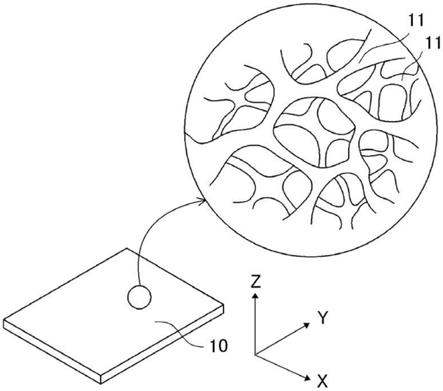
1.本发明涉及金属多孔体及金属多孔体的制造方法。本技术要求2020年3月27日提交的日本技术第2020
‑
057177号的优先权,引用所述日本技术所记载的全部记载内容。
背景技术:2.具有三维网状结构的骨架的片状金属多孔体被用于需要耐热性的过滤器、电池用电极片、催化剂担载体以及金属复合材料等各种用途。例如,作为镍制金属多孔体的celmet(住友电气工业株式会社制:注册商标)被广泛应用于镍氢电池等碱蓄电池的电极、工业用除臭催化剂的载体等各种工业领域。此外,作为铝制金属多孔体的aluminum
‑
celmet(住友电气工业株式会社制:注册商标)由于在有机电解液中也稳定,所以能够用作锂离子电池的正极。
3.所述金属多孔体能够通过如下方式制造:对具有三维网状结构的骨架的树脂多孔体的骨架的表面进行导电化处理后,通过电镀处理对所述树脂多孔体的骨架的表面实施金属镀覆,接下来除去树脂多孔体(例如参考专利文献1、专利文献2)。作为所述树脂多孔体,能够优选使用例如聚氨酯树脂。
4.现有技术文献
5.专利文献
6.专利文献1:日本特开平05
‑
031446号公报;
7.专利文献2:日本特开2011
‑
225950号公报。
技术实现要素:8.本发明的一个实施方式的金属多孔体是具有三维网状结构的骨架的平板状金属多孔体,包含多个单元,
9.在将所述金属多孔体的厚度方向的单元直径和与厚度方向正交的方向的单元直径的比(厚度方向的单元直径/与厚度方向正交的方向的单元直径)设为单元直径比的情况下,满足以下式(1)和式(2):
10.0.4≤单元直径比≤1.0 式(1),
11.0.50<与厚度方向正交的方向的单元直径/(金属多孔体的厚度/单元直径比)≤1.50式(2)。
附图说明
12.图1是表示本发明的金属多孔体的一个例子的概要的图。
13.图2是本发明的金属多孔体的一个例子的截面照片。
14.图3是本发明的金属多孔体的三维网状结构的结构单位的示意图。
15.图4是表示具有三维网状结构的骨架的金属多孔体的孔隙率(%)与压缩率(%)的关系的图。
16.图5是表示在本发明的金属多孔体的制造方法的一个例子中,将金属多孔体在与厚度方向正交的方向切断的工序的概要的图。
具体实施方式
17.[本发明要解决的问题]
[0018]
在使用聚氨酯树脂来作为树脂多孔体的情况下,首先,通过剥离(peeling)或者切片将块状的聚氨酯树脂加工成平板状。接下来对聚氨酯树脂的骨架的表面进行导电化处理。在对骨架的表面被导电化处理后的所述树脂多孔体施加金属镀覆时,在电镀液中对所述树脂多孔体附加某种程度的张力。在将聚氨酯树脂进行剥离或者切片、或者进行导电处理、电镀处理时,为了树脂多孔体维持三维网状结构的骨架,树脂多孔体的厚度需要是与厚度方向正交的方向的单元直径的2倍以上。因此,例如为了制造厚度为1.0mm的金属多孔体,需要使用与厚度方向正交的方向的单元直径为0.50mm以下的树脂多孔体。换言之,在使用厚度为1.0mm以下的树脂多孔体的情况下,不能够制造与厚度方向正交的方向的单元直径大于0.50mm的金属多孔体。
[0019]
作为制造厚度为1.0mm以下的金属多孔体的方法,也可以考虑例如先制造厚度大于1.0mm的金属多孔体再将其压延成厚度为1.0mm以下的方法。然而,在通过压延使厚度为1.0mm以下的金属多孔体中,单元在厚度方向被压塌,结果孔隙率变小。因此,在将通过压延使厚度为1.0mm以下的金属多孔体用作例如过滤器情况下,存在压力损失增大的问题。
[0020]
因此本发明的目的在于提供一种厚度小于与厚度方向正交的方向的单元直径的2倍的平板状金属多孔体。
[0021]
[本发明的实施方式的说明]
[0022]
首先,列举本发明的实施方式进行说明。
[0023]
[1]本发明的一个实施方式的金属多孔体是具有三维网状结构的骨架的平板状金属多孔体,包含多个单元,
[0024]
在将上述金属多孔体的厚度方向的单元直径和与厚度方向正交的方向的单元直径的比(厚度方向的单元直径/平面方向的单元直径)设为单元直径比的情况下,满足以下式(1)和式(2):
[0025]
0.4≤单元直径比≤1.0 式(1),
[0026]
0.50<与厚度方向正交的方向的单元直径/(金属多孔体的厚度/单元直径比)≤1.50式(2)。
[0027]
根据本实施方式,能够提供一种厚度小于与厚度方向正交的方向的单元直径的2倍的平板状金属多孔体。
[0028]
[2]上述金属多孔体的上述与厚度方向正交的方向的单元直径可以大于0.4mm且为1.70mm以下。
[0029]
根据本实施方式,能够提供一种即使与厚度方向正交的方向的单元直径大于0.4mm,厚度也为0.8mm以下的金属多孔体。
[0030]
[3]上述金属多孔体的厚度可以为0.5mm以上且1.2mm以下。
[0031]
根据本实施方式,能够提供一种即使厚度非常薄为1.2mm以下,与厚度方向正交的方向的单元直径也大于0.6mm的金属多孔体。
[0032]
[4]上述金属多孔体的孔隙率可以为94%以上且99%以下。
[0033]
根据本实施方式,能够提供一种孔隙率高的金属多孔体。
[0034]
[5]上述金属多孔体的单位面积重量可以为100g/m2以上且250g/m2以下。
[0035]
根据本实施方式,能够提供一种非常轻质的金属多孔体。
[0036]
另外,单位面积重量是指相对于根据俯视金属多孔体时的外形算出的面积的金属多孔体的重量。
[0037]
[6]本发明的一个实施方式的金属多孔体的制造方法是制造上述[1]中所述的金属多孔体的方法,包括:
[0038]
对具有三维网状结构的骨架的平板状的树脂多孔体的骨架的表面进行导电化处理的工序;
[0039]
接下来在上述树脂多孔体的上述骨架的表面镀覆金属的工序;
[0040]
接下来除去上述树脂多孔体来得到厚板状金属多孔体的工序;以及
[0041]
接下来将上述厚板状金属多孔体在与厚度方向正交的方向切断,得到金属多孔体的工序。
[0042]
根据本实施方式,可以提供一种能够制造厚度小于与厚度方向正交的方向的单元直径的2倍的平板状金属多孔体的方法。
[0043]
[7]上述金属多孔体的制造方法可以进一步包括:
[0044]
将在上述与厚度方向正交的方向切断了的上述金属多孔体在厚度方向进行压缩的工序。
[0045]
根据本实施方式,可以提供一种能够更稳定地保持平板形状的金属多孔体的制造方法。
[0046]
[本发明的实施方式的详细内容]
[0047]
以下对本发明的实施方式的金属多孔体以及金属多孔体的制造方法的具体例进行更详细的说明。另外,本发明并不限定于这些示例,而是由权利要求的范围所表示的,意在包含与权利要求的范围等同的含义和范围内的全部变更。
[0048]
<金属多孔体>
[0049]
以下一边参考图1至图3一边说明本发明的实施方式的金属多孔体10的各结构。
[0050]
金属多孔体10具有三维网状结构的骨架11。金属多孔体10整体上具有平板状的外观。为了容易理解三维网状结构,在图3中,将三维网状结构的结构单位当作正十二面体。三维网状结构的结构单位包含一个单元12。如图2、图3所示,单元12包含气孔13,气孔13是由三维网状结构的骨架11形成的立体状的空间。在将三维网状结构的结构单位当作正十二面体时,单元直径规定为正十二面体的最长对角线。
[0051]
骨架11典型地是由金属或合金的膜构成的,骨架11的内部是中空的。
[0052]
作为构成骨架11的金属,可以举出例如镍、铝或铜等。此外,作为构成骨架11的合金,能够举出通过在上述金属中不可避免地或者有意地添加其他金属而合金化的合金。作为构成骨架11的合金,能够举出例如铬、钴和锡等与镍合金化所成的合金(nicr、nico、nisn等)。此外,骨架11也可以通过在上述金属或者上述合金的表面进一步镀覆其他金属而成为具有两层以上金属或合金的膜的层叠结构。
[0053]
金属多孔体10如上所述包含作为立体状空间的气孔13并且具有三维网状结构。因
此能够与仅具有平面状的孔的二维网状结构体(例如冲孔金属、网格等)明确区分。
[0054]
进而,如图1至图3所示,金属多孔体10由于具有三维网状结构的骨架11,所以能够与纤维互相缠绕而形成的无纺布等那样的结构体明确区分。
[0055]
金属多孔体10由于具有这样的三维网状结构,所以具有从表面连结到内部的多个气孔。
[0056]
金属多孔体10的与厚度方向(图1中的z轴方向)正交的方向(图1中的与x
‑
y平面平行的平面中的任意方向)的单元直径是指:用显微镜等在至少10个视场观察金属多孔体10的主面,求出每1英寸(25.4mm=25400μm)的单元12的平均数量(nc),通过以下式(3)计算出的值。
[0057]
与厚度方向正交的方向的单元直径=25400μm/nc式(3)
[0058]
另外,单元数的测量依据jis k6400
‑
1:2004附件1(参考)中软质发泡材料的单元数的求取方法来进行(试验片尺寸的规定除外)。
[0059]
金属多孔体10的厚度方向的单元直径是指:通过以下式(4)计算出的值、或者是实际测量金属多孔体10的厚度方向的截面的单元直径的值。
[0060]
厚度方向的单元直径=与厚度方向正交的方向的单元直径
×
(1
‑
压缩率/100)
ꢀꢀ
式(4)
[0061]
另外,式(4)中的压缩率(%)能够从图5所示的表示孔隙率与压缩率的关系的图表中求取。在图5中,纵轴表示金属多孔体的孔隙率(%),横轴表示金属多孔体的压缩率(%)。
[0062]
此外,在实际测量金属多孔体10的厚度方向的截面的单元直径的情况下,将如下测量的值作为厚度方向的单元直径。
[0063]
首先,将金属多孔体10包埋于树脂并在厚度方向切断,观察其截面。接下来,在上述截面中任意画出十个单元12的圆周,算出它们的单元直径的平均值。
[0064]
金属多孔体10的孔隙率定义为下述式(5)。
[0065]
孔隙率(%)=[1
‑
{mp/(vp
×
dp)}]
×
100 式(5)
[0066]
mp:金属多孔体的质量[g]
[0067]
vp:金属多孔体的外观的形状的体积[cm3]
[0068]
dp:构成金属多孔体的金属的密度[g/cm3]
[0069]
金属多孔体10的厚度能够通过例如数字测厚仪测量。
[0070]
式(1)中单元直径比表示制造后的金属多孔体10在厚度方向被压缩的程度。单元直径比可以为0.4以上且1.0以下,优选为0.5以上且1.0以下,更优选为0.7以上且1.0以下。
[0071]
单元12的形状由于能够模型化成正十二面体,所以在金属多孔体10没有通过压延等在厚度方向被压缩的情况下,厚度方向的单元直径和与厚度方向正交的方向的单元直径没有差异。因此,单元直径比为1.0的情况意味着金属多孔体10在制造后在厚度方向没有被压缩。因此,例如在将金属多孔体10用作过滤器的情况下,从减小压力损失的观点出发,优选单元直径比接近1.0。另外,单元直径比为0.4的情况意味着金属多孔体10的厚度方向的压缩率为60%。
[0072]
另外,金属多孔体10的压缩率如上所述可以根据图4所示的图表求取,但在已知金属多孔体10的压缩前和压缩后的厚度的情况下,也能够通过压缩率(%)=(1
‑
(金属多孔体的压缩后的厚度/金属多孔体的压缩前的厚度))
×
100来算出。
[0073]
在式(2)中,“(金属多孔体的厚度/单元直径比)”表示在厚度方向压缩前的金属多
孔体10的厚度。这是因为如上所述单元直径比表示金属多孔体10在厚度方向被压缩的程度,因此通过压缩后的金属多孔体10的厚度除以单元直径比可以计算出压缩前的金属多孔体10的厚度。
[0074]
金属多孔体10的与厚度方向正交的方向的单元直径根据金属多孔体10的用途适当选择即可。作为一个例子,可以举出与厚度方向正交的方向的单元直径优选大于0.40mm且为1.70mm以下,更优选为0.5mm以上且1.1mm以下,进一步优选为1.0mm以下。
[0075]
金属多孔体10的与厚度方向正交的方向的单元直径即使大于0.40mm,也能够使厚度达到例如1.0mm以下或0.5mm以下。因此,例如将金属多孔体10用作过滤器的情况下能够做得薄而孔不至于过细,也能够减小压力损失。此外,在用作电池的电极的情况下能够提高活性物质的填充性,在用作氢发生装置的电极的情况下能够提高在电极产生的气体的逸出性。
[0076]
金属多孔体10的厚度根据金属多孔体10的用途适当选择即可。作为一个例子,金属多孔体10的厚度优选为0.5mm以上且1.2mm以下。
[0077]
金属多孔体10即使厚度为1.2mm以下,也能够使与厚度方向正交的方向的单元直径大于0.6mm。
[0078]
金属多孔体10如果在厚度方向没有被压缩,则具有除去在制造时用作基材的树脂多孔体的体积份的孔隙率。金属多孔体10的孔隙率根据压缩率以图4所示图表的方式变化。例如,即使金属多孔体10被压延至压缩率为60%左右,金属多孔体10的孔隙率也依然大于90%。
[0079]
金属多孔体10的孔隙率根据金属多孔体10的用途适当选择即可。作为一个例子,金属多孔体10的孔隙率优选为94%以上且99%以下,更优选为96%以上且99%以下,进一步优选为97%以上且99%以下。
[0080]
金属多孔体10的单位面积重量根据金属多孔体10的用途适当选择即可。在需要非常轻质的金属多孔体的情况下,优选例如金属多孔体10的单位面积重量为100g/m2以上且250g/m2以下。金属多孔体10由于是通过将基于所谓电镀法制造的金属多孔体在与厚度方向正交的方向切断而得到的,所以单位面积重量是切断前的金属多孔体的单位面积重量的1/2以下。因此,容易提供非常轻质的金属多孔体10。当然,根据金属多孔体的用途,也可以提供单位面积重量大的金属多孔体。
[0081]
<金属多孔体的制造方法>
[0082]
本发明的实施方式的金属多孔体的制造方法包括:对具有三维网状结构的骨架的平板状的树脂多孔体的骨架的表面进行导电化处理的工序;在上述骨架的表面被导电化处理后的上述树脂多孔体的骨架的表面镀覆金属的工序;在镀覆了上述金属后除去上述树脂多孔体来得到金属多孔体的工序;以及将除去上述树脂多孔体而得到的金属多孔体在与厚度方向正交的方向切断的工序。以下对各工序进行详细叙述。
[0083]
(对树脂多孔体的骨架的表面进行导电化处理的工序)
[0084]
在该工序中,首先,准备具有三维网状结构的骨架的平板状的树脂多孔体(以下仅记为“树脂多孔体”)。作为树脂多孔体,能够使用聚氨酯树脂、三聚氰胺树脂等。
[0085]
树脂多孔体用作制造金属多孔体时的基材。因此,树脂多孔体的与厚度方向正交的方向的单元直径、孔隙率以及厚度只要与作为制造目标的金属多孔体相同即可。
[0086]
接下来,通过在树脂多孔体骨架的表面涂布含有碳粉末等导电性粉末的涂料,对树脂多孔体的骨架的表面进行导电化处理。作为碳粉末,可以举出例如炭黑等非晶碳粉末、石墨等碳粉末。
[0087]
(镀覆金属的工序)
[0088]
该工序是将骨架的表面被导电化处理后的树脂多孔体用作基材,镀覆金属的工序。由于树脂多孔体的骨架的表面被导电化处理,所以金属的镀覆优选通过电镀来进行。
[0089]
镀覆在树脂多孔体上的金属的种类没有特别限定。金属的种类根据金属多孔体的用途适当选择即可。例如,在为镍、铝或铜等金属的情况下,能够通过公知的镀覆方法进行电镀。另外,也可以镀覆两种以上的金属而合金化。例如,能够在镀覆镍后,镀覆铬、钴、锡等而与镍合金化。另外,也能够通过镀覆两种以上金属,使金属多孔体10的骨架11成为具有两层以上金属或合金的膜的层叠结构。
[0090]
金属的镀覆量没有特别限定,以使要制造的金属多孔体10具有优选单位面积重量的方式来调整镀覆量即可。另外,金属多孔体10是通过将除去镀覆了金属的树脂多孔体所得到的金属多孔体在与厚度方向正交的方向切断而得到的。因此,对于镀覆金属的工序中金属的镀覆量,注意将金属多孔体10的单位面积重量调整成切断前的金属多孔体的单位面积重量的1/2以下即可。
[0091]
(除去树脂多孔体的工序)
[0092]
该工序是从骨架的表面形成有金属或合金的膜的结构体中除去用作基材的树脂多孔体的工序。树脂多孔体的除去能够通过例如在大气等氧化性环境下,以600℃以上且800℃以下左右、优选以600℃以上且700℃以下左右的温度进行热处理来实施。由此,烧去用作基材的树脂多孔体,得到骨架由上述金属或合金的膜形成的金属多孔体。另外,在除去树脂多孔体后,可以根据需要在还原性环境下进行热处理,对氧化了的金属或合金进行还原。
[0093]
(切断金属多孔体的工序)
[0094]
如图5所示,该工序是通过将除去树脂多孔体所得到的厚板状金属多孔体20在与厚度方向(图1中的z轴方向)正交的方向切断而得到本实施方式的金属多孔体10的工序。如上所述,当用作基材的树脂多孔体不具有与厚度方向正交的方向的单元直径的2倍以上的厚度时,不能够保持三维网状结构的骨架,结构被破坏。与此相对,本发明人发现,如果镀覆了金属之后,骨架的强度增大,能够以厚度小于与厚度方向正交的方向的单元直径的2倍的方式切断金属多孔体。在该工序中,只要以能得到满足式(2)的金属多孔体10的方式切断厚板状金属多孔体20即可。
[0095]
切断厚板状金属多孔体20的方法没有特别限定,例如用夹具将厚板状金属多孔体20的主面彼此固定,通过旋转刀具等将主面之间切断即可。此外,在图5所示的例子中,将厚板状金属多孔体20在与厚度方向z正交的方向分为两份,也可以分为三份以上。例如,如果是使用厚度为2.0mm左右的树脂多孔体制造的厚板状金属多孔体20,则能够将其分为三份而得到厚度为约0.66mm的三片金属多孔体10。
[0096]
(压缩金属多孔体的工序)
[0097]
该工序是将在与厚度方向正交的方向切断了的金属多孔体10在厚度方向进行压缩的工序。通过将金属多孔体10在厚度方向进行压缩能够使金属多孔体10成为期望的厚
度,此外,可更稳定地保持平板形状,提高操作性。当在厚度方向压缩金属多孔体10时,单元12被压塌,孔隙率变小。因此,在满足式(1)的范围内,根据金属多孔体10的利用用途压缩成优选的厚度和孔隙率即可。
[0098]
实施例
[0099]
以下,基于实施例更详细地对本发明进行说明。这些实施例只不过是示例,本发明的金属多孔体等并不限定于这些实施例。
[0100]
[实施例1]
[0101]
作为具有三维网状结构的骨架的树脂多孔体,准备厚度为2.0mm的聚氨酯片。树脂多孔体的孔隙率为96%。与厚度方向正交的方向的单元直径为0.85mm。
[0102]
通过将聚氨酯片浸渍在碳悬浮液中并使其干燥来进行聚氨酯片的骨架表面的导电化处理。碳悬浮液的成分为:含有25%的石墨和炭黑,并含有树脂粘结剂、渗透剂以及消泡剂。炭黑的粒径为0.5μm。
[0103]
在对骨架的表面进行了导电化处理的聚氨酯片的骨架的表面镀覆镍,使得单位面积重量为500g/m2。镍的镀覆采用瓦特浴(硫酸镍300g/l、氯化镍50g/l、硼酸30g/l)来进行。
[0104]
镀覆镍后,通过以650℃加热10分钟,烧去用作基材的聚氨酯片。然后在除去聚氨酯片后,进一步在h2∶n2=3∶1的环境中以1000℃进行20分钟的热处理,由此对氧化了的镍进行还原处理。
[0105]
如图5所示,将进行了还原处理后的金属多孔体在与厚度方向z正交的方向切断成两片。由此,得到两片厚度为1.0mm的金属多孔体no.1。
[0106]
[实施例2]
[0107]
将在实施例1中制造的金属多孔体no.1在厚度方向进行压缩使其厚度为0.5mm,制造了金属多孔体no.2。
[0108]
[实施例3]
[0109]
使用厚度为3.0mm、与厚度方向正交的方向的单元直径为0.85mm、孔隙率为96%的聚氨酯片,进而将进行了还原处理后的金属多孔体在与厚度方向z正交的方向切断成三片。其他条件与实施例1相同,制造了三片金属多孔体no.3。
[0110]
[实施例4]
[0111]
将在实施例3中制造的金属多孔体no.3在厚度方向进行压缩使其厚度为0.5mm,制造了金属多孔体no.4。
[0112]
[实施例5]
[0113]
使用厚度为2.0mm、与厚度方向正交的方向的单元直径为0.54mm、孔隙率为96%的聚氨酯片。其他条件与实施例1所记载的制造方法相同,制造了厚度为1.0mm的金属多孔体no.5。
[0114]
[实施例6]
[0115]
将在实施例5中制造的金属多孔体no.5在厚度方向进行压缩使其厚度为0.5mm,制造了金属多孔体no.6。
[0116]
[实施例7]
[0117]
使用厚度为2.5mm、与厚度方向正交的方向的单元直径为1.27mm、孔隙率为96%的聚氨酯片。其他条件与实施例1所记载的制造方法相同,制造厚度为约1.2mm的金属多孔体,
将其进行压延使得厚度为1.0mm,制造了金属多孔体no.7。
[0118]
[实施例8]
[0119]
将在实施例7中制造的金属多孔体no.7在厚度方向进行压缩使其厚度为0.5mm,制造了金属多孔体no.8。
[0120]
[比较例1]
[0121]
将在实施例1所记载的制造方法中进行了还原处理后的金属多孔体不切断,而进行压缩使其厚度为0.5mm。其他条件与实施例1相同,制造了金属多孔体no.9。
[0122]
[比较例2]
[0123]
将在实施例7中进行了还原处理后的金属多孔体在与厚度方向z正交的方向切断成三片。其他条件与实施例7相同,制造了三片金属多孔体no.10。金属多孔体no.10的厚度应为约0.8mm。但是,金属多孔体no.10超过了式(2)的数值范围,因此难以维持三维网状结构的骨架,由于切断工序的作业中、作业后的少量冲击,骨架就发生了折断,三维网状结构的大部分都损坏。在表1示出了切断工序后应得到的金属多孔体的各种数值。
[0124]
[比较例3]
[0125]
准备了厚度为1.0mm、与厚度方向正交的方向的单元直径为0.54mm、孔隙率为96%的聚氨酯片。但是,聚氨酯片不能够维持三维网状结构的骨架,三维网状结构的大部分都损坏。
[0126]
在表1示出关于金属多孔体no.1至no.10的结构的各测量值和计算值。
[0127]
[表1]
[0128][0129]
如表1所示,金属多孔体no.1至no.8均为“与厚度方向正交的方向的单元直径/(金属多孔体的厚度/单元直径比)”大于0.5、厚度小于与厚度方向正交的方向的单元直径的2倍的金属多孔体。因此,即使厚度为0.5mm左右,也能够保持高孔隙率。此外,能够制造即使厚度为1.0mm以下,厚度方向的单元直径也为0.50mm以上的金属多孔体。孔隙率大、单元直径大的金属多孔体能够优选用于例如压力损失少的过滤器。
[0130]
根据本发明的实施方式的金属多孔体,能够根据金属多孔体的用途选择更优选的单元直径、孔隙率、厚度、单位面积重量。
[0131]
附图标记说明
[0132]
10:金属多孔体;
[0133]
11:骨架;
[0134]
12:单元;
[0135]
13:气孔;
[0136]
20:厚板状金属多孔体。