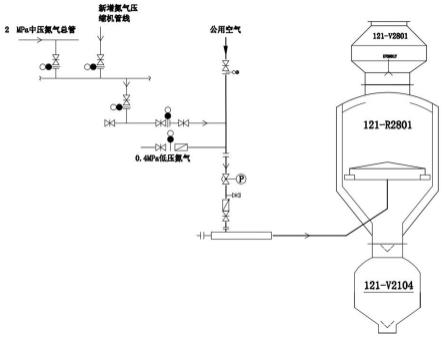
1.本技术涉及一种碎煤加压气化装置系统试压的工艺方法。
背景技术:2.碎煤加压气化炉多因设备故障(煤灰锁上下阀故障)和易损设备寿命到期更换(煤灰锁上下阀,炉篦偏心套填料等)造成设备停运,停运后的设备检修和配件更换必须对气化炉炉体进行解体,根据《工业企业煤气安全规程》gb6222-2005中要求对新增和大修后的煤气发生炉再开车前必须对设备进行试压试验。
3.碎煤加压气化炉设计运行压力为4.0mpa,配套公用工程空分装置所产装置空气压力为0.4mpa,氮气压力等级为0.4mpa和2.0mpa两种,根据《固定式压力容器安全技术监察规程》tsg21-2016 3.2.13.1规定气密性试验压力应为压力容器设计压力。碎煤加压气化单元的试压压力为4.6(g)mpa。公用工程提供的试压介质压力无法满足拆检大修的碎煤加压气化炉做严密性压力试验。为了实现严密性试验所需压力等级的气源,前期通过液氮槽车拉运空分装置所产液氮,然后通过液氮撬装设备打压为碎煤气化炉进行试压试验。在使用此种方案进行试压试验的过程中如果存在设备泄漏量大,液氮槽车的液氮存储量有限,消漏后需要多次进行重复性的提压试压。造成大幅度延长气化炉开车时间和浪费试压介质的情况,同时也很大程度的增加了经济成本。
4.按照原设计院提供的工艺包,碎煤加压气化炉大修后液压强度试验后,气化炉一般解体后的再开车严密性试验采用低压试验(试压介质为0.4mpa的氮气),试压结束后在气化炉开车阶段由工艺气提压做2.0mpa-4.0 mpa等级气密,在整个提压过程中对气化炉重点泄漏部位进行查漏和热紧。由于开车过程中随着设备压力的升高如出现泄漏,泄漏的介质多为粗煤气(主要成分为co、h2、ch4等可燃气体),有毒有害、高温高压,在此过程中查漏和带压热紧容易造成很大的安全风险甚至发生气化闪爆等恶性事故。如不进行带压热紧会造成开车炉不得不停车泄压消漏,对后期气化炉开车过程中整个床层的培养和开车后工况的调整造成了一定的困难。
技术实现要素:5.针对上述现有缺陷,本技术的目的在于提出一种碎煤加压气化装置系统试压的工艺方法。
6.本技术的目的是这样实现的:一种碎煤加压气化装置系统试压的工艺方法,包括以下步骤:步骤1、用低压氮气管线对气化炉进行0.4mpa的气密;微开气化炉空气调节阀对气化炉缓慢升压,控制升压速率≤0.05mpa/min,气化炉与夹套的压差不大于 50kpa;步骤2、当压力达到 0.4mpa 时,关闭气化炉空气调节阀,对气化炉进行 0.4mpa气密检查。对各法兰检查,填写气密确认表。检查合格后倒盲0.4mpa低压氮气盲板,导通2.0mpa中压氮气盲板;
步骤3、用2.0mpa中压氮气将气化炉压力升到2.0mpa时,停止升压;关闭气化炉空气调节阀,对气化炉进行 2.0mpa气密检查。对各法兰检查,填写气密确认表;步骤4、关闭2.0mpa中压氮气阀门,倒盲进框架中压氮气阀后盲板,导通新增氮气压缩机进框架管线阀后盲板,使用新增氮气压缩机向气化炉充压;步骤5、调整空气调节阀,对气化炉缓慢升压,控制升压速率≤0.05mpa/min,气化炉与夹套小于50kpa;步骤6、气化炉最终提压至 4.6 mpa,检查无泄漏,保压 2 小时后气密结束。
7.步骤7、气化炉缓慢泄压至常压,控制泄压速率≤0.05mpa/min,气化炉与夹套的压差不大于50kpa。
8.由于实行上述技术方案,本技术通过使用本单位公用工程空分单元所产中压氮气(2.0mpa)作为碎煤加压气化单元严密性试验介质气源,同时增加一套往复式压缩机将压力为2.0mpa的中压氮气经压缩、冷却、分离等过程提压至4.6mpa,然后在气化炉开车前分级对碎煤加压气化单元进行严密性试验。若试验过程中存在泄漏,气密介质为惰性气氮气可以带压消漏,如无法带压消漏及时泄压消漏,减少气化炉开车过程中的泄漏风险同时缩短开车时间,有效降低开车费用。
附图说明
9.本技术的具体结构由以下的附图和实施例给出:图1是本技术的系统结构示意图;图2是2mpa-4.6mpa气密试验流程图;图3是氮压机试验工艺流程图。
10.图例:121v2801煤锁,121r2801气化炉,121v2104灰锁,1、储气罐,2、氮气压缩机,3、一级分离器,4、一级进气缓冲器,5、一级排气缓冲器,6、一级冷却器,7、油冷却器,8、稀油站,9、气化炉。
具体实施方式
11.本技术不受下述实施例的限制,可根据本技术的技术方案与实际情况来确定具体的实施方式。
12.实施例:如图1、2所示,一种碎煤加压气化装置系统试压的工艺方法,包括以下步骤:步骤1、用低压氮气管线对气化炉进行0.4mpa的气密;微开气化炉空气调节阀对气化炉缓慢升压,控制升压速率≤0.05mpa/min,气化炉与夹套的压差不大于 50kpa;步骤2、当压力达到 0.4mpa 时,关闭气化炉空气调节阀,对气化炉进行 0.4mpa气密检查。对各法兰检查,填写气密确认表,检查合格后倒盲0.4mpa低压氮气盲板,导通2.0mpa中压氮气盲板;步骤3、用2.0mpa中压氮气将气化炉压力升到2.0mpa时,停止升压;关闭气化炉空气调节阀,对气化炉进行 2.0mpa气密检查,对各法兰检查,填写气密确认表;步骤4、关闭2.0mpa中压氮气阀门,倒盲进框架中压氮气阀后盲板,导通新增氮气压缩机进框架管线阀后盲板,使用新增氮气压缩机向气化炉充压;
步骤5、调整空气调节阀,对气化炉缓慢升压,控制升压速率≤0.05mpa/min,气化炉与夹套小于50kpa;步骤6、气化炉最终提压至 4.6 mpa,检查无泄漏,保压 2 小时后气密结束。
13.步骤7、气化炉缓慢泄压至常压,控制泄压速率≤0.05mpa/min,气化炉与夹套的压差不大于50kpa。
14.进一步的,步骤4中,碎煤加压气化炉2.0mpa气密结束后,关闭2.0mpa中压氮气总管进气化炉a/b/c三个框架的界区阀,同时导盲盲板,然后导通新增氮气压缩机进2.0mpa中压氮气总管的盲板,打开氮压机的出口管线的截止阀。通过氮压机将2.0mpa的中压氮气往复压缩提压到4.6mpa打回2.0mpa中压氮气总管界区阀后为气化a/b/c三个框架的气化炉做严密性试验。
15.步骤5中,升压过程中如果发现泄漏联系维保单位紧固,紧住后继续升压。如果紧不住或泄漏大,气化炉泄至常压进行消缺。
16.步骤6中,如果发现泄漏联系检修单位紧固,紧住后气密升压结束。如果紧不住或泄漏大,气化炉泄至常压进行消缺。
17.步骤1前的大修后开车前严密性试验:使用0.4mpa的低压氮气作为气密介质经过煤锁气压缩机向气化炉充压至4.0mpa;如多台气化炉同时做严密性试验,煤锁气压缩机打气量不足时,使用新增氮气压缩机配合使用提压至4.6mpa。
18.碎煤加压气化装置整个严密性试验使用氮气作为气密介质,采用三个压力等级的氮气气源(0.4mpa、2.0mpa、4.6mpa)。氮气气源(0.4mpa、2.0mpa)由本厂空分装置自产,氮气气源(4.6mpa)由新增氮压机加压2.0mpa中压氮提供(一开一备)。
19.碎煤加压气化装置严密性试验过程采用5级气密,压力等级分别在0.4mpa级、1.0mpa级、2.0mpa级、3.0mpa级、4.6mpa级。在不同的压力等级下进行保压查漏,在低压力等级气密试验查漏消漏合格后方可进入更高等级压力进行气密试验,直至做到设计压力4.6mpa。
20.提供气源的三个压力等级的氮气源(0.4mpa、2.0mpa、4.6mpa)进入碎煤加压气化装置是通过气化炉原配置的空气管线甩头接入。单炉空气管线界区截止阀后承压为600lb,三个气源在充压气密过程中使用空气管线的阀组进行控制(包括调节阀、单向阀、孔板流量计)。在使用该段管线进行气密试验时,需提前倒盲空气界区阀阀后盲板。
21.新增氮气压缩机使用空分装置自产的2.0mpa中压氮气作为气源往复压缩后压力提至4.6mpa打回2.ompa的中压氮气总管进气化装置界区阀后,此时确保2.0mpa中压氮气总管界区阀已倒盲。(2.0mpa、4.6mpa)两种压力等级同用一条总管线,只许进行压力切换。同时两种压力氮气入气化炉也可走同一条工艺流程。
22.如图3所示,氮气压缩机试验工艺流程,来自中压氮气管网的2.0mpa、温度30℃的氮气经储气罐1稳压后,进入一级进气缓冲器4,经氮气压缩机2压缩至4.6mpa、114℃后进入一级排气缓冲器5,再进入一级冷却器6冷却至40℃,进入一级分离器3分离工艺液体,分离后的工艺液体排入油冷却器7,冷却后排入稀油站8,气体由一级分离器3顶部出去分两路,一路去气化a/b/c三个框架各气化炉9,另一路返回一级进气缓冲器4前进口管线,用于调整机组负荷和开停车。
23.气化炉开车前即完成国家规范要求相应压力等级下严密性试验避免了开车过程
中气密的不安全性。使用氮气(惰性气体)在气密消漏过程中减少了现行方案气密使用工艺气气密的危险性。避免了气密过程中出现泄漏后现行方案需要停车泄压进行消漏,延长了开车时间同时造成了开车原料的浪费,增加了气化炉开车的成本。
24.上述说明仅仅是为清楚地说明本技术所作的举例,而并非是对本技术的实施方式的限定。凡是属于本技术的技术方案所引申出的显而易见的变化或变动仍处于本技术的保护范围之列。