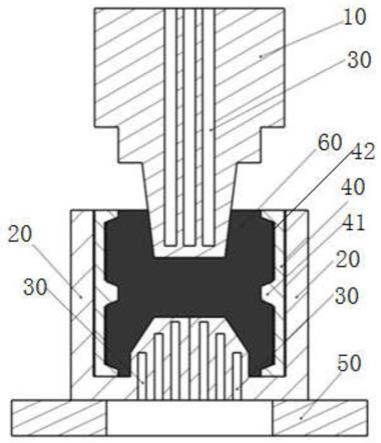
1.本发明涉及一种用于挖掘装载机的自润滑轴套,尤其涉及一种高承载自润滑复合轴套制备方法及装置。
背景技术:2.目前,轴套通常采用合金钢或铜合金等材料直接加工而成,另有粉末冶金轴套通过合金粉末的烧结工艺制备,典型的自润滑轴套比如镶嵌固体润滑剂轴套,镶嵌式石墨铜套自润滑轴套采用的复合材料是一种新型的抗极压固体润滑材料,由金属底材与嵌入底材的孔或槽中的固体润滑剂膏体构成。
3.传统的钢套或合金材料轴套,因不具备自润滑特性,其注脂周期间隔较短。粉末冶金含油轴套存在压溃强度较低,无法承受重载使用工况的缺陷。镶嵌式石墨铜套自润滑轴套由于镶嵌石墨槽较浅,长期恶劣磨损工况下镶嵌式石墨磨损后,其自润滑效果将大打折扣,后期磨损加速。
技术实现要素:4.本发明的目的是提供一种高承载自润滑复合轴套制备方法及装置,将传统轴套材料作为基体,在摩擦表面通过热压固结方法形成厚度大、自润滑效果好的自润滑耐磨涂层,同时提升复合轴套整体抗压溃强度,保证复合轴套在重载工况下具备长时间、高效率自润滑效果。
5.本发明为实现上述发明目的采用如下技术方案:
6.本发明提供了一种高承载自润滑复合轴套的制备方法,包括:
7.按成分配比sic、鳞片状石墨与电解铜粉,称取定量的混合粉末;
8.将预制的凹模安装在工作转台的下方,在凹模中心放入预制的基体,其中所述凹模内部预制有加热体,所述基体在内壁两端面及中部预留凸台,且所述基体在相邻凸台之间加工有凸起;
9.在基体的内环装入定量的混合粉末;
10.将预制的凸模安装在主缸上,并与所述凹模中心对中,其中所述凹模内部预制有加热体;
11.启动凸模与凹模内部的加热体,进入保温状态;
12.定速下行主缸,通过主缸上的凸模对基体内的混合粉末进行热压固结;
13.当主缸运行至设定行程,切换控制方式为定压控制;
14.启动工作转台,主缸面压开始加压,并保压固定时长;
15.停止主缸及工作转台,控制不同加热温度进入保温状态,分别保温固定时长;
16.冷却脱模。
17.进一步地,按质量百分比计算出sic、鳞片状石墨与电解铜粉的质量,称取总重为900g的混合粉末。
18.进一步地,将混合粉末与紫铜球按球料比4:1装入混料罐,通过高能球磨法在三维混料机上混料16h,得到混合均匀的混合粉末。
19.进一步地,启动所述凸模与凹模内部的加热体,控制温度为750℃进入保温状态。
20.进一步地,以5.5mm/min速度下行主缸,通过主缸上的凸模对基体内的混合粉末进行热压固结。
21.进一步地,当主缸运行至设定行程,切换控制方式为定压控制,保持主缸面压为25mpa。
22.进一步地,启动工作转台,转速为18.5mm/min,同时,主缸面压以1mpa/min加压至50mpa,并保压20min。
23.进一步地,停止主缸及工作转台,控制温度为450℃进入保温状态,保温20min;
24.控制温度为150℃进入保温状态,保温10min。
25.本发明提供了一种高承载自润滑复合轴套的制备装置,包括凸模与凹模;
26.其中所述凸模与凹模内部预制有加热体;
27.所述凹模的中心设置有基体,所述凹模的内底壁与所述基体的内壁之间形成用于成型自润滑耐磨层的容置腔,所述凸模安装在主缸的输出端,所述凹模安装在工作转台上。
28.进一步地,所述基体在内壁两端面及中部预留凸台,且所述基体在相邻凸台之间加工有凸起。
29.本发明的有益效果如下:
30.与现有的轴套相比,只需在常规合金轴套上热压固结一层自润滑耐磨层,确保了高承载自润滑复合轴套具备较好的自润滑性能与较高的抗压溃性能;另外,基体内壁的凸起与凸台均有利于复合轴套的耐磨涂层的冶金结合效果。保压状态下工作转台带动模具、基体与自润滑耐磨粉末涂层转动,可以使得自润滑耐磨粉末涂层内部形成以径向分布的梯度成分与梯度性能特征。可以使得自润滑耐磨涂层从中心至外圆周在微观尺寸上形成梯度分布,内表层至外表层微观组织尺寸从大到小分布,外表层细小组织尺寸与颗粒更易与基体内表面形成高的冶金结合,提升结合强度;内表层大组织尺寸与颗粒更易在磨损初期形成最佳的自润滑效果。当自润滑耐磨涂层从内表层至外表层发生磨损时,其自润滑和耐磨效果呈相反的趋势变化,即磨损初期,自润滑效果最佳兼具一定的耐磨性,磨损中后期,当润滑效果形成后,自润滑颗粒释放将减缓,自润滑耐磨涂层的耐磨性得到提升。因此,较高的耐磨涂层冶金结合效果、较好的自润滑性能、较强的耐磨性能使得该高承载自润滑复合轴套具有较长服役寿命、较好自润滑效果、较高抗压溃强度并兼具有利于保护摩副轴类件、经济环保及易于产业化应用等优点,可广泛应用于工程机械各类转动零部件的连接。
附图说明
31.图1为根据本发明实施例提供的一种高承载自润滑复合轴套的制备装置的剖面示意图。
具体实施方式
32.采用常规的合金钢或铜合金管材作为基材,对其摩擦表面通过热压固结的方法形成一层自润滑耐磨涂层。具体为,对基材按尺寸进行机加工,形成摩擦表面的凸起与端部台
阶;制备热压固结模具;制备自润滑混合粉末;通过加热与压制、扭转相结合的方式将自润滑混合粉末固结在基材摩擦表面,最后通过适量机加工成形零件。可通过工况及使用要求,合理选用基材。可通过工况及使用要求,选用最适宜的自润滑混合粉末成分配比。
33.实施案例
34.基体采用高力黄铜,复合粉末原料为:电解铜粉(300目,45μmm,纯度≥99.5%);鳞片状石墨(300目,45μmm,纯度≥99.9%);β
‑
sic颗粒(0.5μmm,纯度≥99.9%);二硫化钼(500目,纯度≥99.9%)。成分配比如下,铜粉:石墨:sic颗粒:二硫化钼=86:10:2:2(wt%)。
35.本发明提供了一种高承载自润滑复合轴套的制备方法,其制造工艺按步骤为:
36.步骤一,配制混粉。按成分配比(质量百分比)计算出sic、鳞片状石墨与电解铜粉的质量,称取总重为900g的混合粉末。将混合粉末与紫铜球(球料比4:1)装入混料罐,通过高能球磨法在三维混料机上混料16h,得到混合均匀的混合粉末。
37.步骤二,模具制备。根据轴套尺寸及基体材料占比与粉末成形工艺的特性,并预留机加工余量,制备符合要求的凸模10与凹模20,凸模10与凹模20在内部均先预制加热体(即加热棒30)。
38.步骤三,基体制备。根据轴套尺寸及基体材料占比,制备符合要求的基体40。基体40在内壁两端面及中部预留凸台41,本次加工一次成型两件轴套零件,基体40在内壁机加工凸起42。基体40内壁的凸起42与凸台41均有利于复合轴套的耐磨涂层的冶金结合效果。
39.步骤四,热压固结。将凸模10对中固定在底板50并安装在工作转台上,在凹模20中心放入基体40。将凸模10安装在主缸上,与凹模进行中心对中。根据体积密度与成形空间换算,在基体40内环装入500g混合粉末。启动凸模10与凹模20加热功能,控制温度为750℃进入保温状态,同时以5.5mm/min速度下行主缸,对基体40内混合粉末进行热压固结。
40.当主缸运行至设定行程,切换控制方式为定压控制,保持主缸面压为25mpa。启动下工作转台,转速为18.5mm/min,同时,主缸面压以1mpa/min加压至50mpa,并保压20min。保压状态下工作转台带动模具、基体与自润滑耐磨粉末涂层转动,可以使得自润滑耐磨粉末涂层内部形成以径向分布的梯度成分与梯度性能特征。可以使得自润滑耐磨涂层从中心至外圆周在微观尺寸上形成梯度分布,内表层至外表层微观组织尺寸从大到小分布,外表层细小组织尺寸与颗粒更易与基体内表面形成高的冶金结合,提升结合强度;内表层大组织尺寸与颗粒更易在磨损初期形成最佳的自润滑效果。当自润滑耐磨涂层从内表层至外表层发生磨损时,其自润滑和耐磨效果呈相反的趋势变化,即磨损初期,自润滑效果最佳兼具一定的耐磨性,磨损中后期,当润滑效果形成后,自润滑颗粒释放将减缓,自润滑耐磨涂层的耐磨性得到提升。
41.步骤五,停止主缸及工作转台,控制加热棒30温度为450℃进入保温状态,保温20min。控制加热棒30温度为150℃进入保温状态,保温10min。随后空冷至室温,最后脱模,根据零件尺寸进行机加工,对凸台41进行中间截断,一次成型两件轴套零件。
42.因此,较高的耐磨涂层冶金结合效果、较好的自润滑性能、较强的耐磨性能使得该高承载自润滑复合轴套具有较长服役寿命、较好自润滑效果、较高抗压溃强度并兼具有利于保护摩副轴类件、经济环保及易于产业化应用等优点,可广泛应用于工程机械各类转动零部件的连接。
43.本发明提供了一种高承载自润滑复合轴套的制备装置,包括凸模10与凹模20,其中所述凸模与凹模内部预制有加热体(即加热棒30),在凹模20的中心设置有基体40,在凹模20的内底壁与基体40的内壁之间形成用于成型复合自润滑耐磨层60的容置腔,凹模20安装在主缸的输出端,凹模20安装在工作转台上;
44.基体40在内壁两端面及中部预留凸台41,且基体40在相邻凸台41之间加工有凸起42,基体40内壁的凸起42与凸台41均有利于复合自润滑耐磨层的冶金结合效果。
45.以上所述仅是本发明的优选实施方式,应当指出,对于本技术领域的普通技术人员来说,在不脱离本发明技术原理的前提下,还可以做出若干改进和变形,这些改进和变形也应视为本发明的保护范围。