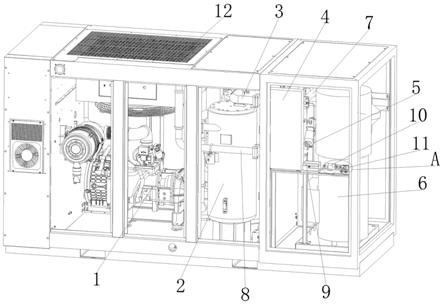
1.本发明涉及压缩空气净化的技术领域,更确切地说涉及一种催化无油压缩系统的安全供气方法。
背景技术:2.压缩空气作为一种廉价的动力源,被广泛应用于各行各业,如设备驱动、物料输送、干燥、吹料、吹扫、气动仪表元件、自动控制等。制备压缩空气的压缩机功率大,工作时对润滑和散热的要求都很高,相比干式压缩机或水润滑压缩机等无油压缩机,使用润滑油的压缩机能获得更好的润滑效果,散热效率更高,成本也更低,但是产出的压缩空气中会不可避免地含有油类杂质。而在电子、食品、医药、纺织等特殊行业中,由于油类杂质会对产品品质、生产仪器、环境甚至操作人员的健康产生危害,所以这些行业对压缩空气的品质要求较高,有些甚至明确要求采用无油压缩空气。因此,现有技术通常会在油润滑压缩机的排气端配置催化净化器来构建无油压缩系统,通过将压缩空气通入催化净化器中,使压缩空气中的油类杂质被催化分解成二氧化碳和水,从而使压缩空气得到净化。
3.上述净化后的压缩空气的含油量是否符合行业的生产用气要求,还需要检测才能确定。由于压缩空气本身气压高,在催化净化器内又被加热到180-200℃的高温,且油类杂质分解后又产出了水,要采用现有技术的含油量检测设备来检测净化后的压缩空气的含油量,就必须要先对净化后的压缩空气进行减压、降温、除水处理,而且现有技术的含油量检测设备的检测速率也没有高压气体的流速快,往往是检测结果还未出来,被检测的压缩空气就已经进入用户的用气设备中了,如此就使得含油量检测设备的检测数据出现滞后的弊端,不能实时反映从催化净化器中排出的压缩空气的含油量,也无法实时反映输入用户的用气设备中的压缩空气的含油量,更不能在压缩空气输入用户的用气设备之前就提早反馈出其含油量。如果压缩机出现密封件失效而导致润滑油泄漏跑油,含油量检测设备会由于这个弊端而无法第一时间发现产出的压缩空气中含油量超标,一旦含油量超标的压缩空气输入用户的用气设备中,就会给用户的生产造成经济损失。另外,用户用气时需要连续不断地向其供给压缩气体,对于从催化净化器中实时排出的压缩空气,含油量检测设备在没有检测出结果之前,既不能把未知含油量的压缩气体供给用户,也无法中断对用户的用气设备供气,这个问题业内一直未能解决。
技术实现要素:4.本发明要解决的技术问题是,提供一种催化无油压缩系统的安全供气方法,既能对催化净化器排出的压缩空气的含油量进行实时检测,又能避免将含油量未知的压缩气体输入用户的用气设备内,还能连续不断地向用气设备供给压缩气体,且能确保输入用气设备中的压缩气体的含油量均不超标,避免含油量超标的压缩空气给用户造成损失,保障用户用气品质,确保用户用气安全。
5.本发明的技术解决方案是,提供一种催化无油压缩系统的安全供气方法,使用压
缩机压缩气体,使用催化净化器催化分解压缩气体中的油类杂质,使用含油量检测设备检测催化净化器排出的压缩气体的含油量,使用缓冲设备对催化净化器排出的压缩气体进行缓冲减速并对外排出,使用显示屏显示含油量检测设备的检测结果即压缩气体的含油量,具体实施步骤如下:1)确定含油量检测设备的检测时间t1,即从压缩气体从催化净化器排出到显示屏显示出检测结果的时长;2)根据含油量检测设备的检测时间t1,设定压缩气体需要在缓冲设备内缓冲的时间t2,使t2》t1;3)根据压缩气体需要在缓冲设备内缓冲的时间t2,设计并确定缓冲设备的结构;4)将含油量检测设备和缓冲设备均安装在催化净化器的排气管上,使压缩气体先经过含油量检测设备检测再进入缓冲设备内缓冲;5)实时监控显示屏的显示结果,若显示压缩气体的含油量不超标,则将缓冲设备的排气端与用气设备连接,使催化无油压缩系统对用气设备供气;若显示压缩气体的含油量超标,则切断缓冲设备的排气端与用气设备的连接,使催化无油压缩系统停止对用气设备供气。
6.与现有技术相比,本发明的催化无油压缩系统有以下优点:确定含油量检测设备的检测时间t1和压缩气体需要在缓冲设备内缓冲的时间t2,使t2》t1,在被检测的压缩气体的含油量检测结果出来之前,被检测的压缩气体会一直在缓冲设备中缓冲减速流动,不会直接输入用户的用气设备中,既能对催化净化器排出的压缩空气的含油量进行实时检测,又能避免将含油量未知的压缩气体输入用户的用气设备内;在确保压缩气体的含油量不超标的前提下,将缓冲设备的排气端与用气设备连接,使催化无油压缩系统能连续不断地向用气设备供给压缩气体,保障用户用气品质;在压缩气体的含油量超标时,切断缓冲设备的排气端与用气设备的连接,使催化无油压缩系统停止对用气设备供气,避免含油量超标的压缩空气给用户造成损失,确保用户用气安全。
7.优选的,步骤1)中在催化净化器的排气端或者含油量检测设备的进气端设置第一气压传感器,初始上电后,压缩机启动,第一气压传感器检测到压缩机的额定排气压力的时间记为t01,显示屏的显示结果变化的时间记为t02,t1=t02-t01。采用此方式,能较准确地确定含油量检测设备的检测时间t1,为确定压缩气体需要在缓冲设备内缓冲的时间t2以及设计对应的缓冲设备的结构作依据。
8.优选的,步骤3)中,在缓冲设备的进气端和排气端分别设置第二气压传感器和第三气压传感器,初始上电后,压缩机启动,第二气压传感器检测到压缩机的额定排气压力的时间记为t03,第三气压传感器检测到压缩机的额定排气压力的时间记为t04,t2=t04-t03,设计并验证缓冲设备的结构能使t2》t1。采用此方式,能较准确地确定压缩气体需要在缓冲设备内缓冲的时间t2,能据此设计并验证对应的缓冲设备的结构,确保t2》t1。
9.优选的,缓冲设备上设置有缓冲排气管,缓冲设备通过缓冲排气管对外排出压缩气体,缓冲排气管上设置有供气管和对空排气管,供气管用于对接用气设备并为用气设备供气,对空排气管用于对空排放压缩气体;当初始上电及步骤5)中的显示屏显示压缩气体的含油量超标时,供气管封闭,对空排气管打开;当步骤5)中的显示屏显示压缩气体的含油量不超标时,供气管打开,对空排气管封闭。采用此方式,在压缩气体的含油量不超标时,供
气管打开,对空排气管封闭,使催化无油压缩系统对用气设备供气;在压缩气体的含油量超标时,供气管封闭,使催化无油压缩系统停止对用气设备供气,对空排气管打开,使催化无油压缩系统产出的压缩气体能始终对外排出,避免排气不畅危及整机安全。
10.优选的,还使用警报器,步骤5)中,当显示屏显示压缩气体的含油量超标时,警报器发出声音和\或灯光警报。采用此方式,不用工作人员实时盯着显示屏,在压缩气体的含油量超标时,警报器发出警报能提醒工作人员及时切断对用气设备的供气,保障用户用气安全,并提醒工作人员及时采取措施排查故障,保障整机安全。
11.优选的,压缩机采用喷油螺杆压缩机,喷油螺杆压缩机排出的压缩气体依次通过油气分离器、气液分离器之后再通入催化净化器中,油气分离器用于分离压缩气体中的油液,气液分离器用于分离压缩气体中的液态水。采用此方式,喷油螺杆压缩机润滑效果好、散热效率高、成本低,产出的压缩空气经油气分离器去除油液、经气液分离器去除液态水后,再输入催化净化器中,能减小催化净化器内催化剂的负载,延长催化净化器的使用寿命,也有利于保障用户用气的品质。
12.优选的,从气液分离器排出的压缩气体先通过热交换器再进入催化净化器,从催化净化器中排出的压缩气体先通过热交换器再通过缓冲设备,热交换器对催化净化器排出的压缩气体进行热回收,并对气液分离器排出的压缩气体进行预热。采用此方式,可以对催化净化器的排气进行余热回收,现有技术中,压缩气体在催化净化器内要被加热到180-200℃的高温后,油类物质才能被催化分解,采用热交换器使催化净化器排出的压缩空气对气液分离器排出的压缩空气进行预热,使催化净化器减轻对压缩气体加热的负担,可以在节能的同时提高催化净化器的工作效率,保证供气效率。
13.优选的,所述的热交换器即为缓冲设备,热交换器内设置有两条蜿蜒曲折的u型换热管道,两条u型换热管道交错设置,从气液分离器排出的压缩气体通过一条u型换热管道进入催化净化器中,从催化净化器中排出的压缩气体通过另一条u型换热管道后对外排出,压缩气体在u型换热管道内被缓冲减速。采用此方式,通过热交换器内蜿蜒曲折的u型换热管道对压缩气体换热并缓冲减速,可以在节能的同时给含油量检测设备的检测争取时间,避免被检测的压缩气体在其含油量检测结果出来之前就被输入用户的用气设备中,保证供气品质;将气体换热与缓冲的功能集成在热交换器上,也有利于减小整机的体积。
14.优选的,催化净化器的排气管上设置有细长的检测支管,一部分从催化净化器中排出的压缩气体进入检测支管内,再依次通过降温装置降温、除水装置除水和减压装置减压后进入含油量检测设备检测。采用此方式,催化净化器排出的压缩气体中,仅有一小部分会从细长的检测支管进入含油量检测设备检测,不会影响催化无油压缩系统的供气气量;被检测的一小部分压缩气体在进入含油量检测设备检测之前,先依次通过降温装置降温、除水装置除水和减压装置减压后,有利于保证检测的准确率。
15.优选的,减压装置设置在含油量检测设备上,含油量检测设备还包括含油量检测芯和排气单向阀,减压装置包括减压阀体、压力传感器和电磁阀,减压阀体用于对降温除水后的压缩气体减压,压力传感器用于检测经减压阀体减压后的气体气压以及在气体气压合格时打开电磁阀,电磁阀用于将减压后的气体导入含油量检测芯内,含油量检测芯用于检测气体的含油量,含油量检测芯与排气单向阀连通,经含油量检测芯检测后的气体通过排气单向阀对空排放。采用此方式,含油量检测设备集成有减压、检测、排气功能,体积小,安
装方便,减压阀体、压力传感器和电磁阀能保证压缩气体得到有效的减压,避免压缩气体气压过高、流速过快而影响检测效果,保证供气安全,排气单向阀能使经过检测后气体对外排出,还能避免外界的空气进入含油量检测芯中影响检测结果。
附图说明
16.图1为本发明中采用的催化无油压缩系统的结构示意图。
17.图2为图1中a区域的结构放大图。
18.如图中所示:1、喷油螺杆压缩机,2、气液分离器,3、气液分离排气管,4、间壁式热交换器,5、催化进气管,6、催化净化器,7、催化排气管,8、热交换排气管,9、电子冷却器,10、过滤吸附罐,11、含油量检测设备,11-1、减压阀体,11-2、压力传感器,11-3、电磁阀,11-4、含油量检测芯,11-5、排气单向阀,12、散热器。
具体实施方式
19.为了更好得理解本技术,将参考附图对本技术的各个方面做出更详细的说明。应理解,这些详细说明只是对本技术的示例性实施方式的描述,而非以任何方式限制本技术的范围。在说明书全文中,相同的附图标号指代相同的元件。
20.在附图中,为了便于说明,已稍微夸大了物体的厚度、尺寸和形状。附图仅为示例而非严格按比例绘制。
21.还应理解的是,用语“包括”、“具有”、“包含”、“包含有”,当在本说明书中使用时表示存在所述的特征、整体、步骤、操作、元件和/或部件,但不排除存在或附加有一个或多个其他特征、整体、步骤、操作、元件、部件和/或它们的组合。此外,当诸如
“…
至少一个”的表述出现在所列特征的列表之后时,修饰整个所列特征,而不是修改列表中的单独元件。
22.实施例1:本发明的催化无油压缩系统的安全供气方法,使用的催化无油压缩系统如图1中所示,包括压缩机、油气分离器(未图示)、气液分离器2、催化净化器6、热交换器、含油量检测设备11、电子冷却器9、过滤吸附罐10、散热器12和显示屏(未图示),压缩机采用喷油螺杆压缩机1,散热器12安装在喷油螺杆压缩机1的上方,喷油螺杆压缩机1在工作时压缩空气并采用润滑油润滑,散热器12则及时对喷油螺杆压缩机1进行散热降温。热交换器采用间壁式热交换器4,间壁式热交换器4内设置有两条蜿蜒曲折的u型换热管道,两条u型换热管道交错设置。喷油螺杆压缩机1的排气口与油气分离器的进气口连通,油气分离器的排气口与气液分离器2的进气口连通,气液分离器的排气口设置有气液分离排气管3,催化净化器6的进气口设置有催化进气管5,气液分离排气管3和催化进气管5分别与间壁式热交换器4内的同一条u型换热管道的两端连通,催化净化器6的排气管是催化排气管7,催化排气管7与间壁式热交换器4内的另一条u型换热管道的一端连通,间壁式热交换器4内的另一条u型换热管道的另一端设置有热交换排气管8,热交换排气管8经过散热器12与外界连通。催化排气管7上设置有细长的不锈钢材质的检测支管,检测支管的管壁上设置有作为降温装置的电子冷却器9,检测支管的出气口与作为除水装置的过滤吸附罐10的进气口连通,过滤吸附罐10的出气口与含油量检测设备11连通,含油量检测设备11的检测结果通过显示屏实时显示。
23.如图2中所示,含油量检测设备11上设置有减压装置、含油量检测芯11-4和排气单
向阀11-5,减压装置包括依次连接的减压阀体11-1、压力传感器11-2、电磁阀11-3,过滤吸附罐10的出气口与减压阀体11-1连接,减压阀体11-1对过滤吸附罐10内排出的压缩气体减压,并导入压力传感器11-2内,压力传感器11-2检测由减压阀体11-1导入的气体气压,并在气体气压合格后打开电磁阀11-3,电磁阀11-3打开后将减压气体导入含油量检测芯11-4,由含油量检测芯11-4检测减压气体的含油量,导入含油量检测芯11-4的减压气体在检测后经由排气单向阀11-5对外排放。
24.本发明的催化无油压缩系统在配置间壁式热交换器4的时候,首先要实施以下步骤:1)确定含油量检测设备11的检测时间t1,在催化排气管7上细长的不锈钢材质的检测支管的入口设置第一气压传感器,初始上电后,压缩机启动,第一气压传感器检测到喷油螺杆压缩机1的额定排气压力的时间记为t01,显示屏的显示结果变化的时间记为t02,t1=t02-t01,即从压缩气体从催化排气管7排出到显示屏显示出检测结果的时长;2)根据含油量检测设备11的检测时间t1,设定压缩气体需要在间壁式热交换器4内缓冲的时间t2,使t2》t1;3)间壁式热交换器4内与催化排气管7和热交换排气管8均连接的另一条u型换热管道的两端,分别设置第二气压传感器和第三气压传感器,初始上电后,喷油螺杆压缩机1启动,第二气压传感器检测到喷油螺杆压缩机1的额定排气压力的时间记为t03,第三气压传感器检测到喷油螺杆压缩机1的额定排气压力的时间记为t04,t2=t04-t03,验证该条u型换热管道是否能使t2》t1,根据压缩气体需要在间壁式热交换器4内缓冲的时间t2,调整并确定该条u型换热管道长度和结构;4)将含油量检测设备11与检测支管连接,将催化排气管7和热交换排气管8分别连接在一条u型换热管道的两端,使压缩气体从催化排气管7排出后先经过含油量检测设备11检测再进入间壁式热交换器4内缓冲。
25.启动本发明中的催化无油压缩系统,由喷油螺杆压缩机1对常温常压的空气进行压缩并排出,压缩空气经油气分离器分离出油液后进入气液分离器2中,由气液分离器2进行二次旋分分离除去液态水,再由气液分离排气管3导入间壁式热交换器4内的一条u型换热管道内,此时的压缩空气大约80℃左右,然后从间壁式热交换器4内流出并经由催化进气管5进入催化净化器6内,催化净化器6外包裹有保温棉,催化净化器6内设置有催化剂,压缩空气在催化净化器6内被加热到180-200℃,然后在催化剂的作用下进行复杂的催化氧化反应,将c6+含碳化合物分解成二氧化碳和水,使压缩气体得到净化;净化后的压缩气体一小部分经由检测支管通过电子冷却器9降温,再进入过滤吸附罐10内除水和固态杂质,最后进入含油量检测设备11检测其含油量,而净化后的压缩气体的绝大部分则经由催化排气管7导入间壁式热交换器4内的另一条u型换热管道内,再由热交换排气管8经散热器12冷却排水后对外排出。此过程中,净化后的压缩气体会与净化前的压缩气体在间壁式热交换器4内进行间壁热传导,回收净化后的压缩气体的热量,并对即将进入催化净化器6内的压缩气体进行预热,节能效果好,也使催化净化器6内的催化反应更有效率,而且间壁式热交换器4中的u型换热管道还能对净化后的压缩气体进行缓冲减速,将净化后的压缩气体延迟对外排出,即热交换排气管8即缓冲排气管,在被检测的压缩气体的含油量检测结果出来之前,该部分压缩气体都不会被输入用户的用气设备中。
26.实时监控显示屏的显示结果,若显示压缩气体的含油量不超标,则将热交换排气管8与用气设备连接,使催化无油压缩系统对用气设备供气;若显示压缩气体的含油量超标,则切断热交换排气管8与用气设备的连接,使催化无油压缩系统停止对用气设备供气。
27.本发明的催化无油压缩系统的安全供气方法之所以要对净化后的压缩气体先进行缓冲减速再排出,是由于含油量检测设备11的检测速率没有压缩气体的流速快,为了确保用户用气安全,在压缩气体的含油量检测结果出来之前,该部分含油量不明的压缩气体都不允许被输入用户的用气设备中。举例说明,压缩气体a从催化净化器6内排出后,压缩气体a中的一小部分气体进入含油量检测设备11中被检测含油量,压缩气体a中的绝大部分气体则进入作为缓冲设备的间壁式热交换器4内缓冲减速,在检测结果显示在显示屏上之前的这段时间内,进入间壁式热交换器4内的压缩气体a一直都未从间壁式热交换器4内流出,直至显示屏上显示出压缩气体a的含油量符合用户用气标准的数值之后,压缩气体a才从热交换排气管8排出并对外输入到用户的用气设备中,有效保障了用户用气品质,在催化无油压缩系统整机运行正常的情况下,压缩气体的含油量不超标,本发明的催化无油压缩系统可以持续不间断的对用户的用气设备供气,保障用户的用气。一旦显示屏上显示出压缩气体a的含油量超标,则立即切断热交换排气管8对用户的用气设备供气,首先确保用户用气安全,然后采取停机检查的措施,排查是喷油螺杆压缩机1跑油还是催化净化器6故障,保护整机安全。
28.实施例2:本实施例中的催化无油压缩系统的安全供气方法与实施例1中的区别在于,本实施例中采用的催化无油压缩系统中,热交换排气管8上设置有供气管和对空排气管,供气管用于对接用气设备并为用气设备供气,对空排气管用于对空排放压缩气体,供气管和对空排气管上均设置有阀门。当初始上电及显示屏显示压缩气体的含油量超标时,供气管的阀门封闭,对空排气管的阀门打开,使产出的压缩气体通过对空排气管对外排出,避免排气不畅危及整机安全;当显示屏显示压缩气体的含油量不超标时,供气管的阀门打开,对空排气管的阀门封闭,通过供气管持续不间断的对用户的用气设备供气,保障用户的用气。
29.供气管和对空排气管上的阀门均可以采用电控设备自动控制,由电控设备实时采集含油量检测设备11关于压缩气体含油量的检测结果,并根据压缩气体含油量的检测结果自动控制供气管阀门和对空排气管阀门的打开或者关闭,如此,本实施例中采用的催化无油压缩系统可以实现自动化运行,不需要工作人员值守。另外,本实施例中采用的催化无油压缩系统中还可以设置声光警报器,由电控设备根据压缩气体含油量的实时检测结果自动控制声光警报器是否发出警报,当压缩气体含油量的实时检测结果超标时,电控设备控制声光警报器发出声音和灯光警报,及时提醒工作人员采取停机检查的措施,排查是喷油螺杆压缩机1跑油还是催化净化器6故障,保护整机安全。
30.以上仅为本发明的具体实施例,并非用来限定本发明的实施范围;如果不脱离本发明的精神和范围,对本发明进行修改或者等同替换,均应涵盖在本发明权利要求的保护范围当中。