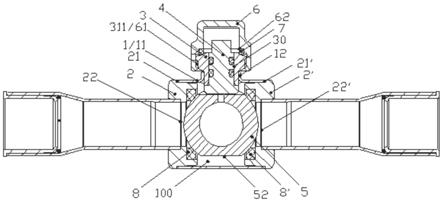
1.本发明涉及流体控制技术领域,具体涉及一种球阀。
背景技术:2.图1为背景技术中一种球阀的局部结构示意图。如图1所示,球阀包括壳体01、阀杆02和定位销03,壳体01的上端设有限位凸台011,定位销03横向穿设于阀杆02,通过定位销03与限位凸台011抵接,能够限制阀杆02的周向移动行程。背景技术的球阀,依靠定位销03与限位凸台011的配合止动,定位销03一般通过手工压入阀杆02的定位销孔021,定位销孔021的尺寸精度要求高,阀杆02的加工难度较大。
3.有鉴于此,如何降低阀杆的加工难度是本领域技术人员持续关注的技术问题。
技术实现要素:4.本发明的目的是提供一种球阀,包括壳体、阀杆套、阀杆、阀芯,所述壳体与所述阀杆套固定连接,所述阀芯设于所述壳体球阀的内腔;所述阀杆包括杆部、键部和径向凸出部,所述杆部至少部分位于所述阀杆套的轴向通孔,所述键部至少部分位于所述阀芯的凹槽,所述阀杆能够带动所述阀芯转动,所述径向凸出部自所述键部朝径向凸出,所述径向凸出部凸出于所述杆部;所述阀杆套的下段包括轴向限位部和径向限位部,所述径向凸出部能够与所述径向限位部抵接限制所述阀杆的转动行程,所述径向凸出部能够与所述轴向限位部抵接限制所述阀杆轴向向上脱出。
5.本发明所提供的球阀,包括阀杆套、阀杆和阀芯,阀杆包括杆部、键部和径向凸出部,杆部至少部分位于阀杆套的轴向通孔,键部至少部分位于阀芯的凹槽,径向凸出部自键部朝径向凸出,径向凸出部凸出于杆部;阀杆套的下段包括轴向限位部和径向限位部,径向凸出部能够与径向限位部抵接限制阀杆的转动行程,径向凸出部能够与轴向限位部抵接限制阀杆轴向向上脱出。本方案优化了球阀的止动结构,相对于背景技术取消了定位销,无需加工定位销孔,降低了阀杆的加工难度。
附图说明
6.图1:背景技术中一种球阀的局部结构示意图;
7.图2:本发明提供的一种球阀的剖面示意图;
8.图3a:图2中阀杆套的结构示意图;
9.图3b:图3a中阀杆套的倒置示意图;
10.图4:图2中阀杆的结构示意图;
11.图5:图2中阀杆与阀杆套的配合示意图;
12.图6:图2中阀芯的结构示意图;
13.图7:图2中阀杆、阀杆套和阀芯的配合示意图;
14.图8:图7中i处的放大示意图;
15.图9:另一种阀杆的结构示意图;
16.图10:图9中杆件的结构示意图;
17.图11:图9中连接件的结构示意图。
18.图2至图11中:
19.1-壳体、100-内腔;
20.11-本体部、12-伸出部;
21.2-第一阀座、21-第一台阶部;
[0022]2’-
第二阀座、21
’-
第二台阶部;
[0023]
22-流路进口、22
’-
流路出口;
[0024]
3-阀杆套、30-轴向通孔;
[0025]
31-大径段、32-小径段、321-下端部;
[0026]
311-外螺纹部、312-第一锥部、313-第二锥部;
[0027]
33-轴向凸出部、331-第一侧壁、332-第二侧壁;
[0028]
4/4
’-
阀杆、41-杆部、42-键部;
[0029]
41'-杆件、411'-定位孔、412
’-
横槽;
[0030]
42'-连接件、421
’-
凸台、422
’-
定位杆;
[0031]
43-径向凸出部;
[0032]
5-阀芯、51-凹槽、511-凹槽底、52-平台部;
[0033]
6-阀帽、61-内螺纹部、62-内台阶部;
[0034]
7-密封圈、8-第一密封垫、8
’-
第二密封垫。
具体实施方式
[0035]
本发明的核心是提供一种球阀,包括阀杆套、阀杆和阀芯,阀杆包括杆部、键部和径向凸出部,杆部至少部分位于阀杆套的轴向通孔,键部至少部分位于阀芯的凹槽,径向凸出部自键部朝径向凸出,径向凸出部凸出于杆部;阀杆套的下段包括轴向限位部和径向限位部,径向凸出部能够与径向限位部抵接限制阀杆的转动行程,径向凸出部能够与轴向限位部抵接限制阀杆轴向向上脱出。本方案优化了球阀的止动结构,相对于背景技术取消了定位销,无需加工定位销孔,降低了阀杆的加工难度。
[0036]
为了使本技术领域的人员更好地理解本发明方案,下面结合附图和具体实施方式对本发明作进一步的详细说明。
[0037]
这里需要说明的是,本文中所涉及的上和下等方位词是以图2至图11中零部件位于图中及零部件相互之间的位置来定义的,只是为了表达技术方案的清楚及方便。应当理解,本文所采用的方位词不应限制本技术请求保护的范围。
[0038]
图2为本发明提供的一种球阀的剖面示意图;图3a为图2中阀杆套的结构示意图;图3b为图3a中阀杆套的倒置示意图;图4为图2中阀杆的结构示意图;图5为图2中阀杆与阀杆套的配合示意图;图6为图2中阀芯的结构示意图;图7为图2中阀杆、阀杆套和阀芯的配合示意图;图8为图7中i处的放大示意图。
[0039]
如图2至图8所示,球阀包括壳体1、第一阀座2、第二阀座2’、阀杆套3、阀杆4和阀芯5。壳体1为管状,包括本体部11和凸出部12,凸出部12从本体部11的周向外壁凸出。具体的,
本体部11由不锈钢管材或板材冲压拉伸成型,凸出部12在本体部11的基础上冲孔翻边拉伸成型。
[0040]
第一阀座2与第二阀座2’由不锈钢型材通过锻造成型,阀芯5位于第一阀座2与第二阀座2’之间,第一阀座2的外周壁包括第一台阶部21,第二阀座2’的外周壁包括第二台阶部21’,第一台阶部21与第二台阶部21’相向设置,即第一台阶部21的台阶面与第二台阶部21’的台阶面相对。壳体1的一端置于第一台阶部21,壳体1的另一端置于第二台阶部21’,第一阀座2、第二阀座2’与壳体11焊接固定。第一阀座2包括流路进口22,第二阀座2’包括流路出口22’,第一阀座2与阀芯5之间设有第一密封垫8,第二阀座2’与阀芯5之间设有第二密封垫8’。
[0041]
阀杆套3大致呈圆环状,通过不锈钢型材车加工成型。阀杆套3包括轴向延伸的轴向通孔30,阀杆4贯穿该轴向通孔30,阀杆4与阀芯5键槽连接,阀杆4能够带动阀芯5转动。阀杆套3包括上段和下段,本实施例中,上段为大径段31,下段为小径段32,大径段31的外径大于小径段32的外径。大径段31作为上段,小径段32作为下段,小径段32至少部分位于壳体1的凸出部12内,小径段32的外壁与凸出部12的内壁焊接固定。小径段32包括下端部321和自下端部321轴向向下凸出的轴向凸出部33,该轴向凸出部33包括第一侧壁331和第二侧壁332,第一侧壁331所在的平面和第二侧壁332所在的平面形成的夹角为90度,轴向凸出部33为2个,且相对于轴向通孔30的中心轴线对称设置。本实施例中,小径段32的下端部321作为轴向限位部,轴向凸出部33作为径向限位部。
[0042]
阀杆4为不锈钢棒料一体车加工制成,包括杆部41、键部42和径向凸出部43,键部42位于杆部41的下方。杆部41为圆柱状,杆部41贯穿阀杆套3的轴向通孔30,杆部41至少部分位于轴向通孔30。键部42至少部分位于阀芯5的凹槽51,阀杆4转动能够带动阀芯5转动。径向凸出部43自键部42朝径向凸出,径向凸出部43凸出于杆部41的外周壁,径向凸出部43能够与轴向凸出部33(径向限位部)的第一侧壁331或第二侧壁332抵接以限制阀杆4的转动行程,径向凸出部43能够与小径段32的下端部321(轴向限位部)抵接以限制阀杆4轴向向上脱出。
[0043]
本实施方案,通过在阀杆套3的下段设置轴向限位部和径向限位部,阀杆4包括杆部41、键部42和径向凸出部43,杆部41至少部分位于阀杆套3的轴向通孔30,键部42至少部分位于阀芯5的凹槽51,径向凸出部43凸出于杆部41的外周壁,径向凸出部43能够与轴向凸出部33(径向限位部)的第一侧壁331或第二侧壁332抵接以限制阀杆4的转动行程,径向凸出部43能够与小径段32的下端部321(轴向限位部)抵接以限制阀杆4轴向向上脱出。本方案优化了球阀的止动结构,相较于背景技术取消了定位销,阀杆4无需加工定位销孔,其有益效果在于,降低了阀杆的加工难度;另一方面,能够缩短阀杆4的长度,利于实现小型化。
[0044]
进一步的,如图2、图3a、图3b所示,球阀还包括阀帽6和密封圈7。阀杆套3的大径段31的外壁包括外螺纹部311,阀帽6的内壁包括内螺纹部61,通过外螺纹部311与内螺纹部61螺合使得阀帽6与阀杆套3固定连接。大径段31的上段包括第一锥部312,第一锥部312朝远离阀芯5方向外径渐小,即其锥面大致朝阀帽6方向。阀帽6还包括台阶面朝下的内台阶部62,密封圈7位于内台阶部62与第一锥部312之间,通过拧紧阀帽6,将密封圈7挤压于第一锥部312,提高了球阀的密封性能。
[0045]
进一步的,大径段31的下段包括第二锥部313,第二锥部313朝远离阀芯5方向外径
渐大,即其锥面大致朝阀芯5方向。如此,通过设置第二锥部313,在球阀制造过程中,焊环(未示出)容易沿第二锥部313的锥面卡入壳体1的凸出部12的上端与第二锥部313之间,便于安装焊环,提高生产效率。
[0046]
图9为另一种阀杆的结构示意图;图10为图9中杆件的结构示意图;图11为图9中连接件的结构示意图。
[0047]
如图9、图10、图11所示,阀杆也可以设置成分体结构。阀杆4’包括杆件41’和连接件42’,杆部41设于杆件41’,键部42和径向凸出部43设于连接件42’。具体的,杆件41’下段设置横槽412’,连接件42’上段设置凸台422’,杆件41’与连接件42’通过横槽412’与凸台422’配合连接,杆件41’能够带动连接件42’转动。进一步,为使杆件41’与连接件42’配合定位更可靠,杆件41’还开设有轴向的定位孔411’,相应的,连接件42’上段设有定位杆421’,定位杆421’位于定位孔411’。本实施方案中,杆件41’由不锈钢棒料车加工制成,连接件42’由金属粉末冶金一体制成。如此设计,相比上述实施例中阀杆一体车加工方案,本实施例的方案能够降低材料成本。
[0048]
本实施例中,如图7、图8所示,凹槽51的凹槽底511设置为平底结构,相应的,与其配合的阀杆4的键部42也设置为平底结构,即键部42为平底。如此设置,球阀在关阀状态下,有利于阀芯5在流体压差作用下朝流路出口22’侧位移,从而压紧第二密封垫8’以提高密封性;另一方面,使阀芯5不易产生晃动,不会因阀芯5晃动划伤与其配合的第一密封垫8和第二密封垫8’,能够提高第一密封垫8和第二密封垫8’的使用寿命。
[0049]
更进一步,如图8所示,本实施例中,键部42与凹槽51的凹槽底511之间设有间隙a,定义键部42伸入凹槽51的尺寸为b,则满足a≤b/2。如此设置,能够提高球阀开关阀时的动作可靠性。
[0050]
如图2所示,阀芯5的下段具有平台部52,平台部52位于第一密封垫8与第二密封垫8’之间。如此,一方面降低了阀芯5的材料成本、减少了阀芯5的重量,另一方面,阀芯5的高度降低便于阀芯5装入壳体1内,也有利于降低球阀整体的高度,实现小型化。
[0051]
本文中应用了具体个例对本发明的原理及实施方式进行了阐述,以上实施例的说明只是用于帮助理解本发明的方法及其核心思想。应当指出,对于本技术领域的普通技术人员来说,在不脱离本发明原理的前提下,还可以对本发明进行若干改进和修饰,这些改进和修饰也落入本发明权利要求的保护范围内。