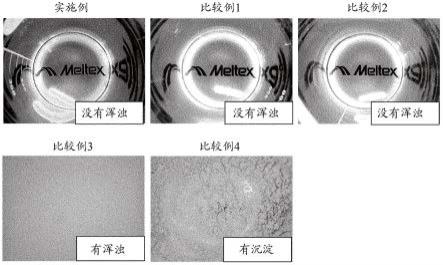
1.本发明涉及一种用于滚镀的镀锡液,特别是涉及一种抑制在使用以往的镀锡液的情况下出现的霉菌的产生的镀锡液。
背景技术:2.一直以来,镀锡液在电子部件材料领域中被广泛用作端子镀敷、防氧化腐蚀用镀敷的镀敷液。近年来,由于对无铅焊料的需求,还使用镀锡来代替焊料镀敷。
3.即使在使用镀锡液的技术领域中,在作为芯片部件的叠层陶瓷电容器的领域中,通常也在该叠层陶瓷电容器的外部电极的表面形成镀锡层。对于该叠层陶瓷电容器的外部电极的镀锡层而言,焊料润湿性优异,作为在经过回流焊等表面安装工艺而表面安装于印刷电路板时有用的镀层发挥功能。
4.作为对上述芯片部件那样的小部件进行镀锡的方法,有使用被称为滚筒的容器的方法。通过将投入有被镀敷物的滚筒浸渍于镀锡液中并在使滚筒旋转的同时进行镀敷,能够一次性大量地镀敷小的被镀敷物。
5.用于滚镀的普通镀锡液除了包含作为锡离子供给源的锡盐以外还包含各种无机酸和有机酸、ph值调节剂等添加物。具体而言,专利文献1公开了一种镀锡液,其建浴后的溶液寿命长、长期保存性优异、并且能够在超过30℃的浴温下使用。
6.现有技术文献
7.专利文献
8.专利文献1:日本公开专利公报“特开2006-328528号公报”
技术实现要素:9.发明要解决的课题
10.有时将专利文献1中公开的镀锡液的ph值从弱酸性调节至接近中性,且在超过30℃那样的浴温环境下进行镀浴和随后的水洗。此时,由于镀敷液的ph值接近中性、且在超过30℃的浴温环境下,而且镀敷液中包含成为霉菌的营养素的柠檬酸等有机酸,因此,有时会出现如下问题:在镀敷工序后的水洗工序的水洗水中产生霉菌,所产生的霉菌附着在被镀敷物上而使镀敷品质变差。
11.因此,为了防止在水洗工序中产生霉菌,考虑在水洗水中投入防霉剂。然而,由于水洗水大量地使用,因此需要大量地投入防霉剂,从而存在使用的防霉剂的成本变高、需要向水洗水中投入防霉剂的工序等问题。
12.本发明是鉴于这样的情况而完成的,其目的在于提供在镀锡工序后的水洗工序中即使在超过30℃的浴温环境下也能够抑制水洗水中产生霉菌的滚镀用镀锡液。
13.用于解决课题的技术手段
14.为了解决该课题,经过潜心研究,结果想出了以下的发明。
15.为了实现上述目的,本发明的滚镀用镀锡液的特征在于,其是在滚镀中使用的镀
锡液,所述滚镀用镀锡液包含选自以下的化学式1所示的聚亚烷基双胍化合物及其盐中的一种或两种以上作为防霉剂。
16.[化学式1]
[0017][0018]
[式中,r1为碳原子数2~8的亚烷基,n为2~18的整数。]
[0019]
发明效果
[0020]
对于本发明的滚镀用镀锡液而言,通过使该镀锡液中包含选自聚亚烷基双胍化合物及其盐中的一种或两种以上,即使在该镀锡液的ph值从弱酸性至接近中性、且超过30℃的浴温环境下,在镀锡工序后的水洗工序中也能够抑制水洗水中产生霉菌。
附图说明
[0021]
图1是确认在镀锡液中添加了防霉剂时的浴外观中有无浑浊或沉淀所得到的结果。
[0022]
图2是使用添加了防霉剂的镀锡液而成膜的镀锡被膜的外观确认结果。
[0023]
图3是针对使用添加了防霉剂的镀锡液而成膜的镀锡被膜的膜厚进行测定的结果。
[0024]
图4是针对使用添加了防霉剂的镀锡液而成膜的镀锡被膜的焊料润湿性进行测定的结果。
[0025]
图5是针对使用添加了防霉剂的镀锡液进行滚镀时的凝聚率进行计算的结果。
[0026]
图6是在使用添加了防霉剂的镀锡液进行滚镀后再进行水洗的水洗水中的霉菌培养试验结果。
具体实施方式
[0027]
以下,对本发明的包含防霉剂的滚镀用镀锡液进行说明。
[0028]
1.防霉剂的实施方式
[0029]
添加至本发明的滚镀用镀锡液来使用的防霉剂为选自以下的化学式1所示的聚亚烷基双胍化合物及其盐中的一种或两种以上。在镀锡液中加入镀锡所需成分以外的物质通常会对镀锡被膜的品质带来不良影响。然而,在使用添加了该防霉剂的滚镀用镀锡液进行镀锡的情况下,没有对所成膜的镀锡被膜的品质带来不良影响。进而,在使用添加了该防霉剂的滚镀用镀锡液进行镀锡后的水洗工序中,可抑制水洗水中产生霉菌。
[0030]
[化学式1]
[0031][0032]
[式中,r1为碳原子数2~8的亚烷基,n为2~18的整数。]
[0033]
聚亚烷基双胍化合物及其盐等双胍系化合物具有阳离子的性质,吸附至具有负电荷的细菌表面从而发挥杀菌效果。基于该效果可知,可用于食品制造机械或器具和医疗器械或器具等的杀菌或除菌,并且,由于其对人体影响小、安全性也高,因此还可用于隐形眼镜的清洗液或除菌喷雾等。
[0034]
这里,本发明的防霉剂(即选自聚亚烷基双胍化合物及其盐中的一种或两种以上)优选添加至滚镀中使用的镀锡液来使用。这是因为即使在该镀锡液的ph值从弱酸性至接近中性、且超过30℃的浴温环境下,在镀锡工序后的水洗工序中,也能够抑制水洗水中产生霉菌。进而,不会对所成膜的镀锡被膜的品质带来不良影响。
[0035]
而且,选自聚亚烷基双胍化合物及其盐中的一种或两种以上优选为选自聚六亚甲基双胍及其盐中的一种或两种以上。这是因为在镀锡工序后的水洗工序中,能够进一步抑制水洗水中产生霉菌、且不会对所成膜的镀锡被膜的品质带来不良影响。
[0036]
在向镀锡液中添加与本发明的防霉剂不同的防霉剂的情况下,存在不溶于镀敷液、镀敷液发生白浊之类的在镀敷液中以浴外观的形式呈现的问题,故而不理想。进而,在用添加了与本发明的防霉剂不同的防霉剂的镀锡液而成膜的镀锡被膜中,存在被膜品质、膜厚不均、焊料润湿性变差的问题,故而不理想。另外,在用添加了与本发明的防霉剂不同的防霉剂的镀锡液进行滚镀的情况下,会产生被镀敷物彼此粘附的双片粘着的问题而使成品率变差。因此,存在生产率降低的问题,故而不理想。
[0037]
2.滚镀用镀锡液的实施方式
[0038]
本发明的滚镀用镀锡液在包含作为锡离子供给源的锡盐、金属络合剂、导电盐、辅助导电盐、ph值调节剂和抗氧化剂的镀锡液中包含上述的防霉剂即选自聚亚烷基双胍化合物及其盐中的一种或两种以上。而且,该选自聚亚烷基双胍化合物及其盐中的一种或两种以上优选为选自聚六亚甲基双胍及其盐中的一种或两种以上。通过使本发明的滚镀用镀锡液中包含上述防霉剂,即使在该镀锡液的ph值从弱酸性至接近中性、且超过30℃的浴温环境下,也能够在镀锡工序后的水洗工序中抑制水洗水中产生霉菌。
[0039]
2-1.锡盐
[0040]
作为本发明的滚镀用镀锡液的锡离子供给源的锡盐是可溶于水的亚锡盐(以下简称为“锡盐”)。而且,该锡盐优选使用选自甲磺酸锡、硫酸锡、乙磺酸锡、羟乙基磺酸锡中的一种或两种以上。
[0041]
而且,本发明的滚镀用镀锡液中的锡盐的含量以锡换算计优选为4.5g/l~30g/l。在锡盐含量以锡换算计低于4.5g/l的情况下,电流效率下降、镀敷速度不能满足工业上要求的生产率,同时还会损害镀锡层的平滑性、膜厚均匀性。另一方面,在锡盐含量以锡换算
计超过30g/l的情况下,镀敷液中的锡量变多,锡的电沉积速度过快而难以控制镀层的膜厚,而且不能规避生成锡氧化物沉淀。
[0042]
进而,本发明的滚镀用镀锡液中的锡盐的含量以锡换算计更优选为10g/l~20g/l。这是因为:从工业生产方面来看,进行镀锡时的镀敷条件通常会有一定程度的变动,考虑到镀敷条件的不可控的不可避免的变动,能够形成品质更稳定的镀锡层。
[0043]
2-2.金属络合剂
[0044]
本发明的滚镀用镀锡液的金属络合剂使镀锡液中由锡盐供给的锡离子形成螯合物而稳定化。而且,该金属络合剂优选使用选自葡萄糖酸钠、葡萄糖酸或其盐、柠檬酸或其盐、焦磷酸或其盐中的一种或两种以上。这是因为这里记载的金属络合剂与由作为锡离子供给源的锡盐在溶液中电离出的锡离子高效地形成螯合物。
[0045]
而且,本发明的滚镀用镀锡液中的金属络合剂的含量优选为50g/l~300g/l。在金属络合剂的含量低于50g/l的情况下,在上述的镀敷液中的锡盐含量的前提下难以与镀敷液中的所有锡离子形成螯合物,存在游离的锡离子,因此,无法防止生成氧化锡沉淀。另一方面,即使金属络合剂的含量超过300g/l,对于与上述的镀敷液中的锡离子形成螯合物而言也是过剩的量,从而成为资源的浪费。
[0046]
2-3.导电盐
[0047]
本发明的滚镀用镀锡液的导电盐使将镀锡液电解时的通电状态变得稳定,提高锡析出的电流效率,提高生产率。而且,该导电盐优选使用选自硫酸铵、硫酸钠、硫酸钾中的一种或两种以上。这是因为镀锡液的品质变化最小、并且也没有杂质残留至镀锡层中。
[0048]
而且,本发明的滚镀用镀锡液中的导电盐的含量优选为1g/l~200g/l。在导电盐的含量低于1g/l的情况下,无法获得使进行电解时的通电稳定性提高的效果。而且,即使导电盐的含量超过200g/l,电解时的通电稳定性也不会额外地提高,因此成为资源的浪费。
[0049]
2-4.辅助导电盐
[0050]
本发明的辅助导电盐是为了使将镀锡液电解时的通电状态变得稳定而与上述导电盐一并使用的。而且,该辅助导电盐优选使用选自甲磺酸、乙磺酸、硫酸、羟乙基磺酸中的一种或两种以上。这是因为通过与上述导电盐一并使用,可使将镀锡液电解时的通电状态变得稳定且不会影响进行镀锡时的镀敷液性状。
[0051]
而且,本发明的辅助导电盐的含量优选为1.5g/l~300g/l。在辅助导电盐的含量低于1.5g/l的情况下,无法获得使进行电解时的通电稳定性提高的效果。而且,即使辅助导电盐的含量超过300g/l,电解时的通电稳定性也不会额外地提高,因此成为资源的浪费。
[0052]
2-5.ph值调节剂
[0053]
本发明的滚镀用镀锡液的ph值调节剂是为了调节成如下的ph值而使用的,该ph值适合使镀锡液中由锡盐供给的锡离子与金属络合剂反应而形成锡螯合物、而且实现使暂时生成的锡螯合物变得稳定以及最终使本发明的镀锡液适合进行镀锡。而且,该ph值调节剂优选使用选自氢氧化钠、氢氧化钾、氨水中的一种或两种以上。选择这些化合物作为ph值调节剂是因为可以形成良好的镀锡层且不会影响进行镀锡时的镀敷液性状。
[0054]
经上述ph值调节剂调节的本发明的滚镀用镀锡液的ph值优选为3.5~8.0。这是因为:在镀锡液的ph值处于低于3.5的强酸性区域时,将实施镀锡的被镀敷物的表面中未实施镀敷的部分侵蚀的可能性变高。而且,若镀锡液的ph值超过8.0,则会损害所生成的锡螯合
物的稳定性,锡无法固定而成为锡离子,生成氧化锡的沉淀,因而使作为镀锡液的溶液寿命缩短。
[0055]
2-6.抗氧化剂
[0056]
本发明的滚镀用镀锡液的抗氧化剂优选使用选自异抗坏血酸、邻苯二酚、对苯二酚、抗坏血酸盐中的一种或两种以上。这是为了防止因空气与镀敷液接触而导致自然氧化,高效地防止生成锡氧化物的沉淀。
[0057]
而且,本发明的滚镀用镀锡液的抗氧化剂的含量优选为0.1g/l~30g/l。在抗氧化剂的含量低于0.1g/l的情况下,无法获得充分的抗氧化效果。而且,即使抗氧化剂的含量超过30g/l,也无法获得额外的抗氧化效果,无法期待延长镀锡液的寿命。而且,因过量添加抗氧化剂而导致作为镀锡液的品质发生变化,故而不优选。因而,更优选上述抗氧化剂的浓度在1g/l~10g/l浓度的范围内使用。这是因为能够获得可靠的抗氧化效果、且能够可靠地防止因过量添加抗氧化剂而导致的作为镀锡液的品质变化。
[0058]
2-7.防霉剂
[0059]
本发明的防霉剂优选添加至上述的滚镀用镀锡液来使用。
[0060]
而且,本发明的滚镀用镀锡液中的防霉剂的含量优选为0.1g/l~30g/l。在该防霉剂的含量低于0.1g/l的情况下,不能充分发挥防止产生霉菌的效果,故而不优选。在该防霉剂的含量超过30g/l的情况下,防止产生霉菌的效果不变,添加的防霉剂的成本上升,故而不优选。
[0061]
防霉剂的含量的上限值更优选为20g/l。这是因为可以抑制所添加的防霉剂的成本。而且,防霉剂的含量的上限值进一步优选为10g/l。这是因为可以进一步抑制所添加的防霉剂的成本。
[0062]
3.镀锡方法的实施方式
[0063]
使用本发明的滚镀用镀锡液的镀锡方法优选为:将投入有被镀敷物的滚筒浸渍于镀锡液中,在浴温10℃~50℃的条件下进行电解。该镀敷方法的特征在于能够在浴温10℃~50℃的范围内进行镀敷操作。在浴温低于10℃的情况下,粗大的镀锡结晶析出,难以得到平滑且膜厚均匀性优异的镀锡层。另一方面,在浴温超过50℃的情况下,镀敷液水分的蒸发气散变得显著,镀锡液的组成急剧地变动,而且还会促进金属锡的氧化,溶液寿命也变短。而且,使用本发明的滚镀用镀锡液进行镀锡时的电流密度优选采用0.05a/dm2~0.5a/dm2的范围。在该电流密度低于0.05a/dm2的情况下,当然会使锡的析出速度缓慢,不能满足工业生产率。相对于此,若采用超过0.5a/dm2的电流密度,则会损害镀锡被膜的平滑性。
[0064]
4.被镀敷物的实施方式
[0065]
以上所述的本发明的滚镀用镀锡液是在能够一次性大量地镀敷的滚镀中使用的镀液,适合形成可替代片式(chip type)叠层陶瓷电容器、片式陶瓷线圈、片式陶瓷热敏电阻、电感器(inductor)、压敏电阻(varistor)、电阻器等的小型部件的镀锡层。
[0066]
以上说明的本发明的实施方式是本发明的一个方面,可以在不偏离本发明的主旨的范围内进行适当变更。另外,列举以下实施例来更具体地说明本发明,但本发明并不限定于以下的实施例。
[0067]
实施例
[0068]
在实施例中,使用了meltex株式会社制造的镀锡液melplate sn-2680(其被调整
成使锡盐、金属络合剂、导电盐、辅助导电盐和抗氧化剂为具体实施方式中所示范围的成分浓度)。然后,在该镀锡液中添加2g/l的聚六亚甲基双胍作为防霉剂,调制成滚镀用镀锡液。
[0069]
然后,使用氢氧化钠作为ph值调节剂,将该镀锡液的ph值调节至5.0。
[0070]
比较例
[0071]
〔比较例1〕
[0072]
在比较例1中,使用2g/l的苯扎氯铵作为防霉剂,除此以外,与实施例同样操作,调制成滚镀用镀锡液。
[0073]
〔比较例2〕
[0074]
在比较例2中,使用2g/l的次氯酸钠作为防霉剂,除此以外,与实施例同样操作,调制成滚镀用镀锡液。
[0075]
〔比较例3〕
[0076]
在比较例3中,使用2g/l的二癸基二甲基氯化铵作为防霉剂,除此以外,与实施例同样操作,调制成滚镀用镀锡液。
[0077]
〔比较例4〕
[0078]
在比较例4中,使用2g/l的百里酚作为防霉剂,除此以外,与实施例同样操作,调制成滚镀用镀锡液。
[0079]
〔评价〕
[0080]
a.浴外观
[0081]
将实施例和比较例1~4的镀锡液放入烧杯中,确认镀锡液的浴外观中有无浑浊或沉淀,将所得的结果示于图1。由图1所示的浴外观的结果判明了在使用比较例3的二癸基二甲基氯化铵作为防霉剂时镀敷液会浑浊。而且,判明了在使用比较例4的百里酚作为防霉剂时镀敷液中会产生沉淀。即,表明了比较例3的二癸基二甲基氯化铵和比较例4的百里酚不适合作为添加于本发明的滚镀用镀锡液中的防霉剂。因而,使用实施例、比较例1、比较例2的镀敷液进行了以后的试验。
[0082]
b.通过滚镀形成的镀锡被膜的评价
[0083]
为了评价通过滚镀而成膜的镀锡被膜,使用实施例和比较例1、比较例2的镀锡液,向滚筒中投入2012形状mlcc(叠层陶瓷电容器)和电阻器,在以下的滚镀条件下实施了滚镀。
[0084]
滚筒:株式会社山本镀金试验器制造迷你滚筒1-b型
[0085]
浴量:2l
[0086]
浴温度:40℃
[0087]
电流密度:0.2a/dm2[0088]
阳极:99.99%锡板
[0089]
镀敷时间:30分钟
[0090]
搅拌:通过滚筒进行的旋转10rpm.
[0091]
b-1.镀锡被膜的外观评价
[0092]
使用hitachi high-tech corporation制造的扫描电子显微镜s-3400n,观察了在上述的滚镀条件下成膜的镀锡被膜的外观。将镀锡被膜的外观确认结果示于图2。对于使用添加了聚六亚甲基双胍作为防霉剂的实施例的镀锡液而成膜的镀锡被膜的外观而言,在
mlcc和电阻器上都均匀地析出锡晶体,并且晶粒整齐良好。
[0093]
对于使用比较例1的镀锡液(添加了苯扎氯铵作为防霉剂)而成膜的镀锡被膜的外观而言,虽然在mlcc和电阻器上都均匀地析出锡晶体,但晶粒不整齐。
[0094]
对于使用比较例2的镀锡液(添加了次氯酸钠作为防霉剂)而成膜的镀锡被膜的外观而言,在mlcc和电阻器上都不均匀地析出锡晶体,并且晶粒也不整齐。
[0095]
b-2.镀锡被膜的膜厚评价
[0096]
针对在上述的滚镀条件下成膜的被镀敷物中随机选择的5个被镀敷物的镀锡被膜的膜厚,使用bruker axs株式会社制造的荧光x射线分析装置m4tornado进行了观察。将镀锡被膜的膜厚测定结果示于图3。这里,将良好的膜厚范围设为3.0μm~7.0μm。条形图的顶端值是5个被镀敷物的镀锡被膜的膜厚的平均值。而且,与条形图一起显示的误差棒的最低点表示所测定的膜厚的最小值,误差棒的最高点表示所测定的膜厚的最大值。
[0097]
根据使用实施例的镀锡液(添加了聚六亚甲基双胍作为防霉剂)而成膜的镀锡被膜的膜厚测定结果,mlcc和电阻器的膜厚的平均值为5.3μm、5.0μm,为良好的膜厚范围的大致中心值。而且,根据误差棒显示的幅度,表明镀锡被膜的膜厚的波动幅度为1.0μm~1.3μm左右。
[0098]
根据使用比较例1的镀锡液(添加了苯扎氯铵作为防霉剂)而成膜的镀锡被膜的膜厚测定结果,mlcc和电阻器的膜厚的平均值均为5.0μm,为良好的膜厚范围的中心值。而且,根据误差棒显示的幅度,表明镀锡被膜的膜厚的波动幅度为1.5μm左右。
[0099]
根据使用比较例2的镀锡液(添加了次氯酸钠作为防霉剂)而成膜的镀锡被膜的膜厚测定结果,mlcc和电阻器的膜厚的平均值均偏离了良好的膜厚范围。而且,根据误差棒显示的幅度,表明镀锡被膜的膜厚的波动幅度为2.5μm~4.0μm左右。
[0100]
b-3.镀锡被膜的焊料润湿性评价
[0101]
为了评价焊料润湿性,进行了如下试验。首先,对于在上述的滚镀条件下成膜的被镀敷物,通过在105℃、100%rh、4小时的条件下的压力锅蒸煮试验(pct)进行了镀锡被膜的加速劣化处理。之后,使用株式会社rhesca制造的焊料测试仪(solder checker)5200tn,通过弧面沾锡法(meni scograph method),在以下条件下测定了自将试验片(压力锅蒸煮试验处理后的被镀敷物)浸渍于焊膏起至润湿应力值变为零为止的时间即零交叉时间(zero-cross time)。
[0102]
锡膏组成:sn:ag:cu=96.5:3.0:0.5
[0103]
测定方法:快速加热升温法
[0104]
槽温度:245℃
[0105]
gap/depth:0.05mm
[0106]
测定次数:5次
[0107]
将零交叉时间的测定结果示于图4。这里的合格基准设定成零交叉时间为3秒以下。条形图的顶端值是5次测定的零交叉时间的平均值。而且,与条形图一起显示的误差棒的最低点表示所测定的零交叉时间的5次测定值中的最小值,误差棒的最高点表示零交叉时间的5次测定值中的最大值。
[0108]
根据使用实施例的镀锡液(添加了聚六亚甲基双胍作为防霉剂)而成膜的试验片的零交叉时间的测定结果,mlcc和电阻器的零交叉时间的平均值均为1.6秒,为合格基准即
3秒以下。而且,根据误差棒显示的幅度,表明零交叉时间的波动幅度为0.5秒左右。
[0109]
根据使用比较例1的镀锡液(添加了苯扎氯铵作为防霉剂)而成膜的试验片的零交叉时间的测定结果,虽然mlcc的零交叉时间的平均值为1.7秒左右,但电阻器的零交叉时间的平均值为3.1秒,偏离了合格基准。而且,根据误差棒显示的幅度,表明零交叉时间的波动幅度为1.0秒~3.0秒左右。
[0110]
根据使用比较例2的镀锡液(添加了次氯酸钠作为防霉剂)而成膜的试验片的零交叉时间的测定结果,mlcc的零交叉时间的平均值为3.8秒,偏离了合格基准,电阻器未显示出焊料润湿性,无法测定零交叉时间。而且,根据误差棒显示的幅度,表明mlcc的零交叉时间的波动幅度为3.5秒左右。
[0111]
c.凝聚评价
[0112]
在滚镀中,为了评价有无被镀敷物彼此聚集而凝聚的现象,使用实施例和比较例1、比较例2的镀锡液,向滚筒中投入200g直径为1.0mm的镀镍虚设球(dummy ball),在以下的滚镀条件下实施了滚镀。
[0113]
浴量:2l
[0114]
浴温度:40℃
[0115]
电流密度:0.2a/dm2[0116]
镀敷时间:30分钟
[0117]
滚筒:株式会社山本镀金试验器制造迷你滚筒1-b型
[0118]
搅拌:通过滚筒进行的旋转10rpm.
[0119]
阳极:99.99%锡板
[0120]
根据以下的数学式1所示的公式计算凝聚率。将凝聚率的评价结果示于图5。这里的合格基准设定成凝聚率为0.5%以下。
[0121]
[数学式1]
[0122][0123]
根据使用实施例的镀锡液(添加了聚六亚甲基双胍作为防霉剂)进行滚镀后的凝聚率的评价结果,凝聚率为0.1%,结果满足合格基准。
[0124]
根据使用比较例1的镀锡液(添加了苯扎氯铵作为防霉剂)而成膜的进行滚镀后的凝聚率的评价结果,凝聚率为28.9%,不满足合格基准。
[0125]
根据使用比较例2的镀锡液(添加了次氯酸钠作为防霉剂)而成膜的进行滚镀后的凝聚率的评价结果,凝聚率为0.0%,结果满足合格基准。
[0126]
d.霉菌培养试验
[0127]
为了确认抑制在滚镀后的水洗工序的水洗水中产生霉菌的效果,使用实施例和比较例1、比较例2的镀锡液,向滚筒中投入2012形状mlcc(叠层陶瓷电容器)和电阻器,在与上述的“通过滚镀形成的镀锡被膜的评价”中所示的条件相同的滚镀条件下实施了滚镀。之后,通过水洗工序对镀锡后的mlcc和电阻器进行了水洗。然后,在jnc株式会社制造的微生物检测培养基mc-mediapad上涂布上述的水洗后的水洗水,在35℃下培养48小时。
[0128]
需要说明的是,为了比较,使用除了不添加防霉剂以外与实施例同样操作而调制
成的滚镀用镀锡液,进行mlcc和电阻器的滚镀,之后,使用将镀锡后的mlcc和电阻器进行了水洗的水洗工序中的水洗水,与上述同样地进行培养。将作为霉菌培养试验结果的、微生物检测培养基的培养后的照片示于图6。
[0129]
对于使用添加了防霉剂的实施例、比较例1、比较例2的镀锡液进行镀锡后的水洗工序中使用的水洗水而言,在微生物检测培养基中没有产生霉菌。另一方面,对于使用未添加防霉剂的情况下的镀锡液进行镀锡后的水洗工序中所使用的水洗水而言,在微生物检测培养基中产生了霉菌。
[0130]
e.评价结果汇总
[0131]
将迄今为止实施的评价项目及其结果汇总于表1。由表1表明,可防止产生霉菌、且所有评价结果均良好的是作为所添加的防霉剂使用聚六亚甲基双胍的实施例的镀锡液。另一方面,表明比较例的镀锡液在任意一个以上评价项目中出现了问题,不能用作镀锡液。
[0132]
[表1]
[0133]
评价项目实施例比较例1比较例2比较例3比较例4浴外观良好良好良好差差被膜外观良好不良差不适用不适用被膜膜厚良好良好差不适用不适用焊料润湿性良好不良差不适用不适用凝聚率良好差良好不适用不适用防止产生霉菌良好良好良好不适用不适用综合判定良好差差差差
[0134]
综上所述,对于本发明的滚镀用镀锡液而言,通过使镀锡液中包含选自聚亚烷基双胍化合物及其盐中的一种或两种以上作为防霉剂,即使在该镀锡液的ph值从弱酸性至接近中性、且超过30℃的浴温环境下,也不会对使用该镀锡液而成膜的镀锡被膜的品质带来不良影响。另外,确认了在使用有该镀锡液的镀锡工序后的水洗工序中可抑制水洗水中产生霉菌。
[0135]
产业上的可利用性
[0136]
本发明的滚镀用镀锡液通过使镀锡液中包含本发明的防霉剂,即使在该镀锡液的ph值从弱酸性至接近中性、且超过30℃的浴温环境下,也能够在镀锡工序后的水洗工序中抑制水洗水中产生霉菌,并且不会对使用该镀锡液而成膜的镀锡被膜的品质带来不良影响。因而,在滚镀工序后的水洗工序中,无需为了防止产生霉菌而向水洗水中供给防霉剂。换言之,解决了在水洗水中投入防霉剂的情况下的需要大量地投入防霉剂而使防霉剂的成本变高、需要向水洗中投入防霉剂的工序等问题。即,能够降低水洗工序中的成本和作业负担。