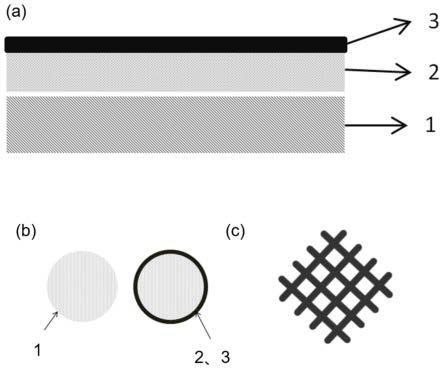
1.本发明涉及质子交换膜水电解技术领域,具体涉及一种质子交换膜水电解池用低成本金属纤维毡扩散层及其制备方法和应用。
背景技术:2.pem(质子交换膜)水电解制氢是一种利用全氟磺酸质子交换膜作为固体电解质的水电解制氢技术,具有高效率、电解槽运行灵活的特点,能够适应多种可再生能源发电的波动性。
3.扩散层是pem水电解制氢堆中的重要组件,是连接双极板和膜电极的桥梁。具体地,在阳极侧,水通过扩散层来到膜电极表面发生分解,释放出氧气、质子与电子。质子和电子分别经扩散层通过质子交换膜和外电路来到阴极侧发生反应生成氢气。为保证反应的效率与连续性,扩散层需要具备丰富的孔道与导电性能,以使得不同物质的扩散与传导能够顺畅进行,对材料的机械性能、导电性能、化学稳定性均有较高要求。目前主要应用的扩散层材料为钛。基本工艺流程为将直径为微米尺度的钛丝编织成钛网,而后加压制得具有多孔特征的钛纤维毡,最后在其表面涂覆耐腐蚀、化学稳定性良好的保护涂层。常用的保护涂层材料有贵金属、贵金属氧化物、金属氮(碳)化物等。提升扩散层的电化学与机械性能、降低制备成本是相关领域的重要研究方向。
4.目前已有一系列与pem水电解池扩散层中金属纤维毡相关的研究,cn202210543492.3提出了一种催化剂负载的扩散层及其制备方法,采用钛作为基材,进行表面预处理后涂覆含有pt、ta2o5的耐蚀中间层,最后在其上制备iro5催化活性层。该制备工艺是一种典型的pem扩散层制备工艺,制备耐蚀涂层的方法为涂覆热解法,过程简单但附着力较差。cn201910960166.0公布了一种用三种金属氧化物作为混合保护涂层制备涂敷液,涂在钛纤维毡上的扩散层制备方法,该方法通过掺入催化活性更优更廉价的钌和稳定性更强的钽以替代贵金属保护涂层的方法,降低了扩散层的制备成本、提高了稳定性,但并未在工艺上进行改进,使用简单涂覆的方法在金属纤维毡表面附加保护涂层难以精确控制涂层厚度,而过厚的保护涂层对实际的水电解过程是冗余的;cn202011481503.7公布了一种固态聚合物电解质水电解池扩散层的制备方法,其选用多孔镍板、钛纤维毡等作为扩散层基材,并通过电镀、烧结、真空溅射等方法在基材上沉积贵金属或贵金属氧化物涂层,无须在扩散层上加工流场,有效降低了电解池成本,使电解池结构更紧凑,但该制备方法中所述电镀、烧结、真空溅射等涂层处理工艺同样难以得到极小厚度的保护涂层,在成本控制上仍有提升的空间。此外,以上专利中扩散层的金属基材均为钛,其价格为不锈钢的5倍,成本高昂。
5.通过不同方式改良pem水电解堆中膜电极的疏水性能,以提高高湿度环境下系统的电流密度近年来也成为了新研究方向之一。cn202010568425.8公开了一种用于形成用作气体扩散层的疏水性导电微孔层的方法,其将碳颗粒与聚五氟苯乙烯聚合物在有机溶剂溶
液中一起配置在分散体中,在支撑物的表面形成分散体的沉积物并干燥形成疏水微孔层,在20%、50%的相对湿度,80℃和1.5bar环境下,在燃料电池中的电压≥0.6v,电流密度为2a/cm2。cn202220055412.5公开了一种pem电解水用膜电极,其中在催化剂层与气体扩散层之间设置了一层疏水层,通过在气体扩散层的基材表面上制备以聚四氟乙烯(ptfe)等疏水性树脂和碳黑等导电性材料为主成分的疏水薄膜来改良膜电极的疏水性。上述方法均能使系统在高湿度环境下仍维持高电流密度,但疏水涂层不具备耐蚀性,在高电位下长时间工作后性能将大幅度劣化。
技术实现要素:6.本发明的目的就是为了克服上述现有技术存在的缺陷中的至少一个而提供一种电化学性能、有利于pem电解池的传质与反应,涂层致密度高、可改善腐蚀情况的质子交换膜水电解池用低成本金属纤维毡扩散层及其制备方法和应用。
7.本发明的目的可以通过以下技术方案来实现:
8.本发明使用不锈钢替代钛丝,预先在表面进行特殊涂层处理后,再编织、压制成金属纤维毡,用于电解池扩散层时具备良好电化学性能,同时减少了贵金属用量,提高了经济性,具体方案如下:
9.一种质子交换膜水电解池用低成本金属纤维毡扩散层,该扩散层包括由金属丝形成的金属纤维毡基材以及金属纤维网上的疏水涂层,所述的金属丝表面沉积有耐蚀涂层。
10.进一步地,所述的金属丝为不锈钢丝,直径为20-200μm,优选20-120μm;
11.所述耐蚀涂层的成分为贵金属、金属氧化物、金属氮化物或金属碳化物;
12.所述的耐蚀涂层为二氧化硅基涂层。
13.进一步地,所述不锈钢丝的元素组成比例为fe:60-80at.%,cr、ni和mn:0.5-30at.%,还包括不高于5at.%的微量元素;
14.所述的贵金属包括au、ag、pt、pb、ru或ir,所述的金属氧化物包括ir、nb、ti、zr、ta或sn的氧化物,所述的金属氮化物或金属碳化物包括nb、ti、zr或ta的氮化物或碳化物;
15.所述二氧化硅基涂层的前驱体包括硅烷偶联剂和氧化剂。
16.进一步地,所述的微量元素包括c、p、s、n或si;
17.所述的金属氧化物具体包括iro
x
,nbo
x
、tio
x
、zro
x
、tao
x
或sno
x
;
18.所述的金属氮化物或金属碳化物具体包括nbc
x
/n
x
、tic
x
/n
x
、zrc
x
/n
x
或tac
x
/n
x
,其中x为非金属元素原子比例,范围为0.1-90at.%;
19.所述的硅烷偶联剂包括1h,1h,2h,2h-全氟辛基三氯硅烷、双(二异丙氨基)乙硅烷、正硅酸四乙酯或十七氟癸基三甲氧基硅烷;氧化剂包括臭氧或氧气。
20.一种如上所述质子交换膜水电解池用低成本金属纤维毡扩散层的制备方法,该方法包括以下步骤:
21.在金属丝表面沉积耐蚀涂层;
22.将金属丝编织成金属纤维网;
23.将金属纤维网压制得到金属纤维毡基材;
24.在金属纤维毡基材表面沉积疏水涂层,得到质子交换膜水电解池用低成本金属纤维毡扩散层。
25.进一步地,金属丝沉积前进行预处理,形成直径20-120μm的金属丝;
26.所述的沉积为气相沉积,包括化学气相沉积,物理气相沉积或原子层沉积,沉积工作温度为25-900℃,沉积厚度为1-2000nm;
27.所述的金属纤维网经过加压、加温,压制得到金属纤维毡基材。
28.进一步地,所述的预处理包括拉拔、洗涤和干燥;
29.所述的沉积具体包括等离子体增强化学气相沉积、热丝化学气相沉积、气溶胶辅助化学气相沉积、磁控溅射沉积、多弧离子沉积或原子层沉积,沉积厚度为3-60nm;
30.所述加压的压力为100-500mpa,优选100-200mpa,加温的温度为1000-1250℃,保温时间为1-4h。
31.进一步地,所述的洗涤,采用水、酸、酮或醇;
32.沉积耐蚀涂层时的工作温度为300-700℃或200-300℃,沉积厚度为45-55nm;沉积疏水涂层时的工作温度为50-300℃,沉积厚度为4-6nm;
33.所述加温的过程为先升温至1000-1250℃,保温1-4h后,再冷却至600-700℃。
34.进一步地,所述的酸包括质量分数30-38%的盐酸,所述的酮包括丙酮,所述的醇包括乙醇。
35.一种如上所述质子交换膜水电解池用低成本金属纤维毡扩散层的制备方法,该方法包括以下步骤:
36.对金属丝进行拉拔、洗涤和烘干等预处理后,再进行如下操作:
37.采用气相沉积技术在金属丝表面沉积一层耐蚀涂层;
38.将金属丝通过平纹或斜纹编织法编织成金属纤维网;
39.使用压力机对一定量的金属纤维网加压、加温,压制得到金属纤维毡;
40.采用气相沉积技术在金属纤维毡表面沉积一层疏水涂层。
41.具体而言,该方法包括以下步骤:
42.金属丝的预处理:将待制备的不锈钢丝经拉拔成20-120μm纤维状、依次使用无机酸/碱溶液、丙酮、无水乙醇、去离子水对表面超声清洗并将其烘干,取出后再用大量去离子水及无水乙醇冲洗,去除表面的氧化物、污迹等。
43.沉积耐蚀涂层:以贵金属、贵金属氧化物、金属氮/碳化物作为反应前驱体,经预处理的金属丝作为基材进行反应。在腔体中通入氢气或者通过等离子体鸿基活化衬底表面并增加反应位点密度,然后采用气相沉积技术沉积耐蚀涂层。
44.编织压制成毡:将沉积保护涂层后的金属丝通过平纹或斜纹编织法编织成金属纤维网。清洗后使用压力机加压,置于高温真空烧结炉中进行烧结,保温一定时间后得到金属纤维毡材料。
45.将成形后的金属纤维毡置于原子层沉积或化学气相沉积腔体中,制备二氧化硅基疏水涂层。
46.一种如上所述质子交换膜水电解池用低成本金属纤维毡扩散层的应用,该扩散层应用于水电解池。
47.与现有技术相比,本发明具有以下优点:
48.(1)本发明在对金属丝进行编织、压制处理前预先进行耐蚀涂层的沉积,实现了不锈钢丝原子级覆盖的腐蚀防护,使得低成本不锈钢丝作为扩散层基材成为可能;
49.(2)本发明使用化学气相沉积方法进行保护涂层的沉积,便于精确控制沉积涂层的厚度,制备得到的涂层致密度高,能够有效改善金属纤维毡在质子交换膜电解池高电位工作环境下的腐蚀情况。
附图说明
50.图1为本发明中扩散层的形貌图;
51.图2为实施例2中扩散层的腐蚀电流密度;
52.图3为实施例2中扩散层的水接触角;
53.图4为本发明的部分工艺流程图;
54.图中标号所示:1-不锈钢毡,2-耐蚀涂层,3-疏水涂层。
具体实施方式
55.下面结合附图和具体实施例对本发明进行详细说明。本实施例在以本发明技术方案为前提下进行实施,给出了详细的实施方式和具体的操作过程,但本发明的保护范围不限于下述的实施例。
56.一种质子交换膜水电解池用低成本金属纤维毡扩散层及其制备方法和应用,如图1和4,图1(a)为本发明扩散层截面图;(b)为本发明保护涂层沉积剖面图;(c)为沉积保护涂层后的不锈钢丝编织方法示意图。金属纤维毡专用于pem水电解池扩散层,基材为不锈钢,在编织、压制前预先对金属丝进行耐蚀涂层与疏水涂层处理;所述耐蚀涂层处理所用沉积方法为气相沉积技术,涂层为贵金属涂层、贵金属氧化物涂层、金属氮/碳化物涂层中的一种;所述疏水涂层处理所用沉积方法为气相沉积技术,涂层为二氧化硅基涂层。基于以上技术方案,优选的,所述气相沉积技术为闭合非平衡闭合非平衡磁控溅射技术、原子层沉积(ald)技术,沉积涂层为氮化钛、铂或碳化铌,具体包括如下步骤:
57.(1)金属丝的预处理:将待制备的金属丝经拉拔成70-120μm纤维状后置于50-70℃、30-38%的hcl中酸洗3-10min,取出后再用大量去离子水及无水乙醇冲洗。去除表面的氧化物、污迹等。
58.(2)沉积耐蚀涂层:以贵金属、贵金属氧化物、金属氮/碳化物作为反应前驱体,经预处理的金属丝作为基材进行反应,反应温度根据沉积涂层的不同可选择300-700℃、200-300℃范围,最终沉积45-55nm厚的薄膜。
59.(3)沉积疏水涂层:以双(二异丙氨基)乙硅烷(bdipads)作为前驱体,以臭氧作为反应物,以金属丝为基材,反应温度50-300℃,一个反应周期内轮流通入2s bdipads、30s氮气、5s臭氧、60s氮气,最终沉积约5nm厚的薄膜。
60.(4)编织压制成毡:将沉积保护涂层后的金属丝通过平纹或斜纹编织法编织成金属纤维网。随后使用压力机在100-200mpa范围内加压,清洗后置于1000-1250℃的高温真空烧结炉中进行烧结,保温1-4小时后随炉缓慢冷却1小时,使炉内温度降至650℃,得到金属纤维毡材料。
61.实施例1
62.一种质子交换膜水电解池用低成本金属纤维毡扩散层及其制备方法和应用,以不锈钢丝为基材,在其表面原子层沉积制备50nm tin涂层和二氧化硅基疏水涂层,工艺过程
如下:
63.(1)不锈钢丝预处理:依次使用去离子水、丙酮、无水乙醇对不锈钢双极板表面超声清洗并将其烘干;
64.(2)将预处理过的不锈钢丝悬空挂于原子层沉积炉腔内,抽真空至本底真空3
×
10-5
torr后。通入300s氩气并使衬底与环境达到热平衡,然后通入10s混合气体,即体积15% h2和余量ar,采用13.56mhz的射频电源产生等离子体,功率为400w,工作压强为200pa,工作温度为300℃。根据衬底比表面积循环若干次后,通入100% h2并保持120s使衬底表面悬键充分钝化。
65.(3)采用ticl4和nh3为前驱体,脉冲交替注入真空腔进行反应,ticl4注入1s,ar注入2s,nh3注入4s,控制沉积温度为390℃,通过控制循环次数控制涂层厚度为50nm。
66.(4)将沉积保护涂层后的金属丝通过平纹或斜纹编织法编织成金属纤维网,使用压力机在200mpa范围内加压,清洗后置于1250℃的高温真空烧结炉中进行烧结,保温3小时后随炉缓慢冷却1小时,使炉内温度降至650℃,得到金属纤维毡材料。
67.(5)以双(二异丙氨基)乙硅烷作为前驱体,以臭氧作为反应物,以金属丝为基材,反应温度50-300℃,一个反应周期内轮流通入2s双(二异丙氨基)乙硅烷、35s氮气、10s臭氧、60s氮气,最终沉积约5nm厚的二氧化硅基涂层。
68.将制备完成的扩散层置于腐蚀测试池中,在2v/she工作电位下运行24小时,记录得腐蚀电流密度《10μa/cm2,远低于未沉积耐蚀涂层tin涂层时测的电流密度436μa/cm2。腐蚀溶液中金属离子析出量分别为:fe,720ppb;cr,281.1ppb,远低于热压后再沉积耐蚀涂层的样品:fe,648ppm,cr,1330ppm。与钛极板在1.4mpa工作环境下接触电阻为9.9mω/cm2。
69.实施例2
70.一种质子交换膜水电解池用低成本金属纤维毡扩散层及其制备方法和应用,以不锈钢丝为基材,在其表面采用非平衡闭合场磁控溅射制备50nm nbc涂层和二氧化硅基疏水涂层,工艺过程如下:
71.(1)不锈钢丝预处理:依次使用去离子水、丙酮、无水乙醇对不锈钢双极板表面超声清洗并将其烘干;
72.(2)将预处理过的不锈钢丝悬挂于炉腔内的行星转架台上,保持转架转速为4r/min,抽真空至本底真空3
×
10-5
torr后,充入氩气并保持工作气压为4
×
10-4
torr,不锈钢基体施加偏压-700v,使离子对基体表面持续轰击,清除表面上的钝化膜,清洗时间30min;
73.(3)通入30sccm氩气作为溅射气体,保持基体偏压在-60v,开启nb靶电流保证靶材功率2.6w/cm2,在不锈钢丝表面沉积纯nb金属过渡层,沉积时间600s。
74.(4)通入30sccm氩气作为溅射气体,并通入4sccm反应气体乙炔,保持基体偏压在-60v,沉积时间约1200s;
75.(5)将沉积保护涂层后的金属丝通过平纹或斜纹编织法编织成金属纤维网,使用压力机在200mpa范围内加压,清洗后置于1250℃的高温真空烧结炉中进行烧结,保温3小时后随炉缓慢冷却1小时,使炉内温度降至650℃,得到金属纤维毡材料。
76.(6)以双(二异丙氨基)乙硅烷作为前驱体,以臭氧作为反应物,以金属丝为基材,反应温度50-300℃,一个反应周期内轮流通入2s双(二异丙氨基)乙硅烷、35s氮气、10s臭氧、60s氮气,最终沉积约5nm厚的疏水涂层。
77.将以上扩散层在1.6v/she工作电位下运行10小时、在0.84v/she工作电位下运行24小时,记录得腐蚀电流密度均<10μa/cm2,如图2所示,水接触角》100
°
,如图3所示。
78.综上可知,本发明使用不锈钢与耐蚀、疏水涂层技术方案代替传统钛基扩散层,在质子交换膜水电解池中表现出优异的耐蚀性和耐久性,可以满足电解堆中长期稳定运行要求,同时显著降低了质子交换膜水电解制氢堆的材料成本。
79.本发明中涂层高度耐腐蚀性的关键因素在于耐蚀涂层沉积工序优先于不锈钢基扩散层的热压成型,不锈钢丝热压成型后,内部存在大量微米孔隙,现有涂层沉积技术难以实现微观上的100%覆盖,而腐蚀后离子析出量为ppb量级证明了本发明的涂层覆盖程度较传统方法有显著提升。同时,本发明中的沉积技术采用原子层沉积技术或非平衡磁控溅射,这两种沉积技术可以保证涂层基底与沉积介质(前驱体或等离子体)充分接触,同样保证了涂层沉积的致密度与覆盖度。
80.以上所述,仅是本发明的较佳实施例而已,并非是对本发明作其它形式的限制,任何熟悉本专业的技术人员可能利用上述揭示的技术内容加以变更或改型为等同变化的等效实施例。但是凡是未脱离本发明技术方案内容,依据本发明的技术实质对以上实施例所作的任何简单修改、等同变化与改型,仍属于本发明技术方案的保护范围。