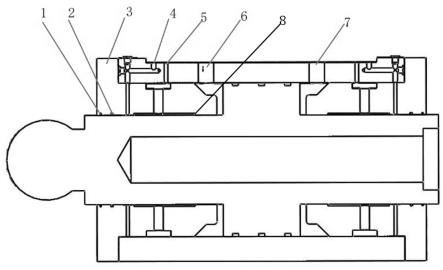
1.本发明属于液压缸技术领域,具体涉及一种用于高频振动的具有织构化的高频重载油缸密封及静压支撑结构。
背景技术:2.在当今的振动试验台的设计和具体实验过程中,液压缸会承受侧向加载力且要求液压缸作高频运动(大于50hz),而传统的液压缸中的活塞杆和导向套之间的摩擦力大,无法满足高频要求,且导向套无法承受很大的径向力加载,无法满足目前振动实验台的需求。
技术实现要素:3.本发明为解决现有液压缸中活塞和导向套之间的摩擦大以及径向承载力小的技术问题,提供一种具有织构化的高频重载油缸密封及静压支撑结构。
4.本发明是采用如下技术方案实现的:一种具有织构化的高频重载油缸密封及静压支撑结构,在油缸的活塞杆上套设有中心开孔的静压支撑,所述静压支撑包括套在油缸缸筒和活塞杆之间的支撑套筒以及套在活塞杆伸出缸筒部分上的端盖;所述端盖通过一个端面与油缸缸筒端面螺栓连接,端盖中心孔内壁固定有与活塞杆密封接触的密封件;支撑套筒内壁与活塞杆外壁之间周向设有至少一组油膜支撑结构,每组油膜支撑结构由多个油膜间隙组成,每个油膜间隙内充有使活塞杆悬浮的一层油膜;对应每个油膜间隙,支撑套筒上沿径向开有一个进油槽;对应一组油膜支撑结构,油缸缸筒上开有一个静压支撑回油口和一个静压支撑进油口,且油缸缸筒内壁与支撑套筒外壁之间开有一道环形油路,该道环形油路与静压支撑进油口和多个进油槽相连通;在支撑套筒内壁开有一道环形油路作为回油槽,该回油槽与静压支撑回油口相连通。
5.静压支撑结构代替了原有油缸的导向套,密封件与静压支撑互为一体。活塞杆悬浮在一层油膜上,与静压支撑结构不接触。通过这条狭窄的油膜间隙,使得摩擦力降低。静压支撑的压力供给由外接液压系统提供。泄漏的油液通过卸油槽(回油槽)流进回油口,不需要吸出。
6.进一步的,油缸套筒内壁与活塞杆外壁进行织构化处理形成织构,进而构成油膜间隙。
7.在静压支撑结构和活塞杆接触的地方进行织构化,进一步提高了本发明的密封的性能,主要体现在增强端面承载能力、减少摩擦磨损、减小了泄漏。
8.进一步的,每个进油槽内均安装有管状的阻尼安装件,进油槽装配不同孔径的阻尼件来实现油膜进油量调节,进而调节油液压力。
9.与现有技术相比,本发明的有益效果是:1、本发明所述具有织构化的高频重载油缸密封及静压支撑的结构,静压支撑结构代替了原有油缸的导向套,密封件与静压支撑互为一体。活塞杆悬浮在一层油膜上,与静压支撑结构不接触。进一步增强端面承载能力、减少摩擦磨损、减小泄漏。
10.2、本发明所述具有织构化的高频重载油缸密封及静压支撑的结构,在静压支撑结构和活塞杆接触的地方进行织构化。织构的存在可以有效地降低接触面之间的摩擦系数,形成较厚的油膜,提高摩擦磨损特性,使得摩擦副接触面减少硬接触,有效降低磨损损耗。
11.3、本发明所述具有织构化的高频重载油缸密封及静压支撑结构,静压支撑进油口下方的静压支撑阻尼孔可调节,调节油膜间隙的油液压力,进而控制油膜刚度。
12.本发明在具有较高侧向力和较高频率(大于50hz)的场合具有非常大的优势和应用前景。
附图说明
13.图1本发明整体结构示意图。
14.图1中:1-防尘圈,2-格莱圈,3-静压支撑,4-静压支撑回油口,5-静压支撑进油口,6-油缸左进油口,7-油缸右进油口,8-油膜间隙。
具体实施方式
15.实施例1一种具有织构化的高频重载油缸密封及静压支撑结构,在油缸的活塞杆上套设有中心开孔的静压支撑3,所述静压支撑3包括套在油缸缸筒和活塞杆之间的支撑套筒以及套在活塞杆伸出缸筒部分上的端盖;所述端盖通过一个端面与油缸缸筒端面螺栓连接,端盖中心孔内壁固定有与活塞杆密封接触的密封件;支撑套筒内壁与活塞杆外壁之间周向设有至少一组油膜支撑结构,每组油膜支撑结构由多个油膜间隙8组成,每个油膜间隙8内充有使活塞杆悬浮的一层油膜;对应每个油膜间隙8,支撑套筒上沿径向开有一个进油槽;对应一组油膜支撑结构,油缸缸筒上开有一个静压支撑回油口4和一个静压支撑进油口5,且油缸缸筒内壁与支撑套筒外壁之间开有一道环形油路,该道环形油路与静压支撑进油口5和多个进油槽相连通;在支撑套筒内壁开有一道环形油路作为回油槽,该回油槽与静压支撑回油口4相连通。回油槽开在靠近端盖的位置,从油膜间隙漏出的油液经过活塞杆与支撑套筒之间的间隙进入回油槽,又通过回油槽以及静压支撑回油口4流出。
16.油缸套筒内壁与活塞杆外壁进行织构化处理形成织构,进而构成油膜间隙8。所述密封件包括防尘圈1和格莱圈2。
17.本发明在具有较高侧向力和较高频率(大于50hz)的场合具有非常大的优势和应用前景。
18.本发明同时也可以存在侧向加载力的工况,静压支撑结构代替了原有油缸的导向套,密封件与静压支撑互为一体。活塞杆悬浮在一层油膜上,与静压支撑结构不接触。通过这条狭窄的轴承间隙(油膜间隙),压力降低。静压轴承的压力供给由压力系统内部提供。
19.活塞杆通过多个油膜间隙8中的压力作用而被液压浮动。此时静压支撑结构和密封是唯一的结构件。只有防尘圈可能引起可以忽略不计的极小量的摩擦。在此种密封组合装置中的流体静力作用可以使活塞杆顶住可能出现的横向剪力而对准中心。流体静压支撑的压力是由内部的系统压力提供的。接触的防漏油密封和防尘圈不承受压力。因此只产生很小的在整个压力范围内恒定的残余摩擦。泄漏的油液通过回油槽流进回油口,不需要吸出。同时在静压支撑结构和活塞杆接触的地方进行织构化,进一步提高了本发明的密封的
性能,主要体现在增强端面承载能力、减少摩擦磨损、减小了泄漏;使得机械密封在保证优良的密封性能下能够更好的工作。本发明提供了一种密封性能强、泄露小,摩擦磨损少,可以用在高频和高侧向力工况下的结构。
20.实施例2每个进油槽内均安装有管状的阻尼安装件,进油槽内开有内螺纹,阻尼安装件外壁设有外螺纹,二者通过螺纹连接。阻尼安装件有不同的规格,做成不同的内径,根据工作需要进行更换,以便实现油膜进油量调节,进而调节油液压力。
21.实施例3多个油膜间隙8环绕活塞杆外壁周向等间距均布,共用一个静压支撑回油口4和一个静压支撑进油口,相应的进油槽环绕支撑套筒周向等间距分布;每个油膜间隙8走向均与活塞杆轴向平行,这样的结构设计能够确保活塞杆被油膜支撑的更加稳定,运行时摩擦力更小且更平稳。
22.实施例4静压支撑回油口4和静压支撑进油口5连接有独立的液压系统。油缸缸筒和支撑套筒上开有推动活塞杆运动的油缸左进油口6和油缸右进油口7;所述油膜支撑结构为两组,分别位于油缸左进油口6的左侧以及油缸右进油口7的右侧。每个油膜支撑结构包含四个等间距环布的油膜间隙。两组油膜支撑结构布置在活塞杆的左右两端,油膜起到的支撑力更大,这样能够保证活塞杆运行更加稳定。油缸左进油口6和油缸右进油口7在从油缸缸筒过渡到支撑套筒的位置处为斜口。该处静压支撑结构有助于液压油的进入。
23.下面结合附图和实例对本发明作进一步说明。
24.如图1所示,一种用于具有织构化的高频重载油缸密封及静压支撑结构,主要是用静压支撑结构代替了原有油缸的导向套,密封件与静压支撑互为一体。活塞杆悬浮在一层油膜上,与静压支撑结构不接触。通过这条狭窄的轴承间隙,使得摩擦力降低。静压轴承的压力供给由外接液压系统提供。泄漏的油液通过卸油槽(回油槽)流进回油口,不需要吸出。同时在静压支撑结构和活塞杆接触的地方进行织构化,进一步提高了本发明的密封的性能,主要体现在增强端面承载能力、减少摩擦磨损、减小了泄漏。
25.本发明通过多次有效的试验,既能够保证液压系统提供的压力,也能够保证活塞杆受到较小摩擦力,同时增大了径向载荷的承受力,织构化的表面进一步增强了端面承载能力、减少摩擦磨损、减小了泄漏,能够更好的适应一些重大实验台特殊的需求。
26.其中油缸左进油口6、油缸右进油口7通过高频响应换向伺服阀来控制油液的方向和速度。而静压支撑的卸油口4和静压支撑的进油口5由独立的液压油路系统连接,减少了一套液压系统时液压缸换向产生的压力冲击,延长了液压缸的使用寿命。