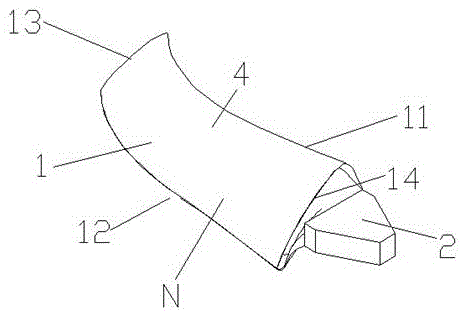
本实用新型属于通风机用叶片
技术领域:
,具体涉及一种用于轴流风机的弯掠式叶片。
背景技术:
:弯掠叶片的成型自上世纪六十年代初提出了,受到世界各国研究人员的高度重视,一些工业发达国家相继开展了弯掠叶片的气动试验和数值计算,并取得了一定的研究成果。随理论和实验研究的发展,弯掠叶片作为螺旋桨和压气机叶片,在气动性能和声学特性上的优点愈来愈被研究人员所证实。美国nasa研究中心1984年的报告指出,采用弯掠螺旋桨的航空发动机,油耗降低15%-40%;近声场降低16dba以上。美国发动机公司已经制造成功具有弯掠静叶和动叶的航空涡轮,级效率达到93%。弯掠方案成功用于飞机机翼的设计以降低跨音和超音飞行时的阻力这一事实,一直鼓励着内流工作者将此思想用于风扇和压气机的设计。现有技术中,有将其用于轴流风机的,但是,其具体是通过弯曲以及下压,但是弯曲和下压都是靠近叶柄端设置,即从根部开始弯掠,实现掠式叶片效果。但是实际工作中,设置从根部开始的掠式叶片,具有以下缺点:1、由于风机工作时,根部不工作,故其从根部开始弯折,作用较小;2、从根部开始弯折下压时,张力大,耗损多;3、从根部开始弯折下压,叶片扭曲部位较多,进而风量风压损失大;同时,为了补充这一损失,需要补弦长,而弦长补的较大,导致叶片宽度以及长度均需要加宽。故现有技术中,在根部开始弯折,形成的风压降低等,无法实现很好的工作效率。技术实现要素:本实用新型的目的在于提供一种通过前部弯曲,形成前弯的掠叶片,提高了降噪效率。为达到上述目的,本实用新型的技术方案如下:一种用于轴流风机的弯掠式叶片,包括叶片主体以及设置于叶片主体端部用于连接叶片主体与电机转轴的连接头;所述叶片主体包括左缘面、右缘面、前缘面和后缘面,分别与左缘面、右缘面、前缘面和后缘面连接的压力面以及与压力面相对的吸力面:所述压力面朝向吸力面向前弯掠,且前弯和前掠的起始点相同,所述压力面朝向吸力面的前掠角度为1°-10°;从所述叶片主体的左缘面延伸至右缘面形成所述叶片主体的宽度,所述叶片主体的宽度在常规工艺尺寸的基础上加宽2%-10%。本技术方案中,通过弯掠,进而叶片工作中,产生的噪音,在下压弯曲处,力得到充分分解,进而噪音的速度变化快,降噪明显。如果只弯不压,风压在此处增加,进而降噪增压,且不增加功率。同时,相比于其它技术,本技术方案中,前掠角度较小,即弯曲较小,叶片加宽少。现有技术中,根部弯折,叶片主体的宽度,至少加快20%,浪费材料,降噪效率不佳。本技术方案中,通过较小的弯掠,以及较少的加宽叶片,实现了降噪的效果。作为本实用新型的进一步改进,所述压力面朝向吸力面的前弯角度为1°-12°。本实施例中,为了避免前弯角度过大时,造成的损失以及后期的弦补,设置前弯角度为1°-12°,此时弯曲角度小,叶片之间安装后,风机使用中,风量风压损失小,提高了风机性能。作为本实用新型的进一步改进,所述压力面朝向吸力面的前掠角度为1°-8°。将掠角从最大10°变为8°,首先,与现有技术掠角基本在15°以上相比,掠角变小,弦补偿少,叶片在原来基础上的加宽量少;当在满足轴流风机的性能时,不仅节省更多的材料;而且叶片重量减轻,搬运方便;同时,能够实现降噪的效果。作为本实用新型的进一步改进,由所述前缘面向后缘面延伸方向为叶片主体的长度方向,沿所述长度方向,所述叶片分为7段弧形,从所述前缘面至所述后缘面,相邻所述弧形之间的弦长差,呈阶梯状递减。进而7段弧形之间,开始相差较大,后面相差越来越小,直至平稳,使得整个弧形结构的过度从陡至平稳,便于靠近前缘面下压弯掠,实现降噪效果。作为本实用新型的进一步改进,7段所述弧形中,以与前缘面连接的为第1段弧形,所述弯掠起始点设置于第3段弧形至第4段弧形之间。本技术方案中,弯掠的起始点,大概位于叶片长度的40%-50%处之间,且靠近前缘面设置,一方面,此时曲线切点从仿真角度来说,效果最佳,同时,迎着气流,力的降解好,降噪效果明显;另一方面,靠近前缘面,远离靠近电机的根部,提高做功,降低风压损耗。作为本实用新型的进一步改进,7段所述弧形中,以与前缘面连接的为第1段弧形,从第1段弧形至第7段弧形,所述弧形对应的弦与电机的安装角度逐渐变小,所述安装角度为6°-40°。安装角度,即弧形与叶片中轴线之间的夹角,通过这一夹角的逐渐变小,进而使得弧形对应的切线越来越靠近叶片的中轴线,便于安装。本实施例中,当安装角小于6°时,叶片与平面之间平行或者夹角过小,转动时无风力,起不到风机的送风作用;如果安装角度太大,大于40°,则对于轴流风机,起不到轴流风机的性能。作为本实用新型的进一步改进,所述连接头为梯形结构或者圆柱形结构。设置多种结构的连接头,使得叶片的安装得到进一步扩展,进而应用是,能够匹配不同的安装方式。作为本实用新型的进一步改进,所述连接头为梯形结构时,所述叶片主体与连接头通过扭曲段连接。当采用梯形结构时,其与轮毂安装中,梯形为直面结构,其与轮毂的弧形安装角度不易调整,即从直面到弧面,安装难,角度难调整;而增加扭曲段,扭曲段上增加弧形段,使得其能够通过弧形段与轮毂方便安装。作为本实用新型的进一步改进,所述扭曲段为多面体结构扭曲5°-40°后形成的扭曲结构,所述多面体结构为圆柱体、四方体、六面体中的一种。采用多面体扭曲,一方面,多面体容易被扭,就像扭麻花一样,方便实现;同时,设定扭曲角度,避免过度扭曲,使得扭曲段强度降低,叶片容易断裂。作为本实用新型的进一步改进,所述连接头一体设置于叶片主体端部或所述连接头通过连接件可拆卸连接于所述叶片主体端部。通过多种设置方式,实现了叶片的多种方式生产,同时,可以根据材料,决定其生产方式;采用一体化设置,结构简单,安装方便,但是不易调整角度,叶片或者连接头任一损坏时,整个结构不能用;而采用连接件可拆卸连接,可以叶片与连接头任意匹配,角度方便调整。通过上述技术方案,本实用新型的有益效果是:本技术方案中,通过弯掠,进而叶片工作中,产生的噪音,在下压弯曲处,力得到充分分解,进而噪音的速度变化快,降噪明显。如果只弯不压,风压在此处增加,进而降噪增压,且不增加功率。同时,相比于其它技术,本技术方案中,前掠角度较小,即弯曲较小,需要补的弦长越小,叶片加宽少。如果采用从根部弯掠,则整个叶片的宽度需要增加至少20%,生产出的叶片,又宽又重,导致风机性能比较差。本实用新型中,采用较小角度的弯掠,进而叶片宽度补充2%-10%,叶片宽度补充少,节省材料,风机性能好。本实用新型中,通过采用中上部以上弯掠,能更好的保证风机的风量风压性能,同时起到较好的降噪效果。现有技术中,从根部开始弯掠,为了实现降噪以及风量风压性能,则叶片宽度较宽,比一般叶片增加20%-40%左右的宽度,浪费材料;采用中上部弯掠,叶片相对宽度减少,节省材料,保证风量风压的同时,有降噪效果。弯掠一般都会降低风压风量,为了弥补风压风量,都需要增加叶片宽度。附图说明为了更清楚地说明本实用新型实施例或现有技术中的技术方案,下面将对实施例或现有技术描述中所需要使用的附图作简单地介绍,显而易见地,下面描述中的附图仅仅是本实用新型的一些实施例,对于本领域普通技术人员来讲,在不付出创造性劳动的前提下,还可以根据这些附图获得其他的附图。图1为本实用新型提供的一种用于轴流风机的弯掠式叶片的立体图之一;图2为本实用新型提供的一种用于轴流风机的弯掠式叶片的立体图之二;图3为本实用新型提供的一种用于轴流风机的弯掠式叶片的立体图之三;图4为本实用新型提供的一种用于轴流风机的弯掠式叶片的立体图之四;图5为本实用新型提供的一种用于轴流风机的弯掠式叶片的立体图之五;图6为本实用新型提供的一种用于轴流风机的弯掠式叶片的立体图之六;图中数字和字母所表示的相应部件名称:1、叶片主体;2、连接头;3、扭曲段;4、弯掠结构;11、左缘面;12、右缘面;13、前缘面;14、后缘面;m、压力面;n、吸力面。具体实施方式为了使本实用新型实现的技术手段、创作特征、达成目的与功效易于明白了解,下面结合具体图示,进一步阐述本实用新型。实施例1参照附图1-3所示,本实用新型公开的一种用于轴流风机的弯掠式叶片,包括叶片主体1以及设置于叶片主体1端部用于连接叶片主体1与电机转轴的连接头2,所述叶片主体1包括左缘面11、右缘面12、前缘面13和后缘面14,分别与左缘面11、右缘面12、前缘面13和后缘面14连接的压力面m以及与压力面m相对的吸力面n:所述压力面m朝向吸力面n向前弯掠,且前弯和前掠的起始点相同,所述压力面朝向吸力面的前掠角度为1°-10°。本实施例中个,弯掠时,具体以叶片主体1的中心线为轴,开始弯掠。本技术方案中,通过弯掠,进而叶片工作中,产生的噪音,在下压弯曲处,力得到充分分解,进而噪音的速度变化快,降噪明显。如果只弯不压,风压在此处增加,进而降噪增压,且不增加功率。参照附图4-6所示,本实施例中,弯掠后,在叶片主体1上形成弯掠结构4。本实施例中,如果以与轮毂垂直的横截面形成平面,则其设有横向的x轴以及y轴,高度方向为y轴,水平方向为x轴,则具体是朝x轴弯,朝y轴掠,进而叶片在整个空间上,是有一定的弯掠角存在的。通过分析可知,风机总噪声级与叶片速度的六次方成正比。根据分析,风机噪声源基本上是偶极子性质的。进一步可推出,噪声是由于叶片作用于流过风机的空气上脉动力所引起的。可以认为风机离散频率噪声源有两个,一个是随着转子叶片运动的压力场引起的螺旋桨式的噪声,另一个是气动干涉引起的叶片脉动力噪声。风机动、静叶片之间的距离是干涉噪声的重要因素。本实施例中,通过前部的弯掠,降低了风机的噪声,具体是,由于弯掠作用,使得叶片作用于流过风机的空气上的脉动力改变,引起的降噪。同时,采用较小的前掠角度,进而需要补充的弦长变少,叶片整体的长宽等结构无需补充过多,进而叶片作用于流过风机的空气上脉动力会改变,进而实现降噪。同时,相比于其它技术,本技术方案中,前掠角度较小,即弯曲较小,需要补的弦长越小,叶片加宽少。众所周知,弯掠角度越大,则叶片弯掠后,需要补充宽度,进而需要补充叶片宽度,增加叶片重量,以满足轴流风机的性能;本技术方案中,通过较小的弯掠,实现了降噪的效果,且需要补充的叶片宽度少。轴流风机在使用中,是有性能要求的,如果叶片不弯不掠,则形成的是直叶片,构成的是离心风机。轴流风机,用途非常广泛,就是与风叶的轴同方向的气流,如电风扇,空调外机风扇就是轴流方式运行风机。之所以称为"轴流式",是因为气体平行于风机轴流动。轴流式风机通常用在流量要求较高而压力要求较低的场合。轴流式风机固定位置并使空气移动。轴流风机主要由风机叶轮和机壳组成,结构简单但是数据要求非常高。离心风机和轴流风机主要区别在于:1、离心风机改变了风管内介质的流向,而轴流风机不改变风管内介质的流向;2、前者安装较复杂;3、前者电机与风机一般是通过皮带带动转动轮连接的,后者电机一般在风机内;4、前者常安装在空调机组进、出口处,锅炉鼓、引风机,等等。后者常安装在风管当中、或风管出口前端。此外还有斜流(混流)风机,风压系数比轴流风机高,流量系数比离心风机大。填补了轴流风机和离心风机之间的空白。同时具备安装简单方便的特点。混流式(或轴向冲流式)风机结合了轴流式和离心式风机的特征,尽管它看起来更像传统的轴流式风机。将弯曲板形叶片焊接在圆锥形钢轮毂上。通过改变叶轮上游入口外壳中的叶片角度来改变流量。机壳可具有敞开的入口,但更常见的情况是,它具有直角弯曲形状,使电机可以放在管道外部。排泄壳缓慢膨胀,以放慢空气或气体流的速度,并将动能转换为有用的静态压力。本实施例中,如果前掠角度小于1°,则形成离心风机,通过上述描述可知,离心风机,其特点以及工作方式等与轴流风机相差较大,无法实现某些领域轴流风机的效果。本实施例中,压力面m朝向吸力面n的前弯角度为1°-12°。同上,前弯角度过大,则需要补偿的弦长过大,造成本体的过大;过小,则无弯曲,机会形成直叶片。本实施例中,弯掠后,叶片前端朝前,形成多个角度的叶面,进而其工作中,与空气等形成多个角度的力,能够将之前的噪音得到多次分解,进而降低了噪音。比如说,之前的噪音,只能通过一个角度分解,进而和分解力一样的道理,则每个方向的力比较大,当多个角度分解后,与之前整个力相比,每个方向上的力比较小,当有多个相反或者相向方向的力时,力被分解,甚至抵消;噪音也是同理。现有技术中,其主要是从根部开始弯曲,下压;为了满足轴流风机的性能,此时,弯掠的叶片相比于本申请,弯掠面大,需要补偿的弦长较多,则叶片整体质量增加,耗材多,叶片总量增加时,转动中的消耗功率等也较大;同时,实际工作中,叶片主要是前面做工,根部不做工,噪音产生在前端,此时根部弯曲,力分解较早,进而前部产生的噪音还是没有得到分解,降噪效果差;最后,从根部开始弯掠,张力大,风量和风压都被耗损,效率低。同时,现有技术中,弯掠角度过大,使得风量风压被大量耗损,风机效率得到降低。本实施例中,加工设计时,叶片主体1的宽度增加2%-10%,具体地,叶片宽度为从所述叶片主体1的左缘面11延伸至右缘面12,设计时,将叶片主体1的宽度在常规工艺尺寸的基础上加宽2%-10%。实施例2参照附图1所示,作为进一步改进以及提升优化,本实施例中,为了提高降噪的效果,本实施例中,述压力面朝向吸力面的前弯角度为1°-12°;前掠角度为1°-8°。为了避免前弯角度过大时,造成的损失以及后期的弦补,设置前弯角度为1°-12°,此时弯曲角度小,叶片之间安装后,风机使用中,风量风压损失小,弦长补充少。将掠角从最大10°变为8°,首先,与现有技术掠角基本在15°以上相比,掠角变小,弦补偿少,叶片在原来基础上的加宽量少;当在满足轴流风机的性能时,不仅节省更多的材料;而且叶片重量减轻,搬运方便;同时,能够实现降噪的效果。具体地,最佳前掠角度为1°-3°,前弯角度为8°。本实施例中,前弯前掠的起始端相同,同时都是朝向前缘面弯掠,如果弯掠起始点不同,则弯和掠差异大,从叶片外观来看,叶片结构不够美观。本实施例中,叶片宽度相比于现有技术,叶片的宽度加宽2%-10%,优选5%。现有技术中,在根部弯掠,则叶片需要加宽20%,叶片重量以及宽度都增加较大,浪费材料。实施例3参照附图1-3所示,进一步地,由所述前缘面13向后缘面14延伸方向为叶片主体1的长度方向,沿所述长度方向,所述叶片分为7段弧形,从所述前缘面13至所述后缘面14,相邻所述弧形之间的弦长差,呈阶梯状递减。进而7段弧形之间,开始相差较大,后面相差越来越小,直至平稳,使得整个弧形结构的过度从陡至平稳,便于靠近前缘面下压弯掠,实现降噪效果。同时,后面差异小,弯掠起来,比较方便加工,弯掠角度小的情况下,整个结构更加匹配。本实施例中,7段所述弧形中,以与前缘面连接的为第1段弧形,所述弯掠起始点设置于第3段弧形至第4段弧形之间。本技术方案中,弯掠的起始点,设置于中间位置,大概位于叶片长度的40%-50%处之间,且靠近前缘面13设置,一方面,此时曲线切点从仿真角度来说,效果最佳,同时,迎着气流,力的降解好,降噪效果明显;另一方面,靠近前缘面,远离靠近电机的根部,提高做功,降低风压损耗。进一步地,7段所述弧形中,以与前缘面连接的为第1段弧形,从第1段弧形至第7段弧形,所述弧形对应的弦与电机的安装角度逐渐变小,所述安装角度为6°-40°。安装角度,即弧形与叶片中轴线之间的夹角,通过这一夹角的逐渐变小,进而使得弧形对应的切线越来越靠近叶片的中轴线,便于安装。本实施例中,当安装角小于6°时,叶片与平面之间平行或者夹角过小,转动时无风力,起不到风机的送风作用;如果安装角度太大,大于40°,则对于轴流风机,起不到轴流风机的性能。表格1为本实施例中,叶片的性能参数。其中,beta为安装角度。位置/参数半径弦长比率gxgybeta第1段350.0227.3411.297.7010.6434.67第2段458.33209.9110.490.209.8226.45第3段566.67198.009.885.099.2721.33第4段675.00191.009.382.088.9417.80第5段783.33186.508.780.148.7315.17第6段891.67183.008.178.648.5613.11第7段1000181.007.577.788.4711.44本实施例中,通过这样的设置,加快了风机的降噪效果。实施例4进一步地,本实施例中,为了匹配多种安装方式,叶片上的连接头2可以采用梯形结构或者圆柱形结构。设置多种结构的连接头,使得叶片的安装得到进一步扩展,进而应用是,能够匹配不同的安装方式。参照附图4-6所示,本实施例中,连接头2为梯形结构,此时,由于安装时,轮毂为圆弧面,为了适应安装,将所述叶片主体1与连接头2通过扭曲段3连接。当采用梯形结构时,其与轮毂安装中,梯形为直面结构,其与轮毂的弧形安装角度不易调整,即从直面到弧面,安装难,角度难调整;而增加扭曲段,扭曲段上增加弧形段,使得其能够通过弧形段与轮毂方便安装。进一步地,参照附图所示,扭曲段3为多面体结构扭曲5°-40°后形成的扭曲结构,所述多面体结构为圆柱体、四方体、六面体中的一种。采用多面体扭曲,一方面,多面体容易被扭,就像扭麻花一样,方便实现;同时,设定扭曲角度,避免过度扭曲,使得扭曲段强度降低,叶片容易断裂。本实施例中,所述连接头2一体设置于叶片主体端部或所述连接头通过连接件可拆卸连接于所述叶片主体端部。通过多种设置方式,实现了叶片的多种方式生产,同时,可以根据材料,决定其生产方式;采用一体化设置,结构简单,安装方便,但是不易调整角度,叶片或者连接头任一损坏时,整个结构不能用;而采用连接件可拆卸连接,可以叶片与连接头任意匹配,角度方便调整。本实施例中,当连接头2为圆柱形结构时,无需本实施例中的扭曲段3,此时,圆柱形结构的外表面与轮毂便于安装,具体地,圆柱形结构可以为两头圆台结构中间通过圆柱体连接。现有技术中,当匹配梯形的连接头2时,叶片主体1具有安装方便的特点;如果是圆柱形的连接头2,则无需要,具体角度方便调节的特点,但是为了更好的安装,则需要结构复杂的轮毂,因为圆弧连接,容易打滑等。本实施例中,具体地,叶片主体1的后缘面14处的最大厚度是20-40mm。如果太薄,则强度弱,太厚的话,扭曲段3更厚,难以加工。以上显示和描述了本实用新型的基本原理和主要特征和本实用新型的优点。本行业的技术人员应该了解,本实用新型不受上述实施例的限制,上述实施例和说明书中描述的只是说明本实用新型的原理,在不脱离本实用新型精神和范围的前提下,本实用新型还会有各种变化和改进,这些变化和改进都落入要求保护的本实用新型范围内。本实用新型要求保护范围由所附的权利要求书及其等效物界定。当前第1页12