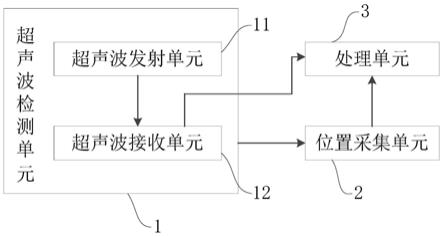
本发明属于无损检测领域,具体地说,涉及一种工件缺陷的检测装置及其检测方法。
背景技术:碳纤维复合材料质轻、力学性能优良、可设计性强,但碳纤维复合材料在制造过程中或者在使用过程中会形成各种形式的缺陷,因此,研究碳纤维复合材料应用构件中缺陷的检测与识别手段极为重要。而碳纤维复合材料的低导电和低热导率特性加大了无损探伤的难度,碳纤维结构件通常较为复杂且受力作用极易产生微小裂纹以及分层现象,分层缺陷发生在碳纤维复合材料内部层与层之间,不容易直接观察和检测;目前,检测材料内部缺陷的方法一般利用超声检测技术,超声检测是指利用超声波对内部缺陷进行检查的一种无损探伤方法,用发射探头向工件表面通过耦合剂发射超声波,超声波在构件内部传播时遇到不同界面将有不同的反射信号(回波),利用不同反射信号传递到探头的时间差,可以检查到工件内部的缺陷。根据在荧光屏上显示出的回波信号的高度、位置等可以判断缺陷的大小,不能显示出缺陷的三维立体图像,超声检测直观性较差。有鉴于此特提出本发明。
技术实现要素:本发明要解决的技术问题一在于克服现有技术中超声检测直观性较差的不足,提供一种锁定机构及过滤器。为解决上述技术问题,本发明采用技术方案的基本构思是:本发明的一方面,提供工件缺陷的检测装置,包括用于检测工件缺陷数据信息的超声检测单元,位置采集单元以及处理单元;所述位置采集单元与所述超声检测单元连接,用于采集超声检测单元在工件检测面上移动的位置信息;所述处理单元分别与所述位置采集单元以及所述超声检测单元连接,用于将工件缺陷的数据信息与该缺陷在特定位置的位置信息一一对应转换成缺陷的可视三维图像。进一步地,所述超声检测单元包括用于发射超声波至工件内部的超声波发射单元,以及超声波接收单元;所述超声波接收单元用于接收工件反射回来的超声波,并将超声波信息信号输出;所述处理单元与所述超声波接收单元连接,用于接收超声波信息信号;优选地,所述超声检测单元包括一超声波探头。进一步地,所述位置采集单元包括第一位置记录仪、第二位置记录仪以及数据采集器;
所述第一位置记录仪以及所述第二位置记录仪与所述超声波探头连接,用于分别记录所述超声波探头在x轴方向以及y轴方向上的位置,并将各自的位置信息输出;所述数据采集器分别与所述第一位置记录仪以及第二位置记录仪连接,用于采集超声波探头的位置信息,并将位置信息信号输出;所述处理单元与所述数据采集器连接,用于接收位置信息信号。进一步地,所述处理单元包括具有操作面板以及显示面板的处理器;所述处理器将超声波信息信号以及位置信息信号一一对应转换成缺陷的三维图像;所述显示面板用于显示缺陷的三维图像。本发明的另一个目的在于提供一种工件缺陷的检测方法,以增强缺陷检测的直观性,该工件缺陷的检测方法采用上述技术方案提供的工件缺陷检测方法,包括:处理单元将超声检测单元检测的工件缺陷的数据信息与位置采集单元采集的超声检测单元在工件检测面上的位置信息一一对应转换成缺陷的三维图像。进一步地,超声波探头检测工件缺陷的数据信息,并将检测到的数据信息输出;第一位置记录仪以及第二位置记录仪分别记录超声探头在x、y轴的位置信息,并将各自的位置信息输出;数据采集器采集x、y轴方向的位置信息,并将x、y轴方向的位置信息信号输出;处理器接收超声波信息信号以及x、y轴方向的位置信息信号,以及处理器从超声波探头读取缺陷相对检测面的埋深,且将该埋深与x、y轴方向的位置信息相组合得到缺陷在工件中的三维空间位置信息;处理器将数据信息信号以及相应的三维空间位置信息一一对应转换成缺陷的三维图像。进一步地,包括:将生成的缺陷的三维图像进行图像二值化,得到缺陷的三维二值化图像。进一步地,包括:处理器接收缺陷数据信息信号,将缺陷的数据值对应不同的rgb颜色值,再将缺陷的数据值对应位置信息。进一步地,包括:s1:将待测工件置于操作台上并固定;s2:在超声波探头接触工件检测面的表面涂上耦合剂;s3:选择检测面的一个位置,超声波探头对该位置的检测面进行扫描,执行步骤s5,该位置检测结束,执行步骤s4;s4:手动将超声波探头移动至下一位置继续检测,执行步骤s5;s5:处理器将接收到的缺陷数据信息和缺陷在该位置的位置信息一一对应转换成三维图像;优选地,所述耦合剂为油或凡士林。进一步地,包括:规定超声波探头由上一位置移动到下一位置进行检测的时间间隔。采用上述技术方案后,本发明与现有技术相比具有以下有益效果。1.本发明提供的检测装置包括超声检测单元,位置采集单元以及处理单元;位置
采集单元与超声检测单元连接,处理单元分别与位置采集单元以及超声检测单元连接,处理单元将工件缺陷的数据信息与该缺陷在特定位置的位置信息一一对应转换成缺陷的三维图像,增强了缺陷的直观性;2、本发明提高的检测方法包括处理单元将超声检测单元检测的工件缺陷的数据信息与位置采集单元采集的超声检测单元在工件检测面上的位置信息一一对应转换成缺陷的三维图像,增强了缺陷的直观性;3、本发明提高的检测方法包括将得到的三维图形进行图像二值化,图像的二值化使图像中数据量大为减少,从而能凸显出目标的轮廓。下面结合附图对本发明的具体实施方式作进一步详细的描述。
附图说明
附图作为本发明的一部分,用来提供对本发明的进一步的理解,本发明的示意性实施例及其说明用于解释本发明,但不构成对本发明的不当限定。显然,下面描述中的附图仅仅是一些实施例,对于本领域普通技术人员来说,在不付出创造性劳动的前提下,还可以根据这些附图获得其他附图。在附图中:图1是本发明实施例提供的工件缺陷的检测装置的流程图;图2是本发明实施例提供的工件缺陷的检测装置的结构示意图;图3是本发明一种实施例提供的工件缺陷的检测方法的流程图;图4是本发明另一种实施例提高的工件缺陷的检测方法的流程图。图标:1
‑
超声检测单元;11
‑
超声波发射单元;12
‑
超声波接收单元;13
‑
超声波探头;2
‑ꢀ
位置采集单元;21
‑
第一位置记录仪;22
‑
第二位置记录仪;23
‑
数据采集器;3
‑
处理单元;31
‑ꢀ
处理器;32
‑
显示面板;33
‑
操作面板;4
‑
工件;5
‑
操作台。需要说明的是,这些附图和文字描述并不旨在以任何方式限制本发明的构思范围,而是通过参考特定实施例为本领域技术人员说明本发明的概念。
具体实施方式
为使本发明实施例的目的、技术方案和优点更加清楚,下面将结合本发明实施例中的附图,对实施例中的技术方案进行清楚、完整地描述,以下实施例用于说明本发明,但不用来限制本发明的范围。在本发明的描述中,需要说明的是,术语“上”、“下”、“前”、“后”、“左”、“右”、“竖直”、“内”、“外”等指示的方位或位置关系为基于附图所示的方位或位置关系,仅是为了便于描述本发明和简化描述,而不是指示或暗示所指的装置或元件必须具有特定的方位、以特定的方位构造和操作,因此不能理解为对本发明的限制。在本发明的描述中,需要说明的是,除非另有明确的规定和限定,术语“安装”、“相连”、“连接”应做广义理解,例如,可以是固定连接,也可以是可拆卸连接,或一体地连接;可以是机械连接,也可以是电连接;可以是直接相连,也可以通过中间媒介间接相连。对于本领域的普通技术人员而言,可以具体情况理解上述术语在本发明中的具体含义。如图1所示,本发明的实施例中提供了一种工件4缺陷的检测装置,包括用于检测工件 4缺陷数据信息的超声检测单元1,位置采集单元2以及处理单元3;
位置采集单元2与超声检测单元1连接,用于采集超声检测单元1在工件4检测面上移动的位置信息;处理单元3分别与位置采集单元2以及超声检测单元1连接,用于将工件4缺陷的数据信息与该缺陷在特定位置的位置信息一一对应转换成缺陷的三维图像;本发明的实施例中,超声检测单元1检测工件4内部的缺陷数据信息,并将上述缺陷数据信息信号输出,位置采集单元2采集超声检测单元1在工件4检测面上的位置信息,并将上述位置信息信号输出,处理单元3接收上述缺陷数据信息信号以及位置信息信号,且将缺陷数据信息与该缺陷在特定位置的位置信息一一对应转换成缺陷的可视三维图像,该检测装置可根据缺陷的位置得到缺陷的可视三维图像,能够得出特定位置的缺陷的三维图像,增强了缺陷的直观性;对于该检测装置而言,该检测装置可用于检测多种工件4的内部缺陷,该工件4可为碳纤维结构、钢铁等。如图1以及图2所示,本发明的实施例中,超声检测单元1包括用于发射超声波至工件4内部的超声波发射单元11,以及超声波接收单元12;超声波接收单元12用于接收工件4反射回来的超声波,并将超声波信息信号输出;处理单元3与超声波接收单元12连接,用于接收超声波信息信号;本发明的实施例中,超声波发射单元11向工件4表面通过耦合剂发射超声波,超声波在工件4内部传播时遇到不同界面将有不同的反射信号,超声波接收单元12将上述反射信号接收且输出至处理单元3,处理单元3接收上述信号;其中,超声检测单元1包括一超声波探头13,该超声波探头13可在市面上购买得到;超声波探头13在检测时,超声波探头13与工件4的检测面接触,且其工件4的检测面接触的超声波探头13上涂有耦合剂,上述耦合剂可为油、凡士林等等。如图1以及图2所示,本发明的实施例中,位置采集单元2包括第一位置记录仪21、第二位置记录仪22以及数据采集器23;第一位置记录仪21以及第二位置记录仪22与超声波探头13连接,用于记录超声波探头 13在x轴方向以及y轴方向上的位置,并将各自的位置信息输出;数据采集器23分别与第一位置记录仪21以及第二位置记录仪22连接,用于采集超声波探头13的位置信息,并将位置信息信号输出;处理单元3与数据采集器23连接,用于接收位置信息信号;本发明的实施例中,第一位置记录仪21以及第二位置记录仪22分别于超声波探头13连接,在检测时,超声波探头13在工件4检测面上的一个位置进行检测完毕后,可手动移动超声波探头13至下一个位置,第一位置记录仪21以及第二位置记录仪22便是测量超声波探头 13移动后在x轴方向的位置以及在y轴方向的位置,得出缺陷在x轴方向的位置以及在y轴方向的位置,数据采集器23采集超声波探头13的位置信息,并将该位置信息的信号输出,处理单元3接收位置信息的信号,将位置信息与工件4缺陷的数据信息一一对应;需要说明的是,上述的位置信息包括x轴方向的位置以及在y轴方向的位置外,还包括 z轴方向的位置,z轴方向的位置信息的获取是通过处理器31从超声波探头13读取缺陷相对检测面的埋深,埋深与x、y轴方向的位置信息相组合得到缺陷在工件4中的三维空间位置信息;第一位置记录仪21以及第二位置记录仪22可在市面上购买,只有能够记录到超
声波探头13移动后的位置信息即可。如图1以及图2所示,本发明的实施例中,处理单元3包括具有操作面板33的处理器 31;处理器31将超声波信息信号以及位置信息信号一一对应转换成缺陷的三维图像;显示面板32用于显示缺陷的三维图像;本发明的实施例中,处理器31具有操作面板33以及显示面板32,操作面板33可用于手动修改设置参数,通过操作面板33操作监控程序执行等等,处理器31将超声波信息信号和位置信息信号一一对应转换成缺陷的可视三维图像,转换成的可视三维图像通过显示面板32显示出来,能够比较直观地查看特定位置的缺陷的三维图像。具体地,该工件缺陷的检测装置还包括一操作台5,由上可获得,超声检测单元1包括超声波探头13,位置采集单元2包括第一位置记录仪21、第二位置记录仪22以及数据采集器23,处理单元3包括具有操作面板33以及显示面板32的处理器31,第一位置记录仪21、第二位置记录仪22、数据采集器23以及处理器31均设于操作台1上,工件4放置或固定于操作台1上,超声波探头13可通过手动在工件4的检测面上移动,超声波探头13与第一位置记录仪21以及第二位置记录仪22连接,且与处理器31信号通讯,第一位置记录仪21以及第二位置记录仪22均通过数据采集器23与处理器31信号通讯。如图3所示,本发明的另一个目的在于提供一种工件4缺陷的检测方法,采用上述技术方案提供的工件4缺陷检测装置,包括:处理单元3将超声检测单元1检测的工件4缺陷的数据信息与位置采集单元2采集的超声检测单元1在工件4检测面上的位置信息一一对应转换成缺陷的三维图像;本发明的实施例中,超声检测单元1检测工件4内部的缺陷数据信息,并将上述缺陷数据信息信号输出,位置采集单元2采集超声检测单元1在工件4检测面上的位置信息,并将上述位置信息信号输出,处理单元3接收上述缺陷数据信息信号以及位置信息信号,且将缺陷数据信息与该缺陷在特定位置的位置信息一一对应转换成缺陷的可视三维图像,该检测方法可根据缺陷的位置得到缺陷的可视三维图像,能够得出特定位置的缺陷的三维图像,增强了缺陷的直观性;对于该检测方法而言,该检测方法可用于检测多种工件4的内部缺陷,该工件4可为碳纤维结构、钢铁等。如图3所示,本发明的实施例中,包括:超声波探头13检测工件4缺陷的数据信息,并将检测到的数据信息输出;第一位置记录仪21以及第二位置记录仪22分别记录超声探头在x、y轴的位置信息,并将各自的位置信息输出;数据采集器23采集x、y轴方向的位置信息,并将x、y轴方向的位置信息信号输出;处理器31接收超声波信息信号以及x、y轴方向的位置信息信号,以及处理器31从超声波探头13读取缺陷相对检测面的埋深,且将该埋深与x、y轴方向的位置信息相组合得到缺陷在工件4中的三维空间位置信息;处理器31将数据信息信号以及相应的三维空间位置信息一一对应转换成缺陷的三维图像;本发明的实施例中,对于缺陷在工件4中的三维空间位置的确定方式为:第一位置
记录仪21记录超声波探头13在x轴方向的位置信息,也就是缺陷在x轴方向的位置信息,第二位置记录仪22记录超声波探头13在y轴方向的位置信息,也就是缺陷在y轴方向的位置信息,处理器31读取的缺陷相对检测面的埋深为缺陷在z轴方向的位置信息,从而获得缺陷在工件4中的三维空间位置信息;处理器31将缺席数据信息与三维空间位置信息对应、合并并处理成图像,建立几何模型,得到三维图像,对三维图像进行可视化检测,得到最终的可视三维图像。本发明的实施例中,包括:将生成的缺陷的三维图像进行图像二值化,得到缺陷的三维二值化图像。本发明的实施例中,三维图像的二值化:检测图像的处理基于机器视觉的缺陷目标自动识别与提取实现图像二值化,以ksw熵方法作为图形分割的阈值选取方法,并利用选取的最优阈值,在碳纤维几何模型的基础上,matlab对图像进行分割,提取缺陷目标,实现图像的二值化,在算法上引入图像的二次统计特性,改善图像的分割质量,图像的二值化使图像中数据量大为减少,从而能凸显出目标的轮廓。本发明的实施例中,包括:处理器31接收缺陷数据信息信号,将缺陷的数据值对应不同的rgb颜色值,再将缺陷的数据值对应位置信息;本发明的实施例中,单次测得的缺陷数据值对应的rgb颜色值细化,颜色区分更加明显,图像分割更加精准,手动次数增加,相应地整合得到的检测图像及二值化图像拥有更高的精确性。如图4所示,本发明的实施例中,包括:s1:将待测工件4置于操作台上并固定;s2:在超声波探头13接触工件4检测面的表面涂上耦合剂;s3:选择检测面的一个位置,超声波探头13对该位置的检测面进行扫描,执行步骤s5,该位置检测结束,执行步骤s4;s4:手动将超声波探头13移动至下一位置继续检测,执行步骤s5;s5:处理器31将接收到的缺陷数据信息和缺陷在该位置的位置信息一一对应转换成三维图像;耦合剂为油或凡士林;本发明的实施例中,包括:规定超声波探头13由上一位置移动到下一位置进行检测的时间间隔;本发明的实施例中,工件4为碳纤维结构,具体地,将待测的碳纤维结构水平置于操作台上,并对上述待测的碳纤维结构固定,在检测过程中避免碳纤维结构位置移动,导致在x 轴方向以及y轴方向的位置不准确;在操作台上对定时器定时,规定每一次检测的时间间隔,提高检测效率以及准确性;在超声波探头13接触检测面的表面涂上一层油;选择检测面的一个位置,超声波探头13接触探测面,超声波探头13对该位置的检测面进行扫描,处理器31 将接收到的缺陷数据信息和缺陷在该位置的位置信息对应、合并并处理成图像,建立几何模型,得到三维图像,对三维图像进行可视化检测,得到最终的可视三维图像;将可视三维图像进行二值化处理,分析得到三维二值化图像;超声波探头13在该位置检测结束后,手动移动超声波探头13至检测面的下一个位置进行检测,同时,第一位置记录仪21以及第二位置记录仪22记录超声波探头13移动后的位置,处理器31进行接收并处理的操作。
需要说明的是,第一位置记录仪21以及第二位置记录仪22对位置的记录与超声波探头13检测同时进行,耦合剂为油或凡士林。以上仅是本发明的较佳实施例而已,并非对本发明作任何形式上的限制,虽然本发明已以较佳实施例揭露如上,然而并非用以限定本发明,任何熟悉本专利的技术人员在不脱离本发明技术方案范围内,当可利用上述提示的技术内容作出些许更动或修饰为等同变化的等效实施例,但凡是未脱离本发明技术方案的内容,依据本发明的技术实质对以上实施例所作的任何简单修改、等同变化与修饰,均仍属于本发明方案的范围内。