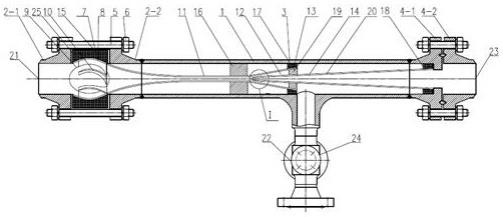
1.本实用新型涉及天然气处理技术领域,特别是涉及冷凝分离超音速分离器,具体指一种芯体一体化可拆型超音速分离器。
背景技术:2.从天然气的气田中开采出的混合天然气中含有水蒸气、二氧化碳和硫化物等混合气体,并且湿蒸汽一般都处在高饱和的状态,所以容易对运输管道造成堵塞或者腐蚀等破坏。因此,脱除水和液泾是天然气生产中的必要环节。
3.天然气脱水的主要方法吸收法、冷凝法、吸附法以及膜分离法等。溶剂吸收法设备设置繁多、系统庞大并且投资费用高。冷凝法采用的制冷设备主要是节流阀及透平膨胀机,节流阀的不可逆性会造成能量损失,透平膨胀机的制造难度较大、可靠性差,因为其有高速运动部件。固体吸附法的吸附剂易中毒和破碎粉化,再生时耗能高;对于大型设备,其投资和操作费用高。膜法天然气脱水存在着渗透过程中烃损失相对较大,水汽对聚合物膜会产生塑化与溶胀作用等缺陷。
4.超音速分离器是基于气体动力学、热力学以及流体力学的研究而开发出的新型的利用超音速产生低温环境的一种冷凝分离技术。超音速旋流分离器是将膨胀降温、旋流式气/液分离、再压缩等工艺在一个密闭紧凑的装置里完成。是低温冷凝方法的一种静设备,其优点是有密闭无泄漏、无需化学药剂(乙二醇或甲醇)、设备工艺及结构简单,等熵效率高且压降较小,结构紧凑轻巧、简单可靠(无移动部件)、支持无人值守等优点,实现了节约成本和保护环境的双重效益。但该技术的研究历史还不长,此技术具有很好的研究前景,但是我国对此项技术的研究才刚起步,依然处于初期阶段,尚停留在气体超音速流体过程中的流动特性和装置雏形结构研究上。目前仍存在诸多问题尚待解决,如:中心体与外部套筒固定方式比较复杂,加工难度大;旋流段,分离段,扩压段之间法兰连接,增加了泄露和产生激波的风险。
技术实现要素:5.本实用新型提供一种可拆型、结构简单、性能优良的超音速分离器,为进一步优化现有超音速分离器结构、降低加工难度提供一种可行方案。
6.本实用新型采用的技术方案如下:
7.一种芯体一体化可拆型超音速分离器,包括超音速分离器壳体及安装于超音速分离器壳体内的一体化超音速分离器芯体;所述一体化超音速分离器芯体包括轴向顺次设置的旋流段,laval 喷管段,分离段及扩压管段;所述laval 喷管段的末端外部固接有固定翅片,该固定翅片与超音速分离器壳体内壁适配贴合;而所述分离段的分离翼末端设置有分离翼末端限位环,该分离翼末端限位环内环面与分离翼末端环面固接,外环面与超音速分离器壳体内壁适配贴合;分离翼末端内壁与扩压管段间设有固定支撑板,该固定支撑板平行于超音速分离器壳体轴线设置后其上部与分离翼内表面固接,下部与扩压管段外表面固
接从而形成可整体抽出更换的一体化超音速分离器芯体。
8.所述一体化超音速分离器芯体前端的旋流段通过始端定位环密封轴向定位安装于超音速分离器壳体的前端法兰上,而扩压管段末端通过末端限位锻环轴向定位于后端固定法兰凸缘上。
9.所述固定支撑板沿扩压管段圆周方向呈60
°
~90
°
均布,其流体流向端为尖劈锥形。
10.所述旋流段包括旋流器外壳,椭圆球型中心锥和制旋叶片;所述椭圆球型中心锥与旋流器外壳同轴设置,并置于旋流器外壳内部,所述制旋叶片的始端为锥面结构,呈螺旋状固接于旋流器外壳和椭圆球型中心锥之间。
11.所述芯体一体化可拆型超音速分离器包括饱和气相进口,液相出口,干气出口;所述饱和气相进口设置于超音速分离器壳体的前端法兰处,液相出口开于所述分离翼与扩压管段间的超音速分离器壳体上;所述干气出口设置于超音速分离器壳体的后端法兰处。
12.所述液相出口处设有疏水阀。
13.本实用新型的有益效果是:
14.(1)本实用新型无噪音,在分离过程中不使用化学物品,无环境污染,设计合理,处理量大,无能耗,使用方便
15.(2)本实用新型不需要外部能量,只需通过分离器本身的结构,利用介质自身的能量转换,即可实现饱和湿天然气的旋流和膨胀加速,并在所形成低温低压环境下,天然气中的水蒸气凝结析出。
16.(3)本实用新型在析出液相水滴之后,还能在环形腔内部强大的离心力作用下,将该液相水滴甩向分离翼的壁面,之后从分离腔排除,从而实现冷凝液的分离,而剩余的干燥天然气在扩压管段内,将压力和温度得到恢复,满足天然气外输要求。
17.(4)本实用新型同时也解决了中心体与外部套筒固定方式复杂,加工难度大的问题;避免了以往法兰连接,产生泄露和激波的情况发生。
附图说明
18.图1为本实用新型结构示意图;
19.图2为本实用新型一体化超音速分离器芯体结构示意图;
20.图3为本实用新型旋流发生器立体示意图;
21.图4为本实用新型固定支撑板入口端截面示意图;
22.图5为本实用新型固定支撑板出口端截面示意图;
23.图6为图1中i部放大图;
24.图中编号:1—超音速分离器壳体2-1/2-2—前端固定法兰3-连接管段4-1/4-2—后端固定法兰、5—螺栓、6—螺母、7-旋流段、8—旋流器外壳、9—椭圆球型中心锥、10—制旋叶片、11—laval喷管段、12—分离段、13—分离翼、14—扩压管段、15—始端定位环、16—固定翅片、17—分离翼末端限位环、18—末端限位锻环、19—固定支撑板、20—一体化超音速分离器芯体、21—饱和气相进口、22—液相出口、23—干气出口、24-疏水阀、25-密封垫片。
具体实施方式
25.下面结合附图对本实用新型进一步说明。
26.参见图1,一种芯体一体化可拆型超音速分离器,包括超音速分离器壳体1及安装于超音速分离器壳体1内的一体化超音速分离器芯体20。
27.上述超音速分离器壳体1包括前端固定法兰,连接管段3,后端固定法兰,密封垫片25、螺栓5、螺母6。前端固定法兰之 2-1部和后端固定法兰之4-1部分别焊接于连接管段3的前后端,并分别于前端固定法兰之 2-2部和后端固定法兰之4-2部相配合后通过螺栓5、螺母6连接。
28.所述一体化超音速分离器芯体为包括轴向顺次设置的旋流段7,laval 喷管段11,分离段12及扩压管段14;所述laval 喷管段11的末端外部焊接有固定翅片16,该固定翅片16与超音速分离器壳体1内壁适配贴合,防止不恰当操作引起喷射管振动。而所述分离段12的分离翼13末端设置有分离翼末端限位环17,该分离翼末端限位环17内环面与分离翼13末端环面焊接,外环面与超音速分离器壳体1内壁适配贴合,分离翼末端限位环17用于固定分离翼倾斜角度及超音速分离器芯体的整体位置。分离翼13末端内壁与扩压管段14间设有固定支撑板19,该固定支撑板19平行于超音速分离器壳体1轴线设置后其上部与分离翼13内表面固接,下部与扩压管段14外表面固接从而形成可整体抽出更换的一体化超音速分离器芯体20。
29.所述一体化超音速分离器芯体前端的旋流段7通过始端定位环15密封轴向定位安装于超音速分离器壳体1的前端法兰上,而扩压管段14末端通过末端限位锻环18轴向定位于后端固定法兰凸缘上。
30.具体为:旋流器外壳8环面上焊接有与前端法兰垂直面平齐的始端定位环15,始端定位环15在轴向方向固定于两片法兰面之间且与法兰垂直面间设有密封垫片25,始端定位环15内环面与旋流器外壳8贴合焊接,外环面与螺栓5形成的圆环面贴合,固定于螺栓5内部。所述扩压管段14末端设有末端限位锻环18,扩压末端限位锻环18内环面与扩压管段14末端圆周方向焊接连接,外环面与超音速分离器壳体1贴合,轴向方向由后端固定法兰凸缘面限位。
31.超音速分离器入口进料是轴向进入,因流速较高,会引起一体化超音速分离器芯体的振动与轴向偏移,进行轴向定位安装,能够有效防止一体化超音速分离器芯体的振动和轴向偏移。
32.分离翼13末端与扩压管段14间设有垂直固定支撑板19,该固定支撑板19平行于轴线焊接在分离翼末端的1/4~1/5处,固定支撑板沿扩压管段圆周方向60
°
~90
°
均布,其流体流向端为尖劈锥形。固定支撑板19主要固定流体流道间隙间距,同时使得超音速分离器芯体一体化,且可以起到液体导流的作用。固定支撑板前端尖劈锥形的的坡面结构使得液体顺利流出,且流动阻力小。
33.如图3所示,所述旋流段7包括旋流器外壳8,椭圆球形中心锥9和制旋叶片10,所述的椭圆球形中心锥9与旋流器外壳8同轴,并置于旋流器外壳8内部,所述旋流叶片10的始端为锥面结构,呈螺旋状焊接固定于旋流器外壳8和椭圆球形中心锥9之间;此结构有助于气体进入螺旋叶片形成螺旋流,而且对气流的阻力小。
34.分离翼与扩压管间设有液体流出通道,分离翼倾斜偏离水平角度由液滴旋流切向
流速确定,分离翼与扩压管段间隙与液滴成核量决定。扩压管段入口呈坡面状,其坡面平行于分离翼倾斜面。坡面有利于液体甩出壁面。
35.所述芯体一体化可拆型超音速分离器包括气相进口21,液相出口22,干气出口23。所述饱和气相进口21设置于超音速分离器壳体1的前端法兰处,液相出口22开于所述分离翼13与扩压管段14间的超音速分离器壳体1上;所述干气出口23设置于超音速分离器壳体1的后端法兰处。
36.如图6所示,所述扩压管段14与分离翼13间的液体流出通道为环形分离腔,扩压管段14插入分离段12中的端部形状为尖劈锥形。所述环形分离腔置于扩压管段14的入口截面处,分离环截面将扩压管段14的入口截面分为内层截面和外层截面,外层截面与分离翼内壁、尖劈锥形外壁之间形成,外层截面为分离器入口端,分离器出口端与液相出口连接;内层截面与尖劈锥形内壁之间形成扩压器,内层截面为扩压管段入口端,扩压管段出口端与干气出口23相连接。
37.所述液相出口22处设有疏水阀24,防止气体从液体流道滑出。
38.本实用新型的工作原理:在一定的压力温度下,饱和湿天然气以平稳的速度进入芯体一体化的可拆型超音速分离器中,经过一小段直管段之后,在旋流器的作用下,饱和湿天然气产生离心力。根据角动量守恒定律,饱和湿天然气离心加速度随着旋转半径的减小而增大,使得旋流强度不断增强,从而形成具有足够切向流速的旋流饱和湿天然气。
39.在旋流饱和湿天然气进入laval 喷管段后,旋流饱和湿天然气发生绝热膨胀并被加速至超音速,同时旋流饱和湿天然气的温度和压力迅速降低,将天然气的热能和压能转换为动能,动能进一步增大,此时在laval 喷管段中形成低温低压的环境。当laval 喷管段环境中的温度低至使旋流饱和湿天然气达到过饱和状态时,可凝物达到露点温度以下被冷凝出来,强大的离心力将其甩到laval 喷管段靠近分离翼壁面或者分离翼壁面上。
40.旋流饱和天然气在进入laval 喷管段之后,由于laval 喷管段中的流道半径逐渐减小,因此根据角动量守恒定律,旋流饱和湿天然气的旋流角速度将自动增加。通过laval 喷管段喉径时,旋流饱和湿天然气的旋转直径大幅减小,从而使得旋流饱和湿天然气的旋转角度进一步增加,此时旋流饱和湿天然气能够产生可达1x106m/s2倍的切向加速度,这样就充分保证了凝结出来的小液滴可以被旋流排出超音速旋流分离器。
41.旋流饱和湿天然气混合物中凝结出的小液滴在如此大的离心力作用下被甩向分离构件的内腔壁面并形成液膜。而由液膜形成的液滴将沿着分离翼的内腔壁运动,最终流入环形分离中并通过液相出口排出超音速旋流分离器,这样就实现了饱和湿天然气的气液分离。而由于天然气含湿混合物在气流中的停留时间相对于水合物较低的形成速度来说是极短的,因此不会在整流式超音速旋流分离器中形成水合物,由此从整个过程可以看出,在完全不需要添加化学药剂的情况下,即可将饱和湿天然气中的液相排出。
42.在旋流饱和湿天然气中的液相被排出之后形成的旋流干燥天然气流入了扩压器中,而此时从laval 喷管段流出的干燥天然气带有强烈旋流,如果这样直接进入输送管道会造成非常大的损失。由此,该旋流饱和湿天然气需要首先在扩压器中经过一小段扩压作用使速度被降低,这时天然气的动能转化为压能和热能,使旋流干燥天然气的温度和压力得到一定的回升。使得干燥天然气的温度和压力能够在扩压器中达到管道的输送要求,之后通过直流管的出口流出。