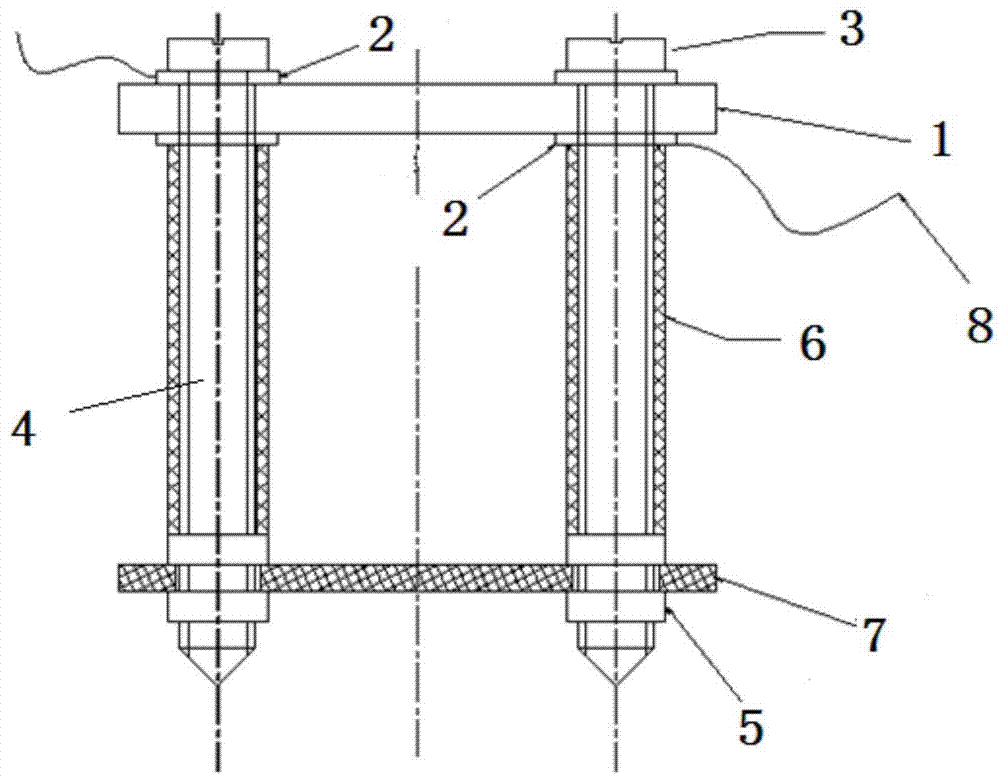
本发明属于金属腐蚀防护
技术领域:
,具体涉及一种电流作用下电气设备用铜材料的腐蚀加速测试评价方法。
背景技术:
:随着全球经济的快速发展,金属材料被越来越多的应用到电气专备及工作设施之中,金属材料的腐蚀和防护问题也逐渐暴露出来。世界各国每年因各类腐蚀带来的直接经济损失高达其国民生产总值的2%~4%,而电气设备用铜材料作为电气设备内部元器件的重要组成部分,铜及其合金的失效无疑会使设备内部暴露在更为恶劣的环境中,为了避免电气设备和工作设施所用的铜材料因腐蚀破坏而造成的早期失效,减少损失,对金属材料的腐蚀行为进行研究十分必要。目前国内外对于金属腐蚀行为的研究采用室内模拟试验和室外暴露试验两种方式,室外暴露试验方法周期较长,试验参数不能控制,且由于户外条件的差异,得出的户外暴露试验结果往往不具有普遍性。室内模拟试验以腐蚀类型分别对金属进行均匀腐蚀、点腐蚀、晶间腐蚀、缝隙腐蚀和应力腐蚀的研究,这些腐蚀研究考虑了气候因素及机械外力对腐蚀的影响,但通常设备带电后会有不同程度的漏电流通过,此电流的很小但是会加速金属的腐蚀。因此,有必要综合考虑影响铜及其合金材料腐蚀的因素,提供一种包含小电流及环境腐蚀性气体二氧化硫、盐雾及放置角度等因素的多因素复合试验方法,对电气设备用铜及其合金材料的腐蚀行为进行测试评价,以便对电气设备的金属腐蚀进行预防和维护,延长电气设备的使用寿命,减少资源浪费和降低企业生产成本。技术实现要素:本发明所要解决的技术问题是提供一种电流作用下电气设备用铜材料的腐蚀加速测试评价方法,考虑了电气设备用铜及其合金材料在实际使用过程中带电运行,存在泄漏电流加载在铜及其合金材料的情况,能更好地对铜及其合金材料的实际使用情况进行腐蚀计算,该测试方法结果准确,适用性强。解决上述技术问题,本发明所采用的技术方案如下:一种电流作用下电气设备用铜材料的腐蚀加速测试评价方法,包括以下步骤:步骤s1、选取电气设备用铜材料样品制备测试样品,并对样品进行表面处理;步骤s2、制作试样;将试样进行分组,每组分别与不同的标准电阻串联,形成不同试样组;步骤s3、将步骤2制作的不同试样组依次并联之后与恒流源串联一起形成回路;选取梯度电流,各试样组分别通入梯度电流中不同电流值,在电流作用下进行二氧化硫盐雾循环试验,根据测得各试样组进行二氧化硫盐雾循环试验前后的电阻值,计算不同试样组的腐蚀深度△h,并筛选敏感电流is;步骤s4、将敏感电流is对应的该组试样组,通电流is进行二氧化硫盐雾循环试验,计算敏感电流is对应的该组试样组的腐蚀深度△h;步骤s5、计算试样组的腐蚀速率c,通过腐蚀速率即可对工业环境下电气设备用铜材料的腐蚀情况进行评价。本发明中,所述铜材料为铜及其合金材料。所述步骤s1中测试样品样品尺寸为100mm*10mm*3mm,样品两端打孔,孔径均为3mm。所述步骤s1中样品进行表面处理包括对非镀层铜样品表面处理和铜镀层样品表面处理;对于非镀层铜样品表面处理,包括以下步骤:步骤s1a、用180号砂纸将试片的四边、角及孔打磨光亮;步骤s1b、用200号砂纸干打磨,打磨后的试片存放在干燥器中待洗;步骤s1c、用镊子夹取脱脂棉将打磨后的试片在溶剂汽油中擦洗;步骤s1d、将试片浸入无水乙醇中,在室温下进行超声清洗10分钟;步骤s1e、将试片在热无水乙醇50-60℃中擦洗干净;步骤s1f、用冷风吹干样品,然后将试片置于干燥器中待用。对于铜镀层样品表面处理,依次按照步骤s1d—步骤s1f进行表面处理。所述步骤s2中试样的制作为将样品用绝缘螺丝、绝缘柱、绝缘螺母通过样品两端的孔进行固定,在绝缘柱外围套塑料套管,形成试样。所述步骤s2中每三个试样分为一组,所述标准电阻的电阻值为1ω、10ω、100ω、1kω。所述步骤s3中梯度电流分别为1ma、10ma、100ma、1000ma。本发明中,在电流作用下二氧化硫盐雾循环试验一个循环周期为24h,包括先通恒定直流电流进行二氧化硫盐雾循环试验12h,再断电静置进行二氧化硫盐雾循环试验12h。进一步地,所述二氧化硫盐雾循环试验在35±2℃下进行,每6h进行一次持续喷盐雾并接入二氧化硫气体操作,操作时间持续1h,半小时喷盐雾,半小时通入二氧化硫气体。所述盐雾中nacl浓度为5%,盐雾沉降量为1.0-2.0ml/80cm2*h;所述二氧化硫气体的接入量为每300l试验箱中,加入2l二氧化硫气体。所述试样组中的不同试样分别采取倾斜15°、30°、45°放置。所述试样组完成二氧化硫盐雾循环试验后进行后处理。进一步地,所述后处理为试样组在室温条件下用酸液清洗五分钟,然后吸干表面水分并擦干净腐蚀产物,最后用无水乙醇对试样进行清洗并用冷风吹干。所述酸液是质量分数为5%-10%的硫酸溶液或质量分数为15%-20%的盐酸溶液。所述步骤s3中敏感电流is通过以下方式获得:比较不同试样组的腐蚀深度△h大小,选取腐蚀深度△h最大值所对应的电流值作为敏感电流is。所述步骤s3中在电流作用下二氧化硫盐雾循环试验进行2个循环周期。所述步骤s4中在电流is作用下二氧化硫盐雾循环试验进行10个循环周期。本发明中,不同试样组的腐蚀深度△h,通过以下方式得到:式中:△h—腐蚀深度,mm;a,b—试样片的原始宽度和厚度,mm;r'n—试样组试验后的平均电阻,ω;rn—试样组初始平均电阻,ω。进一步地,所述试样组初始平均电阻rn为对试样组进行通电流前试样组中每个试样原始电阻值总和的平均值。所述试样组试验后的平均电阻r'n为试样组进行通电流二氧化硫盐雾试验及后处理后试样组中每个试样电阻值总和的平均值。所述步骤s5中试样组的腐蚀速率通过以下方式得到:式中:c—腐蚀速度,mm/a;t—试验时间,h;8760—年小时数。本发明方法为在常规盐雾加速试验的基础上考虑工业环境中二氧化硫腐蚀性气体,提出二氧化硫与盐雾交替施加进行加速试验,并考虑电气设备通常均为带电运行,在试验过程中对试验通入不同等级电流,从不同放置角度对铜片进行腐蚀加速试验。由于加速试验对铜片腐蚀的影响会使铜片的截面积变小电阻增大,通过试验前后电阻的变化,进一步计算出腐蚀深度,判别出在该环境条件下电流对加速试验的敏感值,结合常规实验室经常采用的失重法测量腐蚀速率与f分布对电阻法测量铜片腐蚀速率方法进行评测。与现有技术相比,本发明具有以下有益效果:(1)本发明方法考虑了电气设备用铜及其合金材料在实际使用过程中带电运行中存在泄漏电流加载在铜及其合金材料的情况,能更好地对铜及其合金材料的实际使用情况进行腐蚀计算,以便更好地对电气设备的金属腐蚀进行预防和维护。(2)本发明综合了影响电气设备铜及其合金材料的多个因素,对铜及其合金材料进行多因素复合模拟试验,在采用盐雾加速试验的基础上,增加了电流、二氧化硫、温度三个试验因素,并通过不同放置角度不同电流作用下的二氧化硫盐雾加速试验,筛选出对腐蚀影响最大的敏感电流,通过电阻的变化值进一步计算出铜及其合金的腐蚀速率,该测试方法结果准确,适用性强。(3)本发明采用的试验电流小,试验设备操作简单,安全隐患较低。附图说明下面结合附图和具体实施例对本发明的技术方案作进一步的详细说明:图1为本发明制作试样的结构示意图;图2为本发明测试电路的电流敏感值筛选连接原理图;图3为本发明腐蚀加速试验电路连接原理图;图中附图标记说明:1-样品;2-接线柱;3-绝缘螺丝;4-绝缘柱;5-绝缘螺母;6-塑料套管;7-pvc板;8-导线。具体实施方式如图1-3所示的一种电流作用下电气设备用铜材料的腐蚀加速测试评价方法,包括以下步骤:步骤s1、选取电气设备用铜材料样品制备测试样品,样品尺寸为100mm*10mm*3mm,样品两端打孔,孔径均为3mm。对于非镀层铜样品,依次按照以下步骤进行表面处理:步骤s1a、用180号砂纸将试片的四边、角及孔打磨光亮;步骤s1b、用200号砂纸干打磨,打磨后的试片存放在干燥器中待洗;步骤s1c、用镊子夹取脱脂棉将打磨后的试片在溶剂汽油中擦洗;步骤s1d、将试片浸入无水乙醇中,在室温下进行超声清洗10分钟;步骤s1e、将试片在热无水乙醇50℃中擦洗干净;步骤s1f、用冷风吹干样品,然后将试片置于干燥器中待用。对于铜镀层样品,依次按照步骤s1d-步骤s1f进行表面处理。样品经表面处理后放入干燥器中存放备用。步骤s2、制作试样:将样品1从干燥器内取出后,接线柱2放置在样品1两侧夹住样品1,绝缘螺丝3穿过接线柱2和样品1上的孔将样品1固定在两根套设有塑料套管6的绝缘柱4顶部,塑料套管6对接线柱2和样品1起支撑作用。两根绝缘柱4底部通过pvc板7连接,绝缘螺母5将pvc板7固定在绝缘柱4上。两根绝缘柱4上的接线柱2分别与导线8连接。试样具体结构如图1所示。取三个相同规格试样(无镀层),依次串联后再与标准电阻串联,形成试样组,依照此法做四组试样组,每组串联的电阻分别为1ω、10ω、100ω、1kω。有镀层试样的制作同无镀层试样。步骤s3、将步骤2制作的不同试样组按照图2依次并联之后与恒流源串联一起形成回路,对试样进行通流前,测量每一个试样片的原始电阻rn(mω),试样片的原始电阻rn测试应在样品取出干燥器1h内进行,rn,n=1,2,…,24;具体见表1。取无镀层和有镀层试样组各四组,试样片依次编号1、2、……、23、24,并分为a、b、……、g、h八组,其中1-3号试样为无镀层a组,4-6号试样为无镀层b组,7-9号试样为无镀层c组,10-12号试样为无镀层d组,13-15号试样为有镀层e组,16-18号试样为有镀层f组,19-21号试样为有镀层g组,22-24号试样为有镀层h组。a、b、……、g、h八组串联的标准电阻分别为1kω、100ω、10ω、1ω、1kω、100ω、10ω、1ω。根据下式计算八个试样组的原始平均电阻ra,rb,……,rh。表1每个试样片的原始电阻值(单位:mω)r1100.3r2100.5r3100.4r4100.8r5100.6r6100.2r7100.2r8100.4r9100.6r10100.6r11100.5r12100.7r13100.1r14100.2r15100.3r16100.3r17100.4r18100.2r19100.4r20100.3r21100.3r22100.1r23100.2r24100.3计算八组试样组的平均原始电阻rn(mω),具体见表2:表2每个试样组的平均电阻(单位:mω)选取四种直流电流i1、i2、i3、i4,i1=1ma、i2=10ma、i3=100ma、i4=1000ma。将八组试验组按图2进行连接,恒流源通电流2222ma,则a、b、……、g、h八组各支路的电流分别为1ma、10ma、100ma、1000ma、1ma、10ma、100ma、1000ma。由于试验回路中各试样组分别串联步骤s2中标准电阻,且试验电阻为欧姆级,各试样为毫欧级,根据串联电路中电流值相同,可近似认为各分支回路的电压降等于标准电阻上的电压降,由于各分支回路电压降相等,则恒流源提供的总电流为各分支电流的和,则图2中总电流值为2222ma。在35±2℃下,a、b、……、g、h八组试样组通恒定直流电流2222ma进行二氧化硫盐雾循环试验12h,每6h进行一次持续喷盐雾并接入二氧化硫气体操作,操作时间持续一小时,半小时喷盐雾,半小时通入二氧化硫气体。每一试验周期开始时的二氧化硫理论浓度为体积百分比0.67%,即在容积为300l的试验箱中,每试验周期加入2l二氧化硫气体。每组试样组的三个试样分别采取倾斜15°、30°、45°放置,然后断电,在35±2℃下进行断电静置二氧化硫盐雾循环试验12h,其中nacl浓度为5%,盐雾沉降量为1.0-2.0ml/80cm2*h。以此作为1个循环,共进行2个循环,共试验48h。二氧化硫盐雾循环试验结束后,将试样组取出,室温条件下用质量分数5%-10%的硫酸溶液清洗五分钟后,然后用滤纸吸干表面水分并用橡皮擦干净腐蚀产物,最后用无水乙醇对试样进行清洗并用冷风吹干。采用直流微电阻仪测试每一个试样试验后的电阻r'n,n=1、2、……、23、24,见表3。参照平均原始电阻的计算方法计算a、b、……、g、h八组试样组试验后的平均电阻r'n(mω),见表4。表32个循环试验后每个试样片的电阻(单位:mω)表42个循环试验后每个试样组的平均电阻(单位:mω)rarbrcrdrerfrgrh101.50105.50111.73111.93101.20105.20111.33111.67然后计算a、b、……、g、h八组试样组的腐蚀深度△h,具体见表5:式中:△h—腐蚀深度,mm;a,b—试样片的原始宽度和厚度,mm;r'n—试样组试验后的平均电阻,ω;rn—试样组初始平均电阻,ω。比较无镀层试样组△ha、△hb、△hc、△hd,有镀层试样组△he、△hf、△hg、△hh,选取最大值者对应的电流值作为敏感电流is。表5每个试样组的腐蚀深度(单位:mm)△ha△hb△hc△hd△he△hf△hg△hh0.010.040.100.100.010.040.100.10依上表可以看出△hc=△hd>△hb>△ha,△hg=△hh>△hf>△he,而c组电流100ma小于d组1000ma,g组电流100ma小于h组1000ma,因此选取第二组和第六组所施加的电流作为敏感电流,即is=100ma。步骤s4、将敏感电流is对应的该组试样组重新编号无镀层试样组为s1、s2、s3,有镀层试样组为s4、s5、s6,用分析天平对试样片进行称重,记为m1、m2、m3、m4、m5、m6,具体见表7、表8,置于盐雾箱中,在35±2℃下,按图3将试样依次串联,通电流is进行二氧化硫盐雾循环试验12h,每6h进行一次持续喷盐雾并接入二氧化硫气体操作,操作持续一小时,半小时喷盐雾,半小时通入二氧化硫气体。每一试验周期开始时的二氧化硫理论浓度为体积百分比0.67%,即在容积为300l的试验箱中,每试验周期加入2l二氧化硫气体。每组试样组的三个试样分别采取倾斜15°、30°、45°放置,然后断电,在35±2℃下进行断电静置二氧化硫盐雾循环试验12h,其中nacl浓度为5%,盐雾沉降量为1.0-2.0ml/80cm2*h。以此作为1个循环,共进行10个循环,共试验240h。二氧化硫盐雾循环试验结束后,将试样组取出,室温条件下用质量分数5%-10%的硫酸溶液或15%-20%的盐酸溶液清洗五分钟后,然后用滤纸吸干表面水分并用橡皮擦干净腐蚀产物,最后用无水乙醇对试样进行清洗并用冷风吹干。用分析天平对每个试样片进行称重,记为m1’、m2’、m3’、m4’、m5’、m6’,具体见表7、表8;采用直流微电阻仪测试每一个试样试验后的电阻,见表6。参照平均原始电阻的计算方法计算无镀层试样组和有镀层试样组试验后的平均电阻r(mω):表610个循环试验后每组试样片的电阻值(单位:mω)r7(s1)119.4r8(s2)118.5r9(s3)119.3r19(s4)118.6r20(s5)118.8r21(s6)118.6r无=119.07mω;r有=118.67mω。然后计算两组试样组的腐蚀深度△h:△h无=0.072mm;△h有=0.072mm。其中每个试样的腐蚀深度为:无镀层△hs1=0.080mm,△hs2=0.060mm,△hs3=0.075mm;有镀层△hs4=0.071mm,△hs5=0.074mm,△hs6=0.072mm。步骤s5、计算试样组的平均腐蚀速率c,计算公式如下:式中:c—腐蚀速率,mm/a;t—试验时间,h;8760—年小时数。c无=2.63mm/a;c有=2.63mm/a。其中每个试样的腐蚀速率分别为:无镀层:cs1=2.58mm/a,cs2=2.62mm/a,cs3=2.54mm/a;有镀层:cs4=2.71mm/a,cs5=2.67mm/a,cs6=2.67mm/a。通过腐蚀速率即可对工业环境下电气设备用铜材料的腐蚀情况进行评价。用f分布对本发明电流作用下电气设备用铜材料的腐蚀加速测试评价方法进行评价。由于失重法测量腐蚀速率:cz=m0-m1/st式中:cz—金属失重腐蚀速率,g/(m2·h);m0,m1—腐蚀前后金属的质量,g;s—暴露在腐蚀介质中的表面积,m2;t—试样的腐蚀时间,h。表7无镀层试样组腐蚀前后质量(单位:g)表8有镀层试样组腐蚀前后质量(单位:g)用失重法计算出腐蚀速率如下所示:无镀层:cz1=2.63g/(m2·h),cz2=2.67g/(m2·h),cz3=2.58g/(m2·h);有镀层:cz4=2.75g/(m2·h),cz5=2.71g/(m2·h),cz6=2.71g/(m2·h)。用单位时间的腐蚀深度表示金属的腐蚀速率,换算公式如下:ct=cz*365*24*10/104*ρ=8.76*cz/ρ式中:ct—腐蚀速率,mm/a;ρ—试验金属的密度,g/cm3;cz—金属失重腐蚀速率,g/(m2·h)。则每个试样的腐蚀速率为:无镀层:ct1=2.58mm/a,ct2=2.62mm/a,ct3=2.54mm/a;有镀层:ct4=2.71mm/a,ct5=2.67mm/a,ct6=2.67mm/a。计算出用两种方法测得的腐蚀速率f值其中:无镀层f=1.14;有镀层f=1.73查f分布表,置信度为95%时f表=9.28,表明用本发明的电阻法测量的腐蚀速率与用失重法测量的数据没有显著差异,测试结果准确。上述实施例仅本发明的较佳实施例,但不作为对本发明保护范围的限制,在不脱离本发明基本技术思想前提下,本发明还可以做出其它多种形式的等效修改、替换或变更,均落在本发明的保护范围之中。当前第1页12