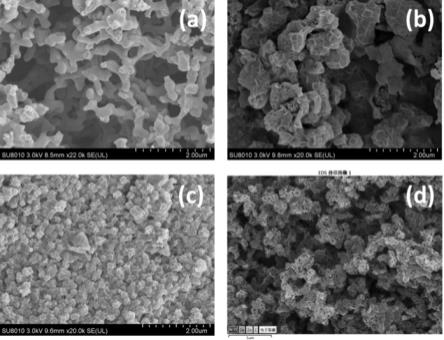
s.;zheng,l.;wang,y.;gu,l.;chen,c.;peng,q.;wang,d.;li,y.adv.mater.2018,30,e1706508.[4]cui,x.;ren,p.;deng,d.;deng,j.;bao,x.energy&environmentalscience2016,9,123-129.[5]zhang,l.;jia,y.;gao,g.;yan,x.;chen,n.;chen,j.;soo,m.t.;wood,b.;yang,d.;du,a.;yao,x.chem.2018,4,285
−
297.[6]fei,h.;dong,j.;feng,y.;allen,c.s.;wan,c.;volosskiy,b.;li,m.;zhao,z.;wang,y.;sun,h.;an,p.;chen,w.;guo,z.;lee,c.;chen,d.;shakir,i.;liu,m.;hu,t.;li,y.;kirkland,a.i.;duan,x.;huang,y.nat.catal.2018,1,63
−
72.[7]fei,h.;dong,j.;arellano-jimenez,m.j.;ye,g.;dongkim,n.;samuel,e.l.;peng,z.;zhu,z.;qin,f.;bao,j.;yacaman,m.j.;ajayan,p.m.;chen,d.;tour,j.m.nat.commun.2015,6,8668.[8]chen,w.x.;pei,j.j.;he,c.t.;wan,j.w.;ren,h.l.;zhu,y.q.;wang,y.;dong,j.c.;tian,s.b.;cheong,w.c.;lu,s.q.;zheng,l.r.;zheng,x.s.;yan,w.s.;zhuang,z.b.;chen,c.;peng,q.;wang,d.s.;li,y.d.angew.chem.,int.ed.2017,56,16086
−
16090.[9]zhang,h.;hwang,s.;wang,m.;feng,z.;karakalos,s.;luo,l.;qiao,z.;xie,x.;wang,c.;su,d.;shao,y.;wu,g.j.am.chem.soc.2017,139,14143
−
14149.[10]chen,y.;ji,s.;wang,y.;dong,j.;chen,w.;li,z.;shen,r.;zheng,l.;zhuang,z.;wang,d.;li,y.angew.chem.,int.ed.2017,56,6937
−
6941.[11]yin,p.;yao,t.;wu,y.;zheng,l.;lin,y.;liu,w.;ju,h.;zhu,j.;hong,x.;deng,z.;zhou,g.;wei,s.;li,y.angew.chem.,int.ed.2016,55,10800
−
10805.
技术实现要素:为解决现有技术的不足,本发明拟有效解决金属有机框架-碳基催化剂合成途径存在的问题,拟提供一种单原子分散碳基催化剂及其制备方法,该碳基催化剂在形成了大量均匀分散的活性位点的基础上,还在其结构中构造了大量孔道,促进了传质作用。本发明对于获得高效二氧化碳电催化还原体系具有重要意义。
[0007]
为实现上述发明目的,本发明提供了下述技术方案。
[0008]
本发明提供了一种单原子分散碳基催化剂,所述单原子为过渡金属单原子,选自铁、镍或钴中的一种或多种,所述催化剂的微观结构由若干呈珊瑚状的微米结构交错形成,所述珊瑚状的微米结构又由若干纳米级别的球状结构堆叠而成;且若干珊瑚状微米结构交错形成了大量的微米级孔道。
[0009]
本发明提供了上述单原子分散碳基催化剂的制备方法。该制备方法包括两个制备过程。
[0010]
过程一,首先通过溶液-溶胶-凝胶-灼烧法合成过渡金属原子掺杂的氧化锌。具体的:乙酸锌与过渡金属的硝酸盐溶解在无水乙醇中形成混合溶液;在该步骤控制乙酸锌与其他过渡金属硝酸盐的配比可调控最终掺杂氧化锌中过渡金属的比例。柠檬酸加入乙醇中形成柠檬酸乙醇溶液,将该柠檬酸乙醇溶液缓慢加入至上述混合溶液中,并快速持续搅拌,得到主要由柠檬酸锌络合物组成、掺杂有过渡金属柠檬酸络合物的溶胶。将溶胶转移至烘箱中直至溶剂无水乙醇完全挥发,得到透明的、高黏度的凝胶,该凝胶中不再存在柠檬酸盐的离子晶体,而是一种高度交联、高度分散的结构。将凝胶转移至马弗炉中高温灼烧,得到过渡金属原子均匀掺杂的氧化锌。该过程制得的过渡金属原子掺杂氧化锌中,过渡金属原子的掺杂形式为替代氧化锌晶格中的部分锌原子,且过渡金属原子均匀的分散在了氧化锌晶体中、没有形成团聚或其他多晶结构;过渡金属原子掺杂氧化锌为纤锌矿结构,保留了和氧化锌标准样一样的六方晶型的晶体结构;且该过程制得的过渡金属原子掺杂氧化锌的微观形貌呈现为纳米级别的球状结构,具有高比表面积。
[0011]
更为具体的,过程一包括如下步骤:1)向100 ml无水乙醇中加入二水乙酸锌,然后搅拌加热至60℃-75℃,至乙酸锌完全溶解,制备浓度为0.02-0.1 mol/l的乙酸锌乙醇溶液。然后向乙酸锌乙醇溶液中加入浓度为0.003 mol/l的过渡金属硝酸盐乙醇溶液,使溶液中锌和过渡金属离子的摩尔比为99.5:0.5-95:5,继续搅拌,形成混合溶液。
[0012]
2)向上述混合溶液中以5 ml/min的滴加速率缓慢加入30-60 ml的浓度为0.8 mol/l柠檬酸乙醇溶液并以700 r/min-1000 r/min的速度进行磁力快速搅拌,然后转移至常温环境以700 r/min-1000 r/min的速度持续快速磁力搅拌30 min(注意上述所有过程应尽量避免无水乙醇的挥发以保持溶液浓度不变),形成溶胶。
[0013]
3)将溶胶转移至60 ℃-70 ℃烘箱中,使无水乙醇缓慢完全挥发,最终形成凝胶。
[0014]
4)上述凝胶转移至带盖坩埚中,放入马弗炉,按5 ℃/min的速率升温至600 ℃,并维持3-12 h,最终得到过渡金属原子均匀掺杂的氧化锌。
[0015]
在该过程中,首先乙酸锌与过渡金属的硝酸盐溶解在无水乙醇中形成混合溶液,在该混合溶液中各离子处于高度均匀分散的状态,而在快速搅拌的条件下柠檬酸乙醇溶液的加入使得这种高度分散的状态得以保持,使得在随后的凝胶状态及高温灼烧处理过程中体系均保持均匀状态,过渡金属原子没有形成团聚、均匀的分散在整个体系中,从而最终得到保留了和氧化锌标准样一样的六方晶型晶体结构、过渡金属原子均匀掺杂的氧化锌,该过程为后续获得具有大量均匀分散的活性位点的催化剂奠定了基础。
[0016]
过程二,过渡金属原子掺杂的氧化锌与2-甲基咪唑高温下生成zif-8,再通过zif-8有机框架的热解碳化与酸洗去除氧化锌的步骤得到最终产物,即所述单原子分散碳基催化剂。更为具体的,过程二的步骤如下。
[0017]
1)将过程一制得过渡金属原子掺杂的氧化锌与2-甲基咪唑以1:0.8-1:3.6的摩尔比置于管式炉中,以氩气为载气,以2-10℃/min的升温速率持续升温至800℃-1000 ℃,维持0.5-2 h,然后自由降温至室温;2)将上述高温反应的产物与稀盐酸混合搅拌3-12 h,其中盐酸浓度为0.1 mol/l,过滤洗涤干燥得到最终的单原子分散碳基催化剂。
[0018]
在该过程中,掺杂的氧化锌具有的高比表面积有效促进了高温下与2-甲基咪唑的
反应,与氧化锌中的锌原子结合,且以具有六方晶型纤锌矿晶体结构的掺杂氧化锌为模板,生成zif-8。在氧化锌与2-甲基咪唑高温反应的过程中,氧化锌中掺杂的过渡金属原子替代了部分锌原子,进入到zif-8的框架之中。由于zif-8框架的限域作用,在高温处理过程中过渡金属原子与配位的氮原子结合能进一步增强,形成了金属-氮催化活性位点,而锌原子则在高温中完全挥发,最终zif-8完全碳化,金属-氮活性位点得以保留并保持了高度分散状态,形成过渡金属单原子分散负载的碳基催化剂。而在后续的酸洗过程中,作为骨架的氧化锌经酸洗后在催化剂中留下大量孔道,促进了传质作用。
[0019]
本发明首先通过形成具有过渡金属原子高度分散的柠檬酸锌-过渡金属柠檬酸盐凝胶,凝胶在高温处理过程中进一步获得未发生晶体结构改变的均匀掺杂氧化锌;然后以该掺杂氧化锌模板生成zif-8,又进一步利用了zif-8有机框架金属负载量高、对金属原子有效限域的特点,从而制得本发明的催化剂具有过渡金属单原子高分散、几乎无金属团聚、具有大量均匀分散活性位点的特点。同时,本发明以掺杂氧化锌模板生成的zif-8,以氧化锌作为微米级骨架结构形成,该zif-8在热解碳化后,经酸洗后去除的氧化锌微米级骨架,在催化剂中留下大量微米级孔道结构,促进了传质作用。因此,本发明利用上述技术方案,有效解决了金属有机框架-碳基催化剂合成途径存在的“热解金属有机框架大量的活性位点存在于微孔、介孔之中,传质过程的速度极大地限制了该类催化剂的的催化效率”等问题。同时具有的大量均匀分散活性位点和快速的传质通道,使得本发明的催化剂具备优异的催化性能。
[0020]
与现有技术相比,本发明催化剂的制备方法,还具有下述优点:本发明制备的过渡金属单原子负载的碳基催化剂以金属掺杂的氧化锌为模板,使得掺杂的过渡金属原子的种类、掺杂量、掺杂比例等具有高度可控的特点。作为模板的掺杂氧化锌通过溶液-溶胶-凝胶的路径制备,在乙酸锌-过渡金属硝酸盐乙醇溶液状态下各离子均匀分散,而在快速搅拌的条件下柠檬酸乙醇溶液的加入使得这种高度分散的状态得以保持,使得在随后的凝胶状态及高温处理过程中体系均保持均匀状态,所以最终得到晶体结构未发生改变的掺杂氧化锌。正是这样的稳定均匀的体系使得可以方便地通过调控溶液状态下过渡金属的种类、比例、含量来调控最终催化剂中的过渡金属种类、比例与含量。
[0021]
本发明另一方面提供了一种上述方法制备得到的单原子分散碳基催化剂,单原子为过渡金属原子铁、钴、镍中的一种或者任意组合,本发明还提供了上述的单原子分散碳基催化剂在电催化还原二氧化碳为一氧化碳的应用。
[0022]
优选的,所述的应用为:以ag/agcl电极作为参比电极,以pt柱作为对电极,以高负载量单原子分散碳基催化剂为原料制作工作电极,电解质溶液为0.1 m-0.5 m khco3溶液,且为二氧化碳溶解饱和状态;在0.84 v-1.44 v范围内进行恒电压电催化还原。
[0023]
优选的,单原子分散碳基催化剂制作的工作电极,须在cv活化之后,再应用于电催化还原中。
[0024]
优选的,将单原子分散碳基催化剂与0.5 % nafion、无水乙醇按10 mg、100 μl、900 μl的比例混合并超声处理2 h、搅拌12 h至分散均匀,得到ink,取100 μl ink均匀涂布在1 cm
×
1 cm的碳纸上,得到电解池阴极。将所得阴极在0.5 m且二氧化碳溶解饱和的khco3溶液中cv活化后作为工作电极用于三电极体系。常温常压下可达到95 %的一氧化碳
选择性。
附图说明
[0025]
图1为铁掺杂氧化锌(图中“zn
0.99
fe
0.01
o”)、六方晶型氧化锌(图中“zincite”)(a)、铁单原子分散碳基催化剂fesac(b)的xrd谱图。
[0026]
图2为实施例1中的铁掺杂氧化锌zn
0.99
fe
0.01
o(a)、铁单原子分散的碳基催化剂fesac的sem形貌图(b)、以纳米氧化锌为模板制备的铁负载碳基催化剂fesac-i-n(c)及fesac的元素分布图(d)。
[0027]
图3为实施例1铁单原子分散的碳基催化剂fesac中氮元素与铁元素的xps图。
[0028]
图4为实施例1的铁单原子分散的碳基催化剂fesac与对比例1中的铁负载的碳基催化剂fesac-i及对比例2中fesac-i-n的lsv曲线。
[0029]
图5为实施例1的铁单原子分散的碳基催化剂fesac与对比例1中的铁负载的碳基催化剂fesac-i及对比例2中fesac-i-n的法拉第效率曲线。
[0030]
图6为实施例1的铁单原子分散的碳基催化剂fesac与对比例1中的负载的碳基催化剂fesac-i及对比例2中fesac-i-n的一氧化碳分电流曲线。
具体实施方式
[0031]
为了有效的理解本发明,下面会结合实施例和附图进一步阐述本发明,应注意本发明并不限于这些实施例,本领域的技术人员在本发明的核心理论下所作出的非实质性改进和调整,仍归属于本发明的保护范围内。
[0032]
实施例1:1.铁单原子分散的碳基催化剂(后面内容及各说明书附图中,为了表述方便,将本实施例制得的铁单原子负载的碳基催化剂记为fesac)的制备:在制得铁掺杂氧化锌zn
0.99
fe
0.01
o的基础上,与2-甲基咪唑在氩气氛围中在管式炉中进行高温反应,然后经酸洗、过滤洗涤干燥,得到最终的催化剂。具体为:(1)称取0.407 g的铁掺杂氧化锌、0.977 g的2-甲基咪唑,置于2 cm
×
2 cm
×
10 cm的带盖刚玉舟中,其中,铁掺杂氧化锌置于刚玉舟中部,对应载气的下风向;2-甲基咪唑置于刚玉舟头部,对应载气的上风向。
[0033]
(2)将刚玉舟装入4 cm
×
3mm
×
60cm 的石英管中部,然后将石英管置于管式炉石英管中,两端放置刚玉炉塞,使刚玉舟对应管式炉热电偶位置。
[0034]
(3)使用真空泵对管式炉抽真空,抽至真空后,打开氩气流量计阀门,对管式炉充气至表压为零,反复三次,确保空气被完全排出管式炉。最后调节氩气流量为10 ml/min,管式炉尾端与大气连通。
[0035]
(4)设置升温程序,按5 ˚
c/min的升温速率由常温持续升温至900 ˚
c,维持1 h,然后自由降温至室温。
[0036]
(5)将反应产物与50 ml 0.1 mol/l的盐酸混合搅拌6 h,然后过滤洗涤干燥,得到最终的催化剂。
[0037]
本实施例中铁掺杂氧化锌zn
0.99
fe
0.01
o的制备过程为:(1)称取1.317 g的二水乙酸锌,加入至100 ml无水乙醇中,然后将该体系搅拌加
热至70 ℃,至乙酸锌完全溶解,然后向该溶液中加入20 ml的0.003 mol/l硝酸铁乙醇溶液,继续搅拌10 min,形成混合溶液。
[0038]
(2)向上述溶液中以5 ml/min的滴加速率缓慢加入50 ml 0.8 mol/l柠檬酸乙醇溶液,同时伴随800 r/min的电磁搅拌,然后转移至常温环境以相同搅拌速度搅拌30 min(注意上述过程应尽量避免无水乙醇的挥发),形成溶胶。然后转移至70 ℃烘箱中,使无水乙醇缓慢完全挥发,最终形成凝胶。
[0039]
(3)将上述凝胶转移至带盖坩埚中,放入马弗炉,按5 ℃/min的速率升温至600 ℃,并维持6 h,最终得到铁掺杂氧化锌zn
0.99
fe
0.01
o。
[0040]
2.电极的制备与活化处理(1)使用三电极体系,将制备所得的催化剂与0.5 % nafion、无水乙醇按10 mg、100 ul、900 ul的比例混合并超声处理2 h、搅拌12 h至分散均匀,得到ink,分四次取100 ul ink均匀涂布在1 cm
×
1 cm的碳纸上,作为工作电极,以ag/agcl电极作为参比电极,以pt柱电极作为对电极,使用h型双室电解池,以0.5 m且二氧化碳溶解饱和的khco3溶液为电解质。
[0041]
(2)使用上海辰华chi 660e电化学工作站,采用cv程序,测试区间在0.84 v-1.64 v vs. ag/agcl,扫速为50 mv/s,循环50圈,直到电极达到稳定状态。
[0042]
3.线性扫描伏安法(lsv)测试电极活化后,切换程序为lsv程序,测试区间为0.84 v-1.64 v vs. ag/agcl,扫速为25 mv/s。
[0043]
4.气相分析色谱(gac)测试lsv测试后,切换程序为i-t程序,电压由0.84 v vs. ag/agcl至1.44 vs. ag/agcl,每隔0.1 v取一测试点。将电解池的出气口与气相色谱连通。气相色谱每隔15 min进样一次,同样测试电压每隔15 min同时改变一次。
[0044]
实施例2:相比实施例1,将单原子金属铁替换成钴,其余步骤与工艺参数与实施例1完全一致,其中锌源与钴源、掺杂氧化锌与2-甲基咪唑的配比量按照摩尔比,即本实施例锌源与钴源、掺杂氧化锌与2-甲基咪唑的摩尔比与实施例1中锌源与铁源、掺杂氧化锌与2-甲基咪唑的摩尔比相同。本实施例制得钴单原子分散的碳基催化剂(记为:cosac)。
[0045]
实施例3:相比实施例1,将单原子金属铁替换成镍,其余步骤与工艺参数与实施例1完全一致,其中锌源与镍源、掺杂氧化锌与2-甲基咪唑的配比量按照摩尔比,即本实施例锌源与镍源、掺杂氧化锌与2-甲基咪唑的摩尔比与实施例1中锌源与铁源、掺杂氧化锌与2-甲基咪唑的摩尔比相同。本实施例制得镍单原子分散的碳基催化剂(记为:nisac)。
[0046]
实施例4:相比实施例1,将锌源与铁源的摩尔比改为99.5:0.5, 其余步骤与工艺参数与实施例1完全一致,即在制备铁掺杂氧化锌阶段,硝酸铁乙醇溶液的加入量改为10 ml。本实施例制得铁单原子分散的碳基催化剂(记为:fesac-0.5)。
[0047]
实施例5:相比实施例1,将锌源与铁源的摩尔比改为95:5, 其余步骤与工艺参数与实施例1
完全一致,即在制备铁掺杂氧化锌阶段,硝酸铁乙醇溶液的加入量改为100 ml。本实施例制得铁单原子分散的碳基催化剂(记为:fesac-5)。
[0048]
发明人在研究中反复进行了实验验证,实施例2-5制得的各样品与实施例1制得的fesac在形貌上类似、催化性能相当。在实施例1-5的工艺基础上,在一定范围调整各工艺参数,也仍然可以得到与实施例1-5相当的结果,均可以达到本发明目的。其中一定范围调整的各工艺参数包括:制备铁、钴、镍掺杂氧化锌时,乙酸锌乙醇溶液的摩尔浓度为0.02-0.1 mol/l,乙醇溶液中锌离子与铁、钴、镍离子的摩尔比95.5:0.5-95:5内,柠檬酸乙醇溶液的加入量为30-60 ml,马弗炉高温灼烧的时间为3-12 h;另,掺杂氧化锌、2-甲基咪唑在1:0.8-1:3.6的摩尔比范围内调整配比量,反应时间0.25 h-2 h,酸洗时间3 h-12 h均可获得本发明的铁、钴或镍单原子分散碳基催化剂。
[0049]
对比例1:1.铁负载的碳基催化剂(本对比例制得的铁负载的碳基催化剂记为fesac-i,其中“i”代指impregnation)的制备:在合成的铁负载的氧化锌的基础上,与2-甲基咪唑在氩气氛围中在管式炉中进行高温反应,再经酸洗、干燥得到最终的催化剂。具体为:(1)称取0.407 g的铁负载的氧化锌、0.977 g的2-甲基咪唑,置于2 cm
×
2 cm
×
10 cm的带盖刚玉舟中,其中,铁负载的氧化锌置于刚玉舟中部,对应载气的下风向;2-甲基咪唑置于刚玉舟头部,对应载气的上风向。
[0050]
(2)将刚玉舟装入4 cm
×
3mm
×
60cm 的石英管中部,然后将石英管置于管式炉石英管中,两端放置刚玉炉塞,使刚玉舟对应管式炉热电偶位置。
[0051]
(3)使用真空泵对管式炉抽真空,抽至真空后,打开氩气流量计阀门,对管式炉充气至表压为零,反复三次,确保空气被完全排出管式炉。最后调节氩气流量为10 ml/min,管式炉尾端与大气连通。
[0052]
(4)设置升温程序,按5 ˚
c/min的升温速率由常温持续升温至900 ˚
c,维持1 h,然后自由降温至室温。
[0053]
(5)将反应产物与50 ml 0.1 mol/l的盐酸混合搅拌6 h,然后过滤洗涤干燥,得到最终的催化剂。
[0054]
本实施例中铁负载的氧化锌,其中铁原子是通过常规的浸渍法负载在氧化锌上的,其制备过程为:(1)称取1.317 g的二水乙酸锌,加入至100 ml无水乙醇中,然后将该体系搅拌加热至70 ℃,至乙酸锌完全溶解。
[0055]
(2)向上述溶液中缓慢加入50 ml 0.8 mol/l柠檬酸乙醇溶液,然后转移至常温环境持续搅拌30 min(注意上述过程应尽量避免无水乙醇的挥发),形成溶胶。然后转移至70℃烘箱中,使无水乙醇缓慢完全挥发,最终形成凝胶。
[0056]
(3)将上述凝胶转移至带盖坩埚中,放入马弗炉,按5 ℃/min的速率升温至600 ℃,并维持6 h,得到氧化锌。
[0057]
(4)将0.407 g的上述氧化锌与50 ml去离子水混合搅拌至均匀,然后向混合液中缓慢滴加0.5 ml 0.1m硝酸铁溶液,继续搅拌至1 h。过滤、洗涤、干燥,得到铁负载的氧化锌。
[0058]
2.电极的制备与活化处理
(1)使用三电极体系,将制备所得的催化剂与0.5 % nafion、无水乙醇按10 mg、100 ul、900 ul的比例混合并超声处理2 h、搅拌12 h至分散均匀,得到ink,分四次取100 ul ink均匀涂布在1 cm
×
1 cm的碳纸上,作为工作电极,以ag/agcl电极作为参比电极,以pt柱电极作为对电极,使用h型双室电解池,以0.5 m且二氧化碳溶解饱和的khco3溶液为电解质。
[0059]
(2)使用上海辰华chi 660e电化学工作站,采用cv程序,测试区间在0.84 v-1.64 v vs. ag/agcl,扫速为50 mv/s,循环50圈,直到电极达到稳定状态。
[0060]
3.线性扫描伏安法(lsv)测试电极活化后,切换程序为lsv程序,测试区间为0.84 v-1.64 v vs. ag/agcl,扫速为25 mv/s。
[0061]
4.气相分析色谱(gac)测试lsv测试后,切换程序为i-t程序,电压由0.84 v vs. ag/agcl至1.44 vs. ag/agcl,每隔0.1 v取一测试点。将电解池的出气口与气相色谱连通。气相色谱每隔15 min进样一次,同样测试电压每隔15 min同时改变一次。
[0062]
对比例2:1.以纳米氧化锌为模板制备的铁负载的碳基催化剂(本对比例制得的铁负载的碳基催化剂记为fesac-i-n,其中“i”代指impregnation,“n”代指纳米氧化锌)的制备:在铁负载的纳米氧化锌的基础上,与2-甲基咪唑在氩气氛围中在管式炉中进行高温反应,再经酸洗、干燥得到最终的催化剂。由于纳米氧化锌不具备微米级骨架结构,最终得到的催化剂不具备微米级孔道结构。具体制备过程为:(1)称取0.407 g的铁负载的纳米氧化锌、0.977 g的2-甲基咪唑,置于2 cm
×
2 cm
×
10 cm的带盖刚玉舟中,其中,铁负载的氧化锌置于刚玉舟中部,对应载气的下风向;2-甲基咪唑置于刚玉舟头部,对应载气的上风向。
[0063]
(2)将刚玉舟装入4 cm
×
3mm
×
60cm 的石英管中部,然后将石英管置于管式炉石英管中,两端放置刚玉炉塞,使刚玉舟对应管式炉热电偶位置。
[0064]
(3)使用真空泵对管式炉抽真空,抽至真空后,打开氩气流量计阀门,对管式炉充气至表压为零,反复三次,确保空气被完全排出管式炉。最后调节氩气流量为10 ml/min,管式炉尾端与大气连通。
[0065]
(4)设置升温程序,按5 ˚
c/min的升温速率由常温持续升温至900 ˚
c,维持1 h,然后自由降温至室温。
[0066]
(5)将反应产物与50 ml 0.1 mol/l的盐酸混合搅拌6 h,然后过滤洗涤干燥,得到最终的催化剂。
[0067]
本实施例中铁负载的纳米氧化锌,其中铁原子是通过常规的浸渍法负载在氧化锌上的,其制备过程为:将0.407 g的纳米氧化锌与50 ml去离子水混合搅拌至均匀,然后向混合液中缓慢滴加0.5 ml 0.1m硝酸铁溶液,继续搅拌至1 h。过滤、洗涤、干燥,得到铁负载的纳米氧化锌。
[0068]
2.电极的制备与活化处理(1)使用三电极体系,将制备所得的催化剂与0.5 % nafion、无水乙醇按10 mg、
100 ul、900 ul的比例混合并超声处理2 h、搅拌12 h至分散均匀,得到ink,分四次取100 ul ink均匀涂布在1 cm
×
1 cm的碳纸上,作为工作电极,以ag/agcl电极作为参比电极,以pt柱电极作为对电极,使用h型双室电解池,以0.5 m且二氧化碳溶解饱和的khco3溶液为电解质。
[0069]
(2)使用上海辰华chi 660e电化学工作站,采用cv程序,测试区间在0.84 v-1.64 v vs. ag/agcl,扫速为50 mv/s,循环50圈,直到电极达到稳定状态。
[0070]
3.线性扫描伏安法(lsv)测试电极活化后,切换程序为lsv程序,测试区间为0.84 v-1.64 v vs. ag/agcl,扫速为25 mv/s。
[0071]
4.气相分析色谱(gac)测试lsv测试后,切换程序为i-t程序,电压由0.84 v vs. ag/agcl至1.44 vs. ag/agcl,每隔0.1 v取一测试点。将电解池的出气口与气相色谱连通。气相色谱每隔15 min进样一次,同样测试电压每隔15 min同时改变一次。
[0072]
图1为铁掺杂氧化锌(图中“zn
0.99
fe
0.01
o”)、六方晶型氧化锌标准样(图中“zincite”)(a图)、铁单原子分散碳基催化剂fesac(b图)的xrd谱图。可以看出通过溶液-溶胶-凝胶-灼烧途径制得的过渡金属掺杂氧化锌没有除氧化锌特征峰以外的任何峰,这表明过渡金属均匀的分散在了氧化锌晶体中,没有形成团聚或其他多晶结构;掺杂氧化锌的峰位置与峰高与六方晶型的氧化锌标准样基本一致,这表明过渡金属的掺杂没有影响到氧化锌的晶体结构,即过渡金属的掺杂形式是替代了氧化锌晶格中的部分锌原子。对于高温灼烧后形成的铁单原子分散碳基催化剂,可以观察到只存在平滑的碳峰,这表明金属原子在高温处理过程中被严格限域,没有发生团聚,氧化锌在酸洗过程中也被完全去除;左侧的高峰表明石墨碳的大量存在,这是高温处理的结果,有利于催化剂的高电流与高稳定性。
[0073]
图2为实施例1中的铁掺杂氧化锌zn
0.99
fe
0.01
o(a)、铁单原子分散的碳基催化剂fesac的sem形貌图(b)、对比例2中以纳米氧化锌为模板制备的铁负载的碳基催化剂fesac-i-n(c)及fesac的元素分布图(d)。a图中铁掺杂氧化锌呈珊瑚状,珊瑚结构又由纳米级别的小球构成,这样的结构具有较大的比表面积,有利于高温下与2-甲基咪唑的反应。b图显示铁单原子分散的碳基催化剂具有相对于铁负载氧化锌模板更加膨胀的珊瑚状结构,这是由于氧化锌在形成zif-8框架的过程中会发生体积的膨胀,而zif-8的碳化导致的体积缩小则比较小;从图中可以看到,显然最后形成的铁单原子分散的碳基催化剂fesac形貌、结构上继承了铁掺杂氧化锌,也就是说,在铁掺杂氧化锌和2-甲基咪唑高温形成的zif-8复制了铁掺杂氧化锌的形貌结构,因此,使得经过后续的碳化、尤其是氧化锌骨架被酸洗后,原氧化锌骨架位置自然的形成了传质通道。而c图则显示以纳米氧化锌为模板制备的催化剂没有形成传质通道,多面体结构紧密堆积在一起,这种结构将严重影响内部活性位点参与反应。d图中fesac元素分布图显示出铁元素在碳结构中的均匀分布,与xrd的表征结果对应。
[0074]
图3为实施例1铁单原子分散的碳基催化剂fesac中氮元素(a图)与铁元素(b图)的xps图。氮元素与铁元素是与催化剂催化表现密切相关的主要元素。可以看出,氮元素在催化剂中的存在形式为石墨氮与金属氮,掺杂氧化锌与2-甲基咪唑生成的zif-8具有两种微观结构,一种以锌原子为配位中心,一种以掺杂过渡金属原子为配位中心,以锌原子为中心的结构在高温下会失去锌原子,没有配位金属的氮原子在石墨化过程中成为氮掺杂石墨烯
中的石墨氮;以掺杂过渡金属为中心的结构在高温下结合能增强,在石墨化过程中保留在石墨结构中,此时与金属配位的氮原子以金属氮形式存在。铁元素以正三价的形式存在,这与溶液状态下铁元素的价态一致,在该状态下铁元素具有较高的结合能与稳定性。
[0075]
图4为实施例1的铁单原子分散的碳基催化剂fesac与对比例1中的铁负载的碳基催化剂fesac-i及对比例2中fesac-i-n的lsv曲线。可以看出三种催化剂的过电势基本一致,但fesac在相同电压下表现出更大的电流。这说明,三种催化剂的催化路径基本一致,抑制析氢副反应的能力大致相同,但是fesac的活性位点更多。这是由于一方面fesac的模板掺杂氧化锌在均相条件下制得,可以在铁不团聚的条件下获得更多的单原子铁,使得催化剂中的铁含量更高,而浸渍获得的铁负载氧化锌中的铁元素只存在于氧化锌表面;另一方面,掺杂氧化锌中的铁元素全部存在于氧化锌晶格中,进而在zif-8中受到严格限域,因此团聚的几率更小,而浸渍获得的铁负载氧化锌部分铁元素以物理吸附的形式存在于氧化锌表面,这部分铁元素易在高温下团聚,进而进一步减少单原子活性位点。fesac-i相对于fesac-i-n在相同电压下表现出更大的电流则是因为fesac-i-n由于缺乏通道结构,扩散作用进一步抑制了反应的进行。
[0076]
图5为实施例1的铁单原子分散的碳基催化剂fesac与对比例1中的铁负载的碳基催化剂fesac-i及对比例2中fesac-i-n的法拉第效率曲线。前两种催化剂的最高法拉第效率大致相同,这是两种催化剂催化路径、抑制析氢能力均大致相同的结果,但在高电势区间,实施例1的fesac的效率更高,导致了更宽的电势窗口,这表明该催化剂在高电势下的稳定性更好。fesac-i-n的最大法拉第效率劣于前两种催化剂,主要原因是当二氧化碳与一氧化碳的扩散受到明显限制时,氢离子在电极表面获得了更多电子,表现为析氢增多,法拉第效率下降。
[0077]
图6为实施例1的铁单原子分散的碳基催化剂fesac与对比例1中的负载的碳基催化剂fesac-i及对比例2中fesac-i-n的一氧化碳分电流曲线。fesac的一氧化碳分电流显著大于fesac-i及fesac-i-n,这是由于实施例1的fesac具有更多的活性位点,在相同电势下不仅可以保持相似或更高的法拉第效率,还可以产生更多的表面反应,因此一氧化碳分电流显著增大。
[0078]
应注意,以上所述的具体实施方法对本发明的技术方案和应用结果进行了详细的说明,请读者理解以上实施例仅为最优选实施例,并不用于限制本发明,相关技术人员在本发明的核心理论范围内所进行的修改或等价替换等,均应属于本发明的保护范围。