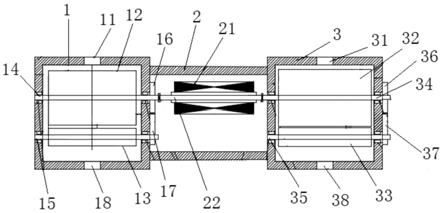
1.本技术涉及真空技术领域,具体而言,涉及一种直排式罗茨泵。
背景技术:2.罗茨真空泵(简称罗茨泵)是一种双转子的容积式真空泵,在泵腔内,两个转子相互垂直地安装在一对平行轴上,由于罗茨泵腔内无摩擦,转子可以高速转动,而且腔室内无润滑油,可实现无油清洁的抽气过程,特别是在1~100pa入口压力范围内具有大抽速,适合于入口压力0.01~100pa下需要大抽速的真空系统中使用,如真空冶炼排气、真空镀膜设备预抽、食品、化工、医药、轻纺等行业真空蒸馏、浓缩、干燥等工艺过程。此外,半导体器件的生产离不开洁净的真空环境,对于半导体晶圆、显示屏及太阳能电池等严苛型应用场景,罗茨泵是首选产品,它能够提供高洁净真空环境的同时,高效的缩短抽空时间。
3.但是,在气体压力较高时,由于罗茨泵转子在高速运转的过程中大量的气体聚集在泵体出口处,造成出口处压力急剧上升,温度升高,高温气体在热传导作用下会使转子发生热膨胀效应,造成主动转子与从动转子之间,转子与腔体之间的间隙变小,进一步加剧了温升效应,最终使得转子之间或者转子与腔体之间的发生磕碰,轻则造成转子损坏,重则直接烧坏电机,对罗茨泵造成不可逆转的损坏。因此,在真空机组中,罗茨泵不能够独立运行,必须有前级泵的配合才能正常工作,在可配罗茨泵的前级泵中,通常采用旋片泵、滑阀泵等油泵,无法实现罗茨泵机组的真正无油运行。虽然,目前市场上在小型罗茨泵上通过多级转子的形式实现了可以在大气压力下直接运行,但是,由于极限压力、特别是加工难度大、成本高等因素的影响,此结构形式在涉及、半导体、化工、冶金等大规模应用的大中型罗茨泵上无法实现应用。
技术实现要素:4.本技术的主要目的在于提供一种直排式罗茨泵,通过一个电机带动在两个不同压缩比的抽空腔体分段压缩抽空气体,采用两级压缩实现罗茨泵在大气压下开始抽气,取消了传统罗茨真空机组中的前级油泵,为大抽速下的洁净真空环境提供了一种新的途径。
5.为了实现上述目的,本技术提供了一种直排式罗茨泵,包括依次连接的第一腔体、第二腔体以及第三腔体,第一腔体、第二腔体以及第三腔体之间设置有密封胶圈,第一腔体的第一出气口通过连接管与第三腔体的第二进气口连通。
6.进一步的,第一腔体还包括第一进气口、第一转子结构以及第一齿轮组,其中:第一进气口设置在第一腔体壳体的顶部;第一齿轮组设置在第一腔体壳体的右侧,包括第一上齿轮和第一下齿轮;第一转子结构设置在第一腔体的内部,包括第一主动转子和第一从动转子,第一主动转子通过第一主动转轴与第一上齿轮连接,第一从动转子通过第一从动转轴与第一下齿轮连接。
7.进一步的,第三腔体还包括第二出气口、第二转子结构以及第二齿轮,其中:第二出气口设置在第三腔体壳体的底部;第二齿轮组设置在第三腔体壳体的右侧,包括第二上
齿轮和第二下齿轮;第二转子结构设置在第三腔体的内部,包括第二主动转子和第二从动转子,第二主动转子通过第二主动转轴与第二上齿轮连接,第二从动转子通过第二从动转轴与第二下齿轮连接。
8.进一步的,第二腔体包括电机以及传动轴,电机设置在传动轴上,传动轴的一端通过联轴器与第一主动转轴连接,另一端通过联轴器与第二主动转轴连接。
9.进一步的,第一转子结构为三叶型结构。
10.进一步的,第二转子结构为双叶型结构。
11.进一步的,第一转子结构与第一腔体壳体的间隙距离小于第二转子结构与第三腔体壳体的间隙距离。
12.进一步的,第一主动转子与第一从动转子之间的间隙距离小于第二主动转子与第二从动转子之间的间隙距离。
13.进一步的,第一腔体内部的压缩比大于第三腔体内部的压缩比。
14.进一步的,第一转子结构和第二转子结构均采用铝制铸造结构。
15.本发明提供的一种直排式罗茨泵,具有以下有益效果:
16.本技术通过一个电机带动在两个不同压缩比的抽空腔体分段压缩抽空气体,采用两级压缩实现了罗茨泵在大气压下开始抽气,解决了常规罗茨泵在运行过程中须配置旋片泵、滑阀泵等前级油泵的问题,减少了对真空环境的油气污染,真正实现了罗茨泵机组的无油洁净空间,为罗茨泵机组、特别是大抽速罗茨泵机组提供了洁净真空的环境。
附图说明
17.构成本技术的一部分的附图用来提供对本技术的进一步理解,使得本技术的其它特征、目的和优点变得更明显。本技术的示意性实施例附图及其说明用于解释本技术,并不构成对本技术的不当限定。在附图中:
18.图1是根据本技术实施例提供的一种直排式罗茨泵的内部结构示意图;
19.图2是根据本技术实施例提供的一种直排式罗茨泵的气路框架示意图;
20.图3是根据本技术实施例提供的一种直排式罗茨泵的第一转子结构的示意图;
21.图4是根据本技术实施例提供的一种直排式罗茨泵的第二转子结构的示意图;
22.图中:1-第一腔体、11-第一进气口、12-第一主动转子、13-第一从动转子、14-第一主动转轴、15-第一从动转轴、16-第一上齿轮、17-第一下齿轮、18-第一出气口、2-第二腔体、21-电机、22-传动轴、3-第三腔体、31-第二进气口、32-第二主动转子、33-第二从动转子、34-第二主动转轴、35-第二从动转轴、36-第二上齿轮、37-第二下齿轮、38-第二出气口、4-连接管。
具体实施方式
23.为了使本技术领域的人员更好地理解本技术方案,下面将结合本技术实施例中的附图,对本技术实施例中的技术方案进行清楚、完整地描述,显然,所描述的实施例仅仅是本技术一部分的实施例,而不是全部的实施例。基于本技术中的实施例,本领域普通技术人员在没有做出创造性劳动前提下所获得的所有其他实施例,都应当属于本技术保护的范围。
24.如图1-2所示,本技术提供了一种直排式罗茨泵,包括依次连接的第一腔体1、第二腔体2以及第三腔体3,第一腔体1、第二腔体2以及第三腔体3之间设置有密封胶圈,第一腔体1的第一出气口18通过连接管4与第三腔体3的第二进气口31连通。
25.具体的,本技术实施例提供的直排式罗茨泵能够作为独立的抽空机组或者抽空机组的前级泵使用,采用两级压缩的方式,实现了罗茨泵在大气压下直接运行抽气,解决了常规罗茨泵在运行过程中须配置旋片泵、滑阀泵等前级油泵的问题。本技术实施例包括三个腔体,三个腔体为分体式结构,三个腔体之间采用密封胶圈进行密封,其中第二腔体2分别与第一腔体1和第三腔体3连接,主要用于对第一腔体1和第三腔体3内部的转子结构进行驱动,从而实现气体压缩,第一腔体1直接连接于真空腔体或真空管道,气体在第一腔体1内进行首次压缩,然后通过第一出气口18进入连接管4内,连接管4可以采用波纹软管,气体在连接管4内流动后通过第二进气口31进入到第三腔体3,在第三腔体3内进行二次压缩后排入到外界,完成整个抽气过程,在抽气的过程中,通过在不同压力区间设计不同压缩比的抽空腔体,解决了常规罗茨泵在较大压缩比下因热膨胀造成转子与转子碰撞、转子与腔体碰撞的问题,实现了罗茨泵在大气压下的直接抽空。
26.进一步的,第一腔体1还包括第一进气口11、第一转子结构以及第一齿轮组,其中:第一进气口11设置在第一腔体1壳体的顶部;第一齿轮组设置在第一腔体1壳体的右侧,包括第一上齿轮16和第一下齿轮17;第一转子结构设置在第一腔体1的内部,包括第一主动转子12和第一从动转子13,第一主动转子12通过第一主动转轴14与第一上齿轮16连接,第一从动转子13通过第一从动转轴15与第一下齿轮17连接。第一腔体1主要用于气体的进入以及第一次压缩,气体通过壳体顶部的第一进气口11进入到第一腔体1内部,然后通过电机21的旋转运动,第一主动转轴14带动第一主动转子12以及第一上齿轮16转动,在齿轮的传动下,第一下齿轮17也会同步进行转动,并且通过第一从动转轴15带动第一从动转子13转动,这样气体在第一主动转子12和第一从动转子13同步反向旋转的作用下,实现了第一次压缩,压缩后的气体通过壳体底部的第一出气口18进入到连接管4内。
27.进一步的,第三腔体3还包括第二出气口38、第二转子结构以及第二齿轮,其中:第二出气口38设置在第三腔体3壳体的底部;第二齿轮组设置在第三腔体3壳体的右侧,包括第二上齿轮36和第二下齿轮37;第二转子结构设置在第三腔体3的内部,包括第二主动转子32和第二从动转子33,第二主动转子32通过第二主动转轴34与第二上齿轮36连接,第二从动转子33通过第二从动转轴35与第二下齿轮37连接。第三腔体3主要用于气体的第二次压缩以及排出,从第一腔体1内排出的气体进入到连接管4内,然后通过壳体顶部的第二进气口31进入到第三腔体3内部,然后通过电机21的旋转运动,第二主动转轴34带动第二主动转子32以及第二上齿轮36转动,在齿轮的传动下,第二下齿轮37也会同步进行转动,并且通过第二从动转轴35带动第二从动转子33转动,这样气体在第二主动转子32和第二从动转子33的作用下,实现了第二次压缩,压缩后的气体通过壳体底部的第二出气口38排出到外界,完成整个抽气过程。
28.进一步的,第二腔体2包括电机21以及传动轴22,电机21设置在传动轴22上,传动轴22的一端通过联轴器与第一主动转轴14连接,另一端通过联轴器与第二主动转轴34连接。电机21设置在第二腔体2内部,主要用于驱动两侧腔体内部转子结构进行转动,电机21通过较长的传动轴22分别与第一主动转轴14和第二主动转轴34连接,抽气时,开启电机21,
在电机21及传动轴22的驱动下,第一主动转轴14和第二主动转轴34会同时转动,从而带动第一主动转子12和第二主动转子32进行同步转动,并且在齿轮组的传动下,第一从动转子13和第二从动转子33也会同时进行转动,从而在第一腔体1内部和第三腔体3内部形成两个压缩比不同的抽空腔体,从而实现对内部气体的压缩。
29.进一步的,如图3所示,第一转子结构为三叶型结构。
30.进一步的,如图4所示,第二转子结构为双叶型结构。
31.具体的,第一转子结构采用三叶型,第二转子结构采用双叶型,主要为了使第一腔体1与第三腔体3内部的压力和压缩比不同,采用三叶型结构的转子,能够减轻转子重量,降低电机21功率,使得第一腔体1具有较小的容积利用率和返流,采用双叶型结构的转子,使得第三腔体3具有较大的容积利用率和较大的抽速,使得第三腔体3能够快速及时的抽取第一腔体1内的压缩气体,并且实现较低的极限压力。
32.进一步的,第一转子结构与第一腔体1壳体的间隙距离小于第二转子结构与第三腔体3壳体的间隙距离。
33.进一步的,第一主动转子12与第一从动转子13之间的间隙距离小于第二主动转子32与第二从动转子33之间的间隙距离。
34.进一步的,第一腔体1内部的压缩比大于第三腔体3内部的压缩比。
35.具体的,第一转子结构与第一腔体1壳体的间隙距离小于第二转子结构与第三腔体3壳体的间隙距离,第一主动转子12与第一从动转子13之间的间隙距离小于第二主动转子32与第二从动转子33之间的间隙距离,从而使得第一腔体1内部的压缩比大于第三腔体3内部的压缩比,第一腔体1内的间隙较小,压缩比大,返流小,可实现低压下的气体抽空,第三腔体3内的间隙较大,压缩比小,可适应较大的机械应力和热应力,实现在大气压下的直接抽气。
36.进一步的,第一转子结构和第二转子结构均采用铝制铸造结构。采用铝制铸造结构主要为了减少转子的重量,降低电机21的功耗,第一转子结构和第二转子结构的叶轮为空心结构,叶轮上均设置有圆柱孔,第一转子结构和第二转子结构与转轴之间的连接方式均为分体式结构,转轴通过热胀法插入到转子结构内。此外,第一主动转轴14、第二主动转轴34、第一从动转轴15、第二从动转轴35以及传动轴22均采用高强度材料45crmo,可以增加转轴在高转速下的强度。
37.以上所述仅为本技术的优选实施例而已,并不用于限制本技术,对于本领域的技术人员来说,本技术可以有各种更改和变化。凡在本技术的精神和原则之内,所作的任何修改、等同替换、改进等,均应包含在本技术的保护范围之内。