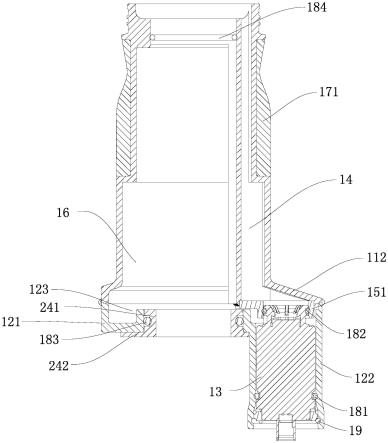
1.本实用新型涉及一种空气弹簧结构,尤其是涉及一种双气室空气弹簧活塞结构件。
背景技术:2.空气弹簧是安装在车体和转向架之间的一种重要的减振部件,车辆在运行过程中的点头、摇头、蛇形以及侧倾动作都作为激励振幅施加在空气弹簧上,而空气弹簧具有的多自由度形变和减振消能的功能使其在各种激励振幅条件下,都能起到良好的减振作用,保证车辆安全平稳的运行。
3.传统的空气弹簧为单气室结构,为了使空气弹簧具有较大的刚度调节范围,能在不同的驾驶工况下,既能够提供良好的操控性,又能够提供良好的舒适性驾驶体验,通过调整工作腔容积改变大小刚度,多气室结构的空气弹簧提供了可行的解决方案。
4.目前,研究最多的是双气室结构的空气弹簧,其多数在top mount壳体或活塞结构件中开辟出一个副气室空间。但是,现有的双气室空气弹簧存在以下问题:1)在样件验证阶段,其活塞结构件的活塞壳体与活塞基座注塑成型,一方面,活塞壳体与活塞基座的制备需借助注塑模具;另一方面,活塞壳体与活塞基座连接时需借助热熔模具,即活塞结构件样件需两种模具辅助,导致活塞结构件样件的制作成本较高。2)在样件验证阶段,无法实现悬架对双气室空气弹簧不同刚度目标梯度的验证调试需求。3)由于双气室空气弹簧布置空间原因导致部分副气室结构设计受限,因此结构设计难度较大。
技术实现要素:5.本实用新型所要解决的技术问题是提供一种双气室空气弹簧活塞结构件,活塞结构件的样件制作成本低,且能够实现悬架对双气室空气弹簧不同刚度目标梯度的验证调试需求;副气室结构设计简单,空间利用率大。
6.本实用新型解决上述技术问题所采用的技术方案为:一种双气室空气弹簧活塞结构件,包括活塞壳体、活塞基座和电磁阀,其特征在于:所述的活塞壳体和所述的活塞基座均为铝制结构件,所述的活塞壳体内设置有直通的主副气室通道,所述的主副气室通道的上端口位于所述的活塞壳体的顶端、下端口位于所述的活塞壳体的底端,所述的主副气室通道的下端口上焊接有一块铝制的活塞镶块,所述的活塞镶块具有一个阀连接部,所述的主副气室通道的下端口仅通过所述的阀连接部的内孔与所述的主副气室通道外连通,所述的活塞基座主要由基座本体和阀安装座组成,所述的基座本体具有一个腔口朝上的环形凹腔,所述的阀安装座上下开口且一体设置于所述的基座本体的周向一侧,且所述的阀安装座的顶部与所述的环形凹腔连通,所述的活塞壳体的底端边缘与所述的活塞基座的顶端边缘对齐并焊接,所述的阀连接部伸入所述的阀安装座的顶部内,所述的电磁阀自所述的阀安装座的底部竖直伸入并组装于所述的阀安装座内,所述的阀连接部套接于所述的电磁阀的顶端上,所述的活塞壳体的内腔与所述的环形凹腔构成副气室,所述的电磁阀的阀芯打
开时所述的副气室通过所述的主副气室通道与双气室空气弹簧的主气室连通。
7.所述的活塞壳体上设置有能够实现悬架对双气室空气弹簧不同刚度目标梯度的验证调试需求的活塞可调腰线机构。
8.所述的活塞壳体主要由一体设置的壳体主体和壳体底座组成,所述的壳体主体的上部外径小且下部外径大,所述的壳体主体的上部靠近顶端位置沿周向设置有凸环,所述的壳体主体的下部的顶端具有一个环形台面,所述的活塞可调腰线机构限制于所述的凸环与所述的环形台面之间,所述的壳体底座的顶端与所述的壳体主体的底端一体连接,所述的壳体底座设计为与所述的活塞基座相适配的形状。将壳体主体设计成台阶状结构,利用凸环和环形台面来限制活塞可调腰线机构的安装空间,使得整体结构更为紧凑,更为美观;将壳体底座设计为与活塞基座相适配的形状,这样壳体底座的底部边缘能够与活塞基座的顶部边缘完全对齐再焊接。
9.所述的活塞可调腰线机构包括两块结构相同的径向截面为半圆形状的腰型块,所述的腰型块的下部外径与所述的壳体主体的下部的外径一致,所述的腰型块的上部具有一逐渐内陷结构形成腰部,所述的腰型块嵌于所述的凸环与所述的环形台面之间,两块所述的腰型块相对并通过卡扣连接构成一个整体使该整体抱住所述的壳体主体的上部。在验证调试时可设计不同内陷程度腰部的腰型块,这样通过替换不同的腰型块可实现不同的刚度目标梯度需求。
10.所述的电磁阀通过o型圈密封组装于所述的阀安装座内,所述的电磁阀通过卡簧固定于所述的阀安装座内;所述的阀连接部密封套接于所述的电磁阀的顶端上。一般情况下o型圈设置于电磁阀的下部,卡簧位于电磁阀靠近底端的位置上。
11.与现有技术相比,本实用新型的优点在于:
12.1)由于活塞壳体和活塞基座及活塞镶块均为铝制结构件,而铝制结构件不仅可以采用机加工进行制备,而且也可以采用模具成型,因此在样件验证阶段,活塞壳体和活塞基座及活塞镶块采用机加工进行制备,无需模具辅助,大大降低了活塞结构件样件的开发成本和开发周期;而在生产环节,则活塞壳体和活塞基座及活塞镶块采用模具成型,可以实现批量生产。
13.2)通过在活塞壳体内设置一个直通的主副气室通道,在主副气室通道的下端口上焊接一块铝制的活塞镶块,活塞镶块具有一个阀连接部,主副气室通道的下端口仅通过阀连接部的内孔与主副气室通道外连通,而活塞基座主要由基座本体和阀安装座组成,基座本体具有一个腔口朝上的环形凹腔,阀安装座上下开口且一体设置于基座本体的周向一侧,且阀安装座的顶部与环形凹腔部分交叠以形成连通,活塞壳体的内腔与环形凹腔构成副气室,这种结构使得副气室结构设计简单,空间利用率大。
14.3)活塞壳体上设置一个活塞可调腰线机构,这样在样件验证阶段,通过更换不同的腰型块能够实现悬架对双气室空气弹簧不同刚度目标梯度的验证调试需求。
15.4)使用该活塞结构件的双气室空气弹簧通过电磁阀的阀芯的开闭来控制主气室和副气室的工作状态:当电磁阀的阀芯关闭时,双气室空气弹簧只有主气室工作,副气室不参与工作,为悬架提供高刚度弹簧特性;当电磁阀的阀芯打开时,双气室空气弹簧的主气室和副气室共同工作,主气室与副气室通过主副气室通道连通,为悬架提供低刚度弹簧特性,能够实现整车对于空气弹簧低刚度驾驶体验的舒适性设计需求。电磁阀实现了主气室与副
气室工作状态切换,为悬架提供所需高低刚度空气弹簧弹性特性需求。
16.5)该活塞结构件的分体式结构(活塞壳体、活塞基座、活塞镶块焊接成一体)实现了在样件验证阶段采用常规制作工艺的可操作性,且主副气室通道的形成,实现了主副气室通道气密性检测可操作性,确保了主副气室通道焊接密封可靠性。
附图说明
17.图1为本实用新型的活塞结构件的立体结构示意图;
18.图2为本实用新型的活塞结构件的主视图;
19.图3为图2的a-a向剖视图;
20.图4为本实用新型的活塞结构件中的活塞壳体的结构示意图一;
21.图5为本实用新型的活塞结构件中的活塞壳体的结构示意图二;
22.图6为本实用新型的活塞结构件中的活塞壳体的结构示意图三;
23.图7为本实用新型的活塞结构件中的活塞镶块焊接于活塞壳体上后的结构示意图;
24.图8为本实用新型的活塞结构件中的活塞镶块与电磁阀的连接结构示意图;
25.图9为本实用新型的活塞结构件中的活塞基座的结构示意图;
26.图10为本实用新型的活塞结构件中的腰型块的结构示意图;
27.图11为本实用新型的活塞结构件的轴向剖视结构示意图;
28.图12为使用本实用新型的活塞结构件的双气室空气弹簧的整体结构示意图;
29.图13为使用本实用新型的活塞结构件的双气室空气弹簧的局部结构的轴向剖视结构示意图;
30.图14为电磁阀的结构示意图。
具体实施方式
31.以下结合附图实施例对本实用新型作进一步详细描述。
32.本实用新型提出的一种双气室空气弹簧活塞结构件,如图所示,其包括活塞壳体11、活塞基座12和电磁阀13,活塞壳体11和活塞基座12均为铝制结构件(如采用铝合金材质制成),活塞壳体11内设置有直通的主副气室通道14,主副气室通道14的上端口位于活塞壳体11的顶端、下端口位于活塞壳体11的底端,主副气室通道14的下端口上焊接有一块铝制的活塞镶块15,活塞镶块15具有一个阀连接部151和一块封板152,封板152封住主副气室通道14的下端口除阀连接部151对应位置外的其余部分,主副气室通道14的下端口仅通过阀连接部151的内孔与主副气室通道14外连通,活塞基座12主要由基座本体121和阀安装座122组成,基座本体121具有一个腔口朝上的环形凹腔123,阀安装座122上下开口且一体设置于基座本体121的周向一侧,且阀安装座122的顶部与环形凹腔123部分交叠以形成连通,活塞壳体11的底端边缘与活塞基座12的顶端边缘对齐并焊接,阀连接部151伸入阀安装座122的顶部内,电磁阀13自阀安装座122的底部竖直伸入并组装于阀安装座122内,阀连接部151套接于电磁阀13的顶端上,活塞壳体11的内腔与环形凹腔123构成副气室16,电磁阀13的阀芯131打开时副气室16通过主副气室通道14与双气室空气弹簧的主气室26连通,电磁阀13的阀芯131关闭时副气室16不与双气室空气弹簧的主气室26连通,具体的,电磁阀13的
顶端具有中心通气口132和侧通气口133,中心通气口132与主副气室通道14直接连通,侧通气口133与副气室16直接连通,电磁阀13的阀芯131打开时中心通气口132与侧通气口133之间连通,电磁阀13的阀芯131关闭时中心通气口132与侧通气口133之间不连通。
33.进一步改进的,活塞壳体11主要由一体设置的壳体主体111和壳体底座112组成,壳体主体111的上部1111外径小且下部1112外径大,壳体主体111的上部1111靠近顶端位置沿周向设置有凸环113,壳体主体111的下部1112的顶端具有一个环形台面114,凸环113与环形台面114之间设置有能够实现悬架对双气室空气弹簧不同刚度目标梯度的验证调试需求的活塞可调腰线机构17,壳体底座112的顶端与壳体主体111的底端一体连接,壳体底座112设计为与活塞基座12相适配的形状。将壳体主体111设计成台阶状结构,利用凸环113和环形台面114来限制活塞可调腰线机构17的安装空间,使得整体结构更为紧凑,更为美观;将壳体底座112设计为与活塞基座12相适配的形状,这样壳体底座112的底部边缘能够与活塞基座12的顶部边缘完全对齐再焊接。
34.具体的,活塞可调腰线机构17包括两块结构相同的径向截面为半圆形状的腰型块171,腰型块171的下部外径与壳体主体111的下部1112的外径一致,腰型块171的上部具有一逐渐内陷结构形成腰部1711,腰型块171嵌于凸环113与环形台面114之间,两块腰型块171相对并通过卡扣(图中未示出)连接构成一个整体使该整体抱住壳体主体111的上部1111。在验证调试时可设计不同内陷程度腰部1711的腰型块171,这样通过替换不同的腰型块171可实现不同的刚度目标梯度需求。
35.具体的,电磁阀13通过第1个o型圈181密封组装于阀安装座122内,电磁阀13通过卡簧19固定于阀安装座122内;阀连接部151通过第2个o型圈182密封套接于电磁阀13的顶端上。一般情况下第1个o型圈181设置于电磁阀13的下部,卡簧19位于电磁阀13靠近底端的位置上。
36.一种使用上述的双气室空气弹簧活塞结构件的双气室空气弹簧,其主要由top mount(顶部支架)壳体21、囊皮22、缓冲块23、活塞结构件1、减震器密封座24、活塞杆25组成,top mount壳体21与囊皮22通过扣合环缩径的方式装配在一起,囊皮22与活塞结构件1中的活塞壳体11的壳体主体111的顶部通过扣合环缩径的方式装配在一起,缓冲块23设置于囊皮22内,且套设于活塞杆25外,缓冲块23的顶部与top mount壳体21连接,减震器密封座24的柱体部分241伸入活塞基座12的基座本体121的中心通孔内,减震器密封座24的柱体部分241与基座本体121的中心通孔之间采用第3个o型圈183密封连接,实现双气室空气弹簧的封闭密封,减震器密封座24的圆盘部分242与基座本体121的外底面紧贴,活塞杆25穿过减震器密封座24、活塞壳体11的内腔、囊皮22、缓冲块23与top mount壳体21连接,壳体主体111的上部靠近顶端位置的内壁与活塞杆25之间密封连接,top mount壳体21、囊皮22、壳体主体111的顶端围成的空间构成了主气室26,壳体主体111的上部1111靠近顶端位置的内壁与活塞杆25密封连接处构成了主气室26与副气室16的分界线,该分界线通过第4个o型圈184密封隔绝了主气室26与副气室16,使主气室26与副气室16相互独立,只有通过电磁阀13的阀芯131开闭来控制主气室26和副气室16的工作状态。使用该活塞结构件1的双气室空气弹簧通过电磁阀13的阀芯131开闭来控制主气室26和副气室16的工作状态:当电磁阀13的阀芯131关闭时,双气室空气弹簧只有主气室26工作,副气室16不参与工作,为悬架提供高刚度弹簧特性;当电磁阀13的阀芯131打开时,双气室空气弹簧的主气室26和副气室16共同
工作,主气室26与副气室16通过主副气室通道14连通,为悬架提供低刚度弹簧特性,能够实现整车对于空气弹簧低刚度驾驶体验的舒适性设计需求。