技术问题,本发明的技术方案为:一种基于超细化钢渣的高炉煤气脱酸剂,按重量份数计,由以下组分制成:氢氧化钙20~65份,钢渣10~40份,活性组分5~15份,改性剂5~15份,发泡剂5~10份及粘结剂5~15份。
8.其中,所述钢渣来自于钢铁企业在炼钢生产中产生的废弃物,为精炼渣、转炉渣和电炉渣中的一种或多种。
9.其中,所述活性组分为硝酸锌和硝酸铝中的一种或两种;所述改性剂为氢氧化钠、碳酸钠、碳酸氢钠和尿素中的一种或两种;所述发泡剂为甲基纤维素。
10.一种高炉煤气脱酸剂的制备方法,包括下述步骤:步骤1,将钢渣由上而下进料于湿磨机中,与水混合后,湿磨20~60分钟形成钢渣浆体;步骤2,将活性组分溶解于水中,将形成的均一溶液与氢氧化钙20~65份加入到步骤1的钢渣浆体中,湿磨10~30分钟,形成混合物a;步骤3,将改性剂溶解于水中,将形成的均一溶液缓慢滴加到步骤2形成的混合物a中,保持边滴边搅拌,滴加完毕后继续搅拌15~30分钟,之后将形成的混合物置于高压反应釜中,于恒温鼓风干燥箱中150~200
°
c下反应2-8小时;反应结束后取出自然冷却,过滤,得到膏状固体混合物b;步骤4,将发泡剂及粘结剂置于步骤3得到的混合物b中,搅拌均匀后,挤出成型,得到成型物料;步骤5,将步骤4所得成型物料放入恒温鼓风干燥箱中,于80~150
°
c下干燥2~8小时,得到初级产品;步骤6,将步骤5干燥后的初级产品放入马弗炉中,于300~500℃下,焙烧1~4小时,然后自然冷却到室温,得到高炉煤气脱酸剂。
11.其中,所述步骤1中钢渣与水的重量比为(10~40):(20~90);所述步骤2中活性组分与水的重量比为(5~15):(10~40);所述步骤3中改性剂与水的重量比为(5~15):(10~40)。
12.一种采用上述高炉煤气脱酸剂的脱酸系统,包括依次相连的高炉、重力除尘装置、
布袋除尘器、脱酸塔、水解塔、减压阀组、脱硫塔和高炉煤气柜,所述减压阀组与trt余压发电装置连接;所述脱酸塔包括呈圆筒状的塔体,所述塔体的进气侧连接有进气变径锥,所述进气变径锥连接煤气入口管道,所述塔体的出气侧连接有出气变径锥,所述出气变径锥连接有煤气出口管道,所述进气变径锥与所述塔体的连接处设有进气流均布装置,所述出气变径锥与所述塔体的连接处设有出气流均布装置,所述塔体内竖直设有用于高炉煤气脱酸的反应仓,所述反应仓内部装填有所述高炉煤气脱酸剂;所述脱酸塔顶部设置有高炉煤气脱酸剂的进料口和进料切断阀,所述脱酸塔底部设置有高炉煤气脱酸剂的卸料口和卸料切断阀,所述进料切断阀下方设有进料仓,所述进料仓位于所述塔体的顶壁上方,所述卸料切断阀的上方设有锥形料斗,所述锥形料斗位于所述塔体的底壁下方,所述反应仓的进气侧和出气侧分别设有整流格栅。
13.其中,所述反应仓为两个,分别为用于粗脱酸的一级反应仓和用于精脱酸的二级反应仓,所述进气流均布装置与所述一级反应仓之间构成第一气体整流层,所述一级反应仓和所述二级反应仓之间构成第二气体整流层,所述二级反应仓与所述出气流均布装置之间构成第三气体整流层。
14.其中,所述脱酸塔中间设置检修口;所述煤气入口管道上设有进气压力表和进气体抽检装置,所述煤气出口管道上设有出气压力表和出气体抽检装置,所述脱酸塔中间设有检修口。进气压力表用于检测煤气入口管道中气体的压力,出气压力表用于检测煤气出口管道中气体的压力,进气体抽检装置和出气体抽检装置用于检测煤气脱酸前后高炉煤气中酸性气体如hcl和h2s的浓度。
15.根据所述气体抽检装置的示数来判断脱酸塔中的脱酸剂是否需要更换。若出气抽检装置中显示hcl的浓度大于10mg/nm3时,则表示脱酸剂已失效,需要更换新的脱酸剂。
16.其中,高炉煤气脱酸剂的外观为蜂窝状、四叶草状、空心球状或空心柱状,将其用于高炉煤气精脱硫工艺前端的煤气预处理段,用于脱除高炉煤气中的酸性气体如hcl、h2s等。所述脱酸塔内脱酸剂的使用压力210~230kpa,使用温度120~180℃,煤气通过脱酸塔的空速在1000~3000h-1
,床层失效条件为脱酸塔后煤气中hcl浓度大于10mg/nm3。
17.高炉煤气和脱酸剂采用错流方式布置。所述的错流方式,指的是高炉煤气的流动方向和高炉煤气脱酸剂的流动方向是垂直的。具体而言,在脱酸过程中,高炉煤气从所述脱酸塔一侧的煤气入口管道进入脱酸塔内部完成脱酸,脱酸后的煤气从脱酸塔另一侧的煤气出口管道流出,气体的流动方向为水平。在所述脱酸塔中,脱酸剂从脱酸塔顶部的进料口经过进料仓进入脱酸塔内部,使用一段时间后,失效后的脱酸剂经过脱酸塔底部的卸料口排出脱酸塔,高炉煤气脱酸剂的流动方向为竖直。所述的这种错流方式的益处在于:一方面可以最大限度地降低脱酸前后的煤气压力损失(<500pa/m),保证后端trt余压发电装置的运行不受影响;另一方面,采用错流方式的脱酸塔占地面积小,小身量,起大作用,非常适合脱酸场地有限的空间使用。
18.本发明提供的技术方案,与现有技术相比,具有以下有益效果:
①
本发明所涉及的高炉煤气脱酸剂的制备方法简单,脱酸容量高,使用寿命长;由于制备原料中加入了工业固废,显著降低脱酸剂的生产成本,提高了脱酸剂的强度,解决了工业固废污染环境及浪费资源的问题。
19.②
本发明所涉及的脱酸剂采用的湿法细磨联合水热的制备方法制得,一方面促
进了钢渣中cao充分水化生成ca(oh)2等活性脱酸组分,同时促使钢渣内部成了大量的晶格缺陷,提高了活性组分在晶格内部的分散度,改善了脱酸性能。另一方面,钢渣湿法细磨过程提高了其中胶凝性成分的分散度,从而改善了脱酸剂的整体机械强度。
20.③
本发明所涉及的脱酸剂在制备过程中通过加入改性剂,提高了脱酸剂表面碱性活性中心的数量,从而可以显著改善脱酸剂的脱酸性能。
21.④
本发明所涉及的脱酸剂及脱酸系统使用在高炉煤气水解系统前,可以有效保护后端水解剂免受毒化,显著提高水解剂的使用寿命,同时减少后续设备腐蚀及满足后端用户so2的超低排放要求;
⑤
本发明所涉及的整个脱酸系统无废水排放,不会增加煤气含水率,不会降低煤气热值,不影响后续trt发电。
22.⑥
本发明所涉及的错流式脱酸系统,一方面可以最大限度地降低脱酸前后煤气的压力损失(<500pa/m),保证后端trt余压发电装置的运行不受影响;另一方面,整个脱酸系统占地面积小,非常适合脱酸场地有限的空间使用。
附图说明
23.图1为本发明中脱酸系统的工艺流程图;图2为本发明中脱酸塔侧视的结构示意图;图3为本发明中脱酸塔俯视的结构示意图;图中,1、高炉;2、重力除尘装置;3、布袋除尘器;4、脱酸塔;5、水解塔;6、trt余压发电装置;7、减压阀组;8、脱硫塔;9、高炉煤气柜;41.塔体,42.进气变径锥,43.煤气入口管道,44.出气变径锥,45.煤气出口管道,46.进气流均布装置,47.出气流均布装置,48.反应仓,49.进料口,410.进料切断阀,411.卸料口,412.卸料切断阀,413.进料仓,414.锥形料斗,415.整流格栅,416.第一气体整流层,417.第二气体整流层,418.第三气体整流层,419.检修口,420.进气压力表,421.进气体抽检装置,422.出气压力表,423.出气体抽检装置。
具体实施方式
24.下面将结合本发明具体实施例,对本发明的技术方案进行清楚、完整地描述,显然,所描述的实施例仅是本发明的一部分实施例,而不是全部的实施例。基于本发明中的实施例,本领域普通技术人员在没有做出创造性劳动前提下所获得的所有其他实施例,都属于本发明保护的范围。
25.实施例1本实施例提供一种基于超细化钢渣的高炉煤气脱酸剂,按重量份数计,由以下成分组成:氢氧化钙40份,钢渣25份,硝酸锌10份,氢氧化钠10份,甲基纤维素5份及膨润土10份。
26.其中,所述钢渣来自于钢铁企业在炼钢生产中产生的废弃物,为精炼渣。
27.本实施例提供了上述高炉煤气脱酸剂的制备方法,包括下述步骤:步骤1,按重量份计,将25份钢渣由上而下进料于湿磨机中,与55份水混合后,湿磨40分钟形成钢渣浆体;步骤2,按重量份计将硝酸锌10份溶解于25份水中,将形成的均一溶液与氢氧化钙
40份加入到步骤1的钢渣浆体中,湿磨20分钟,形成混合物a;步骤3,按重量份计将氢氧化钠10份溶解于25份水中,将形成的均一溶液缓慢滴加到步骤2形成的混合物a中,保持边滴边搅拌,滴加完毕后继续搅拌20分钟,之后将形成的混合物置于高压反应釜中,于恒温鼓风干燥箱中180
°
c下反应6小时;反应结束后取出自然冷却,过滤,得到膏状固体混合物b;步骤4,按重量份计将甲基纤维素5份及膨润土10份置于步骤3得到的混合物b中,搅拌均匀后,挤出成型,得到成型物料;步骤5,将步骤4所得成型物料放入恒温鼓风干燥箱中,于100
°
c下干燥5小时,得到初级产品;步骤6,将步骤5干燥后的初级产品放入马弗炉中,于400℃下,焙烧2.5小时,然后自然冷却到室温,得到高炉煤气脱酸剂。
28.本实施例采用上述高炉煤气脱酸剂的脱酸系统,如图1-图3所示,包括依次相连的高炉1、重力除尘装置2、布袋除尘器3、脱酸塔4、水解塔5、减压阀组7、脱硫塔8和高炉煤气柜9,所述减压阀组7与trt余压发电装置6连接;所述脱酸塔4包括呈圆筒状的塔体41,所述塔体41的进气侧连接有进气变径锥42,所述进气变径锥42连接煤气入口管道43,所述塔体41的出气侧连接有出气变径锥44,所述出气变径锥44连接有煤气出口管道45,所述进气变径锥42与所述塔体41的连接处设有进气流均布装置46,所述出气变径锥44与所述塔体41的连接处设有出气流均布装置47,所述塔体41内竖直设有用于高炉煤气脱酸的反应仓48,所述反应仓48内部装填有所述高炉煤气脱酸剂;所述脱酸塔4顶部设置有高炉煤气脱酸剂的进料口49和进料切断阀410,所述脱酸塔4底部设置有高炉煤气脱酸剂的卸料口411和卸料切断阀412,所述进料切断阀410下方设有进料仓,所述进料仓位于所述塔体41的顶壁上方,所述卸料切断阀的上方设有锥形料斗,所述锥形料斗位于所述塔体41的底壁下方,所述反应仓48的进气侧和出气侧分别设有整流格栅415。
29.其中,所述反应仓48为两个,分别为用于粗脱酸的一级反应仓和用于精脱酸的二级反应仓,所述进气流均布装置46与所述一级反应仓之间构成第一气体整流层416,所述一级反应仓和所述二级反应仓之间构成第二气体整流层417,所述二级反应仓与所述出气流均布装置47之间构成第三气体整流层418。
30.其中,所述脱酸塔4中间设置检修口419;所述煤气入口管道43上设有进气压力表420和进气体抽检装置421,所述煤气出口管道45上设有出气压力表422和出气体抽检装置423,所述脱酸塔4中间设有检修口419。进气压力表420用于检测煤气入口管道43中气体的压力,出气压力表422用于检测煤气出口管道45中气体的压力,进气体抽检装置421和出气体抽检装置423用于检测煤气脱酸前后高炉煤气中酸性气体如hcl和h2s的浓度。根据所述气体抽检装置的示数来判断脱酸塔4中的脱酸剂是否需要更换。若出气抽检装置中显示hcl的浓度大于10mg/nm3时,则表示脱酸剂已失效,需要更换新的脱酸剂。
31.其中,高炉煤气脱酸剂的外观为蜂窝状,将用于高炉煤气精脱硫工艺前端的煤气预处理段,用于脱除高炉煤气中的酸性气体如hcl、h2s等。所述脱酸塔4内脱酸剂的使用压力220kpa,使用温度150℃,煤气通过脱酸塔4的空速在2000h-1
,床层失效条件为脱酸塔4后煤气中hcl浓度大于10mg/nm3。
32.工作时,打开进料口切断阀,将本实施例制备的脱酸剂由脱酸塔4顶部的进料口和
进料仓,装填到一级反应仓和二级反应仓中,用于高炉煤气的脱酸处理。经过脱酸后,从气体抽检装置处检测出煤气中hcl的浓度为2mg/nm3,穿透氯容约为25%,如表1所示。运行一段时间后,当气体抽检装置处检测出煤气中hcl的浓度大于10mg/nm3,认为脱酸剂已经失效,需要更换新的脱酸剂。此时,打开卸料切断阀失效后的脱酸剂经由料斗和卸料口411排出脱酸塔4。待进料或卸料操作完成后,保证进料切断阀410或卸料切断阀412处于关闭状态。
33.经过干法布袋除尘后的高炉煤气,由煤气入口管道43进入脱酸塔4流经进气变径锥42、进气流均布装置46和第一气体整流层416,从反应仓一侧的整流格栅415进入到一级反应仓中进行粗脱酸,粗脱后的气体从一级反应仓另一侧的整流格栅415处流出,进入到第二气体整流层417,实现粗脱酸后气体的均匀混合。混匀后的气体经过整流格栅415进入到二级反应仓中进行精脱酸,精脱后的气体从二级反应仓另一侧的整流格栅415处流出,进入到第三气体整流层418,实现精脱酸后气体的均匀混合。混匀后的气体经过出气流均布装置47和出气变径锥44后,进入到煤气出口管道45中,至此完成整个高炉煤气的脱酸。
34.实施例2本实施例提供一种基于超细化钢渣的高炉煤气脱酸剂,按重量份数计,由以下成分组成:氢氧化钙20份,钢渣40份,硝酸铝5份,碳酸钠15份,甲基纤维素5份及膨润土15份。
35.其中,所述钢渣来自于钢铁企业在炼钢生产中产生的废弃物,为转炉渣。
36.本实施例提供了上述高炉煤气脱酸剂的制备方法,包括下述步骤:步骤1,按重量份计,将40份钢渣由上而下进料于湿磨机中,与90份水混合后,湿磨20分钟形成钢渣浆体;步骤2,按重量份计将硝酸铝5份溶解于10份水中,将形成的均一溶液与氢氧化钙20份加入到步骤1的钢渣浆体中,湿磨10钟,形成混合物a;步骤3,按重量份计将碳酸钠15份溶解于40份水中,将形成的均一溶液缓慢滴加到步骤2形成的混合物a中,保持边滴边搅拌,滴加完毕后继续搅拌30分钟,之后将形成的混合物置于高压反应釜中,于恒温鼓风干燥箱中150
°
c下反应8小时;反应结束后取出自然冷却,过滤,得到膏状固体混合物b;步骤4,按重量份计将甲基纤维素5份及膨润土15份置于步骤3得到的混合物b中,搅拌均匀后,挤出成型,得到成型物料;步骤5,将步骤4所得成型物料放入恒温鼓风干燥箱中,于80
°
c下干燥8小时,得到初级产品;步骤6,将步骤5干燥后的初级产品放入马弗炉中,于300℃下,焙烧4小时,然后自然冷却到室温,得到高炉煤气脱酸剂。
37.本实施例的脱酸系统与实施例1相同,采用的是本实施例的高炉煤气脱酸剂。
38.其中,高炉煤气脱酸剂的外观为四叶草状,将用于高炉煤气精脱硫工艺前端的煤气预处理段,用于脱除高炉煤气中的酸性气体如hcl、h2s等。所述脱酸塔4内脱酸剂的使用压力210kpa,使用温度180℃,煤气通过脱酸塔4的空速在1000h-1
,床层失效条件为脱酸塔4后煤气中hcl浓度大于10mg/nm3。
39.工作时,打开进料口切断阀,将本实施例制备的脱酸剂由脱酸塔4顶部的进料口和进料仓,装填到一级反应仓和二级反应仓中,用于高炉煤气的脱酸处理。经过脱酸后,从气体抽检装置处检测出煤气中hcl的浓度为2mg/nm3,穿透氯容约为22%,如表1所示。运行一段
时间后,当气体抽检装置处检测出煤气中hcl的浓度大于10mg/nm3,认为脱酸剂已经失效,需要更换新的脱酸剂。此时,打开卸料切断阀,失效后的脱酸剂经由料斗和卸料口411排出脱酸塔4。待进料或卸料操作完成后,保证进料切断阀410或卸料切断阀412处于关闭的状态。
40.实施例3本实施例提供一种基于超细化钢渣的高炉煤气脱酸剂,按重量份数计,由以下成分组成:氢氧化钙65份,钢渣10份,硝酸锌15份,碳酸氢钠5份,甲基纤维素10份及膨润土5份。
41.其中,所述钢渣来自于钢铁企业在炼钢生产中产生的废弃物,为电炉渣本实施例提供了上述高炉煤气脱酸剂的制备方法,包括下述步骤:步骤1,按重量份计,将10份钢渣由上而下进料于湿磨机中,与20份水混合后,湿磨60分钟形成钢渣浆体;步骤2,按重量份计将硝酸锌15份溶解于40份水中,将形成的均一溶液与氢氧化钙65份加入到步骤1的钢渣浆体中,湿磨30分钟,形成混合物a;步骤3,按重量份计将碳酸氢钠5份溶解于10份水中,将形成的均一溶液缓慢滴加到步骤2形成的混合物a中,保持边滴边搅拌,滴加完毕后继续搅拌15分钟,之后将形成的混合物置于高压反应釜中,于恒温鼓风干燥箱中200
°
c下反应2小时;反应结束后取出自然冷却,过滤,得到膏状固体混合物b;步骤4,按重量份计将甲基纤维素10份及膨润土5份置于步骤3得到的混合物b中,搅拌均匀后,挤出成型,得到成型物料;步骤5,将步骤4所得成型物料放入恒温鼓风干燥箱中,于150
°
c下干燥2小时,得到初级产品;步骤6,将步骤5干燥后的初级产品放入马弗炉中,于500℃下,焙烧1小时,然后自然冷却到室温,得到高炉煤气脱酸剂。
42.本实施例的脱酸系统与实施例1相同,采用的是本实施例的高炉煤气脱酸剂。
43.其中,高炉煤气脱酸剂的外观为空心球,将用于高炉煤气精脱硫工艺前端的煤气预处理段,用于脱除高炉煤气中的酸性气体如hcl、h2s等。所述脱酸塔4内脱酸剂的使用压力230kpa,使用温度120℃,煤气通过脱酸塔4的空速在3000h-1
,床层失效条件为脱酸塔4后煤气中hcl浓度大于10mg/nm3。
44.工作时,开进料切断阀,将本实施例制备的脱酸剂由脱酸塔4顶部的进料口和进料仓,装填到一级反应仓和二级反应仓中,用于高炉煤气的脱酸处理。经过脱酸后,从气体抽检装置处检测出煤气中hcl的浓度为2mg/nm3,穿透氯容约为26%,如表1所示。运行一段时间后,当气体抽检装置处检测出煤气中hcl的浓度大于10mg/nm3,认为脱酸剂已经失效,需要更换新的脱酸剂。此时,打开卸料切断阀,失效后的脱酸剂经由料斗和卸料口411排出脱酸塔4。待进料或卸料操作完成后,保证进料切断阀410或卸料切断阀412处于关闭状态。
45.实施例4本实施例提供一种基于超细化钢渣的高炉煤气脱酸剂,按重量份数计,由以下成分组成:氢氧化钙45份,钢渣25份,硝酸锌12份,碳酸钠8份,甲基纤维素5份及膨润土5份。
46.本实施例提供了上述高炉煤气脱酸剂的制备方法,包括下述步骤:
步骤1,按重量份计,将25份钢渣由上而下进料于湿磨机中,与60份水混合后,湿磨45分钟形成钢渣浆体;步骤2,按重量份计将硝酸锌12份溶解于25份水中,将形成的均一溶液与氢氧化钙50份加入到步骤1的钢渣浆体中,湿磨25分钟,形成混合物a;步骤3,按重量份计将碳酸钠8份溶解于20份水中,将形成的均一溶液缓慢滴加到步骤2形成的混合物a中,保持边滴边搅拌,滴加完毕后继续搅拌20分钟,之后将形成的混合物置于高压反应釜中,于恒温鼓风干燥箱中180
°
c下反应7小时;反应结束后取出自然冷却,过滤,得到膏状固体混合物b;步骤4,按重量份计将甲基纤维素5份及膨润土5份置于步骤3得到的混合物b中,搅拌均匀后,挤出成型,得到成型物料;步骤5,将步骤4所得成型物料放入恒温鼓风干燥箱中,于100
°
c下干燥5小时,得到初级产品;步骤6,将步骤5干燥后的初级产品放入马弗炉中,于400℃下,焙烧2小时,然后自然冷却到室温,得到高炉煤气脱酸剂。
47.本实施例的脱酸系统与实施例1相同,采用的是本实施例的高炉煤气脱酸剂。
48.其中,高炉煤气脱酸剂的外观为空心柱状,将用于高炉煤气精脱硫工艺前端的煤气预处理段,用于脱除高炉煤气中的酸性气体如hcl、h2s等。所述脱酸塔4内脱酸剂的使用压力225kpa,使用温度170℃,煤气通过脱酸塔4的空速在2500h-1
,床层失效条件为脱酸塔4后煤气中hcl浓度大于10mg/nm3。
49.工作时,打开进料口切断阀,将本实施例制备的脱酸剂由脱酸塔4顶部的进料口和进料仓,装填到一级反应仓和二级反应仓中,用于高炉煤气的脱酸处理。经过脱酸后,从气体抽检装置处检测出煤气中hcl的浓度为2mg/nm3,穿透氯容约为28%,如表1所示。运行一段时间后,当气体抽检装置处检测出煤气中hcl的浓度大于10mg/nm3,认为脱酸剂已经失效,需要更换新的脱酸剂。此时,打开卸料切断阀,失效后的脱酸剂经由料斗和卸料口411排出脱酸塔4。待进料或卸料操作完成后,保证进料切断阀410或卸料切断阀412处于关闭状态。
50.对比例1本实施例提供一种基于超细化钢渣的高炉煤气脱酸剂及其制备方法和脱酸系统,其与实施例1的区别之处仅在于,不使用氢氧化钙,使用钢渣65份来制备高炉煤气预处理产品。
51.打开进料口切断阀,将本实施例制备的脱酸剂由脱酸塔4顶部的进料口和进料仓,装填到一级反应仓和二级反应仓中,用于高炉煤气的脱酸处理。经过脱酸后,从气体抽检装置处检测出煤气中hcl的浓度为2mg/nm3,穿透氯容约为7%,如表1所示。运行一段时间后,当气体抽检装置处检测出煤气中hcl的浓度大于10mg/nm3,认为脱酸剂已经失效,需要更换新的脱酸剂。此时,打开卸料切断阀,失效后的脱酸剂经由料斗和卸料口411排出脱酸塔4。待进料或卸料操作完成后,保证进料切断阀410或卸料切断阀412处于关闭的状态。
52.对比例2本实施例提供一种基于超细化钢渣的高炉煤气脱酸剂及其制备方法和脱酸系统,其与实施例3的区别之处仅在于,不使用钢渣,使用氢氧化钙65份来制备高炉煤气预处理产品。
53.打开进料口切断阀,将本实施例制备的脱酸剂由脱酸塔4顶部的进料口和进料仓,装填到一级反应仓和二级反应仓中,用于高炉煤气的脱酸处理。经过脱酸后,从气体抽检装置处检测出煤气中hcl的浓度为2mg/nm3,穿透氯容约为24%,如表1所示。运行一段时间后,当气体抽检装置处检测出煤气中hcl的浓度大于10mg/nm3,认为脱酸剂已经失效,需要更换新的脱酸剂。此时,打开卸料切断阀,失效后的脱酸剂经由料斗和卸料口411排出脱酸塔4。待进料或卸料操作完成后,保证进料切断阀410或卸料切断阀412处于关闭的状态。
54.对比例3本实施例提供一种基于超细化钢渣的高炉煤气脱酸剂及其制备方法和脱酸系统,其与实施例4的区别之处仅在于,不使用碳酸氢钠,使用氢氧化钙53份来制备高炉煤气预处理产品。
55.打开进料口切断阀,将本实施例制备的脱酸剂由脱酸塔4顶部的进料口和进料仓,装填到一级反应仓和二级反应仓中,用于高炉煤气的脱酸处理。经过脱酸后,从气体抽检装置处检测出煤气中hcl的浓度为2mg/nm3,穿透氯容约为15%,如表1所示。运行一段时间后,当气体抽检装置处检测出煤气中hcl的浓度大于10mg/nm3,认为脱酸剂已经失效,需要更换新的脱酸剂。此时,打开卸料切断阀,失效后的脱酸剂经由料斗和卸料口411排出脱酸塔4。待进料或卸料操作完成后,保证进料切断阀410或卸料切断阀412处于关闭的状态。
56.实验例对实施例1-4和对比例1-3中的高炉煤气脱酸剂的性能进行检测,以高炉煤气中存在的hcl为代表性酸性气体,判断脱酸剂的脱酸性能。将粒径为5mm的脱酸剂装在立式固定床反应器(φ50mm
×
300mm)中,反应温度控制在150℃,模拟高炉煤气化学成分体积比控制为co/co2/n2/h2=28/12/59/1,煤气流量控制在5l/min,煤气中hcl气体的初始质量浓度控制在2000mg/m3。采用离子色谱检测出口气体中hcl的浓度,当出口中hcl的浓度大于2mg/m3时,认为脱酸剂已穿透,从通气开始到脱酸剂被穿透持续的时间定义为穿透时间;脱酸剂穿透时吸收氯的质量分数称之为穿透氯容量,用穿透氯容量来评价脱酸剂的性能。参照hg/t 2783-2020 分子筛抗压碎力试验方法测定脱酸剂的机械强度。参照gb/t 30202.1-2013 脱硫脱硝用煤质颗粒活性炭试验方法第1部分堆积密度测定脱酸剂的堆积密度。
57.表1脱酸剂的性能指标检测结果如表1所示,从实施例3和对比例2的试验结果可以看出,与不添加钢渣的脱酸剂相比较,添加钢渣后的脱酸剂在径向抗压强度和穿透氯容方面均有大幅度改善。原因在于,在脱酸剂
的制备过程中,钢渣经过湿法细磨后,其中的cao发生充分水解转化为ca(oh)2等碱性物质,这些是活性很高的脱酸成分。经过湿法细磨后的钢渣和氢氧化钙具有较高的表面能,同时内部形成了较多的晶格缺陷,提高了活性组分在其晶格内部的分散度,从而改善了脱酸性能。另一方面,钢渣本身含有大量胶凝性物质如硅酸三钙、硅酸二钙等,湿法细磨促使钢渣中的f-cao进一步水化,同时伴随钢渣内部的晶格畸变,使细磨能量转化为钢渣粉的内能和表面能,进一步提高了钢渣的胶凝性,从而促使脱酸剂的机械强度大幅度改善。
58.从实施例4和对比例3的试验结果可以看出,添加了改性剂的脱酸剂,具有显著提高的穿透氯容,原因在于改性剂的加入提高了脱酸剂表面碱性活性中性的数量,从而改善了整体的脱酸性能。
59.以上所述仅为本发明的较佳实施例而已,并不用以限制本发明,凡在本发明的精神和原则之内,所作的任何修改、等同替换、改进等,均应包含在本发明的保护范围之内。