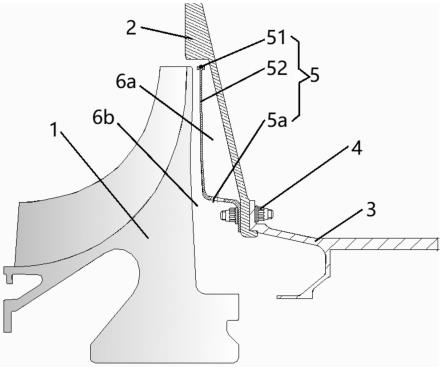
1.本发明涉及航空发动机技术领域,特别涉及一种自适应发动机状态变化的离心叶轮背腔旋流控制组件。
背景技术:2.对于采用离心压气机的中小型航空发动机,叶轮背腔常采用径向内流的引气形式,对于压比大于20的高压比发动机,离心叶轮背腔绝对压力大,背腔旋流系数值对腔压影响很大,进而影响整机转子轴向力。
3.离心叶轮背腔产生轴向力的原因是由离心叶轮出口根部引出的高压空气直接作用在背腔旋转侧上,在水平方向上产生向前的轴向力,发动机的离心叶轮自身也存在很大的向后的气动轴向力,离心叶轮背腔的轴向力起着平衡离心叶轮气动力的重要作用,离心叶轮背腔轴向力和离心叶轮气动力之间的差值在发动机轴向力计算建模中所占比重较大。
4.由于离心压气机在低转速下压比低,低转速下叶轮背腔和离心叶轮平衡后的轴向力差值很小,低状态下存在方向向后的轻载、反向问题,而高转速下离心叶轮虽可达到预期设计压比,此时叶轮背腔和离心叶轮平衡后的轴向力差值又可能过大,导致发动机方向向前的转子轴向力过大,甚至超出轴承的许用载荷,现有常规叶轮背腔引气技术方案不能起到随发动机状态变化的自适应腔压、轴向力调节功能,因此设计一种自适应发动机状态变化的离心叶轮背腔旋流控制组件,来实现离心叶轮背腔压力随发动机状态变化自适应调节是极为必要的。
技术实现要素:5.针对现有技术的不足,本发明提供了一种自适应发动机状态变化的离心叶轮背腔旋流控制组件,目的是为了具备根据发动机输出动力的大小变化来自动调节离心叶轮背腔引气状态的能力,解决目前发动机处于慢车低状态时,存在高压转子的轴向力方向向后的轻载、反向问题,以及发动机大状态下,高压转子向前的轴向力太大,超出轴承许用负荷的情况的问题。
6.为实现上述目的,本发明提供如下技术方案:一种自适应发动机状态变化的离心叶轮背腔旋流控制组件,包括离心叶轮,所述离心叶轮外侧设有径扩机匣,所述径扩机匣底部固定连接有内机匣,所述离心叶轮背腔侧设有引气调节机构,所述引气调节机构包括有导流隔板,所述导流隔板上设有密封装置,且所述导流隔板底部开设有一圈通孔,所述导流隔板选用材料的线膨胀系数大于径扩机匣选用材料的线膨胀系数。
7.所述径扩机匣底部安装有螺栓,且所述径扩机匣通过螺栓与内机匣固定连接,所述导流隔板顶部安装有o型密封圈。
8.所述o型密封圈与径扩机匣腔体内壁间留设有0.45mm冷态间隙。
9.所述导流隔板相向于内机匣一端通过螺栓与径扩机匣和内机匣固定连接。
10.所述导流隔板一侧与径扩机匣腔体内壁间围成内引气通道,所述导流隔板另一侧
与离心叶轮背腔侧围成外引气通道。
11.所述内机匣底部固定安装有节流篦齿,所述节流篦齿底端呈相向于外引气通道设置。
12.所述径扩机匣相向于内机匣一侧连接面呈斜面设置,所述内引气通道的内径自上而下逐渐增大。
13.所述通孔设置于导流隔板曲率半径最小位置,且呈周向设置。
14.所述导流隔板与离心叶轮背腔旋转侧之间轴向距离为3~5mm。
15.所述导流隔板外径与离心叶轮出口根部半径相同,且所述导流隔板的内径约为外径的50%~70%。
16.与现有技术相比,本发明提供了一种自适应发动机状态变化的离心叶轮背腔旋流控制组件,具备以下有益效果:
17.1、利用导流隔板和径扩机匣所采用合金热膨胀变形性能间的差异,实现发动机离心叶轮背腔引气从慢车等低转速状态到高转速状态的自适应切换,在慢车等低转速状态时,径扩机匣和导流隔板上o型密封圈间存在径向间隙,离心叶轮背腔引气通过此径向间隙后穿过通孔,在离心叶轮背腔旋转侧形成径向外流,提高腔压,增加发动机转子向前轴向力,解决低转速状态下转子轴向力向后的轻载、反向问题,当发动机转速上推至大状态时,零件温度可高达400℃,受不同合金之间热膨胀性能差异的影响,o型密封圈外缘与径扩机匣间形成密封,导流隔板与径扩机匣间的内引气通道径向间隙闭合,离心叶轮背腔引气沿外引气通道形成纯径向内流引气形式,可提高叶轮背腔旋流系数,降低腔压,解决发动机在高转速状态下高压转子向前轴向力过大问题,进而实现根据发动机转速,对离心叶轮背腔引气形式进行自动切换。
18.2、当发动机处于高转速状态下,由于设置的导流隔板和离心叶轮背腔旋转侧之间轴向距离控制在3~5mm,使得外引气通道呈狭窄设置,在引气流量一致的条件下,径向内流流速增加,科氏力加速引气气流周向速度,降低离心叶轮背腔风阻功耗和引气温升,提高离心叶轮背腔气流的径向压降,有效保障了对高转速状态下发动机向前的转子轴向力的折减作用,防止该轴向力与离心叶轮气动力差值过大,超出轴承的许用载荷。
19.3、由于导流隔板曲率半径较小的底部弯折区域周向布置了一圈通孔,当发动机处于低速状态时,通孔起通流作用,部分气流可穿过通孔进入外引气通道并向上形成径向外流,来降低离心叶轮背腔旋流提高腔压,增加发动机转子向前轴向力,当发动机上推高转速时,由于o型密封圈外缘与径扩机匣间密封,通过通孔可使内引气通道内部空间与外部空气进行热交换,防止零件局部温度过高。
20.本发明的其它特征和优点将在随后的说明书中阐述,并且,部分地从说明书中变得显而易见,或者通过实施本发明而了解。本发明的目的和其他优点可通过在说明书以及附图中所指出的结构来实现和获得。
附图说明
21.为了更清楚地说明本发明实施例或现有技术中的技术方案,下面将对实施例或现有技术描述中所需要使用的附图作一简单地介绍,显而易见地,下面描述中的附图是本发明的一些实施例,对于本领域普通技术人员来讲,在不付出创造性劳动的前提下,还可以根
据这些附图获得其他的附图。
22.图1示出了现有技术的离心叶轮组件的结构示意图;
23.图2示出了现有技术的离心叶轮组件的受力分析图;;
24.图3示出了现有技术的离心叶轮背腔径向内流引气的coriolisforce(科式力)分析图;
25.图4示出了现有技术的离心叶轮背腔径向外流引气的coriolisforce(科式力)分析图;
26.图5示出了根据本发明实施例的一种自适应发动机状态变化的离心叶轮背腔旋流控制组件的结构示意图;
27.图6示出了根据本发明实施例的o型密封圈和导流隔板的细部示意图;
28.图7示出了根据本发明实施例的发动机小状态下离心叶轮背腔引气状态示意图;
29.图8示出了根据本发明实施例的发动机大状态下离心叶轮背腔引气状态示意图;
30.图9示出了根据本发明实施例的发动机最大状态下结构有限元分析的径向变形示意图;
31.图10示出了根据本发明实施例的发动机最大状态下结构有限元分析的径向变形局部放大示意图;
32.图11示出了现有技术的发动机慢车状态常规径向内流引气下的叶轮背腔旋流系数分布图;
33.图12示出了根据本发明实施例的发动机慢车状态常规径向外流引气下的叶轮背腔旋流系数分布图;
34.图13示出了现有技术的发动机慢车状态常规径向内流引气下的叶轮背腔静压系数分布图;
35.图14示出了根据本发明实施例的发动机慢车状态常规径向外流引气下的叶轮背腔静压系数分布图。
36.图中:1、离心叶轮;2、径扩机匣;3、内机匣;4、螺栓;5、引气调节机构;51、o型密封圈;52、导流隔板;5a、通孔;6a、内引气通道;6b、外引气通道。
具体实施方式
37.为使本发明实施例的目的、技术方案和优点更加清楚,下面将结合本发明实施例中的附图,对本发明实施例中的技术方案进行清楚、完整地说明,显然,所描述的实施例是本发明一部分实施例,而不是全部的实施例。基于本发明中的实施例,本领域普通技术人员在没有做出创造性劳动前提下所获得的所有其他实施例,都属于本发明保护的范围。
38.请参照图1,现有常规发动机离心叶轮引气组件,离心叶轮、径扩机匣和内机匣为静子件,径扩机匣和内机匣之间周向通过均布螺栓连接以传递载荷,径扩机匣内径安装面较叶轮背腔旋转侧轴向保证一定距离,以保证径扩机匣和内机匣之间的螺栓有足够的安装空间。
39.请参照图2,离心叶轮出口根部引出的高压空气直接作用在背腔旋转侧上,在水平方向上产生向前的轴向力,同时,发动机的离心叶轮自身也存在很大的向后的气动轴向力,离心叶轮背腔的轴向力起着平衡离心叶轮气动力的重要作用,离心叶轮背腔轴向力和离心
叶轮气动力之间的差值在发动机轴向力计算建模中所占比重大。
40.请参照图3,根据旋转盘腔中科氏力作用理论:其中f代表科氏力,m为质点的质量,为相对于转动参考质点的运动速度,为旋转体系的角速度,
“×”
表示两个向量的矢量乘积,科氏力f的方向满足右手螺旋法则;当叶轮背腔引气为径向内流时,科氏力起加速叶轮背腔旋流作用,叶轮背腔径向压降大,平均腔压小,可起到减小叶轮背腔向前轴向力的作用,并且转静轴向距离越小,科氏力对叶轮背腔旋流的加速作用越明显,高转速下压气机压比增大,离心叶轮绝对压力高,叶轮背腔和离心叶轮平衡后的轴向力差值过大,甚至超出轴承允许负荷。
41.请参照图4,当叶轮背腔引气为径向外流时,科氏力起削弱叶轮背腔旋流作用,可起到降低叶轮背腔径向压降,提高腔压,增加叶轮背腔向前轴线力的作用,因此对于发动机转速较低的小状态情形,叶轮向前的轴向力较小,存在转子轴向力出现方向向后的轻载、反向问题,通过调整引气使其径向外流,可适当增加叶轮背腔轴向力和离心叶轮气动力之间的差值。
42.请参照图6,引气调节机构5包括有导流隔板52,导流隔板52采用高膨胀合金材料制作,导流隔板52顶部安装有o型密封圈51。
43.请参照图5,,一种自适应发动机状态变化的离心叶轮背腔旋流控制组件,包括离心叶轮1,离心叶轮1外侧设有径扩机匣2,径扩机匣2底部安装有螺栓4,且径扩机匣2通过螺栓4固定连接有内机匣3,离心叶轮为旋转件,径扩机匣和内机匣为静子件,径扩机匣2采用低膨胀合金制作,离心叶轮1背腔侧设有引气调节机构5,且导流隔板52底部开设有一圈通孔5a,o型密封圈51与径扩机匣2腔体内壁间留设有0.45mm左右冷态间隙,导流隔板52相向于内机匣3一端通过螺栓4与径扩机匣2和内机匣3固定连接,导流隔板52一侧与径扩机匣2腔体内壁间围成内引气通道6a,且导流隔板52另一侧与离心叶轮1背腔侧围成外引气通道6b,当发动机处于低速状态时,通孔5a起通流作用,部分气流可穿过通孔5a进入外引气通道6b并向上进行径向外流,来降低离心叶轮1背腔旋流提高腔压,增加发动机转子向前轴向力,当发动机上推高转速时,由于o型密封圈51外缘与径扩机匣2间密封,通过通孔5a可使内引气通道6a内部空间与外部空气进行热交换,防止零件局部温度过高,内机匣3底部固定安装有节流篦齿,节流篦齿底端呈相向于外引气通道6b设置,气流通过离心叶轮1背腔旋转侧沿径向向内流动,在外引气通道6b底部通过节流篦齿用于后面级零部件的冷却,径扩机匣2相向于内机匣3一侧连接面呈斜面设置,内引气通道6a自上而下的内径呈逐渐扩张,保证导流隔板52、径扩机匣2和内机匣3之间的螺栓4有足够的安装空间,通孔5a设置于导流隔板52曲率半径较小位置,且呈周向设置,导流隔板52和径扩机匣2所用材质的膨胀系数存在明显差异,且导流隔板52的膨胀系数大于径扩机匣2的膨胀系数,随着发动机转速的升高,零件温度会随之上升,导流隔板52和径扩机匣2之间径向间隙实现密封,叶轮背腔形成径向内流引气形式,科氏力加速引气气流周向速度,降低离心叶轮1背腔风阻功耗和引气温升,提高离心叶轮1背腔气流的径向压降,防止该轴向力与离心叶轮1气动力差值过大;导流隔板52外径与离心叶轮1出口根部半径相同,且导流隔板52的内径约为外径的50%~70%,沿图3所标记旋转轴方向,将导流隔板52从右向左投影,投影面呈圆环形状,该圆环内圈直径约为外圈直径的50%~70%。
44.请参照图7,图示为发动机处于低转速状态时,离心叶轮1背腔引流的情况,径扩机匣2和o型密封圈51间存在径向间隙,离心叶轮1背腔引气通过此径向间隙后穿过通孔5a,在离心叶轮1背腔旋转侧形成径向外流,增加腔压,增大发动机转子向前轴向力,解决低转速状态下转子轴向力向后的轻载、反向问题。
45.请参照图8,图示为发动机处于高转速状态时,离心叶轮1背腔引流的情况,当发动机处于高转速时,零件温度高达400℃,受合金热膨胀机理影响,导流隔板52产生更大的膨胀,使得位于导流隔板52顶部的o型密封圈51外缘与径扩机匣2间的冷态间隙封闭,导流隔板52与径扩机匣2间的内引气通道6a径向间隙呈闭合状态,离心叶轮1背腔引气沿外引气通道6b形成单一的径向内流,可提高叶轮背腔旋流系数,降低腔压,解决发动机在高转速状态下高压转子向前轴向力过大问题。
46.表一:gh696线膨胀系数
[0047][0048]
请参照表一,示出了《中国航空材料手册》第2卷公开的gh696线膨胀系数示意图,本发明在有限元计算分析中,导流隔板52采用高膨胀系数的gh696材料,进行对比分析。
[0049]
表二:gh903线膨胀系数
[0050][0051]
请参照表二,示出了《中国航空材料手册》第2卷公开的gh903线膨胀系数示意图,本发明在有限元计算分析中,径扩机匣2采用低膨胀系数的gh696材料,进行计算。
[0052]
请参照图9,示出了以径向变形量数据为纵坐标的分析图,通过有限元计算,得出在发动机处于高转速状态下,径扩机匣2径向变形量为0.51mm,导流隔板52径向变形量为1.1mm,导流隔板52的径向变形大于径扩机匣2的径向变形。
[0053]
请参照图10,示出了发动机处于高转速状态下,结构有限元分析的径向变形量局部放大示意图。
[0054]
表三:有限元变形计算结果
[0055]
位置材料半径mm400℃径向变形mm径扩机匣gh9032100.51导流隔板gh696209.551.1间隙差0.45-0.59
[0056]
请参照表三,示出了径扩机匣2和导流隔板52在400℃下的有限元变形分析图,径
扩机匣2与导流隔板52初始冷态径向间隙为0.45mm,从图9有限元分析中得出径扩机匣2和导流隔板52径向变形数据后,得知二者径向间隙差较冷态条件降低了0.59mm,在发动机最大状态下径扩机匣2和导流隔板52上o型密封圈51之间的径向缝隙可以达到过盈密封的状态,从而实现离心叶轮1背腔引气从径向外流向径向内流的切换。
[0057]
表四:叶轮背腔轴向力结果(kgf,方向向后为正)
[0058][0059]
请参照表四,示出了现有常规技术方案和本发明的离心叶轮1背腔轴向力对比分析图,常规叶轮背腔引气技术方案只能是径向内流引气或者径向外流引气的其中一种,采用本发明技术方案,发动机在地慢等小状态下为径向外流引气方案,该状态下较常规径向内流引气可增加高压转子向前的轴向力116kgf,对于解决带离心叶轮结构发动机在地慢等小状态下转子轴向力的轻载、反向问题具有显著的作用,当发动机转速上推最大时,受径扩机匣2和导流隔板52之间径向膨胀变形差的影响,切换到径向内流引气形式,可降低发动机转子向前的轴向力937kgf,解决发动机在高转速状态下高压转子向前轴向力过大的问题。
[0060]
图11示出了现有技术的发动机慢车状态常规径向内流引气下的叶轮背腔各位置的旋流系数分布状况,图中k代表旋流系数;
[0061]
图12示出了根据本发明实施例的发动机慢车状态下,径扩机匣和导流隔板存在径向间隙,叶轮背腔形成径向外流引气形式的叶轮背腔各位置的旋流系数分布状况,图中k代表旋流系数;
[0062]
通过对比图11和图12中结构各位置的旋流系数,相较于常规技术方案,采用本技术方案的离心叶轮背腔旋流控制技术组件,在发动机处于慢车状态下,离心叶轮1背腔旋流系数较低,因此其向前的轴向力较大;
[0063]
另外,通过图11与图12间的对比,证明了叶轮背腔径向外流和径向内流引气之间旋流系数和径向压降差别,与表4中所示叶轮背腔轴向力数据形成对应。(对应表4的数据结果)
[0064]
图13示出了现有技术的发动机处于慢车状态时,常规径向内流引气形式下的叶轮背腔各位置的静压系数分布图,图中,cp代表静压系数。
[0065]
图14示出了根据本发明实施例的发动机处于慢车状态时,常规径向外流引气形式下的叶轮背腔各位置的静压系数分布图,图中,cp代表静压系数。
[0066]
通过对比图13和图14中结构各位置的静压系数,相较于常规技术方案,采用本技术方案的离心叶轮背腔旋流控制技术组件,在发动机处于慢车状态下,离心叶轮1背腔静压
系数较大,进一步说明,通过采用本技术方案,可有效解决带离心叶轮结构发动机在地慢等小状态下转子轴向力的轻载、反向问题。
[0067]
本发明通过有限元计算分析,证实了通过采用本技术方案,在进行结构优化设计的同时,利用径扩机匣2和导流隔板52的线膨胀系数差异,克服了常规径向内流可能带来的发动机地慢等小状态转子轴向力轻载、反向问题,以及常规径向外流带来的高转速大状态下发动机转子轴向力过大、甚至超出轴承许用荷载的问题,实现了发动机转子轴向力随转速变化的自适应调节,具备低转速下实现径向外流增加发动机转子向前的轴向力,高转速下切换到径向内流减小高压转子向前轴向力的优势,有效地克服了带离心叶轮结构发动机常见的转子轴向力问题,在实际应用中,所选择高膨胀以及低膨胀材料需结合实际情况进行考虑。
[0068]
尽管参照前述实施例对本发明进行了详细的说明,本领域的普通技术人员应当理解:其依然可以对前述各实施例所记载的技术方案进行修改,或者对其中部分技术特征进行等同替换;而这些修改或者替换,并不使相应技术方案的本质脱离本发明各实施例技术方案的精神和范围。