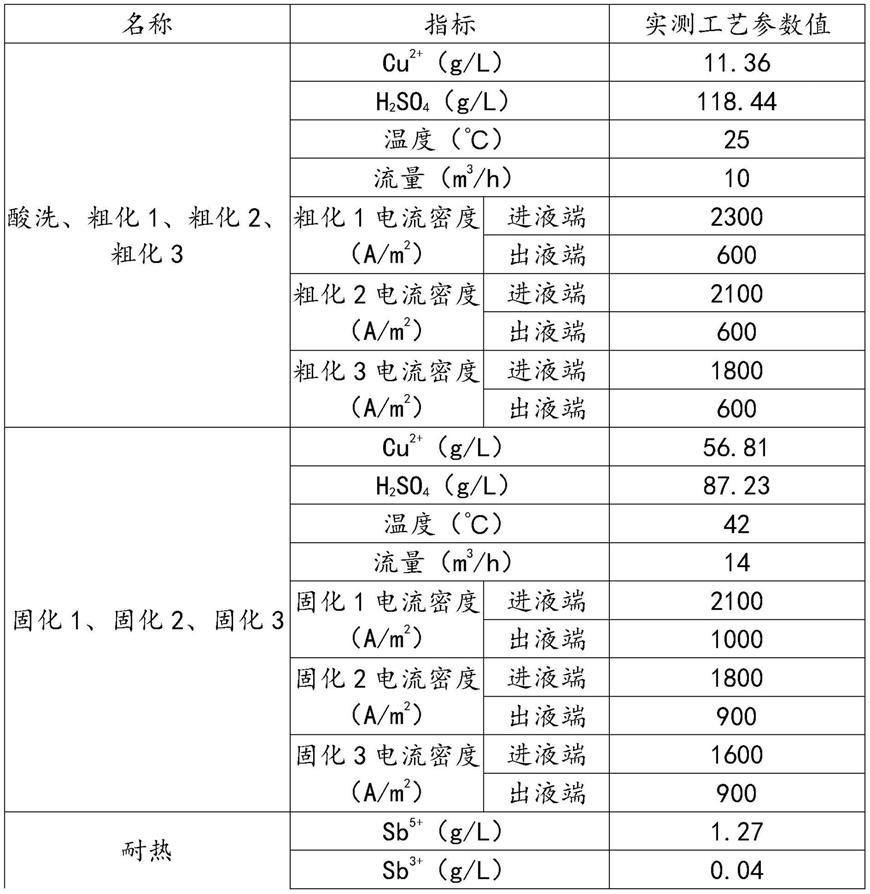
1.本发明属于铜箔表面处理技术领域,具体地,涉及一种提高低轮廓电解铜箔抗剥离强度的表面处理工艺。
背景技术:2.目前便携式电子产品朝轻薄化方向发展,应用功能不断增加,如手机、笔记本电脑、数码相机等,作为电子产品“内部神经”的线路板起关键作用,为达到减少体积和增加功能目的,线路板由双层、四层板已发展到高密度互连(hdi)板级别,线路层数已达到数十层,造成应用于制作hdi板的电解铜箔要求不断提高,尤其是铜箔的抗剥离强度和耐热性方面,都朝着低轮廓度高抗剥离强度方向发展(正常情况下,铜箔表面轮廓度越高,抗剥离强度则越高),同时要保证经受288℃的热冲击后,抗剥离强度不会发生大幅度下降。电解铜箔的抗剥离强度与铜箔毛面的粗糙度有直接关系,一般情况下粗糙度越低抗剥离强度就越低,尤其是低轮廓电解铜箔,如无合适的表面处理工艺,则无法应用到hdi板上。
3.如图1所示,目前低轮廓电解铜箔常规的表面处理流程:放卷、酸洗、粗化1、固化1、粗化2、固化2、粗化3、固化3、水洗、耐热1、水洗、耐热2、水洗、防氧化处理、水洗、硅烷涂覆、烘干、收卷,抗剥离强度主要依靠粗化和固化工序提升,剩余的由硅烷涂覆涂覆工序提升,按此工艺流程生产的低轮廓电解铜箔抗剥离强度容易出现偏低缺陷,且经过热冲击后抗剥离强度降幅在20-30%,应用在hdi板上时因抗剥离强度偏低容易造成细线路脱落缺陷。
技术实现要素:4.本发明的目的在于提供一种提高低轮廓电解铜箔抗剥离强度的表面处理工艺,通过将铜箔经过酸洗、3级粗化和3级固化处理后,在强酸性条件下电镀锌镍锑绒状结构合金耐热层,结合酸性防氧化处理,使两级耐热工序缩短至一级耐热处理工序,不但增加铜箔的抗剥离强度,还能缩短表面处理流程和提高铜箔的耐热性,使低轮廓电解铜箔在hdi板上的应用适应性更强,解决了现有技术中存在的问题。
5.本发明的目的可以通过以下技术方案实现:
6.一种提高低轮廓电解铜箔抗剥离强度的表面处理工艺,主要包括以下工序:放卷、酸洗、粗化1、固化1、粗化2、固化2、粗化3、固化3、水洗、耐热处理、水洗、防氧化处理、水洗、硅烷涂覆、烘干、收卷;
7.所述耐热处理的电镀液温度为25-45℃、sb
5+
为1.0-1.5g/l、sb
3+
为0.02-0.05g/l、zn
2+
为10-20g/l、ni
2+
为5-10g/l、ph为1.5-2.5、流量为3-9m3/h,铜箔光面电流密度为0a/m2,铜箔毛面电流密度为100-300a/m2;耐热处理的作用有两个,一是降低抗剥离强度热损失,二是避免铜金属直接与绝缘基材接触,因线路板受潮后,容易在两线路间形成电解池,造成铜离子迁移到基材表面,导致线路短路,在铜箔毛面电镀一层合金后,能有效防止这种现象。
8.耐热处理是本发明的创新点,常规的耐热处理是在电镀液中加入znso4和niso4,提
供zn、ni离子来源,以焦磷酸钾作为络合剂,用naoh或koh调整电镀液至强碱性再通上适当电流,在铜箔毛面电镀一层锌镍合金,然后还需要增加一级光、毛面强碱性焦磷酸钾镀锌处理,否则产品的抗氧化性和耐热性不能满足需求。
9.进一步地,酸洗的槽溶液温度为23-29℃、cu
2+
为8-14g/l、h2so4为100-140g/l、流量为5-15m3/h;酸洗是在电解生箔工序生产的卷状铜箔为纯铜,在空气中容易氧化,酸洗是利用稀硫酸溶解铜箔表面的氧化铜,达到去除氧化物目的,避免形成铜箔表面色差和内在物性不良。
10.进一步地,粗化1、粗化2和粗化3的电镀液温度为23-29℃、cu
2+
为8-14g/l、h2so4为100-140g/l、流量为5-15m3/h,进液端电流密度为1500-3100a/m2,出液端电流密度为400-800a/m2;通过粗化1、粗化2、粗化3工序在铜箔毛面电镀一层树枝状结晶铜瘤,以增加铜箔毛面比表面积,增加铜箔与绝缘基材的接触面,达到增加铜箔抗剥离强度效果。
11.进一步地,固化1、固化2和固化3的电镀液温度为38-48℃、cu
2+
为40-60g/l、h2so4为100-120g/l、流量为10-20m3/h,进液端电流密度为1300-2900a/m2,出液端电流密度为700-1300a/m2;粗化1、粗化2、粗化3在毛面电镀出来的铜瘤颗粒度较细(<1μm)且松散,容易脱落,所以在此基础上再电镀一层铜,将铜瘤直径加大(增加至1-3μm),增加铜瘤与铜箔之间的接触面,起到固定铜瘤作用。
12.进一步地,防氧化处理的电镀液温度为27-33℃、cr
6+
为0.5-1g/l、n i
2+
为2-4g/l、zn
2+
为0.4-0.8g/l、po
43-为0.4-0.8g/l、ph为3.5-4,流量为5-11m3/h,铜箔光面电流密度为50-100a/m2,铜箔毛面电流密度为50-100a/m2;防氧化处理的主要目的是在铜箔表面电镀一层金属防氧化层,防止铜箔在储存、使用过程中发生氧化现象。
13.本发明的防氧化处理与强碱性镀铬防氧化处理相比,除了有相同的抗氧化性能力外,因采用酸性镀液,可有效节省铜箔表面清洗水量,所以防氧化处理后,常规的防氧化为强碱性处理,需要两级水洗,而本发明的酸性防氧化处理只需要一级水洗即可达到要求。
14.进一步地,在粗化1、粗化2、粗化3、固化1、固化2、固化3的电镀槽中,槽体上端的金属导辊与整流电源的阴极相连,铜箔毛面与金属导辊紧密接触并保证接触面积占金属导辊面积的40%以上,使铜箔作为阴极;槽体中在铜箔毛面一侧安装有与铜箔平行的阳极板,阳极板与整流电源的阳极相连,阳极板为5mm厚钛板,表面涂有iro2和ta2o5的混合物,俗称dsa阳极;当整流电源通上适当电流后,金属离子沉积到铜箔毛面;通过控制表面处理机线速度和整流柜电流大小,可得到适当的金属离子沉积量。
15.进一步地,防氧化处理的电镀槽中铜箔光面一侧还安装有与铜箔平行的阳极板,阳极板与整流电源的阳极相连。
16.进一步地,水洗工序为使用纯水清洗,主要是清洗铜箔表面,防止各槽电镀液在箔面上残留及不同电镀槽间槽液污染,每个水洗槽共有4根水洗喷淋管,光面和毛面各两根。
17.进一步地,硅烷涂覆的槽溶液温度为15-35℃,喷涂流量为1-2m3/h,硅烷偶联剂的浓度为20-30ml/l;通过在铜箔毛面喷涂硅烷偶联剂,进一步增加铜箔抗剥离强度。
18.进一步地,烘干工序为利用石英加热烘箱加温,将经过偶联剂涂覆工序的铜箔表面烘干。
19.进一步地,放卷和收卷的线速度为20-30m/min。
20.电镀液中的cu
2+
在电镀过程中会不断消耗,补充方法是:在溶铜罐中放入适量的铜
料(铜线或铜板),铜料在高温下与空气中的o2发生氧化反应生成cuo,然后再与电镀液中的h2so4反应生成cuso4,补充电镀液中消耗的cu
2+
。
21.电镀液中的sb
3+
、sb
5+
、ni
2+
、zn
2+
、cr
6+
和po
43-通过加入c8h4k2o
12
sb2、niso4、znso4、cro3和h3po4补充,补充时取适量电镀液,加入上述化学品,搅拌至完全溶解后倒入电镀液储罐中循环均匀即可。
22.本发明所涉及的耐热性处理工艺,sb
3+
离子不需要额外添加,溶液中会自主生成,当超出0.05g/l的浓度范围时,添加适量的双氧水,sb
3+
离子发生氧化反应,生成sb
5+
离子,具体添加量按需减少的sb
3+
离子量计算。
23.本发明的有益效果:
24.本发明是在常规的表面处理工艺基础上,将两级耐热处理变更为一级耐热处理,耐热处理工序和防氧化处理工序的碱性电镀液变更为酸性电镀液,具体是在耐热处理电镀液中添加酒石酸锑钾、硫酸锌、硫酸镍等化学品,利用硫酸将电镀液调整为酸性,防氧化处理槽电镀液中添加铬酐、硫酸锌、硫酸镍、磷酸等化学品,按此表面处理工艺制得的低轮廓电解铜箔用高tg170℃无卤半固化片压制覆铜板时,12μm规格铜箔抗剥离强度≥0.90kgf/cm,18μm规格铜箔抗剥离强度≥1.10kgf/cm,热冲击测试288℃漂锡三次,每次10s(按gb/t 29847-2013 7.3条款规定的方法加严测试)处理后,其抗剥离强度热损失率<10%。
附图说明
25.为了更清楚地说明本发明实施例的技术方案,下面将对实施例描述所需要使用的附图作简单地介绍,显而易见地,下面描述中的附图仅仅是本发明的一些实施例,对于本领域普通技术人员来讲,在不付出创造性劳动的前提下,还可以根据这些附图获得其他的附图。
26.图1为常规低轮廓电解铜箔的表面处理工艺的流程图;
27.图2为本发明一种提高低轮廓电解铜箔抗剥离强度的表面处理工艺的流程图;
28.图3为本发明实施例1制得的铜箔毛面的sem图;
29.图4为本发明实施例2制得的铜箔毛面的sem图;
30.图5为本发明对比例1制得的铜箔毛面的sem图。
具体实施方式
31.下面将结合本发明实施例中的附图,对本发明实施例中的技术方案进行清楚、完整地描述,显然,所描述的实施例仅仅是本发明一部分实施例,而不是全部的实施例。基于本发明中的实施例,本领域普通技术人员在没有作出创造性劳动前提下所获得的所有其它实施例,都属于本发明保护的范围。
32.实施例1
33.请参阅图2所示,一种提高低轮廓电解铜箔抗剥离强度的表面处理工艺,主要包括以下工序:放卷、酸洗、粗化1、固化1、粗化2、固化2、粗化3、固化3、水洗、耐热处理、水洗、防氧化处理、水洗、硅烷涂覆、烘干、收卷;
34.各工序的实测工艺参数值如下表1所示:
35.表1
36.[0037][0038]
该实施例制得的铜箔毛面的微观形貌特征请参阅图3所示。
[0039]
实施例2
[0040]
请参阅图2所示,一种提高低轮廓电解铜箔抗剥离强度的表面处理工艺,主要包括以下工序:放卷、酸洗、粗化1、固化1、粗化2、固化2、粗化3、固化3、水洗、耐热处理、水洗、防氧化处理、水洗、硅烷涂覆、烘干、收卷;
[0041]
各工序的实测工艺参数值如下表2所示:
[0042]
表2
[0043]
[0044]
[0045][0046]
该实施例制得的铜箔毛面的微观形貌特征请参阅图4所示。
[0047]
对比例1
[0048]
请参阅图1所示,一种提高低轮廓电解铜箔抗剥离强度的表面处理工艺,主要包括以下工序:放卷、酸洗、粗化1、固化1、粗化2、固化2、粗化3、固化3、水洗、耐热1、水洗、耐热2、水洗、防氧化处理、水洗、硅烷涂覆、烘干、收卷;
[0049]
各工序的实测工艺参数值如下表3所示:
[0050]
表3
[0051]
[0052][0053]
该对比例制得的铜箔毛面的微观形貌特征请参阅图5所示。
[0054]
将实施例1-2和对比例1处理得到的铜箔用高tg170℃无卤半固化片压制成覆铜板,然后按照gb/t 29847-2013 7.3条款规定的方法,热冲击试验条件加严,按288℃漂锡三次,每次10s条件执行,测试热冲击前后抗剥离强度并计算出热损失率,测试数据如下表4所示:
[0055]
表4
[0056][0057]
由表4测试数据可知,与对比例1相比实施例1-2处理后得到的低轮廓电解铜箔的抗剥离强度更高,且在加严热冲击之后,仍具有较高的抗剥离强度,抗剥离强度热损失率远低于常规工艺,具有较好的耐热性。
[0058]
在说明书的描述中,参考术语“一个实施例”、“示例”、“具体示例”等的描述意指结合该实施例或示例描述的具体特征、结构、材料或者特点包含于本发明的至少一个实施例或示例中。在本说明书中,对上述术语的示意性表述不一定指的是相同的实施例或示例。而且,描述的具体特征、结构、材料或者特点可以在任何的一个或多个实施例或示例中以合适的方式结合。
[0059]
以上内容仅仅是对本发明的构思所作的举例和说明,所属本技术领域的技术人员对所描述的具体实施例做各种各样的修改或补充或采用类似的方式替代,只要不偏离发明的构思或者超越本权利要求书所定义的范围,均应属于本发明的保护范围。