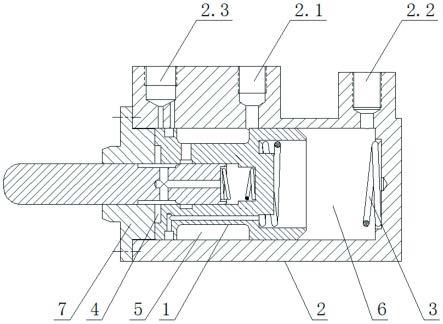
1.本发明涉及拖拉机或其他机动车用助力制动泵技术领域,具体涉及一种助力制动泵残压卸载结构。
背景技术:2.拖拉机或其他机动车辆制动器内的制动液压油处在密闭环境中,在某些特殊条件下,制动器会存在残余压力;如在夏季高温季节,制动液压油受热膨胀,致使制动器内出现残余正压力,又如在冬季寒冷季节,制动液压油遇冷收缩,致使制动器内出现残余负压力(制动液压油不足);此残余压力如不能及时消除,会导致制动钳活塞回位不彻底,从而使拖拉机或其他机动车辆的摩擦片长时间处于摩擦状态,这不仅增加了使拖拉机或其他机动车辆输出功率的无效损耗,还会使摩擦片厚度变薄、制动器间隙增大而影响制动可靠性和制动效能;因此在不同季节需人工检查制动机构内制定液压油的残余压力情况,释放残余正压力或补充制动液压油,因此增加了拖拉机或其他机动车辆维护保养的工作量,如果对制动器维护保养工作进行不到位,则会使拖拉机或其他机动车辆的制动性能存在重大安全事故隐患。
技术实现要素:3.为了克服背景技术中的不足,本发明公开了一种助力制动泵残压卸载结构,包括柱塞组件、助力制动泵壳体;助力制动泵壳体上的回油口设有回油阻尼孔、泄压孔,回油口通过回油阻尼孔、泄压孔与助力制动泵壳体的内孔连通;柱塞组件包括动力柱塞、控制柱塞,控制柱塞滑动设置在动力柱塞的控制柱塞孔中,其中动力柱塞外圆面上设有泄压环槽,动力柱塞侧壁沿轴向设有泄压油道,泄压油道与泄压环槽通过径向设置的通孔连通,构成泄压通道;柱塞组件滑动设置在助力制动泵壳体的内孔中,通过柱塞组件在助力制动泵壳体内孔中滑动,将制动油泵入驱动制动器进行制动;当柱塞组件处于原始位置时,制动器通过泄压通道与制动泵壳体上的回油口连通,因此当制动器内存在残余压力时,残余压力通过泄压通道从回油口自动释放,从而减小了拖拉机或其他机动车辆维护保养的工作量。
4.为了实现所述发明目的,本发明采用如下技术方案:一种助力制动泵残压卸载结构,包括柱塞组件、助力制动泵壳体;所述助力制动泵壳体上设有压力油入口、制动油出口、回油口,压力油入口、制动油出口、回油口与助力制动泵壳体的内孔连通;其中回油口设有回油阻尼孔、泄压孔,回油口通过回油阻尼孔、泄压孔与助力制动泵壳体的内孔连通,其中回油阻尼孔直径为1.0-2.0mm,泄压孔直径为0.3-0.5mm;柱塞组件包括动力柱塞、控制柱塞;
5.动力柱塞中间设有控制柱塞孔,控制柱塞孔为盲孔;控制柱塞孔内圆面上设有动力柱塞内环槽,外圆面上设有动力柱塞外环槽、泄压环槽,动力柱塞外环槽与动力柱塞内环槽通过径向设置的若干通孔连通,动力柱塞侧壁沿轴向设有泄压油道,泄压油道与泄压环槽通过径向设置的通孔连通,构成残压泄放通道;控制柱塞外圆周上设有控制柱塞环槽;
6.控制柱塞滑动设置在动力柱塞的控制柱塞孔中,柱塞组件滑动设置在助力制动泵壳体的内孔中,助力制动泵壳体左端固定设置有端盖,控制柱塞穿过端盖延伸至外部;柱塞组件将助力制动泵壳体内孔分割为高压油腔、环槽腔、制动油腔;
7.助力制动泵残压卸载结构在非工作状态下,压力油入口与回油口处于非连通状态,具体参见说明书附图1;当制动泵工作时,通过脚踏板推动控制柱塞在动力柱塞中滑动,控制柱塞环槽将高压油腔、环槽腔连通,通过压力油入口进入助力制动泵中的液压油进入高压油腔中,推动柱塞组件运动,将制动油腔中的制动油泵入制动器中,实现拖拉机或机动车辆的制动控制;当制动结束,柱塞组件回归原位时,如果制动器内存在残余压力时,残余压力通过制动油腔、残压泄放通道、泄压孔,最终从回油口释放。
8.优选的,柱塞组件还包括动力柱塞堵头;动力柱塞中间的控制柱塞孔为台阶状通孔,其中大孔段为堵头连接孔;动力柱塞堵头固定设置在堵头连接孔中,使控制柱塞孔形成盲孔结构。
9.优选的,控制柱塞位于控制柱塞孔的端部设有防脱挡环,防脱挡环用于防止控制柱塞从制动泵端盖侧脱出。
10.进一步的,动力柱塞与控制柱塞之间设置有控制柱塞复位弹性元件。
11.进一步的,动力柱塞与助力制动泵壳体之间设置有柱塞组件复位弹性元件。
12.进一步的,控制柱塞复位弹性元件、柱塞组件复位弹性元件为螺旋压簧或开槽蝶形簧片组。
13.进一步的,控制柱塞内部设有控制柱塞油孔,控制柱塞油孔与控制柱塞环槽之间通过径向设置的若干通孔连通。
14.进一步的,动力柱塞的控制柱塞孔底部设有动力柱塞油孔;动力柱塞堵头上设有堵头油孔。
15.由于采用如上所述的技术方案,本发明具有如下有益效果:本发明公开的一种助力制动泵残压卸载结构,包括柱塞组件、助力制动泵壳体;助力制动泵壳体上的回油口设有回油阻尼孔、泄压孔,回油口通过回油阻尼孔、泄压孔与助力制动泵壳体的内孔连通;柱塞组件包括动力柱塞、控制柱塞,控制柱塞滑动设置在动力柱塞的控制柱塞孔中,其中动力柱塞外圆面上设有泄压环槽,动力柱塞侧壁沿轴向设有泄压油道,泄压油道与泄压环槽通过径向设置的通孔连通,构成泄压通道;柱塞组件滑动设置在助力制动泵壳体的内孔中,通过柱塞组件在助力制动泵壳体内孔中滑动,将制动油泵入驱动制动器进行制动;当柱塞组件处于原始位置时,制动器通过泄压通道与制动泵壳体上的回油口连通,因此当制动器内存在残余压力时,残余压力通过泄压通道从回油口自动释放,从而减小了拖拉机或其他机动车辆维护保养的工作量,并且从根本上彻底解决了因制动器维护保养工作进行不到位而存在的重大安全事故隐患问题。
附图说明
16.图1为实施例一助力制动泵残压卸载结构结构示意图;
17.图2为实施例一柱塞组件结构示意图;
18.图3为实施例一动力柱塞结构示意图;
19.图4为实施例一控制柱塞结构示意图;
20.图5为助力制动泵壳体结构示意图;
21.图6为实施例一的控制柱塞工作状态示意图;
22.图7为实施例一的柱塞组件工作状态示意图;
23.图8为施例二助力制动泵残压卸载结构结构示意图;
24.图9为实施例二柱塞组件结构示意图;
25.图10为实施例二动力柱塞结构示意图;
26.图11为实施例二控制柱塞结构示意图;
27.图12为实施例二动力柱塞堵头结构示意图;
28.图13为实施例二的控制柱塞工作状态示意图;
29.图14为实施例二的柱塞组件工作状态示意图;
30.图15为施例三助力制动泵残压卸载结构结构示意图;
31.图16为实施例三柱塞组件结构示意图;
32.图17为实施例三动力柱塞结构示意图;
33.图18为实施例三控制柱塞结构示意图;
34.图19为实施例三的控制柱塞工作状态示意图;
35.图20为实施例三的柱塞组件工作状态示意图;
36.图21为实施例四助力制动泵残压卸载结构结构示意图;
37.图22为实施例四柱塞组件结构示意图;
38.图23为实施例四控制柱塞结构示意图;
39.图24为实施例四动力柱塞堵头结构示意图;
40.图25为实施例四的控制柱塞工作状态示意图;
41.图26为实施例四的柱塞组件工作状态示意图。
42.图中:1、柱塞组件;1.1、动力柱塞;1.1.1、控制柱塞孔;1.1.2、动力柱塞外环槽;1.1.3、动力柱塞内环槽;1.1.4、动力柱塞油孔;1.1.5、泄压油道;1.1.6、泄压环槽;1.1.7、堵头连接孔;1.2、控制柱塞;1.2.1、控制柱塞环槽;1.2.2、控制柱塞油孔;1.2.3、防脱挡环;1.3、动力柱塞堵头;1.3.1、堵头油孔;1.4、控制柱塞复位弹性元件;2、助力制动泵壳体;2.1、压力油入口;2.2、制动油出口;2.3、回油口;2.3.1、回油阻尼孔;2.3.2、泄压孔;3、柱塞组件复位弹性元件;4、高压油腔;5、环槽腔;6、制动油腔;7、端盖。
具体实施方式
43.通过下面的实施例可以详细的解释本发明,公开本发明的目的旨在保护本发明范围内的一切技术改进。
44.实施例一:
45.一种助力制动泵残压卸载结构,包括柱塞组件1、助力制动泵壳体2;所述助力制动泵壳体2上设有压力油入口2.1、制动油出口2.2、回油口2.3,压力油入口2.1、制动油出口2.2、回油口2.3与助力制动泵壳体2的内孔连通,其中回油口2.3通过直径1.0mm回油阻尼孔2.3.1和直径为0.5mm的泄压孔2.3.2与助力制动泵壳体2的内孔连通;
46.所述柱塞组件1包括动力柱塞1.1、控制柱塞1.2;在该实施例中,动力柱塞1.1、控制柱塞1.2结构及两者之间的装配关系参见说明书附图2、3、4;
47.动力柱塞1.1中间设有控制柱塞孔1.1.1,左侧端面设有台阶孔,控制柱塞孔1.1.1为盲孔;控制柱塞孔1.1.1内圆面上设有动力柱塞内环槽1.1.3,外圆面上设有动力柱塞外环槽1.1.2、泄压环槽1.1.6,动力柱塞外环槽1.1.2与动力柱塞内环槽1.1.3通过径向设置的四个通孔连通,动力柱塞1.1侧壁沿轴向设有泄压油道1.1.5,泄压油道1.1.5与泄压环槽1.1.6通过一个径向设置的通孔连通,构成残压泄放通道;控制柱塞1.2外圆周上设有控制柱塞环槽1.2.1,控制柱塞1.2内部设有控制柱塞油孔1.2.2,控制柱塞油孔1.2.2与控制柱塞环槽1.2.1之间通过径向设置的四个通孔连通;
48.控制柱塞1.2滑动设置在动力柱塞1.1的控制柱塞孔1.1.1中,构成柱塞组件1;为保证控制柱塞1.2在工作过程中复位可靠,在控制柱塞1.2的右端面与动力柱塞1.1的控制柱塞孔1.1.1底部之间,设置有柱塞复位弹性元件1.4,柱塞复位弹性元件1.4可以采用螺旋压簧或开槽蝶形簧片组,或其他弹性元件;
49.柱塞组件1滑动设置在助力制动泵壳体2的内孔中,助力制动泵壳体2左端固定设置有端盖7,控制柱塞1.2穿过端盖7延伸至助力制动泵外部;动力柱塞1.1左侧端面的台阶孔与端盖7内侧面构成高压油腔4,动力柱塞1.1的动力柱塞外环槽1.1.2与助力制动泵壳体2的内孔壁构成环槽腔5,动力柱塞1.1右端面与助力制动泵壳体2的内孔底部构成制动油腔6;为保证柱塞组件1在工作过程中复位可靠,在动力柱塞1.1右端面与助力制动泵壳体2的内孔底部之间,设置有柱塞组件复位弹性元件3,柱塞组件复位弹性元件3可以采用螺旋压簧或开槽蝶形簧片组,或其他弹性元件;助力制动泵残压卸载结构在未工作状态下(柱塞组件1位于最左端),制动油腔6通过残压泄放通道、泄压孔2.3.2与回油口2.3连通;
50.助力制动泵残压卸载结构在未工作状态下,控制柱塞1.2将动力柱塞内环槽1.1.3关闭,此时高压油腔4与压力油入口2.1阻断,液压油无法进入高压油腔4,柱塞组件1保持不动;当拖拉机或其他机动车辆制动时,踏下制动踏板,制动踏板推动控制柱塞1.2向右滑动,此时控制柱塞环槽1.2.1将高压油腔4与环槽腔5连通,参见说明书附图6;高压油腔4与环槽腔5连通后,压力油入口2.1连接的液压油进入高压油腔4,少量液压油经过回油阻尼孔回流至储油箱中,因回油阻尼孔直径较小(1.0mm),高压油腔维持高压状态,驱动动力柱塞工作,液压油推动柱塞组件1向右滑动,将制动油腔6中的制动油通过制动油出口2.2泵入制动器中,对拖拉机或其他机动车辆进行制动控制,具体参见说明书附图7;
51.在控制柱塞1.2向右滑动过程中,控制柱塞1.2与动力柱塞1.1之间封闭空间的液压油,通过控制柱塞油孔1.2.2进入高压油腔4;在制动结束后,制动踏板对控制柱塞1.2的推力消失,此时控制柱塞1.2与动力柱塞1.1之间封闭空间与高压油腔4连通,因此控制柱塞1.2与动力柱塞1.1之间封闭空间的液压油仍维持高压状态,高压液压油推动控制柱塞1.2向左滑动复位,直至切断高压油腔4、环槽腔5的连通;当高压油腔4、环槽腔5之间的连通被切断后,高压油腔4的压力消失,此时制动油腔6与制动器相连通,因此制动油腔6的制动油维持高压状态,高压制动油推动柱塞组件1向左滑动,制动油腔6中制动油压力下降,结束制动器的制动;在助力制动泵残压卸载结构中,控制柱塞复位弹性元件1.4用于确保控制柱塞1.2的可靠复位,柱塞组件复位弹性元件3用于确保柱塞组件1的可靠复位;
52.当制动结束,柱塞组件1回归原位后,如果制动器内存在残余压力时,残余压力通过制动油腔6、残压泄放通道、泄压孔2.3.2,最终从回油口2.3自动释放,从而省去了人工对拖拉机或其他机动车辆制动系统维护保养的工作量。
53.实施例二:
54.具体参见说明书附图8-14;在该实施例中,柱塞组件1还包括动力柱塞堵头1.3;动力柱塞1.1中间的控制柱塞孔1.1.1为台阶状通孔,其中大孔段为堵头连接孔1.1.7;柱塞堵头1.3通过螺纹连接或焊接固定设置在堵头连接孔1.1.7中,采用动力柱塞堵头1.3的结构设计,可将动力柱塞1.1设计为台阶状通孔,方便控制柱塞孔1.1.1进行磨削加工;
55.在该实施例中,助力制动泵残压卸载结构的工作过程、与制动器残余压力的释放过程与实施例一相同。
56.实施例三:
57.具体参见说明书附图15-20;该实施例与实施例一相比,取消了控制柱塞1.2内部的控制柱塞油孔1.2.2,在动力柱塞1.1的控制柱塞孔1.1.1底部增加了动力柱塞油孔1.1.4;在控制柱塞1.2向右滑动过程中,控制柱塞1.2与动力柱塞1.1之间封闭空间的液压油,通过控制柱塞孔1.1.1底部的动力柱塞油孔1.1.4进入制动油腔6;在制动结束后,制动踏板对控制柱塞1.2的推力消失,此时控制柱塞1.2与动力柱塞1.1之间封闭空间与制动油腔6连通,因此控制柱塞1.2与动力柱塞1.1之间封闭空间的液压油仍维持高压状态,高压液压油推动控制柱塞1.2向左滑动复位,直至切断高压油腔4、环槽腔5的连通;当高压油腔4、环槽腔5之间的连通被切断后,高压油腔4的压力消失,此时制动油腔6与制动器相连通,因此制动油腔6的制动油维持高压状态,高压制动油推动柱塞组件1向左滑动,制动油腔6中制动油压力下降,结束制动器的制动;在助力制动泵残压卸载结构中,控制柱塞复位弹性元件1.4用于确保控制柱塞1.2的可靠复位,柱塞组件复位弹性元件3用于确保柱塞组件1的可靠复位;在该实施例中,制动器内存在残余压力的释放与实施例一相同。
58.实施例四:
59.该实施例与实施例二相比,控制柱塞1.2位于控制柱塞孔1.1.1的端部增加设有防脱挡环1.2.3,相应的动力柱塞1.1中间的控制柱塞孔1.1.1设有相应的挡边台阶孔,此种结构设计可防止控制柱塞1.2从制动泵中脱出;在此结构设计中,防脱挡环1.2.3的外圆与挡边台阶孔的内圆之间设有间隙,防止控制柱塞1.2的防脱挡环与动力柱塞1.1的挡边台阶孔之间出现困油现象,而导致控制柱塞1.2出现滑动阻力偏大的问题;在该实施例中,助力制动泵残压卸载结构的工作过程与制动器残余压力的释放过程与实施例二相同。
60.本发明未详述部分为现有技术。