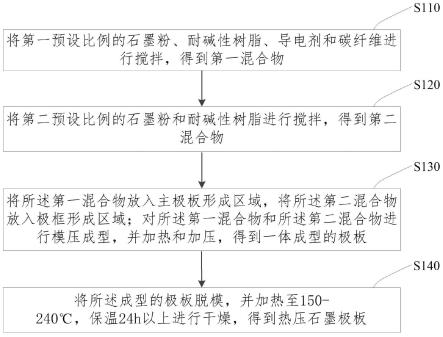
1.本发明涉及电解水制氢的技术领域,特别涉及一种热压石墨极板及其制备方法、碱性电解槽和电解水制氢设备。
背景技术:2.近年来,世界能源发生了重大变化,氢气被誉为“清洁能源”。因此,大规模的电解水制氢方法的研究已被列入国家能源开发计划中,并围绕着电解水制氢设备,开展了大量的研究。电解水制氢目前主要有三种技术路线,即碱性电解(awe),质子交换膜电解(pem)以及固体氧化物电解(soec) 三种技术路线。碱性电解水制氢技术路线最为成熟,成本最低,目前更具经济性。
3.极板是碱性电解槽的关键部件之一,要求具有电导率高、气密性好、机械性能良好、耐腐蚀性好及成本低等特点。在碱性电解槽中,极板大多采用金属极板,金属极板因其具有良好的导电性、导热性、机械加工性等,并且量产工艺成熟。目前,金属极板的成型工艺主要有冲压与液压工艺及橡胶垫成型工艺,冲压工艺具有更高的生产效率,橡胶垫成型工艺能解决生产过程中出现的裂纹、皱纹和表面波纹等问题,但橡胶垫需要时常更换。在碱性电解槽中,金属极板使用过程中存在易腐蚀的缺点,这会对其性能和耐久性产生不利影响;并且金属极板通常由主板和边框焊接,焊接的过程中易产生变形等不利影响。
技术实现要素:4.(一)发明目的
5.本发明的目的是提供一种热压石墨极板及其制备方法、碱性电解槽和电解水制氢设备。
6.(二)技术方案
7.本发明的第一方面提供了一种热压石墨极板,用于碱性电解槽中,所述热压石墨极板包括主极板和极框,所述极框围绕所述主极板的周侧,且所述极框和所述主极板为一体成型结构;其中,所述主极板包括第一预设比例的石墨粉、耐碱性树脂、导电剂和碳纤维;所述极框包括第二预设比例的石墨粉和耐碱性树脂;所述第二预设比例中的耐碱性树脂含量大于所述第一预设比例中的耐碱性树脂含量。
8.进一步地,所述主极板包括第一预设比例的以下组分:石墨粉75-85wt%;耐碱性树脂15-25wt%;导电剂3-5wt%;碳纤维3-7wt%。
9.进一步地,所述极框包括第二预设比例的以下组分:石墨粉40-50wt%;耐碱性树脂50-60wt%。
10.进一步地,所述耐碱性树脂包括环氧树脂、酚醛环氧树脂或乙烯基树脂。
11.进一步地,热压石墨极板还包括镀层,所述镀层形成于所述热压石墨极板的外周表面;其中,所述镀层的材料包括镍或钛。
12.本发明的第二方面提供了一种热压石墨极板的制备方法,用于制备上述的热压石
墨极板,所述的热压石墨极板采用模具进行制备,所述模具包括主极板形成区域和极框形成区域,极框形成区域围绕主极板形成区域的周侧;所述制备方法包括:将第一预设比例的石墨粉、耐碱性树脂、导电剂和碳纤维进行搅拌,得到第一混合物;将第二预设比例的石墨粉和耐碱性树脂进行搅拌,得到第二混合物;将所述第一混合物放入主极板形成区域,将所述第二混合物放入极框形成区域;对所述第一混合物和所述第二混合物进行模压成型,并加热和加压,得到一体成型的极板;将所述成型的极板脱模,并加热至150-240℃,保温24h以上进行干燥,得到热压石墨极板;其中,所述第二预设比例中的耐碱性树脂含量大于所述第一预设比例中的耐碱性树脂含量。
13.进一步地,所述将第一预设比例的石墨粉、耐碱性树脂、导电剂和碳纤维进行搅拌,得到第一混合物,包括:将第一预设比例的石墨粉和耐碱性树脂在球磨机中进行搅拌,再加入导电剂和碳纤维进行搅拌,得到第一混合物。
14.进一步地,所述将第二预设比例的石墨粉和耐碱性树脂搅拌,得到第二混合物,包括:将第二预设比例的石墨粉和耐碱性树脂在球磨机中搅拌,得到第二混合物。
15.进一步地,所述对所述第一混合物和所述第二混合物进行模压成型,并加热和加压,得到一体成型的极板,包括:将所述第一混合物和第二混合物模压成型,并加热至150-240℃,注入压力至9-200mpa,并保压0.5-5min。
16.进一步地,制备方法还包括:对得到的所述热压石墨极板进行表面处理;所述表面处理包括对所述热压石墨极板进行电镀,以使所述热压石墨极板的表面形成镀层。
17.进一步地,所述碳纤维包括碳纤维粉末和短切碳纤维。
18.进一步地,所述导电剂包括碳黑、石墨烯、碳纳米管、活性炭或足球烯。
19.进一步地,所述石墨粉的粒径为38μm-150μm;和/或,所述碳纤维的长度为0.15mm-2mm。
20.本发明的第三方面提供了一种碱性电解槽,包括所述的热压石墨极板。
21.本发明的第四方面提供了一种电解水制氢设备,包括所述的碱性电解槽。
22.(三)有益效果
23.本发明的上述技术方案具有如下有益的技术效果:
24.1、本发明实施例的技术方案,在加热和加压成型时,耐碱性树脂熔化后流动充分浸润石墨的缝隙形成主极板和极框的基体,同时也使得主极板和极框紧密结合从而实现一体成型;其中耐碱性树脂提高了热压石墨极板的气密性,且可以适应碱性电解槽的强碱环境,常见的氢燃料电堆极板不适用于碱性环境;主极板中添加一定量的导电剂和碳纤维,导电剂可选用碳黑,这样可提高主极板的电导率及电学性能;由于极框中耐碱性树脂含量大于主极板中的耐碱性树脂含量,因此相对于主极板,极框的树脂含量更多,使极框的强度和耐腐蚀性进一步增强,可有效提高电解槽的整体性能。
25.2、本发明实施例的技术方案,混合物料通过模压,在模压的同时进行加热和加压,在极短的时间就能成型,大大缩短了成型时间,提高了生产效率,有助于本产品工业化大规模生产,以满足碱性电解槽的使用要求。
26.3、本发明实施例的技术方案,通过将镍层或钛层形成于热压石墨极板的外周表面,这样进一步地可提高热压石墨极板的耐腐蚀性和气密性。将本发明实施例中的热压石墨极板应用于碱性电解槽中,从而可使制得的氢气气体纯度提高,并降低制氢能耗。
附图说明
27.图1是根据本发明一实施方式的一种热压石墨极板的制备方法的流程图;
28.图2是根据本发明另一实施方式的碱性电解槽小室结构示意图;
29.图3是根据本发明又一实施方式的热压石墨极板的结构示意图;
30.图4是图3的a-a剖视图;
31.附图标记:
32.111-极框;112-主极板;113-突起;114-碱液进口;115-碱液和氧气出口;116-碱液和氢气出口;
33.11-热压石墨极板;12-隔膜;13-电极。
具体实施方式
34.为使本发明的目的、技术方案和优点更加清楚明了,下面结合具体实施方式并参照附图,对本发明进一步详细说明。应该理解,这些描述只是示例性的,而并非要限制本发明的范围。此外,在以下说明中,省略了对公知结构和技术的描述,以避免不必要地混淆本发明的概念。
35.相比于燃料电池,碱性电解槽对极板的要求更高,要耐100℃高温,1mpa 以上压强,耐强碱腐蚀,且尺寸需要做大,因此常用于燃料电池的金属极板在碱性电解槽中是不适用的。纯石墨制作的极板具有电导率高、化学稳定性和热稳定性强且耐腐蚀的特点,满足部分碱性电解槽的需求。但石墨缺点也很显著,如强度低脆性大,不能满足极板气密性要求,易使气体纯度降低,且现有技术制作的传统热压石墨极板机械性能差、加工难。金属材料极板存在耐腐蚀性差等问题。
36.针对这些问题,本发明的第一方面提供了一种热压石墨极板,用于碱性电解槽中,所述热压石墨极板11包括主极板112和极框111,所述极框111 围绕所述主极板112的周侧,且所述极框111和所述主极板112为一体成型结构;其中,所述主极板包括第一预设比例的石墨粉、耐碱性树脂、导电剂和碳纤维;所述极框包括第二预设比例的石墨粉和耐碱性树脂;所述第二预设比例中的耐碱性树脂含量大于所述第一预设比例中的耐碱性树脂含量。通过在石墨粉中添加一定比例的耐碱性树脂,可使主极板和极框的化学稳定性和热稳定性增强且具有耐腐蚀的特点,而且可提高热压石墨极板的气密性,以及弯曲强度和抗拉强度等机械性能;在加热和加压成型时,耐碱性树脂熔化后流动充分浸润石墨的缝隙形成主极板和极框的基体,同时也使得主极板和极框紧密结合从而实现直接一体成型,这样省略了后续的一体成型工艺以及可避免由此带来的不利影响。其中耐碱性树脂提高了热压石墨极板的气密性,且可以适应碱性电解槽的强碱环境,常见的氢燃料电堆极板不适用于碱性环境。主极板中添加一定量的导电剂和碳纤维,导电剂可选用碳黑,这样可提高主极板的电导率及电学性能;由于极框中耐碱性树脂含量大于主极板中的耐碱性树脂含量,因此相对于主极板,极框的树脂含量更多,使极框的强度和耐腐蚀性进一步增强,可有效提高电解槽的整体性能。
37.一些实施例中,为了提高主极板的电导率,优选的方案为所述主极板包括第一预设比例的以下组分:石墨粉75-85wt%;耐碱性树脂15-25wt%;导电剂3-5wt%;碳纤维3-7wt%。
38.一些实施例中,为了提高极框的强度和耐腐蚀性,优选的方案为所述极框包括第二预设比例的以下组分:石墨粉40-50wt%;耐碱性树脂50-60wt%。
39.一些实施例中,所述耐碱性树脂包括环氧树脂、酚醛环氧树脂或乙烯基树脂。优选地,耐碱性树脂为酚醛环氧树脂;通过将耐碱性树脂与石墨粉混合成的材料作为热压石墨极板的基体,可提高热压石墨极板的气密性,且可以适应碱性电解槽的强碱环境。利用由环氧树脂、酚醛环氧树脂和乙烯基树脂中的至少一种树脂形成的共聚物作为树脂基体,主极板通过将该树脂基体与石墨粉和碳纤维作为原料组分,导电剂优选碳黑,并通过优化材料成分、配比及成形工艺,可提高主极板的电导率、耐腐蚀性、气密性和强度等机械性能,进而使其可满足碱性电解槽的使用要求。相对于主极板,极框的树脂含量更多,使极框的强度和耐腐蚀性进一步增强,可有效提高电解槽的整体性能。
40.一些实施例中,热压石墨极板还包括镀层,所述镀层形成于所述热压石墨极板的外周表面;其中,所述镀层的材料包括镍或钛。镀层包括镍层或钛层,镍层或钛层可设为单层或多层,其厚度范围可设为20-100μm。镀层可覆盖于热压石墨极板的外周表面,这样进一步地可提高热压石墨极板的耐腐蚀性和气密性。将本发明实施例中的热压石墨极板应用于碱性电解槽中,从而可使制得的氢气气体纯度提高。
41.一些实施例中,所述碳纤维包括碳纤维粉末和短切碳纤维。
42.一些实施例中,所述导电剂包括碳黑、石墨烯、碳纳米管、活性炭或足球烯。优选地,导电剂为碳黑。
43.一些实施例中,所述石墨粉的粒径为38μm-150μm;和/或,所述碳纤维的长度为0.15mm-2mm。
44.本发明的第二方面提供了一种热压石墨极板的制备方法,用于制备上述的热压石墨极板,所述的热压石墨极板采用模具进行制备,所述模具包括主极板形成区域和极框形成区域,极框形成区域围绕主极板形成区域的周侧;如图1所示,所述制备方法具体地包括以下步骤:
45.步骤s110,将第一预设比例的石墨粉、耐碱性树脂、导电剂和碳纤维进行搅拌,得到第一混合物;
46.步骤s120,将第二预设比例的石墨粉和耐碱性树脂进行搅拌,得到第二混合物;
47.步骤s130,将所述第一混合物放入主极板形成区域,将所述第二混合物放入极框形成区域;对所述第一混合物和所述第二混合物进行模压成型,并加热和加压,得到一体成型的极板;
48.步骤s140,将所述成型的极板脱模,并加热至150-240℃,保温24h以上进行干燥,得到热压石墨极板。其中,所述第二预设比例中的耐碱性树脂含量大于所述第一预设比例中的耐碱性树脂含量。
49.该模具的主极板形成区域和极框形成区域可由石蜡等低熔点的材料分隔形成,石蜡是白色、无味的蜡状固体,在约50℃时可熔化。当然也可以是其他分隔件将模具分隔为主极板形成区域和极框形成区域,待第一混合物和第二混合物放入后,将该分隔件取出即可;第一混合物和第二混合物在模具内加热和加压后,耐碱性树脂熔化后流动充分浸润石墨的缝隙形成主极板和极框的基体,同时也使得主极板和极框紧密结合从而实现一体成型。
50.一些实施例中,所述将第一预设比例的石墨粉、耐碱性树脂、导电剂和碳纤维进行
搅拌,得到第一混合物,包括:将第一预设比例的石墨粉和耐碱性树脂在球磨机中进行搅拌,再加入导电剂和碳纤维进行搅拌,得到第一混合物。其中,第一混合物可包括第一预设比例的以下组分:石墨粉75-85wt%;耐碱性树脂15-25wt%;导电剂3-5wt%;碳纤维3-7wt%。
51.一些实施例中,所述将第二预设比例的石墨粉和耐碱性树脂搅拌,得到第二混合物,包括:将第二预设比例的石墨粉和耐碱性树脂在球磨机中搅拌,得到第二混合物。第二混合物可包括第二预设比例的以下组分:石墨粉 40-50wt%;耐碱性树脂50-60wt%。
52.一些实施例中,所述对所述第一混合物和所述第二混合物进行模压成型,并加热和加压,得到一体成型的极板,包括:将所述第一混合物和第二混合物模压成型,并加热至150-240℃,注入压力至9-200mpa,并保压0.5-5min。通过加热和加压,可使极板迅速固化成型,大大缩短了成型时间,提高了生产效率。
53.一些实施例中,制备方法还包括:步骤s150,对得到的所述热压石墨极板进行表面处理;所述表面处理包括对所述热压石墨极板进行电镀,以使所述热压石墨极板的表面形成镀层。可使用电镀法在所得热压石墨极板上镀镍层或镀钛层,以提高热压石墨极板的耐腐蚀性和气密性;将本发明实施例中的热压石墨极板应用于碱性电解槽中,从而可使制得的氢气气体纯度提高。
54.本发明实施例中,利用由环氧树脂、酚醛环氧树脂和乙烯基树脂中的至少一种树脂形成的共聚物作为树脂基体,通过将该树脂基体与石墨粉和碳纤维作为原料组分,导电剂优选碳黑,并对各组分的配比进行优化,使其按照一定的比例混合形成第一混合物;同时,将石墨粉和耐碱性树脂按照一定的比例混合形成第二混合物;将第一混合物和第二混合物放入模具的相应形成区域并通过模压,在模压的同时进行加热和加压,在极短的时间就能成型,大大缩短了成型时间,提高了生产效率,有助于本产品工业化大规模生产,以满足碱性电解槽的使用要求。另外,相对于主极板,极框的树脂含量更多,使极框的强度和耐腐蚀性进一步增强,可有效提高电解槽的整体性能。
55.实施例1
56.步骤s210,取石墨粉70g、环氧树脂粉20g、碳黑5g、碳纤维5g;
57.步骤s220,将步骤s210中的石墨粉、环氧树脂粉在球磨机中搅拌均匀,然后加入炭黑和碳纤维,直至搅拌均匀,得到第一混合物;
58.步骤s230,取石墨粉50g、环氧树脂粉50g;
59.步骤s240,将将步骤s230中的石墨粉、环氧树脂粉在球磨机中搅拌均匀,得到第二混合物;
60.步骤s250,将第一混合物放入模具的主极板形成区域,第二混合物放在模具的极框形成区域,在150℃、20mpa下模压成型,并保压0.5min;
61.步骤s260,将成型的极板脱模,并在150℃的烘箱中保温24h进行干燥。
62.步骤s270,成型极板使用电镀法镀镍,以提高热压石墨极板的耐腐蚀性和气密性;镍层的厚度为50μm。
63.实施例2
64.步骤s310,取石墨粉75g、邻甲酚醛环氧树脂粉15g、碳黑5g、碳纤维 5g;
65.步骤s320,将步骤s310中的石墨粉、邻甲酚醛环氧树脂粉在球磨机中搅拌均匀,然
后加入炭黑和碳纤维,直至搅拌均匀,得到第一混合物;
66.步骤s330,取石墨粉50g、邻甲酚醛环氧树脂粉50g;
67.步骤s340,将步骤s330中的将石墨粉、邻甲酚醛环氧树脂粉在球磨机中搅拌均匀,得到第二混合物;
68.步骤s350,将第一混合物放入模具的主极板形成区域,第二混合物放在模具的极框形成区域,在150℃、20mpa下模压成型,并保压0.5min;
69.步骤s360,将成型的极板脱模,并在150℃的烘箱中保温24h进行干燥。
70.步骤s370,成型极板使用电镀法镀镍,以提高热压石墨极板的耐腐蚀性和气密性;镍层的厚度为60μm。
71.将实施例1和2制备得到的热压石墨极板进行测试,测试结果如表1所示。
72.表1热压石墨极板的测试结果
[0073][0074]
从表1可以看出,实施例1和2制备得到的热压石墨极板的主极板电导率高和热传导高,导电性能优良;极框的弯曲强度和抗拉强度等机械性能优良,且耐腐蚀;一体成型后的热压石墨极板的热稳定性强,整体性能得到了提升。
[0075]
本发明的第三方面提供了一种碱性电解槽,如图2-图4所示,包括阴极、阳极、隔膜;以及,所述的热压石墨极板;所述热压石墨极板位于阴极或阳极的外侧,所述隔膜位于所述阴极和阳极的中间。
[0076]
工业电解水中热压石墨极板11起到支撑电解槽、提供氢气和氧气的流体通道,并分隔氢气和氧气、收集电子、传导热量的作用。本发明实施例中的碱性电解槽主要由电源、电解槽箱体、电解液、电极13(电极包括阴极和阳极)和隔膜12组成。电解液(碱液)是氢氧化钾溶液(koh),其浓度为20%~ 30wt%;隔膜12主要由石棉组成,主要起分离气体的作用,而两个电极则主要由金属合金组成。其工作的主要原理是:在阴极,水分子被分解为氢离子(h
+
)和氢氧根离子(oh-),氢离子得到电子生成氢原子,并进一步生成氢分子(h2);氢氧根离子(oh-)则在阴、阳极之间的电场力作用下穿过多孔的隔膜11,到达阳极,在阳极失去电子生成一个水分子和氧分子。
[0077]
一些实施例中,所述主极板112的厚度小于所述极框111的厚度,以使所述主极板的两个相对侧面均构成电解液的流道;且所述主极板112的相对两个侧面上均设有突起113。所述突起113的高度可设为与所述极框111平齐;或者,突起113的高度可设为略高于极框111。由于主极板112的厚度小于极框111的厚度的设置,主极板112的侧面相对于周侧的极框111形成凹陷区域,该凹陷区域可构成电解液的流道;一方面,突起113以“顶对顶”的形
式起到支撑作用,另一方面,还可以使隔膜两侧的热压石墨极板与电极(阴极或阳极)实现多点接触,尽可能多的接触能够降低小室内部构件的接触电阻;另外突起113还有利于增强电解液流动的扰动程度,减小流道内各处的电解液浓度差,使电解液分布更均匀,从而降低电解水制氢设备的能耗,提高其长期运行的稳定性。
[0078]
一些实施例中,与所述主极板112的侧面相切,所述突起113的截面形状为圆弧形、矩形或多边形。优选的,突起113的截面形状设为圆弧形,这样可使热压石墨极板与电极(阴极或阳极)可有效实现点接触,通过多点接触以降低小室内部构件的接触电阻。
[0079]
一些实施例中,所述突起113设为若干个,所述突起113间隔且错开分布。本发明实施例提供的热压石墨极板可设为圆形、椭圆形、矩形或多边形;突起113的排布可随热压石墨极板的外轮廓形状进行设置,相邻的突起113之间可形成电解液的流道,突起113可设为矩形或圆周形排布阵列,且突起113在横向或纵向上间隔且错开分布,这样有利于增强电解液流动的扰动程度。
[0080]
在本发明实施例中的碱性电解槽的小室中,装配好的电解槽是隔膜12两侧的电极13,以电极13外侧的热压石墨极板11均相互压紧,极框111上设有密封垫,以实现对碱性电解槽中的电解液、制备得到的氧气和氢气进行有效地密封。热压石墨极板11位于电极13的两侧,其作用有点类似于实验室中的电极夹,作用是传导电子,如图2所示,两个热压石墨极板11分别位于一个完整的小室结构的两端,与隔膜12分别形成了阴极区域和阳极区域电解液流动的腔室;电解液从外部进入电解槽小室,阴极电解液与阳极电解液通过碱液进口114进行分流,进入主极板112两侧的阴极区电解液流道与阳极区电解液流道,以实现分区流动,再进入电解液流动的腔室,如此实现了阴极碱液和阳极碱液的分流,在阴极区域制得氧气,氧气和电解液从碱液和氧气出口115流出;在阳极区域制得氢气,氢气和电解液从碱液和氢气出口116 流出;一定程度上减小了氢中氧和氧中氢的含量,保证了电解槽运行的安全性。热压石墨极板11的外周表面上形成有镍层或钛层,这样进一步地可提高热压石墨极板11的耐腐蚀性和气密性;并且可使热压石墨极板11上电解电流密度更均匀,同时减小热压石墨极板11与电极13的接触电阻,增大电流密度,降低制氢能耗。
[0081]
一些实施例中,所述极框111上设有碱液进口114、碱液和氧气出口115、碱液和氢气出口116;所述碱液进口114、碱液和氧气出口115、碱液和氢气出口116均设为圆形、椭圆形、矩形或多边形;且所述碱液进口114位于所述极框111的一侧,所述碱液和氧气出口115、所述碱液和氢气出口116位于所述极框111的相对另一侧。电解液从碱液进口114进入电解槽小室,分别进入阳极区域和阴极区域,生成氧气和氢气,然后氧气和电解液从碱液和氧气出口115流出,氢气和电解液从碱液和氢气出口116流出。由于阳极区的电解液和阴极区的电解液是不能相通混合在一起的,因此可将碱液和氧气出口115与主极板112的一个侧面上的流道相连通;相对应地,可将碱液和氢气出口116与主极板112的另相对一个侧面上的流道相连通;碱液进口114 与主极板112的两个侧面上的流道均连通;这样电解液从外部进入电解槽小室,阴极电解液与阳极电解液通过碱液进口114进行分流,进入阴极区电解液流道与阳极区电解液流道,以实现分区流动。
[0082]
一些实施例中,所述极框111上设有凹槽,所述凹槽形成于靠近所述极框111的边缘,且所述凹槽位于所述碱液进口114、碱液和氧气出口115、碱液和氢气出口116的外侧,所述凹槽内设有密封垫。密封垫的设置可实现对碱性电解槽中的电解液、制备得到的氧气和
氢气进行有效地密封。
[0083]
本发明的第四方面提供了一种电解水制氢设备,包括所述的碱性电解槽。
[0084]
应当理解的是,本发明的上述具体实施方式仅仅用于示例性说明或解释本发明的原理,而不构成对本发明的限制。因此,在不偏离本发明的精神和范围的情况下所做的任何修改、等同替换、改进等,均应包含在本发明的保护范围之内。此外,本发明所附权利要求旨在涵盖落入所附权利要求范围和边界、或者这种范围和边界的等同形式内的全部变化和修改例。