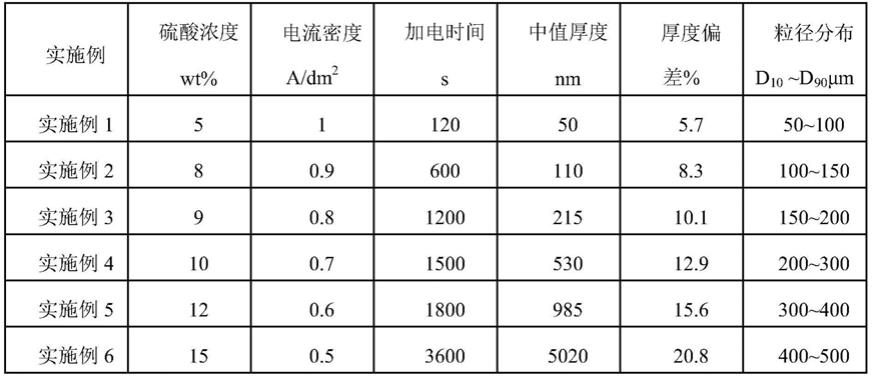
1.本发明属于片状氧化铝领域,涉及一种片状氧化铝及其制备方法与应用。
背景技术:2.片状氧化铝具有耐高温、较好的韧性、化学性质稳定等优良特性,可用于聚合物的填充剂,以提高聚合物器件的使用寿命;可用于陶瓷的增韧剂,以提高陶瓷器件的韧性;可用于耐磨、耐腐蚀等功能涂层;可用于制备耐火材料,如烧结炉、烧结管等。制备片状氧化铝最常用的方法主要有熔盐法、高温烧结法、水热(醇热)法、涂膜法、溶胶一凝胶法和机械法等,但大部分方法所制备的片状氧化铝厚度均匀性和可控性差,而且片径太小,最高只能达到几个微米。商业化最成熟的是采用熔盐法制备片状氧化铝,制备过程晶型控制难,成本高,而且氧化铝的片径小,最高只能达到几个微米,不能满足需求。
技术实现要素:3.本发明的一个目的在于针对现有技术存在的不足,提供一种片状氧化铝,粒径分布d
10
~d
90
为10μm~500μm,优选地为20μm~200μm,更优选地为50μm~100μm;中值厚度为50nm~5000nm,优选地为100nm~1000nm,更优地为200~500nm;厚度偏差≤20%,优选地厚度偏差≤10%。
4.优选地,所述片状氧化铝的粒径分布d
10
~d
90
为10μm~500μm,300μm~400μm,400μm~450μm中的任意范围值。
5.优选地,所述片状氧化铝的中值厚度为50nm,110nm,215nm,530nm,985nm,5020nm之中的任意值及其二者之间的范围值。
6.优选地,所述片状氧化铝的厚度偏差≤21%,≤20.8%,≤15.6%,≤12.9%,≤10.1%,≤10%,≤8.3%,≤5.7%之中的任意值及其二者之间的范围值。
7.本发明中,粒径分布d
10
表示累计10%点的直径值,粒径分布d
90
表示累计90%点的直径值。
[0008]“中值厚度”是指所有统计点厚度值的中间值。
[0009]“厚度偏差”是指任何一个统计点的厚度(h)与中值厚度(h
中值
)之间的偏差比例;计算公式为(h
‑
h
中值
)/h
中值
×
100%。
[0010]
本发明的另一个目的是提供一种片状氧化铝的制备方法,通过以下步骤来实现的:
[0011]
s1:以含有硫酸的溶液为电化学溶液,以含有铝箔的电极为正极,以导电电极为负极,在正极与负极之间施加电流,在含有铝箔的电极表面制备氧化铝膜;
[0012]
s2:将步骤s1制备的表面包含氧化铝膜的铝箔剪切去边缘或剪切成一定尺寸;
[0013]
s3:将步骤s2剪切后的铝箔,在含有铜盐的溶液中浸渍处理,以超声波分散,制备包含氧化铝膜的悬浮液;
[0014]
s4:将步骤s3包含氧化铝膜的悬浮液分离,制备片状氧化铝。
[0015]
本发明中,为了使片状氧化铝发生晶型转变,提高其耐酸碱性,在步骤s4之后将片状氧化铝进行煅烧,煅烧温度为800℃~1200℃,例如800℃、900℃、1000℃、1100℃、1200℃之中的任意温度及其二者之间的范围值,优选地煅烧温度为900℃~1000℃;煅烧时间为1h~12h,例如1h、4h、6h、8h、10h、12h之中的任意时间及其二者之间的范围值,优选地为2h~4h。
[0016]
本发明中,通过电化学方法俗称阳极氧化在铝表面制备氧化铝膜,该过程铝的腐蚀溶解以及氧化铝膜的生成同时进行,硫酸是强腐蚀性酸,浓度低于5wt%时不能生成氧化铝膜,浓度高于15wt%时氧化铝膜变脆,电化学溶液中硫酸的质量分数为5wt%~15wt%,例如5wt%、7wt%、8wt%、9wt%、10wt%、11wt%、12wt%、13wt%、15wt%,优选地为7wt%~9wt%;5wt~15wt%之中的任意质量分数及其二者之间的范围值,优选地为8wt%~10wt%。氧化铝膜制备过程硫酸溶液中的铝离子逐渐增加,当铝离子浓度超过10wt%后,氧化膜很难进一步形成,为了提高氧化铝膜的致密性及厚度均匀性,步骤s1电化学溶液中还包括选自柠檬酸、硼酸、草酸中的至少一种组成的辅助酸;辅助酸的质量分数为0.5wt%~3wt%,例如0.5wt%、1wt%、1.5wt%、2wt%、2.5wt%、3wt%之中的任意质量分数及其二者之间的范围值。加入柠檬酸作为辅助酸,与铝离子络合降低硫酸溶液中的铝离子含量;或者加入硼酸,以防止硫酸溶液温度升高后氧化铝膜变得疏松,或者加入草酸,提高氧化铝膜的韧性,最好三种辅助酸均加入少量。
[0017]
本发明中步骤s1包括硫酸的溶液温度为15℃~35℃,更优选地,溶液温度为19℃~25℃;优选地,在正极与负极之间施加电流为0.5a/dm2~1a/dm2,例如0.5a/dm2、0.6a/dm2、0.7a/dm2、0.8a/dm2、0.9a/dm2、1.0a/dm2之中的任意电流及其二者之间的范围值,优选地为0.6a/dm2~0.8a/dm2;在正极与负极之间施加电流的时间为120s~3600s,优选地时间为600s~1800s。
[0018]
根据本发明是利用铜离子与铝发生置换反应,使铝反应成铝离子,而氧化铝则不与铜离子发生反应,从而将铝与氧化铝膜分离。为了使铜化合物的溶液与铝箔充分接触,将表面包含氧化铝膜的铝箔剪切去边缘,更好地是剪切成一定尺寸,不仅铜化合物与铝箔的接触面积增大,也可以使剥离下来的氧化铝膜粒径更加均匀。一般选用硫酸铜、氯化铜、硝酸铜、乙酸铜中的至少一种铜化合物的溶液,由于氯离子半径小,优选地为氯化铜。铜化合物的浓度影响铝箔溶解的速率以及片状氧化铝的粒径均匀性,步骤s3中铜化合物选自硫酸铜、氯化铜、硝酸铜、乙酸铜中的至少一种,优选地为氯化铜;铜化合物溶液中铜化合物的质量分数为0.5wt%~10wt%,例如0.5wt%、1wt%、2wt%、4wt%、6wt%、8wt%、10wt%之中的任意质量分数及其二者之间的范围值,优选地为1wt%~8wt%,更优选地为2wt%~6wt%;铜化合物溶液温度为25℃~60℃,优选地温度为35℃~50℃;浸渍时间为4h~24h,优选地为8~12h;优选地,铝箔浸渍于铜化合物溶液同时施加50~100w功率超声波分散。
[0019]
本发明中步骤s3铜化合物溶液中还包括0.1wt%~1wt%盐酸,例如0.1wt%、0.2wt%、0.4wt%、0.6wt%、0.8wt%、1.0wt%之中的任意质量分数及其二者之间的范围值,优选地含有0.2wt%~0.6wt%;为了提高铜化合物溶液在铝箔表面的附着性和渗透性,更优地加入0.01wt%~0.5wt%表面活性剂,优选地包括0.05wt%~0.1wt%表面活性剂;优选地表面活性剂选自烷基酚聚氧乙烯醚,十二烷基磺酸钠,十二烷基苯磺酸钠中的至少一种。
[0020]
本发明中,步骤s4将剥离下来的氧化膜,用超声波振荡分散,以降低其粒径,提高粒径一致性,超声波的功率一般为300w~500w,优选地功率为200w~400w;如果功率不能过大,容易将氧化铝膜震碎。超声波分散的时间为1h~24h,优选地时间为4h~8h。
[0021]
根据本发明的另一个方面,提供所述的片状氧化铝、根据所述的制备方法制备的片状氧化铝在功能涂层、颜料、填充剂、增韧剂、耐火材料中的应用。
[0022]
本发明的有益效果:
[0023]
1)本发明的片状氧化铝,厚度均匀,粒径尺寸大,可应用于功能涂层、填充剂、增韧剂、耐火材料等。
[0024]
2)本发明片状氧化铝的制备方法,工艺简单,反应简单易于控制、成本低,具有广阔的应用前景。
具体实施方式
[0025]
下面结合实施例详述本技术,但本技术不局限于这些实施例。
[0026]
根据本发明,提供一种片状氧化铝,其中值厚度为50nm~5000nm,优选地为100nm~1000nm,更优地为200~500nm;厚度偏差≤20%,优选地,厚度偏差≤10%;粒径分布d
10
~d
90
为10μm~500μm,优选地为20μm~200μm,更优选地为50μm~100μm。本发明的片状氧化铝厚度均匀性高,粒径大,可应用于功能涂层、填充剂、增韧剂、耐火材料等。
[0027]
下面进一步通过实施例以详细说明本发明。同样应理解,以下实施例只用于对本发明进行进一步说明,不能理解为对本发明保护范围的限制,本领域的技术人员根据本发明的上述内容作出的一些非本质的改进和调整均属于本发明的保护范围。下述示例具体的工艺参数等也仅是合适范围中的一个示例,即本领域技术人员可以通过本文的说明做合适的范围内选择,而并非要限定于下文示例的具体数值。
[0028]
实施例1~6:以1060铝箔为原材料,将100mm*50mm的有效面积浸入21℃,15wt%硫酸溶液中,以1060铝箔为正极与电源正极连接,以316不锈钢片为负极与电源负极连接,施加恒定电流一段时间,将1060铝箔用纯水清洗2次,用裁切机将铝箔的四个边缘剪切掉,浸入25℃10wt%氯化铜溶液中8h,用80目滤网过滤出氧化铝膜,将氧化铝膜分散在纯水中,置于超声波清洗机中,200w功率的超声波下分散24h,以光学显微镜测试本发明片状氧化铝的粒径分布,以扫描探针显微镜dimension icon测试片状氧化铝的厚度。实施例1~6的实验参数及性能如表1所示。
[0029]
表1实施例1~6的实验参数及性能
[0030][0031]
实施例7:与实施例4不同的是,10wt%硫酸溶液替换为10wt%硫酸和3wt%硼酸,其他与实施例4相同操作。
[0032]
实施例8:与实施例4不同的是,10wt%硫酸溶液替换为8wt%硫酸和2wt%柠檬酸混合溶液,其他与实施例4相同操作。
[0033]
实施例9:与实施例4不同的是,25℃10wt%氯化铜溶液替换为35℃1wt%硫酸铜和0.1wt%盐酸的混合溶液,其他与实施例4相同操作。
[0034]
实施例10:与实施例4不同的是,25℃10wt%氯化铜溶液替换为50℃2wt%氯化铜和0.1wt%十二烷基苯磺酸钠的混合溶液,其他与实施例4相同操作。
[0035]
实施例7
‑
10的性能与实施例4相近。
[0036]
以上所述,仅是本技术的几个实施例,并非对本技术做任何形式的限制,虽然本技术以较佳实施例揭示如上,然而并非用以限制本技术,任何熟悉本专业的技术人员,在不脱离本技术技术方案的范围内,利用上述揭示的技术内容做出些许的变动或修饰均等同于等效实施案例,均属于技术方案范围内。