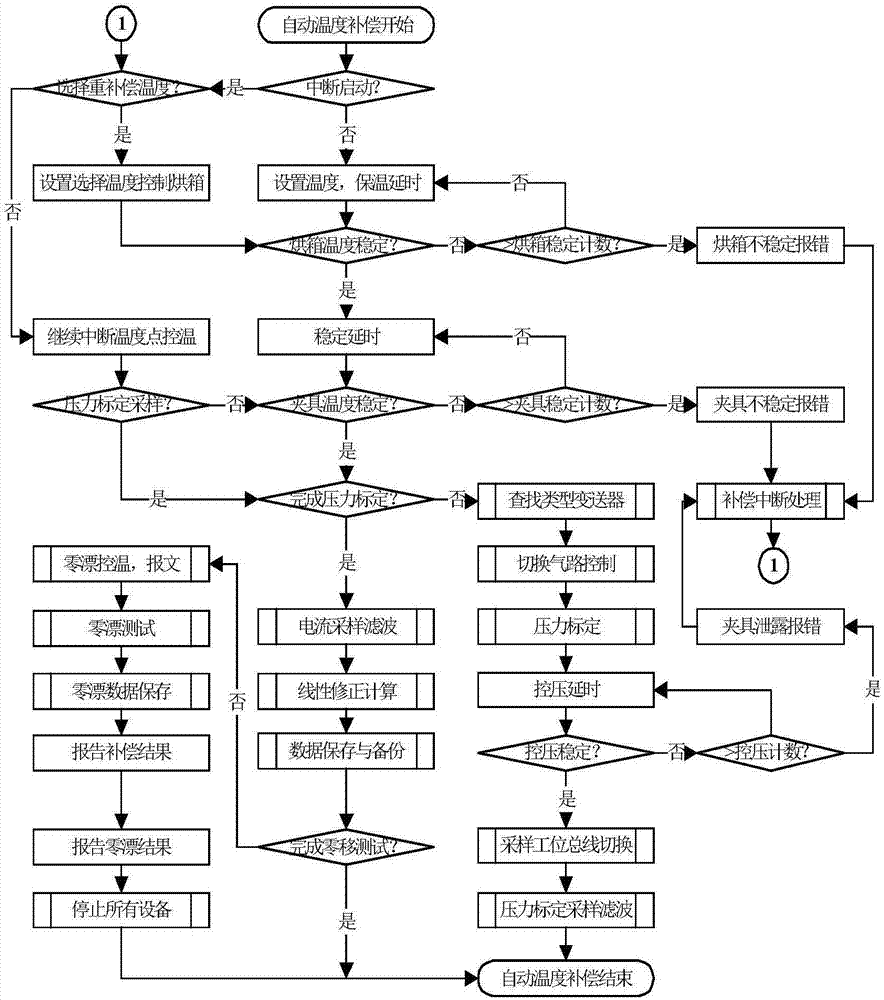
本发明属于流量检测
技术领域:
,特别是涉及一种基于数据库与文件相融合用于标定变送器的温压补偿方法及系统。
背景技术:
:生产压力变送器的企业,针对每台出厂的压力变送器整机仪表都要进行温度和压力的线性补偿修正的生产流程。该生产流程中需要配备一套或多套的温度和压力的标定补偿系统。而且整套标定补偿系统由控制主站、标定设备、控制总线、温压补偿标定电路和供压管道装置组成,如图1所示,为(压力或差压)变送器的温压补偿系统的框架结构图,现对其进行具体说明:控制主站:整套温度和压力标定与补偿系统中的工控机部分,它是该系统的核心,安装在工控机上的自动温度和压力标定补偿软件通过数据总线(rs485总线、hart总线、rs232总线)实现对在线待补偿的压力传感器的压力、温度和电流标定采样,以及相关内部参数、温压补偿修正系数的读写操作;通过gpib总线/usb数据总线实现压力传感器温度和压力标定补偿生产流程中对压力控制器ruska7250和数字万用表agilent34401a的操作控制;通过自主研发的工位以及气路切换控制模块电路实现对在线压力传感器的压力和温度信号的采集。标定设备:包含压力控制器、数字万用表与高低温烘箱。压力控制器ruska7250:用于压力传感器温度和压力的标定补偿生产流程中压力标定的控压设备。数字万用表agilent34401a:用于压力传感器温度和压力的标定补偿生产流程中4-20ma输出检测标定设备。高低温烘箱:用于压力传感器温度和压力的标定补偿生产流程中温度标定设备。控制总线:压力变送器温度和压力的标定补偿系统中的控制总线分为gpib总线和rs485总线。gpib总线:实现自动温度和压力标定补偿软件与压力控制器ruska7250和数字万用表agilent34401a具有ieee488总线型接口设备之间的通讯,使压力/差压变送器温度和压力的标定补偿生产流程中实现对压力标定设备和电流检测设备的自动控制。pci总线:实现自动温度和压力标定补偿软件对温压补偿标定电路的控制,以及气路电磁阀的控制,其目的是达到控制在线待温度和压力标定补偿压力/差压传感器之间hart总线通讯总线的切换和压力标定中供压气路管道的选择切换。rs485总线:实现自动温度和压力标定补偿软件与高低温烘箱设备之间的通讯,使压力变送器温度和压力的标定补偿生产流程中实现对温度标定设备的自动控制。实现自动温度和压力标定补偿软件与在线所有待温度和压力标定的压力/差压传感器之间进行的通讯,并将压力信号和温度信号的原始采样码值回传给控制主站,进行相应的存储,以便于温度和压力标定结束后进行线性修正计算。现有的压力变送器在温度与压力标定补偿时均采用软件代码为主控制流程,参照图2,以程序代码为主导控制的压力变送器自动温压补偿程序的软件流程,具体功能与实现流程如下:步骤1,待补偿压力变送器传感器温度标定的升温或降温代码流程。该阶段主要是自动温度和压力标定补偿软件控制高低温烘箱至温度补偿点,使烘箱烘室内的夹具处于相对温度稳定状态。压力变送器传感器的整个温度补偿流程中共计补偿5个温度点,分别是85℃、55℃、20℃、5℃和-15℃。设置任一温度时,均需要进行升温延时或降温延时,其延时时间为120分钟,自动温度和压力标定补偿软件中时钟消息响应延时机制来完成。在实际的温度补偿应用流程中,自动温度和压力标定补偿软件应用两个判定依据来判定每一个温度点是否处于温度稳定的状态:首先,判定烘箱是否处于稳定状态,如果烘箱的反馈温度围绕设定温度在20分钟内的波动范围不超过0.2℃,则烘箱温度处于稳定状态;其次,判定补偿夹具的温度是否处于稳定状态,如果自动温度和压力标定补偿软件检测每一个补偿夹具上温度传感器的温度在10分钟内波动不超过0.075℃,则压力传感器处于温度稳定状态。当自动温度和压力标定补偿软件检测到烘箱和夹具的温度均处于稳定状态时,便开始进行压力变送器传感器的压力标定采样流程。步骤2,待补偿变送器传感器的压力标定和滤波代码流程。自动温度和压力标定补偿软件完成压力标定采样的流程分五步:步骤2.1,通过pci总线驱动控制矩阵电路中的气路选择电路,控制气路管道的电磁阀,使压力控制器的测试端口与待补偿变送器传感器的补偿端接通,软件要进行气路切换状态进行检测,确保标定压力准确的作用在变送器的补偿端。步骤2.2,依据压力变送器传感器的类型,获取程序代码相应的数据缓冲区中的压力标定补偿点极其相关精度数组数据,从前至后,控制压力控制器至每一个压力标定点,并在压力标定点处于稳定的状态下完成补偿夹具上压力变送器传感器的压力标定采样。步骤2.3,读取程序内部固化工位总线数据缓冲区内相关联的硬件控制参数,通过pci总线驱动控制矩阵电路,使温度和压力补偿标定系统的rs485总线与当前补偿夹具位置001处的待温度和压力标定的压力传感器的rs485总线相连通,同时,使当前补偿夹具上其它位置的待温度和压力标定的压力传感器的rs485总线处于断开状态。通过rs485总线线位置001处的压力传感器发送压力和温度标定指令,延时并接收位置001处的压力传感器回传的压力和温度标定的原始采样数据,最终压力和温度标定的原始采样存储至位置001处所对应的excel文件中,完成当前位置001处将压力传感器的压力和温度标定。步骤2.4,重复步骤2.3,从前至后完成补偿夹具上的所有待温度和压力标定的压力/差压变送器传感器的压力和温度标定采样,及相对应的压力和温度标定采样数据的文件存储过程。步骤2.5,重复步骤2.3至2.4,从前至后完成所有压力标定补偿点下的待温度和压力标定的压力/差压变送器传感器的压力和温度标定采样,及相对应的压力和温度标定采样数据的文件存储过程。步骤3,电流采样和滤波的代码阐述流程。压力变送器传感器的电流标定采样是在温度和压力标定采样完成之后,在每一个温度补偿点下进行的,其采样的流程分为7七步:步骤3.1,读取程序内部固化的工位总线数据缓冲区内相关联的硬件控制参数,通过pci总线驱动控制矩阵电路,使温度和压力补偿标定系统的rs485总线与当前补偿夹具位置001处的待温度和压力标定的压力传感器的rs485总线相连通,同时,使当前补偿夹具上其它位置的待温度和压力标定的压力传感器的rs485总线处于断开状态。步骤3.2,通过rs485总线向位置001处的压力/差压传感器发送4ma电流采样命令。步骤3.3,接收到位置001处的压力/差压传感器回传的4ma电流采样命令应答时,断开测试001处的rs485总线,延时并多次读取数字万用表测试压力变送器传感器输出的4ma电流值,并进行均值滤波处理。步骤3.4,通过pci总线驱动控制矩阵电路再次接通位置001处的待温度和压力标定的压力传感器的rs485总线,延时位置001处的压力传感器发送的20ma电流采样命令。步骤3.5,接收到位置001处的压力传感器回传的20ma电流采样命令应答时,断开测试001处的rs485总线,延时并多次读取数字万用表测试压力变送器传感器输出的20ma电流值,并进行均值滤波处理。步骤3.6,将位置001处的待温度和压力标定的压力传感器的4ma电流采样值存储至位置001处所对应的excel文件中,完成当前位置001处将压力传感器的电流标定采样。步骤3.7,重复步骤3.2至3.6,完成从前至后完成所有压力变送器传感器的电流标定流程。步骤4,文件操作。在进行压力变送器传感器的温度和压力标定补偿修正的生产流程中,主要用到的文件为microsoftofficeexcel2003数据表文件,该文件主要用于压力传感器在温度和压力标定的生产流程中进行相应的温度标定采样码值、压力标定采样码值和电流标定采样码值等原始数据保存,便于压力传感器在温度和压力标定结束后读取对应工位文件数据,进行线性修正运算。步骤5,线性修正算法。建立数学模型,用于线性修正压力变送器传感器因受生产流程中的焊接、充灌、整形等生产工艺的制约,以及整机传感器自身机械结构的特性和应用环境温度的影响,导致压力传感器自身存在非线性、零漂的问题。步骤6,线性修正系数写eeprom代码流程。自动温度和压力标定补偿软件完成补偿工位上每一台压力变送器传感器温度和压力标定补偿的线性修正计算后,便开始将线性修正的非线性常系数写入到对应装夹工位压力变送器主控制板上的eeprom中,这为后续进行压力变送器的温漂测试和现场应用做准备。线性修正系数写eeprom代码流程分四步:步骤6.1,读取程序内部固化数据缓冲器中工位001处的总线控制参数,接通rs485通信总线。步骤6.2,将工位001处的压力传感器的线性修正系数封装成协议包,并发送至工位001处的压力变送器的控制板上的eeprom中。步骤6.3,接收工位001处的压力传感器回传正确的写线性修正系数协议帧后完成工位001处线性修正系数写eeprom操作。步骤6.4,重复步骤6.2至6.3,从前至后完成每一台压力变送器传感器线性修正系数写eeprom操作,并报告写系数结果。步骤7,温度和压力标定补偿流程中的异常处理。压力变送器传感器每一次的自动温度补偿流程都不是一个理想、无异常的流程,这就需要软件能够及时、准确的处理温度补偿流程中出现的异常信息,保证自动温度补偿流程的顺利进行。现有的以程序代码为主导控制的压力变送器自动温压补偿程序在研发和应用阶段,大体上有4个方面的异常现象:第一,pci总线控制球形阀进行气路切换的硬件异常代码处理。第二,pci总线控制矩阵板卡进行工位rs485通信总线选择的异常代码处理。第三,软件与测试仪器之间的通信异常,包括rs485总线、gpib总线通信协议不匹配,报文数据帧丢失等现象。第四,通过rs485总线压力/差压变送器传感器间的通信异常代码处理。步骤8,中断处理的功能。系统软件中引入断点续做功能是为解决变送器生产现场出现中断或终止时,能够及时的恢复生产,而无需重新进行温度补偿,减少时间上的浪费和降低经济上的损失。当软件处于人为终止状态,或是由于补偿夹具存在泄漏和测试仪器、电路异常等原因导致系统软件无法进行下一步动作时,自动温度补偿软件就会在当前的温度补偿点下设置中断标识,以备系统软件重新启动后,提示用户上次温度补偿流程是个未完成的过程,并询问用户是否重新进行断点处的温度补偿和压力标定。中断处理共包括3个功能:第一,重新进行中断时刻的温度标定流程。第二,重新进行中断温度下的压力标定流程。第三,重新进行中断温度下的电流标定流程。步骤9,零点漂移测试。零点漂移测试的目的就是检验经过完整温度补偿和线性修正后压力/差压变送器传感器的精度和零点是否随温度变化而发生漂移。变送器零点漂移测试的温度顺序是-15℃、25℃、85℃和25℃四个温度点。现有系统中采用升温过程中的25℃和降温过程中的25℃进行零点漂移测试,其目的是检测压力变送器传感器经过温度补偿后,在常温下零点的重复性。软件进行温漂测试的流程如下:步骤9.1,依据温漂测试温度的顺序,软件控制烘箱至检测温度,延时等待烘箱和夹具的温度达到检测温度并处于恒温稳定状态。步骤9.2,温度稳定后,控制所有补偿夹具的气路与大气相通,其目的使压力变送器传感器的测试端处于稳定的零压状态。步骤9.3,从前至后依次进行压力变送器传感器在当前温度点下的零点采样,记录并保存数据。步骤9.4,运用每一台压力变送器传感器线性修正的常系数,代入压力变送器传感器零点压力采样值和温度采样值,计算出当前温度下的零点压力输出值,记录并保存数据。步骤9.5,完成所有测试温度点后,进行零点漂移度计算,检验测试工位的变送器是否满足零漂指标要求,记录相关数据,报告用户压力/差压变送器传感器的温漂结果。步骤10,停止标定测试仪器操作,报告压力/差压变送器传感器的线性修正结果。完成零点漂移测试后,就结束了压力/差压变送器传感器的自动温度补偿流程。在软件报告温度和压力标定补偿线性修正结果前,要进行高低温烘箱的停止操作和矩阵切换卡电路的复位操作,其目的是停止所有测试仪器和补偿电路继续处于工作状态。然而,上述以程序代码为主导控制的压力变送器自动温压补偿程序的十个步骤都是在ontimer()时钟消息响应函数中完成的,为了保证压力/差压变送器传感器的温度和压力标定补偿线性修正流程是在非人为干涉下进行的。在程序设计时,首先,要严格按照程序流程进行代码的编写与调试,避免多个时钟并行的现象,否则会造成程序流程的混乱而无法实现压力/差压变送器传感器的自动温度补偿;其次,需要全面的考虑到软件在的温度补偿流程可能出现的异常信息,并在软件上加以相关的异常处理功能,防止异常信息阻碍温度补偿流程的顺利进行;最后,一旦需要增加或减少温度与压力标定数量,或者,需改变待标定的变送器类型时,程序研发人员需花费大量时间与精力进行代码的调试与修改,建立对应的温压补偿修正程序。技术实现要素:鉴于以上所述现有技术的缺点,本发明的目的在于提供一种基于数据库文件标定变送器的温压补偿方法及系统,用于解决现有技术中的自动温压补偿系统以程序代码为主导控制存在的流程固化严重、灵活性与实用性均较差的问题。为实现上述目的及其他相关目的,本发明提供一种基于数据库文件标定变送器的温压补偿方法,包括:步骤a,获取数据库内系统运行状态表内所有属性域状态值;其中,所述系统运行状态表包含起始时间、中断时间、终止时间、温度点位置、温度与运行状态;步骤b,读取所述系统运行状态表运行状态值,根据运行状态值判断是否开始变送器传感器温度与压力标定;步骤c,采集标定现场变送器传感器的温度与压力生成传感器信息记录表,其中,所述传感器信息记录表包含传感器编号、补偿夹具、位置与补偿标识使能;步骤d,对照所述传感器信息记录表,根据温度补偿表中设置的温度补偿点按照从低至高的顺序依次对变送器传感器的温度进行补偿,其中,所述温度补偿表包含各个变送器传感器的温度点位置、温度、补偿状态与恒温延时;步骤e,调用数据表获取变送器传感器的类型、压力控制器地址与驱动端口,选择管道上对应的工装夹具导入标定气压;步骤f,获取变送器传感器补偿标定的压力数据,参考压力标定表中的控压精度根据压力数据调节标定气压,对所述变送器传感器进行标定采样,其中,所述压力标定表包含压力标定顺序、量程百分比与控压精度;步骤g,获取总线切换数据表中各端口编号的驱动端口与驱动数据,写入驱动数据连通对应工号位的待标定的变送器传感器,按照温度、压力与电流的采样指令对当前工位进行标定;所述总线切换数据表包含端口编号、驱动数据线、驱动端口与驱动数据;步骤h,重复步骤g,在不同量程百分比对其它工号位的变送器传感器进行压力标定流程。本发明的另一目的在于提供一种基于数据库文件标定变送器的温压补偿系统,其用于对变送器传感器的温度与压力进行标定补偿,包括:数据库,其包含多个数据表,所述数据表包含系统运行状态表、传感器信息记录表、所述温度补偿表、压力标定设备选择表、压控设备阀门选择表、工装夹具供压选择表、压力标定表和总线切换数据表;工控机,适用于根据数据表内的运行状态、补偿变送器的类型、设备地址、工位矩阵电路控制参数、温度补偿标定顺序、压力补偿标定顺序及精度、以及原始的温度和压力标定采样数据文件生成控制指令,完成变送器传感器的温度与压力补偿标定流程,其中,所述控制指令包含第一、第二与第三控制指令;控制阀,用于根据工控机的第一控制指令开关控制阀,调节标定管道上各工位处的待标定变送器传感器的气路是否导通;压力标定设备,用于根据工控机的第二控制指令控制压力的大小,为变送器传感器提供压力标定所需压力;烘箱,用于根据工控机的第三控制指令调节烘箱温度的大小,为变送器传感器提供温度标定所需温度。如上所述,本发明的基于数据库文件标定变送器的温压补偿方法及系统,具有以下有益效果:相对于以程序代码为主导控制的温压补偿系统,本发明通过数据库与文件相融合,用户通过数据库内数据表配置,即可调节变送器温度与压力标定的数量与类型,如减少或增加温度、压力等补偿标定节点,再或者设置待标定的变送器的类型,其中,无需额外的编程与调试,更改参数即可正常进行标定。本发明的标定流程操作简单,实用性好,可根据用户的需求进行灵活设置。附图说明图1显示为本发明提供的一种变送器的温压补偿系统的框架结构图;图2显示为本发明提供的一种以程序代码为主导控制的压力变送器自动温压补偿程序的软件流程;图3显示为本发明提供的一种基于数据库文件标定变送器的温压补偿方法流程;图4显示为图3中本发明提供步骤e的详细流程图;图5显示为本发明提供的一种基于数据库文件标定变送器的温压补偿方法最佳实施例的流程;图6显示为本发明提供的一种变送器传感器补偿夹具供压气路结构图;图7显示为本发明提供一种基于数据库文件标定变送器的温压补偿系统。具体实施方式以下通过特定的具体实例说明本发明的实施方式,本领域技术人员可由本说明书所揭露的内容轻易地了解本发明的其他优点与功效。本发明还可以通过另外不同的具体实施方式加以实施或应用,本说明书中的各项细节也可以基于不同观点与应用,在没有背离本发明的精神下进行各种修饰或改变。需说明的是,在不冲突的情况下,以下实施例及实施例中的特征可以相互组合。需要说明的是,以下实施例中所提供的图示仅以示意方式说明本发明的基本构想,遂图式中仅显示与本发明中有关的组件而非按照实际实施时的组件数目、形状及尺寸绘制,其实际实施时各组件的型态、数量及比例可为一种随意的改变,且其组件布局型态也可能更为复杂。请参阅图3,本发明提供一种基于数据库文件标定变送器的温压补偿方法流程图,详述如下:步骤a,获取数据库内系统运行状态表内所有属性域状态值;其中,所述系统运行状态表包含起始时间、中断时间、终止时间、温度点位置、温度与运行状态;步骤b,读取所述系统运行状态表运行状态值,根据运行状态值判断是否开始变送器传感器温度与压力标定;步骤c,采集标定现场变送器传感器的温度与压力生成传感器信息记录表,其中,所述传感器信息记录表包含传感器编号、补偿夹具、位置与补偿标识使能;步骤d,对照所述传感器信息记录表,根据温度补偿表中设置的温度补偿点按照从低至高的顺序依次对变送器传感器的温度进行补偿,其中,所述温度补偿表包含各个变送器传感器的温度点位置、温度、补偿状态与恒温延时;步骤e,调用数据表获取变送器传感器的类型、压力控制器地址与驱动端口,选择管道上对应的工装夹具导入标定气压;步骤f,获取变送器传感器补偿标定的压力数据,参考压力标定表中的控压精度根据压力数据调节标定气压,对所述变送器传感器进行标定采样,其中,所述压力标定表包含压力标定顺序、量程百分比与控压精度;步骤g,获取总线切换数据表中各端口编号的驱动端口与驱动数据,写入驱动数据连通对应工号位的待标定的变送器传感器,按照温度、压力与电流的采样指令对当前工位进行标定;所述总线切换数据表包含端口编号、驱动数据线、驱动端口与驱动数据;步骤h,重复步骤g,在不同量程百分比对其它工号位的变送器传感器进行压力标定流程。在本实施例中,本发明以visualc++6.0为开发平台,在软件运行中应用到的数据库为microsoftofficeaccess2003,文件是基于microsoftofficeexcel2003中的*.csv数据表文件。为清楚阐明本发明数据库与文件相融合方法的详细方案,整个技术方案以一套能够容纳48台压力变送器传感器的温度和压力标定补偿系统为例,具体说明是如何应用数据库与文件相融合的方法来实现压力变送器传感器温度和压力标定补偿的自动生产过程。如图6所示,为一套装夹48台压力型变送器传感器补偿夹具供压气路结构示意图。依据压力变送器传感器温度和压力补偿标定的生产流程,从系统开始至程序运行结束会依据数据表中相关参数的状态来引导程序运行的走向。当系统开始时,获取数据库中系统运行状态表内所有属性域状态值,见表1系统运行状态表所示。表1系统运行状态表起始时间:记录新一轮压力变送器传感器进行温度和压力标定的开始时间,非系统软件的启动时间;中断时间:压力变送器传感器在进行温度和压力标定流程中,因电路、设备、通讯、或人为等因素导致系统中断,无法继续进行标定的时间点;终止时间:完成一轮完整的压力变送器传感器的温度和压力标定补偿结束的时间;温度点位置:当前压力变送器传感器温度补偿点位置,见表3温度补偿顺序表;温度:当前压力变送器传感器温度补偿点下的温度值,见表3温度补偿顺序表;运行状态:当前整套温压补偿系统的运行状态记录,0:初始状态,1:正常运行,2:运行中断,3:补偿结束;如果获取系统运行状态表中运行状态值为0,则表示当前系统需要进行新一轮压力变送器传感器的温度和压力标定;如果获取运行状态记录为1,则表示当前系统正常运行正在对压力变送器传感器的温度和压力标定;如果获取运行状态记录为2,则表示当前系统对压力变送器传感器的温度和压力标定处于中断时刻,如果获取运行状态记录为3,则表示当前系统对压力变送器传感器的温度和压力标定已结束。需要一个能够记录当前补偿夹具上对应工位相关压力传感器的信息表,见表2为传感器信息记录表;表2传感器信息记录表表2中的对应属性域的值是由压力变送器传感器温度和压力标定现场使用用户通过温压补偿系统软件输入至该表内的。其中:传感器编号:由厂商依据传感器的使用量程、材质、充灌类型、生产日期以及编码来进行分配id编码,这便于压力变送器产品的生产跟踪,更有利客户使用的查询、跟踪;补偿夹具:是用于安装压力变送器传感器的一种机械工装,依据系统的大小来分配补偿夹具的数量;位置:是指压力变送器传感器所处安装夹具上的位置;补偿标识使能:0,禁止对当前夹具上所对应传感器进行压力、温度标定采样及线性修正;1,允许对当前夹具上所对应传感器进行压力、温度标定采样及线性修正;生产用户完成待补偿压力变送器传感器的信息录入之后,便可启动温压补偿系统软件,进行标定。优选地,在所述步骤d之前,还包括:将当前的时间、以及温度补偿表中温度点位置与温度按属性保存到系统运行状态表,其中,所述温度补偿表包含各个变送器传感器的温度点位置、温度、补偿状态与恒温延时。具体地,将当前系统时间记录到表1中的起始时间属性域,同时,获取表3温度补偿顺序表中的第一个温度补偿标定温度点位置和温度记录至表1中的温度点位置和温度属性域中。通过表1系统运行状态表记录温度点位置和温度,其目的就是为了防止因外界不确定因素导致系统掉电后导致整批次压力传感器的重新补偿,如果表1中记录的温度点位置和温度,一旦系统掉电重启后便,从表1中记录的温度点继续进行压力变送器传感器的温度和压力标定补偿过程。见表3为温度补偿顺序表。表3温度补偿顺序表其中:温度点位置:整批次压力变送器传感器要完成从1至17所对应温度下的温度标定补偿;温度:整批次压力变送器传感器要进行的实际温度标定点;补偿状态:0,禁止当前温度点的温度补偿;1,允许当前温度点的温度补偿;恒温时间:每个对应温度点需要高低温试验箱所需要的恒温时间;由表3可以得出:进行本次的压力变送器传感器的温度和压力标定补偿只需要进行110、80、60、40、20、0、-20℃7个温度补偿点的补偿。在实际的生产应用中,由于不同系列压力变送器传感器需要增加或减少几个温度补偿点,所以,在应用中只需修改表3中补偿状态属性域的值即可,将需要补偿的温度点的补偿状态值设置为1,不需要温度补偿的温度点对应的补偿状态值设置为0。还有一些较为特殊的,也比较常用到情况,即变送器传感器温度补偿标定的顺序不是从高温到低温的顺序,而是从低温到高温的顺序,这种状态下,只需对温度点位置所对应的温度和补偿状态值进行修改即可,例如整批次压力变送器传感器首先进行-40℃的温度补偿,那么就将表3温度点位置1处所对应的温度值改为-40,补偿状态设置为1即可,无需改动温压补偿系统的软件代码,简单修改文件参数而改变程序的走向是即准确要高效。本案例中首先进行的是110℃温度补偿,通过rs485总线1启动高低温试验箱,并设置其温度为110℃,然后恒温120分钟(由表3中温度110℃点需要恒温时间为120分钟),使高低温试验箱内待补偿压力变送器传感器的温度无限的接近110℃。当温度条件满足时,便开始110℃温度补偿点下的压力标定。获取当前进行温压补偿的压力变送器传感器的类型,依据压力变送器传感器的类型选择压力标定设备,见表4为压力标定设备选择表:表4为压力标定设备选择表由于本批次是p2系列(表2传感器信息记录表中的传感器编号的前两个字符可知晓)压力型传感器,由表4压力标定设备选择表可知p2系列传感器的压力标定补偿量程范围为0-100kpa,结合图6压力型变送器传感器补偿夹具供压气路示意图可知,该批次p2系列压力传感器应选用压力标定设备ruska7250压力控制器的量程也应该为0-100kpa,即图6量程为100kpa的ruska7250压力控制器。如图4所示,为本发明提供步骤e的详细流程图,具体包括:步骤e1,获取变送器传感器的类型,根据其类型在压力标定设备选择表匹配压力标定设备;其中,所述压力标定设备选择表包含传感器类型、低端量程、单位与压力控制器地址;步骤e2,根据压控设备阀门选择表中压力控制器地址控制电磁阀开关,使得标定气压传输到管道上;其中,所述压控设备阀门选择表包含压力控制器地址、阀门编号、驱动端口与驱动数据;步骤e3,根据工装夹具供压选择表的驱动端口写入驱动数据,选择管道上对应的工装夹具导入标定气压,其中,所述工装夹具供压选择表包含夹具编号、阀门编号、驱动端口与驱动数据。第一,从表4获取系统需要gpib总线地址为4供压设备,根据表5中控压设备选择信息和表6中的工装夹具供压选择信息将图3中的球形电磁阀v1、v2、v3关闭,球形电磁阀v4、v5、v6、v7、v8打开,其目的是将供压源提供的气体压力通过ruska7250压力控制器后输出标准的预先定义好的压力标定气压,经过标定管道和球形电磁阀v4、v5、v6、v7、v8后到达压力变送器传感器的工装夹具上,使工装夹具上的每一台待压力标定的压力传感器均接受到由ruska7250压力控制器输出给定的压力,见表5控压设备阀门选择表和表6工装夹具供压选择表;表5控压设备阀门选择表压力控制器地址阀门编号驱动端口驱动数据备注4v4160x085v3160x046v2160x027v1160x01其中:压力控制器地址:该项为自动温压补偿系统软件与压力控制器之间实现通讯的gpib总线地址;阀门编号:该项是对压力控制器设备输出气压走向选择控制的球形电磁阀,用来实现ruska7250压力器与压力标定工装夹具之间气路气压走向的选通或是关闭的控制球形电磁阀;驱动端口:该端口为计算机pci总线输出控制的pio-d144/d168接口卡。pci总线可以输出控制pio-d144/d168接口卡的端口范围0-20号端口,并且每个端口共有8位的数据总线,在该本案例中选择端口0-15用于补偿工位rs485总线切换控制,端口16-20用于压力标定的供压系统中球形电磁阀的控制端口;驱动数据:用于控制压力控制器设备输出气压走向选择球形电磁阀开通与关闭;在实际的应用,如果通过pci总线输出向pio-d144/d168接口卡中的端口16中写入数据ox08,则表示球形电磁阀v4处于开通状态,球形电磁阀v1、v2、v3处于关闭状态,此时,工装夹具的供压设备为gpib总线地址为4的控压设备输出供给。注明:表5中的阀门编号、驱动端口、驱动数据都是在研发设计与应用中依据系统所能容纳压力传感器的多少和压力标定管道设计中需要球形阀门的数量进行整理并设计的一个数据表格;表6工装夹具供压选择表夹具编号阀门编号驱动端口驱动数据备注1v5170x102v6170x203v7170x404v8170x80其中:夹具编号:该项是对补偿系统内部安装压力变送器传感器的整套工装夹具压按照实际生产流程中的应用顺序进行编号,便于通过对球形电磁阀的驱动控制实现供压源对待压力标定的传感器进行供压;阀门编号:该项是对压力控制器设备输出气压走向工装夹具选择控制的球形电磁阀,用来实现ruska7250压力器与压力标定工装夹具之间气路气压走向的选通或是关闭;驱动端口:该端口为计算机pci总线输出控制的pio-d144/d168接口卡。pci总线可以输出控制pio-d144/d168接口卡的端口范围0-20号端口,并且每个端口共有8位的数据总线,在该本案例中选择端口0-15用于补偿工位rs485总线切换控制,端口16-20用于压力标定的供压系统中球形阀门的控制端口;驱动数据:用于控制压力控制器设备输出气压走向工装夹具的开通与关闭;在实际的应用,如果通过pci总线输出向pio-d144/d168接口卡中的端口17中写入数据ox10,则表示球形电磁阀v5处于开通状态,球形电磁阀v6、v7、v8处于关闭状态,此时工装夹具1上的所有待压力标定的传感器所供给的压力与压力控制器输出的压力完全相同,而工装夹具v6、v7、v8前端的球形电磁阀处于关闭状态,则表明工装夹具6、7、8上的待压力标定的传感器处于无压力供给状态。在本案例中系统内部的4套工装夹具上均安装有待温压补偿的压力变送器传感器,所以需要给4套工装夹具设备供压,则需要将球形电磁阀v5、v6、v7、v8设置为开通状态,即通过pci总线输出向pio-d144/d168接口卡中的端口17中写入数据oxf0(0x10+0x20+0x40+0x80)。注明:表6中的夹具编号、驱动端口、驱动数据也都是在研发设计与应用中依据系统所能容纳工装夹具的数量,待温压补偿压力变送器传感器的多少和压力标定管道设计中需要球形阀门的数量进行整理并设计的一个数据表格;第二,调用表7,获取p2系列压力传感器的第1个压力补偿标定的压力数据,向gpib总线地址为4的ruska7250压力控制器中写入第1个压力补偿标定的压力数据和ruska7250压力控制输出控制压力精度,控压延时,使整套供压系统内部所有管道与工装夹具的供给压力为p2系列压力传感器的第1个压力补偿标定的压力数据,并且控压精度满足当前点中给出的控压精度,准备压力标定采样,详见表7为p2系列压力标定表。表7p2系列压力标定表压力标定顺序量程百分比控压精度备注110.00120.90.00130.80.00140.70.00150.60.00160.50.00170.40.00180.30.00190.20.001100.150.002110.10.002120.050.005130.00.005其中:压力标定顺序:对在线待温压补偿的压力传感器压力标定顺序的排序,通常是按照排序从小到大的顺序进行压力标定的流程;量程百分比:该表为p2系列压力型传感器的压力补偿标定数据表,最大标定值为100kpa,所以第1个压力补偿标定点的压力为100×1=100kpa,第2个压力补偿标定点的压力为100×0.9=90kpa……以此类推至其它的压力补偿标定点压力值,直到第13个压力补偿标定点的压力零为止;控压精度:指ruska7250压力控制器输出恒定压力的精度;在工程使用中,压力变送器传感器依据自身的机械结构就分为压力型和差压型,对于每一种类型下又会依据实际的使用量程分为多种系列,本案例中只选择了压力型p2系列的传感器进行了压力标定流程的阐述,对于其它类型的压力变送器传感器的压力标定文件设计基本相同,可能出现不同之处就是压力标定点的选取不同,或是压力标定点的顺序不同。第三,获取rs485总线切换数据表(见表8)中的rs485端口编号为1的驱动端口和驱动数据,并通过计算机pci总线接口向pio-d144/d168接口卡中的端口0中写入数据ox01,其它端口写入数据ox00,实现计算机rs485总线接口端与在线待温压补偿的压力传感器的工位01处的rs485总线接口相连通;向工位01处的压力变送器传感器发送温度、压力和电流的温度采样指令,完成当前工位处温度、压力与电流的标定流程;表8rs485总线切换数据表第四,重复步骤第三,完成当前量程百分比为1的压力标定点下其它工位处压力变送器传感器温度、压力和电流的采样,并将原始的采样滤波数据保存至以当前工位1处表号命名的.csv文件中;第五,重复步骤第二至第四,完成除量程百分比为1外的其它量程百分比压力标定点的压力标定流程。如图5所示,为本发明为本发明提供的一种基于数据库文件标定变送器的温压补偿方法最佳实施例的流程,在上述实施例基础上,还包括:步骤i,读取对应工号位的变送器传感器的温度与压力标定的原始数据,根据压力变送器传感器的线性修正数据模型进行修正计算,将计算的结果对应保存到数据库。具体地,依据压力变送器传感器的线性修正数据模型,读取对应工位处压力变送器传感器温度和压力标定流程中的原始数据(存在在对应工位处的*.csv文件)进行修正计算,并将修正结构保存至数据库的线性修正系数表中,通过工控机报告用户温压补偿的结束。如图7所示,为本发明提供一种基于数据库文件标定变送器的温压补偿系统,用于对变送器传感器的温度与压力进行标定补偿,包括:数据库1,其包含多个数据表,所述数据表包含系统运行状态表、传感器信息记录表、所述温度补偿表、压力标定设备选择表、压控设备阀门选择表、工装夹具供压选择表、压力标定表和总线切换数据表;工控机2,适用于根据数据表内的运行状态、补偿变送器的类型、设备地址、工位矩阵电路控制参数、温度补偿标定顺序、压力补偿标定顺序及精度、以及原始的温度和压力标定采样数据文件生成控制指令,完成变送器传感器的温度与压力补偿标定流程,其中,所述控制指令包含第一、第二与第三控制指令;控制阀3,用于根据工控机的第一控制指令开关控制阀,调节标定管道上各工位处的待标定变送器传感器的气路是否导通;压力标定设备4,用于根据工控机的第二控制指令控制压力的大小,为变送器传感器提供压力标定所需压力;烘箱5,用于根据工控机的第三控制指令调节烘箱温度的大小,为变送器传感器提供温度标定所需温度。工控机2,其中该工控机设备硬件、软件的技术要求如下:硬件技术要求:硬盘容量≥320gb、内存≥1gb、pci总线插槽≥5个、9芯全串口2个;软件技术要求:操作系统优选为windowsxp,且在该操作系统下安装visualc++6.0开发平台,microsoftoffice2003,aglient82350bpcigpib接口卡驱动和pio-d144/d168接口卡驱动;数据库1是基于microsoftofficeaccess2003,文件是基于microsoftofficeexcel2003中的*.csv数据表文件,另外,所述数据库还可基于其它excel、sql、db软件构建平台,用于存储变送器传感器的各项参考数据。在图7结构基础上,还包括工装夹具,所述工装夹具连接控压设备,将输出的预设压力通过工装夹具传递到其上每台待标定的变送器传感器。综上所述,本发明相对于以程序代码为主导控制的温压补偿系统,通过数据库与文件相融合,用户通过数据库内数据表配置,即可调节变送器温度与压力标定的数量与类型,如减少或增加温度、压力等补偿标定节点,再或者设置待标定的变送器的类型,其中,无需额外的编程与调试,更改参数即可正常进行标定。本发明的标定流程操作简单,实用性好,可根据用户的需求进行灵活设置。所以,本发明有效克服了现有技术中的种种缺点而具高度产业利用价值。上述实施例仅例示性说明本发明的原理及其功效,而非用于限制本发明。任何熟悉此技术的人士皆可在不违背本发明的精神及范畴下,对上述实施例进行修饰或改变。因此,举凡所属
技术领域:
中具有通常知识者在未脱离本发明所揭示的精神与技术思想下所完成的一切等效修饰或改变,仍应由本发明的权利要求所涵盖。当前第1页12