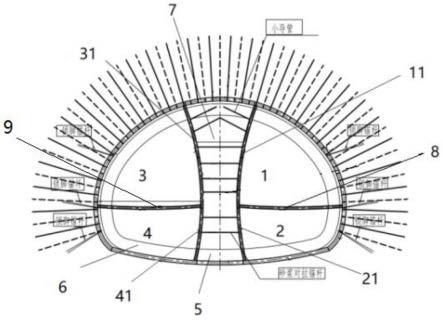
1.本发明涉及隧道施工的技术领域,具体地说是一种双侧壁导坑隧道施工方法,尤其涉及一种减少地表沉降的双侧壁导坑隧道施工方法。
背景技术:2.现有技术中,城市大断面暗挖隧道施工会造成地表沉降、倾斜,严重时会对地表构筑物造成损害,因此施工时往往选择双侧壁导坑法配合机械施工控制地表沉降,但是传统双侧壁导坑法施工进尺较慢、成本较高。
3.同时,传统双侧壁导坑法为了方便两侧导坑和中间核心土施工时均能通行施工机械,横向分块时倾向于大致三等分,致使三部分分块宽度及高度均较小,施工时可选择的机械受限,往往采用一些小型挖掘机配合破碎锤、单勾机或铣挖机,大型机械进洞后净空受限无法正常运转,无法组织施工。
4.因此,急需要一种新型的隧道施工方法,提高施工效率,减小地表沉降。
技术实现要素:5.本发明的目的在于提供一种改进的双侧壁导坑隧道施工方法,通过施工方法的改进、优化临时支护的结构,可以提高30%以上的施工效率,同时临时支护可以重复利用,降低成本。
6.为了实现上述目的,本发明的技术方案是:一种双侧壁导坑隧道施工方法,其特征在于:所述的施工方法包括中间核心土施工和中间核心土两侧的导坑施工,其中两侧导坑的宽度与中间核心土宽度之比为1.3-1.5:1,具体施工步骤如下:a、开挖外侧导坑上台阶部分,施工上台阶部分的初期支护、第一临时强支护和外侧临时仰拱;b、待a步骤进深6-8m时,拆除外侧的临时仰拱,并将拆除的外侧临时仰拱前移用于后续重复使用,开挖外侧导坑下台阶部分,施工下台阶部分的初期支护和第二临时强支护,外侧上、下台阶部分的初期支护互相配合后形成封闭的一侧导坑钢架结构;c、开挖内侧壁导坑上台阶部分,施工上台阶部分的初期支护、第一临时弱支护和内侧临时仰拱;d、待c步骤进深6-8m时,拆除内侧的临时仰拱,并将拆除的内侧临时仰拱前移用于后续重复使用,开挖内侧壁导坑下台阶部分,施工下台阶部分的初期支护、第二临时弱支护,内侧上、下台阶部分的初期支护互相配合后形成封闭的另一侧导坑钢架结构;e、开挖核心土上台阶部分,施工核心土上台阶部分的初期支护,然后拆除核心土内侧对应的第一、第二临时弱支护,形成单侧壁导坑结构;f、继续开挖核心土中、下台阶部分,施工核心土中、下台阶部分的初期支护,使得主洞全周钢架完成封闭成环,然后拆除核心土外侧对应的第一、第二临时强支护;g、施工仰拱和仰拱回填;h、全断面浇筑拱墙。
7.优选的,a步骤中,每次开挖1-2榀钢架间距时,施工外侧上台阶部分的初期支护、第一临时强支护和临时仰拱,然后循环上述工艺。
8.进一步,b步骤中,每次开挖1-2榀钢架间距时,施工外侧下台阶部分的初期支护和
第二临时强支护,外侧上、下台阶部分的初期支护互相配合后形成封闭的一侧导坑钢架结构,然后循环上述工艺。
9.进一步,外侧导坑上、下台阶部分的掌子面前后距离为6-8m,内侧导坑上、下台阶部分的掌子面前后距离为6-8m,两侧导坑的上台阶部分掌子面前后间距为14-16m。
10.更进一步,第一、第二临时强支护包括若干根工字钢架,相邻的工字钢架之间通过钢筋连接,工字钢架的外部喷射有混凝土层;第一、第二临时弱支护包括若干根格栅钢架,相邻的格栅钢架之间通过钢筋拼接而成,格栅钢架与钢筋的外部喷射有混凝土层。
11.相对于现有技术,本发明的技术方案除了整体技术方案的改进,还包括很多细节方面的改进,具体而言,具有以下有益效果:1、本发明所述的改进方案,两侧导坑的宽度与中间核心土宽度之比为1.3-1.5:1,使得施工时可以采用大型机械设备,提高施工效率,同时,外侧上、下台阶部分的初期支护互相配合后形成封闭的一侧导坑钢架结构,内侧上、下台阶部分的初期支护互相配合后形成封闭的另一侧导坑钢架结构,可以有效控制地表沉降,确保地表建筑安全;2、本发明的技术方案的中,开挖核心土上台阶部分,施工核心土上台阶部分的初期支护,然后拆除核心土内侧对应的第一、第二临时弱支护,形成单侧壁导坑结构,既将超大断面有序的化整为零,增强了安全性,又有效的克服了分步小断面对施工效率的影响,解决了以往中间核心土施工不便的问题;3、本发明设置了两种不同结构的临时支护,分别为临时弱支护和临时强支护,采用不同的支护不仅降低了施工成本,同时提高了施工效率,临时支护、临时仰拱还能回收再利用,节约了工程造价;4、本发明施工方法经济、环保,施工中拆除的材料可以反复利用,降低了施工成本,同时由于改进施工步骤和优化施工方法,有效提高了施工效率。
附图说明
12.图1为本发明的施工剖面结构示意图。
13.图2为本发明的一段施工长度的施工方案结构示意图。
14.图3为本发明临时强支护的结构示意图。
15.图4为本发明临时弱支护的结构示意图。
16.图5为本发明格栅钢架的局部放大示意图。
17.图6为图5中a-a向的结构示意图。
18.图7为图5中b-b向的结构示意图。
19.图8为本发明预制仰拱的局部结构示意图。
20.附图标记:1外侧导坑上台阶部分、11第一临时强支护;2外侧导坑下台阶部分、21第二临时强支护;3内侧壁导坑上台阶部分、31第一临时弱支护;4内侧壁导坑下台阶部分、41第二临时弱支护;5仰拱回填、6拱墙、7中部核心土、8外侧临时仰拱、9内侧临时仰拱;10格栅钢架、101混凝土层、102方形钢支架外壳、103 v型支撑钢板、104加强筋、
105左右焊接连板;20工字钢、22钢筋;30吊环、32角钢。
具体实施方式
21.下面将结合附图对本发明的技术方案进行清楚、完整地描述,显然,所描述的实施例是本发明一部分实施例,而不是全部的实施例。基于本发明中的实施例,本领域普通技术人员在没有做出创造性劳动前提下所获得的所有其他实施例,都属于本发明保护的范围。
22.本发明提供了一种双侧壁导坑隧道施工方法,具体参见图1,其与现有技术的区别在于:所述的施工方法包括中间核心土施工和中间核心土两侧的导坑施工,其中两侧导坑的宽度与中间核心土宽度之比为1.3-1.5:1,两侧导坑宽度大,可以容纳大型机械设备进行施工,提高工作效率,同时便于各种物资、设备、材料的运输,具体施工步骤如下:a、开挖外侧导坑上台阶部分1,施工上台阶部分的初期支护、第一临时强支护11和外侧临时仰拱8;b、待a步骤进深6-8m时,拆除外侧的外侧临时仰拱8,并将拆除的外侧临时仰拱8前移用于后续重复使用,开挖外侧导坑下台阶部分2,施工下台阶部分的初期支护和第二临时强支护21,外侧上、下台阶部分的初期支护互相配合后形成封闭的一侧导坑钢架结构;c、开挖内侧壁导坑上台阶部分3,施工上台阶部分的初期支护、第一临时弱支护31和内侧临时仰拱9;d、待c步骤进深6-8m时,拆除内侧的临时仰拱9,并将拆除的内侧临时仰拱9前移用于后续重复使用,开挖内侧壁导坑下台阶部分4,施工下台阶部分的初期支护、第二临时弱支护41,内侧上、下台阶部分的初期支护互相配合后形成封闭的另一侧导坑钢架结构;e、开挖核心土上台阶部分,施工核心土上台阶部分的初期支护,然后拆除核心土内侧对应的第一、第二临时弱支护,形成单侧壁导坑结构;f、继续开挖核心土中、下台阶部分,施工核心土中、下台阶部分的初期支护,使得主洞全周钢架完成封闭成环,然后拆除核心土外侧对应的第一、第二临时强支护;g、拆除施工仰拱和仰拱回填5;h、全断面浇筑拱墙6。
23.实施中,施工方法作用于一段一段连续的施工长度单位中,每个施工长度单位为60-90米。新工法根据内、外侧临时仰拱主要作为临时支护成环的作用,创新性的提出采用预制节段,预制节段的纵向宽度为两个施工长度单位,环向长度为2米,预制节段间设置连接构造(如图8所示端部的角钢结构),内、外侧临时仰拱与初期支护、内、外侧临时仰拱与第一临时强、弱支护间设置低标号混凝土后浇段,施工转换时,拆除低标号后浇段,回收内、外侧临时仰拱并转运前移达到重复利用的目的。本做法可以大大节约工程造价,实现隧道施工的初步预制化。
24.实施例1所述的施工方法作用于一段段连续的施工长度单位中,每个施工长度单位为60-90米,本实施例中采用70米的长度,施工方法包括中间核心土施工和中间核心土两侧的导坑施工,其中两侧导坑的宽度与中间核心土宽度之比为1.3-1.5:1,施工方法作用于一段一段连续的施工长度单位中,每段施工长度单位的具体施工步骤如下:a、开挖外侧导坑上台阶部分,施工上台阶部分的初期支护、第一临时强支护和外侧临时仰拱8;b、待a步骤进深6-8m时,拆除外侧的临时仰拱8,并将拆除的外侧临时仰拱8前移用于后续重复使用,开挖外侧导坑下台阶部分,施工下台阶部分的初期支护和第二临时强支护,外侧上、下台阶部分的初
期支护互相配合后形成封闭的一侧导坑钢架结构;c、开挖内侧壁导坑上台阶部分,施工上台阶部分的初期支护、第一临时弱支护和内侧临时仰拱9;d、待c步骤进深6-8m时,拆除内侧的临时仰拱9,并将拆除的内侧临时仰拱9前移用于后续重复使用,开挖内侧壁导坑下台阶部分,施工下台阶部分的初期支护、第二临时弱支护,内侧上、下台阶部分的初期支护互相配合后形成封闭的另一侧导坑钢架结构;e、开挖核心土上台阶部分,施工核心土上台阶部分的初期支护,然后拆除核心土内侧对应的第一、第二临时弱支护,形成单侧壁导坑结构;f、继续开挖核心土中、下台阶部分,施工核心土中、下台阶部分的初期支护,使得主洞全周钢架完成封闭成环,然后拆除核心土外侧对应的第一、第二临时强支护;g、施工仰拱和仰拱回填;h、全断面浇筑拱墙。
25.具体施工中,a步骤中,每次开挖1-2榀钢架间距时,施工外侧上台阶部分的初期支护、第一临时强支护和外侧临时仰拱8,然后循环上述工艺,这里的初期支护、第一临时弱支护和外侧临时仰拱之间设置低标号混凝土后浇段,便于后续的临时仰拱拆卸再利用。 内、外侧临时仰拱由工字钢和喷射在工字钢周围的混凝土构成,工字钢的一侧设有吊环,内、外侧临时仰拱可以拆除后再重复利用,降低施工成本。
26.b步骤中,每次开挖1-2榀钢架间距时,施工外侧下台阶部分的初期支护和第二临时强支护,外侧上、下台阶部分的初期支护互相配合后形成封闭的一侧导坑钢架结构,然后循环上述工艺。
27.外侧导坑上、下台阶部分的掌子面前后距离为6-8m,内侧导坑上、下台阶部分的掌子面前后距离为6-8m,两侧导坑的上台阶部分掌子面前后间距为14-16m,本实施例中为15m。
28.第一、第二临时弱支护包括若干根格栅钢架,相邻的格栅钢架之间通过钢筋拼接而成,格栅钢架与钢筋的外部喷射有混凝土层。格栅钢架由方形钢支架外壳和设在其内部的v型支撑钢板制成,v型支撑板与钢支架外壳的连接处设有加强筋和左右焊接连板,左右焊接连板上设有上、下焊接孔位。具体施工的时候,格栅钢架一侧的钢筋与上焊接孔位相连,另一侧的钢筋与下焊接孔位相连,这样上下间隔设置,增强强度,保证受力的均匀性,提升支护的受力性能。
29.第一、第二临时强支护包括若干根工字钢,相邻的工字钢之间通过钢筋拼接而成,工字钢与钢筋的外部喷射有混凝土层。同理,这里工字钢一侧的钢筋与工字钢上部进行连接,工字钢另一侧的钢筋与工字钢下部进行连接,提升支护的整体强度和受力性能。
30.c、d步骤中,完成上导坑一段施工进深后,回收内、外侧临时仰拱用于下一个施工长度单位中,每个施工长度单位为60-90米。
31.实施例2所述的施工方法作用于一段段连续的施工长度单位中,每个施工长度单位为60-90米,施工方法包括中间核心土施工和中间核心土两侧的导坑施工,其中两侧导坑的宽度与中间核心土宽度之比为1.4:1,施工方法作用于一段一段连续的施工长度单位中,每段施工长度单位的具体施工步骤如下:a、开挖外侧导坑上台阶部分,施工上台阶部分的初期支护、第一临时强支护和外侧临时仰拱8;b、待a步骤进深6-8m时,拆除外侧的临时仰拱8,并将拆除的外侧临时仰拱8前移用于后续重复使用,开挖外侧导坑下台阶部分,施工下台阶部分的初期支护和第二临时强支护,外侧上、下台阶部分的初期支护互相配合后形成封闭的一
侧导坑钢架结构;c、开挖内侧壁导坑上台阶部分,施工上台阶部分的初期支护、第一临时弱支护和内侧临时仰拱9;d、待c步骤进深6-8m时,拆除内侧的临时仰拱9,并将拆除的内侧临时仰拱9前移用于后续重复使用,开挖内侧壁导坑下台阶部分,施工下台阶部分的初期支护、第二临时弱支护,内侧上、下台阶部分的初期支护互相配合后形成封闭的另一侧导坑钢架结构;e、开挖核心土上台阶部分,施工核心土上台阶部分的初期支护,然后拆除核心土内侧对应的第一、第二临时弱支护,形成单侧壁导坑结构;f、继续开挖核心土中、下台阶部分,施工核心土中、下台阶部分的初期支护,使得主洞全周钢架完成封闭成环,然后拆除核心土外侧对应的第一、第二临时强支护;g、施工仰拱和仰拱回填;h、全断面浇筑拱墙。
32.具体来说,两侧导坑的长度分别为7m,使得效率高的大型机械成为可能的施工选择,一些大型的挖掘机和悬臂式隧道掘进机有了足够周转的空间,两侧导坑施工效率明显提升。
33.为了解决中间核心土施工的问题,本工法调整施工工序,其中一侧临时弱支护在中间核心土开挖时拆除,另一侧临时强支护在二衬施工期拆除。待核心土上台阶开挖完成,施工主洞拱部初期支护后,便可拆除该侧临时弱支护,解决了中间核心土的施工问题。拆除一侧临时弱支护后,整个施工工序实际上从双侧壁导坑法转为单侧壁工法,既将超大断面有序的化整为零增强了安全性,又有效的克服了分步小断面对施工效率的影响。
34.同时,本发明的大断面隧道两侧导坑往往分层施做,设置内、外侧临时仰拱。内、外侧临时仰拱传统做法与临时支护相同,采用工字钢+喷射混凝土的做法。传统方法虽然与岩面接触良好但是拆除时因材料损坏无法重复利用造成较大浪费。
35.本次改进型双侧壁导坑法通过调整施工工序、优化导坑尺寸、优化临时支护等措施可有效提高施工效率30%以上,更迅速有效的通过控制段,对确保地表建筑安全意义重大,同时本发明方法亦可明显降低成本。
36.以上内容是结合具体的优选实施方式对本发明所作的进一步详细说明,不能认定本发明具体实施只局限于上述这些说明。对于本发明所属技术领域的普通技术人员来说,在不脱离本发明构思的前提下,还可以做出若干简单推演或替换,都应当视为属于本发明的保护范围。