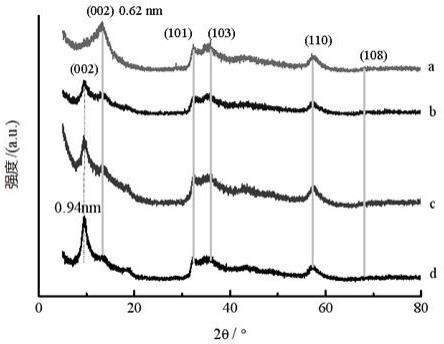
1.本发明是关于新能源,特别是关于一种硫化钼/氟化物主客体催化材料、制备方法及应用。
背景技术:2.利用可再生能源(光、风和水力发电)电解水制氢,可实现碳达峰与碳中和。贵金属铂电极因其析氢过电位低、塔菲尔斜率低而被认为是理想的电解水析氢材料。然而,贵金属资源有限,价格昂贵,因此难以在工业上大规模推广应用。为此,人们开发了非贵金属析氢电催化剂。硫化钼(mos2)因其结构中的硫棱边对氢的吸附类似于pt金属而备受关注。它有三种结构,分别为1t
‑
mos2, 2h
‑
mos2和3r
‑
mos2。1t
‑
mos2结构的八面体配位,具有金属性,属于亚稳态结构;2h
‑
mos2晶型中含有两个mo
‑
s单位,属于稳定态结构;3r
‑
mos2晶型比2h
‑
mos2晶型多了一个mo
‑
s单位,即含有三个mo
‑
s单位, 亦属于亚稳态结构。1t
‑
mos2和3r
‑
mos2稳定性不高,不是理想的析氢电催化剂;2h
‑
mos2比较稳定,但是其导电性差,因此,人们对硫化钼进行了掺杂,比如掺杂镍、钴等金属元素,提高了其析氢性能。上述方法是基于提高活性位点数,从而改善其析氢性能。但是掺杂不能改变离子通道的大小,其析氢能力和稳定性等方面有待提高。
3.公开于该背景技术部分的信息仅仅旨在增加对本发明的总体背景的理解,而不应当被视为承认或以任何形式暗示该信息构成已为本领域一般技术人员所公知的现有技术。
技术实现要素:4.本发明的目的在于提供一种硫化钼/氟化物主客体催化材料、制备方法及应用,其能够扩大硫化钼的离子通道,改善催化剂的微观结构,提升质子传递速率,增强了电化学反应过程中离子的流动性,降低了离子的流动阻力,提高了析氢电催化活性。
5.为实现上述目的,本发明的实施例提供了硫化钼/氟化物主客体催化材料,包括硫化钼基体以及层间插入剂,层间插入剂插入到硫化钼基体的(002)晶面之间,层间插入剂为氟化合物。
6.在本发明的一个或多个实施方式中,层间插入剂插入后的硫化钼基体的(002)晶面之间的面间距为不小于9.0
å
。
7.在本发明的一个或多个实施方式中,层间插入剂占催化材料的摩尔百分数在0.2~7.5%。本发明中层间插入剂在催化材料中的含量占比主要跟反应时层间插入剂的浓度有关。当然也不绝对地排除反应时间、溶剂、温度、压力等其他可能因素的影响。
8.在本发明的一个或多个实施方式中,层间插入剂为氟化钾或氟化钠。
9.在本发明的一个或多个实施方式中,硫化钼/氟化物主客体催化材料的制备方法,包括如下步骤,a、准备mos2基体材料;b、mos2基体材料加入含有层间插入剂的溶液中,在反应条件下降插入剂插入到硫化钼基体的(002)晶面之间。
10.在本发明的一个或多个实施方式中,步骤a为准备钼源溶液和硫源溶液,将硫源溶
液逐滴添加到钼源溶液中并充分混合,将混合液在高压水热反应釜加热反应至反应结束,分离、除杂、干燥获得mos2基体材料。优选的,钼源为钼酸盐,特别是钼酸钠、钼酸钾等。硫源优选为硫脲、硫代硫酸钠等。
11.在本发明的一个或多个实施方式中,步骤a中在高压水热反应釜加热反应为在200
‑
220℃,反应20
‑
24 h。
12.在本发明的一个或多个实施方式中,步骤b为准备层间插入剂溶液,将适量mos2基体材料加入层间插入剂溶液,并在高压水热反应釜加热反应至反应结束,分离、除杂、干燥获得硫化钼/氟化物主客体催化材料。
13.在本发明的一个或多个实施方式中,步骤b中在高压水热反应釜加热反应为在140
‑
200℃,反应7
‑
10h。
14.在本发明的一个或多个实施方式中,硫化钼/氟化物主客体催化材料在催化制氢中的应用。
15.与现有技术相比,本发明的催化材料,将氟化物插入到2h
‑
mos2材料的(002)晶面之间,以至(002)晶面的面间距从6.5
å
增加到9.0
å
之上,增强了电化学反应过程中离子的流动性,降低了离子的流动阻力,提高了析氢电催化活性,从而大大拓宽了电化学反应的离子通道,显著提高了电催化制备氢气的能力。并且本发明制得的氢气为高纯氢气,不含一氧化碳、硫化氢等使燃料电池电极材料中毒的污染物,且简单易行,绿色环保。
附图说明
16.图1是根据本发明一实施方式的不同样品的粉末衍射图, (a) 2h
‑
mos2; (b) kf0.5
‑
mos2; (c)kf0.6
‑
mos
2 和 (d)kf0.75
‑
mos2;图2是根据本发明一实施方式的不同样品的电催化析氢曲线,其中(a) mos2; (b)kf0.25
‑
mos2; (c)kf0.5
‑
mos2; (d)kf0.6
‑
mos2; (e) kf0.75
‑
mos2; (f)pt/c(10%); (g)kf1
‑
mos2。扫描速率为10 mv
·
s
‑1,电解质为1.0mol/l koh;图3是根据本发明一实施方式的mos2‑
kf主客体化合物的xps图;图4是根据本发明一实施方式的mos2‑
kf主客体化合物中钼元素的xps图;图5是根据本发明一实施方式的mos2‑
kf主客体化合物中硫元素的xps图;图6是根据本发明一实施方式的mos2‑
kf主客体化合物中钾元素的xps图;图7是根据本发明一实施方式的mos2‑
kf主客体化合物中氟元素的xps图。
具体实施方式
17.下面结合附图,对本发明的具体实施方式进行详细描述,但应当理解本发明的保护范围并不受具体实施方式的限制。
18.除非另有其它明确表示,否则在整个说明书和权利要求书中,术语“包括”或其变换如“包含”或“包括有”等等将被理解为包括所陈述的元件或组成部分,而并未排除其它元件或其它组成部分。
19.在现有技术中,对于mos2晶体材料的制备都是采用了钼源如钼酸钠等以及硫源如硫脲等,在高温高压下水热反应制备获得。本发明方案在研究中发现,第一步水热反应制备获得的mos2主体材料的晶体质量将极大地影响,第二步水热反应中,层间插入剂导入(002)
晶面之间的可行性。经过对比研究发现,如果第一步水热反应制备获得的mos2晶体材料的质量不高,则在第二步水热反应中发生坍塌,此时也就发生了晶格破坏、侵蚀。
20.本发明中通过严格调整第一步水热反应制备mos2主体材料的反应条件,从而获得高质量的晶体结构,以此高质量的晶体材料为凭借,在第二步水热反应中采用更高的反应条件,具有更高的反应温度、反应时间以及氟化物浓度,才能实现将氟化物插入mos2晶体的(002)晶面之间,进而获得了一种高质量的电化学制氢材料。
21.在本发明方案的实施过程中,为了实现对层间插入剂在催化材料中摩尔百分比含量的调整,选择了以0.05
‑
0.8mol/l的层间插入剂溶液与高质量的mos2晶体粉末进行反应,从而实现了层间插入剂占催化材料的摩尔百分数在0.2~7.5%范围间的调控。在经过实验统计发现,可以认为层间插入剂占催化材料的摩尔百分数与层间插入剂溶液浓度正相关,即在不考虑误差以及波动性的情形下,可以视作浓度为0.05m时,层间插入剂占催化材料的摩尔百分数在0.2%等,这里就不做一一举例。
22.实施例1称取2.42g(0.01mol)钼酸钠(na2moo4.2h2o),溶于30 ml去离子水中,并超声分散30分钟。另称取3.05g(0.04mol)硫脲[(nh2)2cs],溶于30ml去离子水中,超声分散30分钟。将硫脲水溶液逐滴加入到钼酸钠水溶液中,再将混合液超声分散30分钟。超声结束后,将混合水溶液定容至80ml并将其转入100 ml的内衬聚四氟乙烯的高压水热反应釜内,将反应釜密封,然后放入恒温箱中加热至200℃,反应24 h。待反应结束后,自然冷却,抽滤,用去离子水和乙醇洗涤至中性,去除可溶物。将最终得到的产物在真空干燥箱中60℃干燥6 h,制得mos2主体材料。
[0023]
称取kf(2.788g)溶解在80.0 ml 去离子水中以配制浓度为0.6 mol/l的kf溶液。然后,称取0.4 gmos2粉末加入到配制好的kf溶液中。将混合溶液转移到80ml内衬聚四氟乙烯的不锈钢高压釜中,密封并在140℃下保持10h。收集黑色产物并过滤,在真空室中60℃干燥6 h得到主客体kf
‑
mos2复合材料。
[0024]
本实施例获得的kf
‑
mos2复合材料中kf摩尔百分数约5.5%,需要注意的是这里的数据是多次统计平均获得的约数,而非精确值,其波动范围约
±
0.5%。
[0025]
实施例2称取2.42g(0.01mol)钼酸钠(na2moo4.2h2o),溶于30 ml去离子水中,并超声分散30分钟。另称取3.05g(0.04mol)硫脲[(nh2)2cs],溶于30ml去离子水中,也超声分散30分钟。将硫脲水溶液逐滴加入到钼酸钠水溶液中,再将混合液超声分散30分钟。超声结束后,将混合水溶液定容至80ml并将其转入100 ml的内衬聚四氟乙烯的高压水热反应釜内,将反应釜密封,然后放入恒温箱中加热至200℃,反应24 h。待反应结束后,自然冷却,抽滤,用去离子水和乙醇洗涤至中性,去除可溶物。将最终得到的产物在真空干燥箱中60℃干燥6 h,制得mos2主体材料。
[0026]
称取naf(2.015g)溶解在80.0 ml 去离子水中以配制浓度为0.6 mol/l的naf溶液。然后,称取0.4 g制得的mos2粉末加入到配制好的naf溶液中。将混合溶液转移到80ml内衬聚四氟乙烯的不锈钢高压釜中,密封并在160℃下保持9 h。收集黑色产物并过滤,在真空室中60℃干燥6 h得到主客体naf
‑
mos2复合材料。
[0027]
本实施例获得的naf
‑
mos2复合材料中naf摩尔百分数约5.5%,需要注意的是这里
的数据是多次统计平均获得的约数,而非精确值,其波动范围约
±
0.5%。
[0028]
实施例3称取2.42g(0.01mol)钼酸钠(na2moo4.2h2o),溶于30 ml去离子水中,并超声分散30分钟。另称取3.05g(0.04mol)硫脲[(nh2)2cs],溶于30ml去离子水中,也超声分散30分钟。将硫脲水溶液逐滴加入到钼酸钠水溶液中,再将混合液超声分散30分钟。超声结束后,将混合水溶液定容至80ml并将其转入100 ml的内衬聚四氟乙烯的高压水热反应釜内,将反应釜密封,然后放入恒温箱中加热至210℃,反应22h。待反应结束后,自然冷却,抽滤,用去离子水和乙醇洗涤至中性,去除可溶物。将最终得到的产物在真空干燥箱中60℃干燥6 h,制得mos2主体材料。
[0029]
称取naf(2.700g)溶解在80.0 ml 去离子水中以配制浓度为0.8 mol/l的naf溶液。然后,称取0.4 g制得的mos2粉末加入到配制好的naf溶液中。将混合溶液转移到80ml内衬聚四氟乙烯的不锈钢高压釜中,密封并在160℃下保持8 h。收集黑色产物并过滤,在真空室中60℃干燥6 h得到主客体naf
‑
mos2复合材料。
[0030]
本实施例获得的naf
‑
mos2复合材料中naf摩尔百分数约7.5%,需要注意的是这里的数据是多次统计平均获得的约数,而非精确值,其波动范围约
±
0.5%。
[0031]
实施例4:称取0.01mol钼酸钾(k2moo4.2h2o),溶于30 ml去离子水中,并超声分散30分钟。另称取3.05g(0.04mol)硫脲[(nh2)2cs],溶于30ml去离子水中,也超声分散30分钟。将硫脲水溶液逐滴加入到钼酸钠水溶液中,再将混合液超声分散30分钟。超声结束后,将混合水溶液定容至80ml并将其转入100 ml的内衬聚四氟乙烯的高压水热反应釜内,将反应釜密封,然后放入恒温箱中加热至220℃,反应20 h。待反应结束后,自然冷却,抽滤,用去离子水和乙醇洗涤至中性,去除可溶物。将最终得到的产物在真空干燥箱中60℃干燥6 h,制得mos2主体材料。
[0032]
称取naf(2.358g)溶解在80.0 ml 去离子水中以配制浓度为0.7mol/l的naf溶液。然后,称取0.4 g制得的mos2粉末加入到配制好的naf溶液中。将混合溶液转移到80ml内衬聚四氟乙烯的不锈钢高压釜中,密封并在200℃下保持8 h。收集黑色产物并过滤,在真空室中60℃干燥6 h得到主客体naf
‑
mos2复合材料。
[0033]
本实施例获得的naf
‑
mos2复合材料中naf摩尔百分数约6.5%,需要注意的是这里的数据是多次统计平均获得的约数,而非精确值,其波动范围约
±
0.5%。
[0034]
表1.氟化钾
‑
硫化钼复合物的衍射参数
*kf
0.5
‑
mos2、kf
0.6
‑
mos2和 kf
0.75
‑
mos
2 分别表示在0.5、0.6、0.75 mol/l kf溶液中制备的氟化钾
‑
硫化钼复合物,其余部分同理。
[0035]
如图1以及图2
‑
7所示的,本发明方案获得的样品其x
‑
衍射图谱,表明经过反应后,氟化钾
‑
硫化钼复合物仍然具有完整的晶体结构,与未进行第二反应的mos2晶体相比,晶体中晶面(002)的晶面间距提升至9.0
å
以上,表明本方案在充分保证晶格完整性的前提下,实现了氟化钠或氟化钾的有效引入晶面之间。
[0036]
本发明实施例中电化学析氢活性测试包括以下步骤:采用三电极体系对样品进行电催化析氢实验。工作电极的制备具体如下:称取0.10 g的待测样品和0.15 g的石墨粉,利用玛瑙研钵将二者进行研磨,得到充分混合的粉末样品,再向其中滴加0.1 ml的硅油,并充分搅拌得到颗粒细小,均匀的糊状样品。将该样品填入碳糊电极内,并进行打磨处理。以pt片电极作为对电极,饱和甘汞电极作为参比电极,电解质溶液为1.0 m浓度的koh。在常温常压下,进行lsv线性扫描测试,其中扫描速率为10 mv/s。所得析氢电催化曲线如图2所示。
[0037]
氟化钾
‑
硫化钼复合物的电催化析氢曲线如图2所示。在1.0 mol/l的koh溶液中,工作电极为石墨电极时,电位扫描窗口中并没有电催化析氢电流。以不同浓度合成的氟化钾
‑
硫化钼复合物在电流密度为10 ma
·
cm
‑2时,纯mos2的过电位为379mv,而在0.25,0.5,0.6,0.75mol/lkf中制备的复合物,其过电位分别为329 mv,315 mv, 208 mv, 233 mv。其过电位的降低值分别为50mv,64 mv,171 mv,146 mv。
[0038]
前述对本发明的具体示例性实施方案的描述是为了说明和例证的目的。这些描述并非想将本发明限定为所公开的精确形式,并且很显然,根据上述教导,可以进行很多改变和变化。对示例性实施例进行选择和描述的目的在于解释本发明的特定原理及其实际应用,从而使得本领域的技术人员能够实现并利用本发明的各种不同的示例性实施方案以及各种不同的选择和改变。本发明的范围意在由权利要求书及其等同形式所限定。