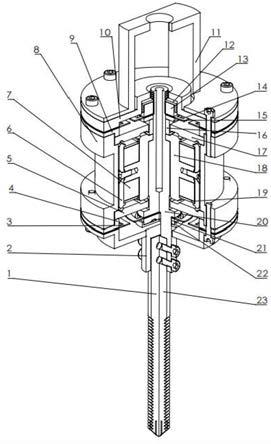
1.本发明涉及硬岩掘进装置技术领域,具体涉及一种双侧磁力驱动式低反力双体振贯装置。
背景技术:2.硬岩钻取通常都是采用旋转电机带动钻头钻取,这种钻取方式耗能大,结构复杂,在钻取过程中会产生大量的热量,这会破坏岩石内部结构的物理特性。单侧磁力驱动式低反力双体振贯装置冲击功以及掘进速率低,不同岩石密度不同,针对密度大的岩石,不仅需要功耗低、发热量低、低反力的振贯装置,更需要较大的冲击功以及掘进速率。但现有的硬岩钻取装置均不能达到功耗低、发热量低、低反力且掘进速率高。
技术实现要素:3.发明目的:本发明提出一种双侧磁力驱动式低反力双体振贯装置,其目的在于解决现有硬岩钻取装置均不能达到功耗低、发热量低、低反力且掘进速率高的问题。
4.技术方案:一种双侧磁力驱动式低反力双体振贯装置,该装置的第一振动组与第二振动组的上端通过上弹簧连接,第一振动组与第二振动组的下端通过下弹簧连接,上弹簧与下弹簧为薄板弹簧,薄板弹簧整体为圆形,分为外圈和内圈,外圈与内圈之间涡旋连接的结构;第一振动组包括外壳、上端盖、下端盖、上衔铁、下衔铁、传感器支架和第一机具,外壳内侧的上部固定卡接有上衔铁,外壳内侧的下部固定卡接有下衔铁,外壳上端依次固定连接有上端盖和传感器支架,外壳上端与上端盖之间固定压紧上弹簧的外圈,外壳下端固定连接有下端盖,外壳下端与下端盖之间固定压紧下弹簧的外圈,下端盖端部固定连接有第一机具;第二振动组包括中心柱、电磁铁、上弹簧压盖、下弹簧压盖、和第二机具,中心柱上端固定套接上弹簧的内圈,中心柱中部固定套接电磁铁,中心柱下部固定套接下弹簧,中心柱底端与第二机具固定连接,第二振动组电磁铁与上衔铁和下衔铁之间均存在1.0-2.0mm初始间隙。
5.进一步的,中心柱上端螺纹连接有上弹簧压盖,内骨架顶端上方依次设置有套筒和上弹簧垫片,套筒套接在中心柱上;上弹簧垫片与上弹簧压盖之间压紧上弹簧内圈,中心柱下端面下方压紧连接有下弹簧压盖,下弹簧压盖与中心柱下端面之间压紧下弹簧内圈。
6.进一步的,电磁铁包括内骨架、外骨架、线圈、垫木,中心柱中部固定套接内骨架,内骨架分为上下两个缠绕区,且内骨架上下两端卡接有垫木,上下两个缠绕区上均缠绕有线圈,内骨架缠绕有线圈处的外周固定套接有外骨架,外骨架和内骨架固定连接。
7.进一步的,第一机具与第二机具之间留有间隙,第一机具与第二机具外侧面采用锯齿形结构,第一机具与第二机具的顶部采用带有排屑槽的锥头结构。
8.优选的,第二振动组电磁铁与上衔铁和下衔铁之间均存在1.5mm初始间隙。
9.本发明具有如下有益效果:本装置结构简单,耗能低,拆卸方便,不同与回转钻取的方式,直线驱动发热量少,钻取效率高,取消了轴承结构,无需润滑,可以应用于航天等复杂的环境。单侧磁力驱动式低反力双体振贯装置由于是一侧的磁力作为驱动力,另一侧的弹簧力作为反弹力,所以冲击功和掘进速率较低,应用范围有限。采用双侧磁力驱动,均由电磁铁提供驱动力,冲击功大和掘进速率高,实用范围广,可适用于多数硬岩,且功耗低、发热量低、低反力且掘进速率高。
附图说明
10.图1本发明实施例的轴测图;图2本发明实施例的局部剖视图;图3本发明第一振动组剖视图;图4本发明第二振动组剖视图;图5本发明零部件涡旋线上弹簧示意图;图6本发明零部件涡旋线下弹簧示意图;图7本发明驱动单元示意图;图8为机具结构示意图;图9为两振动组信号波形图;图10为两振动组工作波形图;图11为电磁力与电流、气隙的关系图;图12为1a电流下掘进速率与频率、占空比的关系图;图13为1.5a电流下掘进速率与频率、占空比的关系图;图14为2a电流下掘进速率与频率、占空比的关系图;图中标注:1、第一机具,2、下端盖,3、下弹簧,4、下衔铁压盖,5、下衔铁,6、外骨架,7、线圈,8、外壳,9、上衔铁压盖,10、上端盖,11、传感器支架,12、上防撞套,13、上弹簧压盖,14、上弹簧,15、上弹簧垫片,16、套筒,17、上衔铁,18、内骨架,19、垫木,20、中心柱,21、下弹簧压盖,22、下防撞套,23、第二机具,24、电磁铁,25、缠绕区。
具体实施方式
11.下面结合附图对本发明作进一步说明。
12.由图1-4所示,一种双侧磁力驱动式低反力双体振贯装置,该装置利用电磁铁分别交替吸放下衔铁5和上衔铁17,使与上、下衔铁相连的第一振动组和与电磁铁相连的第二振动组形成相对运动,该装置的第一振动组与第二振动组的上端通过上弹簧14连接,第一振动组与第二振动组的下端通过下弹簧3连接,第一振动组的衔铁与第二振动组电磁铁之间存在1.0-2.0mm初始间隙,优选第一振动组的衔铁与第二振动组电磁铁之间存在1.5mm初始间隙。间隙过大,则电磁力所提供的驱动力就过小;间隙过小,则冲击行程不够,掘进效果不佳。
13.工作原理:双侧磁力驱动双体振贯装置是采用电磁铁24分别交替吸放下衔铁5和上衔铁17,使与上、下衔铁相连的第一振动组和与电磁铁相连的第二振动组形成交替冲击运动,上侧线圈通电,电磁铁与上衔铁17相吸引,即第二振动组向上运动,第一振动组向下
产生冲击;下侧线圈通电,电磁铁24与下衔铁5相吸引,即第一振动组向上运动,第二振动组向下产生冲击。双侧磁力驱动以提供更大的冲击功和掘进速率。
14.本装置驱动两振动组交替向下做冲击运动依靠的均是电磁力,电磁力远大于弹簧的回复力;双侧的电磁铁与上下两衔铁的初始间隙为1.5mm,每次冲击的实际距离为从上衔铁到下衔铁的距离3mm,本装置的冲击功远大于现有装置的冲击功;因此,本装置在功耗低、发热量低的条件下,能达到很好的掘进破碎效果。
15.弹簧既能复位又能定位,提高了零件功能的利用率。在掘进过程中,由于弹簧的存在,会抵消很大一部分反力,所以装置的低反力特性好。上弹簧14与下弹簧3为薄板弹簧,薄板弹簧整体为圆形,分为外圈和内圈,外圈与内圈之间涡旋连接的结构;图5和图6为上下两薄板弹簧结构图。该弹簧是一种区别于传统弹簧的板弹簧,该弹簧作为柔性支撑使用,由于它的径向支撑能力强,所以起到径向定位作用。弹簧采用与传统弹簧不同的涡旋线薄板弹簧,其具有体积小,质量轻,径向刚度大等优点。薄板弹簧的厚度为1.5mm,涡旋线弹簧能够很好的避免应力集中,涡旋线板弹簧到达工作极限位置时的最大应力小于该弹簧材料的抗拉强度,并且弹簧的轴向刚度为24n/mm,径向刚度为94n/mm,能够起到很好的支撑作用和具有一定的回复力。由于该装置所需弹簧的工作状态为上下多次反复变形,涡旋线弹簧具有良好的疲劳寿命,能够符合本装置的工作条件。
16.如图1-3所示,第一振动组包括外壳8、上端盖10、下端盖2、上衔铁17、下衔铁5、上衔铁压盖9、下衔铁压盖4、传感器支架11和第一机具1,外壳8不导磁,仅起到支撑整体的作用,外壳8内侧的上部止口处固定卡接有上衔铁17,并通过上衔铁压盖9压紧固定;外壳8内侧的下部止口处固定卡接有下衔铁5,并通过下衔铁压盖4压紧固定。外壳8上端依次固定连接有上端盖10和传感器支架11,外壳8上端与上端盖10之间固定压紧上弹簧4的外圈,外壳8下端固定连接有下端盖2,外壳8下端与下端盖2之间固定压紧下弹簧3的外圈,下端盖2端部通过螺钉固定连接有第一机具1。
17.如图1-2、4所示,第二振动组包括中心柱20、电磁铁24、上弹簧压盖13、下弹簧压盖21、和第二机具23,第二振动组的主体为中心柱20,中心柱20上端固定套接上弹簧14的内圈,中心柱20中部固定套接电磁铁24,中心柱20下部固定套接下弹簧3,中心柱20底端通过两个内六角螺钉与第二机具23固定连接。
18.中心柱20上端螺纹连接有上弹簧压盖13,上弹簧压盖13外部套有上防撞套12,内骨架18顶端上方依次设置有套筒16和上弹簧垫片15,套筒16套接在中心柱20上;套筒16用于压紧内骨架18并且使弹簧与外壳上端相平行。通过上弹簧垫片15与上弹簧压盖13之间压紧上弹簧14内圈,中心柱20下端面下方通过两螺钉压紧连接有下弹簧压盖21,下弹簧压盖21与中心柱20下端面之间压紧下弹簧3内圈,下弹簧压盖21外部套有下防撞套22。
19.电磁铁24包括内骨架18、外骨架6、线圈7、垫木19,中心柱20中部固定套接内骨架18,如图7所示,内骨架18分为上下两个缠绕区25,且内骨架18上下两端设置有止口处卡接有垫木19,垫木19用于避免内骨架18上的线圈7脱落,上下两缠绕区的间隙为8mm,能够有效的防止上下两线圈通电时,产生的磁化影响彼此的区域。上下两个缠绕区25上均缠绕有线圈7,内骨架18缠绕有线圈7处的外周固定套接有外骨架6,外骨架6和内骨架18通过螺钉固定连接,内骨架18、外骨架6、线圈7、垫木19组成电磁铁24。
20.第一机具1与第二机具23之间留有0.2mm间隙,防止两机具之间产生相对摩擦。如
图8所示,第一机具1与第二机具23外侧面采用1.5mm
×
1.5mm的锯齿形结构,第一机具1与第二机具23的顶部采用带有排屑槽的锥头结构。第一机具1与第二机具23依次交错冲击硬岩,达到破碎硬岩的作用。
21.装配方式:本装置的驱动机构由电磁铁及上衔铁17、下衔铁5组成。上衔铁17与下衔铁5分别卡在外壳8内侧的止口上,分别通过上衔铁压盖9和下衔铁压盖4压紧固定。下端盖2与第一机具1通过螺钉连接。第二振动组的线圈7缠绕在由软铁制成的内骨架18上,内骨架18上、下方伸出止口,用于卡住垫木19,外侧通过螺钉固定连接外骨架6,形成电磁铁。电磁铁通过内骨架18内侧止口套在中心柱20上,内骨架18内侧止口上依次通过套筒16、上弹簧垫片15和上弹簧压盖13压紧固定。第二机具23通过两个内六角螺钉与中心柱20相连接。上弹簧14放置于上弹簧垫片15上,通过上端盖10压紧,通过上弹簧压盖13与中心柱20进行螺纹连接锁紧,下弹簧3通过下端盖2压紧,通过两螺钉使得下弹簧压盖21和中心柱20下端面固定,固定下弹簧3。上弹簧压盖13与下弹簧压盖21分别套上防撞套12、下防撞套22。为提供均衡的力,第一振动组与第二振动组质量基本一致,第一振动组与第二振动组通过上弹簧14和下弹簧3做柔性支撑,并为其提供回复力。第一机具1与第二机具23依次交错冲击硬岩,达到破碎硬岩的作用。
22.使用方法,步骤如下:步骤1:24v的开关电源连接两驱动器,为两驱动器供电,两驱动器分别连接内骨架18上侧和下侧缠绕的线圈7;并且两驱动器的一端口与dspace的d/a口连接。运用simulink软件搭建该装置的工作框图,通过dspace控制该装置的工况。
23.步骤2:分别对内骨架18上侧和下侧缠绕的线圈7通电,上侧和下侧线圈7通电时间需有延迟,延迟时间为方波信号为0时的时间,或者可以通过方波信号调整,根据不同的振贯对象通过调整方波信号的频率,来调整该装置工作的频率,通过调整方波信号的幅值,来调整通入电流的大小。
24.工作时,该装置通过两驱动器对第一振动组与第二振动组进行驱动,上侧线圈7与下侧线圈7依次交错通入电流,上侧线圈7通入电流时,线圈7与软铁骨架形成电磁铁,电磁铁通过磁力吸引上衔铁17,即第一振动组做向下冲击运动,与此同时上弹簧14和下弹簧3轴向受力变形储存能量,上侧线圈7断电,依靠上弹簧14和下弹簧3回复力使得电磁铁恢复原位。同理,下侧线圈7通入电流时,线圈7与软铁骨架形成电磁铁,电磁铁通过磁力吸引下衔铁5,即第二振动组做向下冲击运动,与此同时上弹簧14和下弹簧3轴向受力变形储存能量,下侧线圈7断电,依靠上弹簧14和下弹簧3回复力使得电磁铁恢复原位。如此反复工作,第一振动组与第二振动组不断相互运动,带动末端的第一机具1与第二机具23交错冲击硬岩。
25.两驱动器通过simulink软件搭建的控制框图的方波信号进行控制,如图9-10,图9为两振动组信号波形图,图10为两振动组工作波形图。方波信号为1时,即线圈通电,方波信号为0时,即线圈断电。其中第一振动组直接通入方波信号,两振动组的方波信号具有一定的相位差,第二振动组相对第一振动组增加一个延时信号,保证两振动组的通电驱动相互交替。当第一振动组通入方波信号开始工作后,第二振动组延时一段时间后通入方波信号开始工作,即呈现第一振动组与第二振动组交替工作。
26.第一振动组与第二振动组皆未通电的时间由方波信号的占空比表示,即1-2*(占
空比)。当占空比为50%时,两振动组皆未通电的时间为0%,当占空比为40%时,两振动组皆未通电的时间为20%。通过调整方波信号的频率,来调整该装置工作的频率,通过调整方波信号的幅值,来调整通入电流的大小。
27.在保证电磁铁不磁饱和的情况下,电流越大,电磁力越大,但是线圈的线径影响限制通入电流的大小,该装置采用0.38mm的铜线圈,最大输入电流不超过2a;频率的大小是依靠所破碎的岩石的共振频率决定;占空比的大小为了决定两振动组通电的间隔时间,留有一定的间隔时间保证振动组依靠弹簧的回复力回复到初始位置。
28.图11为该装置电磁力即驱动力与电流、气隙的关系图。在一定的电流下,上下衔铁与电磁铁之间的气隙越小,用作驱动的电磁力越大。气隙越小,电磁力(驱动力)越大,即越往掘进方向力越大,有利于提高掘进效果。该装置采用的是电磁铁分别吸放上下衔铁达到冲击目的,是依靠电磁力当作其驱动力。图11为该装置电磁力与电流、气隙的关系图。电流越大,该装置的驱动力越大。在一定电流下,上下衔铁与电磁铁之间的气隙越小,电磁力越小。工作气隙越小,该装置的驱动力越大,即越往掘进方向力越大;在该装置一个工作周期内,掘进深度越大,驱动力越大,有利于提高该装置对岩石的破碎效果。
29.为验证本装置的掘进破碎能力,通过试验进行分析,通过调节不同电流、频率以及不同占空比,对具有一定强度的耐火砖的掘进破碎实验,图12-14分别为通入1a、1.5a和2a的电流下该装置的掘进速率与频率和占空比的关系。其中电流幅值为1a时,占空比为50%,掘进频率为50hz的掘进速率最高,为13.5mm/min。电流幅值为1.5a时,占空比为40%,掘进频率为40hz的掘进速率最高,为16.5mm/min。电流幅值为2a时,占空比为40%,掘进频率为30hz的掘进速率最高,为17.8mm/min。输入2a电流幅值、40%占空比和30hz的参数为最优的掘进参数。