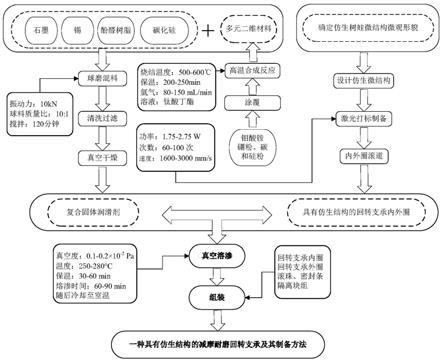
1.本发明涉及一种具有仿生结构的减摩耐磨回转支承及其制备方法,属于回转支承表面加工技术领域。
背景技术:2.回转支承是近六十年在世界范围内随着机械工业的发展而逐渐发展起来的新型机器部件,它广泛应用于起重机械、船舶机械和风力发电装备等设备的调向系统。回转支承是具有回转运动的重要部件,对回转平台的转动副起减少摩擦、降低磨损的作用,回转支承的承载能力以及疲劳寿命直接关系到整个设备的寿命。
3.回转支承在结构形式类似于轴承,采用滚动体~滚道式结构,制造工艺复杂,加工成本高,必须有良好的润滑。在应用方面,回转支承常用于低速重载工况。在外载荷作用下,回转支承的结构致使其外载荷集中作用于小部分滚动体上,从而加大了单个滚动体的受力。因此滚动回转支承经常出现回转齿圈或上下座圈的滚道点蚀、磨损或压溃、齿圈磨损或齿形断裂等各种损坏,这大大降低了其承载能力及使用寿命。在使用中,要经常检测、更换润滑油并及时检查密封圈的完整性,以防异物进入支承内部,也造成了其安装维护困难等问题。故提高回转支承的运行可靠性和疲劳寿命是工程应用上需要研究的重点。
4.影响回转支承寿命的主要因素有使用维护不当、工况条件复杂或润滑不良等原因,引起的滚道点蚀、磨损或压溃等失效形式。回转支承的内外圈与滚动体接触通常采用润滑脂改善摩擦环境,润滑脂在摩擦过程中通过形成润滑油膜来避免摩擦副直接接触来减少磨损,而润滑脂膜存在有限承载能力,当作用载荷超出有限承载能力,润滑脂膜厚度将减少,直至润滑脂膜破裂造成润滑失效致使基体受损。因此,在往复循环载荷作用下,仅通过脂润滑不能保证回转支承的内外圈满足复杂工况需求。为了提高回转支承的运行可靠性和疲劳寿命,急需开发一种新型高性能减摩耐磨的回转支承以满足回转机械在工程应用上的要求。
技术实现要素:5.针对现有技术的不足,本发明目的是提供一种具有仿生结构的减摩耐磨回转支承及其制备方法,所设计制备的回转支承内外圈滚道具有优异的摩擦学性能,摩擦系数和磨损率较低、良好的隔热耐磨和减噪的性能,可以解决现有回转支承回转精度不稳定、疲劳寿命低及内外圈滚道的磨损率高等问题。
6.为实现以上目的,本发明通过以下技术方案予以实现:
7.一种具有仿生结构的减摩耐磨回转支承,其特征在于回转支承的内圈和外圈表面加工正六边形仿生微结构,以石墨、锡、多元二维材料、酚醛树脂和碳化硅作为复合固体润滑剂,将复合固体润滑剂分别填充至回转支承内外圈的仿生微结构中,回转支承内圈正六边形仿生微结构与回转支承外圈正六边形仿生微结构连接有滚珠、密封条与隔离块得到具有仿生结构的回转支承。
8.按上述方案,回转支承的内圈正六边形仿生微结构的几何参数为:正六边形边长为600~800μm;凹槽间距:350~500μm;凹槽深:400~600μm;
9.按上述方案,回转支承的外圈正六边形仿生微结构的几何参数为:正六边形边长为800~1000μm;凹槽间距:400~600μm;凹槽深:500~600μm;
10.按上述方案,所述复合固体润滑剂中各原料按质量百分比包括:石墨15~20 wt.%、锡60~75wt.%、多元二维材料3~5wt.%、酚醛树脂6~12wt.%和碳化硅5~8wt.%;
11.按上述方案,所述复合固体润滑剂中锡粉的粒径范围为50~65μm,纯度在99.5%以上;石墨的粒径范围为110~120μm;碳化硅的粒径范围为70~140μ m,纯度在95%以上;
12.按上述方案,所述多元二维材料主要由钼酸铵、硼、碳和硅混合物基于钼丝为载体,在含有钛酸丁酯的氩气增强气氛中,经过高温反应合成制备得到。其中,各原料按质量百分比包括钼酸铵18~25wt.%、硼粉25~30wt.%、碳 26~34wt.%和硅粉原料粉末20~25wt.%。
13.进一步地,所述多元二维材料的制备方法,主要包括如下步骤:
14.1)混料:按多元二维材料的原料的质量百分比配料,将钼酸铵、硼粉、碳粉和硅粉原料粉末通过研磨机进行研磨混合;
15.2)制备:将混合配料加入适量水制成粘稠状,均匀涂在钼丝上,使用钼丝炉对其进行烧结,烧结温度为500~600℃,保温时间为200~250min,烧结过程中通入氩气,氩气通入量为80~150ml/min,氩气经含有钛酸丁酯容量瓶进入钼丝炉,经高温合成反应制备得到多元二维材料。
16.本发明的目的还在于提供一种具有仿生结构的减摩耐磨回转支承及其制备方法,主要包括如下步骤:
17.(1)前处理:使用前对回转支承的内外圈进行打磨、抛光处理,使其表面粗糙度小于0.04μm。试样抛光完后,放入无水乙醇中用超声波清洗器清洗10~ 15min,清洗完后用吹风机吹干。
18.(2)激光打标:使用激光打标机对回转支承的内外圈按照设计的仿生微流道结构参数进行打标处理,得到具有仿生微结构的回转支承的内外圈。
19.(3)机械混料:将石墨、锡、多元二维材料、酚醛树脂和碳化硅进行机械混合,得到均匀的复合固体润滑剂。
20.(4)熔渗填充:将具有仿生微结构的回转支承的内外圈和复合固体润滑剂采用真空压力熔渗技术将固体润滑剂填充在仿生微结构,得到具有仿生复合润滑剂的回转支承内外圈。
21.(5)组装:将回转支承内外圈和滚珠、密封条和隔离块组装成回转支承,得到具有仿生微结构的回转支承。
22.按上述方案,所述步骤(2)中激光打标机的打标功率为:1.75~2.75w;扫描次数为:60~100次;激光器的扫描速度为:1600~3000mm/s。
23.按上述方案,所述步骤(4)中采用的真空熔渗方法为:将固体复合润滑剂和回转支承的内外圈试样分别放在真空压力熔渗炉内的坩埚和固定支架上,抽真空至0.1~0.2
×
10
~2
pa,加热温度为250~280℃,保温30~60min后,使固体润滑剂浸没试样,同时气压升至
0.5~1.5mpa,熔渗时间为60~90min。随炉冷至室温,取出试样后对其进行打磨抛光处理。
24.本发明所制备的具有仿生结构的减摩耐磨回转支承具备优异的摩擦学性能,摩擦系数和磨损率较低。在测试中的磨损率3.4~5.4
×
10
~8
cm3/(n
·
m),滑动摩擦系数:0.015~0.030,具有较好的减摩耐磨性能。此外,在回转试验平台旋转26000转后,具有仿生结构的回转支承的内圈和外圈滚道表面均未出现压痕,而普通回转支承内圈,不仅有轻微压痕,外圈出现轻微压痕,且具有出现点蚀现象。故具有仿生结构的减摩耐磨回转支承性能参数优于普通回转支承产品。
25.本发明所述的一种具有仿生结构的减摩耐磨回转支承及其制备方法的主要构思如下:针对普通回转支承在往复循环载荷作用下,仅通过脂润滑不能保证回转支承的内外圈满足复杂工况需求,而固体润滑剂在重载和循环载荷条件下仍具有较好的润滑效果,故采用固体润滑技术协同脂润滑能满足复杂工况需求。通常设计的微织构的形式可能会影响基体的性能,受树蛙脚掌(基体)分泌的粘液(固体润滑剂)与表面微纳米结构(微织构)的协同作用在界面(接触界面)产生了较强吸附作用(润滑作用)的启发,通过对树蛙脚底凸起的微纳米结构研究,发现脚趾上皮微结构主要是六边形,故对回转支承的内圈和外圈表面进行正六边形仿生微结构设计制备。而石墨、锡、多元二维材料、酚醛树脂和碳化硅作为复合固体润滑剂,锡是一种软金属,具有较低的剪切强度,在摩擦时软金属会在接触界面形成转移膜,使摩擦发生在转移膜与软金属自身之间,从而降低摩擦、减少磨损,达到润滑作用。石墨和多元二维材料等具有良好的润滑性能,有助于复合润滑剂润滑的效果,能降低材料磨损率、降低摩擦表面磨损,提高回转支承的稳定性和使用寿命。
26.与现有技术相比,本发明有益效果如下:
27.1.本发明的回转支承具有具备优异的摩擦学性能,摩擦系数和磨损率较低。能降低材料磨损率、减少摩擦表面磨损,提高回转支承的稳定性和使用寿命等特点,可以解决现存产品回转支承滚动体和内外圈磨损率高、使用寿命短及稳定性差等问题。
28.2.本发明所述回转支承的内外圈采用仿生树蛙的正六边形微织构,固体润滑剂通过仿生微织构能够更充分的铺展在基体表面,形成一层润滑膜,起到减少摩擦,降低材料磨损的作用。
29.3.本发明所述回转支承,其复合固体润滑剂使用了石墨、锡、多元二维材料、酚醛树脂和碳化硅,多种润滑剂协同作用,提高润滑效果,起到减摩耐磨作用。
30.4.本发明所述回转支承,其复合固体润滑剂中的多元二维材料制备是由钼酸铵、硼粉、碳和硅粉原料粉末用水混合成粘稠状,均匀涂覆在钼丝上,高温合成过程中通入含有钛酸丁酯的氩气进入钼丝炉,促进合成反应。该多元二维材料能提高复合润滑剂的润滑效果,起到减少材料磨损作用。
31.5.本发明所述回转支承,通过复合固体润滑技术结合仿生结构设计,在重载或交变载荷作用下,能够避免润滑脂在润滑过程中,由于润滑脂膜破裂造成润滑失效使基体受损。润滑脂膜存在有限承载能力,当作用载荷超出有限承载能力,润滑脂厚度将减少,直至润滑脂膜破裂造成润滑失效,进而导致内外圈直接对摩而损伤。通过固体润滑和脂润滑的协同作用,可以满足复杂工况下的工程应用。改善摩擦环境,在摩擦副之间形成一层固体润滑膜,避免摩擦副直接接触,从而缓冲摩擦力来减少磨损。
32.本发明所制备的具有仿生结构的减摩耐磨回转支承具备优异的摩擦学性能,摩擦
系数和磨损率较低。在测试中的磨损率3.4~5.4
×
10
~8
cm3/(n
·
m),滑动摩擦系数:0.015~0.030,具有较好的减摩耐磨性能。此外,在回转试验平台旋转26000转后,具有仿生结构的回转支承的内圈和外圈滚道表面均未出现压痕,而普通回转支承内圈,不仅有轻微压痕,外圈出现轻微压痕,而且具有出现点蚀现象。故具有仿生结构的减摩耐磨回转支承性能参数明显优于普通回转支承产品。
附图说明
33.图1是本发明所述的具有仿生结构的减摩耐磨回转支承及其制备方法的工艺流程图;
34.图2是本发明所述的具有仿生结构的减摩耐磨回转支承的仿生微结构设计图;
35.图3是本发明实施例1、2和3的回转支承摩擦系数变化曲线。
具体实施方式
36.为了更好地理解本发明,下面结合实施例对本发明内容进行清楚、完整地描述,但所描述的实施例仅仅是本发明一部分实施例,而不是全部的实施例。
37.下述实施例中,复合固体润滑剂中锡粉的粒径范围为50~65μm,纯度在 99.5%以上;石墨的粒径范围为110~120μm;碳化硅的粒径范围为70~140 μm,纯度在95%以上。
38.下述实施例中,具有仿生结构的减摩耐磨回转支承,加工面在回转支承的内圈滚道和外圈滚道。而减摩耐磨回转支承的仿生微结构设计,分别加工成正六边形仿生微结构。固体润滑剂通过仿生微织构能够更充分的铺展在基体表面,形成一层润滑膜,起到减少摩擦、降低材料磨损的作用。其中,复合固体润滑剂包含石墨、锡、多元二维材料、酚醛树脂和碳化硅,将复合固体润滑剂混合填充至回转支承内外圈的仿生微结构中,得到具有仿生结构的回转支承。而多元二维材料按质量百分比包括钼酸铵18~25wt.%、硼粉25~30wt.%、碳26~ 34wt.%和硅粉原料粉末20~25wt.%混合物基于钼丝为载体,在含有钛酸丁酯的氩气增强气氛中,经过高温反应合成制备得到。
39.对照组
40.未做任何处理的普通回转支承在mft~5000摩擦实验机上进行摩擦磨损测试,其中摩擦实验的对磨球材料是ggr15,往复直线运动的位移为8mm,往复频率为1hz,加载压力为10n,在测试中的磨损率3.8
×
10
~8
cm3/(n
·
m),滑动摩擦系数:0.032。此外,在回转试验平台上对回转支承进行检测,在轴向力25 kn,倾覆力矩80knm,转速为1.5rpm的脂润滑条件下,试验26000转,拆检观测回转支承的内外圈滚道的压痕情况。回转支承的内圈滚道表面出现轻微压痕,外圈滚道表面出现压痕及滚道两端出现点蚀现象。
41.实施例1
42.一种具有仿生结构的减摩耐磨回转支承,其特征在于回转支承的内圈和外圈加工正六边形仿生微结构,以石墨、锡、多元二维材料、酚醛树脂和碳化硅作为复合固体润滑剂,将复合固体润滑剂分别填充至回转支承内外圈的仿生微结构中,回转支承内圈正六边形仿生微结构与回转支承外圈正六边形仿生微结构连接有滚珠、密封条与隔离块得到具有仿生结构的回转支承得到具有仿生结构的回转支承。
43.本实施例中,回转支承的内圈正六边形仿生微结构的几何参数为:正六边形边长
为600μm;凹槽间距:400μm;凹槽深:450μm;回转支承的外圈正六边形仿生微结构的几何参数为:正六边形边长为800μm;凹槽间距:500 μm;凹槽深:550μm;
44.复合固体润滑剂中各原料按质量百分比包括:石墨18wt.%、锡65wt.%、多元二维材料3wt.%、酚醛树脂8wt.%和碳化硅6wt.%;
45.多元二维材料主要由钼酸铵、硼、碳和硅混合物基于钼丝为载体,在含有钛酸丁酯的氩气增强气氛中,经过高温反应合成制备得到。其中,各原料按质量百分比包括钼酸铵20wt.%、硼粉25wt.%、碳30wt.%和硅粉原料粉末25 wt.%。
46.进一步地,多元二维材料的制备方法,主要包括如下步骤:
47.1.混料:按多元二维材料的原料的质量百分比配料,将钼酸铵(2.0g)、硼粉(2.5g)、碳(3.0g)和硅粉(2.5g)原料粉末通过研磨机进行研磨混合;
48.2.制备:将混合配料加入适量水制成粘稠状,均匀涂在钼丝上,使用钼丝炉对其进行烧结,烧结温度为500℃,保温时间为250min,烧结过程中通入氩气,氩气通入量为100ml/min,氩气经含有99.9%浓度的钛酸丁酯容量瓶进入钼丝炉,促进合成反应发生,制备得到多元二维材料。
49.如图1所示,一种具有仿生结构的减摩耐磨回转支承及其制备方法具体包括如下步骤:
50.(1)前处理:使用前对回转支承的内外圈进行打磨、抛光处理,表面粗糙度 0.02μm。试样抛光完后,放入无水乙醇中用超声波清洗器清洗10min,清洗完后用吹风机吹干。
51.(2)激光打标:使用激光打标机对回转支承的内外圈按照设计的仿生微流道结构参数进行打标处理,激光打标机的打标功率为:1.75w;扫描次数为:100 次;激光器的扫描速度为:2000mm/s。得到具有仿生微结构的回转支承的内外圈。
52.(3)机械混料:将石墨(18.0g)、锡(65.0g)、多元二维材料(3.0g)、酚醛树脂(8.0g)和碳化硅(6.0g)一起放入球磨机进行球磨,振动力为10000 n,球料质量比为10:1,搅拌时间为120min;球磨结束后,使用去离子水对混合浆料清洗和不锈钢筛子进行过滤,利用真空干燥箱进行干燥处理,得到复合固体润滑剂粉料;
53.(4)熔渗填充:将具有仿生微结构的回转支承的内外圈和复合固体润滑剂采用真空压力熔渗技术将固体润滑剂填充在仿生微结构,将固体复合润滑剂和回转支承的内外圈试样分别放在真空压力熔渗炉内的坩埚和固定支架上,抽真空至0.1
×
10
~2
pa,加热温度为280℃,保温40min后,使固体润滑剂浸没试样,同时气压升至0.8mpa,熔渗时间为90min。随炉冷至室温,取出试样后对其进行打磨抛光处理,得到具有仿生复合润滑剂的回转支承内外圈。
54.(5)组装:将回转支承内外圈和滚珠、密封条和隔离块组装成回转支承,得到具有仿生微结构的回转支承。
55.本实施例制备的具有仿生结构的减摩耐磨回转支承在mft~5000摩擦实验机上进行摩擦磨损测试,其中摩擦实验的对磨球材料是ggr15,往复直线运动的位移为8mm,往复频率为1hz,加载压力为10n,在测试中的磨损率3.8
×ꢀ
10
~8
cm3/(n
·
m),滑动摩擦系数:0.020,具有较好的减摩耐磨性能。此外,在回转试验平台上对回转支承进行检测,在轴向力25kn,倾覆力矩80knm,转速为1.5rpm的脂润滑条件下,试验26000转,拆检观测回转支承的内外圈滚道的压痕情况。具有仿生结构的回转支承的内圈和外圈滚道表面均未出现压痕及明显摩
擦失效现象。故具有仿生结构的减摩耐磨回转支承性能参数优于普通回转支承产品。
56.实施例2
57.一种具有仿生结构的减摩耐磨回转支承,其特征在于回转支承的内圈和外圈加工正六边形仿生微结构,以石墨、锡、多元二维材料、酚醛树脂和碳化硅作为复合固体润滑剂,将复合固体润滑剂分别填充至回转支承内外圈的仿生微结构中,回转支承内圈正六边形仿生微结构与回转支承外圈正六边形仿生微结构连接有滚珠、密封条与隔离块得到具有仿生结构的回转支承得到具有仿生结构的回转支承。
58.本实施例中,回转支承的内圈正六边形仿生微结构的几何参数为:正六边形边长为700μm;凹槽间距:450μm;凹槽深:500μm;回转支承的外圈正六边形仿生微结构的几何参数为:正六边形边长为900μm;凹槽间距:550 μm;凹槽深:500μm;
59.复合固体润滑剂中各原料按质量百分比包括:石墨15wt.%、锡70wt.%、多元二维材料4wt.%、酚醛树脂6wt.%和碳化硅:5wt.%;
60.多元二维材料主要由钼酸铵、硼、碳和硅混合物基于钼丝为载体,在含有钛酸丁酯的氩气增强气氛中,经过高温反应合成制备得到。其中,各原料按质量百分比包括钼酸铵22wt.%、硼粉30wt.%、碳26wt.%和硅粉原料粉末22 wt.%。
61.进一步地,多元二维材料的制备方法,主要包括如下步骤:
62.1.混料:按多元二维材料的原料的质量百分比配料,将钼酸铵(2.2g)、硼粉(3.0g)、碳(2.6g)和硅粉(2.2g)原料粉末通过研磨机进行研磨混合;
63.2.制备:将混合配料加入适量水制成粘稠状,均匀涂在钼丝上,使用钼丝炉对其进行烧结,烧结温度为550℃,保温时间为220min,烧结过程中通入氩气,氩气通入量为120ml/min,氩气经含有99.9%浓度的钛酸丁酯容量瓶进入钼丝炉,促进合成反应发生,制备得到多元二维材料。
64.如图1所示,一种具有仿生结构的减摩耐磨回转支承及其制备方法具体包括如下步骤:
65.(1)前处理:使用前对回转支承的内外圈进行打磨、抛光处理,表面粗糙度 0.03μm。试样抛光完后,放入无水乙醇中用超声波清洗器清洗12min,清洗完后用吹风机吹干。
66.(2)激光打标:使用激光打标机对回转支承的内外圈按照设计的仿生微流道结构参数进行打标处理,激光打标机的打标功率为:2w;扫描次数为:80次;激光器的扫描速度为:1800mm/s。得到具有仿生微结构的回转支承的内外圈。
67.(3)机械混料:将石墨(15.0g)、锡(70.0g)、多元二维材料(4.0g)、酚醛树脂(6.0g)和碳化硅(5.0g)一起放入球磨机进行球磨,振动力为10000 n,球料质量比为10:1,搅拌时间为120min;球磨结束后,使用去离子水对混合浆料清洗和不锈钢筛子进行过滤,利用真空干燥箱进行干燥处理,得到得到复合固体润滑剂粉料;
68.(4)熔渗填充:将具有仿生微结构的回转支承的内外圈和复合固体润滑剂采用真空压力熔渗技术将固体润滑剂填充在仿生微结构,将固体复合润滑剂和回转支承的内外圈试样分别放在真空压力熔渗炉内的坩埚和固定支架上,抽真空至0.15
×
10
~2
pa,加热温度为260℃,保温50min后,使固体润滑剂浸没试样,同时气压升至1.0mpa,熔渗时间为80min。随炉冷至室温,取出试样后对其进行打磨抛光处理,得到具有仿生复合润滑剂的回转支承内外圈。
69.(5)组装:将回转支承内外圈和滚珠、密封条和隔离块组装成回转支承,得到具有仿生微结构的回转支承。
70.本实施例制备的具有仿生结构的减摩耐磨回转支承在mft~5000摩擦实验机上进行摩擦磨损测试,其中摩擦实验的对磨球材料是ggr15,往复直线运动的位移为8mm,往复频率为1hz,加载压力为10n,在测试中的磨损率4.4
×ꢀ
10
~8
cm3/(n
·
m),滑动摩擦系数:0.025,具有较好的减摩耐磨性能。此外,在回转试验平台上对回转支承进行检测,在轴向力25kn,倾覆力矩80knm,转速为1.5rpm的脂润滑条件下,试验26000转,拆检观测回转支承的内外圈滚道的压痕情况。具有仿生结构的回转支承的内圈和外圈滚道表面均未出现压痕及明显摩擦失效现象。故具有仿生结构的减摩耐磨回转支承性能参数优于普通回转支承产品。
71.实施例3
72.一种具有仿生结构的减摩耐磨回转支承,其特征在于回转支承的内圈和外圈加工正六边形仿生微结构,以石墨、锡、多元二维材料、酚醛树脂和碳化硅作为复合固体润滑剂,将复合固体润滑剂分别填充至回转支承内外圈的仿生微结构中,回转支承内圈正六边形仿生微结构与回转支承外圈正六边形仿生微结构连接有滚珠、密封条与隔离块得到具有仿生结构的回转支承得到具有仿生结构的回转支承。
73.本实施例中,回转支承的内圈正六边形仿生微结构的几何参数为:正六边形边长为800μm;凹槽间距:450μm;凹槽深:500μm;回转支承的外圈正六边形仿生微结构的几何参数为:正六边形边长为1000μm;凹槽间距:550μ m;凹槽深:600μm;
74.复合固体润滑剂中各原料按质量百分比包括:石墨20wt.%、锡60wt.%、多元二维材料5wt.%、酚醛树脂7wt.%和碳化硅:8wt.%;
75.多元二维材料主要由钼酸铵、硼、碳和硅混合物基于钼丝为载体,在含有钛酸丁酯的氩气增强气氛中,经过高温反应合成制备得到。其中,各原料按质量百分比包括钼酸铵24wt.%、硼粉28wt.%、碳26wt.%和硅粉原料粉末22 wt.%。
76.进一步地,多元二维材料的制备方法,主要包括如下步骤:
77.1.混料:按多元二维材料的原料的质量百分比配料,将钼酸铵(2.4g)、硼粉(2.8g)、碳(2.6g)和硅粉(2.2g)原料粉末通过研磨机进行研磨混合;
78.2.制备:将混合配料加入适量水制成粘稠状,均匀涂在钼丝上,使用钼丝炉对其进行烧结,烧结温度为600℃,保温时间为210min,烧结过程中通入氩气,氩气通入量为120ml/min,氩气经含有99.9%浓度的钛酸丁酯容量瓶进入钼丝炉,促进合成反应发生,制备得到多元二维材料。
79.如图1所示,一种具有仿生结构的减摩耐磨回转支承及其制备方法具体包括如下步骤:
80.(1)前处理:使用前对回转支承的内外圈进行打磨、抛光处理,表面粗糙度 0.02μm。试样抛光完后,放入无水乙醇中用超声波清洗器清洗10min,清洗完后用吹风机吹干。
81.(2)激光打标:使用激光打标机对回转支承的内外圈按照设计的仿生微流道结构参数进行打标处理,激光打标机的打标功率为:2.50w;扫描次数为:60 次;激光器的扫描速度为:1600mm/s。得到具有仿生微结构的回转支承的内外圈。
82.(3)机械混料:将石墨(20.0g)、锡(60.0g)、多元二维材料(5.0g)、酚醛树脂(7.0g)和碳化硅(8.0g)一起放入球磨机进行球磨,振动力为10000 n,球料质量比为10:1,搅拌时
间为120min;球磨结束后,使用去离子水对混合浆料清洗和不锈钢筛子进行过滤,利用真空干燥箱进行干燥处理,得到复合固体润滑剂粉料;
83.(4)熔渗填充:将具有仿生微结构的回转支承的内外圈和复合固体润滑剂采用真空压力熔渗技术将固体润滑剂填充在仿生微结构,将固体复合润滑剂和回转支承的内外圈试样分别放在真空压力熔渗炉内的坩埚和固定支架上,抽真空至0.2
×
10
~2
pa,加热温度为250℃,保温60min后,使固体润滑剂浸没试样,同时气压升至0.8mpa,熔渗时间为60min。随炉冷至室温,取出试样后对其进行打磨抛光处理,得到具有仿生复合润滑剂的回转支承内外圈。
84.(5)组装:将回转支承内外圈和滚珠、密封条和隔离块组装成回转支承,得到具有仿生微结构的回转支承。
85.本实施例制备的具有仿生结构的减摩耐磨回转支承在mft~5000摩擦实验机上进行摩擦磨损测试,其中摩擦实验的对磨球材料是ggr15,往复直线运动的位移为8mm,往复频率为1hz,加载压力为10n,在测试中的磨损率3.6
×ꢀ
10
~8
cm3/(n
·
m),滑动摩擦系数:0.018,具有较好的减摩耐磨性能。此外,在回转试验平台上对回转支承进行检测,在轴向力25kn,倾覆力矩80knm,转速为1.5rpm的脂润滑条件下,试验26000转,拆检观测回转支承的内外圈滚道的压痕情况。具有仿生结构的回转支承的内圈和外圈滚道表面均未出现压痕及明显摩擦失效现象。故具有仿生结构的减摩耐磨回转支承性能参数优于普通回转支承产品。
86.以上所述仅是本发明的优选实施方式,应当指出,对于本领域的普通技术人员来说,在不脱离本发明创造构思的前提下,还可以做出若干改进和变换,这些都属于本发明的保护范围。