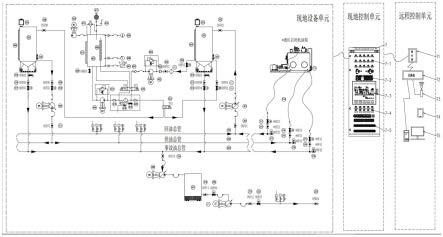
1.本发明涉及水电站运行技术领域,尤其涉及一种水电站液压启闭机液压油品质在线保障系统及其控制方法。
背景技术:2.在水利系统工程中,尤其是水电站,为保证发电厂房设备安全运行,在其引水发电系统的进水口部位设置有事故快速闸门,当机组发生飞逸时,能在动水中快速截断水流以便处理或遏止水道下游发生水淹厂房等重大事故,从而保障电站厂房及设备的安全运行。为实现事故快速闸门能在短时间内快速闭门,目前均采用液压启闭机结构形式对事故快速闸门进行启闭控制,所以事故快速闸门的安全稳定运行直接关系到发电厂及电站的安全。
3.同时,为保障水电站大坝安全运行,大坝本体上会设置一定数量的泄洪孔洞,平时采用工作弧门挡水,当发生来水较大时,则需要开启工作弧门进行紧急泄洪处理,确保电站库区水位控制在安全高度,防止漫坝事故发生;同样,目前泄洪工作弧门均采用液压启闭机结构形式对工作弧门进行启闭控制,由此可见,液压启闭机的安全稳定运行直接关系到发电厂及电站的安全运行,而液压启闭机运行的关键介质就是液压油,如果液压油品质不佳,会使液压启闭机中液压系统执行机构的阀芯发生拒动现象,从而影响应急设备和泄洪设备的正常运行,使设备不能在关键时刻发挥该有的保障功能,对电站安全运行构成重大危险,所以控制好现场液压启闭机油液品质是保障液压启闭机安全运行的关键因素。
4.对于现场运行的液压启闭设备,影响液压油品质的主要因子是油液颗粒度和水分,现有的控制油液品质的主要手段,是在发电机组每年一次机组检修时抽取油样送人工检测,如检查出颗粒度和水分超标后,再对油液进行过滤处理。
5.现有这种方式存在以下缺点:
6.1.一年一次的液压油品质检测,不能及时发现油液变差迹象。
7.2.如果检测发现油液品质不佳,改善油液品质所用时间较长。如果是常规的颗粒度和水封超标,则需要搬运滤油设备至需要被处理的油液设备部位,借助设备油箱充当容器对油液进行循环过滤处理,期间定期将油样送人工检测,直到油液检测结果合格为止。如果检测发现油液变质,则需要将不合格的油液抽排出液压启闭机油箱外部,并采用临时的存油设备将其储存,然后再清理油箱及液压系统各个执行机构,清理完成后,再将新油液(一般颗粒度会超标)注入油箱中,注油完成后再借助油箱充当容器对油液进行循环过滤处理,期间定期将油样送人工检测,直到油液检测结果合格为止。上述两种处理方式,对应急设备来说,停运时间较长,存在一定的安全隐患风险。
8.3.现有设备不具备紧急补油功能。如果发生外部泄漏,油箱内的油液不能满足设备运行需求液位,则导致液压启闭机系统在极端情况下无法工作。
技术实现要素:9.针对现有技术中所存在的不足,本发明提供了一种水电站液压启闭机液压油品质
在线保障系统,该系统能实时监测设备油液品质状态,为管理人员维护油液提供决策数据支持,能对油液中的颗粒和水分进行过滤处理,从而提升液压油品质,能将处理好的液压油,快速的替换至运行设备中,能快速补充设备油箱油液,能快速将事故油液进行排油,从而保障了液压启闭机安全运行。
10.为了解决上述技术问题,本发明采用的技术方案是:
11.水电站液压启闭机液压油品质在线保障系统,它包括回油总管、供油总管和事故油总管,回油总管、供油总管和事故油总管均通过压力软管连通液压启闭机的油箱,事故油总管与事故油池连通,且事故油总管与事故油池之间的管路上连接事故油泵;它还包括:与回油总管连通的回油系统,回油系统包括回油泵和回油罐,回油泵安装在回油罐与回油总管之间;与供油总管连通的供油系统,供油系统包括供油泵和净油罐,供油泵安装在所述净油罐和供油总管之间;以及连接在回油系统与供油系统之间的滤油系统。
12.优选的方案中,所述滤油系统包括水气过滤单元和/或颗粒过滤单元,其中水气过滤单元包括连接在回油罐后端的真空容器和安装在真空容器顶部的真空泵,真空容器与回油罐之间连接吸油泵,真空容器内设置加热器,真空容器顶部连接油雾分离器和空气滤清器,真空容器顶部还连接安全阀;颗粒过滤单元包括连接在吸油泵后端的排放泵和连接在排放泵后端的颗粒过滤器,颗粒过滤器的进口和出口处均连接一单向阀。
13.优选的方案中,滤油系统包括颗粒过滤单元和水气过滤单元,吸油泵的出口连接三位五通换向阀的进口,水气过滤系统和颗粒过滤单元的进口和出口分别连接三位五通换向阀剩余四个端口,以使三位五通换向阀处于三种阀位时,分别实现水气过滤系统单独运行、颗粒过滤单元单独运行、水气过滤系统和颗粒过滤单元同时运行;颗粒过滤单元的后端通过两位三通换向阀分别与净油罐和回油罐连通。
14.优选的方案中,回油总管、供油总管和事故油总管上并列的连通多台液压启闭机的油箱,且回油总管、供油总管和事故油总管与每个液压启闭机的油箱之间的管路上均连接一常开状态的手动球阀和常闭状态的电动球阀。
15.优选的方案中,回油罐、净油罐和真空容器的顶部均连接空气滤清器,真空容器顶部还连接油雾分离器。
16.优选的方案中,净油罐底部与事故油总管连通,且净油罐与所述事故油总管之间的管路上连接常闭状态的电动球阀和常开状态的手动球阀,事故油总管连通事故油池,事故油池与事故油总管之间连接事故油泵,事故油池后端连接放空泵。
17.优选的方案中,还包括设置在液压启闭机的油箱下部的检测装置,检测装置包括温度传感器、液位传感器、水分传感器和污染度传感器之一或组合。
18.优选的方案中,还包括现地控制单元,现地控制单元包括现地控制柜,现地控制柜内安装电控系统和plc控制系统,plc控制系统用于包括控制回油泵、吸油泵、真空泵、供油泵、事故油泵、排放泵、放空泵以及电动球阀动作,现地控制柜上还设置运行状态指示灯、显示屏和控制按钮。
19.优选的方案中,还包括远程控制单元,远程控制单元包括服务器和交换机,还包括与交换机连接的计算机终端和无线ap,以及与无线ap通讯的移动查询终端。
20.本发明还提供了一种水电站液压启闭机液压油品质在线保障系统的控制方法,包括以下步骤:
21.1)设定液压启闭机油液的水分、温度、液位和污染度目标值,检测装置对液压启闭机邮箱内的油液水分、温度、液位和污染度进行检测;
22.2)将检测结果与目标值的对比,油液不合格且设备处于检修状态,则系统进行回油操作,将液压启闭机油箱内油液全部抽取进入回油罐后,启动对液压启闭机油箱运行供油,将净油罐内合格的液压油供输至液压启闭机油箱,待检测装置检测到液压启闭机油箱油液液位达标后停止供油运行;
23.3)根据检测结果对抽回回油罐内的油液进行过滤操作;
24.4)当检测结果为油液颗粒度超标时,启动颗粒过滤单元单独运行:控制沿程电动球阀和吸油泵动作,且三位五通阀动作使经吸油泵流入的油液直接流入颗粒过滤器完成颗粒过滤,并回流进入回油罐,直至回油罐底部的检测装置检测达标后停止运行;
25.5)当检测结果为油液水分或气体超标时,启动水气过滤单元单独运行:控制沿程电动球阀、吸油泵和真空泵动作,且三位五通阀动作使经吸油泵流入的油液直接流入真空罐内完成水分和气体过滤,并回流进入回油罐,直至回油罐底部的检测装置检测达标后停止运行;
26.6)当检测结果为油液颗粒度和水分或气体同时超标时,启动综合滤油运行:控制沿程电动球阀、吸油泵和排放泵动作,且三位五通阀动作使经吸油泵流入的油液先流入真空罐内完成水分和气体过滤,再经排放泵流入颗粒过滤器完成颗粒过滤,并回流进入回油罐,直至回油罐底部的检测装置检测达标后停止运行;
27.7)当检测结果为液压启闭机油箱内油液液位低于设定最低液位时,启动供油操作:控制供油泵和沿程电动球阀动作,将净油罐内的油液输送至液压启闭机油箱内,直至油液液位达标;
28.8)当检测结果为油液变质且设备处于检修状态时,启动排油运行:启动事故油泵及沿程电动球阀,快速的将液压启闭机油箱内的变质油液进行排空处理,待检修人员完成对液压启闭机油箱及浸没在变质油液中的附件清洗后,择机进行供油操作。
29.相比于现有技术,本发明具有如下有益效果:
30.1.本发明能够对需要更换和净化处理的液压油快速完成更换,而不用长时间停机等待处理油液,极大的缩短了检修维护的时间,这样就极大的节约了检修维护成本。
31.2.本发明能够实时的对液压油品质进行监测,当液压油品质不达标时能及时发现并处理,并且处理时先快速更换达标的油液,再对不达标的油液进行净化过滤处理,监控及时,过滤高效,保证了液压启闭机组稳定可靠的不间断运行,进而保障了水电站安全稳定高效运行。
32.3.当液压启闭机邮箱内液压油液位不足时,本发明能及时检测并完成补油,避免启闭机在极端工况下工作带来不可预估的危险和损失。
33.4.本发明能够通过远程检测并监控与启闭机的油液状态,根据不同的检测结果对应进行处理,具有极好的便利性和高效性。
附图说明
34.图1为本发明一种实施例的系统结构示意图。
35.图2为本发明优选实施例的系统结构示意图。
36.图3为本发明中系统运行逻辑框图。
37.上述附图中:101、回油罐油液检测装置;1*1、设备油箱油液检测装置;201、回油总管;202、供油总管;203、事故油总管;2*1、*设备回油电动球阀;2*2、*设备回油手动球阀;2*3、*设备回油管电动球阀;2*4、*设备供油电动球阀;2*5、*设备供油手动球阀;2*6、*设备供油管电动球阀;2*7、*设备事故油电动球阀;2*8、*设备事故油手动球阀;2*9、*设备事故油管电动球阀;301、回油泵进口手动球阀;302、回油泵出口手动球阀;303、滤油吸油口电动球阀;304、滤油吸油口手动球阀;305、真空容器放空球阀;306、滤油回油口电动球阀;307、滤油回油口手动球阀;308、倒油手动球阀;309、供油吸油口手动球阀;310、供油吸油口电动球阀;311、供油手动球阀;312、回油罐放空球阀;313、回油罐事故油手动球阀;314、事故油电动球阀;315、净油罐放空球阀;316、净油罐事故油手动球阀;317、净油罐事故油电动球阀;318、事故油吸油口手动球阀;319、事故油池排油吸油口手动球阀;320、事故油池排油吸油口电动球阀;321、事故油池排油出油口手动球阀;322、事故油池排油出油口电动球阀;401、回油泵;402、吸油泵;403、真空泵;404、排放泵;405、供油泵;406、事故油泵;407、放空泵;501、回油罐;502、净油罐;503、回油罐空气滤清器;504、回油罐可视液位计;505、净油罐空气滤清器;506、净油罐可视液位计;507、事故油池;601、吸油过滤器;602、避震喉;603、吸油泵溢流阀;604、吸油泵出口单向阀;605、真空容器;606、加热器;607、数显传感器;608、指针机械压力表;609、温度计;610、安全阀;611、真空容器空气滤清器;612、油雾分离器;613、真空容器可视液位计;614、排放泵溢流阀;615、三位五通换向阀;616、颗粒过滤器进口单向阀;617、颗粒过滤器;618、压差发讯器;619、颗粒过滤器出口放空球阀;620、颗粒过滤器出口单向阀;621、两位三通换向阀;7、现地控制柜;7-1、指示灯;7-2、plc控制系统;7-3、触摸屏;7-4、控制按钮;7-5、电控系统;71、服务器;72、交换机;73、无线ap;74、移动查询终端;75、计算机终端。
具体实施方式
38.下面结合附图及实施例对本发明中的技术方案进一步说明。
39.在本发明的图文描述中,*表示连接的液压启闭机的设备编号,对应的附图标记表示该编号设备对应的部件,例如当本实施例中连接了3台液压启闭机时,3台启闭机对应的设备回油手动球阀则编号分别为212、222和232;在下文的描述中,根据液压和电气领域的专业描述,为便于规范和通俗理解,本发明中对系统中涉及到的电动阀门和泵进行了编号,以便于通过直观的电气动作表理解系统运行状态,具体编号见下表:
[0040][0041][0042]
另外,本发明中所述的前端指所在元器件的上游,下端指所在元器件的下游,但并不代表该元器件与所述前端或后端的元器件之间无其他元器件连接;阀门被填充为黑色表示初始位为全关,阀门未被填充的表示初始位置为全开。
[0043]
实施例1
[0044]
参阅附图1,作为本发明的一种实施例,提出了一种水电站液压启闭机液压油品质在线保障系统,它包括回油总管201、供油总管202和事故油总管203,回油总管201、供油总管202和事故油总管203均通过压力软管2*10连通液压启闭机的油箱,可布置安装在运行设备沿线通道侧墙上,每个待检测的启闭机根据现场设备位置安装对应的阀门2*1-2*9和3根快速接头软管2*10,实现本装置能与现有的运行设备快速连接,做到本发明装置的通用性;事故油总管203与事故油池507连通,且事故油总管203与事故油池507之间的管路上连接事故油泵407,事故油泵407与事故油总管203之间安装事故油吸油口手动球阀318,事故油池
后端安装放空泵307,放空泵307与事故油池407之间的管路上安装事故油池排油吸油口手动球阀319和事故油池排油吸油口电动球阀320,放空泵307后端安装事故油池排油出油口手动球阀321和事故油池排油出油口电动球阀322;它还包括:与回油总管201连通的回油系统,回油系统包括回油泵401和回油罐501,回油罐501底部安装回油罐放空球阀312,回油泵401安装在回油罐501与回油总管201之间,回油泵401进口处安装回油泵进口手动球阀301,其出口处安装回油泵出口手动球阀302,回油罐501底部与事故油总管203连通,并在此管段上安装回油罐事故油手动球阀313和事故油电动球阀314;与供油总管202连通的供油系统,供油系统包括供油泵405和净油罐502,净油罐502底部安装净油罐放空球阀315,供油泵405安装在净油罐502和供油总管202之间,供油泵405处安装排放泵溢流阀614,净油罐502与事故油总管203连通,并在此管段上安装净油罐事故油手动球阀316和净油罐事故油电动球阀317;以及连接在回油系统与供油系统之间的滤油系统;滤油系统包括水气过滤单元,水气过滤单元包括连接在回油罐501后端的真空容器605和安装在真空容器605顶部的真空泵403,以使真空容器605中形成真空或近真空状态,这样便于油液中的空气与油液实现分离,快速将油液中的气体分离出去,真空容器605与回油罐501之间连接吸油泵402,吸油泵402进口处安装吸油过滤器601,吸油泵进口处安装滤油吸油口电动球阀303和滤油吸油口手动球阀304,以对油液进行初步过滤,为减小系统振动,在吸油泵上端连接避震喉602,还在吸油泵402处安装吸油泵溢流阀603,在吸油泵402后端安装吸油泵出口单向阀604,真空容器605上连接指针机械压力表608和温度计609,在真空容器605外部安装真空容器可视液位计613,以监测真空容器605内的状态,真空容器605内设置加热器606,以加速油液中空气的挥发和析出,真空容器605顶部连接油雾分离器612和空气滤清器611,真空容器605顶部还连接安全阀610,为便于观察回油罐501和净油罐502内的液位,在回油罐501外部安装回油罐可视液位计504,在净油罐502问外部安装净油罐可视液位计506,真空容器605底部连接真空容器放空球阀305。
[0045]
传统运行模式中,启闭机每年进行一次定期检修,如果检测发现油液品质不佳,则对油液抽出进行改善,但改善油液品质所用时间较长。如果是常规的颗粒度和水封超标,则需要搬运滤油设备至需要被处理的油液设备部位,借助设备油箱充当容器对油液进行循环过滤处理,期间定期将油样送人工检测,直到油液检测结果合格为止。
[0046]
本实施例使用后,则可以不定期进行检测,当检测油液品质部合格时,快速抽出不合格油液,然后补入合格油液即可,改善油液品质所需时间短,对正常运行的影响较小。
[0047]
实施例2
[0048]
参阅附图1-附图3,作为本发明的一种优选实施例,在实施例1的基础上,滤油系统包括颗粒过滤单元和水气过滤单元,颗粒过滤单元包括连接在吸油泵402后端的排放泵404和连接在排放泵404后端的颗粒过滤器617,颗粒过滤器617的进口连接颗粒过滤器进口单向阀616,出口处连接颗粒过滤器出口单向阀620和颗粒过滤器出口放空球阀619,颗粒过滤器617所在的管路上安装压差发讯器618,以监测颗粒过滤器617前后端的压力差;吸油泵402的出口连接三位五通换向阀615的进口,水气过滤系统和颗粒过滤单元的进口和出口分别连接三位五通换向阀615剩余四个端口,以使三位五通换向阀615处于三种阀位时,分别实现水气过滤系统单独运行、颗粒过滤单元单独运行、水气过滤系统和颗粒过滤单元同时运行;颗粒过滤单元的后端通过两位三通换向阀621分别与净油罐502和回油罐501连通,颗
粒过滤单元与回油灌501之间的管路上安装滤油回油口电动球阀306和滤油回油口手动球阀307,颗粒过滤单元与净油罐502之间的管路上安装倒油手动球阀308,净油罐502与供油泵405之间连接供油吸油口手动球阀309和供油吸油口电动球阀310,供油泵405与供油总管202之间安装供油手动球阀311;回油总管201、供油总管202和事故油总管203上并列的连通*台液压启闭机的油箱,且回油总管201与每个液压启闭机的油箱之间的压力软管2*10上均连接常开状态的*设备回油手动球阀2*2,和常闭状态的*设备回油管电动球阀2*3,供油总管202与每个液压启闭机的油箱之间的管路上均连接常开状态的*设备供油手动球阀2*5,和常闭状态的*设备供油电动球阀2*4;回油罐501顶部连接回油罐空气滤清器503,净油罐502顶部连接净油罐空气滤清器505,真空容器605的顶部连接真空容器空气滤清器611,真空容器605顶部还连接油雾分离器612。
[0049]
本实施例中,还包括安装在液压启闭机的油箱下部的设备油箱油液检测装置1*1,设备油箱油液检测装置1*1包括温度传感器、液位传感器、水分传感器和污染度传感器,回油罐501底部安装回油罐油液检测装置101;同时还包括现地控制单元和远程控制单元,现地控制单元包括现地控制柜7,现地控制柜7内安装电控系统7-5和plc控制系统7-2,plc控制系统7-2用于包括控制回油泵401、吸油泵402、真空泵403、排放泵404、供油泵405、事故油泵406、放空泵407以及电动球阀动作,现地控制柜7上还设置运行状态指示灯7-1、显示屏7-3和控制按钮7-4;远程控制单元包括服务器71和交换机72,还包括与交换机72连接的计算机终端75和无线ap73,以及与无线ap73通讯的移动查询终端74。
[0050]
在人机控制过程中,通过plc控制系统分析处理检测装置检测出的数据后,输出对应的执行动作指令,从而控制本发明装置各个构件的有效执行。
[0051]
本发明中涉及到的阀门,包含系统管路沿线阀门301-323和总管阀门2*1-2*9,用于阻断油路的通断,以便能按需控制设备油箱中油液的操作处理,包含手动球阀(代号sf)、电动球阀(代号df)和放空球阀(代号fk),其中手动球阀主要用于检修工况下阻断系统油路,为检修人员维护设备创造条件,电动球阀用于装置在运行工况下通断系统油路,可导通需要被操作的设备油箱与系统装置连接,实现对设备油箱的油液品质提升处理,放空球阀再装在存油设备的最底部,用于放空容器内的油液。
[0052]
本发明中涉及到的油泵,为本发明的主要动力源,用于抽、供、排装置内油液,实现油液在装置内按需安全运行,其中回油泵401安装在系统装置回油罐501前端,可将设备油箱内不达标油液抽回到回油罐501内,吸油泵402安装在系统装置过滤设备的进油口部位,为装置提供吸油动力,真空泵403安装在装置真空容器605顶部,可使油液在真空中脱水脱气,排放泵404安装在系统装置回油过滤器前端,为系统装置油液过滤提供动力源,供油泵405安装净油罐502后端,可将净油罐502内合格油液供回到设备油箱内,事故油泵406安装在事故油池507前端,可将设备油箱内事故油液抽排至事故油池507内,放空泵407安装在事故油池507后端,用于将事故油池507内的事故油液抽排至室外中转容器内,方便转运至危化品仓库进行集中处理。
[0053]
本发明涉及到的油罐,为本发明装置的主要存油设备,其单个油罐体积为设备油箱的1.5倍,包含有回油罐501和净油罐502,油罐侧面安装有目视液位计,顶部安装有空气滤清器,回油罐501用于存储抽回的设备油箱内不达标油液,净油罐502用于存储经装置过滤系统处理合格后的油液。
[0054]
本发明中的系统在对油液进行处理时,包含回油处理,滤油处理,供油处理,事故排油处理;可根据检测装置1*1检测结果,将检修状态的设备进行回油处理,并快速的将净油罐内合格的油液置换到设备油箱内;系统可根据检测装置101检测结果,按需处理回油罐501内不达标的油液,该系统能对油液进行单项脱水脱气处理,单项颗粒过滤处理和综合滤油处理,然后将处理达标的油液倒换至净油罐502内备用;同时系统能快速补充设备油箱液位不达标的油液,也能快速将变质油液进行及时排油处理。
[0055]
具体控制方法,包括以下步骤:
[0056]
1)设定液压启闭机油液的水分、温度、液位和污染度目标值,检测装置对液压启闭机邮箱内的油液水分、温度、液位和污染度进行检测;
[0057]
2)将检测结果与目标值的对比,油液不合格且设备处于检修状态,则系统进行回油操作,将液压启闭机油箱内油液全部抽取进入回油罐后,启动对液压启闭机油箱运行供油,将净油罐内合格的液压油供输至液压启闭机油箱,待检测装置检测到液压启闭机油箱油液液位达标后停止供油运行;
[0058]
3)根据检测结果对抽回回油罐内的油液进行过滤操作;
[0059]
4)当检测结果为油液颗粒度超标时,启动颗粒过滤单元单独运行:控制沿程电动球阀和吸油泵动作,且三位五通阀动作使经吸油泵流入的油液直接流入颗粒过滤器完成颗粒过滤,并回流进入回油罐,直至回油罐底部的检测装置检测达标后停止运行;
[0060]
5)当检测结果为油液水分或气体超标时,启动水气过滤单元单独运行:控制沿程电动球阀、吸油泵和真空泵动作,且三位五通阀动作使经吸油泵流入的油液直接流入真空罐内完成水分和气体过滤,并回流进入回油罐,直至回油罐底部的检测装置检测达标后停止运行;
[0061]
6)当检测结果为油液颗粒度和水分或气体同时超标时,启动综合滤油运行:控制沿程电动球阀、吸油泵和排放泵动作,且三位五通阀动作使经吸油泵流入的油液先流入真空罐内完成水分和气体过滤,再经排放泵流入颗粒过滤器完成颗粒过滤,并回流进入回油罐,直至回油罐底部的检测装置检测达标后停止运行;
[0062]
7)当检测结果为液压启闭机油箱内油液液位低于设定最低液位时,启动供油操作:控制供油泵和沿程电动球阀动作,将净油罐内的油液输送至液压启闭机油箱内,直至油液液位达标;
[0063]
8)当检测结果为油液变质且设备处于检修状态时,启动排油运行:启动事故油泵及沿程电动球阀,快速的将液压启闭机油箱内的变质油液进行排空处理,待检修人员完成对液压启闭机油箱及浸没在变质油液中的附件清洗后,择机进行供油操作。
[0064]
上述控制过程中,不同运行操作模式下,系统电气动作表见下表:
[0065]
系统电气动作表
[0066][0067]
最后说明的是,以上实施例仅用以说明本发明的技术方案而非限制,尽管参照较佳实施例对本发明进行了详细说明,本领域的普通技术人员应当理解,可以对本发明的技术方案进行修改或者等同替换,而不脱离本发明技术方案的宗旨和范围,其均应涵盖在本发明的权利要求范围当中。