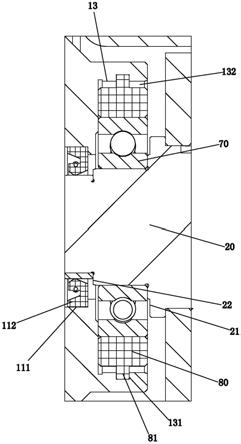
1.本实用新型涉及一种太阳轮能浮动的减速器电机。
背景技术:2.当前,电机减速器一体化中主要采用将电机的前法兰也作为减速器的前壳体的一部分,故电机轴的前轴承的轴承座位于减速器前壳体上,此种轴承座的结构形式目前主要为两种:1.将减速器前壳体直接作为轴承座,与前轴承做紧配合,前轴承作为太阳轮支撑,此为刚性连接。目前由于不可避免的加工精度误差以及装配精度误差,造成减速器中内齿圈、行星轮、行星架、输出轴的位置偏差,结合机械运转时发热带来的膨胀量,将会使太阳轮随之产生位置偏差,而由于前轴承的刚性安装,太阳轮不随整体偏差浮动,使得在运转过程中太阳轮产生偏心跳动,进而降低齿轮寿命;2.取消了前轴承,使太阳轮完全不受前轴承的束缚随减速器内部整体的位置偏差进行浮动,由于少了前轴承的支撑,此时太阳轮易产生振动,过高的转速下可能会引起太阳轮与行星轮的接触齿面之间的碰撞,造成齿面精度破坏,以及噪音的风险。
技术实现要素:3.本实用新型提供了一种太阳轮能浮动的减速器电机,其克服了背景技术所存在的不足。本实用新型解决其技术问题所采用的技术方案是:
4.一种太阳轮能浮动的减速器电机,包括电机和减速机构,所述电机设置有电机轴;所述电机靠近减速机构的一侧设置有第一轴承座,所述第一轴承座内安装有用于支撑电机轴的第一轴承;所述第一轴承和第一轴承座之间安装有浮动件;所述第一轴承座内周壁设有凹槽,所述第一轴承内圈套置在电机轴外,所述浮动件外侧设有凸台,所述浮动件内侧面贴合在第一轴承外圈且所述凸台卡入凹槽内,所述浮动件外侧面与第一轴承座内周壁之间形成有浮动间隙。
5.一较佳实施例之中,所述浮动件为套环,所述凸台固设在套环外侧面。
6.一较佳实施例之中,所述凸台呈环形且位于浮动件外周壁的中间位置,所述凹槽呈环形且位于第一轴承座内周壁的中间位置。
7.一较佳实施例之中,所述浮动件采用弹性的尼龙材质。
8.一较佳实施例之中,所述减速机构包括行星架、输出轴、内齿圈、行星轮、行星轴和太阳轮,所述太阳轮固定套接在电机轴外,所述行星架与输出轴同步转动连接;内齿圈位于行星轮外侧并与行星轮相啮合配合,所述太阳轮位于行星轮内侧且二者相啮合配合;所述行星轴的一端与行星架相限位配合,另一端与输出轴相限位配合,行星轮外套接在行星轴中部,以使行星架和输出轴都随行星轮绕太阳轮公转。
9.一较佳实施例之中,所述行星架与输出轴为固定连接或一体式结构。
10.一较佳实施例之中,所述电机和减速机构一体化安装在同一壳体内。
11.一较佳实施例之中,所述减速机构还包括第二轴承,所述壳体内还设有第二轴承
座,所述第二轴承套置在输出轴和第二轴承座之间。
12.一较佳实施例之中,所述减速机构还包括第三轴承,所述壳体内还设有第三轴承座,所述第三轴承套置在行星架与第三轴承座之间。
13.一较佳实施例之中,所述第一轴承套置在电机轴后端,所述太阳轮固定套接在电机轴前端,所述第二轴承套置在输出轴后端,所述第三轴承套置在行星架后端。本技术方案与背景技术相比,它具有如下优点:
14.1.由于凸台卡入凹槽内,浮动件外侧面与第一轴承座内周壁之间形成浮动间隙,由于加工误差、安装误差以及热膨胀、零件精度等原因使减速机构产生位置偏移时,太阳轮也产生相对的位置偏移量,该偏移量通过电机轴传递至第一轴承处,此时电机轴以凸台与凹槽的配合处作为支点并以跷跷板的形式进行缓冲并抵消该偏移,最终使太阳轮产生浮动,提高了太阳轮的使用寿命。
15.2.浮动件呈套环结构,方便浮动件与第一轴承之间的安装,且不易丢失。
16.3.凸台呈环形且位于浮动件外周的中间位置,凹槽呈环形且位于第一轴承座内周壁的中间位置,使得跷跷板支点位于浮动件外周的中间,既可以保证太阳轮浮动时的稳定,同时凸台不容易从凹槽处脱出。
17.4.浮动件采用弹性的尼龙材质,使得凸台与凹槽之间的装配更加顺畅。
18.5.第一轴承套置在电机轴后端,太阳轮固定套接在电机轴前端,第一轴承和太阳轮同时对电机轴进行限位,又不会使太阳轮容易产生振动,避免太阳轮齿面精度,减少噪声。
附图说明
19.下面结合附图和实施例对本实用新型作进一步说明。
20.图1绘示了一较佳实施例的一种太阳轮能浮动的减速器电机的局部剖视示意图。
21.图2绘示了图1的局部放大示意图。
22.图3绘示了图2的局部放大示意图。
具体实施方式
23.请查阅图1至图3,一种太阳轮能浮动的减速器电机的一较佳实施例,所述的一种太阳轮能浮动的减速器电机,包括电机和减速机构,所述电机设置有电机轴20;所述电机轴20靠近减速机构的一侧设置有第一轴承座13,所述第一轴承座13内安装有用于支撑电机轴20的第一轴承70;所述第一轴承70和第一轴承座13之间安装有浮动件80;所述第一轴承座13内周壁设有凹槽131,所述第一轴承70内圈套置在电机轴20外,所述浮动件80外侧设有凸台81,所述浮动件80内侧面贴合在第一轴承70外圈且所述凸台81卡入凹槽131内,所述浮动件80外侧面与第一轴承座13内周壁之间形成有浮动间隙132。
24.本实施例中,所述凹槽131个数可设为多个且沿着第一轴承座13内周壁环形间隔布置。
25.本实施例中,所述浮动件80为套环,所述凸台81固设在套环外侧面。根据需要,该浮动件80也可为多个独立的t形体,该t形体的突出部为所述的凸台,不以此为限。
26.本实施例中,所述凸台81呈环形且位于浮动件80外周的中间位置,所述凹槽131呈
环形且位于第一轴承座13内周壁的中间位置。或者,凸台81个数可以设为多个且环形间隔布置。且,凸台81的截面形状可以为方形,也可为半圆形、梯形等其他形状。
27.本实施例中,所述浮动件80采用弹性的尼龙材质,或者也可采用其他材质如硅胶、橡胶、金属等,不以此为限。
28.本实施例中,所述电机和减速机构一体化安装在同一壳体内。
29.所述减速机构包括行星架30、输出轴100、内齿圈40、行星轮50、行星轴51和太阳轮60,所述太阳轮60固定套接在电机轴20外,所述行星架30与输出轴100同步转动连接;内齿圈40位于行星轮50外侧并与行星轮50相啮合配合,所述太阳轮60位于行星轮50内侧且二者相啮合配合。所述行星轴51的一端与行星架30相限位配合,另一端与输出轴100相限位配合,行星轮50外套接在行星轴51中部,以使行星架30和输出轴100都随行星轮50绕太阳轮公转。本实施例中,所述行星架30与输出轴100为固定连接;根据需要,所述行星架30与输出轴100也可为一体式结构。内侧是指在径向靠近太阳轮轴线的位置,外侧是指在径向远离太阳轮轴线的位置。
30.本实施例中,还包括第二轴承90,所述壳体内还设有第二轴承座14,所述第二轴承90套置在输出轴100和第二轴承座14之间。
31.本实施例中,还包括第三轴承200,所述壳体内还设有第三轴承座16,所述第三轴承200套置在行星架30与第三轴承座16之间。
32.本实施例中,所述第一轴承70套置在电机轴20后端,所述太阳轮60固定套接在电机轴20前端,所述第二轴承90套置在输出轴100后端,所述第三轴承套置在行星架30后端。
33.本实施例中,所述壳体包括依次连接的后壳体10、前壳体11和前法兰12。本实施例中,后壳体10与前壳体11之间通过螺钉进行锁接,前壳体11与前法兰12之间通过螺钉进行锁接;连接的方式不以此为限,还可以为卡接、扣接等其他连接方式。
34.本实施例中,所述电机轴20安装在后壳体10内且延伸至前壳体11,所述内齿圈40安装在前壳体11上,所述行星轮50、太阳轮60均位于前壳体11,所述输出轴100位于前壳体11且伸出前法兰12,所述第一轴承座13设置在前壳体11后端面,所述第二轴承座14设置在前法兰12后端面,所述第三轴承座16设置在前壳体11前端面。
35.本实施例中,所述电机轴20后端外周设有第一台阶面21,所述第一轴承70位于第一轴承座13和第一台阶面21之间。
36.本实施例中,所述电机轴20后端外周还设有第二台阶面22,所述前壳体11设有穿孔111,所述电机轴20前端穿过该穿孔111后伸入前壳体11与前法兰12之间,另设有第一耐磨垫112,该第一耐磨垫112套置在电机轴20和穿孔111孔壁之间并靠抵在第二台阶面22上。
37.本实施例中,所述前法兰12设有贯孔121,所述输出轴100前端穿过该贯孔121后伸出前法兰12,另设有第二耐磨垫122,该第二耐磨垫122套置在输出轴100和贯孔121孔壁之间。
38.该电机减速器的工作原理为:
39.电机轴20转动,带动太阳轮60同步转动,行星轮40在太阳轮60的啮合作用下产生自转,且行星轮40转动还与内齿圈50产生啮合配合,使行星轮40同时绕太阳轮60公转,行星轮40通过行星轴51带动行星架30和输出轴100绕太阳轮60公转。由于加工误差、安装误差以及热膨胀、零件精度等原因使减速机构产生位置偏移时,太阳轮60也产生相对的位置偏移
量,该偏移量通过电机轴20传递至第一轴承70处,此时电机轴20以凸台81与凹槽131的配合处作为支点并以跷跷板的形式进行缓冲并抵消该偏移,最终使太阳轮60产生浮动,提高了太阳轮60的使用寿命。
40.以上所述,仅为本实用新型较佳实施例而已,故不能依此限定本实用新型实施的范围,即依本实用新型专利范围及说明书内容所作的等效变化与修饰,皆应仍属本实用新型涵盖的范围内。