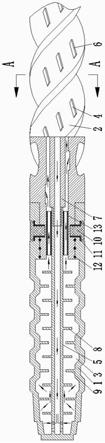
[0001]
本发明涉及钻杆领域,具体涉及一种内冷却钻杆。
背景技术:[0002]
现有技术中对钻杆的冷却常接入水冷系统进行外冷却,使得冷却及其的不方便,且在钻杆钻进过程中频繁挪动钻杆会出现扩孔的现象,导致钻杆轴心的偏差,最终导致使用寿命降低或是直接断裂的情况。
[0003]
因此,为解决以上问题,需要一种内冷却钻杆,能够对钻杆进行自冷却,提高钻杆的使用寿命。
技术实现要素:[0004]
有鉴于此,本发明的目的是克服现有技术中的缺陷,提供内冷却钻杆,能够对钻杆进行自冷却,提高钻杆的使用寿命。
[0005]
本发明的内冷却钻杆,包括相连接的碎渣段和排渣段,所述碎渣段和排渣段内有相连通的冷却通道,所述冷却通道的冷却途径为,先经排渣段对碎渣段冷却,随后继续对排渣段冷却。
[0006]
进一步,所述冷却通道连接水冷系统,所述排渣段上开设有连通冷却通道的回流腔,所述排渣段上开设有连通外界环境的等压孔,所述回流腔连通等压孔。
[0007]
进一步,所述碎渣段和排渣段沿着排渣段轴向方向同轴心设置;所述冷却通道包括连接在碎渣段上的碎渣段水冷管,所述冷却通道还包括连接在排渣段上的排渣段水冷管,所述碎渣段水冷管连通排渣段水冷管。
[0008]
进一步,所述碎渣段水冷管和排渣段水冷管沿着排渣段轴向方向与排渣段同轴心设置。
[0009]
进一步,所述碎渣段水冷管沿排渣段径向方向向碎渣段的内壁延伸,形成碎渣段水冷管挡流板。
[0010]
进一步,所述碎渣段的内壁延伸沿排渣段径向方向向碎渣段延伸,形成碎渣段挡流板。
[0011]
进一步,所述碎渣段水冷管挡流板和碎渣段挡流板沿排渣段轴向方向交错布置,以使得水流方向沿排渣段轴向方向呈波浪形。
[0012]
进一步,所述排渣段上设置有导渣凸筋,所述导渣凸筋沿着排渣段旋近方向排列布置。
[0013]
进一步,所述导渣凸筋沿排渣段径向方向的截面呈朝向排渣段斜向过渡的斜坡,所述斜坡的朝向与排渣段旋近方向一致。
[0014]
进一步,所述等压孔开设在导渣凸筋上。
[0015]
本发明的有益效果是:本发明公开的一种内冷却钻杆,通过设置的自冷却通道使得对钻杆进行冷却,且冷却水还可加快矿渣的导出,使得提高钻孔效率,设置的密闭连接结
构,更是使得在钻进过程中保证良好的结构强度,不会出现旋钻或是托钻的情况。
附图说明
[0016]
下面结合附图和实施例对本发明作进一步描述:
[0017]
图1为本发明的结构示意图;
[0018]
图2为本发明a-a向的结构示意图。
具体实施方式
[0019]
图1为本发明的结构示意图,如图所示,本实施例中的内冷却钻杆包括相连接的碎渣段1和排渣段2,所述碎渣段1用于钻壁,所述排渣段2连接至钻机,所述碎渣段1和排渣段2内有相连通的冷却通道,所述冷却通道连通至冷却系统,对钻杆进行冷却,所述钻壁、钻机和冷却系统均属于现有技术,在此不再赘述,所述冷却通道的冷却途径为,先经排渣段2对碎渣段1冷却,随后继续对排渣段2冷却;通过设置此类的冷却路径,可以充分的对钻杆进行冷却,并且自冷却循环或是直接排出均比外冷却操作难度低,钻杆钻孔精度更高,同时可提高打钻效率,减少外冷却的繁琐步骤。
[0020]
本实施例中,所述冷却通道连接水冷系统,所述水冷系统属于现有技术,更准确的叙述,即为冷却通道的一端连接在水冷系统的出水口,另一端则设置在钻杆内,所述排渣段2上开设有连通冷却通道的回流腔3,所述冷却通道的另一端即连接回流腔3,所述排渣段2上开设有连通外界环境的等压孔6,所述回流腔3连通等压孔6。这样设计的冷却路径即实现了水流先对排渣段2进行冷却,随后对碎渣段1进行冷却,最后回流至排渣段2上的等压孔6排出,实现一次冷却,所述等压孔6为若干个,根据实际情况选择和布置,在此不再赘述;当然冷却途径还可直接回收回流水继续做循环冷却,在此不再赘述,本方案设计将冷却水通过等压孔6排出可以使得排渣段2的渣体更顺畅的排出,且能降低粉尘,更是可以第三次的对排渣段2进行冷却,由于排渣段2连接钻机,不断的冷却可保证其刚度,且排渣更迅速也能使得整体钻杆的轴心更平稳,使得提高钻孔效率的同时,钻孔的精度也得到保证;所述排渣段2上设置有导渣凸筋4,所述导渣凸筋4沿着排渣段2旋近方向排列布置,设置导渣凸筋4可进一步提高对渣滓的排出,且在钻机反转时还能起到碎渣的作用,当钻进困难或是排渣困难时,可反转电机通过设置的导渣凸筋4进行扒渣、碎渣,提高钻孔效率,保证钻孔精度;所述导渣凸筋4沿排渣段2径向方向的截面呈朝向排渣段2斜向过渡的斜坡,所述斜坡的朝向与排渣段2旋近方向一致;此类设计即可保证导渣时的顺畅性,同时也能保证碎渣时结构的强度,保证钻杆整体刚度,提高钻孔效率,本方案中的导渣凸筋4沿排渣段2径向方向的截面为三角形,首先其具备结构强度高稳定性强的优点,其次其只有三条边,没有多余的加工料且不影响钻进,降低钻进负担同时提高碎渣效率,当然导渣凸筋4也可设置成长方体或是锥形等,在此不再赘述,所述导渣凸筋4沿着排渣段2的旋进方向均匀的布置在排渣段2的排渣槽上,当然布置的位置及个数全部依照实际请款布置和选择,其还可交错布置或是对向布置均可,交错布置即为沿着同一方向顺序的交互布置,而对向布置则是两个导对向设置的渣凸筋为一组,多组沿着同一方向顺序的布置,既能起到排渣速度快的作用,又具备碎渣效率高的特点,在此不再赘述,所述等压孔6开设在导渣凸筋4上连通至回流腔3,也就是说冷却水会从导渣凸筋上排出,所述等压孔6开设在导渣凸筋4沿排渣段2径向远离排渣段2的一
个角上,以使得在排出冷却水是排水口较大可对此处产生的碎渣进行润湿,加快排渣,所述等压孔6沿排渣段2径向均连通至回流腔3,本方案中所述回流腔3一直延伸至排渣段2的内腔,但仅通过冷却通道的一个端口连通至回流腔3,然后冷却水从若干个所述的等压孔6排出,起到冷却、加快排渣的作用,当钻机反转时若有部分碎渣进入至回流腔3,也会随着水流的不断涌出继续朝向下一等压孔6排出,且由于钻杆多受径向力作用,而碎渣在受到离心力时,还是会排出,所述回流腔3的终端还可以连接有回收装置,降低阻塞的几率,对钻杆进行一定的保护,起到保障的作用,在此不再赘述。
[0021]
本实施例中,所述碎渣段1和排渣段2沿着排渣段2轴向方向同轴心设置;所述冷却通道包括连接在碎渣段1上的碎渣段水冷管5,所述冷却通道还包括连接在排渣段2上的排渣段水冷管7,所述碎渣段水冷管5连通排渣段水冷管7,同轴心设置的碎渣段1和排渣段2沿着排渣段2,可提高钻杆钻进效率,同时碎渣段水冷管5和排渣段水冷管7的连通还是起到导流的作用;所述碎渣段水冷管5和排渣段水冷管7沿着排渣段2轴向方向与排渣段2同轴心设置;碎渣段水冷管5和排渣段水冷管7也是同轴心设置,同样可以起到加快流体流速且提高冷却效率的作用,当然此处不过多的对冷却途径进行逐一描述,其还可以为蜿蜒盘旋状的冷却水管,或是反复弯折的冷却水管,还可以是蜿蜒盘旋状结合反复弯折状的复合形状的冷却管,在此不再赘述,均可以起到相同的冷却效果,本方案中,所述碎渣段水冷管5沿排渣段2径向方向向碎渣段1的内壁延伸,形成碎渣段水冷管挡流板8;所述碎渣段1的内壁延伸沿排渣段2径向方向向碎渣段1延伸,形成碎渣段挡流板9;所述碎渣段水冷管挡流板8和碎渣段挡流板9沿排渣段2轴向方向交错布置,以使得水流方向沿排渣段2轴向方向呈波浪形,此类结构可以使得水流充分地对钻杆进行冷却,且可使得水冷效果得到极大的改善,相同冷却效果的情况下还可以起到节水的效果,使得水冷更加充分,降低水资源的浪费,水流方向如图所示,即为波浪形,本方案中的碎渣段1采用的是六棱结构的破碎刀,其还可以是三棱的或是直接由壁厚较厚的破碎刀具进行碎渣,在此不再赘述,所述排渣段2采用的是螺旋式槽深较宽的螺旋钻杆,当然排渣段2也可根据实际请款选择,便于排渣同时也利于对导渣凸筋4的布置,在此不再赘述,所述碎渣段水冷管挡流板8和碎渣段挡流板9均为圆盘状结构,便于导流,同时面积更大,当然其布置结构也可是三角形,四边形等结构,在此不再赘述。
[0022]
本实施例中,所述碎渣段1和排渣段2之间通过锁紧段连接,所述碎渣段1沿排渣段2轴向方向靠近排渣段2一端设置有内螺纹,所述排渣段2沿排渣段2轴向方向靠近碎渣段1一端设置有外螺纹,二者螺纹锁紧后通过紧固螺钉10进行径向加固锁紧,所述紧固螺钉10通过防水胶垫11锁紧排渣段2和碎渣段1,所述排渣段2和碎渣段1之间还连接有防水垫圈12,所述防水垫圈12外套在排渣段2上,被固定压紧在排渣段2和碎渣段1之间,起到防止内部冷却水泄露的作用;所述碎渣段水冷管5和排渣段水冷管7也通过螺纹锁紧固定连接,且在二者的连接处还外套有支撑套13,所述支撑套13上开设有导流孔,便于冷却水的流通,设置支撑套13可保证冷却水管的结构强度,同时有着加固碎渣段水冷管5和排渣段水冷管7连接的作用,在此不再赘述。
[0023]
最后说明的是,以上实施例仅用以说明本发明的技术方案而非限制,尽管参照较佳实施例对本发明进行了详细说明,本领域的普通技术人员应当理解,可以对本发明的技术方案进行修改或者等同替换,而不脱离本发明技术方案的宗旨和范围,其均应涵盖在本
发明的权利要求范围当中。