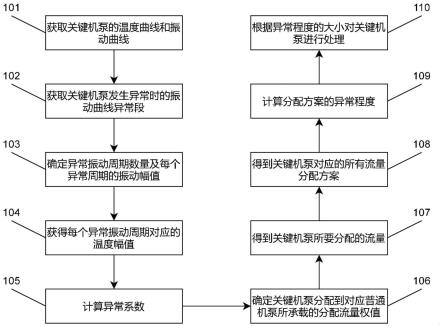
1.本发明涉及人工智能领域,具体涉及一种基于智能物联网的设备故障检测方法。
背景技术:2.钢铁焦化企业属于设备资产密集型企业,现场设备由塔罐、管线、反应器、机泵群、压缩机、透平等设备组成,自动化水平高、生产连续性强,兼有高温、高压、易燃、易爆、易腐蚀、易中毒的特点,一旦设备发生问题,对整个装置的运行将造成严重影响,直接影响企业的经济效益,甚至导致火灾、爆炸、人身伤亡等重大事故。
3.现有的焦化厂机泵的维护以预防性维护结合人工点巡检的方式为主。企业针对某类装置和设备会定期的进行检修,但缺少实时有效的数据,难以达到较好的检修效果,又带来了大量的维护工作和成本的增加。现场的安保系统缺少诊断分析功能或难以有效利用诊断功能,只能发现晚期故障。同时由于缺少设备运行数据,从而影响维修决策。
4.针对这种情况,本发明通过对焦化装置多个关键机泵的振动明显部位均安装检测头,获取振动参数与温度参数,通过分析获取的参数信息,提出了一种基于智能物联网的设备故障检测方法。
技术实现要素:5.本发明提供一种基于智能物联网的设备故障检测方法,以解决现有的不能实时监测机泵状态的问题。
6.本发明的一种基于智能物联网的设备故障检测方法,采用如下技术方案:
7.获取泵组中每个关键机泵的温度曲线与振动曲线;
8.利用关键机泵的振动曲线获取关键机泵发生异常时异常时间段内的振动曲线异常段;
9.利用振动曲线异常段确定该振动曲线异常段中异常振动周期数量及每个异常周期的振动幅值;
10.根据振动曲线异常段提取温度曲线中对应时间段内每个异常振动周期所对应的温度幅值;
11.根据振动曲线异常段内每个异常周期的振动幅值与标准周期振动幅值的差值、振动曲线异常段内所有振动周期的振动幅值与标准周期振动幅值差值的平均值及每个异常振动周期所对应的温度幅值计算该振动曲线异常段的异常系数;
12.获取发生异常的关键机泵分流所对应的普通机泵,根据关键机泵与其对应的普通机泵之间的流量交互量以及距离确定关键机泵分配到其对应的每一个普通机泵所承载的分配流量权值;
13.通过关键机泵的异常系数及该关键机泵所承载的流量得到关键机泵所要分配的流量;
14.根据关键机泵所要分配的分配流量,确定出该关键机泵向其对应的每一个普通机
泵进行流量分配的分配方案;
15.根据每一个分配方案中每个普通机泵所分配的流量及该普通机泵所承载的分配流量权值计算该分配方案的异常程度;
16.选取获得的所有分配方案的异常程度最小值,该异常程度最小值对应的分配方案为最佳方案,当该异常程度最小值不属于设定阈值范围内时,对关键机泵进行人工检修,当该异常程度最小值在设定阈值范围内时,按照最佳分配方案对关键机泵所要分配的流量进行分配。
17.进一步的,所述的一种基于智能物联网的设备故障检测方法,分配完成后还包括:
18.检测分配完成后关键机泵的温度曲线与振动曲线,当出现振动曲线异常段时,计算该振动曲线异常段的的异常系数,对关键机泵的流量进行进一步分配。
19.进一步的,所述的一种基于智能物联网的设备故障检测方法,获取关键机泵发生异常时异常时间段内的振动曲线异常段的方法为:
20.若关键机泵出现连续异常周期时,从第一个异常周期开始,统计设定时间段内的异常曲线,将该异常曲线作为异常时间段内的振动曲线异常段。
21.进一步的,所述的一种基于智能物联网的设备故障检测方法,振动曲线异常段的异常系数的表达式为:
[0022][0023]
式中:γ表示关键机泵在振动曲线异常段的异常系数,α表示异常阶段的第α个振动周期,n表示异常阶段的振动周期数,b
α
表示第α个振动周期关键机泵振动幅值与标准值的差值,表示异常阶段所有振动周期振动幅值与标准差的均值,m(n)表示振动幅值差值的排列熵,h(n)表示温度幅值差值的排列熵。
[0024]
进一步的,所述的一种基于智能物联网的设备故障检测方法,确定关键机泵分配到其对应的每一个普通机泵所承载的分配流量权值的方法为:
[0025]
通过关键机泵与其对应的普通机泵之间的流量交互量和距离得到流量距离比值,通过关键机泵对应的流量距离比值与普通机泵的总流量交互量得到关键机泵分配到其对应的每一个普通机泵所承载的分配流量权值。
[0026]
进一步的,所述的一种基于智能物联网的设备故障检测方法,关键机泵所要分配的流量的表达式为:
[0027]
c=c*γ
[0028]
式中:c表示关键机泵所要分配的流量,c表示关键机泵所承载的流量。
[0029]
进一步的,所述的一种基于智能物联网的设备故障检测方法,异常程度的表达式为:
[0030][0031]
式中:q表示关键机泵和与其有流量交互的普通机泵的异常程度,o表示与关键机泵有流量交互的普通机泵的个数,o表示与关键机泵有流量交互的第o个普通机泵,ρ表示超参数,i表示第i个普通机泵,j表示第j个普通机泵,yi表示第i个普通机泵分配后的流量,g(yi)表示普通机泵增加流量所导致的温度变化,wj表示第j个普通机泵与关键机泵的协助能
力,δxi=y
i-xi表示第i个普通机泵分配的流量,xi表示第i个普通机泵的当前流量,wi表示第i个普通机泵与关键机泵的协助能力,δxj=y
j-xj表示第j个普通机泵分配的流量,yj表示普通机泵分配后的流量,xj表示第j个普通机泵的当前流量。
[0032]
进一步的,所述的一种基于智能物联网的设备故障检测方法,所述流量分配的分配方案中关键机泵向每个普通机泵分配的流量不超过该普通机泵所承载的分配流量权值与该普通机泵承载的最大流量获得的分配流量值。
[0033]
本发明的有益效果是:本发明利用传感器采集设备关键机泵实时运行的振动与温度数据,获取异常关键机泵的异常情况,根据关键机泵与普通机泵之间的关联程度进行自适应调节与报警控制,相对于现有技术,可实时掌握设备状态,实现预测性维护维修,最大限度减少“过修”或“欠修”,同时可有效减少非计划停机次数,保障生产效益;相对于现有技术,通过对设备状态进行判断和预测,可最大限度地降低安全事故风险。
附图说明
[0034]
为了更清楚地说明本发明实施例或现有技术中的技术方案,下面将对实施例或现有技术描述中所需要使用的附图作简单地介绍,显而易见地,下面描述中的附图仅仅是本发明的一些实施例,对于本领域普通技术人员来讲,在不付出创造性劳动性的前提下,还可以根据这些附图获得其他的附图。
[0035]
图1为本发明的一种基于智能物联网的设备故障检测方法的实施例的流程示意图。
具体实施方式
[0036]
下面将结合本发明实施例中的附图,对本发明实施例中的技术方案进行清楚、完整地描述,显然,所描述的实施例仅仅是本发明一部分实施例,而不是全部的实施例。基于本发明中的实施例,本领域普通技术人员在没有做出创造性劳动前提下所获得的所有其他实施例,都属于本发明保护的范围。
[0037]
实施例1
[0038]
本发明的一种基于智能物联网的设备故障检测方法的实施例,如图1所示,包括:
[0039]
101、获取泵组中每个关键机泵的温度曲线与振动曲线;
[0040]
由于焦化装置存在多个机泵,每个机泵所起到的作用各不相同,各个机泵相互协调工作完成焦化任务,其中部分机泵所处位置与控制能力强,处于焦化装置的节点位置,此类机泵工作或发生异常时振动较为明显,通过此类机泵采集到的数据更具备代表性,当焦化装置运行异常时,此类机泵所采集到的数据可以更好的反馈异常。将此类机泵记为关键机泵,在焦化装置多个关键机泵的振动明显部位均安装检测头,检测头用于检测关键机泵振动的运行状态参数,检测头包括振动传感器、温度传感器和依据机泵种类选取的其它所需的传感器,例如对风机类的机泵可增加用于检测风速或风量的传感器,仅在关键机泵的振动明显部位安装检测头,可获取真实有效的例如振动状况或者发热状况等设备数据。
[0041]
分别通过每个关键机泵节点的检测头获取该关键机泵节点的温度数据与振动数据,得到每个关键机泵节点的温度曲线与振动曲线。
[0042]
至此,通过在关键机泵节点振动明显处布置检测头,获取每个关键机泵节点的实
时振动与温度数据。
[0043]
102、利用关键机泵的振动曲线获取关键机泵发生异常时异常时间段内的振动曲线异常段;
[0044]
103、利用振动曲线异常段确定该振动曲线异常段中异常振动周期数量及每个异常周期的振动幅值;
[0045]
104、根据振动曲线异常段提取温度曲线中对应时间段内每个异常振动周期所对应的温度幅值;
[0046]
关键机泵正常工作时,机泵的振动通常呈周期性变化或近似周期性变化,当存在一些外界的影响时,会使得机泵的振动频率出现小范围的波动,打乱原有的周期,但此种变化是小范围的变化,基本不会影响振动周期,当关键机泵出现工作异常时,例如流量(空气流量或液体流量)出现激增时或关键机泵长时间工作,机泵负荷量激增,或机泵内部出现异常(零件故障)都会导致振动周期远远异于机泵正常工作时的振动周期,同时当机泵工作异常时,会伴随着机泵温度的变化,机泵温度变化越剧烈,该机泵出现异常的风险越大,越有可能导致事后抢修,故根据机泵的振动曲线与温度变化曲线判断当前时刻机泵的运行状况,获取机泵异常工作时刻,根据当前时刻异常状况预测异常严重程度,对其进行负荷均摊,通过计算获取负荷影响最小的分摊方法。普通机泵由于所承载的任务关键程度低,故某些普通机泵出现问题时对焦化过程影响较小,而关键机泵所承载的任务关键,故其运行状态影响焦化过程较大。故关键机泵的参数需要实时监控,普通机泵的参数可根据历史数据获取。
[0047]
本实施例要对工作异常的关键机泵进行异常判断并进行准确的控制,需要先计算得到较为准确的工作异常时刻与异常等级,具体过程为:
[0048]
根据振动曲线获取关键机泵的最小振动周期,关键机泵在正常工作时,机泵的功率与运行状态正常,故机泵发生振动也呈周期性振动,此时通过人工标注获取最小振动周期模板。但由于环境因素与一些外界因素的影响(如地面震动),会导致机泵振动曲线的振幅存在细微的差异,故通过原始的振动数据计算振动周期性不准确,此时为了消除外界因素对获取最小周期造成的干扰,需对原始的振动数据进行修改,增加容错范围。以标准最小振动周期模板为参照,对周期内每个时刻的数据增加容错范围,即模板中的某一个值为a,增加容错范围后的值为a
±
β,β即为容错范围,即当实施数据中对应周期中对应时刻的值在a
±
β范围内,则将实时数据修改为a,若不在范围内则保留原始数据,得到对应时刻的修正振动曲线。
[0049]
上述过程考虑到关键机泵在正常工作时发生的振动呈现周期性,获取最小振动周期模板,实时监测关键机泵的振动数据,将实时数据与模板数据进行对比,监测关键机泵是否出现工作异常;同时为消除外界因素对监测结果的影响,对数据增加一个容错范围,例如,若实时监测的振动数据的振动程度为a
′
,对应在模板振动周期的振动程度值为a,考虑容错范围,若a-β≤a
′
≤a+β,则将此时的振动程度修改为a,若a
′
不在[a-β,a+β]之间,则将保留此时的振动程度a
′
。
[0050]
当实时数据出现超出容错范围的振动值时,对当前时刻(振动周期)进行标记,记录此振动周期开始的下一振动周期的振动值,若下一振动周期的振动值同样超出容错范围时,此时需要重点监测该关键机泵的工作状态,即当出现连续的振动异常时,该机泵大概率
出现工作异常,即以标记振动周期开始,记录后续若干连续振动周期的振动状态,该连续若干振动周期为设定的时间段,此连续若干振动周期的数据为异常阶段的数据。
[0051]
105、根据振动曲线异常段内每个异常周期的振动幅值与标准周期振动幅值的差值、振动曲线异常段内所有振动周期的振动幅值与标准周期振动幅值差值的平均值及每个异常振动周期所对应的温度幅值计算该振动曲线异常段的异常系数;
[0052]
异常阶段关键机泵的异常系数的表达式为:
[0053][0054]
式中:γ表示关键机泵在异常阶段的异常系数,α表示异常阶段的第α个振动周期,n表示异常阶段的振动周期数,b
α
表示第α个振动周期关键机泵的振动幅值与标准值的差值,表示异常阶段所有振动周期振动幅值与标准差的均值,m(n)表示振动幅值差值的排列熵,h(n)表示温度幅值差值的排列熵。
[0055]
所述振动幅值差值排列熵m(n)为差值序列(b1,b2,b3...bn)的混乱程度,当差值序列中的差值bn呈线性增长时,此时序列的混乱程度低,即对应的异常阶段的异常程度严重,即下一时刻比上一时刻的运行状况偏离正常运行的程度越大;所述温度幅值差值排列熵h(n)的原理同振动幅值差值排列熵一致,所述温度幅值差值序列为(t1,t2,t3...tn),排列熵为现有技术,其计算方法此处不再概述。
[0056]
计算得到的异常系数γ的值越大,越趋近于1,说明该关键机泵继续按照此运行状态运行下去机泵的状态趋势会越来越差,异常系数γ的值越大,机泵发生严重故障导致事后抢修的概率越大。
[0057]
上述过程表明只有连续振动周期出现振动值超出容错范围,才会将该部分振动周期作为异常阶段,通过关键机泵在异常阶段的振动幅值差值、振动幅值差值排列熵、温度幅值差值排列熵计算关键机泵在异常阶段的异常系数,根据该异常系数确定关键机泵的异常程度。
[0058]
106、获取发生异常的关键机泵分流所对应的普通机泵,根据关键机泵与其对应的普通机泵之间的流量交互量以及距离确定关键机泵分配到其对应的每一个普通机泵所承载的分配流量权值;
[0059]
获取每个机泵的控制能力:机泵在工作时,不同的机泵功率不同,所能控制的流量不同(此处流量为进风量、液体流量等,统称为流量),关键机泵所起到的控制功能强于普通机泵,由此对每个机泵进行控制能力等级划分,分为10个等级,等级越大,所起到的控制效果越强,所控制的流量越多,关键程度越大。
[0060]
分析普通机泵与关键机泵之间的关系,获取普通机泵与关键机泵间的协助能力(即为关键机泵分配到其对应的每一个普通机泵所承载的分配流量权值):普通机泵与关键机泵之间存在流量交互,流量交互量越大,通过改变流量控制参数能够最快达到对关联机泵的调节作用,说明该普通泵与关键机泵之间的关联程度越大,获取某个普通机泵与关键机泵的流量交互量与距离的比值和该普通机泵与所有机泵之间的流量交互量之比(表示该普通机泵与关键机泵之间的流量交互越大且距离越近,越能够更快的分担关键机泵的流量压力),将该比值作为普通机泵与关键机泵的协助能力,表示该普通机泵协助关键机泵能力的大小,该值越大说明协助能力越强,越能分担关键机泵的压力使其尽快恢复正常运行。
[0061]
根据机泵的分布情况,以机泵为节点,节点分为关键节点与普通节点(关键机泵为关键节点,普通机泵为普通节点),关键节点与普通节点之间的边权值为关键机泵与普通机泵间的协助能力,构建一个图结构数据g1。机泵节点的值为机泵控制能力、异常系数构成的向量。
[0062]
107、通过关键机泵的异常系数及该关键机泵所承载的流量得到关键机泵所要分配的流量;
[0063]
当关键节点发生异常时,期望将关键节点的任务分配到与其相关的普通节点上,即期望关键机泵节点的控制能力降低,减少控制量。每一个控制等级对应一个控制量,则关键机泵工作异常需要分配出去的流量为:
[0064]
c=c*γ
[0065]
式中:c表示关键机泵需要分配出的流量,c表示关键机泵控制的流量(即为承载的流量),γ表示异常系数,异常程度越大,则代表需要分出的流量越大。
[0066]
当关键机泵发生异常时,通过上述公式确定需要分配出的流量,分配出部分流量后,关键机泵控制的流量减少,缓解了关键机泵的压力,可以避免设备停机影响生产效益。
[0067]
108、根据关键机泵所要分配的分配流量,确定出该关键机泵向其对应的每一个普通机泵进行流量分配的分配方案;
[0068]
109、根据每一个分配方案中每个普通机泵所分配的流量及该普通机泵所承载的分配流量权值计算该分配方案的异常程度;
[0069]
110、选取获得的所有分配方案的异常程度最小值,当该异常程度最小值不属于设定阈值范围内时,对关键机泵进行人工检修,当该异常程度最小值在设定阈值范围内时,按照最佳分配方案对关键机泵所要分配的流量进行分配。
[0070]
通常情况下,普通节点与关键节点的协助能力越强,分配的任务量越多,但是按照此方法进行分配会导致普通机泵的负荷量增大,导致普通机泵出现异常,此时需要将关键节点的任务分配到普通节点以保障关键节点回归正常,同时保障所有节点的异常程度最小,故建立关键机泵和与其有流量交互的普通机泵的异常程度模型,模型如下:
[0071][0072]
式中:q表示关键机泵和与其有流量交互的普通机泵的异常程度,o表示与关键机泵有流量交互的普通机泵的个数,o表示与关键机泵有流量交互的第o个普通机泵,ρ表示超参数,经验值取1,i表示第i个普通机泵,j表示第j个普通机泵,yi表示第i个普通机泵分配后的流量,g(yi)表示普通机泵增加流量所导致的温度变化,可通过历史数据获取(即普通机泵不同流量所对应的温度曲线表),wj表示第j个普通机泵与关键机泵的边权值,δxi=y
i-xi表示第i个普通机泵分配的流量,xi表示第i个普通机泵的当前流量,wi表示第i个普通机泵与关键机泵的边权值,δxj=y
j-xj表示第j个普通机泵分配的流量,yj表示第j个普通机泵分配后的流量,xj表示表示第j个普通机泵的当前流量。
[0073]
上述式中δx1+...δxi...+...δxj+...δx0=c,q表示关键机泵和与其有流量交互的普通机泵的异常程度,系统期望异常程度q的值最小,且给普通机泵分配的流量不超过该普通机泵所承载的分配流量权值与其普通机泵承载的最大流量获得的分配流量值,此时分配的流量既可以减轻关键节点的负担,使其尽快恢复正常,也可以使普通机泵异常最小。
采用梯度下降法进行求解,得到最优分配量与最小异常程度。
[0074]
通过上述模型求解最优分配量,使得每个普通机泵分配流量后得到的异常程度q尽可能的小,即为将关键机泵部分流量分配出去的同时,普通机泵能在各自负荷量范围内正常工作。
[0075]
根据求解获取的关键节点相关的所有节点的异常程度q值的大小进行等级划分,即当q值在某一区间范围内时,该关键机泵的异常可根据与其相关的普通机泵进行调节,当q值超出阈值范围时,说明通过调节与其相关的普通机泵的流量导致的风险较大,即系统自适应调节会导致整个系统的风险较大,故此时进行系统自适应调节时不适用,此时进行报警,通过报警提示,人工对异常关键机泵进行调节与检修,使其回归正常运行状态。
[0076]
根据异常阶段机泵的异常系数,对出现异常的关键机泵进行人工抽检,检测关键机泵出现工作异常的原因,并给出相应的调节方法,此时将人工调节方法与系统自适应调节方法进行验证,若多个抽检结果均与系统自适应调节结果存在较大差异,此时对超参数ρ进行调节,使其自适应调节结果与人工抽检调节方法的差异尽可能小。
[0077]
本发明的有益效果是:本发明利用传感器采集设备关键机泵实时运行的振动与温度数据,获取异常关键机泵的异常情况,根据关键机泵与普通机泵之间的关联程度进行自适应调节与报警控制,相对于现有技术,可实时掌握设备状态,实现预测性维护维修,最大限度减少“过修”或“欠修”,同时可有效减少非计划停机次数,保障生产效益;相对于现有技术,通过对设备状态进行判断和预测,可最大限度地降低安全事故风险。
[0078]
以上所述仅为本发明的较佳实施例而已,并不用以限制本发明,凡在本发明的精神和原则之内,所作的任何修改、等同替换、改进等,均应包含在本发明的保护范围之内。